Cold Forging
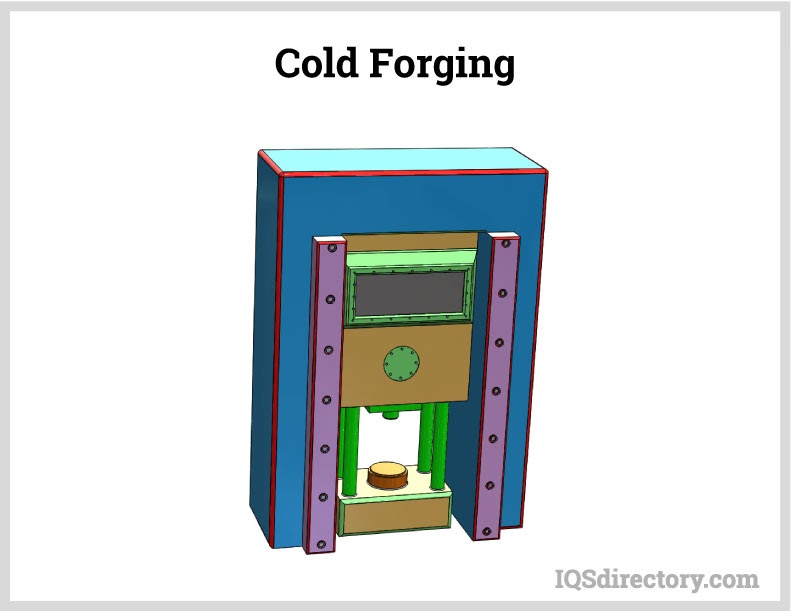
Cold forging is a metal shaping & manufacturing process in which bar stock is inserted into a die and squeezed into a second closed die. The process, completed is at room temperature or below the...
Please fill out the following form to submit a Request for Quote to any of the following companies listed on
This article contains everything you need to know about aluminum forgings, including how they are made, how they are used, and the types of aluminum alloys.
You will learn:
Aluminum forging is a method utilized to process aluminum alloys by exerting pressure and heat to manufacture robust and durable parts. This involves the pressing, pounding, or squeezing of an aluminum billet, workpiece, or cylinder under substantial pressure to create components with enhanced strength. The temperatures employed in the aluminum forging process range from just below to slightly above the recrystallization point, or sometimes even at normal room temperature.
All aluminum forging techniques are considered, including open and closed die forging and rolled ring forging. The selection of a specific forging technique is contingent on the type of product being manufactured and its intended use. Aluminum is exceptionally suitable for numerous applications because of its lightweight nature, strength, ruggedness, corrosion resistance, and forgeability.
The forgeability of aluminum alloys is compared against carbon steel and low alloy structural steel. At ambient temperature, aluminum alloys demonstrate lower deformation resistance compared to carbon steel, which possesses three defined deformation temperature intervals. Aluminum alloys are significantly responsive to temperature nuances, with deformation resistance altering with temperature fluctuations.
Although casting is a prevalent method for shaping aluminum, forging presents extra advantages by infusing deformation energy that refines and augments the alloy's metallurgy. Through forging, the internal microstructure of aluminum ingots is altered, voids and porosity are crushed, and recrystallization is triggered, enhancing the finished product's durability and toughness.
The selection of the appropriate aluminum forging process is vital for harnessing the full potential of this lightweight yet durable non-ferrous metal. Aluminum forging plays a crucial role in various industries—such as automotive, aerospace, construction, marine, and electrical—where reducing overall component mass and improving reliability directly impact performance and efficiency. Aluminum, known for its excellent strength-to-weight ratio, malleability, corrosion resistance, and conductivity, is ideally suited for forging, which is a manufacturing process that shapes and forms metal into high-strength parts using compressive forces. The fundamental concept of forging is to apply pressure—either mechanical or hydraulic—to mold aluminum alloys into precise shapes and sizes that meet demanding engineering specifications.
