Flow Switches
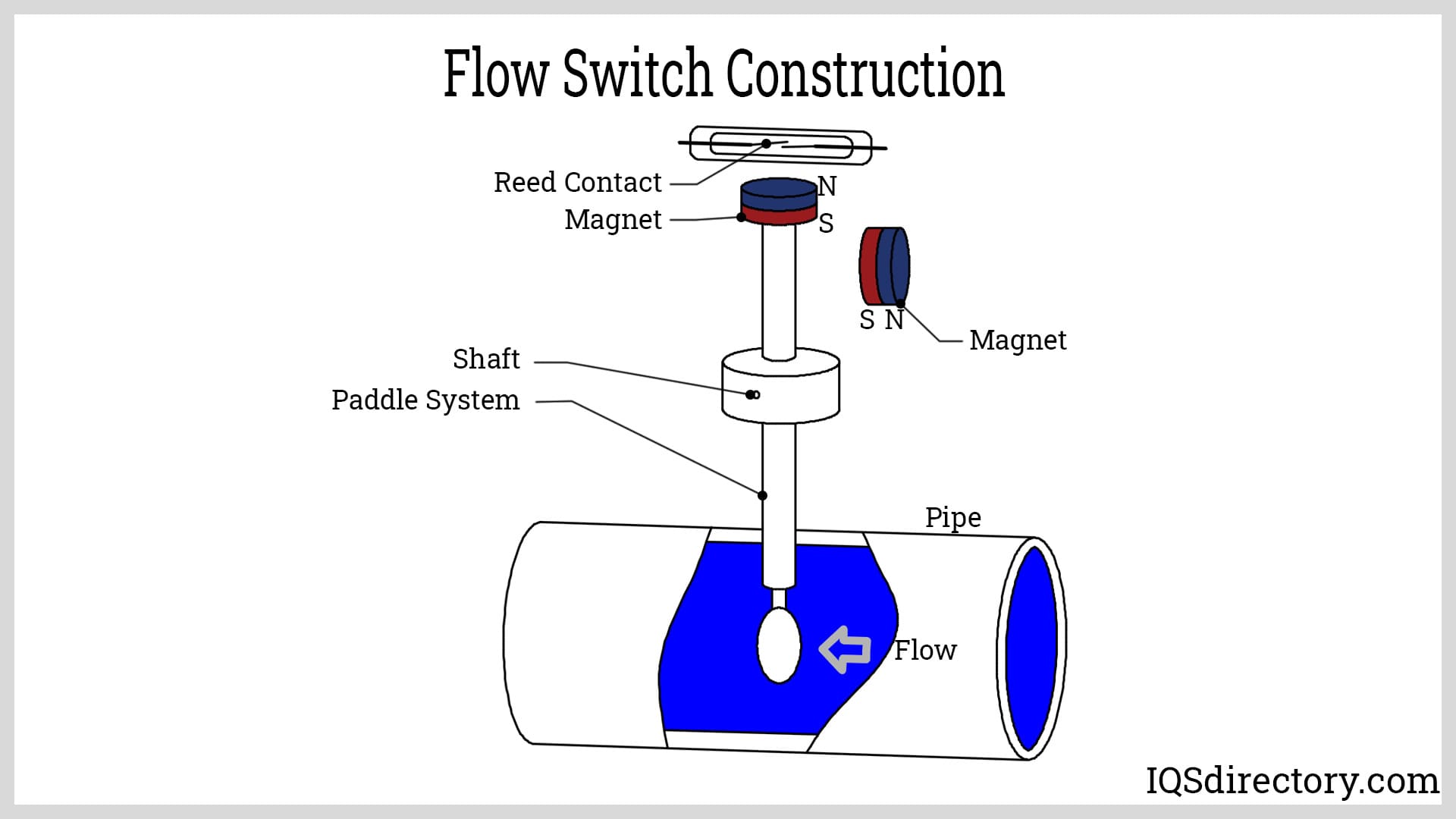
A flow switch is a device that measures the flow rate and liquid pressure within a duct, loop, or system. Flow sensor and flow indication are other names for this switch. The primary purpose of a flow switch is to...
Please fill out the following form to submit a Request for Quote to any of the following companies listed on
This article contains all the information you need to know about Coriolis Flow Meters.
