Aluminum Forging
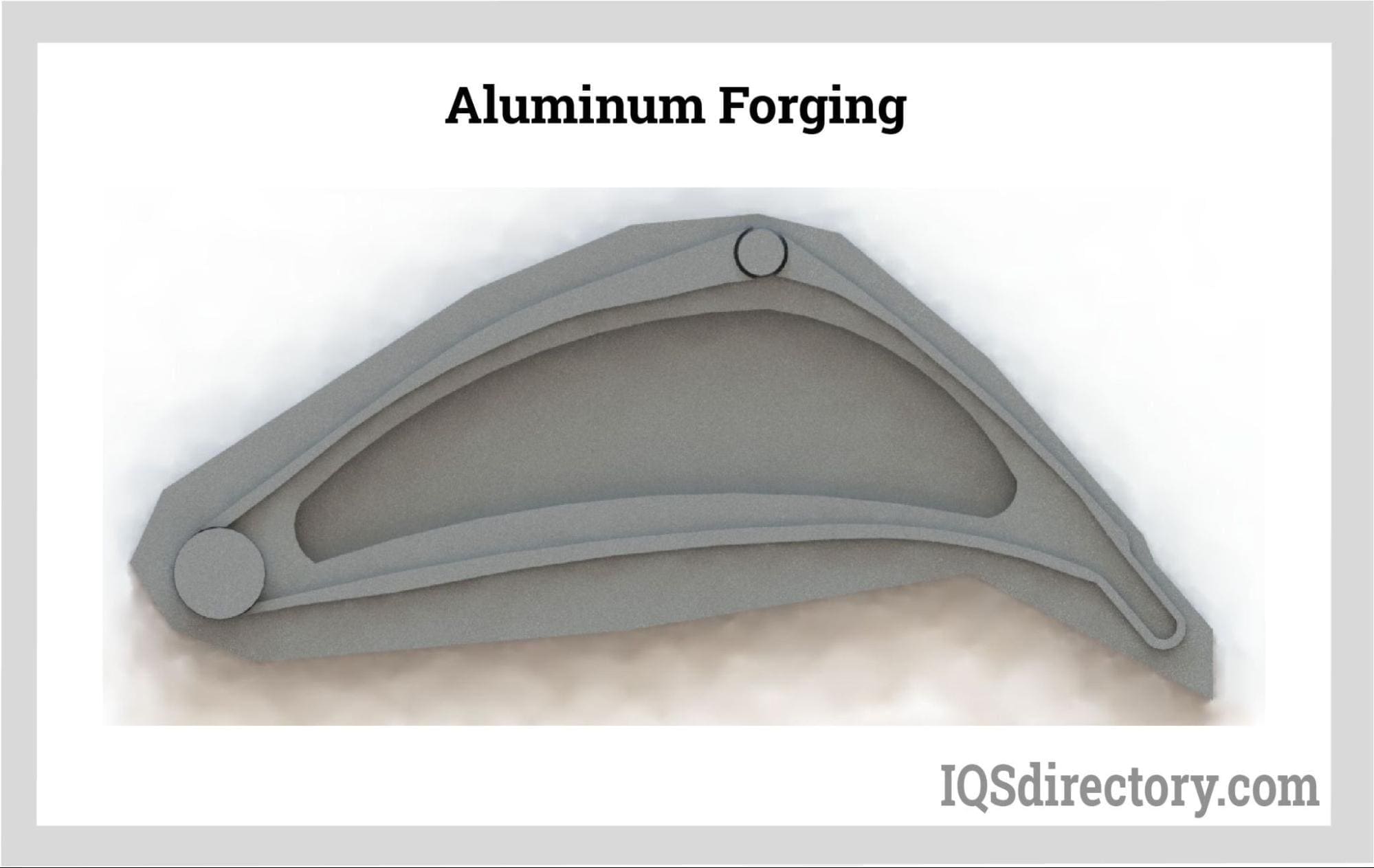
Aluminum forging is a method for processing aluminum alloys using pressure and heat to form high strength, durable products. The process of aluminum forging involves pressing, pounding, and...
Please fill out the following form to submit a Request for Quote to any of the following companies listed on Forgings .
This Article takes an In-depth look at Forging
You will learn more about topics such as:
Forging is an ancient metalworking practice with two primary forms: hot and cold forging. Hot forging dates back several centuries, whereas cold forging became prevalent during the Industrial Revolution of the 19th century. Despite the differences between these methods, they both aim to reshape metal into desired forms. The decision to use hot, cold, or warm forging depends on the metal type and the intended product's final shape.
