Gaskets
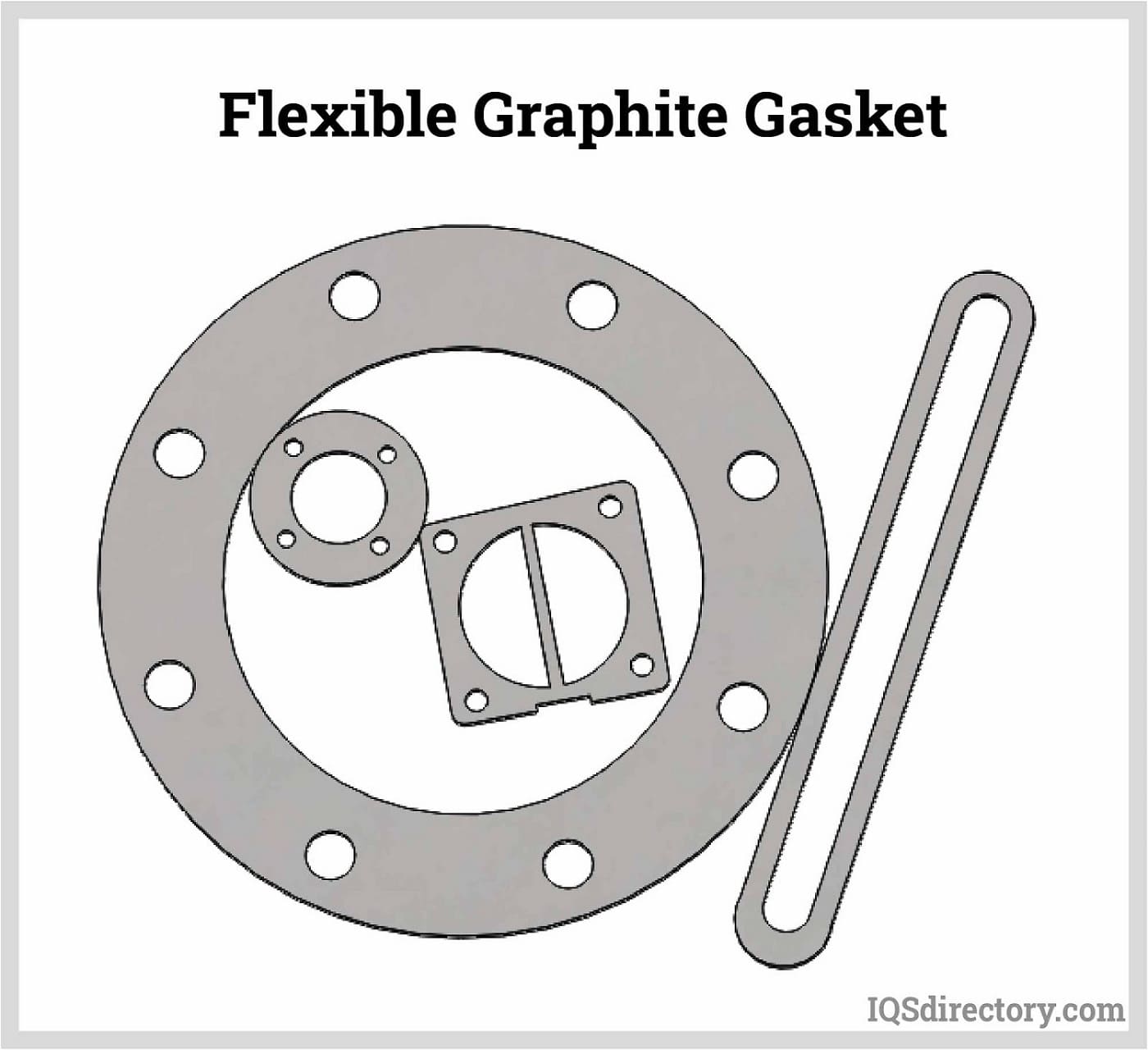
Gaskets are a type of mechanical seal that inhibits leakage by filling the gap between static mating surfaces. It takes advantage of the compressive force that drives the gasket material to plastically flow between the...
