Aluminum Forging
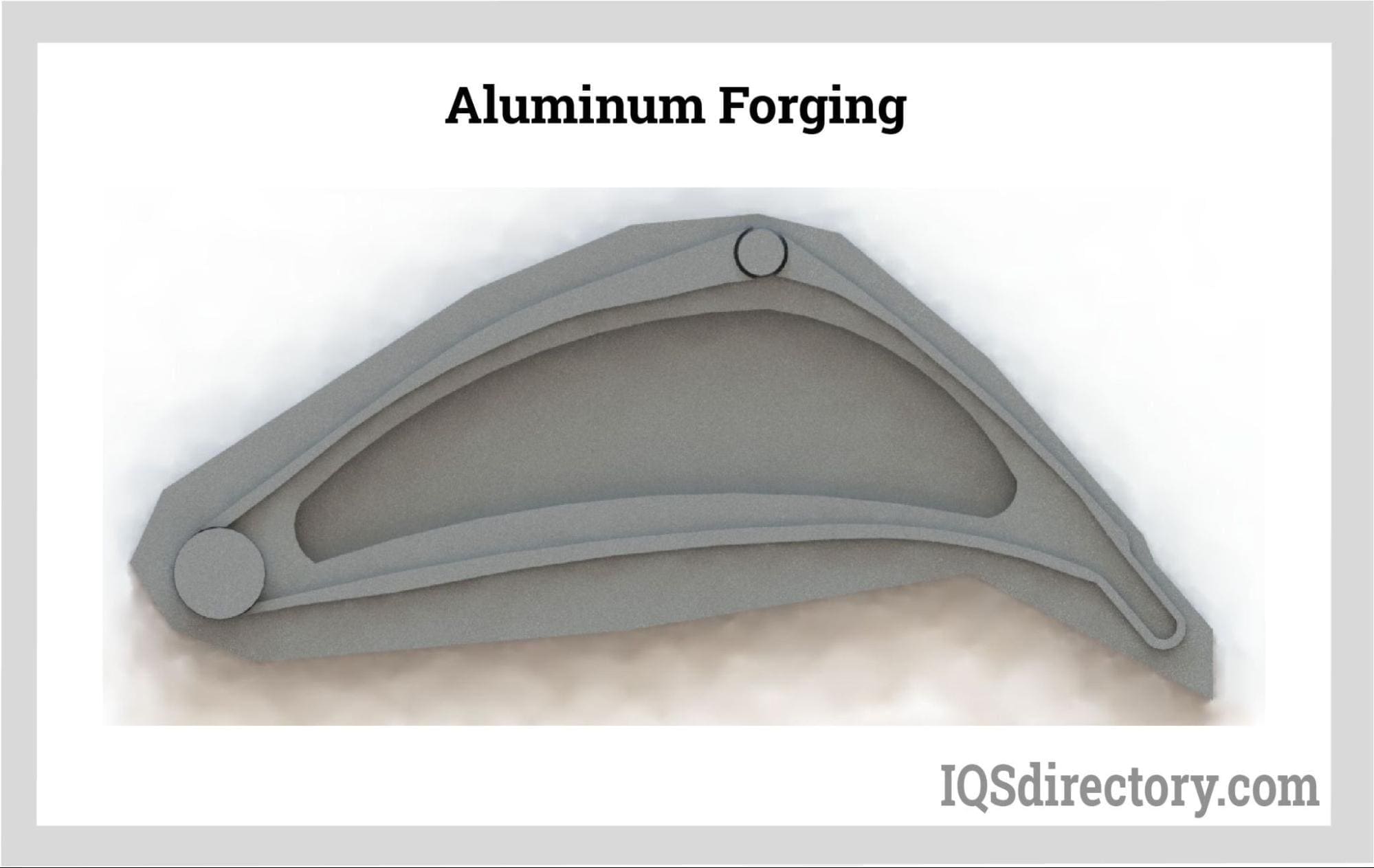
Aluminum forging is a technique for shaping aluminum alloys by applying pressure and heat to produce high-strength, durable products. This process involves methods such as pressing, pounding, and...
Please fill out the following form to submit a Request for Quote to any of the following companies listed on
This article covers everything you need to know about forging.
You will learn about topics such as:
Forging is a metalworking process that focuses on reshaping, deforming, and compressing metal to meet specific designs or blueprints. This can be accomplished through either hot or cold forging methods, which are chosen based on the metal type and design specifications.
