Anodized Aluminum
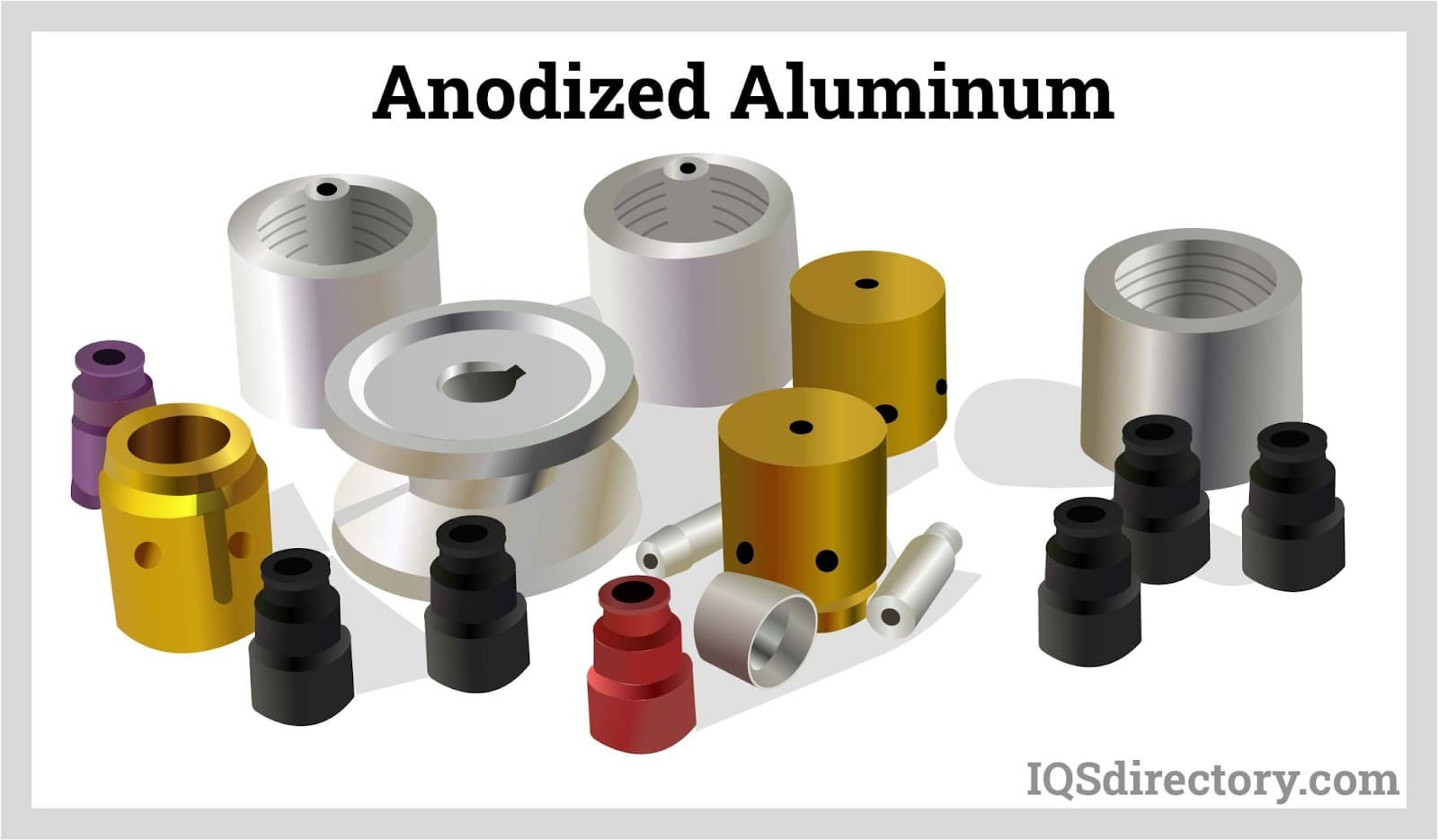
Anodized aluminum is aluminum that has undergone an anodizing process to create an exceptionally durable, corrosion-resistant, and highly aesthetic surface. Anodizing creates a stable aluminum oxide layer fully integrated with...
Please fill out the following form to submit a Request for Quote to any of the following companies listed on
This article will take an in-depth look at heat treating.