You will learn more about topics such as:
A Coriolis flow meter calculates mass flow by harnessing the inertia of a fluid or gas as it travels through a vibrating tube. By placing sensors at the meter's entry and exit points, they can detect oscillations generated by the flow. The fluctuations in these oscillations are directly related to the mass of the material passing through the device. The innovative design and functioning of Coriolis flow meters make them exceptionally dependable for assessing both fluids and gases.
Coriolis flow meters are extensively utilized in numerous industries that manage the flow of liquids, gases, or other fluids. With their cutting-edge technology, they offer precise and consistent readings of mass flow rates, as well as fluid density, viscosity, and temperature.
To grasp the operation of a Coriolis flow meter, it’s essential to understand the Coriolis principle, first described by Gaspard-Gustave de Coriolis in his 1835 paper, "On the Equations of Relative Motion of a System of Bodies." This scientific principle led to what is now known as "The Coriolis Effect," the foundation behind all modern Coriolis flow measurement technology.
In simple terms, the Coriolis effect explains that any moving object on or above the Earth's surface, such as ocean currents or air masses, will experience a lateral drift due to the Earth's rotation. Similarly, in a Coriolis flow meter, the movement of process fluids (liquids or gases) through the meter’s precision-engineered tubes induces specific twisting motions. This twisting—caused by inertial forces—is continuously measured and interpreted to provide accurate flow readings, analogous to the sideways drift observed in the Coriolis effect. As a result, Coriolis flow meters allow for precise and reliable industrial flow measurement of mass, density, and temperature across a wide range of process applications.
Substances such as process liquids, slurries, and gases are frequently transported through pipelines across industries like chemical processing, food and beverage, oil and gas, water treatment, and pharmaceuticals. Each medium presents unique measurement challenges, such as varying densities, viscosities, and flow profiles. Coriolis flow meters have become a preferred flow measurement technology for their unmatched accuracy, especially when measuring mass flow and density in real-time conditions.
Unlike volumetric flow meters, which measure the volume flow rate (e.g., gallons per minute or liters per second), Coriolis mass flow meters provide direct and true mass flow measurement. Mass flow rate is not affected by changes in fluid properties—such as pressure, density, temperature, or viscosity—which can impact volumetric measurements. As a result, Coriolis meters are especially valuable in custody transfer, blending, batching, and other critical flow applications where precise and repeatable mass flow data is required. There is no need for flow meter recalibration across varying fluids, since mass is a constant, making Coriolis flow meters universally applicable for a diverse range of process fluids and gases.
The precision-engineered U-shaped (or sometimes straight or dual-shaped) measuring tube in a Coriolis flow meter is crucial for its core operation. As the process fluid flows through the tube, an exciter induces a controlled harmonic oscillation (vibration). The interaction of this movement with the inertia of the flowing mass causes the tube to deform minimally and twist in response. This deformation generates measurable phase differences, as represented by the fluid force arrows in the diagram below. Coriolis sensors detect these changes to derive accurate mass flow readings.
The exciter, or actuator, is responsible for maintaining the continuous oscillation of the measuring tubes. Precise oscillation is essential for generating the Coriolis effect within the instrument. In the absence of fluid flow, the oscillation remains uniform and symmetrical. As shown in the image below, the exciter is strategically positioned at the lowest point of the tube, between the highly sensitive measurement sensors. This configuration ensures reliable detection of oscillation variations for maximum flow meter accuracy during both zero flow and process conditions.
Specialized electrodynamic pickup sensors are located at both the inlet and outlet of the oscillating tube. These sensors continuously monitor the tube’s motion, capturing changes in phase and amplitude of oscillation. During zero flow, the oscillation pattern remains synchronized. Upon introduction of liquids or gases, the flow creates an inertial lag between the inlet and outlet sensors, resulting in a measurable phase shift. This critical data allows the Coriolis flow meter to directly calculate the mass flow rate independent of fluid properties or flow profile, cementing its reputation as a highly accurate and repeatable industrial flow measurement solution.
The measured phase shift is directly proportional to the mass flowing through the meter at any given moment and forms the core measurement principle of Coriolis flow meters. This produces a linear output that ensures high accuracy and repeatability across varying flow ranges and process conditions. Because this process measures mass flow directly—without inference from volume or velocity readings—it can be used to measure almost any fluid, regardless of viscosity, density, or pressure fluctuations.