Please fill out the following form to submit a Request for Quote to any of the following companies listed on
This article will take an in depth look at gasket materials.
You will understand more about topics such as:
Gasket materials play a pivotal role in crafting gaskets and dictate their functionality and the environments they are suitable for. Gaskets are designed to prevent leaks, ensure tight connections, and keep contaminants at bay in essential processes.
Critical elements like pressure and temperature significantly influence the choice of gasket materials and their suitability for a particular use. Selecting the appropriate material is vital for efficient and effective operations, reducing the frequency of maintenance and repairs.
The following sections will delve into the various materials used for gaskets.
When it comes to choosing gasket materials or designing custom gaskets, there is a wide array of options available. Some of the most prevalent types of gasket materials include:
Solid materials serve as a robust alternative to sponge materials in gasket manufacturing. They provide enhanced durability and an extended lifespan, often outlasting sponge materials by a significant margin. These solid materials are engineered to withstand greater compression forces, making them suitable for high-compression applications.
Gasket formation from solid materials typically involves processes such as waterjet cutting, die cutting, and CNC cutting. Solid materials can also be three-dimensionally molded.
Key solid materials utilized in gasket creation include:
Solid silicone gaskets are predominantly utilized in outdoor settings where minor environmental stresses occur. Ideal for applications subject to extreme temperatures, these gaskets resist sunlight-induced degradation.
Fluorosilicone gaskets are akin to silicone gaskets and offer heightened chemical resistance, expertly enduring fuels, oils, and extreme temperatures. Particularly advantageous in automotive and aerospace fuel systems, fluorosilicone, though pricier, offers valuable benefits over silicone.
Crafted for industrial settings with extreme environmental conditions and substantial wear, nitrile gaskets boast strong chemical resistance to oils and fuels. Select nitrile types are also applicable in food and agricultural sectors.
A more economical option compared to fluorosilicone and silicone, neoprene gaskets are suited for use in applications demanding resistance to liquids such as oils and water. Neoprene is noted for its resilience and elasticity, offering robust resistance to elongation, tearing, fatigue, and abrasion.
Peroxide-cured EPDM gaskets are commonplace in rubber applications known for weather, water, ozone, and UV resistance. Withstanding steam and high temperatures, peroxide-cured EPDM is a cost-effective alternative to silicone, though not suitable for oil exposure.
Renowned for its chemical and oil resistance, synthetic rubber butyl is excellent at warding off moisture and gas escape. It's frequently used in medical and aerospace fields.
Among solid materials, fluoroelastomer stands out due to its remarkable chemical and temperature resistance. Despite its higher cost, fluoroelastomer is a vital material in the aerospace sector where such properties are essential.
Possessing a flat cross-section, fluorocarbon gaskets can be reused in non-critical environments. They serve well in applications needing frequent assembly and disassembly, acting as substitutes for copper gaskets. However, they weaken at high temperatures, limiting their use in such conditions.
Gaskets crafted from sponge materials are typically selected for applications imposing lower compressive forces, such as when:
Sponge materials alleviate compressive stresses on housings and are often preferred for their UL flame ratings. For instance, silicone sponge with a UL94V-0 flame rating is easier to source than its solid counterpart.
Sponge silicones, chosen for their compressibility and softness, excel in applications needing padding and gasketing, offering excellent temperature resistance suitable for outdoor use. Their closed-cell form precludes water absorption and ensures superior compression set. Silicone sponge boasts the longest lifespan among all silicone materials and is available in extra firm, firm, medium, and soft consistencies.
