Gasket Materials
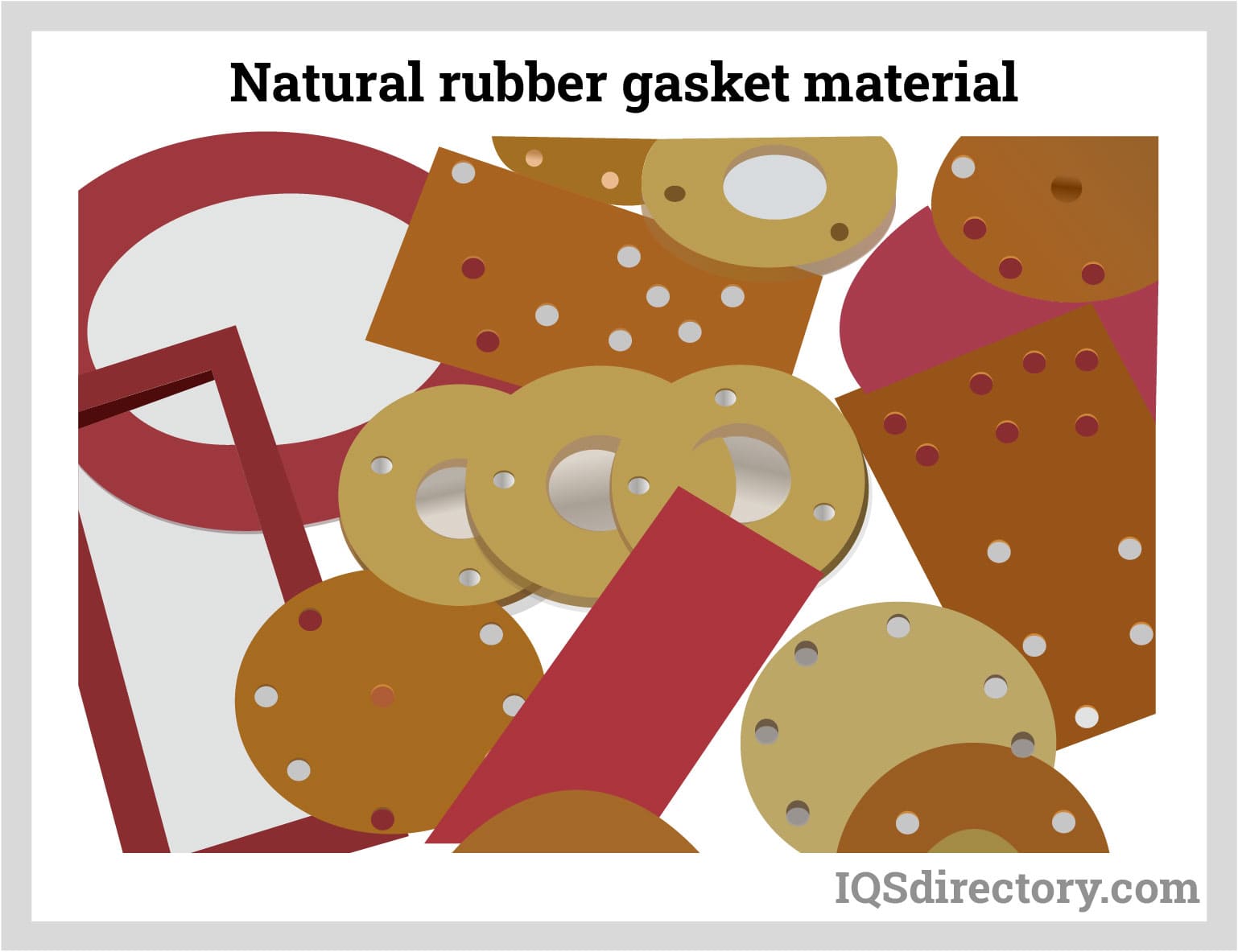
Gaskets are seals that are mechanically made to prevent either process fluids from escaping or contaminants from entering the delicate areas. Each given system has its best suited gasket, and it is critical to make the right...
