Cold Forging
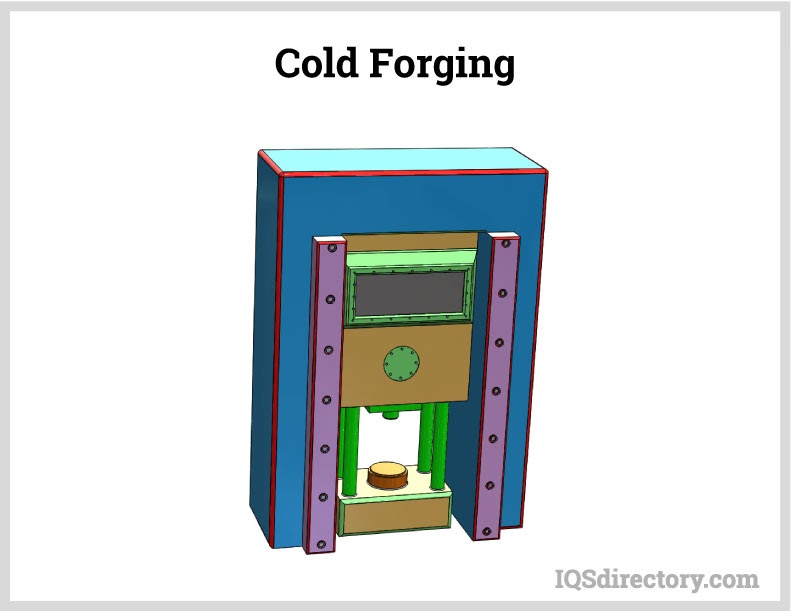
Cold forging is a metal shaping & manufacturing process in which bar stock is inserted into a die and squeezed into a second closed die. The process, completed is at room temperature or below the...
Please fill out the following form to submit a Request for Quote to any of the following companies listed on
A description of drop forging, names of prominent drop forging manufacturers, and an explanation of how drop forging is used
You will learn:
Drop forging is a metalworking technique used to shape and form a metal bar or billet placed between a pair of dies. Through significant force, the metal is compressed into the shape defined by the dies, creating a product or component. This process employs a drop hammer, which is elevated by means of air, belts, or chains, and then driven downward using air, gravity, or hydraulic power. The die consists of two key parts: the lower die, which remains fixed on the forge's anvil, and the upper die, secured to the ram, which is propelled downwards to meet the lower part of the die.
Essentially, drop forging involves repeatedly striking a metal piece until it conforms to the desired shape. The continuous hammer blows ensure the billet adequately fills the die cavity. Forging dies are designed to expel excess metal from the shape, known as flash, which is trimmed in a subsequent finishing process using various methods. Although the main shaping occurs during the hammering into the die, the trimming of the flash happens later to refine the component.
There are two main types of drop forging: open die and closed die, distinguished by the die form. While both processes work similarly, closed dies completely enclose the workpiece, whereas open dies allow the metal to flow outside the die constraints.
Among the various metal forming techniques, drop forging stands out as a highly effective and robust metal shaping process widely used in the manufacturing industry. This metal forging method employs immense force to reshape a heated or cold metal billet into precision components with exceptional mechanical strength and reliability. Drop forging finds applications in sectors such as aerospace, automotive, heavy equipment, oil & gas, agriculture, and construction due to its ability to enhance grain structure, increase load-bearing capacity, and minimize defects.
Drop forging primarily comprises two main processes: open die forging and closed die forging. These drop forging types differ fundamentally in how the die interacts with the workpiece during the deformation process. In closed die drop forging—sometimes called impression die forging—the die completely encloses the metal workpiece, producing complex, high-precision parts with close tolerances. Open die drop forging, also known as smith forging or free forging, utilizes dies that do not fully encase the material, allowing greater freedom and adaptability for creating larger and customized forged components. Understanding the distinctions between these forging processes helps users select the most appropriate method based on project requirements such as production volume, material properties, and desired end-use applications.
While open die forging and closed die forging share core principles—heating a billet and applying force to deform it into a specific shape—they have key differences in die configuration and application. In open die forging, the dies are generally flat, semi-round, convex, concave, or V-shaped surfaces that apply compressive forces without fully enclosing the metal billet. This flexible process accommodates a wide range of sizes, from small mechanical parts to massive forged products weighing several tons, making it ideal for manufacturing large, custom parts or small production runs.