In hot forging, metal is heated well beyond its recrystallization temperature threshold. This temperature varies depending on the metal: for steel, it's up to 1150° C; for aluminum alloys, 360° C to 520° C; and for copper alloys, it ranges from 700°C to 800°C. Keeping the metal's temperature above its recrystallization point is crucial, as falling below this point can lead to the formation of tiny crystals that strain hardens the material, rendering it challenging to work with.
Environmental conditions can impact the hot forging process, as exposure to the atmosphere can lead to oxidation. To mitigate this, forging may occur in an environmentally controlled chamber or through isothermal forging, akin to forging under vacuum conditions.
A key advantage of hot forging lies in its ability to enhance the metal's strength. Hot-forged metals, known for their excellent ductility, can be extensively deformed and reshaped, enhancing their resistance to tensile stress. The process optimizes the internal grain structure of the metal, thereby boosting the final part's strength and structural qualities.
Various parts and components are produced using hot forging due to its capacity to create complex shapes with high precision. It's particularly suitable for metals with high formability, which can be readily deformed. The metal's strength and durability increase post-hot forging, which is versatile enough for crafting customized parts. Moreover, hot forged components boast superior surface finishes compatible with a range of finishing and polishing techniques.
The hot forging process offers numerous benefits, including efficient production of individual parts, albeit with somewhat lower precision compared to other methods. While it can lead to scale formation on metal surfaces, it also reduces metal stress with diminished work hardening temperatures. Additionally, it fosters uniform grain structure, boosts ductility, and addresses chemical inconsistencies in the material.
Despite the many advantages of hot forging, some drawbacks must be taken into account. During the cooling phase, there is a risk of metal warping and brittleness. Some metals are not suitable for hot forging due to potential variations in grain structure and less accurate tolerances.
Though there are a few limitations to hot forging, it remains highly effective for producing aerospace components and aircraft parts. The process enhances the malleability of metals, facilitating the crafting of intricate shapes and detailed designs required in these industries.
Cold forging refers to a metal shaping and deforming process that is performed at or slightly above room temperature where the temperature is kept at near three tenths of the recrystallization point of the metal. Squeezing, bending, shearing, and drawing are the most common cold forging methods. Soft metals such as aluminum or copper are ideal for the process.
The method of cold forging uses compressive force to shape the workpiece by hand or machine. In many cases, the metal is pushed into a die shaped in the form of the final product. It is less expensive than hot forging and produces completed products that require little, if any, finishing. With aluminum, after being cold forged, it is heat treated to strengthen the piece, a process known as "tempering".
The most common metals in cold forging are standard or carbon alloy steels. It is used to produce small, high volume products like fasteners such as nails, screws, rivets, and such. The lack of the need for heat makes it inexpensive and efficient. The types of cold forging methods used depends a great deal on the metal and the required shape. Below are descriptions of some common cold forging processes.
Impression-die forging is a typical cold forging technique where metal is inserted into a die affixed to an anvil. The metal is then hit with a hammer, which shapes it according to the die. Multiple rapid hammer strikes may be applied depending on the specific product requirements.
Also called sizing, squeezing decreases the thickness of metal through pressure application, which varies based on the sizing area, metal type, and the required thickness modification. This technique is usually employed to achieve accurate dimensions in forged pieces.
Cold roll forming produces more attractive finished surfaces with closer tolerances in a variety of shapes that can easily be galvanized, painted, or powder coated. Thin sheets of a metal, usually steel, are rolled into shapes such as floor and roof paneling, C, or Z shapes.
Drawing uses tensile forces to pull or stretch a metal to a particular shape or thickness. There are two forms of drawing – sheet metal and wire, bar, or tube. Drawing can only be applied to certain types of metal or materials that have sufficient tensile strength. Though it may seem similar to cold rolling, it differs in the amount and position of the applied force.
Cold forging has other processes designed for shaping metals. The ones listed here are common but only a few of the many that are in use. It is a popular process with auto manufacturers for the production of steering and suspension parts, certain braking systems, axles, and many other automobile parts.
Various machines are essential for modern forging, allowing for the efficient creation of robust metal parts used across industries like automotive, aerospace, construction, and manufacturing. In the following sections, we highlight several popular brands of forging machinery available in the United States and Canada.
