Gaskets
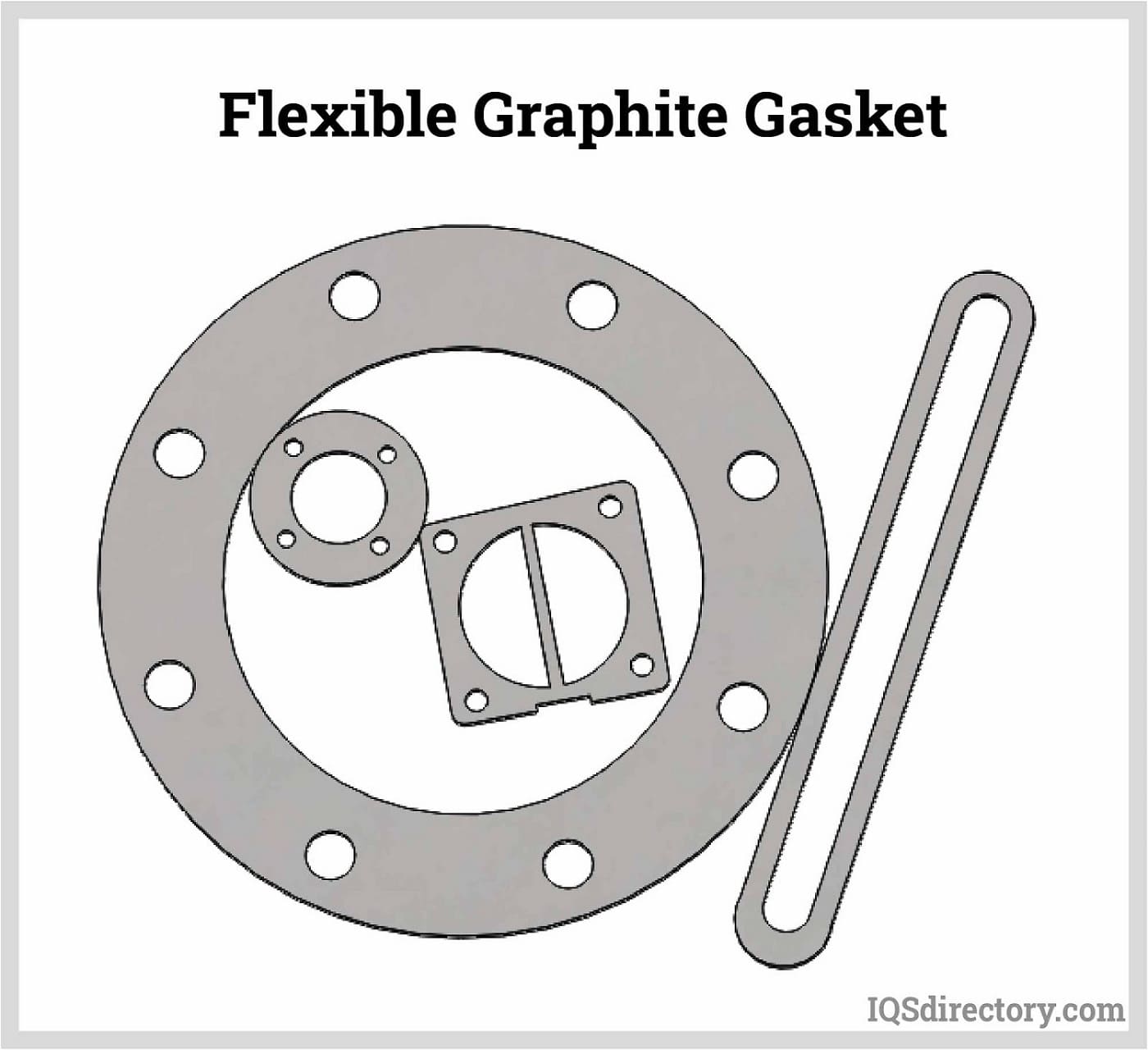
Gaskets are a type of mechanical seal that inhibits leakage by filling the gap between static mating surfaces. It takes advantage of the compressive force that drives the gasket material to plastically flow between the...
Please fill out the following form to submit a Request for Quote to any of the following companies listed on
This article takes an in-depth look at rubber gaskets.