Please fill out the following form to submit a Request for Quote to any of the following companies listed on
This article presents information about the various categories, properties, and applications of gaskets. Read further to learn more about:
Gaskets function as mechanical seals, specifically crafted to block leaks by filling voids present between fixed mating surfaces. Both finely polished and rough surfaces, particularly metal ones, possess inherent roughness or microscopic protrusions that can result in gaps through which liquids may escape. When subjected to compression, the gasket conforms to the surface profile, sealing these gaps effectively by matching the peaks and valleys of the surface.
Gaskets find extensive use across numerous industries involving both pressurized and unpressurized fluids and gases. They are frequently utilized in equipment that contains fluids, including pipes, tanks, heat exchangers, and combustion engines. Gaskets are available in various forms and are rated to meet the distinct needs of each application.
Gaskets and O-rings serve as sealing elements in mechanical and engineering setups to prevent leaks of fluids or gases. While their function is similar, they differ in design, shape, and applications. Here are the primary contrasts between gaskets and O-rings:
Gaskets and seals are crucial in curbing leaks in mechanical systems like engines, pipelines, and containers, but they are not indistinguishable.
Specifically, a gasket is a mechanical component crafted from materials like rubber, metal, or composites, designed to fill the voids between two mating interfaces, thereby forming a secure seal under compression. Gaskets ordinarily find use in static settings where the mated parts undergo minimal movement.
Conversely, a seal is a broader category that includes varied sealing instruments, such as gaskets, O-rings, and lip seals. Seals may be dynamic, suitable for situations with relative movement between paired components, such as those found in hydraulic cylinders or rotating shafts.
While both gaskets and seals are vital for thwarting leaks, they differ in design, function, and the kinds of applications they are best suited for.
Seals, O-rings, and gaskets all serve as mechanical sealing components engineered to prevent fluid or gas leakage across various applications. Although their primary function of sealing is mutual, they exhibit distinct differences in design, shape, and specific uses. Below are the commonalities and contrasts among them:
Gasket manufacturing involves a range of techniques and processes, including cutting, die pressing, and punching. The method selected depends on the material being used and the desired strength and application of the final product. Regardless of the technique, the process always starts with selecting the appropriate material, which is essential for the gasket's performance.
Rotary die cutting utilizes a cylindrical die mounted on a rotary press to cut and shape non-metallic materials. In this process, the material is fed into the cutting station where it interacts with both an anvil cylinder and the rotary die. The anvil and cylinder die move in opposite directions along their horizontal axis. As the cylinder die presses against the anvil, it cuts out the gaskets. This method is efficient for producing large volumes of gaskets with uniform shapes.
Kiss cutting employs a rotary cylinder to cut gaskets from non-metallic materials, similar to rotary die cutting. However, in kiss cutting, the die only partially cuts through the material, leaving a backing layer intact. This backing, which can be made of adhesive material, helps ensure more secure installation of the gasket.
Press die cutting is a widely used method for producing gaskets, particularly for metal and other rigid non-metallic materials. This technique involves a traditional press where the die is mounted on the ram, which then lowers onto the material to cut out the gasket. The force needed varies based on the material being processed. Presses used in this method can be hydraulic, pneumatic, or electrical, with manual operations providing more precise cuts.
Flatbed die cutting is a more straightforward method compared to press die cutting. It features a stationary flat base with a movable head that traverses across the material. The cutting die consists of steel rule strips, which are shaped to form the gasket. These dies are supported by a foam surface that compresses during cutting but shields the sharp steel strips when not in use. This process is particularly well-suited for short production runs due to its simplicity.
Knifeless cutting employs a blade to shape the gasket and is driven by a computer numeric control (CNC) system. This process uses computer-aided design (CAD) to program the dimensions of the gasket, which are then fed into the CNC machine to execute the cut.
Waterjet cutting, although slower than die cutting, does not require traditional tools like dies. This technique uses pressurized water to cut through the material, generating minimal waste and no fumes. The only byproduct is a light mist of water, making waterjet cutting a popular choice for its environmental benefits.
Laser cutting achieves extremely precise gasket tolerances of ±0.0005. Various lasers, including CO2 and ultraviolet types, are used in this process. With ongoing advancements and the introduction of new designs, laser cutting has become the preferred method for producing custom gaskets. Like knifeless and waterjet cutting, it relies on CAD designs that are programmed into CNC machines.
