Door Latches
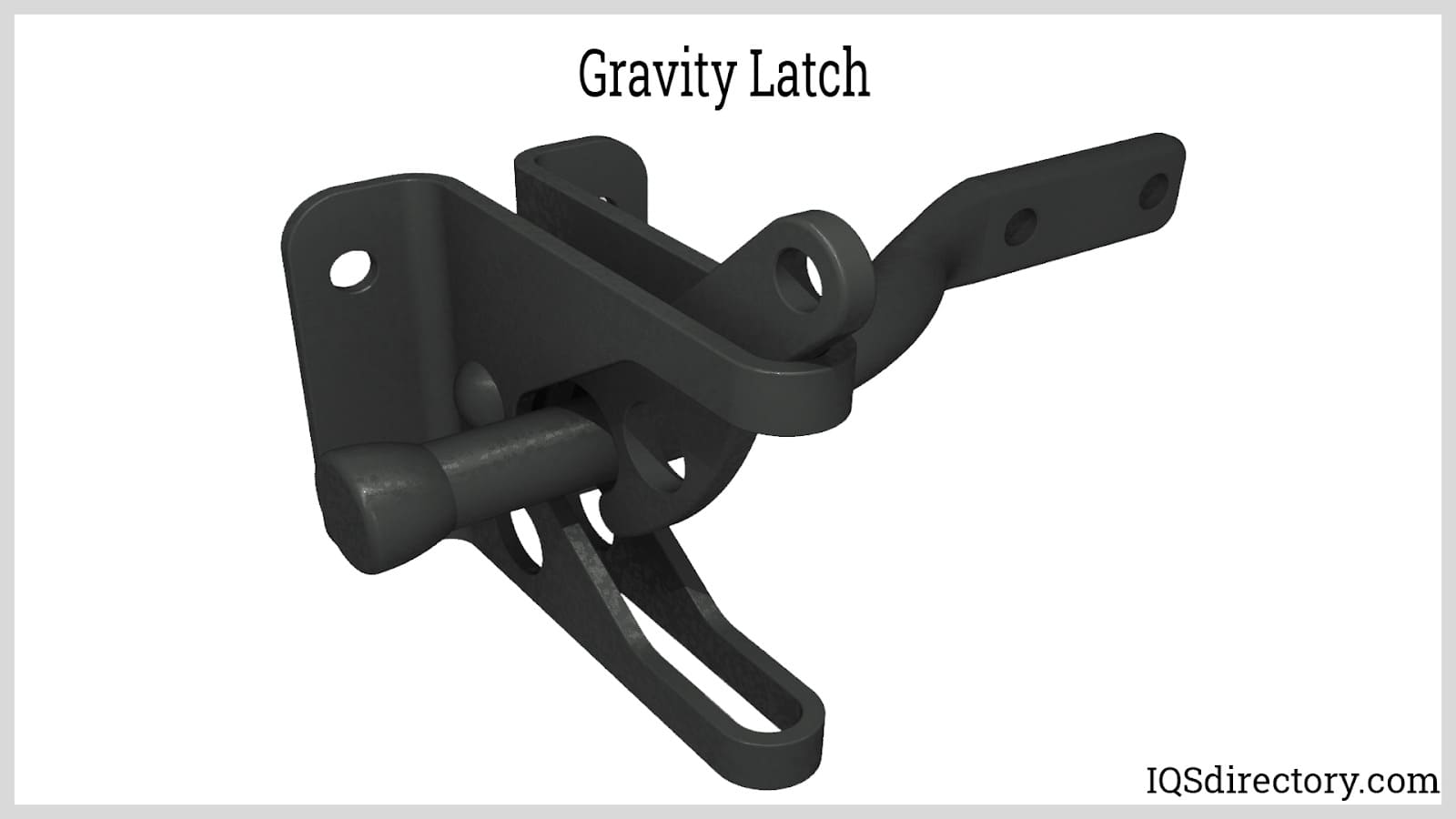
A door latch is a mechanical fastener that connects two surfaces or objects and provides a secure, safe, and strong connection. The latch portion of the mechanism is mounted on a flat surface such that when it meets a...
Please fill out the following form to submit a Request for Quote to any of the following companies listed on Gas Springs .