Forging is broadly classified into hot forging and cold forging, depending on whether the material is forged above or below its recrystallization temperature. From these two base methods, advanced aluminum forging techniques have evolved. These include drop forging, press forging, upset forging, roll forging, rolled ring forging, isothermal forging, open die forging, and closed die forging. Each method is carefully selected based on aluminum alloy grades (such as 6061, 7075, or 2024), component design complexity, mechanical property requirements, production volume, and the final application's needs. Selecting the right forging process is crucial for producing high-performance, cost-effective, and reliable aluminum components used across diverse industries.
With cold forging, aluminum alloys are shaped into intricate and complex forms without significant heat input. This method leverages the plasticity of aluminum—its ability to undergo permanent, high-precision deformation at room temperature while maintaining excellent surface finish and close dimensional tolerances. Since scaling is minimized and energy consumption is lower compared to hot forging, cold forging is an eco-friendly and economical option for high-volume production of precision aluminum parts.
Although aluminum parts can be produced via machining or cutting, these methods are slower, create substantial material waste, and require costly post-processing. Cold forging, however, achieves near-net-shape manufacturing, drastically reducing raw material waste and machining time. It accommodates highly detailed two-dimensional and three-dimensional designs, creating features such as holes, chamfers, pins, fins, steps, and even delicate geometrical patterns in a single, efficient operation. As a result, the production cycle is shorter while the quality and complexity of the output increase.
The core principle of cold forging involves placing an aluminum billet, bar, or workpiece—typically from ducal or high-plasticity alloys—between upper and lower dies and applying compressive force using mechanical or hydraulic vertical presses. The aluminum is deformed precisely to match the die cavity, providing exceptional dimensional accuracy. This advanced aluminum forming technique produces a wide range of finished products, including automotive alternators, starter motors, gears, transmission shafts, electrical connectors, anti-vibration mounts, sporting goods, motorcycle and bicycle components, and high-strength aerospace fasteners.
Key industries utilizing cold forged aluminum include automotive OEMs, electronics manufacturers, and manufacturers of lightweight, high-performance consumer products, where efficiency and repeatability are essential.
The advantages of Cold Forging Aluminum:
Hot forging aluminum leverages elevated temperatures to maximize the metal’s ductility and workability while simultaneously enhancing its mechanical properties. This process produces forged aluminum products with a strength-to-weight ratio often outperforming basic steel, while maintaining the corrosion resistance and thermal conductivity for which aluminum is renowned. Hot forging is preferred for creating parts with intricate geometries, excellent structural integrity, and tailored surface finishes, ranging from smooth polished to sharp and textured profiles. It is the go-to aluminum forming process for high-stress aerospace, motorsport, and defense applications demanding exceptional reliability and performance.
During the hot forging process, aluminum workpieces are heated to their recrystallization temperature—typically between 350°C and 500°C (662°F to 932°F). This enables the forging equipment (such as drop hammers or hydraulic presses) to apply significant pressure, molding the workpiece into the die cavity and achieving the desired final shape. The combination of heat and pressure ensures reduced grain size, improved durability, and higher yield strength. The superior grain flow and structural integrity achieved via hot forging make it ideal for safety-critical components found in aircraft, automotive suspension systems, and heavy machinery.
Careful control of die and workpiece temperature is essential during hot forging to avoid strain hardening, cracks, and other defects. Maintaining appropriate heat distribution ensures the aluminum flows seamlessly within the die, yielding parts with uniform density and minimal porosity. Because of these benefits—including enhanced fatigue strength, excellent weldability, and high thermal and electrical conductivity—manufacturers frequently select hot forging for complex or high-volume projects where lightweight, high-strength components are needed.
Drop forging is a high-speed metal shaping method in which aluminum workpieces are placed between precision die halves and compressed by repeated hammer blows. This dynamic technique is ideal for mass-producing strong and detailed aluminum components. In drop forging, the upper die is attached to a power-driven hammer, while the lower die rests on a stationary anvil. The heated aluminum—often from high-performance 6000 or 7000 series alloys—is struck until it flows and fills the entire die cavity. Any excess aluminum, known as "flash," is squeezed out along the parting lines and subsequently trimmed for material recovery and recyclability, further supporting environmentally sustainable manufacturing.