The article will bring more detail on topics such as:
This section delves into the heat treatment process and its significance.
Heat treatment involves subjecting a material to cycles of heating and cooling to improve its traits, strength, and performance.
The application of heat treatment on metals can enhance malleability for easier forming or increase hardness for greater strength. This process includes various techniques to modify a material's physical characteristics, such as heating or cooling metals to achieve desired qualities.
This part elaborates on the fundamentals and goals of heat treatment.
Heat treatment processes involve heating and cooling metals but vary primarily in three aspects: the temperatures for heating, cooling speeds, and the quenching methods used to reach specific characteristics.
Utilizing suitable equipment is crucial for effective metal heat treatment. This ensures precision in managing heating, cooling, and quenching conditions. The heating chamber must be appropriately equipped with the correct size, type, and gas mixture to accurately control the temperature. Furthermore, selecting a compatible quenching medium ensures the proper cooling of the metal.
The heat treatment process typically consists of three primary steps:
The key goal during the heating phase is to achieve even temperature distribution across the metal. Gradual heating is essential to prevent different parts from expanding at varying rates, which can lead to distortion or cracking. The optimum heating rate depends on several factors:
During this stage, the metal is kept at a designated temperature until the desired internal structure is achieved. The "soak time" is the duration the metal remains at this temperature, determined by its chemical makeup and mass. In cases of uneven cross sections, soaking time typically considers the largest part.
Usually, metals should not be heated straight from room temperature to the soaking temperature in one step. Gradual heating to just below structural transformation points ensures uniform temperature distribution throughout the metal.
After this preheating, the metal is heated quickly to the final temperature. Complex items might require multiple preheating phases to minimize warping.
This phase involves cooling the metal to room temperature, tailored to the metal type and possibly involving a liquid, gas, or a combination. The cooling rate depends on both the metal and the medium, making it critical in shaping the metal's ultimate properties.
Quenching, a rapid cooling process, involves using air, water, oil, brine, or other substances. Frequently linked with hardening, quenching doesn’t always lead to hardening. For instance, water quenching is part of copper annealing, while some metals require slow cooling to harden.
Quenching isn’t suitable for every metal due to possible cracking or warping. Generally, water or brine can rapidly cool metals, whereas oil mixtures are preferable for slower cooling. For carbon steels, water is typically used for hardening; oil serves for alloy steels hardening, while water quenches nonferrous metals.
Heat treatment achieves several key objectives, including:
The different types of heat treatment processes are as follows:
This process entails introducing carbon atoms into the surface and near-surface layers of steel to enhance its surface hardness. It strengthens the metal part’s exterior and improves its microstructure and mechanical properties by allowing carbon to penetrate the surface.
The depth of carbon diffusion is influenced by factors such as the carbon concentration in the atmosphere, the material type, the applied temperature, and the duration of exposure. Hardening occurs after the part is quenched. Carburizing not only increases surface hardness but also improves fatigue strength and wear resistance.
This process is ideally suited for steels with a low carbon content, ranging from 0.05% to 0.3%, and can be applied to parts of varying complexity. Carburizing is particularly effective for metals that require enhanced wear resistance, durability, and fatigue strength, and is typically performed at temperatures between 1562°F and 1832°F (850°C to 1000°C).
Like carburizing, nitriding is a thermochemical case-hardening technique used to enhance the hardness, fatigue life, and wear resistance of metal components. This process involves diffusing nitrogen into the surface of the metal to achieve hardening. Nitriding involves heating a ferrous material and then exposing it to active nitrogen at precisely controlled, subcritical temperatures.
Temperatures applied range between 752°F and 1094°F (400°C to 590°C) during the exposure to active nitrogen, which is below the temperature of the final tempering to ensure that the metal’s mechanical properties are not affected. Nitriding is most effective when carried out on alloy steel materials containing nitride-forming elements. This enables the formation of alloy nitride precipitates with the metal by the nitrogen with ease.
Steels compatible with the nitriding process include 4140, 4130, 4150, 8640, 4340, 15-5, 17-4, 4xx stainless, and nitralloy 135. In addition to its hardening benefits, nitriding can provide anti-galling, anti-seizing, and anti-welding properties. Nitrided metals retain their hardness at temperatures up to 1000 degrees Fahrenheit, making them ideal for a wide range of applications such as bearings, dies, gears, shafts, spray nozzles, feed screws, orifice disks, splines, valves, cylinder liners, and piston rings.
