Aluminum Forging
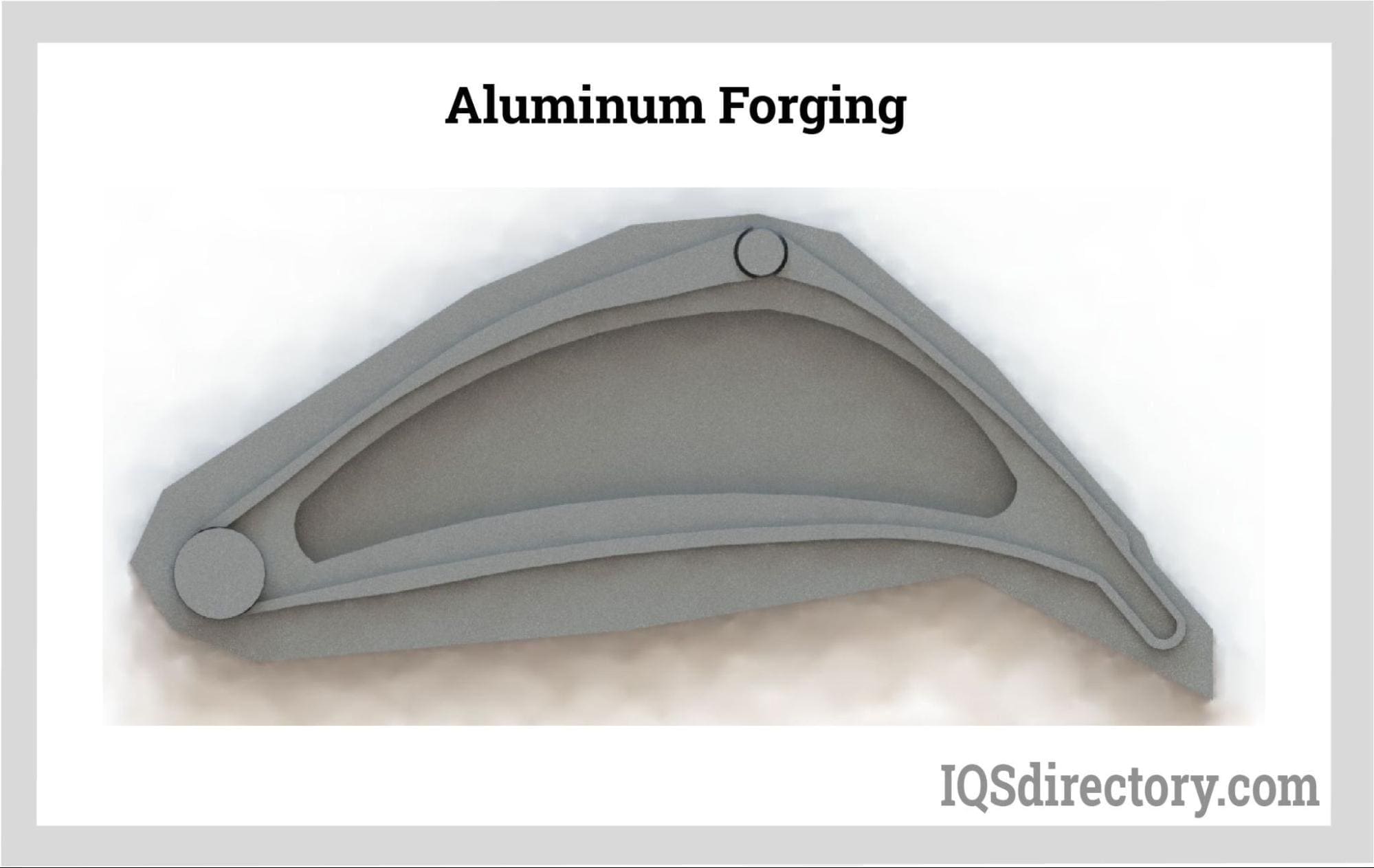
Aluminum forging is a method for processing aluminum alloys using pressure and heat to form high strength, durable products. The process of aluminum forging involves pressing, pounding, and...