This method delivers products with superior mechanical strength, excellent toughness, and outstanding fatigue resistance by aligning the metal’s grain structure with the part’s geometry. Drop forging produces components with precise dimensional accuracy and consistency, making it an optimal solution for high-volume production of tools, automotive chassis components, precision sprockets, hardware, heavy-duty levers, and structural brackets. The resulting aluminum forging shows optimal resistance to wear and impacts, with minimal production waste and the flexibility to create complex, close-tolerance designs.
Rolled ring forging is a specialized aluminum forging process used to create seamless, high-integrity rings from billets or cylinders. Initially, the billet is upset to increase its diameter while reducing its height, after which it is pierced to form a donut-shaped blank. This blank is then placed on a mandrel and shaped further by rollers, expanding its diameter and refining its wall thickness, all while preserving the continuous, defect-free grain flow that forged rings need for demanding service conditions.
This open die process operates at temperatures above the aluminum's recrystallization point, improving ductility and overall grain structure. The mandrel and rollers work in concert to achieve the required inside and outside diameters, wall thickness, and surface finish—all key factors for the part's final mechanical properties. Forged aluminum rings offer significant advantages over cast or welded rings, including improved tensile strength, shock resistance, impact performance, and long-term durability.
Forged rolled rings are widely used in the aerospace, wind energy, automotive, power transmission, and heavy machinery sectors due to their reliability and safety under extreme mechanical and thermal loads. Typical applications include jet engine turbine rings, helicopter gearbox rings, windmill components, pressure vessel end rings, and specialty equipment for hazardous or mission-critical environments.
Open die forging shapes aluminum by working billets or ingots between simple, flat, or contoured dies that do not fully enclose the workpiece. This forging technique is well-suited for producing large, custom aluminum components—such as discs, rings, cylinders, and shafts—with relatively simple geometries and excellent mechanical properties. The repeated impacts and plastic deformation involved in open die forging realign and refine the grain structure, significantly enhancing the toughness, fatigue resistance, and structural integrity of forged aluminum parts. The flexibility of open die forging allows the production of both small and massive custom components, with individual workpieces weighing from several pounds to several tons.
Open die forging is also an optimal solution for short production runs, prototyping, or crafting one-off specialty components for heavy equipment, construction machinery, energy systems, and aerospace. This method lends itself well to applications where superior metallurgical quality, low void content, and resistance to fracture under heavy loads are essential. The open die process may also serve as a pre-forming step, preparing aluminum ingots for subsequent closed die forging, extrusion, or machining to finer tolerances.
Forged products produced through open die forging exhibit improved machinability, outstanding wear properties, and performance that rivals or exceeds both cast and machined products in terms of density and reliability. The process also helps eliminate porosity, inclusions, and internal defects that can compromise safety and function in mission-critical parts.
The process for closed die forging (also known as impression-die forging) utilizes specially machined dies that fully enclose the aluminum billet or blank during deformation. When the upper and lower dies come together, they shape the aluminum to obtain detail-rich profiles and strict dimensional accuracy. Closed die forging can be performed in either a single or multiple stages, depending on the part’s complexity and design requirements. This method works especially well with high-strength heat-treated aluminum alloys—such as 6061, 7075, and 2024—which are widely used in aerospace and performance automotive sectors where precision, safety, and consistency are paramount.
During the closed die forging process, skilled operators or automated forging lines control the force and motion of the dies to achieve grain flow alignment with anticipated service loads. This refining of the billet’s microstructure enhances strength, fatigue resistance, and shock tolerance. Once stamped, the product may only require minimal secondary machining or finishing, minimizing production time and cost.
This forging process is ideal for high-volume production runs because once the dies are manufactured, each part produced features near-identical quality, tightest possible tolerances, and excellent surface finish—significantly decreasing material waste and post-processing costs. Closed die forging can efficiently create parts including connecting rods, precision gears, linkages, suspension parts, brackets, and safety-critical aerospace components.
In summary, closed die forging boosts the cost-effectiveness, consistency, and mechanical properties of common and specialty aluminum products. Eliminating voids and porosity, the process ensures engineered aluminum parts meet the high-impact, lightweight, and fatigue-resistant requirements of modern industries.