Compression molding involves the use of a heated mold where the gasket material is placed in the heated mold and compressed. The compressed material is allowed to cure prior to being released from the mold. It is the perfect process for short low production runs and less intricate gaskets. The process of compression molding is ideal for manufacturers with limited space since the compression mold equipment has a small footprint. The compression molding process is ideal for the fabrication of flexible rubber materials.
Several factors must be considered in the rubber-to-metal bonding process before manufacturing the gasket. One key factor is the type of metal used, which is typically steel but can also be aluminum. This bonding procedure is a sophisticated chemical process that involves the interaction between the metal and the rubber.
The process begins with treating the metal gasket either mechanically or chemically to prepare its surface for the application of the rubber compound.
Its surface is then prepared for the rubber compound application. The bonding mixture comprises a precisely measured blend of bonding agent and solvent, which can be applied to the metal surface by dipping or spraying.
To achieve a secure bond, the metal-rubber gasket is compressed. This step is crucial to prevent any potential detachment or peeling of the rubber from the metal.
Material and form are critical specifications for gaskets, as they determine the gasket's resistance to corrosive environments, extreme temperatures and pressures, mechanical stresses from mating surfaces, and dynamic operational conditions. Based on the material and design, gaskets are categorized into non-metallic, semi-metallic, and metallic types.
Non-metallic gaskets are generally employed for applications with low to moderate fluid pressures. They can handle a wide range of temperatures, depending on the material used. These gaskets are easily produced and supplied as sheets, which can be shaped through die-cutting, kiss cutting, or die pressing. This flexibility means suppliers don’t need to stock various forms, as gaskets can be customized to fit specific requirements.
Key advantages of non-metallic gaskets include their ease of compression and effective sealing with minimal torque. Their adaptability allows them to conform to the specific shape of the application they are intended to seal.
Non-metallic gaskets are made from uniform materials such as flexible graphite sheets, virgin PTFE, or composite fibers and granules embedded in an elastomeric resin. Advances in technology are leading to the development of new, proprietary materials by manufacturers. Examples of common non-metallic gaskets include:
Among the various non-metallic gasket materials, PTFE is the most commonly utilized due to its advantageous properties: it boasts a high melting point, is hydrophobic, chemically inert, features a low friction coefficient, and exhibits remarkable flexural strength. PTFE is particularly valued in chemical processing for its high bonding energy, which provides excellent resistance to chemical reactions and corrosion. However, PTFE can be degraded by fluorinating agents, magnesium, and molten alkali metals.
While PTFE is inherently strong, its mechanical properties are often enhanced by incorporating various fillers. These fillers, which can include glass fibers, carbon, bronze, graphite, and molybdenum sulfide, improve PTFE’s wear resistance, deformation strength, electrical characteristics, thermal conductivity, and friction coefficient.
In addition to its superior chemical resistance, PTFE also offers excellent insulating properties, toughness, and impact resistance. The primary forms of PTFE include virgin PTFE, filled PTFE, biaxially oriented PTFE, and expanded PTFE.
Plastics are cost-effective, versatile materials created from a diverse array of plastic compounds. They are characterized by their lightweight nature, low friction, and effective sealing and insulation properties. Plastics offer high durability and can endure a wide range of temperatures, making them a viable alternative to metal gaskets.
In addition to PTFE, gaskets can be made from various plastics such as ABS, Acetal, Nylon, different types of polyethylene, and polypropylene. The extensive range of plastics available allows for selecting the most suitable material based on sealability, pressure ratings, and temperature requirements for specific applications.
Plastics are generally categorized into two main types: thermoplastics and thermosetting polymers. These categories are distinguished by their production processes and the properties they exhibit, which are influenced by the methods and materials used in their manufacture.
Flexible graphite gaskets are produced by expanding graphite flakes through a combination of intercalation, heating, and compression processes. First, high-quality graphite flakes are treated with acids like nitric, phosphoric, and sulfuric. This treatment generates graphite intercalation compounds, which expand significantly upon heating. During exfoliation, the graphite expands extensively as the intercalated compounds vaporize, creating gas pockets. The result is worm-like or vermiform structures with highly active, rough surfaces. These structures interlock mechanically when compressed, forming a flexible graphite sheet. Although flexible graphite gaskets generally have lower tensile strength compared to other non-metallic options, their strength can be enhanced by incorporating reinforcements, laminates, and inserts.