Please fill out the following form to submit a Request for Quote to any of the following companies listed on
This article takes an in depth look at cold forging.
Cold forging is a metal forming process in which bar stock is inserted into a die and compressed into another enclosed die at ambient temperatures or below the metal's austenite threshold.
This method is remarkably efficient and cost-effective for mass production of components. Cold forging can be classified into procedures like cold, warm, and hot forging, employing tools such as hammers, dies, or presses to shape and deform metal. It differs significantly from machining and casting by producing stronger and higher quality products.
Unlike warm or hot forging, cold forging shapes metal at room temperature by applying localized compressive forces. To achieve the desired outcome, the metal may be subjected to multiple dies or repeated strikes, depending on the part's design complexity.
Cold forging, a crucial manufacturing method in the metal forming industry, offers substantial cost savings and efficiency improvements for mass production of metal parts. This innovative process dramatically reduces labor needs and eliminates many secondary machining steps, minimizing waste and streamlining the production workflow. Advanced cold forging techniques enable manufacturers to produce components at high speeds—often exceeding 1,000 units per hour—which significantly lowers the cost per piece for OEMs and suppliers. By leveraging sophisticated cold heading and press technology, metal coils are automatically fed into high-precision cold forging machines, resulting in efficient throughput and superior quality assurance.
The end products manufactured using cold forging technology demonstrate outstanding surface finish and enhanced dimensional accuracy, as clearly illustrated in the image below. With optimized grain structure and minimal material loss, parts produced through cold forging exhibit superior mechanical properties—including increased tensile strength, wear resistance, and longevity—making them ideal for critical automotive, aerospace, electronics, and construction applications. The range of available cold forging processes enables production of durable, corrosion-resistant, and reliable fasteners, shafts, gears, and complex custom components, meeting diverse user requirements and industry standards.
Before the cold forming process initiates, the workpiece—often a steel or aluminum billet or wire—is typically coated with an anti-sticking lubricant. This step is essential for two main reasons: it prevents galling and adhesion between the metal and die, and it reduces tool wear during high-pressure deformation. Lubricants also facilitate smoother material flow and help to control frictional heat generated during the process, which can reach temperatures between 250°C to 450°C—though still below the recrystallization point of most ferrous and non-ferrous metals. The type and application of forging lubricants vary by manufacturer, with some using advanced phosphate or polymer coatings tailored for specific alloys or manufacturing requirements. While lubrication is a standard best practice, certain high-speed automated cold forging lines may utilize alternative die coatings or surface treatments to maximize throughput and tool life.
Next, the chosen metal coil or rod—often cold-drawn steel, copper, brass, or alloyed aluminum—is introduced into the forging machine, precisely positioned over a specially machined die cavity designed to form the intended part geometry. Most cold forging dies consist of two or more segments: a stationary die beneath the workpiece and a movable upper die attached to a hammer or press ram. This configuration enables precise control over part dimensions, surface texture, and internal structure. Automated coil feeding systems ensure consistent material supply and alignment, optimizing production consistency and minimizing setup time—a key consideration for customers seeking rapid turnarounds and high repeatability in custom component manufacturing.
The heart of the cold forging process is the controlled application of high compressive force through mechanical, hydraulic, or pneumatic means. State-of-the-art cold forging presses use a shaft or slide mechanism equipped with a precision hammer, which descends with immense power onto the workpiece—typically within a few milliseconds. This rapid deformation technique creates dense, uniform material structures while maintaining tight tolerances and repeatable dimensions. Some part geometries may require multiple progressive strokes or sequential dies (multi-stage cold forming) to achieve complex shapes, threaded features, or unique profiles without excess flash or unnecessary machining. The choice of stroke mechanism directly affects productivity, energy consumption, and finished part quality—relevant factors for manufacturers comparing cold forging vs. hot forging or CNC machining alternatives.