The Bulldog 200 by Ajax-CECO is a highly adaptable forging machine, praised for its sturdy design, impressive forging capabilities, and advanced control systems. It is well-regarded for its dependability, long-lasting performance, and versatility in producing various forged parts.
National Machinery's FORMAX Plus series incorporates cutting-edge servo-driven technology, facilitating rapid tool changes and energy-saving operations. These machines are celebrated for their precision, high productivity, and flexibility in accommodating diverse forging applications, earning them widespread acclaim.
Erie Press Systems is known for its electric forging presses, which deliver energy efficiency, precise control, and versatility. These presses offer high force output and customizable settings, making them suitable for forging a variety of materials and shapes. Their popularity is attributed to their sustainability, precision, and ability to meet contemporary manufacturing demands.
Wyman-Gordon excels in manufacturing radial forging machines, which use radial die movement to create components with exceptional strength and integrity. These machines are highly regarded for their precision in shaping, waste reduction, and production of high-quality forged parts.
The MF Series Forging Press from Mitsubishi Heavy Industries America stands out for its robust design and versatility. It excels in various forging tasks with its precise control systems and efficiency, making it ideal for handling multiple materials and complex processes with high reliability.
These machines are widely recognized for their robustness, precise control, and versatility, effectively addressing the needs of modern forging across various industries. However, individual models and their features may differ, so it’s recommended to consult manufacturers or industry experts for the most current information on the latest forging equipment available in the US and Canada.
Cold forging provides various advantages, such as operating at room temperature without the need to heat the metal, which reduces the overall cost of parts. Additionally, it eliminates the need for costly equipment like blast and industrial furnaces used in hot forging.
Cold forging enables the rapid and consistent production of parts with excellent dimensional accuracy, making it ideal for companies that need high volumes and fast delivery. Thanks to computerized processes, each component is produced with identical precision and detail. Additionally, cold forging extends the lifespan of dies, as they are not subjected to the stress and wear associated with hot metals.
Cold forging enhances precision, creating parts with tight tolerances and consistent quality. By closely following design specifications, this method minimizes defects and the need for rework, while also producing components with a refined grain structure.
An important factor, in this era of environmental concerns, is the eco-friendliness of cold forging since parts are shaped and formed under high pressure at room temperature. Unlike other processes, cold forging ensures that there will not be air bubbles or other deformities trapped in the workpiece.
Some of the other benefits of cold forging include improved material usage, lower energy costs, and little to no finishing. With the rising costs of energy and the shortage of materials, cold forging is the solution to producing parts efficiently reducing the effect of those factors.
Aluminum forging is a method for processing aluminum alloys using pressure and heat to form high strength, durable products. The process of aluminum forging involves pressing, pounding, and...
Cold forging is a metal shaping & manufacturing process in which bar stock is inserted into a die and squeezed into a second closed die. The process, completed is at room temperature or below the...
Copper and brass forging is the deformation of copper and brass for the purpose of manufacturing complex and intricate shapes. The temperature at which copper and brass are forged is precision controlled and...
Forging is a metal working process that manipulates, shapes, deforms, and compresses metal to achieve a desired form, configuration, or appearance outlined by a metal processing design or diagram...
In this article, there are key terms that are typically used with open and closed die forging and it is necessary to understand their meaning. Forging is a process in manufacturing that involves pressing, hammering, or...
Rolled ring forging is a metal working process that involves punching a hole in a thick, solid, round metal piece to create a donut shape and then squeezing and pressuring the donut shape into a thin ring...
Forging steel is a manufacturing process used to shape steel by using localized compressive forces, which include hammering, pressing, and rolling. It is a widely used method for producing high quality steel products...
Aluminum casting is a method for producing high tolerance and high quality parts by inserting molten aluminum into a precisely designed and precision engineered die, mold, or form. It is an efficient process for the production of complex, intricate, detailed parts that exactly match the specifications of the original design...
Die casting is a high pressure metal casting process that forces molten metal into a mold. It produces dimensionally accurate precision metal parts that have a flawless smooth finish...
Sand casting is a manufacturing process in which liquid metal is poured into a sand mold, which contains a hollow cavity of the desired shape and then allowed to solidify. Casting is a manufacturing process in which...
Zinc die casting is a casting process where molten zinc is injected into a die cavity made of steel that has the shape, size, and dimensions of the part or component being produced. The finished cast zinc product has...
The casting process is an ancient art that goes back several thousand years to the beginning of written history. The archeological record has finds that document the use of the casting process over 6000 years ago around 3000 BC or BCE...