Plate Heat Exchanger
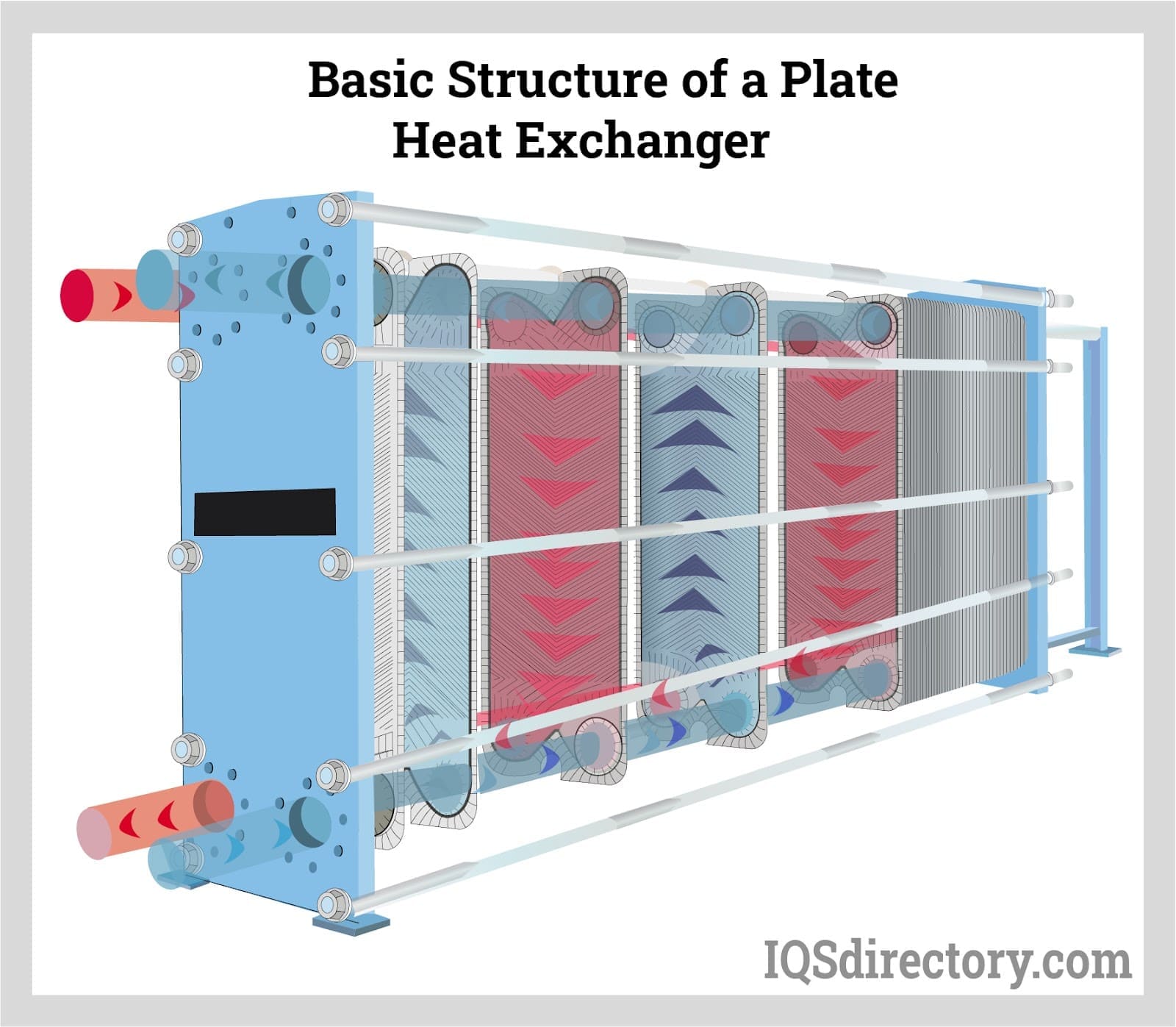
A plate heat exchanger (PHE) is a compact type of heat exchanger that utilizes a series of thin metal plates to transfer heat from one fluid to the other. These fluids are typically at different temperatures...