For those seeking a flexible, soft material, a neoprene blend offers an economical alternative to solid rubber and other sponge materials. It serves various applications such as shock absorption, weatherstripping, and basic sealing, thanks to its closed-cell nature that prevents water infiltration. Neoprene sponge is available in extra firm, firm, medium, and soft densities.
While similar to neoprene blend, the EPDM sponge provides enhanced ozone resistance, making it apt for situations where ozone exposure is significant. This feature, however, makes EPDM pricier than neoprene blend.
Used for applications with minimal compressive forces, foam materials offer lower compression resistance than sponges and are cost-effective for creating basic seals between ducts and primary air layers. While they don't offer robust environmental sealing, they suffice for non-critical sealing tasks.
Known for outstanding temperature tolerance, silicone foams serve in cushion, seal, dampening, and insulating applications with varieties ranging from ultra-soft to extra-firm.
Custom-designed for dust filtering while allowing airflow, filter foams stand out in electronics where dust is an issue.
Polyurethane foams are commonly utilized for gasketing, energy absorption, and seismic sealing due to their affordability compared to silicone foams. They offer a low compression set and are available in numerous densities and firmness levels within each formulation.
Prized for its cost-effectiveness, polyolefin is widely used to produce basic gaskets and prevents contact between two part surfaces.
Form-in-place gaskets are ideal for small gaskets that are cumbersome to die-cut and assemble. These gaskets, suited for intricate electronic devices, reduce overall assembly costs by being directly dispensed and cured within the unit.
Offering excellent sealing properties, silicone sealants and adhesives cure under ambient humidity and perform well against ozone, weather, and compression stresses, as well as functioning as electrical insulators. Uncured silicones adhere to minimal objects when setting, making them great for form-in-place (FIP) gaskets. While they thrive at high temperatures, their low-temperature flexibility is limited.
When speed and production efficiency are imperative, UV materials present an advantage. Needing minimal curing time, these materials expedite production, making them ideal in high-volume, high-throughput environments.
EMI materials are a popular choice for precision and minute gaskets, delivering effective electromagnetic interference (EMI) shielding between two gasket faces. They are extensively used in satellites, aerospace equipment, and testing devices.
This technique employs EMI materials to establish a barrier between two sections of a part or product.
Silicone extrusions integrate two gasket types—EMI shielding and environmental sealing—into one product, with a thin, conductive shield co-extruded over a silicone base. Perfect for fitting gaskets into grooves, extrusions offer lower compression force due to their softer nature compared to FIP dispensation.
Silicone products designed for EMI shielding incorporate conductive fillers such as nickel, copper, or aluminum, offering flexibility across various design shapes and sizes. They are less ideal in harsh environments that might compromise shielding and sealing effectiveness, making them best suited for connector gaskets and printed circuit boards.
These materials are integral in heat dissipation from components, depending on power output over time. Silicones—thanks to high-temperature resilience—are frequently utilized. The right thermal conductivity choice enhances heat dissipation efficiency, with higher outputs necessitating premium materials. Similar to fluorosilicone, silicone materials may be reinforced with tear-resistant cloth inserts.
Among the many gasket materials available, some are more frequently used due to their distinctive characteristics that make them well-suited for specific applications. These include:
These materials are lightweight and stable, with strong resistance to water penetration. They offer good compressibility, minimal lateral flow, and high resistance to oil. Cork is durable, resistant to wear, and unaffected by high temperatures.
These materials combine granulated cork with synthetic rubber polymers, offering the high resilience and flexibility of rubber along with the compressibility of cork. The rubber provides chemical compatibility, sealant properties, and resistance to weather conditions and acids. A variety of rubber gasket materials are available to meet specific chemical resistance needs.
These materials are available in sponge, foam, or solid forms. Regardless of their state, they share characteristics such as stability at high temperatures, general inertness, and resilience. Some of the benefits of silicone include
However, the most common drawback of silicone is that it is not best suited for numerous hydrocarbons and steam.