Hardening is a metalworking process conducted in a vacuum or endothermic atmosphere. Unlike nitriding and carburizing, this is a through-hardening technique that strengthens the metal from the surface to the core without altering the surface carbon content. The process involves heating the metal above its austenitizing temperature, typically in an enclosed furnace. During tempering, metals are heated to temperatures ranging from 698°F to 1004°F (370°C to 540°C). For improved toughness, temperatures between 1004°F and 1112°F (540°C to 600°C) are used.
The austenitizing temperature, which varies depending on the material, is the temperature at which the metal’s crystal structure changes from ferrite to austenite. This principle applies to various alloys, such as titanium, aluminum, and high-nickel alloys, though their structures differ.
Once the metal has transformed into austenite, it is rapidly quenched in oil to convert the crystal structure to martensite. The metal is then tempered to achieve the desired hardness and reduce brittleness. This heating and quenching method is commonly used to harden steel, and similar techniques can also be applied to aluminum, despite its lack of carbon. Hardened metals find applications in various fields, from construction materials to automotive components.
Tempering Temperatures Chart | |||
---|---|---|---|
Color | Hardest | Approximate Temperature (°C) | Uses |
Pale Straw | ↑ | 230 | Lathe tools, Scrapers, Scribers |
Straw | 240 | Drills, Milling Cutters | |
Dark Straw | 250 | Taps & Dies, Punches, Reamers | |
Brown | 260 | Plane Blades, Shears, Lathe Centres | |
Brown/Purple | 270 | Scissors, Press Tools, Knives | |
Purple | 280 | Cold Chisels, Axes, Saws | |
Dark Purple | ↓ | 290 | Screwdrivers, Chuck Keys |
Blue | Toughest | 300 | Springs, Spanners, Needles |
Annealing involves heating a metal part to a specific temperature, maintaining that temperature, and then slowly cooling it. This process relieves residual stresses caused by activities such as cutting, cold working, or machining. Annealing decreases hardness, yield strength, and tensile strength, thereby enhancing ductility and reducing brittleness.
The major purpose of annealing is to make metals more amenable to processes of manufacture like forming, shaping, stamping, hydroforming, forging, bending, and machining. Stress relief includes heating a metal at a relatively low temperature and then allowing it to cool uniformly. The ideal temperature is below 1000 degrees Fahrenheit for copper or steel and below 400 degrees Fahrenheit for aluminum. Like annealing, stress relief purpose is to reduce internal stresses created during machining, forming, or rolling processes.
Annealing is conducted at much higher temperatures compared to stress relief processes, with steel and copper typically heated to 1600°F (870°C) or more, and aluminum to 600°F (315°C) or higher. This elevated temperature allows annealing to relieve more stress than simpler stress relief treatments. Annealing and stress relieving can be carried out using vacuum, endothermic, or air furnaces, and these treatments are applicable to various metals and plastics.
This metal hardening process involves cooling a metal part to cryogenic temperatures to alleviate stress and minimize retained austenite after quenching. Cryogenic treatments typically involve cooling to temperatures as low as -200°F (-128°C) or colder, while sub-zero cooling can reach temperatures of -100°F (-73°C), enhancing the hardening effect.
Cryogenic treatment relieves internal stresses, enabling more precise machining and tighter tolerances. This process enhances the strength of metals, making them suitable for high-performance applications across various industries, including automotive, aerospace, medical, and defense. For example, cryogenic treatment is used to prepare aluminum for extremely cold environments, such as those in space. Other applications for cryogenically treated metal parts include steel tools, cutting tools, and high-performance racing components.
The primary goal of normalizing is to eliminate internal stresses that arise from cold working processes. In this method, steel is heated above its upper critical temperature and then allowed to cool in air. Normalizing enhances the material’s electrical and mechanical properties, machinability, and tensile strength. This heat treatment process is performed to return the material to a standard, uniform structure.
Normalizing involves treating castings and forgings to refine grain structure and relieve stresses. This process is typically applied after cold working operations such as stamping, rolling, and hammering.
In this process, steel is heated in an environment containing sodium cyanide, resulting in the deposition of nitrogen and carbon atoms on its surface. This treatment increases the hardness of the steel.