This article will give an in-depth discussion about Gas Springs.
The article will bring more understanding about:
A gas spring is a hydro-pneumatic device that stores potential energy by compressing gas inside a sealed cylinder. This operation is regulated by a moving piston.
Unlike conventional springs, gas springs do not rely on elastic deformation to function. These springs operate as a completely self-contained unit that requires no additional gas once it has been filled with inert nitrogen during assembly.
No matter the position of the gas spring, the pressure around the piston is consistently uniform, due to the rod’s small cross-sectional area. The force (F) exerted by a gas spring is determined by the pressure differential (P) between internal and external pressures, applied to the rod's cross-sectional area (A). In high-pressure environments, the pressure difference ΔP must be carefully managed.
Gas springs can be examined under different circumstances as follows:
This indicates the maximum range of motion of the rod, ranging from its fully retracted point to its fully extended point.
This term denotes the total length of the gas spring, measured from the midpoint of one end fitting to the midpoint of the opposite end fitting.
This measurement refers to the fully closed length, spanning from the center of one end fitting to the center of the adjacent end fitting. If no end fittings are specified, it pertains to the length from the rod end to the tube end.
This segment of the tube is equipped with grooves to securely hold the guide and seal assembly. Its role is to shield the seal package from damage during piston extension.
In various sectors and applications, gas springs are alternatively known as gas props, gas struts, or gas lifts. These elements are frequently utilized to support or balance mobile loads. The phrase "nitrogen gas springs" is also applied, as nitrogen is the typical gas used in these springs. Nitrogen is chosen for its non-reactive and non-combustible properties, preventing reactions within the internal components.
Gas struts usually feature in vehicle suspensions, incorporating a coil spring to sustain the vehicle's weight and a shock absorber to cushion and dampen shocks and vibrations. A push or pull force is exerted by the pressure applied to the spring. The gas strut not only supports the vehicle but also absorbs impacts from uneven surfaces and assists in wheel turning.
Gas springs that include damping functions are often referred to as gas dampers or gas shocks, depending on their industry and application. These gas shocks support dynamic loads while controlling the system's motion.
Dampers, or "shocks," utilize viscous friction for motion control. They typically function alongside an external spring or with movable parts like panels and doors. The damper produces a force counteracting movement, directly proportional to the velocity of the moving object.
The primary difference between gas springs and coil springs is their method of compression. Coil springs store energy through mechanical deformation, whereas gas springs utilize pressurized gas. Coil springs are often favored for their economical cost, adjustability, faster rebound, and lack of concerns about leaks or seal failures. Conversely, gas springs provide smooth and quiet operation due to their internal pressure mechanism.
With gas springs, force increases exponentially as they are compressed, requiring less initial force to compress them. As the gas spring nears the end of its stroke, the compression force needed rises. In applications requiring multiple springs, gas springs are advantageous over coil springs as fewer gas springs can accomplish the same tasks as multiple coil springs. Since coil springs are mechanical systems, they do not operate with the same smoothness and generate noise.
Gas springs deliver stronger force and require a shorter stroke compared to coil springs, making them more effective for specific applications. Known for their reliability, high performance, and safety, gas springs provide a lifting force at a more controlled speed, requiring fewer units to achieve equivalent results.
The operation of a gas spring, also called a gas strut or gas shock absorber, relies on compressed nitrogen gas acting as an elastic energy storage medium inside a sealed cylinder. This design leverages a 50% mixture of specialized hydraulic oils, such as transformer oil and turbine oil, which play pivotal roles in internal sealing, lubrication, and the smooth transmission of mechanical force. As the piston rod is pushed into the cylinder during compression, the enclosed gas volume decreases, causing a proportional increase in internal pressure in accordance with Boyle’s Law (pressure-volume relationship). The result: the force output by the gas spring grows and peaks when the rod is fully compressed, providing consistent, reliable motion control in applications like automotive tailgates, industrial machinery, and ergonomic furniture.
Referring to the diagram above, as the piston transitions from the fully extended position (P1) to the fully compressed position (P2), the internal gas pressure (solid line) increases while the cylinder volume (dashed line) decreases, illustrating the core thermodynamic behavior of gas springs compared to traditional coil springs.