Open die drop forging utilizes repetitive blows from a forging hammer or hydraulic press, progressively altering the shape and internal grain flow of the workpiece to meet exacting metallurgical standards. The hot forging process of heating the billet increases its plasticity, reduces forging force requirements, and results in improved ductility, toughness, and wear resistance. Additionally, open die forging permits rough shaping as well as finish forging for metal parts with superior strength and fatigue resistance.
Common forged products created by open die forging include discs, hubs, blocks, shafts, step shafts (with or without flanges), sleeves, cylinders, flats, hexes, rounds, and plates. Open die methods are highly adaptable and capable of producing custom shapes for specialized industrial applications. This forging technique is also valued for art smithing, grain refinement, removing defects, and improving machinability of challenging alloys. By reorienting metal grain flow, it markedly enhances fatigue strength and minimizes porosity, leading to components with increased toughness and reliability—benefits essential to users seeking high-performance forged products.
Dies used in open die forging typically consist of a top and bottom die, each crafted to create specific impressions or portions of the final shape. While most open die forging dies are flat, specialized options include round swaging dies, V-dies, mandrels, pins, and loose tools—each selected based on the desired forge configuration and dimensional requirements. Larger or more complex parts may be gradually shaped by passing the billet through a series of dies, ensuring optimal grain flow and structural integrity for high-value metal components.
Notching – During notching, an operator uses a tool resembling a chisel to impart evenly spaced impressions along the circumference of the workpiece. Rotating the material between hammer blows ensures uniform notches, a technique widely used in the forging of axles, crankshafts, and custom mechanical parts.
Shaping – Open die shaping creates diverse profiles and geometries by using machine jaws or fixtures to securely hold and rotate the billet. This process forms uniform forgings with tailored cross-sections, meeting demanding standards for machinery parts, shipbuilding, and renewable energy components.
Closed die forging, also referred to as impression die forging, utilizes precision-machined dies—often made from high-grade tool steel—to form metal into intricate, net-shaped, or near-net-shaped components. Here, the die sets act as a mold: the lower die rests on the anvil while the corresponding upper die is mounted on the ram or hammer. The heated or cold metal billet is inserted, and powerful blows, or a press action, force the material to conform precisely to the cavity contours, achieving complex geometries and tight tolerances essential for critical aerospace, automotive, and energy system parts.
Unlike open die forging, closed die processes ensure material is entirely contained, a factor that reduces excess flash and promotes high repeatability in mass production. The durable dies are engineered with considerations for partition lines, draft angles, ribs, fillets, and radii, enabling optimal metal flow and minimizing tool wear. Advanced die technology also supports near-net shape forging, reducing or eliminating the need for secondary machining operations and resulting in substantial material and labor cost savings.
Closed die drop forging delivers exceptional mechanical properties, as the compressive forces during plastic deformation align the grain structure with the shape of the product. This directional grain flow enhances fatigue strength, impact resistance, and load-carrying capacity, making it ideal for safety-critical components like connecting rods, gears, and levers. While die design and manufacture incurs higher setup costs, it's economically advantageous for high-volume production where uniformity and performance are paramount.
One technical challenge with closed die forging is die life expectancy. Dies are exposed to heavy operational stress and thermal cycling, typically lasting from 5,000 up to 7,000 cycles—although more complex shapes, harder materials, and tight tolerances can significantly reduce die life. Engineers address these limitations through advanced tool steel selection, heat treatment, and innovative die design to maximize longevity and performance.
The optimal design of closed die forging dies—including streamlined radii, effective partition lines, and proper draft angles—facilitates smooth metal flow, reduces internal stresses, and supports manufacturing of precision-forged products for a vast range of industrial uses.
Advantages of Open & Closed Die Forging | |
---|---|
Advantages | |
Better fatigue resistance and improved microstructure. | Grain structure formation increases the tightness and strength of the products. |
Continuous grain flow and finer grain size. | Economic for large production runs. |
Increased strength and longer part life. | No material limitation. |
Less material waste. | Better surface finish. |
Reduced chance of voids | Less or no machining required for its close tolerances. |
Valuable cost savings | Dimensions of tighter tolerances and net shapes can be achieved. |
Cold drop forging, a type of cold forging, involves shaping metal at or near room temperature, eliminating the need for prior heating of the workpiece. This process achieves outstanding dimensional accuracy and an excellent surface finish, meeting stringent requirements for parts used in automotive, electronics, and consumer goods manufacturing. Cold forging is especially well-suited to soft metals like aluminum, copper, and certain low carbon steels, enabling high-speed, high-volume production of components such as fasteners, bolts, rivets, and small precision parts with repeatable quality and low production costs.