When it comes to aluminum forging, choosing the right aluminum alloy is crucial to achieving the required balance of strength, weight, corrosion resistance, and cost. Aluminum’s unique combination of a lightweight profile, high tensile strength, and excellent resistance to environmental deterioration makes it a major material in industries such as automotive manufacturing, aerospace, transportation, and structural engineering. However, not all types of aluminum are suitable for the forging process—a method by which aluminum is heated and shaped by compressive force to increase its mechanical properties and grain structure integrity.
The most widely used alloys for aluminum forging applications are the 6000 series (such as 6061, 6063, and 6082) and the 7000 series (such as 7075), each offering unique physical, chemical, and mechanical properties tailored for specific forged components. Understanding which aluminum alloys meet project requirements is vital for engineers, manufacturers, and procurement professionals when sourcing high-performance forged parts.
Selecting the optimal aluminum alloy involves evaluating several key selection criteria to meet the performance targets of a particular forged product. Below are six crucial factors to consider during the aluminum alloy selection for forging:
As with other metal forging processes, a broad range of aluminum alloys is available to meet diverse project specifications and industry standards. With over 170 years since aluminum’s discovery and a rich history of alloy engineering, both primary and recycled aluminum find application in millions of tons of forged aluminum components across global industries. Recognizing the subtle differences between alloying elements—such as magnesium, silicon, zinc, copper, or manganese—enables end-users to achieve the required blend of formability, durability, and structural performance.
Forged aluminum is renowned for its superior grain structure and mechanical properties compared to cast or extruded aluminum. The forging process refines the internal structure of the metal, enhancing fatigue strength and providing increased reliability for mission-critical applications. Industries often turn to custom aluminum forging when seeking solutions that require enhanced strength, precision tolerances, and robust resistance to failure, such as automotive suspension components, aerospace fittings, defense hardware, hydraulic manifolds, and high-stress machinery parts. The optimal alloy for forging is influenced by the intended environment—such as exposure to saltwater, high temperatures, repeated stress cycles, or the need for electrical conductivity—and the specific forging techniques involved, like open-die, closed-die, or precision forging.
Aluminum Alloy 6061 is a member of the 6000 series, with magnesium and silicon as its major alloying elements (confirmed by its “6” designation). Its composition—98% aluminum, 1% magnesium, 0.6% silicon, 0.28% copper, and 0.2% chromium—provides a unique combination of high strength, corrosion resistance, and excellent workability. The flexibility of 6061 makes it one of the most widely used alloys for industrial aluminum forgings, aircraft parts, marine fittings, automotive frames, and structural components.
Known for outstanding weldability, machinability, and versatile temper designations—including 6061-O (annealed), 6061-T4 (solution heat treated), and 6061-T6 (solution heat treated and artificially aged)—this alloy is easy to form, machine, and finish. Specifications for 6061-T6 forged aluminum highlight its higher yield strength, making it the go-to material for projects where rigidity and strength-to-weight ratio are priorities.
Aluminum alloy 6063 is a medium-strength, highly formable 6000 series alloy tailored for intricate architectural shapes. It excels at extrudability and surface finish due to its composition—primarily magnesium and silicon—which facilitates the formation of complex geometries and seamless cross-sections in forged architectural aluminum components such as window frames, door frames, trim, decorative hardware, and structural tubes.
Available in T4 and T6 tempers, 6063 delivers an excellent blend of lightweight strength and corrosion resistance. Its low copper content boosts its ability to withstand hostile weather and industrial environments, making it a superior option for outdoor structures, building façades, and transportation systems. 6063 forged aluminum is also preferred for projects requiring weldable and anodizable alloys, as it supports a broad range of colored, durable anodized finishes.
Recognized as “architectural aluminum,” 6063 is not only ideal for appearance-driven applications but also for structural uses in challenging climates, supporting both functionality and design flexibility.
Aluminum alloy 6082 stands out for its superior structural strength—the highest among 6000 series forged alloys. Its elevated manganese content (0.4% to 1%) enhances grain structure, resulting in strong resistance to mechanical stress, wear, and deformation during hefty construction or load-bearing applications. This increased strength does not compromise its machinability, making 6082 a favorite among engineers for fabricating precise, durable components.
