AC Motors
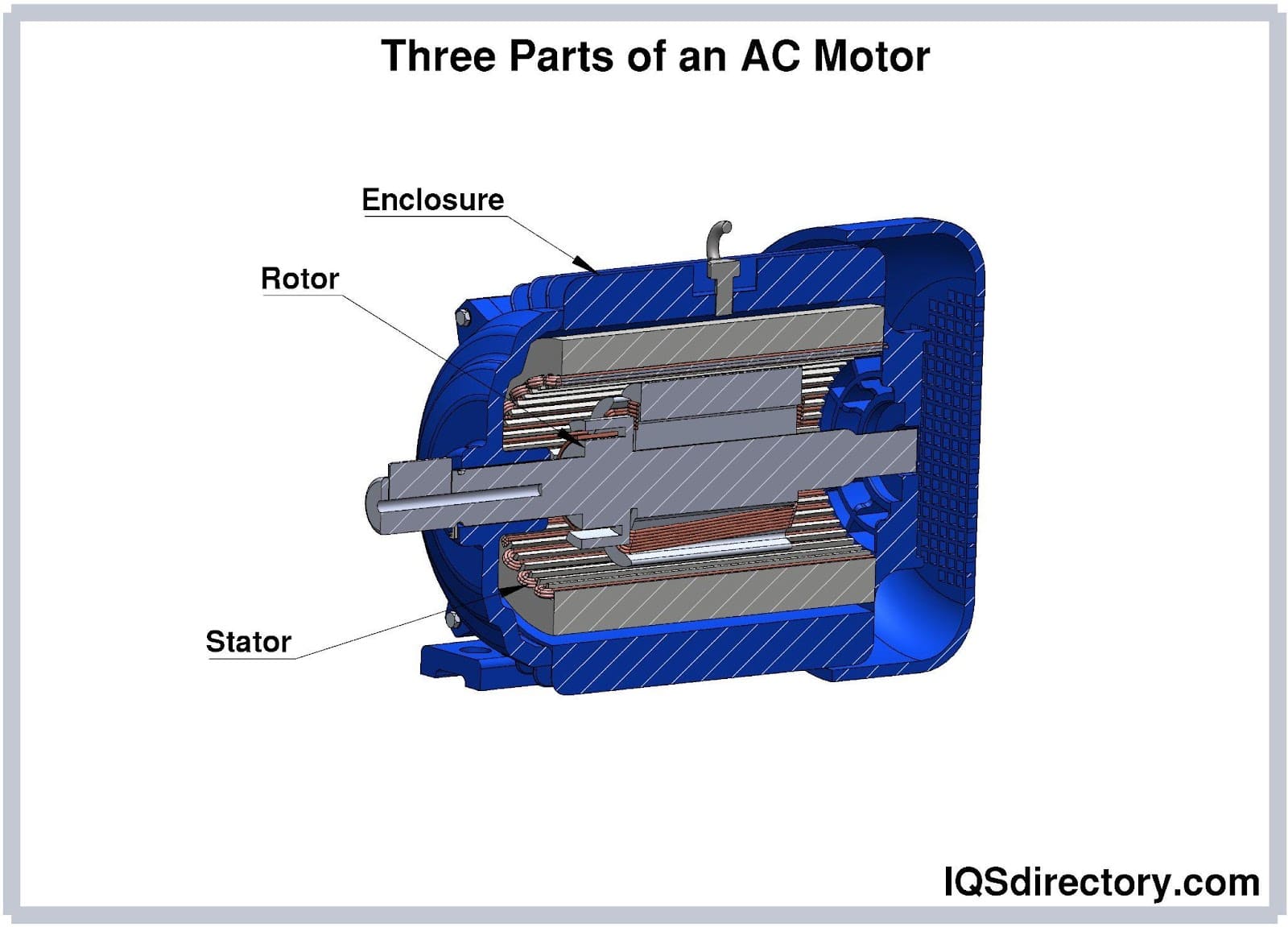
An AC motor is an electric motor that uses alternating current to produce mechanical energy using magnetism blended with alternating current. The structure of an AC motor includes coils that produce a rotating...
Please fill out the following form to submit a Request for Quote to any of the following companies listed on
This article takes an in depth look at fractional horsepower motors.
You will learn more about topics such as:
A fractional horsepower motor is a motor type that operates using either alternating current (AC) or direct current (DC) and provides less than one horsepower, with a peak power capacity of 746 watts. These motors are ideal for compact electronic devices and simple consumer products due to their lower power output. Even in larger systems like vehicles, they can continue operating when the primary power supply is interrupted.