Typically, flexible graphite gaskets include fillers such as foils or tangs, often made of stainless steel, although other materials may also be used.
Phyllosilicates are a group of minerals from the mica family used to make non-oxidizing, high-temperature gasket materials. As non-oxidizing properties, they solve the problem with graphite gaskets, which is their tendency to oxidize, or “coke,” at high temperatures in environments containing oxygen or other oxidizing agents.
The primary phyllosilicates used in gasket production are mica and vermiculite, both of which offer similar temperature and chemical resistance properties. Mica gaskets are created from sheets made by combining mica mineral with a polymer and subjecting them to high heat. Vermiculite, a form of expandable mica, is produced by the flash conversion of water molecules between the layers of its crystal structure.
Mica exhibits excellent resistance to temperatures exceeding 900°F (482°C), where flexible graphite is not suitable. As a gasket material, mica is effective in high-temperature applications and remains stable in the presence of oxygen. It is available in various forms, including laminated, flexible, or rigid, and can be tanged with stainless steel to handle higher pressures. Additionally, mica can be combined with polymers through heat treatment to enhance its flexibility, addressing its otherwise poor sealability.
Vermiculite gaskets offer exceptional heat and chemical resistance, capable of withstanding temperatures up to 1832°F (1000°C). When tanged with stainless steel, vermiculite gaskets can endure pressures of up to 740 psi while maintaining excellent sealability. The superior strength of vermiculite allows it to survive oxidation conditions that would compromise graphite and other gasket materials. Due to its thermal insulation properties, vermiculite gaskets are used in exhaust gas recirculation (EGR) systems where blocking heat flow is essential.
Elastomers are polymers characterized by their highly elastic properties, formed by cross-linking long polymer chains into amorphous structures. The weak intermolecular forces between these polymer chains allow them to be reconfigured when stress is applied. This elasticity enables elastomer gaskets to easily conform to the surface profiles, ensuring a tight seal.
There is a broad selection of elastomers available to meet various requirements, although their chemical and temperature resistance tends to be less than that of PTFE. Depending on the type of curing reaction or vulcanization, elastomers may degrade when exposed to water, ultraviolet light, oils, and certain solvents. High temperatures can cause elastomers to expand and melt, while low temperatures can render them brittle. Common elastomers used in gasket manufacturing include nitrile (NBR), ethylene propylene diene monomer (EPDM), neoprene, silicone, and fluoroelastomer (FKM).
Extruded rubber gaskets are flexible, lightweight, long-lasting, and exceptionally durable. They are made to endure hostile, harsh, and extreme environments, such as applications that involve exposure to chemicals or extremely high temperatures. Extruded rubber gaskets are manufactured using the extrusion process, where the softened rubber is forced through a die and comes in hollow sections, cord shapes, and squares. The properties of hollow cross-sections have exceptional sealing compression.
Extruded gaskets are used in a wide range of applications, such as sunroofs, garage doors, windows, windshields, and boat hatches. Their tensile and sealing strength helps to block noise and protect against moisture and extreme weather conditions. The extrusion process, known for its cost-effectiveness and ability to produce high-quality products, is commonly employed in the manufacture of gaskets.
This type of gasket is made from naturally occurring mineral or synthetic polymer fibers. Asbestos gaskets, one of the earliest forms of compressed fiber gaskets, were used in industrial applications. Asbestos, a naturally occurring silicate mineral with long, thin fibrous crystals, is now being phased out due to health risks such as asbestosis and cancer. Alternatives to asbestos include carbon, graphite, glass, aramid, and other fibers.
Compressed fiber gaskets are made using a process known as beater addition, which is often proprietary. During this process, minerals are beaten to fibrillate the main fibers into tiny fibrils. This spreading of the fibers allows elastomer resins to be added, which bind the fibers together. Common elastomers used in this process include styrene-butadiene rubber (SBR), NBR, neoprene, and EPDM.
Cork is suitable for low-temperature and low-pressure applications. Gaskets are made by compressing granulated cork bark and binding it with an elastomer resin. Cork gaskets are lightweight, flexible, and resistant to water, oil, and other petrochemicals.
Poron Gaskets: Poron is a patented gasket material made from multicellular polyurethane. Its porous structure makes it well suited for thermal insulation, vibration dampening, acoustic dampening, and shock absorption. Polyurethane's inherent resilience and rebound properties make it suitable for sealing because of its reduced creep relaxation.