Today's machinery, tools, and equipment extensively depend on forged components as integral parts of their functionality. From tools to firearms and automotive parts, forged elements are present in a diverse array of products. Despite its ancient origins, forging continues to be a cornerstone of modern metalworking and manufacturing industries.
The forging process has been used for thousands of years in various forms to shape metal. While technological advancements and the development of new metals have brought changes to the process, the fundamental principles remain largely the same. Regardless of the specific method employed, forging always involves the shaping of metal. The basic steps of forging may vary, but they maintain a core similarity across different techniques.
The choice of forging process largely depends on the type of metal being used. Although metals have diverse characteristics and properties—such as weight, tensile strength, and deformation capabilities—nearly all metals can be forged.
TCommon metals used in forging include carbon steel, alloy steel, stainless steel, aluminum, titanium, brass, copper, cobalt, nickel, and molybdenum.
The impact and compression operation used in forging depends on the metal. Heavier metals require heat treatment before forging, while softer metals like aluminum, brass, and copper can be cold forged. Regardless of whether the method is hot or cold, the forging process always involves applying force with a hammer, mold, or heavy weight. This application of force is central to the forging process.
Annealing Annealing is a crucial part of the forging process, aimed at changing the physical shape and properties of a metal. Its primary purpose is to increase the metal's ductility and reduce its hardness, making it more workable. During annealing, the metal is heated above its recrystallization temperature and kept at that temperature while it is being worked. The cooling rate of the metal during annealing varies depending on the type of metal.
Although annealing is primarily associated with hot forging, it is also utilized in cold forging. In cold forging, the metal is heated just enough to allow it to be forged, which means the temperature is slightly below its recrystallization point.
Once the metal becomes pliable, it is formed, shaped, configured, and manipulated to achieve the desired shape. This stage can involve hammering, grinding, molding, compressing, and bending, depending on the chosen method. Regardless of the specific forging process, the metal undergoes a series of stressing steps to transform it into the planned design.
The hardening of the forged part depends on the chosen process. In cold forging, the workpiece hardens through the working process itself, which strengthens the plastic deformation. In contrast, hot forging achieves hardening and strengthening through recrystallization. As the metal is compressed and deformed during forging, its grain structure changes to match the geometry of the forged part. Cold forging enhances fatigue resistance and improves mechanical properties.
As can be seen in the diagram below, the grain flow for forged parts conforms to the shape of the part. This feature enhances the part‘s strength and fatigue resistance.
Tempering strengthens the metal. This process involves heating, shaping, cooling, and reheating, which induces stress. By tempering a forged part, the metal becomes less brittle and more ductile without losing hardness. The result is harder and tougher parts that are both weldable and ductile. This increased toughness also provides greater resistance to wear and abrasion, which is essential for parts that will endure extreme wear and harsh conditions.
While most parts produced by forging can be made using other methods, forging is preferred for its ability to produce exceptionally strong and durable finished products. This process alters the metal's structure through compression, leading to metallurgical recrystallization and realignment of the grain. As a result, the forged parts exhibit higher impact and shear strength, which enhances their longevity and overall usefulness.
The classic image of forging often features a blacksmith hammering out a shape on an anvil. For centuries, manual hammering and shaping of metals have been synonymous with the forging process. However, thanks to technological advancements and developments, forging has significantly evolved beyond the traditional hammer and anvil.
Modern forging employs a variety of advanced techniques and heavy-duty equipment to produce parts crucial for many societal needs. The term "forging" broadly refers to several methods used to transform metal sheets into functional items.
Forging is universally categorized into cold and hot forging. Cold forging shapes metal with minimal heat, while hot forging involves heating metals close to their melting point.
Open die forging, also known as drop forging, shapes a workpiece without fully enclosing the metal within the die. This process involves striking the workpiece with the die until it conforms to the die's shape and form. Before being placed on the anvil for shaping, the workpiece is heated and then hammered to achieve the desired shape.
Closed die forging, or impression forging, involves two die halves moving toward each other to enclose the workpiece or billet. The heated billet, which is roughly the size of the final part, is placed in the bottom die. The force from the meeting dies compresses the billet to shape it into the desired forged part. Although this process is initially more expensive than other forging methods, the investment is justified by the accuracy, quality, and strength of the finished parts.
Cold forging shapes and processes metals at room temperature or just above it. This term encompasses various techniques such as drawing, heading, coining, punching, and thread rolling. In cold forging, the metal is worked at approximately 30% of its recrystallization temperature. This method is particularly suited for soft metals like aluminum and copper. Cold forging offers benefits including reduced post-processing of finished parts, superior surface finishes, enhanced dimensional stability, and lower costs.