Although its anodizing response is weaker (limiting its use in exposed or decorative structures), 6082 is the alloy of choice for industrial construction, heavy-duty scaffolding, bridges, cranes, transportation vehicles, and general engineering forgings. The alloy is also seen in high-strength marine and railway parts. With temper designations such as O (annealed), T4, and T6, 6082 balances weldability, corrosion resistance, and thermal conductivity, paving the way for innovative applications in modern infrastructure. Its hot forging suitability and dimensional stability make it reliable for producing both large billets and precision components in automotive and aerospace sectors.
Aluminum Alloy 7075 is the hallmark of high-performance forging, renowned for delivering the highest strength-to-weight ratio of any aluminum alloy. The significant addition of zinc, copper, and magnesium (unlike 6000 series) grants the material exceptional mechanical properties, offering tensile strength up to 83,000 psi. 7075 aluminum forgings are extensively used in aerospace, defense, competitive sports equipment, and performance automotive components, where maximum static and dynamic strength, as well as stress corrosion resistance, are critical.
Temper variants such as T6, T651, T7351, and T76 provide tiered improvements in stress corrosion resistance, fatigue life, and toughness. While the T6 temper delivers ultimate strength, the T73 grade prioritizes better environmental resistance—ideal for airframes, missile parts, and high-stress tooling. Forged 7075 aluminum is not suited for cryogenic applications due to lower toughness at extremely low temperatures, but its superior performance in normal and elevated temperatures has driven widespread adoption in defense (firearms, rifle receivers), transportation (bicycle and vehicle frames, wheel spacers), and extreme sports (rock-climbing gear, skate frames, lacrosse shafts, hang gliders).
While 6061, 6063, 6082, and 7075 are among the most frequently specified alloys for aluminum forging, a comprehensive range of options exists, including specialty and aerospace grades such as 2014, 2017, and 2618, each optimized for different performance criteria. Choosing the right aluminum alloy improves forged product longevity, safety, and lifecycle cost, reinforcing why material knowledge is central to successful project outcomes. Additional factors, including thickness, formability, temperature exposure, and finishing requirements such as anodizing or coating, also influence alloy decisions for aluminum forged parts in demanding industries.
Types and Mechanical Properties of Forgeable Aluminum Alloys Key - ◎ Excellent - 🞅 Good - △ Fair - 🞩 Poor |
|||||||
---|---|---|---|---|---|---|---|
Desired Properties | Material | Si Content (MASS%) | Mechanical Properties | Forgeability | |||
Former Sumitomo Designation | Temper | Tensile Strength (N/mm)² | Proof Stress (N/mm)² | Elongation (%) | |||
High Strength | 6061 | T6 | 315 | 275 | 19 | ◎ | |
SG210 | T6 | 400 | 360 | 18 | ◎ | ||
GS310 | T6 | 390 | 345 | 18 | ◎ | ||
2011 | T8 | 410 | 315 | 15 | ◎ | ||
2014 | T6 | 480 | 275 | 22 | ◎ | ||
2017 | T4 | 440 | 275 | 22 | ◎ | ||
Abrasion Resistance | 4032 | T6 | 12 | 380 | 315 | 9 | 🞅 |
SC100 | T6 | 10 | 440 | 390 | 8 | 🞅 | |
SC300 | T6 | 10 | 480 | 420 | 8 | 🞅 | |
SC150 | T6 | 15 | 420 | 390 | 2 | △ | |
High-Temperature Strength | 2618 | T6 | 440 | 370 | 10 | ◎ | |
CG29 | T6 | 520 | 400 | 14 | ◎ |
For more on specific grades, suppliers, custom forging services, or to request technical guidance on alloy selection, consult a trusted aluminum forging manufacturer or contact a specialist for expert consultation on sourcing custom forged aluminum parts tailored to your industry's application.
Forging is an ancient metalworking technique that has been utilized for centuries to create items ranging from weapons and cutlery to cookware, jewelry, and structural supports. Originally, the process involved hammering metal on an anvil with heat to shape it. While modern forging methods have become technologically advanced, they still incorporate some of the fundamental techniques used by early metalworkers.
A key advantage of using aluminum for manufacturing components is its smooth, even, and attractive finish, similar to polished silver. While the forging process often yields products with this desirable finish, it can also produce surfaces with sharp serrations and jagged peaks. These variations may necessitate additional finishing or be integral to the product’s intended function and use.