A critical performance parameter in gas spring design is the K-factor, also known as gas spring progression rate. This metric represents the percentage change in generated force between the unloaded (P1) and the fully loaded (P2) positions. Generally, quality gas springs feature a very low K-factor—ranging from 1.05 to 1.8—compared to mechanical compression springs, ensuring steadier force output. Because gas springs are charged to the required force at P1, they offer immediate and consistent lifting or damping capabilities for demanding load management applications. When calculating required gas spring force, always use the force at P1 as your baseline. In related calculations: F represents spring force (in newtons), k is the spring constant (N/mm), and X is the deflection or stroke distance (in millimeters).
In addition to lubricating essential moving parts—such as the piston, internal seals, and piston rod—the oil contained in a gas spring contributes significantly to damping control. Proper damping ensures that as the gas spring nears its full extension, motion slows gently, minimizing the risk of damage, noise, or operator injury. The damping process is regulated by controlling how the gas and hydraulic oil flow through the piston assembly, often via specialized orifices or shims.
Optimal damping is achieved when the piston approaches the oil column near the maximum extension point, especially when the gas spring is installed in a rod-down orientation—a mounting strategy preferred for maximizing lifespan and consistent operation. Many industrial gas springs and OEM replacement shocks are engineered with adjustable or self-regulating damping to accommodate varying load weights and motion profiles.
Key factors influencing damping characteristics include:
Operating temperature directly affects both force output and damping characteristics of a gas spring. As temperatures rise, the pressure inside the cylinder climbs, while oil viscosity decreases—this combination accelerates extension speed but diminishes damping effect. Conversely, at lower temperatures, spring force lowers as viscosity increases, causing a slower extension with enhanced shock absorption. Selecting temperature-rated gas springs or models designed for harsh environments is essential for reliability in automotive, aerospace, and manufacturing settings.
Viscosity—defined as a fluid's resistance to flow and shear—plays a substantial role in energy absorption and velocity control. Higher oil viscosity generates greater resistance, increasing damping and providing smoother, safer deceleration of the spring’s movement. When ambient or operating temperatures increase, viscosity falls, reducing damping efficiency. Specifying the correct hydraulic fluid is critical for applications requiring precise speed control or consistent gas strut performance.
The volume of oil inside the gas spring directly impacts when and how forcefully the damping zone is engaged. Higher oil volumes cause the spring to enter the slow, controlled damping phase earlier in its extension, providing greater motion restraint—especially important in heavy-duty or safety-critical applications.
The pour point of the oil is the lowest temperature at which it remains pourable and fluid. When oil falls below this threshold and becomes semi-solid, flow ceases, disabling damping and preventing the gas spring from reaching its full stroke. To avoid operational failure, ensure oil specifications align with expected environmental conditions.
Metering in gas springs refers to regulating the extension and compression speed by altering the size of the piston’s orifices or incorporating restrictive flow channels. By precisely controlling these flow paths, a pressure drop is induced across the piston, which governs the speed at which the gas strut extends or retracts. For rapid movement, larger orifices reduce flow restriction, increasing extension speed; for controlled, gentle motion, smaller orifices enhance resistance, slowing the cycle.
Breakaway friction is another notable consideration in gas spring application. After extended periods of inactivity, friction between the seals, piston rod, and cylinder walls can increase as lubrication migrates and seals conform to micro-imperfections. The first movement after rest requires additional force, which is important to factor into design and selection for precision automotive hoods, medical equipment, or motion control systems.
Safe use of gas springs is paramount due to the risks posed by high-pressure containment. Always adhere to these critical guidelines to prevent gas spring malfunction, product failure, or safety hazards:
Following these gas spring safety best practices ensures equipment longevity, optimum performance, and user safety in various industrial, commercial, and automotive applications.
To ensure reliable performance and long service life, always consult your gas spring manufacturer’s documentation for specific recommendations, allowable mounting orientations, and preventive maintenance schedules.
Looking for OEM gas strut solutions, customized industrial gas springs, or Aftermarket gas shock absorbers? Browse our curated selection of industry leaders specializing in advanced force technology, precision engineering, and tailored support for a wide range of market sectors—including automotive, heavy equipment, and ergonomic hardware. Choose the right gas spring supplier to ensure the best balance of high-performance force management, durability, and cost-effectiveness for your application.