Natural rubber offers excellent recovery properties and strong resistance to most inorganic salts, alkalis, and mild acids. However, it is unsuitable for use with oils and solvents and does not perform well when exposed to ozone, oxygen, or sunlight.
One of the special properties of natural rubber gaskets is its resistance to the effects of ultraviolet light, which makes them ideal for outdoor use.
Urethanes are known for their excellent aging and abrasion resistance, although they are not ideal for extreme temperatures. Key characteristics of urethanes include:
This material offers excellent resistance to UV light and ozone, with good tear strength and strong resilience. However, it can be easily damaged by petroleum-based fuels. Key characteristics include:
As previously discussed, various gasket materials are available in the industry, each designed to meet specific criteria. The formulations and grades of these materials can be derived from different substances to suit diverse applications.
The formulations and grades of rubber can be tailored for a wide range of applications, depending on the operating and environmental conditions.
Some of the materials used in the formulations and grades include:
These materials are used in molding processes such as transfer molding, compression molding, and injection molding to create gaskets in various sizes and shapes.
Some of the materials used in the formulations and grades include:
This has cells that are separated fully from the other surrounding cells in order to prevent fluid intrusion.
Closed-cell sponge rubbers are available in densities that range from soft, medium to hard. Some of the materials used in the formulations and grades include:
This material features interconnected cells that allow liquids, gases, and other fluids to pass through. Open-cell sponge rubbers come in five density levels, ranging from soft to extra firm.
Some of the materials used in the formulations and grades include:
These materials are composed of non-asbestos fibers, such as aramid or fiberglass, combined with rubber. This formulation enhances their performance under pressure and temperature conditions.
Some of the materials used in the formulations and grades include:
Cork offers high flexibility and compressibility. When combined with rubber materials like neoprene or nitrile, it creates a gasket that is resistant to solvents, oils, and fuels.
Some of the materials used in the formulations and grades include:
These materials do not have electrical conductivity and are used in electrical applications.
Some of the materials used in the formulations and grades include:
These materials are used to protect electronic and electrical devices from radio frequency and electromagnetic interference.
Some of the materials used in the formulations and grades include:
Fiber materials encompass a range of types, including insulating fiber, cellulose fiber, synthetic fiber, and vegetable fiber.
Some of the materials used in the formulations and grades include:
These are all the materials formed by gas trapped within separate or interconnected cells in a solid or liquid.
Some of the materials used in the formulations and grades include:
This is a material based on wool and is formed by exposing it to heat, moisture, and pressure.
Some of the materials used in the formulations and grades include:
Flexible graphite gaskets have superior compressive strength and recovery with very little creep. Three common types of graphite gasket sheets are reinforced (tanged, metal, metal foil, or polymer inserted), pure, and laminated with some varieties of laminated gaskets available with an adhesive backed. Flexible graphite gaskets are resistant to a wide variety of chemicals and are used in cryogenic applications and high temperature applications of 800°F up to 850°F with special grades able to withstand temperatures up to 1000°F (continuous). In oxygen free environments, gaskets are capable of sealing up to 5400°F. They provide a high performance seal in extreme conditions such as high pressure and high temperature applications.
Although flexible graphite gaskets have very low mechanical strength, they can be reinforced by being combined with fiberglass or layers of various metals such as stainless steel, nickel, Inconel, or aluminum and fabrics like fiberglass or polymer films. Much like rubber, flexible graphite gaskets have excellent compressive strength and good recovery.
Some of the grades of flexible graphite sheets include:
In addition to its high resistance to temperature, pressure, and chemicals, flexible graphite excels as a heat spreader due to its excellent thermal conductivity. It also serves as an electromagnetic interference (EMI) shield, effectively suppressing unwanted noise and electrical currents.
The outstanding properties of flexible graphite make it perfect for high-temperature applications that demand tight seals under critical conditions, such as aerospace engines, heavy truck exhaust systems, and steam power plants. It is also an excellent choice for sealing valves due to its thermal heat transfer and dissipation capabilities.