In addition to phase shift, the sensors capture the natural resonant frequency of the vibrating tube, which correlates directly to the density of the process fluid or gas. Advanced Coriolis flow meters harness this resonance data in real time, allowing for simultaneous measurement of mass flow, density, and—through calculations—volume flow. Integrated temperature sensors further optimize accuracy by compensating for thermal expansion or contraction of the tubes. This comprehensive suite of measurements is critical for applications demanding both mass and density measurement, such as blending, dosing, or quality control in process industries.
The advanced digital controller integrated into the flow meter processes the acquired data from phase shift, tube vibration, and temperature sensors. It converts these precise Coriolis measurements into standardized outputs for mass flow, volumetric flow, and density, which are viewable on the user interface display. Mass flow readings are typically displayed in pounds per hour (lb/hr) or kilograms per hour (kg/hr), depending on the application and the type of flow meter configuration.
Coriolis flow meters offer significant flexibility, high turn-down ratios, and adaptability, making them suitable for a wide range of industrial flow measurement applications. Available in sizes as small as 0.04 inches (1 mm) for laboratory and specialty chemical services—or as large as 12 inches (300 mm) for oil and gas transfer pipelines—these meters are engineered for scalability. When selecting a Coriolis flow meter, it is important to consider parameters such as pipe size, pressure rating, required flow range, chemical compatibility, and integration into process control systems, all of which should be addressed prior to purchase and installation to ensure both reliability and longevity.
The versatility of modern Coriolis flow meters extends to the advanced digital outputs, diagnostics, and communication protocols offered. Some models offer integrated diagnostics for predictive maintenance, remote flow monitoring, and compliance with industry standards (such as AGA, API, or ISO for custody transfer and fiscal measurement). While most meters deliver similar sets of flow and density data, they can differ in configuration, calibration, and utility features depending on complexity and manufacturer. The core parameters and functionalities typically provided by a Coriolis flow meter include:
In summary, the Coriolis flow meter stands out as an industry-leading technology in process instrumentation for direct mass flow measurement, offering high accuracy, minimal maintenance, and the ability to handle a wide array of challenging fluids and gases. Whether ensuring the precise transfer of chemicals, monitoring fuel oil delivery, or guaranteeing product quality in food and beverage operations, Coriolis flow meters deliver reliable, real-time data. By understanding their operating principles and selection considerations, you can leverage Coriolis flow meters to maximize process efficiency, minimize downtime, and achieve compliance with modern flow measurement standards.
Coriolis flow meters are essential measurement instruments for accurately determining fluid and gas flow rates in industrial processes. Their unmatched precision helps manufacturers optimize profitability, uphold product quality, and ensure operational efficiency. Even minor discrepancies in mass flow measurement or density readings can result in costly product losses or process downtime, making the use and selection of high-performance flow meters critical. To prevent these issues, rigorous and continuous calibration as well as real-time monitoring of the entire flow measurement system are necessary.
Coriolis flow meters are categorized based on their internal tube design and flow path configuration, with variants including single-tube, dual-tube, continuous loop, straight-tube, U-shaped, micro-bend, and triangle-shaped designs. Each configuration is engineered for specific applications, flow media, and installation requirements, offering distinct advantages in terms of accuracy, reliability, and maintenance. Since the introduction of the first single-tube Coriolis meter, technological advancements have greatly improved their stability, resistance to vibration, and capability to measure challenging process fluids such as viscous liquids, slurries, and multiphase flows.
The single-tube Coriolis flow meter is commonly used for measuring high-velocity fluid flows, especially in applications where minimizing pressure drop and reducing fouling is principal. By restricting the cross-sectional area within the tube compared to the process pipeline, measurement sensitivity is increased. Tube distortion—created when the fluid induces Coriolis acceleration—is detected against a fixed reference point or plane. To produce measurable displacement, the tube is subjected to high-amplitude oscillation or bending forces at a firmly anchored point. These meters excel in chemical processing, beverage manufacturing, and custody-transfer systems for liquids and gases. They are also known for simplified cleaning and lower maintenance in Clean-In-Place (CIP) processes.
In the dual-tube Coriolis flow meter, a flow manifold splits the process stream into two parallel, U-shaped tubes. These tubes are vibrated at a fixed frequency, and as the fluid passes through, Coriolis forces twist the tubes in proportion to the actual mass flow rate. This deformation generates a measurable time or phase difference between inlet and outlet pickoff sensors. The system employs magnets and pickoff coils positioned at both ends to monitor oscillation waveforms. Dual-tube meters offer superior immunity to external pipe vibration and pressure fluctuations, making them ideal for high-precision industrial flow, gas distribution networks, blending operations, and custody transfer in the oil and gas industry.