Once the metal component is fully formed, efficient part removal becomes critical for maintaining workflow and avoiding production bottlenecks. In modern high-volume cold forging facilities, automated systems—such as conveyors, pick-and-place robots, or pneumatic ejectors—remove finished parts from the die without manual intervention, reducing costs, minimizing human error, and enabling seamless integration with downstream quality inspection or packaging lines. Automation ensures repeatability and traceability, key metrics for industries requiring strict adherence to ISO 9001 or IATF 16949 quality standards.
Handling and post-processing requirements depend on part complexity and final specifications. Simple cold-forged parts—such as nuts, bolts, or washers—may be trimmed to remove minor excess material (flash) and sent directly to finishing or shipping. For more intricate components, additional die operations, secondary forming, precision punching, or rolling may be required to achieve tight tolerances, special grooves, threads, or other engineered features. Automated die transfer systems allow components to move swiftly between processing stations, maximizing output and reducing lead times. For large or heavy forgings, material handling equipment such as forklifts, hi-los, or overhead cranes transport components to their next destination. Throughout these processes, producers often perform real-time inspection and measurement, utilizing statistical process control (SPC) and non-destructive testing (NDT) to assure zero-defect quality essential for mission-critical industries.
When evaluating cold forging services, buyers should consider the manufacturer’s technological capabilities, equipment range (such as multi-station presses and progressive die systems), material expertise, available secondary operations (like heat treating, plating, or coatings), and compliance with industry standards. Comparing cold forging with alternative processes—such as hot forging, CNC machining, or metal stamping—helps clients select the best solution for their application, balancing factors like cost, part performance, production speed, and customization flexibility. Requesting samples, reviewing case studies, and visiting supplier facilities further ensures informed purchasing decisions and optimal supply chain reliability.
This chapter explores six key benefits of cold forging, a highly efficient and innovative metal forming process used extensively in manufacturing industries such as automotive, aerospace, electronics, and construction. Cold forging offers numerous advantages over traditional hot forging and machining methods, positioning it as a preferred choice for high-volume, precision-driven production.
Below, you’ll find in-depth details on why cold forging is valued in modern manufacturing, comparisons with other metal forming processes, and how its specific benefits can translate to cost savings, higher quality, and sustainable production. Whether you are evaluating cold forging versus hot forging or considering the best technique for custom components, this section will help clarify how cold forging fulfills various user intents in sourcing or purchasing precision metal parts.
Cold forging is exceptionally cost efficient due to its elimination of high-temperature heating equipment, intricate tooling, and expensive extra finishing operations. By working metals at or near room temperature, the process saves substantial energy costs typically incurred by furnaces, induction heaters, or kilns required in hot forging. In fact, cold forging delivers up to a 70% reduction in raw material waste compared to machining techniques, supporting lean manufacturing principles and material yield optimization.
Unlike many subtractive metalworking processes, cold forging uses near-net-shape forming, resulting in minimal scrap and achieving tight tolerances in the finished part immediately after processing. Only minor post-processing or deburring may be necessary, driving significant labor cost savings. As a result, cold forging provides excellent value for industries seeking volume production of bolts, fasteners, shafts, and custom precision components.
Cold forging technology enables rapid, continuous production due to its streamlined workflow where raw material blanks are inserted directly into the automated forging press. Modern machinery and robotics have made it possible to fully automate feeding, forming, and ejection of finished parts, thereby reducing downtime, operator involvement, and cycle times.
High-speed cold forging equipment can produce complex components within fractions of a second, dramatically increasing throughput for automotive, electronics, and consumer goods manufacturing. This efficiency makes cold forging an optimal solution for businesses requiring just-in-time (JIT) inventory, reliable supply chain fulfillment, and scalable mass production.