Please fill out the following form to submit a Request for Quote to any of the following companies listed on
This article presents all the information you need to know about heat exchangers.
Read further and learn more about:
Heat exchangers are pieces of equipment designed to facilitate the transfer of heat between two fluids without enabling them to intermix. This is accomplished by employing a barrier with excellent thermal conductivity, expertly crafted to prevent the fluids from direct contact while still enabling effective heat exchange. Within the heat exchanger, the working fluid either absorbs heat from or releases heat to the process fluid, leading to heating or cooling of that fluid stream. With technological advancements and improvements in material properties, a wide array of heat exchangers are continuously being developed to cater to increasingly varied and specialized applications.
The process of heat transfer in a heat exchanger encompasses both convection across the fluids and conduction through the dividing wall. The design begins with determining the heat transfer coefficient, also known as the U-factor, using Newton's law of cooling as a basis. Engineers also utilize the logarithmic mean temperature difference (LMTD) to assess the temperature driving force essential for heat transfer. Additionally, they evaluate whether the involved fluids are in identical or different phases, like liquid-to-liquid or vapor-to-liquid, as these conditions influence both the design and efficacy of the heat exchanger.
The warm and cool fluids might be sectioned off by a high thermally conductive wall, typically composed of materials such as steel or aluminum. Alternatively, they might directly come into contact with one another.
Heat exchangers are distinct from systems powered by fuel, electricity, or nuclear means. For example, boilers necessitate that both the heat source and the receiving medium are fluids. Fluids are categorized as substances that flow under shear stress or an external force, and include liquids, gases, and vapors.
All heat exchangers function based on the same fundamental thermodynamic principles and mechanisms of heat transfer, which describe how thermal energy is transferred on a macroscopic scale. In a heat exchanger system, three elements interact: the hot fluid, the cold fluid, and the separating wall between them. Energy flows from the hot fluid, through the barrier, and into the cold fluid. Understanding the following thermodynamic principles is key to grasping how heat exchangers operate:
First Law of Thermodynamics: The first law, known as the Law of Conservation of Energy, states that energy, whether in the form of heat or work, cannot be created or destroyed. It can only be transferred to another system or converted into different forms. In heat exchangers, this principle is represented by the heat balance equation, which can be expressed as:
(Heat In) + (Generation of Heat) = (Heat Out) + (Accumulation of Heat)
The first law, known as the Law of Conservation of Energy, states that energy, whether in the form of heat or work, cannot be created or destroyed. It can only be transferred to another system or converted into different forms. In heat exchangers, this principle is represented by the heat balance equation, which can be expressed as:
The heat transfer mechanism in heat exchangers involves a combination of conduction and convection. The driving force behind this transfer is the temperature difference between the inlet and outlet temperatures of the heat exchanger and the corresponding temperatures of the process stream.
Approach Temperature:The heat transfer mechanism in heat exchangers involves both conduction and convection. The driving force for heat transfer is the temperature difference between the inlet and outlet temperatures of the fluids, minus the temperature difference of the process stream.
All heat exchangers have an optimal approach temperature that must be considered when selecting one for a particular application. Misjudging this approach temperature can result in choosing an inappropriate heat exchanger for the process.
Conduction: This is the transfer of heat energy by direct collisions of adjacent molecules. A molecule with higher kinetic energy will transfer thermal energy to a molecule with lower kinetic energy. It occurs more readily in solids. For heat exchangers, it takes place on the wall separating the two fluids. Fourier‘s Law of Heat Conduction states that the rate of heat transfer normal to the material‘s cross-section is proportional to the negative temperature gradient. The proportionality constant is the material‘s thermal conductivity.
Q = -k A
Where Q is the rate of heat transfer, k is the material‘s thermal conductivity, A is the area normal to the direction of the flow of heat, and dT/dx is the temperature gradient.