The cold drop forging process imparts significant strain hardening to the metal, increasing yield strength and hardness while reducing ductility. Both open die and closed die techniques can be employed, depending on part complexity and volume. Durable, high-strength dies—often coated with advanced wear-resistant films—are essential due to the intense pressures involved. Workpieces are pre-treated with lubricants to minimize friction and prevent sticking, as die contact temperatures can rise to between 250°C and 450°C (482°F and 842°F) through the forging action alone.
Key advantages of cold forging include eco-friendly operation (reduced energy consumption), minimal material waste, and the capability to produce close tolerances without extensive secondary machining. Cold forging processes may be combined in succession (e.g., heading, extrusion, coining) to achieve complex forms, and modern equipment supports high automation for industry scalability. For manufacturers, engineers, and procurement professionals searching for reliable, cost-effective metal forming solutions, cold drop forging offers an attractive alternative to traditional hot forging—especially for intricate, mass-produced components.
Selecting between open die forging, closed die forging, and cold drop forging depends on several critical project factors, including part size, production volume, alloy selection, required tolerances, and application-specific performance standards. For large, custom metal components with grain structure optimization, open die forging offers flexibility and strength. When manufacturing precision parts with complex geometries and high repeatability, closed die forging provides superior dimensional control and mechanical reliability. For cost-sensitive, high-volume production—especially with non-ferrous metals—cold drop forging can dramatically lower per-part costs while maintaining quality.
Evaluating material properties such as ductility, tensile strength, and toughness is essential, as is consideration of post-forging treatments like heat treating, surface finishing, and mechanical testing. Reputable drop forging suppliers and manufacturers will provide comprehensive consultation, design engineering, and quality assurance services to address your unique application needs and ensure optimal results.
If you are ready to source forged metal products, outline your requirements—including part drawings, target tolerances, material specifications, and annual quantity forecasts—when contacting manufacturers. This ensures you receive accurate quotes, lead times, and technical support, accelerating your procurement process and maximizing the value of your investment in drop forging technology for your industry.
The selection of the optimal metal is a critical factor in the drop forging process, as the material's characteristics, physical properties, and response to high temperatures directly impact product quality and durability. Forging manufacturers must carefully consider strength, malleability, corrosion resistance, tensile strength, and cost-effectiveness when recommending metals for forging applications. Although a wide range of metals can be used in drop forging, the three most commonly employed are various grades of steel, copper, and aluminum, due to their favorable forging properties and suitability for a broad spectrum of forged components. Another important consideration is how each metal reacts when subjected to the intense heat and pressure that the forging process demands, as well as its grain flow enhancement, which increases mechanical strength and fatigue resistance.
Additionally, manufacturers' expertise and available forging equipment often influence the choice of metals, since some facilities specialize in specific alloys or are outfitted for particular metal groups. Collaboration with clients during the design and engineering phase—including detailed assessment of CAD renderings—ensures optimal material choice for the end application. This process aligns the forged part's intended function with both the physical attributes of the metal and the forging services the manufacturer offers, leading to higher performance parts and reduced waste.
Steel is the most widely used metal for drop forging, prized for its exceptional strength, versatility, high demand, and favorable cost-performance ratio. As an iron-carbon alloy, steel's properties can be precisely engineered by varying carbon content and incorporating additional alloying elements such as manganese, nickel, chromium, or molybdenum. These modifications yield many types of steel, enabling manufacturers to select grades that provide the optimal combination of toughness, ductility, wear resistance, and corrosion resistance for specific forging projects.
Under lower temperatures, steel exhibits a ferrite and iron carbide structure, while at higher forging temperatures, its crystalline structure transforms into an austenitic phase, enhancing its workability and strength. In drop forging operations, austenitic steel grades are preferred for their superior durability and capacity to withstand the repeated hammering intrinsic to closed-die forging. While there are over 3,000 steel grades available, only selected ones—with the appropriate balance of resilience, thermal stability, and forgeability—are suitable for forging robust, precision-engineered products.