Traditional metalworking methods can introduce material defects such as porosity, fatigue, and grain boundary weaknesses due to thermal cycling or inconsistencies in heating. Cold forging addresses these issues by processing metals at ambient temperatures, greatly reducing the risk of unwanted metallurgical reactions. The result is a forged component with a dense, uniform grain structure that enhances both strength and fatigue resistance.
While cold forging improves many mechanical properties and minimizes risks like micro-cracking, it is essential to note that the process may pose its own challenges, such as increased die wear for very hard materials or limitations for highly complex part geometries. Nonetheless, the process is widely adopted for critical safety components and high-tolerance parts due to its material integrity.
Cold forged parts are known for their superior mechanical properties, such as higher tensile strength, improved fatigue resistance, and enhanced dimensional stability. The forging process strengthens the metal’s grain flow, resulting in parts that can endure high stress, heavy loads, and repeated cycling—even under extreme conditions. Unlike machined parts that may exhibit weak points at cut surfaces, cold forged products exhibit continuous, uninterrupted grain structure for maximum reliability and longevity.
Cold forging delivers consistent, repeatable, and tight tolerances throughout an entire production run, assuming proper die maintenance. This high degree of dimensional accuracy is critical for industries such as automotive, aerospace, and electronics that demand uniformity across large production batches. Every forged component emerges nearly identical to the prototype, making the process ideal for mass-producing precision fasteners, connectors, pins, and bearing components.
Cold forging offers exceptional design flexibility for manufacturers and engineers. Advanced die technology enables the creation of intricate shapes, complex geometries, and customized contours—all in a single forming operation. This comparative design freedom reduces the need for costly secondary machining, drilling, or finishing steps, streamlining the manufacturing process and supporting faster product development cycles.
More manufacturers are choosing cold forging for innovative applications, leveraging its capacity to produce parts with features such as undercuts, flanges, and threads, which may be challenging or impractical with other metalworking methods.
Cold forging enables manufacturers to achieve high production rates, often exceeding 50 pieces per minute and, with optimized automation, up to 400-450 pieces per hour. The actual output may be influenced by factors such as part complexity, material hardness, and die design. This high throughput makes cold forging a strategic choice for OEMs, fastener manufacturers, and suppliers seeking scalable solutions and rapid fulfillment of bulk orders.
Cold forging is compatible with a broad spectrum of metals, allowing manufacturers to tailor parts for specific mechanical properties, corrosion resistance, and performance. Commonly cold forged metals include carbon steel, alloy steel, and stainless steel for high-strength industrial applications, as well as softer metals like aluminum, brass, and copper for electrical and decorative uses. Material selection is based on required specifications, end-use applications, and cost considerations, making cold forging extremely versatile.
This image showcases a diverse array of cold forged bolts made from copper, brass, aluminum, and steel. Each material is chosen to match application-specific needs such as tensile strength, electrical conductivity, or corrosion resistance. By offering broad material compatibility, cold forging is an optimal process for industries seeking durable, reliable components with tailored physical and mechanical properties.
In summary, cold forging stands out for its cost efficiency, speed, environmental benefits, and capacity to deliver consistently high-quality metal parts for diverse manufacturing requirements. Whether comparing cold forging vs. hot forging or evaluating the best production method for your application, understanding these benefits is essential for making informed sourcing and purchasing decisions.
The primary distinction between hot forging and cold forging lies in temperature: cold forging deforms metals at room temperature, creating strain and stress, whereas hot forging involves heating the metals before shaping them.
The critical factor in the temperature range is the austenite stage. Cold forging occurs below this stage, while hot forging involves heating the metal to temperatures beyond the austenite phase.
Hot forging is conducted at very high temperatures, which helps prevent strain and hardening while reducing the stress flow and energy required to shape and deform metals. After cooling, the metals retain their new shape. The forming process typically involves hydraulic, pneumatic, or mechanical presses.