Read further to find out more about topics such as:
Rubber gaskets are versatile components crafted to seal the small gaps between two connected surfaces or joints. They are commonly used in various applications, such as sealing flange faces within piping systems, cylinder heads in vehicles, engine blocks, tank rims, covers, as well as door edges and frames. These gaskets operate by adjusting and fitting into the discrepancies of the hard surfaces they come in contact with. The sealing function is accomplished as the components compress the gasket, causing it to deform and establish a robust seal.
The superior sealing capability of rubber stems from its elastomeric nature. Both natural and synthetic rubbers belong to the elastomer family, which are polymers distinguished by their exceptional elasticity. This flexibility emerges from the cross-linking of lengthy polymer chains into amorphous formations. The moderately weak intermolecular forces present among these chains allow them to adapt when subjected to stress. This adaptability permits elastomeric gaskets to conform to a variety of surface profiles, guaranteeing a reliable seal.
Rubber gaskets provide several advantages over metallic and other non-metallic gaskets due to their distinctive properties. Their elasticity, or ability to deform and return to shape, is crucial for creating tight seals. Additionally, rubber gaskets are easier to manufacture and can be made from various raw materials. Below are some of the key benefits of using rubber gaskets.
Rubber gaskets are produced by blending raw rubber with various additives and shaping them into the desired form. Rubber, whether thermosetting or thermoplastic, exhibits excellent formability. In its liquid or uncured state, it readily flows into molds and dies. After curing or hardening, the material can be easily cut or machined to precise dimensions. Compared to metallic and other non-metallic gaskets, rubber gasket production involves lower heat and pressure, leading to reduced tooling costs and lower overall operating expenses.
Rubber's unique microstructure enables it to stretch or compress without damaging or degrading its properties. This flexibility allows rubber gaskets to create effective seals by conforming to the surfaces they seal. Compared to metallic gaskets, which often rely on grooved, serrated, or corrugated surfaces to create a labyrinth seal, rubber gaskets provide a more adaptable and effective sealing solution. Although metallic gaskets also deform to some extent, the seal remains metal-to-metal, which can be less flexible than rubber's conforming capability.
Unlike other gasket types, there is a degree of flexibility and freedom in choosing the right material for a particular application. This is due to the nature of producing elastomeric materials. Raw elastomers such as raw synthetic rubbers can be produced from different hydrocarbon compounds. After producing this raw material, its properties are further modified by different additives such as stabilizers, fillers, antioxidants, and reinforcements. This design flexibility allows the production of countless engineered rubber gasket materials, most of which are patented by large manufacturers.
In contrast, metallic gaskets are usually restricted to materials like stainless steel, while mineral gaskets are typically made from mica or vermiculite. Graphite gaskets are limited to highly pure, exfoliated graphite. The only gasket type with a comparable range to rubber gaskets is compressed fiber gaskets, which also incorporate elastomeric materials.
When used within their intended specifications, rubber gaskets are highly durable and stable. They can withstand various chemical and environmental factors, including acids, alkalis, oxygen, ozone, water, heat, and UV light. However, their resistance depends on the type of rubber and the additives used. Fluorocarbon-based elastomers, such as FKM and PTFE, offer excellent corrosion resistance. Additionally, materials like SBR, Butyl, and EPDM also provide strong chemical and aging resistance.
Another advantage of rubber gaskets lies in the diverse raw materials used during compounding, which allows for customization of their physical properties. Key properties such as hardness, compression set, compressive modulus, tensile strength, and elongation can be adjusted based on the required sealing performance and fluid pressure. For instance, if a gasket is too soft, it may fail under higher pressures, while a gasket that is too hard may require excessive compressive force from flange bolts. By carefully formulating the rubber compound, gaskets can be optimized to strike the right balance among these properties to suit specific applications.
Unlike metallic gaskets, rubber gaskets can initially be produced as sheets of gasket material. These sheets are provided to fabricators and end-users for crafting custom gaskets to fit irregular mechanical joints and surfaces. Fabricators can use various machining methods, such as hand cutting, die-cutting, water-jet cutting, and laser cutting, to create these custom gaskets. Laser cutting, in particular, is favored for producing precise gaskets.
In addition to cutting, other fabrication methods are used to form rubber gaskets, including elastomer forming techniques such as extrusion and injection molding. These processes involve creating specialized tools or molds to shape the gasket. Unlike cutting methods, these tools are not limited to a single profile; they can be customized to match the specific geometry of the mating surfaces. Typically, these molds are crafted using computer-aided manufacturing (CAM) techniques, which ensures precise profiling.