The continuous loop Coriolis flow meter utilizes a looped, uninterrupted tube arrangement that allows process fluid to circulate without being split. Operating on the same Coriolis principle, this design enhances performance for fluids prone to crystallization, scaling, or plugging, thanks to its larger, smoother passages. Additional components—such as electromagnetic drivers, magnets, and non-intrusive sensors—optimize stability and ensure reliable mass flow and density measurements. This flow meter is especially advantageous in applications handling viscous fluids, slurries, polymers, or aggressive chemicals. Continuous loop designs reduce maintenance intervals and the risk of clogging for industries such as wastewater treatment, pulp and paper, and food processing.
Straight tube Coriolis flow meters are available in single or dual straight-tube variants. As the process fluid traverses rigid tubes, induced Coriolis acceleration causes measurable flexure—detected by precision sensors and strain gauges. Compared to curved-tube meters, the straight-tube design offers lower pressure drop and reduced potential for residues to accumulate. Straight-tube Coriolis meters are preferred for sanitary applications, pharmaceutical processing, and biotechnological production where strict hygiene standards and seamless cleaning are required. The inherent rigidity and self-draining features help minimize contamination and simplify maintenance routines.
U-shaped Coriolis flow meters feature a classic dual-tube design, with two tubes bent into a U shape and equipped with a magnetic and coil assembly. Sensitive pickoff sensors are positioned at the tube's inlet and outlet to detect oscillation. The Coriolis force generated by the moving fluid is directly proportional to its mass flow rate and density. U-shaped meters provide robust, repeatable measurements in a wide variety of industrial environments, making them a popular choice for both liquid and gas flow measurement, batching, blending, and filling operations. Their symmetrical design delivers high accuracy even in fluctuating temperature or pressure conditions.
The micro-bend Coriolis meter employs U-shaped tubes with a significantly tighter radius of curvature. This compact configuration results in a smaller footprint, lower installation cost, and minimized pressure losses compared to traditional designs. Micro-bend flow meters are highly suitable for process skids, hazardous area installations, and precision dosing applications where space constraints, energy efficiency, and quick response times are essential. Additionally, their low-pressure differential makes them a strong option for laboratory analysis and specialty chemical dosing.
Triangle-shaped Coriolis flow meters offer an ultra-compact, single-tube design engineered for low-flow and low-pressure industrial applications. Their triangular configuration enables superior installation flexibility in tight spaces, while maintaining high accuracy for both liquid and gas service. Many models feature multivariable capability, allowing simultaneous mass flow, volumetric flow, temperature, and density measurement. Triangle-shaped meters are frequently used in precision chemical injection, analytical instrumentation, pilot processes, and microfluidics, where space, repeatability, and versatility are paramount.
Choosing the optimal Coriolis flow meter involves consideration of several factors, including process fluid type (liquid, gas, or slurry), flow rate range, temperature and pressure limits, installation constraints, and required measurement accuracy. For hygienic or sanitary operations, straight-tube and single-tube designs with self-draining features are recommended. For processes with viscous, abrasive, or particle-laden fluids, continuous loop or dual-tube meters offer greater durability and lower maintenance. If installation space is limited, micro-bend or triangle-shaped models provide reliable performance in compact footprints. Additionally, many Coriolis meters are capable of multivariable measurements, providing real-time mass flow, volumetric flow, density, and temperature readings for comprehensive process control.
By aligning your unique needs with the Coriolis meter’s tube configuration and measurement technology, you ensure accurate, reliable, and cost-effective flow management across diverse industries such as oil & gas, chemical production, pharmaceuticals, food & beverage, and water treatment.
Coriolis flow meters are versatile and can be installed in various types of pipes, regardless of orientation or vibrations. To ensure optimal performance, it is recommended to place piping supports on both sides of the meter. If the installation guidelines specify the need for special supports, it indicates that the meter may be sensitive to vibrations. Manufacturers often supply pulsation dampeners, flexible connectors, or clamping brackets to mitigate the effects of vibrations.
There are several types of supports available for Coriolis flow meters, which include U rest, Y rest, U bolt clamp, pipe hangers, and block clamps. These support mechanisms are not normally necessary, especially for newer versions.
Before starting the installation process, several factors need to be carefully considered to ensure the meter operates correctly. While modern Coriolis flow meters are generally resilient to vibrations, they should still be supported with standard piping supports on both sides of the meter.