One of the significant costs associated with hot forging is the production of dies and molds. These are made from high-strength steel designed to endure the extreme temperatures, resist fatigue, and possess the necessary ductility, toughness, and tensile strength.
While many hot forging techniques are similar to those used in cold forging, additional methods include gas forming, die quenching, draw forming, and isothermal forging.
The process type determines the metal's temperature during shaping. In certain methods, the metal is fully melted and either poured into a mold or forced through a die. In other processes, the metal is annealed and then shaped under compression and pressure using a die or mold.
The primary drawback of the heating process in forging is the significant amount of pollutants generated, which varies depending on the type of furnace used. This issue has been a persistent challenge since the early days of the industrial revolution and continues to be a concern for manufacturers. The video below illustrates the volume of fumes produced.
To forge parts, metals must be heated beyond the austenite stage, which typically requires temperatures above 300°F and can reach into the thousands of degrees. Achieving these temperatures necessitates the use of large furnaces or kilns.
Hot forging involves a complex process that includes heating the metal, shaping it, and then cooling it. While the actual stamping, deforming, or shaping may take about the same time as cold forging, the heating and cooling phases require careful management and can extend the overall process duration.
Heating and cooling metals enhance their strength, toughness, and ductility, though they can reduce hardness. During cooling, metals may warp or change shape, and these potential issues should be considered during the engineering phase.
Hot forging can result in oxidation, leading to scaling that discolors the metal's surface and complicates finishing processes.
The key difference between cold forging and hot forging lies in the temperature used. Hot forging involves heating the metal above its austenite stage, which alters its microstructure and eliminates internal stress, making it more ductile. In contrast, cold forging does not involve heating, allowing the metal to maintain its original strength and microstructure.
The characteristics of cold forgings are as follows:
In cold forging, metals are shaped at room temperature, below their austenite stage. This approach reduces costs by eliminating the need for expensive furnaces and heating equipment.
Production speeds vary from seven pieces per minute for low-volume machines to up to 400 pieces per minute for high-volume systems.
Cold forging utilizes specialized machines that perform operations such as squeezing, bending, shearing, and drawing. The cost of this equipment varies widely based on its technology and size.
Cost savings in cold forging are primarily due to material efficiency and production speed. Material savings arise from minimal scrap production, with reductions of up to 70%. Additionally, the rapid production rate significantly lowers the cost per unit.
This machine from Stalcop, shown below, operates with no emissions or pollutants. It is fully enclosed and self-contained, eliminating carbon and other pollutants since heating of the metal is not required.
The diagram below illustrates how cold forging realigns the grain structure of metals to match the flow of the final part. This process reduces porosity fatigue, enhances shearing strength, and minimizes risks to material integrity. While the metal becomes stronger and more resilient through straining, it also loses ductility and becomes more brittle.
Before forging, it is crucial to remove any scaling, such as rust or corrosion, that may have developed during storage. Failure to do so can result in the part exhibiting similar deterioration issues as seen in hot forging.
Minimal finishing is needed with cold forging. Once a part is processed, it is ready for use or shipping with little to no additional work required.
Cold forging is not without its drawbacks. As with any production method, it has its own limitations and constraints that should be considered before selecting it for your next project.
Technological advancements and progress in metal processing have led to the creation of various cold metal shaping and forming techniques. While each method caters to specific needs, they are all optimized for efficient and rapid production, often eliminating the need for additional finishing steps.
The eight most widely used cold forging methods include:
While the following descriptions offer a foundational understanding of the various cold forging methods, it's important to note that other processes exist, which will be covered later in this chapter.
Another crucial factor in cold forging is the type of lubricant used. Common choices include zinc phosphate or various polymer coatings. Despite being performed at room temperature, the bending and shaping actions can raise the metal's temperature. The right lubricant helps prevent errors, reduces the likelihood of the workpiece sticking to the die, and extends the lifespan of the tools.