Rubbers can be specially formulated to comply with FDA standards for use in food, beverage, and pharmaceutical manufacturing. Examples of such FDA-approved rubbers include nitrile, neoprene, silicone, EPDM, and FKM. To qualify as food-grade, the rubber must be made from compounds that have been approved by the FDA, ensuring that any substances in the rubber do not pose health risks if they come into contact with consumables. Additionally, these rubber compounds must exhibit properties like resistance to bacterial growth, chemical and thermal stability, and must not impart any taste or odor.
Rubber gaskets find applications across various industries due to their versatility. They are particularly effective in general-purpose settings involving low to medium pressures and temperatures. Their strengths are most evident in environments dealing with chemicals, water, and hydrocarbons. Different rubber formulations can provide resistance to specific groups of chemicals, enhancing their suitability for specialized applications.
Here are some common applications for rubber gaskets.
In industrial settings, rubber gaskets are commonly employed for utility and chemical processing lines. They are generally suitable for low to medium pressure applications. While most rubber gaskets are rated for around 150 psi (10 bars), certain high-performance types, such as PTFE gaskets, can handle pressures up to 800 psi (55 bars).
Rubber gaskets are widely used in plumbing applications due to their affordability and resistance to corrosion and degradation caused by water, chlorides, and biological factors. They are commonly found in household fixtures such as faucets and drains.
In automotive applications, there are two primary types of rubber gaskets. The first type is used for sealing low-pressure and passive components, such as doors and windows. These gaskets are made entirely of rubber and are designed to absorb shocks while preventing the ingress of water and air. Additionally, oil and solvent-resistant rubber gaskets are employed in fuel supply and hydraulic lines to ensure durability and reliability in these demanding environments.
The second type includes gaskets used in engine and transmission components, such as the oil pan gasket, exhaust gasket, and head gasket. These are generally composite gaskets rather than pure rubber gaskets. They often incorporate mineral fibers or steel reinforcements within a rubber matrix to enhance their strength and durability.
In aerospace applications, rubber gaskets are used to seal systems such as fuel supply, hydraulics, propellants, and oxidizers. They are engineered to withstand harsher conditions, including higher stresses and temperatures. To handle exposure to combustion and extreme heat, these gaskets are often flame-retardant to prevent fire hazards. Additionally, some gaskets are designed with special properties like electrical conductivity and antistatic features to protect aircraft instruments and sensitive signals from interference caused by stray currents or electromagnetic fields. Gaskets with electromagnetic shielding capabilities are known as EMI gaskets.
In marine equipment and ships, rubber gaskets are utilized to seal hatches, doors, and windows. Their resilience makes them ideal for these applications, as they effectively absorb shocks and impacts. Rubber's ability to withstand significant deflection and compression under heavy loads further enhances its suitability. Additionally, rubber gaskets are resistant to corrosion from environments with high chloride levels, making them durable in marine conditions.
Rubber is an excellent choice for sealing covers, nozzles, holes, and ports on containers for liquids or bulk solids. Its affordability, effective sealing properties, and resistance to fluid degradation make it highly suitable for these applications. Different rubber types offer varying levels of chemical resistance. For instance, nitrile and neoprene gaskets are effective against fuels, oils, and petroleum-based solvents. Fluorocarbon-based rubbers provide strong resistance to acids and alkalis, while silicone gaskets are favored for their resistance to water and moisture in wet environments.
As noted in the previous chapter, rubber is a preferred material for food and pharmaceutical manufacturing due to its ability to be produced from non-toxic, FDA-approved substances. Rubber gaskets are commonly used in food, beverage, and drug processing facilities to seal valves, pipe joints, and various equipment ports and fixtures.
Rubbers are typically categorized based on the monomers used to create their polymer chains. These monomers can include hydrocarbons like ethylene, methylene, propylene, isoprene, and fluorocarbons. The structure of the polymer chain defines the fundamental properties of the rubber. Additional components such as curatives and additives further modify these properties, leading to various subclassifications within the main rubber types.
Here are some of the most commonly used rubber gasket materials available on the market.
Ethylene propylene diene monomer (EPDM) is an elastomer created through the copolymerization of ethylene and propylene. It offers excellent weather resistance, as well as strong insulating and dielectric properties. EPDM performs well mechanically across a broad temperature range, both high and low. Chemically, it resists acids, alkalis, alcohols, and ketone-based solvents, and it provides adequate resistance to water and steam.