Convection: Convection in heat exchangers occurs through the bulk motion of the fluid against the surface of the wall, thus transferring thermal energy. This phenomenon is represented by Newton‘s Law of Cooling which states the rate of heat loss is proportional of a body to the difference of the temperature of the body and its surroundings (for this instance, the wall and the fluid).
Q = h A ΔT
In this equation, QQ represents the rate of heat transfer, AA is the area perpendicular to the direction of heat flow, and \Delta TΔT is the temperature difference between the wall and the bulk fluid. The convective heat transfer coefficient, hh, is determined by the wall dimensions, the physical properties of the fluid, and the characteristics of the fluid flow.
In a heat exchanger with a conductive partition, heat is transferred from the hot fluid to the cold fluid in the following sequence:
Up to this point, we've referred to the two fluids in a heat exchanger as hot and cold based on their roles in heat transfer. In industrial processes, however, these fluids are classified as process fluids and utility fluids. The process fluid is typically the more valuable and costly fluid, which may include raw materials, products, or by-products. In contrast, the utility fluid—often water, air, or steam—serves as the heating or cooling agent for the process fluid.
The following are the flow configurations used for the process and utility fluids in heat exchangers:
Countercurrent Flow: In countercurrent flow heat exchangers, the process and utility fluids move in opposite directions. This configuration is the most efficient and widely used because it maintains a large temperature difference between the fluids across the length of the heat exchanger, leading to more uniform heat transfer and reduced thermal stress. Additionally, it allows the cold fluid's outlet temperature to approach the hot fluid's inlet temperature (the highest temperature). Countercurrent flow also requires less surface area compared to the co-current flow configuration.
Co-current or Parallel Flow: In co-current or parallel-flow heat exchangers, the process and utility fluids flow in the same direction. This configuration is suitable when the outlet temperatures of both fluids are nearly equal. However, the temperature difference between the fluids is initially large at the inlet and decreases significantly along the length of the heat exchanger, leading to increased thermal stress and potential material failure. As a result, co-current flow is less efficient compared to countercurrent flow.
Cross Flow: In co-current or parallel-flow heat exchangers, the process and utility fluids flow in the same direction. This configuration is suitable when the outlet temperatures of both fluids are nearly equal. However, the temperature difference between the fluids is initially large at the inlet and decreases significantly along the length of the heat exchanger, leading to increased thermal stress and potential material failure. As a result, co-current flow is less efficient compared to countercurrent flow.
Hybrid Flow: Hybrid flow heat exchangers are created by manufacturers to combine the characteristics of the above-mentioned flow configurations. Examples of hybrid flow patterns are shell-and-tube heat exchangers, cross flow-counter flow, and multi-pass flow heat exchangers.
A heat exchanger is a type of heat transfer equipment that falls into two main categories: recuperative and regenerative exchangers.
These heat exchangers are designed with separate flow paths for the two fluids, allowing them to exchange heat simultaneously. They are further divided into two categories: indirect contact and direct contact heat exchangers.
Indirect Contact Heat Exchangers utilize a conductive wall to separate the two fluids. They are the most employed heat exchangers:
Also known as hairpin or jacketed pipe exchangers, double-pipe heat exchangers are among the simplest heat transfer devices. They consist of two concentric pipes of different diameters. The process fluid flows through the smaller inner pipe, while the utility fluid circulates through the annular space between the two pipes. The wall of the inner pipe serves as the conductive barrier for heat transfer. While the countercurrent flow pattern is most commonly used, these exchangers can also be configured for co-current flow.
Double-pipe heat exchangers are ideal for heating or cooling small flow rates of fluids. They are cost-effective, flexible in design, and easy to maintain. Typically constructed from pipes of the same length interconnected with fittings at the ends, they can be arranged to optimize floor space. However, they are less effective for higher heating duties compared to other types of heat exchangers.
Shell and tube heat exchangers consist of a bundle of tubes enclosed within a large cylindrical vessel, known as the shell. Like double-pipe heat exchangers, the wall of the tubes serves as the conductive barrier. The process fluid flows through the tubes, while the utility fluid circulates around the outside of the tubes within the shell.