Fractional horsepower motors have numerous applications. Their minimal vibration makes them suitable for equipment demanding high precision. Among the types of fractional horsepower motors are stepper and servo motors, both providing a high degree of input accuracy. They are particularly popular in robotics due to their precision and ease of control.
Though fractional horsepower motors are very small, they have the same characteristics as larger electric motors. They are widely used since they can fit into any device. As with large electric motors, fractional horsepower motors use an electromagnetic field to change electricity into mechanical energy.
Fractional horsepower motors are categorized based on the type of current they use, the method of current application, and their overall design. They are available in numerous sizes and configurations, which contributes to their adaptability for various applications.
Brushed series motors were the first electric motors and date back to the middle of the first industrial revolution. Though brushless motors have replaced them, they are still found in certain applications. The modern brush motor has an axle, rotor, commutator, stator, magnets, and brushes.
In a brush motor, permanent magnets are positioned on the outer part, while the armature, which rotates within, is located on the inside. The permanent magnets act as the stator, and the rotating armature serves as the rotor. The armature contains an electromagnet that, when energized, generates a magnetic field interacting with the stator magnets. This interaction causes the armature to rotate through 180°.
To maintain the armature's rotation, the electromagnet's poles need to be alternated. This task is managed by brushes that adjust the polarity and supply power to the commutator, which in turn energizes the windings. The brushes, in conjunction with the commutator, make contact with the rotating armature electrodes, thereby reversing the magnetic polarity.
A brushless motor is a type of synchronous electric motor that employs a step motor controller to generate rotation, converting electrical energy into mechanical energy. Unlike brushed motors, brushless motors do not use a commutator, which is a key distinction between the two types.
In a brushless motor, the windings are positioned on the stator, which eliminates the need for brushes. This contrasts with brushed motors, where the magnets are stationary and the wires rotate. The absence of brushes and a commutator reduces friction, lowers the motor's heat output, and enhances overall efficiency.
A permanent split capacitor (PSC) fractional horsepower motor features a cage rotor and two windings: a main winding and an auxiliary winding, similar to a split phase motor. It includes a capacitor connected in series with the starting winding, while another capacitor, "C", remains permanently connected to the circuit, serving both starting and running conditions. This setup allows the motor to function as a balanced two-phase motor, providing smooth torque and quiet operation. The permanent capacitor splits the single-phase input into a two-phase supply, enabling the motor to start on its own.
A reluctance motor operates similarly to a single-phase induction motor, featuring end rings at both ends. As with other electric motors, the core components of a reluctance fractional horsepower motor include the stator and rotor, which are separated by an air gap. The motor functions by aligning the rotor's speed with the stator's rotating magnetic field, achieving precise operation.
The distinctive design of a reluctance fractional horsepower motor allows it to provide high power density at a minimal cost. The motor operates on the principle that magnetic materials align more easily within a magnetic field, reducing reluctance and optimizing performance.
One notable characteristic of a series fractional horsepower motor is its capability to generate high torque during startup. This is due to its unique construction, where the motor winding is connected in series with the armature winding, setting it apart from other electric motor designs. The armature and field windings use large conductors that offer minimal resistance to current flow. Because of their size, these conductors can handle a significant amount of current, which saturates the coils and creates a powerful magnetic field.
A servo motor is a type of rotary motor designed for precise control over angular position, acceleration, and velocity. These motors are commonly used in closed-loop control systems, such as in robotics and CNC machines. They rely on position feedback to regulate rotational speed, motion, and positioning.
The positioning of the shaft is determined by a control signal input. If the actual position deviates from the specified requirements, the controller makes adjustments to correct it. Servo motors are integrated between the input system and the process, utilizing feedback from the process to fine-tune their positioning.
A shaded-pole motor is the simplest of AC motors and consists of a rotor assembly and stator pole. Aside from the rotor and pole, shaded-pole motors have windings that are shaded and unshaded. The shaded portion of the motor’s winding is a copper ring, which acts as its secondary winding. The unshaded winding creates a lower strength magnetic field. The magnetic flux created by the interaction of the windings increases the torque after it has started. Shaded-pole motors move in one direction and are found in washing machines.
A split phase fractional horsepower motor features a single cage rotor and a stator equipped with two windings: the main winding and the starting winding. These windings are spaced 90° apart. The main winding has low resistance and high inductive reactance, while the starting winding exhibits high resistance and low inductive reactance.