Lubricant manufacturers offer a variety of products to fit each type of cold forging process. Pictured are graphite lubricants, but graphite free types are available as well as calcium aluminate, aluminum fluoride, and phosphate coatings.
Bending involves using a press and die to force the workpiece against a shaping tool, a process also known as pyramid rolling. This method is sometimes employed to prepare a piece for subsequent cold forging processes. The workpiece is deformed along a single axis to achieve the desired angle.
Rolling is a forming process where metal is passed through a pair of rotating rollers for plastic deformation caused by compressive force. The compressive stresses produce friction between the rolls and the metal stock‘s surface. It is commonly used for the processing of steel.
In closed die forging, the workpiece is shaped by successive mechanical blows after it has been placed between two die halves. Since the hammer strikes the workpiece multiple times, some producers refer to closed die forging as drop forging. As the metal is struck, it flows into the cavities of the die changing it to the shape of the die.
Drawing involves pulling the workpiece through a die using tensile force applied at the die's exit. This process reduces the cross-sectional area of the workpiece while increasing its length. The resulting metal components achieve tighter dimensional tolerances compared to those produced by rolling.
In cold extrusion, a billet or slug is pushed through a die under compressive force that shapes it into the profile of the final part. After extrusion, the piece is cut to the desired length and either prepared for shipment or sent for additional processing. The compressive force in cold extrusion can reach up to 20,000 kN (approximately 2007 tons), and the process can be performed in forward, backward, or both directions.
Forward extrusion involves pushing the metal forward through the die.
Backward extrusion involves pushing the metal into the die in reverse, creating holes or cups with a thicker bottom compared to the sides.
Lateral extrusion applies force sideways, perpendicular to the extrusion direction, to add a secondary feature to the profile.
Open die forging uses two flat dies that lack a pre-cut profile. The workpiece is progressively shaped through multiple processes, allowing for a wide variety of shapes and sizes. This method is commonly used for large metal components that demand high structural integrity. Deformation is achieved by repositioning the workpiece throughout the process.
Squeezing, or sizing, is a specific type of open die forging where force is applied over a short distance to achieve precise dimensional finishes.
Ring forging involves creating a circular workpiece with a central hole, resembling a donut shape. As the pierced piece is rotated, it is hammered and compressed. This process results in seamless rings with precise diameters and excellent strength.
Swaging, also known as radial forging, involves deforming a workpiece to ensure that two parts fit together precisely. It is an automated and highly reliable process. There are two main types of swaging: tube swaging and radial swaging. Tube swaging resembles extrusion, where the workpiece is pushed through a die. Radial swaging, on the other hand, uses a hammer to press the workpiece through two or more dies.
When searching for a cold forging manufacturer, you'll encounter more methods than the seven discussed here. Understanding these basic methods will enable you to engage knowledgeably with producers and interpret industry terminology effectively.
As with any advanced production technique, cold forging continues to evolve with the development of new methods and technologies. Automation and robotics are increasingly significant factors, transforming the industry rapidly. Consulting a forging specialist can help you identify the process that best meets your requirements.
Cold forging equipment is available in three main types: hydraulic, pneumatic, and mechanical. While some suppliers focus on just one variety, most offer a range of options based on price and operational needs. Modern machines often incorporate technology and automation, as illustrated by the servo cold forging press from Marvel Machinery shown below. Part designs are typically created using engineering software like CAD.
The hydraulic die forging hammer is engineered to deliver maximum force with minimal investment. It can create a diverse range of impressions using various dies. This hammer operates on hydraulic principles, where an incompressible liquid is housed in a cylinder. When the liquid is compressed by a piston, it drives a shaft with the die attached downward onto the workpiece.
The screw press is suited for large deformations due to its slow pressing speed. It is effective for flashless dies and long rod forgings. Its design accommodates single-slot dies for bending and final forging operations. An electric motor drives the screw, which presses the die onto the workpiece.