Roll forging is a process that uses heated metal and opposing rolls to shape and deform a workpiece. The part's shape and dimensions are determined by the geometric patterns cut into the rolls. As the workpiece passes between the rolls, they partially turn to form the part. The geometric patterns on the rolls cover about one-fourth to three-fourths of their surface area. The grooves in the rolls create a variable cross-section on the workpiece, which can be further refined through secondary finishing.
In rolled ring forging, the workpiece is first shaped into a donut or oval by removing the central portion. It is then heated to make it workable and pressed between a driver roll, an idler roll, and axial rolls, all rotating simultaneously. The workpiece sits on the idler roll, which gradually moves it against the driver roll, expanding its diameter and thinning its walls. The axial rolls manage the ring's width as it is rotated by the idler roll. The result is a seamless oval ring, suitable for manufacturing gears, valves, clutches, and bearings.
The rolled ring process offers several advantages, including stronger components, reduced machining requirements, a robust grain pattern, and compatibility with a wide range of materials. The diagram below provides an example of rolled ring forging.
Upset forging, also known as heading, can be performed either hot or cold. This process involves upsetting the end of the workpiece to increase its cross-sectional area. It is typically used with horizontal bar workpieces and is commonly employed to produce nails, screws, nuts, and bolts. The desired shape is often achieved using a punch or die, and in some cases, both methods are utilized to obtain the final form.
The stages of the process are illustrated below in this cold forging example, where a rod is secured in the lower portion and repeatedly struck by various dies to achieve the desired shape.
The isothermal forging method takes a unique approach to heating the workpiece. For metals and alloys with low temperature forgeability, processing can be challenging. Isothermal forging addresses this by maintaining the workpiece at its highest temperature throughout the process. This is achieved by heating the die to a temperature that is at or slightly below that of the workpiece. This method eliminates the mold work interface and enhances the characteristics of the final part.
Multidirectional forging is a time and cost saving hot forging process for the production of complex and intricate parts. A mill length steel bar is inserted into the forging machine at room temperature. As the bar enters the machine, it is super-heated by induction coils to temperatures between 2000° F and 2400° F. The bar is then descaled and formed into blanks, which progress into the forging mechanism. A precisely timed series of forming stages shape the blanks. After this, the completed parts are cooled and finished by cold forming.
As the heated workpiece passes through the multidirectional forge, it is fully shaped in a single step, with rams applying force from both horizontal and vertical directions.
Most metals can be shaped and formed through forging. As the process has been refined and developed, the range of metals that can be forged has steadily increased, since all metals respond to heat and compression. Forging is valued for its ability to produce parts with exceptional mechanical properties while minimizing waste. The goal of the process is to deform metals into a desired shape, enhancing their fatigue resistance and strength.
While most metals can be forged, carbon, alloy, and stainless steels are the most commonly used. Forging is capable of producing large quantities of parts both efficiently and economically, regardless of the type of metal.
Carbon steel is malleable, easily processed, and forgeable, and it responds well to heat treatment. Its main advantages include low cost, versatility, strength, and ease of deformation and shaping. It is the most commonly used metal for forging parts and components across various industries.
Stainless steels are iron alloys enriched with chromium, along with other elements to enhance their structure and properties. These additions improve the metal's formability, strength, and toughness. The key benefit of stainless steel is its resistance to corrosion and rust, which makes it suitable for a wide range of environmental and processing conditions.
Stainless steel is a broad term encompassing a variety of metals with different grades, each offering distinct performance characteristics due to their varying compositions. The 300 and 400 series grades are commonly used for forging.
The 300 series is made of iron and chromium nickel alloys.
The 400 series of stainless steel is 11% chromium and 1% manganese with a higher carbon content, which gives it a martensitic crystalline structure, which gives this grade of stainless steel higher wear resistance and strength.
Alloyed steel is combined with various elements such as manganese, silicon, nickel, titanium, copper, chromium, tungsten, molybdenum, and aluminum in different proportions. These additional elements enhance the steel's basic properties, including hardness, corrosion resistance, strength, formability, weldability, and ductility. Steel with more than 8% of its weight in alloying elements is classified as high alloy steel. When the carbon content exceeds 8%, the steel becomes more challenging to form, whereas with a carbon content below 3%, the steel is more easily formable.