It’s essential to assess the installation environment for temperature extremes and hazardous conditions before purchasing the meter. If the environment has special requirements, there are Coriolis flow meters designed to withstand high temperatures and hazardous conditions.
Coriolis flow meters are classified into various categories such as Class I, Class II, and so on, with further subdivisions into groups like A, B, C, D, etc. These classifications specify the appropriate use of the meter, including the types of fluids or gases it can measure. Ensuring that the meter matches the correct classification for its intended application is crucial, as using an incorrect meter could lead to inaccurate readings or safety issues.
The installation orientation of a Coriolis flow meter should align with the type of material being monitored. Meters must be positioned correctly to accommodate the specific fluids, gases, liquids, water, or slurries they will measure. The chart below provides a brief overview of various orientations.
Be sure to compare the preferred orientations with alternate options and consider the inclusion of the three different types of Coriolis flow meters depicted.
Sensors should be positioned away from potential sources of interference, such as pumps, as their vibrations can affect readings. When installing sensors in a series, ensure they are spaced at least two meters apart. Regardless of the flow meter's temperature range, consider the effects of pipe expansion and contraction.
In addition to following orientation guidelines, the meter should be mounted along a straight section of piping, avoiding high or low points and drop lines. During installation, ensure that the measuring tube or tubes are filled with the medium to be measured.
Each model, type, design, and size of Coriolis flow meter requires its own specific zeroing procedure. Zeroing is an automated calibration process accessible through the meter's zero setting menu. Simply selecting 'yes' initiates the zero calibration.
Before performing the zeroing process, allow the meter to warm up according to the manufacturer's instructions, which could range from five to twenty minutes depending on the model.
For accurate zeroing, ensure that the meter's tubes are filled with the measuring fluid or gas, avoiding any trapped air. This can be achieved by circulating the fluid through the meter at speeds between two to six feet per second for several minutes.
Successful calibration requires that the meter is fully charged with the material being measured while ensuring zero flow conditions. The standard error factor is 0.05 kilograms per minute, which represents the maximum deviation during measurement.
After setting the zero stability, the meter should deliver optimal performance, often surpassing other measurement methods. It is recommended to perform the zeroing process three or four times to check for any potential interference.
Among various types of flow meters, Coriolis flow meters stand out as the most versatile, precise, and adaptable. They utilize the Coriolis effect to measure mass flow, density, and temperature. As fluid moves through a pipe, it encounters a deflecting force due to the Coriolis inertial effect, which correlates with the mass flow rate. The force exerted by the fluid on the oscillating tube determines the mass flow rate.
The distinctive design of Coriolis flow meters enables them to accurately measure both viscous and non-conductive fluids, which other meters may not be able to handle. A single Coriolis flow meter is capable of measuring mass flow, volumetric flow, density, and temperature. The oscillatory movement of the meter's tubes generates Coriolis force, which is directly related to the mass of the flowing substance.
The measurement of mass flow is preferred over volumetric flow, which measures in terms of gallons per minute. Mass flow meters measure fluid flow in terms of weight such as pounds or kilometers per second, which is considered to be a more accurate measure especially in custody transfer.
Inside the flow tube of the meter, a drive coil induces vibrations at the tube's natural frequency. Even in the absence of flow, the tube vibrates, and the pickoffs generate signals based on these vibrations. This movement is observed between the two tubes.
When fluid enters the tube or tubes, they start to twist or oscillate rapidly. This acceleration creates a measurable force on the tubes that correlates with the mass of the flowing material. The material inside the tube interacts with this force, known as the Coriolis force. The distinction between no flow and flow is illustrated in the diagram below.
The time difference recorded between the inlet and outlet sensors is used to calculate the mass flow rate. Additionally, this signal can be utilized to determine the material's density. The Coriolis flow meter measures by observing the tube or tubes' movement at its operational frequency. As the material's density changes, so does the frequency; increased density leads to a decrease in frequency, while decreased density results in an increased frequency. For measuring the density of gases, a different type of measurement device is required, as Coriolis flow meters are not suitable for this purpose.
The viscosity of a fluid is assessed through the torsional action occurring at the center of the tube, where a counter-oscillating mass is positioned. As the fluid flows, the shear force exerted by the moving tube affects the fluid's viscosity. This change in viscosity alters the tube's oscillation pattern, which the meter detects and translates into a numerical value.