Shell and tube heat exchangers are ideal for heating and cooling liquids with high flow rates, temperatures, and pressures. To increase operational efficiency, they can be designed to have multiple passes wherein one fluid comes in contact with the other several times.
Aside from the shell and tubes, other essential components of a shell and tube heat exchanger are:
Tube Sheet: The tubes are secured by inserting them into holes in a plate known as a tube sheet. The tubes extend through the tube sheet to direct the inlet and outlet flow of the process fluid. The pitch, which is the distance between the tubes, is typically 1.25 times the tube's outer diameter and can be arranged in either a triangular or square pattern.
Turbulator: The turbulator is a device that induces high velocity of the tube fluid and subsequently prevents fouling of the tubes while at the same time increasing heat transfer capacity.
Plate and Frame Heat Exchangers: Plate and frame heat exchangers utilize corrugated plates joined by gaskets, welding, or brazing to prevent fluid mixing. The plates feature inlet and outlet ports at the corners for fluid passage. The flow paths for the fluids are the spaces between the plates, arranged in alternating hot-cold-hot-cold streams. The fluids flow in a countercurrent configuration, with the hot fluid moving downward through the plates and the cold fluid flowing upward.
The design of plate and frame heat exchangers offers a large heat transfer area, high turbulence, and increased resistance to fouling. As a result, they achieve higher overall heat transfer coefficients and efficiencies compared to tubular heat exchangers. However, the fluids experience a high-pressure drop due to elevated wall shear stress, which increases pumping costs. Additionally, this type of heat exchanger is not recommended for fluids with significant temperature differences.
A crucial component of a plate and frame heat exchanger is the frame, which compresses the plates together to create a series of parallel flow channels alternating between hot and cold fluids. The corrugated metal plates are assembled into packs and secured to the frame with bolts.rubber gaskets between the plates to prevent fluids from mixing or leaking.
Plate and frame heat exchangers are classified depending on how the plates are joined.
Gasketed Plate Heat Exchangers: These heat exchangers use gaskets to connect and seal the plates. They are commonly used in industries requiring frequent sanitation, such as food and beverage processing. Gasketed plates help reduce maintenance costs due to their ease of cleaning, disassembly, and reassembly. Additional plates can be added to enhance the heat exchanger's capacity and throughput. However, a drawback of this design is the potential for leakage.
Plate Fin Heat Exchangers: These heat exchangers feature alternating layers of corrugated metal fins and flat metal plates known as parting sheets. The fluid streams flow through the spaces created between the fins and parting sheets. The parting sheets serve as the primary heat transfer surface, while the fins provide a secondary heat transfer surface and support the plates against high internal pressures. Sidebar components are included to prevent mixing of the two fluid streams. All parts are bonded through brazing, and most designs use a countercurrent flow configuration.
Plate fin heat exchangers are highly regarded for their compact design and high ratio of heat transfer area to heat exchanger volume, which makes them space-efficient and lightweight. They also achieve efficiencies greater than 95%. These heat exchangers are commonly used in aerospace, cryogenic air separation, and refrigeration applications.
Direct Contact Heat Exchangers Direct contact heat exchangers do not use a conductive partition and instead rely on direct contact between the fluids for heat exchange. They are ideal for situations involving two immiscible fluids or when one of the fluids undergoes a phase change. Due to their simpler design, they are more cost-effective. These exchangers are commonly used in seawater desalination, refrigeration systems, and waste heat recovery. Examples of direct contact heat exchangers include direct contact condensers and natural draft cooling towers. cooling towers, driers, and steam injection.
Also known as regenerators or capacitive heat exchangers, regenerative heat exchangers use a heat storage medium that comes into contact with both the hot and cold fluids, which are typically gases. They are commonly used in power plants, glass and steel manufacturing, and heat recovery systems. However, there is a risk of contamination since the same medium interacts with both fluid streams.