These gaskets are composites of metallic and non-metallic materials. The metallic component provides structural strength and increased toughness, while the non-metallic part enhances sealing. The various combinations of metal and non-metal components, along with different available styles, make semi-metallic gaskets suitable for almost every condition. However, semi-metallic gaskets are supplied in specific sizes and shapes and cannot be cut and shaped like non-metallic gaskets. They must be dimensionally compatible with the mating surfaces, usually flange faces for piping. The different types of semi-metallic gaskets are as follows.
This type of semi-metallic gasket consists of V-shaped metal strips wound alternately with a filler material. The gasket is supported by an inner and outer ring. The inner ring, which is in contact with the process liquid, has higher material requirements compared to the outer ring, which is typically made of carbon steel. Generally, the inner ring and metal windings are made from stainless steel, while the filler material can be PTFE, non-asbestos fibers, or graphite.
This type features a filler material that is partially or entirely enclosed within a metal jacket. Various forms and configurations are available, including single, double, and corrugated jackets. Sealing is achieved through the deformation of the metal overlap, which is thicker than the rest of the envelope. This thicker section handles most of the compressive load, ensuring a reliable seal.
Corrugated metal gaskets consist of a thin metal ring with a wave or corrugated pattern and are coated with a soft layer of non-metallic material, such as graphite, PTFE, or ceramic. These gaskets work by allowing the soft layer to conform to surface irregularities. They are particularly suited for uneven flanges or flanges with surface imperfections.
CMG gaskets are designed for specialty flanges and are not intended for use with piping. Their applications are somewhat limited, so careful consideration is needed when choosing them for a particular use. The optimal applications for CMG gaskets are in heat exchangers and expansion joints within petrochemical industries, where they offer resistance to radical shearing and provide slight compressibility and recovery.
This type of semi-metallic gasket features a grooved metal ring covered with a non-metallic facing material. Similar to corrugated gaskets, sealing occurs as the gasket is compressed, causing the soft material to conform to the flange surface. The grooves in the metal create concentric rings that apply additional pressure to the soft material, enhancing sealing performance and providing structural support. However, the facings on Camprofile gaskets are very thin, approximately 0.020 inches (0.50 mm), which limits their ability to conform to uneven flange surfaces. Consequently, these gaskets require flanges to be flat and free of surface irregularities for effective sealing.
Non-metallic gaskets and filler sealing materials fail under extremely high temperatures and pressures. In such cases, solid metallic gaskets are necessary. These gaskets are commonly used for sealing boilers and heat exchangers. Like semi-metallic gaskets, metallic gaskets come in standard shapes and sizes and must be dimensionally compatible with the mating surfaces. The primary types of metallic gaskets include ring-joint, flat metal, and grooved metal gaskets.
These gaskets feature thick cross-sections designed for high-temperature and high-pressure applications. They function by being tightly compressed between mating surfaces, which forces the metal into any surface imperfections and leak paths. The materials used for these gaskets are softer than the flange material. Examples of RTJ gasket materials include soft iron, low carbon steel, stainless steel, and special alloys such as Inconel and Hastelloy.
Unlike RTJ gaskets, this type of metal gasket features a thinner cross-section. These gaskets are cut from sheet metal, allowing them to be made to fit any surface shape and size. They function similarly to non-metallic gaskets but are more suitable for higher temperature applications. Additionally, they are intended for use only in applications with high bolt loads.
Grooved metal gaskets are similar to flat metal gaskets but feature serrations or grooves on their surface. The peaks of these concentric rings experience higher stresses when the gasket is loaded. Sealing is achieved by creating a labyrinth seal effect along the grooved surface. Grooved metal gaskets are often made from materials such as stainless steel or other alloys.
This type of gasket does not primarily rely on compression along the mating surfaces for sealing. Instead, it achieves sealing through a permanent welded connection between the surfaces. Welded gaskets are commonly made from materials such as stainless steel, carbon steel, or other metals that offer good resistance to corrosion and high-temperature conditions.
When selecting a gasket for an application, it is crucial to explore all the application parameters in detail to ensure the proper choice. To simplify this process and guide customer decisions, manufacturers have developed an acronym that represents the essential factors to consider: S.T.A.M.P., which stands for "Size, Temperature, Application, Media, and Pressure."