During the cyaniding process, the metal part is immersed in a molten cyanide salt bath maintained at 950 degrees Celsius. The salts used include sodium carbonate, sodium chloride, soda ash, and sodium cyanide. The metal remains in the molten cyanide for approximately 15 to 20 minutes. As sodium cyanide decomposes, it produces carbon and nitrogen from carbon monoxide, which are then diffused into the surface, hardening it. After this, the part is removed from the bath and quenched in oil or water.
Case hardening involves hardening the outer layer of a metal part while leaving the interior relatively soft. For metals with low carbon content, such as steel and iron, additional carbon is infused into the surface. This process is typically used as a final step after the metal has been machined.
Case hardening involves applying high heat along with various elements and chemicals to create a hardened outer layer. While hardening can make metals more brittle, case hardening is advantageous for applications that need a flexible core combined with a durable wear-resistant surface. The temperatures used in case hardening range from 320°F to 428°F (160°C to 220°C).
This is a process whereby the hardness and strength of aluminum alloys are increased. These aluminum alloys are a specific subset namely the cast and wrought alloys that are precipitation hardenable. The alloys of aluminum that are precipitation hardenable include the 8xxx, 7xxx, 6xxx, 2xxx series. To add on top, there may be a requirement for annealing for parts that have experienced strain hardening during the process of their forming.
Common heat treatments for aluminum include homogenizing, annealing, natural aging, solution heat treatment, and artificial aging. The furnace temperatures for these processes typically range from 203°F to 401°F (95°C to 205°C). It’s important to note that aluminum heat treating differs significantly from the heat treating of steel.
This heat treating process involves using a filler metal to join two pieces of metal. The filler metal has a lower melting point than the metals being joined. It can either be added to the joint during the heating of the parts or placed beforehand.
In brazing parts with small clearances, the filler can flow into the joint through capillary action. The molten filler’s temperature exceeds 1544°F (840°C). The joints made by the brazing process are usually stronger than soldered joints. Brazing can be carried out on multiple metals. Before initiating the brazing process, it is important to prepare the surfaces by chemical or mechanical cleaning.
This heat treating process utilizes electromagnetic induction to precisely heat metals. It relies on induced electrical currents within the metal to generate heat. This method is highly favored for bonding, hardening, or softening metals and other conductive materials. In contemporary manufacturing, induction heat treating offers an effective blend of consistency, speed, and control.
While the fundamental principles are well-established, advances in solid-state technology have made induction heat treating a cost-effective and straightforward method for various applications, including treating, joining, heating, and materials testing. This process allows precise control over physical characteristics through the use of an electrically heated coil.
Induction hardening can be tailored to each section of a metal part, enhancing specific features without compromising overall ductility. For example, it provides superior durability to shaft sections and bearing journals while maintaining the necessary flexibility for handling shock loads and vibrations. It also enables hardening of intricate parts like valve seats and internal bearing surfaces without causing distortion, allowing for targeted improvements in durability and ductility as required.
Heat treatment for steel can have various types, which are:
The goal of annealing is to counteract the effects of hardening. This process is used to relieve stress, enhance ductility, soften the metal, and improve its grain structure. Without proper preheating, welding can create temperature inconsistencies within a metal part, with some areas being molten while others remain at room temperature.
Such inconsistencies can weaken the metal, causing internal stresses and creating hard, brittle spots as the weld cools. Annealing effectively addresses these issues by relieving internal stresses and correcting common problems associated with welding.
Normalizing steel is crucial for eliminating internal stresses caused by machining, heat treatment, forming, forging, casting, or welding. Uncontrolled stress can lead to metal failure, so normalizing steel before hardening ensures the success of projects by addressing these stresses.
Hardening aims not only to increase the strength of steel but also to enhance its overall robustness. While it boosts strength, hardening also reduces ductility, making the metal more brittle. After hardening, tempering may be necessary to mitigate some of the brittleness.
Typically, steels are hardened using the initial stages of heat treatment: slow heating and soaking at a uniform temperature. The third stage of the process may differ.
During hardening, metals are rapidly cooled by immersing them in oil, water, or brine. Most steels require this rapid cooling, known as quenching, to achieve hardness, although a few can be air-cooled. As alloys are added to steel, the required cooling rate decreases, reducing the risk of warping or cracking.