Higher viscosity results in reduced torsional oscillation of the tube, requiring additional power to maintain the oscillation. This power requirement reflects the dynamic viscosity of the fluid. In a dual-tube Coriolis flow meter, the oscillation can be observed through the blue arrows in the diagram, representing the upward and downward movements of tubes A and B.
The process temperature effect refers to the variation in sensor accuracy resulting from changes in the process temperature compared to the temperature at which the sensor was calibrated. This variation is managed during the zeroing procedure under actual process conditions.
Additionally, the accuracy of density measurements can be influenced by the process temperature if it deviates from the calibration temperature.
Coriolis flow meters are widely used for measuring mass, density, temperature, and viscosity across various substances due to their adaptability and precision. They maintain accurate measurements regardless of material disturbances and can be installed at any point along a pipe.
Their inherent ability to measure mass flow, combined with their linearity and accuracy, makes Coriolis flow meters particularly suitable for custody transfer operations, where precise measurement of fluids or gases is crucial during transactions.
Coriolis flow meters are preferred for their exceptional accuracy, which can be as precise as 0.1%. This high level of precision is a major factor behind their widespread adoption in recent years.
These flow meters are highly versatile, capable of measuring a broad range of substances. They are unaffected by ambient conditions and can handle a variety of gases, liquids, and fluids, including high-viscosity liquids, two-phase liquid-solid or liquid-gas mixtures, and dense high-pressure gases.
Coriolis flow meters are resilient to variations in flow velocity caused by upstream or downstream disturbances. For optimal performance, especially in cases of non-uniform flow, installing the meter on a straight section of pipe can enhance accuracy, as illustrated in the diagram below.
Measuring viscosity—essentially the thickness or texture of a fluid, or its resistance to deformation—can be challenging for many standard meters. However, Coriolis flow meters are designed to accurately measure viscosity without being affected by it. These meters provide detailed information on a fluid's thickness and its flow properties. For instance, as shown in the image below, fluids vary in how easily they flow, with the fluid on the left demonstrating smoother flow compared to the more resistant fluid on the right.
A Coriolis flow meter is a versatile instrument that offers a comprehensive set of readings on the movement and properties of materials within a pipeline. While its primary function is to measure mass flow, it also provides data on volume, density, temperature, and other parameters. Although specific readings may vary among different Coriolis flow meter models, they generally include measurements for mass, density, temperature, and viscosity.
Bidirectional flow, while less common in production settings, requires accurate measurement in both flow directions. Unlike many meters that need extensive calibration for bidirectional flow, Coriolis flow meters are designed to handle such measurements with ease due to their inherent adaptability and straightforward adjustment capabilities.
Some fluids are complex mixtures of liquids and gases, presenting challenges for measurement due to their unique properties. Coriolis flow meters excel in these situations, adapting to various fluid characteristics without issue. They are capable of measuring diverse substances such as asphalt, molasses, syrup, glucose, and slurries, contributing to their widespread adoption.
In food production, equipment must adhere to strict standards set by the Food and Drug Administration (FDA), which includes regular cleaning and sanitization. Coriolis flow meters are well-suited for this environment as they can be easily cleaned and sanitized to comply with FDA regulations. They are commonly used to monitor the transfer of oils, cooking solutions, and water in the food industry.
A flow switch is a device that measures the flow rate and liquid pressure within a duct, loop, or system. Flow sensor and flow indication are other names for this switch. The primary purpose of a flow switch is to...
A magnetic flow meter is a volumetric flow meter that uses electrodes connected to the liquid flow to measure the velocity of fluids in a tube or pipe. The unique design of magnetic flow meters allows them to take their readings without the need for any moving parts...
A mass flow meter is a way of measuring the volume or mass of a gas or liquid passing through a system at a specific point in the flow system. They are used to measure linear, nonlinear, mass, and volumetric flow rates...
A rotameter is a device that measures the flow of fluid volume per unit time in a closed tube. There are diverse rotameters applications, including chemical injection/dosing and tank blanketing. A rotameter can be said...
An ultrasonic flow meter measures the flow of a liquid or gas by sending ultrasonic waves across a pipe, containing the flow in the direction of the flow and in the opposite direction of the flow. The ultrasonic waves and the velocity of...
A flow meter is a flow rate measuring device used to determine the linear or nonlinear mass and volumetric flow of a liquid or a gas. The many names of flow meters include flow gauge, flow indicator, liquid meter, and flow rate sensor...