Aluminum is a lightweight, ductile metal that offers excellent forgeability, corrosion resistance, and high strength-to-weight ratio, making it invaluable for aerospace forging, automotive drop forged parts, and lightweight structural applications. The range of aluminum alloys available provides options with varying combinations of strength, machinability, conductivity, and weldability—ensuring designers can match material properties to specific application needs. Aluminum’s natural oxide layer contributes to its corrosion resistance, but specific grades offer enhanced properties for demanding service environments.
Aluminum alloys for drop forging are primarily chosen from the 6000 and 7000 series, which are engineered for strength, toughness, and resistance to stress and fatigue failure. The most frequently drop forged aluminum alloys include 6061, 6063, 6082, and 7075, each tailored for distinct performance characteristics in forged metal parts:
Copper and its alloys are selected for drop forging primarily for their superior thermal and electrical conductivity, workability, and inherent corrosion resistance. As in other forging metals, copper's functionality can be expanded by alloying with elements such as tin, zinc, or nickel—producing brass, bronze, copper-nickel, and other specialized grades. Each copper alloy exhibits unique properties suited to different industrial applications, including plumbing, marine, electrical, and decorative forging.
Although less common than steel, aluminum, or copper, titanium is a valuable choice for drop forging when a combination of extreme strength, lightweight construction, and resistance to corrosion or high temperatures is required. With a strength-to-weight ratio comparable to carbon and stainless steel but at 40% less weight, titanium drop forged parts excel in aerospace forgings, biomedical implants, and high-performance automotive components. Forged titanium products can withstand continuous service at temperatures up to 537.78°C (1000°F) without compromising structural integrity. The primary limitation for titanium drop forging is the high raw material and processing costs, which can be up to 30 times higher than traditional stainless steels. As a result, titanium is reserved for critical, high-value applications where its superior properties justify the investment.
When selecting the best metal for your forged component, it's crucial to consider not just mechanical properties, but also cost, production volume, part complexity, and application-specific requirements such as heat or corrosion resistance. Partnering with an experienced drop forging manufacturer ensures you select the ideal material—whether it's forged steel for high-stress industrial parts, aluminum for low-mass transport applications, copper alloys for electrical conductivity, or titanium for cutting-edge industries—maximizing performance and return on investment for your project.
The drop forging process is completed using different forms of equipment with each form following the basic principles of drop forging, which is to repeatedly strike a workpiece until it takes on the desired shape and form. The key component in drop forging is the impression hammer that can take several different shapes and designs powered by air or hydraulics.
Hammers are classified as single effect, double effect, and counterblow, depending on the drive for the ram. The purpose of the hammer on a drop forge is to provide impact strain to deform a workpiece. The hammer thrusts the ram at the workpiece multiple times and is described by the energy of the blows or strokes it delivers.
Air powered drop hammers are the most powerful drop forging machine. Although they were introduced during the first industrial revolution, air powered drop hammers have remained in general use with hammers that can reach up to 350 inches per second. The basic construction of an air powered hammer is that of all forms of drop forges and includes an anvil base that is supported by two columns that guide the ram.
A significant upgrade to air powered drop hammers is the addition of programmable air hammers that allow operators to set the number of blows and the force of each blow. The programmability makes cycle times faster and running clearances are lowered due to the ram guiding method. The configurations of the forging have a closer match to provide tighter tolerances with cycle rates at 80 to 120 strokes per minute.
With the board drop hammer, maple boards are attached to the ram and are used to raise the ram using rollers that are pressed against the board. At a preset height, the pressure on the rolls is released and the ram drops by gravity or an operator. Unlike pneumatic and hydraulic drop forges, there is no force applied to the ram, which falls by gravity with the force of the blows to the workpiece dependent on the weight of the ram, which can range between 453.59 kg up to 2267.96 kg (1000 lbs. to 5000 lbs.).
Board drop hammers are an old design that are used in situations where power is expensive or difficult to get.
Air lift drop hammers use compressed air to lift the ram, a process that is similar to board drop hammers. They are a gravity type of drop forge that allows the length of the stroke and the velocity of the ram to be controlled to vary the amount of energy that is delivered to the workpiece. A steel rod connected to a piston lifts the ram using the force of the compressed air. Once the ram is raised, it is held in position by an air circuit that controls a clamp to hold the ram. The force of the ram is program controlled, which also controls the number of blows.