Flexible graphite is widely used across various products and applications. Different manufacturers of flexible graphite gaskets employ their own methods for identifying and classifying their products. They provide information and data to help in selecting the flexible graphite sheets that best suit specific applications.
Mixing these polymers with other substances enhances their characteristics. The formulations and grades incorporate materials such as:
These are materials that can withstand exposure to extreme temperatures.
Some of the materials used in the formulations and grades include:
Spiral wound gaskets are designed to withstand high temperatures and pressures while effectively preventing leaks. They are composed of an outer ring, an inner ring, and a sealing material.
Numerous machines are available for producing a range of gasket materials, including rubber, cork, silicone, and fiber-based substances. These machines play a crucial role in modern industry by enabling the efficient and precise manufacturing of gaskets. Gaskets are essential components in sectors like automotive, aerospace, construction, and manufacturing, where they provide sealing and prevent leaks, thereby ensuring the integrity and reliability of equipment and systems. Below, we review various brands offering machines for gasket material production, available in the United States and Canada.
The FlashCut Gasket Cutting System by Atom FlashCut has likely become popular due to its precise cutting capabilities, versatile software, and ability to handle a broad range of gasket materials. These features enable efficient and accurate production, making it a favored choice among gasket manufacturers.
Dieffenbacher's Fiberforge machine merges extrusion and lamination processes to create gasket materials with continuous lengths, customized profiles, and superior sealing properties. This innovative approach and the high-quality results it delivers have contributed to its widespread popularity.
The Zemat RCE Gasket Cutting Machine from Zemat Technology Group has gained popularity for its efficiency, high cutting speed, and precision. These features enable gasket manufacturers to streamline their production processes and meet stringent requirements effectively.
Sutherland Presses provides gasket-specific compression molding presses renowned for their precise control over temperature, pressure, and molding time. Their ability to consistently produce high-quality gaskets with superior sealing properties has made these machines highly sought after in the industry.
The Rolmacon Gasket Die Cutting Machine from Rolmacon Global Ltd is likely popular for its precise and efficient die cutting capabilities. Its ability to deliver high productivity and customization makes it well-suited for gasket manufacturers who require speed, accuracy, and flexibility.
Please be aware that specific models and features may have changed since the last update. For the most current information on the latest models and capabilities of machines used for producing gasket materials in the United States and Canada, it is recommended to consult the manufacturers or industry resources.
Most of the materials discussed earlier can be provided with or without a pressure-sensitive adhesive backing. Adding this backing reduces installation time and labor. However, it is not recommended for use in applications such as:
Several considerations should be kept in mind when choosing a gasket material appropriately for an intended application. These key considerations include:
Pressure: the pressure range that the gasket should withstand.
Temperature: the temperature range that the gasket should withstand.
Ozone and UV Exposure: how exposed will the gasket be to ozone and UV radiation.
Media: will the gasket be exposed to corrosive or abrasive fluids.
Product Standards: are there any specific product requirements within the industry.
Industry Standards: are there any industry-specific standards affecting the choice of gaskets.
Temperature considerations are usually the primary factor in selecting a gasket material, as temperature can significantly affect the material's properties, including sealing performance, compression set, and maximum stress tolerance. Both internal and external temperatures are crucial; for instance, gaskets exposed to direct sunlight may experience internal temperatures exceeding 140 degrees. Conversely, gaskets exposed to freezing temperatures can become stiff or brittle, increasing the risk of failure. Additionally, gaskets subjected to alternating cycles of cold and warmth may develop a high compression set.
UV and ozone exposure can lead to the degradation of rubber gaskets. Ozone is not only present in the atmosphere but can also be generated by electrical enclosures with high-voltage components. Both UV and ozone can break down the carbon bonds in the backbone polymers, causing the gaskets to dry, harden, scale, crack, and flake. Organic rubber gaskets, such as Buna-Nitrile, natural rubber, and synthetic isoprene, degrade more quickly under these conditions. In contrast, silicone and EPDM materials offer better resistance to UV exposure.