The outcome of aluminum forging is heavily influenced by the design and configuration of the die used in production. Aluminum design engineers take client specifications to create dies with precise dimensions and configurations for forging the desired products. The main constraint of the process is the manufacturability of the design. Computer-aided design (CAD) technology allows for pretesting of designs before actual production begins, ensuring feasibility and precision.
Aluminum forging creates components, parts, products, and instruments that exhibit superior strength compared to those produced through casting and machining. The forging process aligns the grain structure of the component with its shape, thereby enhancing its strength and durability. Forged aluminum is particularly well-suited for applications that demand high resistance to repetitive loading, frequent impact, and harsh conditions, thanks to its exceptional impact resistance and strength.
Aluminum forging is typically less expensive compared to other manufacturing processes when factors like material cost and lead times are equal. The tooling required for aluminum forging is generally more affordable than that for aluminum die casting, and the process yields a higher production rate.
Forging enhances the mechanical properties of aluminum alloys by altering their microstructure. This results in increased tensile strength, yield strength, toughness, and fatigue resistance.
Unlike other aluminum forming methods that may produce products with porosity and voids, aluminum forging utilizes compressive forces to eliminate these imperfections. This results in increased durability, performance, and reliability of the final products.
Aluminum forging avoids issues with shrinkage by heating the metal to just below or above its recrystallization point. The billet or workpiece is processed in its solid form, ensuring precise dimensional accuracy and integrity.
One of the key advantages of aluminum forging is the retention of aluminum's exceptional properties. Despite the shaping and manipulation involved, the forging process does not compromise any of aluminum’s beneficial characteristics.
Modern manufacturing emphasizes reducing waste, and aluminum forging supports this goal. The flash produced from open and closed die forging can be easily reused and recycled, minimizing waste. Aluminum is highly recyclable and can be processed repeatedly without loss of quality.
Aluminum forging excels in high-volume production, efficiently creating thousands of complex and intricate shapes in a short period. The timeline from design introduction to finished product delivery can be as brief as two months or less, with minimal waste generated despite large production quantities.
Cold forging is a metal shaping & manufacturing process in which bar stock is inserted into a die and squeezed into a second closed die. The process, completed is at room temperature or below the...
Copper and brass forging is the deformation of copper and brass for the purpose of manufacturing complex and intricate shapes. The temperature at which copper and brass are forged is precision controlled and...
Forging is a metal working process that manipulates, shapes, deforms, and compresses metal to achieve a desired form, configuration, or appearance outlined by a metal processing design or diagram...
In this article, there are key terms that are typically used with open and closed die forging and it is necessary to understand their meaning. Forging is a process in manufacturing that involves pressing, hammering, or...
Rolled ring forging is a metal working process that involves punching a hole in a thick, solid, round metal piece to create a donut shape and then squeezing and pressuring the donut shape into a thin ring...
Forging steel is a manufacturing process used to shape steel by using localized compressive forces, which include hammering, pressing, and rolling. It is a widely used method for producing high quality steel products...
The ancient art of forging falls into two distinct categories – hot and cold where hot forging has been around for centuries while cold did not begin until the industrial revolution of the 19th Century. Though they are quite different ...
Aluminum casting is a method for producing high tolerance and high quality parts by inserting molten aluminum into a precisely designed and precision engineered die, mold, or form. It is an efficient process for the production of complex, intricate, detailed parts that exactly match the specifications of the original design...
Die casting is a high pressure metal casting process that forces molten metal into a mold. It produces dimensionally accurate precision metal parts that have a flawless smooth finish...
Sand casting is a manufacturing process in which liquid metal is poured into a sand mold, which contains a hollow cavity of the desired shape and then allowed to solidify. Casting is a manufacturing process in which...
Zinc die casting is a casting process where molten zinc is injected into a die cavity made of steel that has the shape, size, and dimensions of the part or component being produced. The finished cast zinc product has...
The casting process is an ancient art that goes back several thousand years to the beginning of written history. The archeological record has finds that document the use of the casting process over 6000 years ago around 3000 BC or BCE...