Nitrile rubber, also known as acrylonitrile butadiene rubber (NBR), is produced by copolymerizing acrylonitrile and butadiene. It is commonly used for its resistance to fuels, oils, and petroleum-based solvents, making it ideal for sealing automotive engine components. However, nitrile rubber has relatively lower mechanical properties and performs poorly at low temperatures compared to other rubber materials. To address these limitations, reinforcing fillers are often added.
Neoprene, also known as chloroprene rubber (CR), is synthesized through the emulsion polymerization of chloroprene. It is renowned for its flame-retardant properties. The chlorine content in its polymer chain enhances its resistance to oxidation, ozone, and oil, though its oil resistance range is not as extensive as that of nitrile rubbers. Additionally, neoprene tends to be more costly than natural rubber and exhibits poor performance at low temperatures.
Natural rubber is derived from the latex of the Hevea tree and consists primarily of the polymer chain polyisoprene. It is recognized for its resilience and resistance to fatigue. However, its performance can often be outmatched by synthetic rubber types. Additionally, natural rubber gaskets generally have limited resistance to ozone and oil.
Silicone rubbers feature a silicon-oxygen backbone rather than a carbon-based structure. They are known for their excellent resistance to oxygen, ozone, heat, light, and moisture. Despite these advantages, silicone rubbers tend to be more costly and offer only moderate mechanical properties compared to organic (carbon-based) rubbers. Additionally, they have limited resistance to petroleum-based chemicals.
Butyl rubber (IIR) is a copolymer of isobutylene and isoprene, with the isoprene content carefully controlled to achieve the desired level of unsaturation. Its low unsaturation makes butyl rubber highly resistant to most chemicals, both gaseous and liquid, and it exhibits exceptional aging resistance when properly vulcanized. Due to its superior impermeability, butyl rubber is commonly used in seals for equipment handling compressed air and process gases.
Styrene-butadiene rubber (SBR) is produced through the emulsion polymerization of styrene and butadiene, and is commonly known as red rubber in commercial blends. As a general-purpose rubber, SBR rivals natural rubber in terms of tear, abrasion, and thermal resistance properties. Due to its lower cost, SBR gaskets are often favored over natural rubber options.
Santoprene is a proprietary gasket material classified as a thermoplastic vulcanizate (TPV) or thermoplastic elastomer (TPE). It consists of dynamically vulcanized EPDM dispersed within a polypropylene matrix. Its thermoplastic nature allows it to be melted and recycled. Santoprene offers strong resistance to degradation from ultraviolet light and ozone. This trademarked material is currently owned by ExxonMobil.
Polyurethane, commonly known as urethane, is created by reacting polyether or polyester glycols with diisocyanates and curing agents. It is a versatile material appreciated for its wide range of physical properties, which can be tailored through various formulations. Polyurethane is known for its exceptional resilience, abrasion resistance, and weathering durability.
Poron is a patented gasket material composed of multicellular polyurethane or polyurethane foam. Its porous structure makes it ideal for applications requiring thermal insulation, vibration and acoustic damping, and shock absorption. The resilience and rebound characteristics of polyurethane contribute to its effectiveness in sealing applications by minimizing creep relaxation.
FKM, or fluorocarbon rubber, is a type of rubber made from the copolymerization of vinylidene fluoride (VDF) with other chemicals like hexafluoropropylene (HFP) and tetrafluoroethylene (TFE). Commercially, it is known under the trade name Viton. Viton gaskets are high-performance and relatively expensive, designed for use in demanding environments such as automotive and aerospace applications. They excel in high-temperature conditions and are resistant to oils, fuels, acids, and alkalis.
Although it is technically a plastic, PTFE is widely used as a gasket material in chemical processing due to its exceptional bonding energy. This property grants PTFE remarkable resistance to chemical reactions and corrosion. Additionally, PTFE features a low coefficient of friction, outstanding insulating capabilities, high toughness, and good impact resistance.
Rubber gaskets can be manufactured through various processes, each affecting the quality, precision, and characteristics of the final product. These methods come with their own sets of advantages and limitations. Below, you will find an overview of some of these manufacturing processes.
Die-cutting is a bulk manufacturing technique where shapes are cut from flat stock material using a tool known as a die. This die is a specialized tool with the product's two-dimensional profile and features a sharp edge, often referred to as the steel rule. The cutting process involves pressing the die into the material on the machine’s bed, with a single downward motion shearing the material into the desired shape.