Gas springs, or gas struts, are precision-engineered mechanical devices that utilize pressurized gas to provide controlled motion, damping, and load support in a wide range of industrial, automotive, aerospace, medical, and furniture applications. Selecting and designing a gas spring requires careful evaluation of its internal components, material options, pressure ratings, and application-specific requirements to ensure optimal safety, durability, and performance. The diagram below illustrates the essential gas spring components that must be assessed during the design process.
The gas spring rod is a vital part responsible for guiding the piston and transferring force. Three primary types of gas spring rods are commonly used in industry: polished carbon steel, precision-ground steel, and corrosion-resistant stainless steel. Surface treatments—such as salt bath nitriding, chrome plating, or advanced black nitriding—increase rod longevity and enhance durability in harsh operational environments. When selecting the rod, consider factors like stroke length, operating cycles, and exposure to corrosive agents. The rod’s length always exceeds the spring stroke to ensure adequate extension, but remains shorter than the total tube length to prevent overtravel and potential system failure.
Different surface treatments offer varied compliance and performance advantages. Chrome-plated rods, for example, are often scrutinized for environmental and chemical compliance due to the use of chromium, which may not meet certain industry regulations. In contrast, black nitride rods provide a smoother surface and a corrosion resistance rating equivalent to or better than chromium-plated rods, while also satisfying environmental standards.
Nitrotec surface treatment is widely recognized among manufacturers for its exceptional performance and eco-friendly attributes. This protective process delivers the following benefits for gas spring rods:
The gas spring tube is typically manufactured from high-strength carbon steel, powder-coated steel, or stainless steel, each capable of withstanding elevated internal pressures essential for high-load or heavy-duty gas springs. Key criteria influencing tube selection include tensile strength, wall thickness, burst pressure, and internal surface finish. A properly finished internal surface reduces seal wear and increases cycle life, which is essential for applications such as vehicle hoods, machinery covers, and ergonomic furniture. In corrosive or outdoor environments, choosing a stainless steel gas spring tube improves reliability and service life.
The guide and seal package serves as both a rod bearing surface and a gas tight sealing interface, minimizing friction and preventing nitrogen leakage or contaminant entry. High-performance plastic composites are frequently used for guides due to their self-lubricating properties, while zinc or brass guide options are specified for heavy-duty or custom gas springs. The incorporation of bearing sleeves further optimizes smooth articulation and reduces wear on the rod surface. Seals are predominantly constructed of durable rubber or advanced elastomeric materials, chosen for their chemical resistance and ability to withstand repeated pressure cycling without failure.
The piston assembly, typically manufactured from zinc, lightweight aluminum, or robust plastic polymers, is engineered to control the flow of pressurized nitrogen between the two sides of the gas spring. This regulates the gas spring’s damping characteristics, impacting the rate of extension and compression, response speed, and load-bearing capacity. A secure piston-to-rod connection is critical for mechanical safety, ensuring the rod remains properly retained and preventing potential ejection during high-pressure operation or accidental overloads.
The end plug functions as a pressure seal at the tube end and doubles as a mounting point, securing various end fittings such as eyelets, clevis brackets, or threaded studs. Its design must withstand not only internal gas pressure, but also the tensile loads generated throughout the gas spring’s duty cycle. For custom gas spring solutions, end plug options should be matched to the mounting requirements of the application.
Industrial gas springs are exclusively filled with nitrogen gas because of its inert, stable, and non-flammable nature. Nitrogen maintains precise pressure levels over time—critical for applications where consistent extension force, load support, and motion control are required. Choosing the correct charge pressure is central in gas spring sizing; consider load specifications, ambient temperature variations, and safety margins. Proper nitrogen filling ensures no reactive chemical by-products form within the spring, providing long-term reliability and minimizing internal corrosion risks.
Additional Key Gas Spring Design Considerations
By carefully evaluating these gas spring design factors, engineers and buyers can select or specify the ideal product for their application, reducing field failures, maintenance costs, and downtime. For more guidance on custom gas spring solutions, consult with an experienced manufacturer or request technical data sheets relevant to your use case.