Air lift hammers are capable of delivering 50 to 75 strokes per minute. The popularity of air lift hammers is due to their lower maintenance cost and ease of operation.
With counterblow drop hammers, an upper ram is driven downward or sideways using steam or air as a lower ram moves upward or sideways to meet the other ram. Since there is no anvil, the workpiece is placed between the two rams and is shaped by their upward and downward action or sideways action for horizontal counterblow forges. The design of the counterblow hammer is to overcome the shortcomings of the traditional hammer and anvil method. Hammer and anvil drop hammer forges have to be positioned vertically such that the excess energy generated by each blow of the hammer can be dissipated into the structure of the forge or the surface below the forge.
Counterblow forges can be positioned horizontally since any excess energy created by the shaping of the workpiece becomes recoil. The two rams of a counterblow hammer strike one another, which reduces the force that is absorbed by the frame of the forge. Only one of the hammers is powered and moves the otherram by a coupling that is hydraulically powered. The mechanism of the counterblow hammer produces a unique flow pattern on the workpiece. As with traditional hammer and anvil drop forges, counterblow hammers can use open and closed dies.
The idea for counterblow forging is based on the idea that two bodies of equal mass forced toward each other will concentrate the absorption of energy. When a workpiece is placed between them, it is deformed by the impact of the energy generated by the two masses. The nature of the impact energy is preset and regulated for precise time controls to provide consistent energy for metal deformation.
The speeds and cycles for counterblow hammers is the same as double acting hammers with lower productivity due to the inability to perform multiple impressions. Tolerances have a broader span and guiding clearances are twice as much as those for traditional hammer and anvil forges. Also, loading, handling, and unloading are far easier with traditional hammer and anvil drop forges. Counterblow hammers are widely used in Europe with a few located in the United States. The largest counterblow hammers can deliver 900,000 foot pounds of energy and are used for the manufacture of very large workpieces.
Drop forging is used to manufacture a wide assortment of high tolerance products and produces components and parts for industries that require high strength and durable products. The factor that differentiates drop forging from any other manufacturing technique is the grain structure of the finished products.
The alignment of the grains in a metal determines the characteristics and properties of the products produced from a metal. Various methods are used to shape products and help maintain the original grain structure. Drop forging is one of the primary shaping methods that helps maintain and improve the grain structure of products to give the products strength and a lasting enduring quality.
Drop forging improves the mechanical properties of metals, which results in products having exceptional strength, toughness, and durability as well as resistance to fatigue and impact. The deformation process aligns the grain structure, reducing weak points and improving structural integrity.
One of the major reasons to use drop forging is the compressive force that is applied to a workpiece, which eliminates internal voids, porosity, and defects in the metal. As a result, workpieces have improved structural integrity and strength. It is essential that any defects, deformities, or voids in the metal be removed, the removal of which enables components to endure heavy loads, vibrations, and stressful operating conditions.
As every designer and engineer knows, the dimensional accuracy of a part is necessary in order to achieve tight tolerances and consistent shapes. With drop forging, dies and controlled deformation ensure that products meet design specifications and fit into the assemblies for which they are designed. The accuracy and consistency of drop forging removes the need for secondary machining and adjustments.
Components for applications can be produced using a variety of manufacturing processes. One of the factors that influences the decision as to what method will be used to produce a component is the cost of the process, which, in some cases, can be too high and impractical. Drop forging is a high-volume process capable of producing thousands of parts in a short time. It reduces material waste due to its accuracy and produces high strength to weight ratio parts.
Although there are specific metals that perform best when drop forged, the number of metals that can be used in the process are endless and range from soft easily formable metals to high hardness ones that require more aggressive deforming. This factor allows designers, engineers, and manufacturers to choose metals that best fit their project based on the desired properties of an application.
The versatility in the choice of metals allows designers and engineers to create components with intricate details, complex configurations, and unique and unusual geometries, which would be difficult and expensive to produce using any other manufacturing process. The shape, size, and form of a part can be produced in any customized shape such that it exactly fits design requirements and needs.
Changes to grain flow is important in regard to the manufacturing of components that have to withstand high stress and impact. The adjustment of grain flow during the drop forging process improves the impact and fatigue resistance of parts, which makes it less likely that they will fail by fracturing or cracking during use. In addition, drop forging increases the ductility of metals, a factor that allows them to undergo changes in shape without breaking.