An external resistor is placed in series with the starting winding, creating an imbalance in current between the windings and resulting in a non-uniform rotating field. This setup provides a starting torque that is 1.5 to 2 times greater than the running torque. Once the motor reaches its synchronous speed, the starting winding is automatically disconnected from the circuit.
A stepper fractional horsepower motor is a DC motor that moves in steps and has multiple coils organized in phases. When the phases are energized in sequence, the motor rotates. They are normally chosen for applications that require precision motion control, such as automation and robotics.
In a synchronous fractional horsepower motor, the rotation of the shaft is the same as the applied current. The total number of rotations the shaft makes is equal to the current and is the same as the AC cycles. A synchronous motor has multiple phases AC electromagnets on the stator that produce a rotating magnetic field. A permanent magnet is synced with the rotating magnetic field.
Fractional horsepower motors serve versatile roles across a variety of applications, especially where compact size and high performance are required. They are commonly used in direct current (DC) configurations for tasks that demand precision and automation.
Designing a fractional horsepower motor involves evaluating several key factors, with torque and speed being paramount. Additionally, the choice between a brushed or brushless motor must be considered based on the specific needs of the application.
Fractional horsepower motors are characterized by their output power of 746 watts or less and frame sizes under 104 mm². Their typical power ranges vary: AC motors generally offer from 1/20th hp to 1 hp, DC motors range from 1/100th hp to 1/2 hp, brushless motors span from 1/35th hp to 1/2 hp, and universal motors cover from 1/100th hp to 2 1/2 hp. Smaller variants are classified as sub-fractional or micro motors.
Micro motors are extremely compact and lightweight, optimized for low power consumption and minimal electromagnetic interference. They are designed for use in confined and intricate spaces with limited power availability. Both brushed and brushless micro motors are available, each offering distinct benefits for specific use cases.
Fractional horsepower motors can be powered by either AC or DC sources. AC motors may be single-phase or three-phase, with most being single-phase types, such as shaded pole or split-phase motors. Single-phase motors operate on a pulsating current, requiring additional current to initiate movement. While they are generally less efficient than three-phase AC motors, they tend to have a longer lifespan and require minimal maintenance.
DC motors come in two main types: brushed and brushless. Brushless DC motors are synchronous and utilize a closed-loop controller to manage the switching of DC currents.
Three key factors determine the power of a fractional horsepower motor: horsepower, torque, and speed. Horsepower measures the motor's overall work output, while torque represents the angular force the motor can exert. Speed refers to how quickly the motor rotates.
Horsepower is directly related to the product of speed and torque. It's crucial for the motor's power to align with the workload it will handle. Although it might seem intuitive to choose a more powerful motor, optimal efficiency is achieved by matching the motor's horsepower to the specific demands of the workload.
The following formula calculates horsepower. The constant 5252 converts James Watt's original unit of 33,000 foot-pounds per minute into Newton meters per second.
Horsepower (HP) = (Torque × Speed)/5252
Enclosures serve to house the internal components of a motor and shield the mechanism from damage. They come in various materials, including plastic, aluminum, and steel. There are ten different classes of fractional horsepower motor enclosures, each designed for specific conditions: Open Drip Proof (ODP), Totally Enclosed Fan Cooled (TEFC), Totally Enclosed Air Over (TEAO), Totally Enclosed Non-Ventilated (TENV), Totally Enclosed Force Ventilated (TEFV), Weather Proof Level 1 (WP1), Weather Proof Level 2 (WP2), Totally Enclosed Air to Air Cooled (TEAAC), Totally Enclosed Water to Air Cooled (TEWAC), and Explosion Proof (XP).
Bearings are crucial components in electric motors, serving to minimize friction and wear. They enable shafts to rotate efficiently at high speeds by converting sliding motion into rolling motion, thereby reducing power loss. The two most prevalent types of bearings are ball bearings and cylindrical roller bearings.
Ball bearings achieve rolling motion through balls situated within a race or cage. They are designed for high-speed operations and low friction, and are suitable for handling light to medium loads. In electric motors, ball bearings are typically used in direct-coupled applications to manage both radial and axial loads.
Cylindrical roller bearings are engineered to support heavy loads at very high speeds. They are housed in a cage that keeps the rollers separated, reducing friction. Their superior performance is attributed to the increased contact surface area provided by the cylindrical rollers.
Fractional horsepower motors are utilized in applications where precision and accuracy are paramount. Despite their small size, these motors are equipped with highly efficient gear systems that can handle a wide array of tasks with exceptional consistency. They are intricately designed, requiring a high level of skill and expertise.