Joints are susceptible to deformation when pressure is applied to a system, making the selection of a gasket material that can withstand such pressure crucial. Many modern gaskets feature a PxT rating factor, which indicates the maximum pressure and temperature limits they can endure.
Industries such as automotive, aerospace, consumer electronics, and others must comply with Federal EMI product standards. Components and internal wires can emit EMI and act as antennas, necessitating control over EMI radiation. To manage this, electronic components are housed in conductive enclosures, with the lid and enclosure requiring complete contact. Thus, selecting the right conductive gasket is crucial. These gaskets not only help attenuate EMI but also provide environmental sealing.
Considering the media to which the gasket will be exposed is crucial. Generally, sealing liquids is easier than sealing gases, which should be evaluated after determining the temperature and pressure ranges. Chemical resistance is also essential, as certain chemicals can impact the gasket’s structural integrity and functional properties. It is important to assess the gasket’s chemical resistance in relation to temperature, as some fluids can become aggressive at higher temperatures. Therefore, a gasket that performs well at ambient temperatures may not maintain the same effectiveness at elevated temperatures.
Gaskets serve as mechanical seals to prevent process fluids from leaking and to keep contaminants out of sensitive areas. Each system requires a specifically suited gasket, making it essential to choose the right one for each application. It is important to balance various factors when selecting a gasket.
Gaskets are a type of mechanical seal that inhibits leakage by filling the gap between static mating surfaces. It takes advantage of the compressive force that drives the gasket material to plastically flow between the...
The head gasket is a motor engine component that seals the combustion part of the engine so that oil and the motor coolant circulate. The head gasket also seals the combustion chamber inside the engine...
Rubber gaskets are elastic components used for mechanically sealing the microscopic gap between two mating surfaces or joints. Examples of these surfaces are flange faces of piping and fittings, mating surfaces of an...
Molding is a manufacturing process that uses a mold - the latter being a solid container used to give shape to a piece of material. It is a forming process. The form is transferred from the mold to the material by...
Die cutting is the mass fabrication of cut-out shapes by shearing a stock material such as paper and chipboard using tooling called a die. A die is a specialized tool used in manufacturing to cut or shape a material fitted into a press...
Hydraulic seals are a form of gasket-like rings that are used to fill gaps between hydraulic cylinder components. Many different components are found in hydraulic cylinders, some of which get in...
Kiss cutting is a method for cutting into a material where the upper layers are pierced, but the back layer is left intact. The term "kiss" refers to the way the blade touches the upper layers of the material and leaves a pattern...
An O-ring is a round elastic loop that is used as a seal for static and dynamic applications. Their main purpose is to serve as a seal between structures such as pipes, tubes, in pistons, and cylinders. O-rings are made of...
Rubber injection molding is when uncured rubber is transformed into a usable product by injecting raw rubber material into a mold cavity made of metal. The applied pressure produces a chemical reaction like...
Rubber molding is a process of transforming uncured rubber or an elastomer into a usable product by transferring, compressing, or injecting raw rubber material into a metal mold cavity...
A rubber O ring is a mechanical gasket in the shape of a torus or donut and is used for static and dynamic applications where there is relative motion between parts and the possibility of friction. Some of the benefits of rubber O rings are...
There are several methods to perform rubber overmolding, and each method has its own unique advantages and disadvantages. The choice of method typically depends on the design and material requirements of the product being...
Silicone rubber molding is a method for shaping, forming, and fabricating silicone rubber parts and products using a heated mold. The process involves compressing or injecting silicone rubber into a mold...
A grommet edging is a flexible rubber or plastic strip that covers rough and sharp surfaces found in openings and edges of panel walls to protect the passing electrical cables, wires, and other sensitive components...