The C-frame design is ideal for forming, punching, bending, and multi-pressing applications. Available in single or double crank configurations, these presses offer punch forces ranging from 110 to 400 tons and slide strokes between 110 and 280 mm. They can accommodate die heights from 435 to 600 mm and are suitable for producing small parts.
The pneumatic-powered press is capable of handling all die pressing functions. It features a pneumatically operated friction clutch and brake. The press's power is generated by an air compressor, which uses air pressure in a cylinder with a piston to drive the forging hammer onto the workpiece.
Among the various cold forging machines, mechanical presses are becoming less common due to their need for substantial size to generate the required force. They use a flywheel to store energy from a motor. When activated, the flywheel drives the hammer or ram onto the die. Although it can deliver power over multiple rotations, the press must pause to allow the motor to recharge the flywheel before resuming its cycles.
Among the various types of cold forging equipment, hydraulic and pneumatic presses are the most prevalent due to their compact size, adjustable force capabilities, and programmability. When evaluating production options, it's important to consider the types of equipment available from a producer, as modern and well-maintained equipment is more likely to yield higher-quality parts.
Numerous machines are available for cold forging, and they play a crucial role in modern industry. Cold forging allows for the cost-effective and efficient production of high-strength metal components used in sectors such as automotive, hand tools, and military hardware. Below, we highlight some prominent brands of cold forging machines used in the United States and Canada:
Hatebur's HF-series machines are renowned for their high-speed precision forging, advanced automation, and multi-station design. These features enable the efficient production of complex metal components with exceptional accuracy.
Sakamura USA provides SACMA Cold Formers, known for their versatility, precision, and high productivity in cold forging. These machines offer precise control over forging parameters and can produce a diverse range of components efficiently.
National Machinery's FORMAX Plus machines are distinguished by their advanced servo-driven technology, rapid tool change capabilities, and energy-efficient operation. These features enhance precision and productivity in cold forging applications, ensuring high-quality component manufacturing.
Carlo Salvi's CF-Series machines are renowned for their high-performance cold forging capabilities. They provide exceptional control over force and displacement, feature rapid tool change systems, and incorporate advanced monitoring and control technologies.
Nakashimada Engineering Works offers the NBF-series machines, which are celebrated for their sophisticated cold forging technology, accurate parameter control, and rapid production speeds. These attributes ensure both high efficiency and dependability in the manufacturing of components.
Keep in mind that details such as specific models, features, or components may have changed since my last update. For the most current information on the latest cold forging machines and their capabilities in the United States and Canada, it’s best to check with the manufacturers or relevant industry resources.
Cold forging offers a wide array of choices when you are choosing a metal for a project. The different varieties include hard metals such as carbon steel, alloy steel, and stainless steel. Aluminum, brass, copper, silicon, and magnesium are soft metals that can be used. The one requirement for any metal is that it has a hardness of 44 HRC or lower on the Rockwell scale.
Copper is highly suitable for cold forging due to its excellent ductility and malleability. It can be easily shaped, bent, or stretched with minimal force, resulting in components that are resistant to corrosion and rust.
Aluminum is a lightweight, non-ferrous metal with a low density. It melts at approximately 1220°F and is known for its malleability, as well as its resistance to rust and corrosion.
Carbon steel is an iron-carbon alloy, with its various grades determined by the carbon content. It is known for its outstanding strength and ductility.
Stainless steel is widely used for its corrosion resistance, aesthetic appeal, and strength. While the term "stainless steel" broadly refers to steel with these properties, it actually encompasses a range of grades, each defined by its specific alloy composition.
Low carbon steels with a carbon content of 0.1% to 0.25%. Cold forging improves strain hardening in steel removing the need for austenitization, quenching, or annealing.