Die-cutting is a favored method for producing rubber gaskets due to its straightforward process, cost-effective tooling, minimal material waste, and high production efficiency. This technique is commonly employed for gaskets used in general applications like plumbing and container sealing.
Water jet cutting is a non-conventional method that utilizes a high-velocity stream of water to cut various materials, including rubber. The process involves pumping water at extremely high pressures through a small nozzle, converting fluid pressure into a high-speed jet. This powerful jet cuts through the material by impingement and erosion.
Water jet cutting is ideal for fabricating gaskets that are sensitive to pressure and temperature, as it minimizes stress on the material and avoids burning the edges. However, a key limitation is that the stock material must be resistant to water to prevent degradation during the cutting process.
Laser cutting is a non-conventional technology that employs a highly concentrated beam of light, known as a laser, to cut materials. The laser beam is directed along the cutting lines, causing the material to rapidly vaporize or sublimate at the exposed areas, resulting in precise cuts.
Laser cutting is favored for its precision and clean cutting process. Unlike water jet cutting, it does not involve wetting the product, which avoids issues like swelling and degradation. Additionally, laser cutting equipment typically requires less maintenance compared to water jet cutting machinery.
Flush cutting is a mechanical process that utilizes a small, oscillating knife to cut through soft and semi-rigid materials like rubber. The knife is mounted on a robotic system and controlled by a CNC program, allowing for precise and automated cutting.
Flush cutting is a precision technology similar to water jet and laser cutting. It offers the advantage of not subjecting the material to pressure, high temperatures, or water. However, it is less effective for cutting harder materials.
Injection molding is primarily a plastic forming process but can also be used for molding rubber. In this process, the rubber is first melted to a manageable viscosity or, in the case of liquid uncured rubbers, directly injected. The molten rubber is then injected into a mold, which has a negative image of the final product. Inside the mold, the rubber solidifies, cures, and cools. After the hardening phase, the molded rubber gasket is released.
Injection molding is especially useful for producing rubber gaskets with rounded or complex three-dimensional shapes, such as O-rings. Unlike cutting methods, which are limited to flat profiles, injection molding allows for the creation of gaskets with intricate geometries and detailed designs.
The process of rubber gasket extrusion involves pushing a rubber compound through a specialized die to create gaskets with the desired cross-sectional shape. This method is versatile and can be used with different types of rubber, such as EPDM, silicone, neoprene, Viton, and natural rubber.
Extrusion starts by introducing the rubber compound into a hopper, which is designed to funnel the material into the extrusion barrel. Modern systems often feature automated hoppers for efficient material handling.
During extrusion, a helical screw inside the barrel moves the rubber compound forward, while heating elements warm the material to make it more flexible. The rubber is subjected to increasing pressure and temperature as it progresses towards the die. Once the rubber exits the die, it may expand or swell depending on the hardness of the material and the formulation used.
Once the rubber exits the extrusion die, it undergoes vulcanization to achieve the required tensile strength. This curing process involves heating the rubber and can be accomplished through methods such as steam curing, continuous curing, or by cutting the rubber to specific lengths. Vulcanization is a chemical process that typically uses sulfur to cross-link the rubber molecules. During this stage, the rubber may expand or contract in both its cross-sectional area and length, depending on the formulation of the rubber compound.
Vulcanization is a chemical treatment that enhances the physical characteristics of rubber. This process boosts the rubber's tensile strength and its resistance to swelling and wear. It primarily involves heating rubber in the presence of sulfur.
The vulcanization technique was pioneered by Charles Goodyear during the early stages of the industrial revolution. He found that using an accelerator could speed up the vulcanization process at lower temperatures. Sulfur plays a crucial role in this process by chemically bonding with rubber to create cross-links between the long molecular chains.
Steam curing is suitable for small quantities of extruded rubber and is considered a safe vulcanization method. Rubber subjected to steam curing exhibits excellent durability, making it particularly effective for gaskets used in bonding applications.
Continuous curing is used for processing larger quantities or sizes of gaskets. This method employs microwaves or a salt bath to gradually cure rubber. It is energy-efficient and produces rubber gaskets with more uniform profiles.