Choosing the right gasket for any application requires a thorough examination of various factors. To help streamline this process and assist customers in making informed decisions, manufacturers use the acronym S.T.A.M.P., which stands for "Size, Temperature, Application, Media, and Pressure." This acronym encapsulates the key considerations for selecting an appropriate gasket.
Temperature has a significant impact on both the mechanical and chemical properties of gaskets. Mechanically, two key effects are influenced by temperature: creep and relaxation. Creep refers to the gradual thinning of the gasket when exposed to a constant load, while relaxation denotes the reduction in compressive stress under continuous deformation. As temperatures rise, these issues become more pronounced, diminishing the gasket's sealing effectiveness. Chemically, high temperatures can adversely affect materials such as graphite and elastomer resins. Graphite gaskets may suffer from oxidation at elevated temperatures, which depletes the material and compromises sealing ability. Similarly, elastomer resins in full elastomer gaskets or as binders can undergo additional curing or vulcanization due to heat, leading to increased brittleness and reduced tensile strength. It is essential to review the pressure-temperature curves or maximum operating limits of gaskets before purchase to ensure they meet the requirements of the specific application.
Choosing the appropriate gasket size involves considering the specific application and the equipment it will be fitted into. The application type and the gasket's installation environment guide the selection process and influence the choice of materials for manufacturing the gasket.
The characteristics of the process fluid, such as pressure and temperature, play a crucial role, while environmental effects are less significant. The nature of the process fluid also affects gasket compatibility. Exposure to oxidizing agents, acids, alkalis, oils, water, and abrasive substances can deteriorate the material in contact with the fluid. Composites are often favored in such scenarios because they feature a highly chemical-resistant inner layer that withstands fluid attacks while preserving the sealing and structural integrity of the remaining components.
During normal operation, gaskets are subjected to three primary forces: the bolt or flange load, hydrostatic end force, and blowout force from internal pressure. The internal pressure within a vessel or pipe affects both hydrostatic and blowout forces. If these forces surpass the gasket's tensile strength, it may lead to rupture or leakage. It is essential that the gasket can withstand the maximum internal pressure, typically tested at 1.5 times the working pressure. Gaskets are often rated with pressure classifications or standards set by engineering organizations like ASME and DIN.
The thickness of gaskets typically doesn’t impact metal and semi-metallic types significantly, as these are manufactured to specific thicknesses based on their pressure ratings. However, for non-metallic gaskets, thickness plays a more critical role. Thicker non-metallic gaskets usually come with reduced pressure and temperature tolerances. To achieve effective sealing, these thicker gaskets require more compressive force. On the other hand, thinner non-metallic gaskets generally provide superior blowout resistance, reduced creep and relaxation, and enhanced compressive strength. Ideally, choosing the thinnest non-metallic gasket that can adequately conform to the flange surface is recommended for optimal performance.
Gaskets function as mechanical seals designed to bridge the gap between two surfaces to prevent leaks of fluids, gases, or other materials. They provide numerous advantages in a range of industrial and mechanical settings:
Gaskets find extensive use across various industries. Below are some typical applications and functions of gaskets:
In a system, safety mechanisms are intentionally designed to fail in the event of process abnormalities to protect other components. Gaskets, being one of the weakest points in the system, often fail first during overpressure situations in pipes or pressure vessels. Even with proper specifications, gaskets can still fail due to various reasons. The following are some of the most frequent causes of gasket failures:
Over Compression: Over compression can lead to permanent gasket failure. Signs of over-compression are bulging or extrusion of the gasket material, or inward buckling for spiral wound gaskets. Non-metallic gaskets are typically limited to 15,000 psi. Metallic gaskets are designed to be crushed at higher pressures up to 30,000 psi.
Sealing components are essential in mechanical engineering and fluid management, ensuring systems function efficiently and safely. Among the most widely used are gaskets and O-rings, both designed to prevent leaks but differing in design, application, and performance. Understanding these distinctions helps engineers select the right solution for their needs.
Gaskets create a seal between two mating surfaces, preventing leakage under compression. They come in various shapes, sizes, and materials tailored to different environments. Depending on the application, they can be made from rubber, cork, paper, silicone, metal, or composite materials, each offering unique resistance to temperature, pressure, and chemical exposure.