The following outlines the different types of gas springs:
This gas spring type includes a rod connected to a piston inside a sealed cylinder. The cylinder is charged with high-pressure nitrogen, which creates significant force. These gas springs are known for their reliability and compact design, making them ideal for various lifting and counterbalancing tasks.
These gas springs allow the piston rod to be locked at any position along its stroke. The locking mechanism is activated by a plunger connected to the piston rod. When the plunger is pressed, the rod functions as a compression gas spring. Releasing the plunger locks the rod in place at the chosen position. Key components of locking gas springs include the piston rod, cylinder, piston valve, guide, and seals, among others.
These gas springs are tailored for specific applications and are suited for a range of industrial uses. They come in various materials, including EPDM, polyurethane, Viton, and others, to meet different requirements.
These gas springs feature an extra shroud mechanism encircling the rod. This mechanism locks the gas spring in place when it is fully extended.
Tension and traction gas springs apply some force or maintain the tension that helps to provide tension on the belt drive and mechanical assemblies. These springs operate in a way that is directly opposite to the way that compression gas springs operate. The springs come in a variety of sizes and stroke ranges, which aid in determining its force range and k factor. These types of springs are manufactured from stainless steel. They control the pulling and adjustment as per requirement.
These gas springs are ideal for use in corrosive environments and are available in various types, including compression and locking springs. Unlike micro gas springs, all stainless-steel gas springs are equipped with a release valve. This valve assists in the operation by releasing gas once the desired force is achieved.
These gas springs are designed to control the speed and motion of the spring using hydraulic oil. They are commonly used in applications where movement is directed, such as with doors, lids, and covers. They offer a load capacity ranging from 10 to 150 lbs and come with various speed characteristics to suit different application needs.
This chapter will explore the advantages and uses of gas springs.
Gas springs offer numerous advantages, including: a high force range up to 12000N, diverse designs and sizes, unlimited cycle lifespan, no need for external power sources, the capability for opening angles greater than 90 degrees, silent operation, and relatively low cost. Here are additional details on the benefits of gas springs:
Gas springs require minimal maintenance compared to traditional coil springs. Consisting of components like pistons, seals, and fittings enclosed within a cylinder, they need no cleaning, oiling, or lubrication. Their self-contained design simplifies maintenance, as there are no external parts to manage.
Gas springs are designed for durability, often outlasting other types of springs. Unlike coiled metal springs that rely on mechanical operation, gas springs are protected by a gas-filled cylinder, which reduces wear and tear. They offer approximately 100,000 strokes and have a longer lifespan, making them a cost-effective choice as they do not need frequent replacement.
Many gas springs come with a locking feature. While some gas springs are non-locking, you can select models that offer locking capabilities. This feature provides an advantage over traditional springs by allowing precise positioning and stability.
Gas springs offer ergonomic benefits by providing smooth and controlled action under compressive force. The piston retracts smoothly into the cylinder, making them suitable for applications like office chairs and other furniture where ergonomic design is crucial.
Gas springs come with a variety of mounting options, including ball and socket, rod end, clevis, eyelet, threaded, tapered end, and bumper or rod end unattached.
Gas springs are used in various applications, including:
This chapter will cover factors to consider when selecting gas springs and the key points for their installation.
When selecting a gas spring, the following factors should be considered:
Several key performance specifications must be evaluated when selecting a gas spring, including compressed length, absorber stroke, extended length, maximum force (P1), and maximum cycles per minute.
When selecting a gas spring, it is important to consider the following physical specifications:
This specifies the desired diameter of the housing cylinder.
This specifies the desired diameter of the extending rod.
The available mounting options include:
This mounting uses a spherical bearing that allows for multi-axis rotation. It features a ball end with an integral threaded stud.
These involve mating fork mounts.
The cylinder side has a tapered end that fits snugly into a corresponding tapered mounting hole.
This option includes standard threads at the ends for mounting or attaching accessories.
Here, the rod and load are not directly attached, but the rod has a bumper at the end to engage with the moving load.
This refers to the material used to manufacture the gas spring. Common materials include aluminum, steel, stainless steel, and thermoplastic. For applications near saltwater or in food and medical environments, materials with rust-inhibiting properties or UV coatings may be chosen.