The grain flow created by drop forging directly affects the mechanical properties of a component or part. It determines the push or pull of grains when placed under stress or fatigue. Since cracks are more likely to occur parallel to the grain structure, stress applied to a component should be perpendicular to the grain structure. Drop forging produces components that have their grain structure aligned in the direction of maximum strength
The durability and strength of forged parts is why they are used in power generating industries, the defense industry, and aerospace. In essence, the use of finely structured grain formation is essential for industries that cannot afford unreliable components.
One of the fascinating facts about drop forging is its origins, which dates back hundreds of years to China where bronze and iron were hammered into weapons, tools, and household items. The original version of drop forging did not involve impact machinery that applied tons of force to a metal piece but was performed by a strong man with a hammer. It is amazing that this ancient manufacturing art has progressed through the ages to become an essential part of so many industries.
As any mechanic or engineer can tell you, components for automobiles have to be exceptionally strong and durable. It is for this reason that critical parts of cars are produced using drop forging.
Drop forged parts for automobiles are extremely critical and require the highest amount of strength and durability. Hand tools are on a more practical level and require the same characteristics. In most cases, they have a simple design and are normally forged from a single billet. From DIY users up to professionals, hand tools have to be made of materials that won’t fail and are dependable.
Of all the various industries, the construction industry depends on tools and components that are capable of withstanding the pressure and stress of constant use. Although it is common to find hand tools as part of construction, there are more critical tools that require greater strength and endurance due to the importance of the application for which they are used.
The guiding principle for all aeronautics components is reliability and safety. Unlike the parts for other industries, failure of parts in the aeronautics industry can mean the loss of lives. The critical nature of aerospace necessitates the use of drop forging to produce the highest quality and most reliable components.
Drop forging is a manufacturing process that applies multiple blows of several tons to a workpiece to shape and form it into a viable component, part, or product.
The dies of drop forging can be open or closed and are factors that differentiate drop forging processes.
The wide use of drop forging is due to the reliability and dependability of the parts that are manufactured by the process. During the compression of a workpiece, the grain structure of the metal is changed to create different and more durable properties.
Drop forging is an ancient manufacturing process that began hundreds of years ago with a man with a hammer and progressed over the centuries to become a highly efficient and reliable form of manufacturing.
Industries that rely on tight tolerances and dimensionally accurate parts depend on drop forging for the most critical parts of their assemblies.
Cold forging is a metal shaping & manufacturing process in which bar stock is inserted into a die and squeezed into a second closed die. The process, completed is at room temperature or below the...
Copper and brass forging is the deformation of copper and brass for the purpose of manufacturing complex and intricate shapes. The temperature at which copper and brass are forged is precision controlled and...
Forging is a metal working process that manipulates, shapes, deforms, and compresses metal to achieve a desired form, configuration, or appearance outlined by a metal processing design or diagram...
In this article, there are key terms that are typically used with open and closed die forging and it is necessary to understand their meaning. Forging is a process in manufacturing that involves pressing, hammering, or...
Rolled ring forging is a metal working process that involves punching a hole in a thick, solid, round metal piece to create a donut shape and then squeezing and pressuring the donut shape into a thin ring...
Forging steel is a manufacturing process used to shape steel by using localized compressive forces, which include hammering, pressing, and rolling. It is a widely used method for producing high quality steel products...
The ancient art of forging falls into two distinct categories – hot and cold where hot forging has been around for centuries while cold did not begin until the industrial revolution of the 19th Century. Though they are quite different ...
Aluminum casting is a method for producing high tolerance and high quality parts by inserting molten aluminum into a precisely designed and precision engineered die, mold, or form. It is an efficient process for the production of complex, intricate, detailed parts that exactly match the specifications of the original design...
Die casting is a high pressure metal casting process that forces molten metal into a mold. It produces dimensionally accurate precision metal parts that have a flawless smooth finish...
Sand casting is a manufacturing process in which liquid metal is poured into a sand mold, which contains a hollow cavity of the desired shape and then allowed to solidify. Casting is a manufacturing process in which...
Zinc die casting is a casting process where molten zinc is injected into a die cavity made of steel that has the shape, size, and dimensions of the part or component being produced. The finished cast zinc product has...
The casting process is an ancient art that goes back several thousand years to the beginning of written history. The archeological record has finds that document the use of the casting process over 6000 years ago around 3000 BC or BCE...