Aluminum is classified as a soft metal because of its low melting point. Despite being lightweight and easily shaped, aluminum is strong and highly resistant to corrosion and rust. Typically, it is alloyed with other metals to enhance its inherent properties. One of aluminum's key advantages is its ability to be continuously recycled without losing its characteristics or quality.
Copper, similar to aluminum, is classified as a soft metal and is easily formable. During the forging process, copper is typically used in bar form. Forged copper benefits from an improved microstructure and maintains its mechanical properties. Copper forging involves a hot closed die process, where the copper is heated using induction.
Titanium is a high strength, low density metal with exceptional corrosion resistance; it is ductile and has a high melting point. Parts produced from titanium have properties similar to those found in carbon steel forgings but are much lighter. A major benefit of titanium is its ability to withstand high temperature environments —up to 1000° F. The excellent strength to weight ratio of titanium makes it ideal for engine and aircraft components as well as valves for the chemical industry.
Brass is an alloy of copper and zinc, with its mechanical properties varying based on the amounts of zinc and other elements. This combination results in brass being harder yet softer than copper, with a lower melting point. Its excellent formability makes brass ideal for applications requiring exceptional thermal and electrical conductivity. Like copper, brass is resistant to corrosion and rust, making it suitable for environments where durability and longevity are essential.
Nickel forgings are ideal for high-temperature environments where severe conditions and wear resistance are crucial. The forging process shapes nickel into geometric forms that often require no further machining and enhances the metal's grain structure. Nickel is forged using hot forging with a closed die, which helps the metal maintain its flow stress. This characteristic makes nickel particularly well-suited for industries such as aerospace, oil, defense, and marine, where durability and performance are essential.
The metal forging process involves shaping and forming metals through compressive force, applied via hammering, pressing, stressing, or rolling. Forging processes are categorized into cold and hot forging, depending on the temperature at which the metal is deformed.
Forging is essential in manufacturing many critical components used in product production and industrial operations. Despite numerous technological advances in the industry, forging remains central to efficient, cost-effective, and high-quality production.
A drop hammer machine features two dies: one mounted on a stationary anvil and the other attached to a ram. A heated billet is positioned in the lower, stationary die. The ram repeatedly brings the upper die down onto the stationary die with significant force to shape the billet. The number of hammer strikes required depends on the specific item being produced.
There are various types of drop hammers:
A board drop hammer depends on gravity to supply the speed at which the hammer will strike the workpiece.
A belt-driven drop hammer operates similarly to a board drop hammer but uses a belt mechanism. The ram is connected to a belt, which is controlled by rollers that grip it. As the ram rises, the belt slackens. When the rollers are released, the ram drops and strikes the workpiece.
Power drop hammers use pressurized air to raise the ram and accelerate the dropping speed.
Press forging machines operate on the same principle as drop forging but use a continuous compressive force rather than multiple blows. Like drop hammer machines, press forging machines feature a die with two halves: one on the anvil and the other connected to the ram. Instead of applying concussive force, the upper die gradually squeezes and compresses the workpiece into the lower die. This compression force is applied by a hydraulically driven or screw-driven ram, which uniformly penetrates the workpiece and induces plastic deformation throughout its volume.
The core of a roll forging machine consists of opposing rollers that shape the workpiece and support the dies. Support rails provide constant tension to the rollers, allowing the framework to maintain a low spring constant. During operation, the rollers are pressed together with more force than needed to deform the workpiece. Backup rollers, positioned asymmetrically to the workpiece's plane, support the work rollers. A hydraulic cylinder drives the work rollers together, applying consistent and steady pressure to shape the workpiece.
In upsetter forging, the workpiece is positioned between two horizontal grooved dies that secure it while one end is rammed and punched to deform it. The term "upsetting" refers to altering the shape of a billet, bar, or bloom by increasing its cross-sectional area on the horizontal plane. This process, also known as heading, involves applying pressure to a hot or cold rod or billet to achieve the desired shape.
A rotary forging machine functions by placing the workpiece inside a circular housing with rotatable anvils that have dies on one end. The workpiece is positioned at the center of a set of rollers and anvils contained within a rotating cage. As the cage spins, the rollers drive the anvils to repeatedly hammer or impact the workpiece until it achieves the desired shape.
Numerous machines are available for forging, playing a crucial role in today's society by producing strong, durable, and custom-shaped metal components for industries such as automotive, agriculture, construction, and oil. Below, we explore some prominent brands of forging machines used in the United States and Canada:
The Ajax-CECO Bulldog 200 is a versatile forging machine renowned for its durable construction, high forging capacity, and adaptable control systems, which facilitate the efficient production of a diverse array of forged components.