Following hardening, whether by flame or case, the internal stresses from rapid cooling result in steel that is excessively hard and brittle. Tempering can address this by reducing brittleness and relieving internal stresses. During tempering, the hardness achieved from hardening is decreased, and specific physical properties are developed.
Tempering always follows hardening, softening the steel in the process. Although some softness is unavoidable, the degree of hardness lost can be controlled by adjusting the tempering temperature. Unlike other heat treatments conducted at temperatures above the metal’s upper critical point, tempering occurs at temperatures below this point.
The heat treatment of stainless steel varies based on the type of stainless steel and the requirements of the final product. Methods such as hardening, annealing, and stress relieving enhance the ductility and corrosion resistance of the metal while also producing hard structures capable of withstanding abrasion and high mechanical stresses. Stainless steel types include martensitic, austenitic, and ferritic, each requiring different heat treatment approaches.
This type is the most widely used among stainless steels. It is characterized by its austenitic structure at normal temperatures, with no phase changes occurring. Heat treatment cannot harden this stainless steel type; instead, hardening is achieved through cold working. The most common heat treatment for austenitic stainless steel is solution treatment.
This stainless steel type maintains a ferritic structure at both normal and elevated temperatures, without undergoing a phase change. However, when it contains elements such as nitrogen and carbon, it can form an austenitic structure at high temperatures. This steel type cannot be hardened through heat treatment and is typically subjected to annealing to reduce internal stresses and facilitate further processing.
Martensitic stainless steel is characterized by a distinct phase change point. It has an austenitic structure at high temperatures and can transform into martensite during cooling. This transformation hardens the steel. Due to its high chromium content and good hardenability, martensitic stainless steel can undergo various heat treatment processes such as quenching and tempering.
This chapter will explore the different applications and advantages of heat treating.
Heat treating is primarily used in metallurgy, but it is also employed in the production of various materials, such as glass. Additionally, heat treatment is applied in several other areas, including:
Heat treating can:
Heat treating can alter or enhance the properties of a metal, including:
Heat treatment enhances workability and machinability:
Heat treating reduces internal stresses, which improves the ease of manufacturing. For instance, if a metal is too hard to shape or machine, it can be stress-relieved or annealed to lower its hardness. Similarly, if plastic deforms post-machining, annealing or stress relieving can prevent this deformation. Induction flame heat treating can selectively soften specific areas of a part while leaving the rest unaffected.
Heat treatment increases wear resistance and durability:
Heat treating, particularly through hardening, can enhance a part's wear resistance. This process can harden metals either on the surface or throughout, making them stronger, more durable, and more resistant to wear.
Heat treatment boosts strength and toughness:
There is often a trade-off between strength and toughness; as strength increases, toughness may decrease, potentially leading to brittleness. Heat treatment can specifically improve tensile strength, yield strength, and fracture toughness. Case hardening, for example, increases strength but may require tempering to reduce brittleness. The degree of tempering is adjusted based on the desired ultimate strength of the material.
Heat treatment improves magnetic properties:
Materials such as 1008 or 316 can become magnetized when work-hardened. A specialized annealing process can reduce magnetic permeability, which is crucial for parts used in electronic environments.
Heat treating or heat treatment is a process in which controlled heat is applied to a material to alter its properties like strength, durability, wear resistance, etc. There are many processes of heat treatment available including nitriding, carburizing, induction flame hardening for treating only a single area of a metal part, brazing for joining two metal parts.
All these methods of heat treatment offer different results when applied. Therefore the stages involved in each heat treatment process together with the conditions specified must be taken into consideration when selecting a heat treatment method, in order to come up with a good product with the desired properties.
Anodized aluminum is aluminum that has undergone an anodizing process to create an exceptionally durable, corrosion-resistant, and highly aesthetic surface. Anodizing creates a stable aluminum oxide layer fully integrated with...
Industrial coatings are a type of substance that is spread over a surface of various derivatives like concrete or steel. They are engineered chemically to give protection over industrial products that include pipelines and...
Metal products are found everywhere in our houses at work. In its raw form, plucked from nature, metal is hard, crude, and unattractive. To make the best use of it, it needs to be finished, polished, and...
Metal plating refers to a process where a thin layer of metal coating is placed on the surface, or substrate, of a metal part, component, or product. The process can consist of electroplating, which...