Suitable Alloy | Cold Formability Characteristic |
---|---|
Copper | Excellent |
Gold, Silver and most of their Alloys | Excellent |
Brass- Cartridge Brass | Good |
Platinum, palladium, tantalum, and their alloys | Most are cold formable. |
Titanium and its alloys | Pure Ti and alloys with high ductility, yes, but alloys like 6-4 are only hot head able. |
Nickel and its alloys | Pure Ni yes, alloys with room temperature elongation of 20% or more, yes. |
Iron and steels | Pure iron, yes. Steels, depends on the steel. Many are cold formable. |
When selecting a metal for a project, thorough research is crucial. Different metals respond to plastic deformation and shaping in various ways. The chosen metal should meet the final use requirements and desired strength. Consulting with a forging expert can provide valuable insights to help you make an informed decision.
Cold forging is capable of producing components of various sizes with exceptional dimensional precision and structural accuracy. Its cost-effectiveness and rapid production speed have made it a preferred method in manufacturing.
Cold forging's exceptional strength, reliability, and cost-effectiveness make it highly appealing for the automotive industry. Cold forged components are used in high-stress areas due to their superior shock resistance. Parts such as drive trains, drive shafts, and struts or shocks benefit from this process. The diagram below illustrates various undercarriage components of a car that are manufactured through cold forging.
Connectors like nails, bolts, rivets, and nuts have long been manufactured through cold forging. The process is favored by hand tool producers due to its ability to achieve tight tolerances and high dimensional accuracy, making it preferable to machining and other methods.
The military adheres to stringent specifications for hardware, often opting for cold forging in the production of shell casings, bullets, and other military equipment. This method ensures high reliability and performance under demanding conditions. The precise tolerances and strength of cold forged components make them ideal for military applications.
Cold forging is used for gear production because it eliminates the need of cutting in gear shaping. Gears can be produced from billets that are less than 50 mm or shaped using coiled wire. Some annealing may be necessary to remove residual stress and work hardening. An important benefit of cold forged gears is how smoothly and quietly they intermesh.
Aluminum forging is a method for processing aluminum alloys using pressure and heat to form high strength, durable products. The process of aluminum forging involves pressing, pounding, and...
Copper and brass forging is the deformation of copper and brass for the purpose of manufacturing complex and intricate shapes. The temperature at which copper and brass are forged is precision controlled and...
Forging is a metal working process that manipulates, shapes, deforms, and compresses metal to achieve a desired form, configuration, or appearance outlined by a metal processing design or diagram...
In this article, there are key terms that are typically used with open and closed die forging and it is necessary to understand their meaning. Forging is a process in manufacturing that involves pressing, hammering, or...
Rolled ring forging is a metal working process that involves punching a hole in a thick, solid, round metal piece to create a donut shape and then squeezing and pressuring the donut shape into a thin ring...
Forging steel is a manufacturing process used to shape steel by using localized compressive forces, which include hammering, pressing, and rolling. It is a widely used method for producing high quality steel products...
The ancient art of forging falls into two distinct categories – hot and cold where hot forging has been around for centuries while cold did not begin until the industrial revolution of the 19th Century. Though they are quite different ...
Aluminum casting is a method for producing high tolerance and high quality parts by inserting molten aluminum into a precisely designed and precision engineered die, mold, or form. It is an efficient process for the production of complex, intricate, detailed parts that exactly match the specifications of the original design...
Die casting is a high pressure metal casting process that forces molten metal into a mold. It produces dimensionally accurate precision metal parts that have a flawless smooth finish...
Sand casting is a manufacturing process in which liquid metal is poured into a sand mold, which contains a hollow cavity of the desired shape and then allowed to solidify. Casting is a manufacturing process in which...
Zinc die casting is a casting process where molten zinc is injected into a die cavity made of steel that has the shape, size, and dimensions of the part or component being produced. The finished cast zinc product has...
The casting process is an ancient art that goes back several thousand years to the beginning of written history. The archeological record has finds that document the use of the casting process over 6000 years ago around 3000 BC or BCE...