Hot splicing involves using heat, pressure, and a splicing film made of polyethylene to join the ends of rubber profiles, creating tightly bonded gaskets. The heat used can be conventional or infrared, which helps bond the polyethylene film. Hot splicing achieves stronger molecular bonds compared to traditional vulcanization. This technique is suitable for gaskets cut by water jet to ensure clean and precise edges.
Numerous machines are designed for the production of rubber gaskets, playing a crucial role in modern manufacturing. These machines ensure the efficient and accurate creation of sealing components for diverse industries, including automotive, aerospace, and marine sectors. They are essential for producing reliable seals that prevent leaks and maintain operational integrity. Below, we highlight several prominent brands recognized for their expertise in supplying machinery for rubber gasket production:
Atom FlashCut provides the FlashCut Gasket Cutting System, renowned for its high precision in cutting, adaptable software, and capability to work with a range of rubber materials for gasket manufacturing. Its effectiveness, accuracy, and versatility make it a preferred choice in the industry.
Dieffenbacher is known for its Fiberforge machine, which integrates extrusion and lamination techniques to create rubber gaskets with continuous lengths and tailored profiles. This advanced method ensures outstanding sealing performance and high-quality results, contributing to its widespread use in the industry.
Zemat Technology Group offers the Zemat RCE Gasket Cutting Machine, renowned for its rapid cutting speed and precise performance in the production of rubber gaskets. Its effectiveness and dependability have made it a favored choice in the industry.
Sutherland Presses focuses on compression molding presses designed specifically for gaskets, including those for rubber. These machines provide accurate control over temperature, pressure, and molding duration, which guarantees uniform quality and effective sealing properties. Their dependability and high-quality results contribute to their widespread use in the industry.
Rolmacon Global Ltd is known for the Rolmacon Gasket Die Cutting Machine, which excels in delivering precise and efficient die cutting for rubber gaskets. The machine's speed, precision, and capability to accommodate various gasket designs have made it a favored choice in the industry.
Keep in mind that the details regarding specific models, features, or components may have changed since this update. For the latest information, it is advisable to reach out to the manufacturers directly or consult current industry resources for updates on machines used in rubber gasket production in the United States and Canada.
Gaskets are a type of mechanical seal that inhibits leakage by filling the gap between static mating surfaces. It takes advantage of the compressive force that drives the gasket material to plastically flow between the...
Gaskets are seals that are mechanically made to prevent either process fluids from escaping or contaminants from entering the delicate areas. Each given system has its best suited gasket, and it is critical to make the right...
The head gasket is a motor engine component that seals the combustion part of the engine so that oil and the motor coolant circulate. The head gasket also seals the combustion chamber inside the engine...
Molding is a manufacturing process that uses a mold - the latter being a solid container used to give shape to a piece of material. It is a forming process. The form is transferred from the mold to the material by...
Die cutting is the mass fabrication of cut-out shapes by shearing a stock material such as paper and chipboard using tooling called a die. A die is a specialized tool used in manufacturing to cut or shape a material fitted into a press...
Hydraulic seals are a form of gasket-like rings that are used to fill gaps between hydraulic cylinder components. Many different components are found in hydraulic cylinders, some of which get in...
Kiss cutting is a method for cutting into a material where the upper layers are pierced, but the back layer is left intact. The term "kiss" refers to the way the blade touches the upper layers of the material and leaves a pattern...
An O-ring is a round elastic loop that is used as a seal for static and dynamic applications. Their main purpose is to serve as a seal between structures such as pipes, tubes, in pistons, and cylinders. O-rings are made of...
Rubber injection molding is when uncured rubber is transformed into a usable product by injecting raw rubber material into a mold cavity made of metal. The applied pressure produces a chemical reaction like...
Rubber molding is a process of transforming uncured rubber or an elastomer into a usable product by transferring, compressing, or injecting raw rubber material into a metal mold cavity...
A rubber O ring is a mechanical gasket in the shape of a torus or donut and is used for static and dynamic applications where there is relative motion between parts and the possibility of friction. Some of the benefits of rubber O rings are...
There are several methods to perform rubber overmolding, and each method has its own unique advantages and disadvantages. The choice of method typically depends on the design and material requirements of the product being...
Silicone rubber molding is a method for shaping, forming, and fabricating silicone rubber parts and products using a heated mold. The process involves compressing or injecting silicone rubber into a mold...
A grommet edging is a flexible rubber or plastic strip that covers rough and sharp surfaces found in openings and edges of panel walls to protect the passing electrical cables, wires, and other sensitive components...