Schuler's SMG Series machines are renowned for their precision, high-speed forging capabilities, and advanced automation features. These attributes ensure reliable and efficient production of forged parts with complex shapes and stringent tolerances.
Nedschroef Machinery provides the RF series of forging machines, designed for high-volume production. These machines feature advanced hydraulic systems, rapid die change capabilities, and optimized energy consumption, making them ideal for cost-effective forging operations.
ERIE Press Systems specializes in electric forging presses that are recognized for their energy efficiency, precise control, and versatility. These presses offer high force output and programmable settings, making them suitable for forging a wide range of materials and shapes.
Clearing's FBF Forging Presses feature robust construction, adjustable stroke and speed controls, and a range of tonnage options. These features ensure reliable and accurate forging processes for various components.
Please be aware that specific models, features, or components may vary. For the most current information on the latest models and capabilities of forging machines in the United States and Canada, it is recommended to consult the respective manufacturers or industry resources.
Forging is an ancient technique that has been utilized for centuries to produce and shape metal components. Over the years, this method has been refined, reinvented, and adapted to manufacture parts for a wide range of modern appliances and equipment.
Given its long history and continuous advancement, it's impossible to list all the applications for forged products. However, some notable uses include tools for home workshops, large pipeline fittings, components for agricultural machinery, and parts for spacecraft.
The strength, reliability, and durability of forged components make them ideal for heavy duty stressful applications.
The primary advantage of using forged parts in the automotive industry is the cost-effectiveness of the forging process, which still yields high-quality and reliable components. Forged parts are commonly used in areas subjected to shock, stress, and impact, such as wheel spindles, kingpins, axle beams, ball joints, and steering arms. Additionally, in the powertrain, forged components like transmission parts, connecting rods, differentials, and clutches are valued for their durability and longevity.
The agriculture industry requires parts, machines, components, and connectors to be highly durable to endure the rigors of farm work and harsh conditions. In addition to durability, cost-effectiveness is crucial, similar to the automotive industry. Farm machinery must meet these demands, which is why manufacturers turn to forging to meet these needs.
Similar to agriculture, the oil industry demands that parts and components be both durable and reliable, particularly for valves and fittings. The exceptional mechanical properties of forged parts make them well-suited for the harsh conditions and high-pressure applications in oil production. Oil fields expose equipment to a variety of corrosive fluids and extreme conditions, making it essential for valve bodies, flanges, reducers, and saddles to be resistant to corrosion, wear, and heat while performing effectively in diverse environments.
Most people encounter forged parts through hand tools, such as hammers, pliers, wrenches, and garden tools. Forged hand tools are known for their superior quality, exceptional performance, and guaranteed reliability. Although tools can be made using various shaping and forming techniques, forged tools are clearly labeled to assure customers that they are receiving the highest quality products.
The railroad industry demands equipment that is strong, durable, machinable, and cost-effective. Components such as gears, transmissions, levers, joints, hubs, and rollers must perform with precision and accuracy under heavy-duty conditions. Given that most railroad equipment is constructed from steel, it’s clear why forging is crucial to the industry.
Industries that rely on metal components and parts for their operations depend on forging for the production and fabrication of these elements. This includes sectors such as textiles, paper, power generation, and chemical production. Each of these industries needs reliable and readily available equipment to ensure uninterrupted and efficient production.
Whether a weapon is intended for a casual hunter or a soldier in a combat zone, it must perform flawlessly and immediately. Forged parts are essential for the main components of all types of weaponry. Given that weapons are often used under harsh and demanding conditions, they need to be durable and robust to withstand these environments. For these reasons, forged parts are fundamental to the construction of high-performance weapons.
A factor that influences the performance of an aircraft is the strength to weight ratio, which has an impact on the craft‘s range and payload. To produce safe and reliable aircraft, special alloys are created that have the durability and weight to meet the performance needs of aircraft applications. Aircraft production requires precision and accuracy such that each part and component fits flawlessly and works together harmoniously. The strength and endurance of forged parts make them a necessity.
Forging has remained a fundamental method of metal forming for many years due to its numerous advantages. Machinery, engines, and technical equipment rely on forging to deliver strong, durable, and reliable parts that ensure optimal performance in various conditions. Manufacturers and producers depend on forging to supply high-quality components for their products because of the consistent and beneficial performance of forged parts.