Typically flat, gaskets conform to the shape of the surfaces they seal. Common types include spiral-wound, ring-type joint (RTJ), sheet, and custom-cut gaskets. Industries such as automotive, plumbing, food processing, and heavy machinery rely on gaskets to seal engine components, pipe connections, and complex machinery parts.
O-rings are torus-shaped seals, commonly made from elastomers like nitrile rubber, silicone, or fluoroelastomers (e.g., Viton). These flexible seals work by compressing between two components, forming a tight barrier against leaks.
Their material selection depends on the operating conditions—Buna-N for petroleum applications, silicone for high-temperature environments, and fluoroelastomers for chemical resistance. With a circular cross-section, O-rings can seal in any direction, making them ideal for dynamic applications where movement or vibration occurs. Hydraulic and pneumatic systems, aerospace components, and consumer products like faucets and appliances frequently utilize O-rings for their compact and reliable sealing properties.
The primary distinction between gaskets and O-rings lies in their shape and function. Gaskets conform to complex surfaces, while O-rings provide a simple, uniform seal within a groove. Installation also differs—gaskets often require precise alignment and special tools, whereas O-rings are easier to install, typically fitting into a designated groove.
Gaskets excel at sealing large, flat surfaces, making them ideal for flanged connections. O-rings, however, deform to fill gaps, offering superior sealing performance in dynamic environments. Cost considerations also vary—gaskets can be more affordable in standard applications but become expensive when customized. O-rings, often produced in standard sizes, are cost-effective in bulk but may need frequent replacement in harsh conditions.
Selecting between gaskets and O-rings depends on the specific application. Gaskets offer versatility for sealing large, irregular surfaces, while O-rings excel in dynamic, space-constrained environments. Understanding material properties, installation requirements, and performance characteristics ensures engineers choose the most effective sealing solution. Both components play a critical role in maintaining the integrity and longevity of mechanical systems across industries.
Gaskets are seals that are mechanically made to prevent either process fluids from escaping or contaminants from entering the delicate areas. Each given system has its best suited gasket, and it is critical to make the right...
The head gasket is a motor engine component that seals the combustion part of the engine so that oil and the motor coolant circulate. The head gasket also seals the combustion chamber inside the engine...
Rubber gaskets are elastic components used for mechanically sealing the microscopic gap between two mating surfaces or joints. Examples of these surfaces are flange faces of piping and fittings, mating surfaces of an...
Molding is a manufacturing process that uses a mold - the latter being a solid container used to give shape to a piece of material. It is a forming process. The form is transferred from the mold to the material by...
Die cutting is the mass fabrication of cut-out shapes by shearing a stock material such as paper and chipboard using tooling called a die. A die is a specialized tool used in manufacturing to cut or shape a material fitted into a press...
Hydraulic seals are a form of gasket-like rings that are used to fill gaps between hydraulic cylinder components. Many different components are found in hydraulic cylinders, some of which get in...
Kiss cutting is a method for cutting into a material where the upper layers are pierced, but the back layer is left intact. The term "kiss" refers to the way the blade touches the upper layers of the material and leaves a pattern...
An O-ring is a round elastic loop that is used as a seal for static and dynamic applications. Their main purpose is to serve as a seal between structures such as pipes, tubes, in pistons, and cylinders. O-rings are made of...
Rubber injection molding is when uncured rubber is transformed into a usable product by injecting raw rubber material into a mold cavity made of metal. The applied pressure produces a chemical reaction like...
Rubber molding is a process of transforming uncured rubber or an elastomer into a usable product by transferring, compressing, or injecting raw rubber material into a metal mold cavity...
A rubber O ring is a mechanical gasket in the shape of a torus or donut and is used for static and dynamic applications where there is relative motion between parts and the possibility of friction. Some of the benefits of rubber O rings are...
There are several methods to perform rubber overmolding, and each method has its own unique advantages and disadvantages. The choice of method typically depends on the design and material requirements of the product being...
Silicone rubber molding is a method for shaping, forming, and fabricating silicone rubber parts and products using a heated mold. The process involves compressing or injecting silicone rubber into a mold...
A grommet edging is a flexible rubber or plastic strip that covers rough and sharp surfaces found in openings and edges of panel walls to protect the passing electrical cables, wires, and other sensitive components...