Fractional horsepower motors have a vast range of applications, from dispensing medication to operating door mechanisms. Their versatility and various designs make them adaptable to numerous conditions and purposes.
Fan motors are typically straightforward in design and can be either synchronous or asynchronous. They come in various sizes and types to suit different applications. To adjust the fan's speed, a frequency inverter is used to modify the frequency. Most fan motors run on direct current (DC).
Fractional horsepower motors are employed in computers to drive the hard disk, enabling it to spin and access stored data. Additionally, a fan, which is crucial for cooling the computer's components during operation, also relies on these small, compact motors. Despite their size, these motors are highly precise and dependable, fitting seamlessly within the computer's casing.
Air conditioners utilize various fractional horsepower motors, including those for the blower and the compressor. The compressor regulates the refrigerant lines, which are central to the air conditioning system. Additionally, the fan circulates air over the condenser unit to enhance the heat exchange between the refrigerant and the outdoor air.
A windshield wiper fractional horsepower motor is a compact tube motor attached to the wiper arm. A linkage system connects the motor to the wiper arms, while the wiper arm links the motor to the wiper blade. When the car's switch is turned on, a fuse sends a signal to the wiper motor, which includes information on the desired speed for the wiper arm's movement.
Fractional horsepower motors are used to adjust the position of car seats for both drivers and passengers. By pressing the buttons on the side of the seat, these motors control movements such as moving the seat forward or backward, raising or lowering it, adjusting the headrest, and tilting the seat. Relays activate the motors based on the signals received from the seat switches.
The two types of fractional horsepower motors used in the manufacture and production of robots are DC motors and servo motors. Stepper motors are also used for specialty robotic functions. The many types of motors used in robotics control motion, including vertical, radial, rotational, pitch, roll, yaw, and movement motions.
Fractional horsepower motors are well-suited for robotics because of their compact size and precise control. Their diverse range allows for selecting a motor that matches specific robotic functions, movements, and operational conditions.
The six applications mentioned are just a small fraction of the many ways fractional horsepower motors are used. Whenever a compact motor is needed, it's highly likely that a fractional horsepower motor is the solution.
An AC motor is an electric motor that uses alternating current to produce mechanical energy using magnetism blended with alternating current. The structure of an AC motor includes coils that produce a rotating...
A DC motor or direct current motor is an electrical machine that transforms electrical energy into mechanical energy by creating a magnetic field that is powered by direct current. When a DC motor is powered, a magnetic field is created...
An electric motor is an electric machine that converts electrical energy to mechanical energy. Most electric motors work via the interaction of the motor magnetic field and electrical current in a wound wire to...
Power supplies are electrical circuits and devices that are designed to convert mains power or electricity from any electric source to specific values of voltage and current for the target device...
An AC power supply is a type of power supply used to supply alternating current (AC) power to a load. The power input may be in an AC or DC form. The power supplied from wall outlets (mains supply) and...
An AC power cord is a detachable way of providing an alternating current of electric energy from a mains power supply to an electrical appliance or equipment. Serving industries like...
A DC DC power supply (also known as DC DC Converter) is a kind of DC power supply that uses DC voltage as input instead of AC/DC power supplies that rely on AC mains supply voltage as an input...
A DC power supply is a type of power supply that gives direct current (DC) voltage to power a device. Because DC power supply is commonly used on an engineer‘s or technician‘s bench for a ton of power tests...
Electrical plugs, commonly known as power plugs, are devices responsible for supplying and drawing current from a receptacle to the circuitry of an electrical appliance...
Gear drives, sometimes referred to as gear trains and gearboxes, are mechanisms consisting of an assembly of gears, shafts, and other machine elements for mounting the rotating parts...
By definition a power supply is a device that is designed to supply electric power to an electrical load. An electrical load refers to an electrical device that uses up electric power. Such a device can be anything from...
A NEMA connector is a method for connecting electronic devices to power outlets. They can carry alternating current (AC) or direct current (DC). AC current is the typical current found in homes, offices, stores, or businesses...
A power cord is an electrical component used for connecting appliances to an electrical utility or power supply. It is made from an insulated electrical cable with one or both ends molded with connectors...
A programmable power supply is a method for controlling output voltage using an analog or digitally controlled signal using a keypad or rotary switch from the front panel of the power supply...
Thomas Edison developed the power distribution system in 1882. He wrapped a copper rod in jute, a soft shiny fiber from plants, as an insulator. The jute wrapped copper rod was placed in a pipe with a bituminous compound...