The controlled deformation inherent in the forging process leads to metallurgical soundness and exceptional mechanical properties. This outcome is achieved through pre-working the metal before forging, which establishes optimal grain flow and directional properties, enhancing strength, ductility, and resistance to impact and fatigue.
Other metal fabrication methods can disrupt grain flow, exposing cut ends that may lead to fatigue and increased susceptibility to corrosion. In contrast, the forging process preserves the grain flow, aligning it with the shape and contour of the component. This continuity in grain flow enhances the fatigue and corrosion resistance of forged parts.
Engineers and designers can enhance the strength of their components by leveraging their understanding of how forging influences grain flow. This knowledge allows them to design parts that are more resistant to fatigue and failure. Forging enables the selection of optimal materials and heat treatments for each component, resulting in improved mechanical strength, resilience, and impact resistance.
The forging process enables parts to have varying thicknesses while maintaining a high strength-to-weight ratio. This capability to mass-produce parts with different thicknesses in a single operation reduces time, production costs, and manufacturing runs. Additionally, it ensures consistent material flow across each forging, regardless of the material used.
Custom forgings are created quickly and cost-effectively using a diverse array of materials and design specifications, across various sizes. Thanks to numerous innovations in forging technology, custom designs are produced with greater efficiency and affordability. Unconventional shapes and configurations are now more feasible and are crafted with enhanced precision.
The primary benefit of forging is the strength it provides for completed products. This is the result of the metal being able to retain its grain structure and alignment during the forging process. Preprocessing and pre-working of the metals removes any concerns for contaminants that could damage or harm a component‘s strength. During recrystallization, metals solidify flawlessly since potential harmful contaminants have already been removed.
A significant advantage for the auto industry is the high production rates achievable through forging. In cold forging, parts are rapidly and efficiently produced, with the entire process taking mere seconds. In hot forging, production times extend to minutes due to the heating of metals. Regardless of the component, the forging process can be seamlessly and cost-effectively integrated into existing manufacturing operations.
While some forged parts may need post-production finishing, most come out of the forging process with complete finishes and flawless surfaces. This characteristic contributes significantly to increased production efficiency.
The simplicity of the forging process results in reduced downtime and fewer defective or low-quality parts. In today’s business environment, this is crucial for meeting order deadlines and lowering production costs.
One of the most significant issues in metal production is waste, which can be both costly and damaging. A key advantage of forging is its lack of waste—any excess metal from the process can be repurposed and recycled. Unlike many manufacturing methods where managing scrap and waste incurs substantial labor and time costs, forging eliminates these expenses, allowing for a greater focus on production.
Aluminum forging is a technique for shaping aluminum alloys by applying pressure and heat to produce high-strength, durable products. This process involves methods such as pressing, pounding, and...
Cold forging is a metal shaping & manufacturing process in which bar stock is inserted into a die and squeezed into a second closed die. The process, completed is at room temperature or below the...
Copper and brass forging involves shaping these metals to create complex and intricate forms. The forging process is carefully controlled to maintain precise temperatures, ensuring...
This article covers essential terms related to open and closed die forging, which are crucial for understanding the process. Forging, a manufacturing technique, involves pressing, hammering, or...
Rolled ring forging is a metalworking process where a thick, solid, round metal piece is first punched to create a donut shape. This shape is then squeezed and pressed into a thin ring...
Forging steel is a manufacturing technique that shapes steel using localized compressive forces, such as hammering, pressing, and rolling. This method is widely employed to produce high-quality steel products...
The ancient art of forging is divided into two main categories: hot forging and cold forging. Hot forging has a long history, dating back centuries, while cold forging only emerged during the 19th-century Industrial Revolution. Despite their differences, both techniques...
Aluminum casting is a process used to create high-tolerance, high-quality parts by pouring molten aluminum into a precisely engineered die, mold, or form. This method is highly efficient for producing complex and detailed components that match the exact specifications of the original design.
Die casting is a high-pressure metal casting process where molten metal is injected into a mold. This technique yields precision metal parts that are both dimensionally accurate and have a flawlessly smooth finish.
Sand casting is a manufacturing process where liquid metal is poured into a sand mold, which has a hollow cavity shaped to the desired form, and then allowed to solidify. This method creates a final product that matches the shape of the mold.
Zinc die casting is a process in which molten zinc is injected into a steel die cavity, which is shaped to match the dimensions of the desired part or component. The result is a finished cast zinc product with...
The casting process is an ancient technique with roots stretching back several thousand years to the dawn of written history. Archaeological evidence indicates that casting was used over 6,000 years ago, around 3000 BC or BCE.