It is crucial to know the weight and dimensions of the object being moved. A spring scale can be used to measure the weight for optimal results.
The gas spring's range of motion should not be restricted, so the body must fit properly within the assembly.
This indicates the temperature range within which the gas spring can function effectively.
Understanding the load's geometry and weight is essential for determining the appropriate mounting position, required counter-balancing force, and potential compromises. Mounting the gas spring with its center of gravity close to the pivot point helps in predicting its operation more accurately.
The longevity of a gas spring depends on proper lubrication of its seals. For optimal performance, the spring should be installed with the rod facing downward (refer to figure 2.1 below) or with the rod guide positioned lower relative to the cylinder attachment.
In applications such as car boots, the spring may pivot between the fully open and closed positions during the opening process. It is crucial to install the spring with its rod facing downward when fully compressed inside the cylinder (see figure 2.1 below).
This orientation is recommended because it aids in proper lubrication of the guide and seals while ensuring effective braking. The rod surface maintains gas pressure and should be protected from damage caused by blunt or abrasive objects and corrosive chemicals.
When installing the spring, avoid placing strain on the seal by ensuring proper alignment of the lower and upper fittings. Maintaining this alignment throughout the stroke is essential. Jointed fittings that allow for alignment adjustments can be used. Rigid attachments may transmit vibrations to the seals, so it is important to leave a small gap between the fixing screws and the attachments and to use at least one jointed attachment for fixing the spring. Smooth pins are preferred over threaded bolts to prevent thread crest damage.
Ensure that the thrust force of the gas spring exceeds the pulling forces to prevent exceeding the normal rod sliding speed. The recommended operating temperature range is -30°C to +80°C. In damp or cold environments, frost on the seals may affect the gas spring’s performance and longevity.
Gas springs are designed to assist with lifting or counterbalancing heavy loads for either the operator or the structure they are installed in. Any other usage requires a careful assessment by the designer or manufacturer to ensure safety and durability.
Side loads on the spring or rod are a primary cause of gas spring failure. It is crucial to avoid any side contact with the gas spring, as even minor contact can lead to premature failure. Sometimes, users might intentionally apply force to the side of the gas spring to support another mechanism, which can result in early spring failure.
Twisting forces should also be avoided on the end connector of a gas spring. To prevent twisting failure, a ball and socket connector is used to eliminate any torque on the connector.
Gas springs have a diversity of benefits over other types of springs due to their design and manufacture. They can be used in many applications including office furniture and industrial equipment. To choose the right gas spring for a particular application, one must know the specifications of the gas spring. Gas springs are long lasting as long as they are used under the correct specified conditions.
A door latch is a mechanical fastener that connects two surfaces or objects and provides a secure, safe, and strong connection. The latch portion of the mechanism is mounted on a flat surface such that when it meets a...
A gate latch is a locking mechanism that is used to secure gates on fences or stakes on truck beds using a metal bar and lever that is raised to open the latch and lowered to close it. Although they do not have...
Latches are mechanical components that allow the temporary joining of parts that are moving relative to each other. They are actuated to release the coupling and allow the two parts to separate. Latches are mostly seen on doors and enclosure...
A lock is a mechanism designed to connect an opening to its frame using a latch, solid cylinder, bolt, or some other form of a solid metal plunger that extends into the strike. They are metal devices that prevent entry or access for privacy, security, or...
A magnetic door latch is a type of latch that consists of a striking pad and a magnet and is used to keep doors and gates closed. Magnetic door latches are also known as magnetic door stops, magnetic door catches, and door magnets...
A rotary latch is a locking mechanism that secures openings such as doors, enclosures, cabinets, and panels so that they are locked and unable to accidentally open. They are referred to as slam latches since...
Rubber latches are latches made of rubber or are composed of rubber components. They are used in the automotive, aerospace, and medical equipment industries due to their flexibility, durability, and non-abrasive properties...
A spring latch is a mechanical device that is utilized in the joining of two separate components in order to prevent movement or opening. A spring latch is locked with a spring compression so that it will not be released...
A vibration absorber is a single degree of freedom (DOF) spring-mass system that eliminates or reduces the vibration of a harmonically excited system such as the rotation of engines, motors, generators, belts, etc...