There are two types of regenerative heat exchangers:
Static Regenerators: Static regenerators, or fixed bed regenerators, do not have mechanical parts that facilitate the flow of hot and cold fluids. The fluids are made to pass through the channel by a system of pipes and ducts, fitted with valves that act as a "switch" during the separate release of the hot and cold fluids. The hot fluid is made to flow first at a certain length of time. Once the heat storage medium accumulates enough heat, the valve connecting the reservoir of the hot fluid is switched off. The cold fluid is then allowed to flow through the channel, which absorbs the heat coming from the hot fluid.
Operation of static regenerators is semi-batch since the flow of the fluids is intermittent. To achieve a continuous operation, two channels must be used.
Dynamic Regenerators: These heat exchangers feature a rotating element that contains the heat storage medium. The hot and cold fluid streams flow simultaneously on opposite sides of the rotating wheel, aligned parallel to its axis of rotation. As the wheel turns, it absorbs heat from the hot fluid stream and releases it to the cold fluid stream as it rotates.
Adiabatic wheel heat exchangers feature a rotating wheel and an intermediate fluid that aids in the heat exchange process. The wheel is designed with threaded surfaces to enhance its heat transfer area and rotates through the fluid where the heat exchange occurs. This distinctive structure enables effective heat transfer between gases. Adiabatic wheel heat exchangers are highly efficient and are particularly valuable in processes that require minimal heat exchange.
Pillow plate heat exchangers are known for their low pressure loss and exceptionally high heat transfer coefficient. Their unique design, which differs significantly from conventional heat exchangers, has contributed to their widespread use and popularity. Central to their design are three-dimensional, lightweight, wavy plates—hence the term "pillow." These plates are stacked into plate banks and include an inlet distributor and outlet collector. Each plate consists of laser-welded metal sheets stacked on top of one another.
During the manufacturing of the plates, after welding, they undergo a hydroforming process where they are inflated using pressures ranging from 60 to 80 bar. This process creates channels that are hermetically sealed. For the hydroforming to be effective, the laser-welded plates must have uniform thickness.
Pillow heat exchangers combine the pressure and temperature resistance of shell and tube heat exchangers with the cost-effectiveness and compact design of plate heat exchangers. Their reduced heat transfer surface contributes to process stability. The wavy pattern of the plates is crucial for their thermohydraulic performance, promoting turbulent flow of the heat carriers within.
A plate heat exchanger (PHE) is a compact type of heat exchanger that utilizes a series of thin metal plates to transfer heat from one fluid to the other. These fluids are typically at different temperatures...
A shell and tube heat exchanger (STHE) is a type of heat exchanging device constructed using a large cylindrical enclosure, or shell, that has bundles of perfectly spaced tubing compacted in its interior. Heat exchanging is the transfer of heat from one substance or medium to a similar substance or medium...
Air cooled chillers are refrigeration systems that cool fluids and work in tandem with the air handler system of a facility. Air cooled chillers are types of chillers that rely on the use of fans to reject heat outside the...
A chiller is a cooling mechanism designed to produce fluids that can lower temperatures by removing heat from the fluid. The type and use of a chiller depends on the required temperature and kind of refrigerant, which can be a liquid or a gas...
Cooling towers are specialized heat exchangers that remove heat from water mainly by means of latent heat loss from evaporation while coming into contact with an airstream. Aside from evaporative cooling, water is also cooled by sensible heat transfer due to the temperature difference between air and water...
A glycol chiller is a chilling system that uses a percentage of glycol mixed with water to create extremely low temperatures far beyond the freezing point of water. The two types of glycol are ethylene glycol based or propylene glycol based...
Laser cooling is a multi-process that includes a number of techniques in which atomic and molecular samples are cooled down to a temperature near absolute zero. These techniques depend on...
Open loop cooling tower makes use of direct contact with the air in order to cool down the water. It is essentially a heat exchanger. In these types of cooling towers, there is the partial heat transfer due to heat exchange between...
A water chiller, or chilled water system, is a type of refrigeration system which uses water as a secondary refrigerant. They are used for larger, more complex, heating, ventilating, air conditioning, and refrigeration (HVACR) applications...