Band Heaters
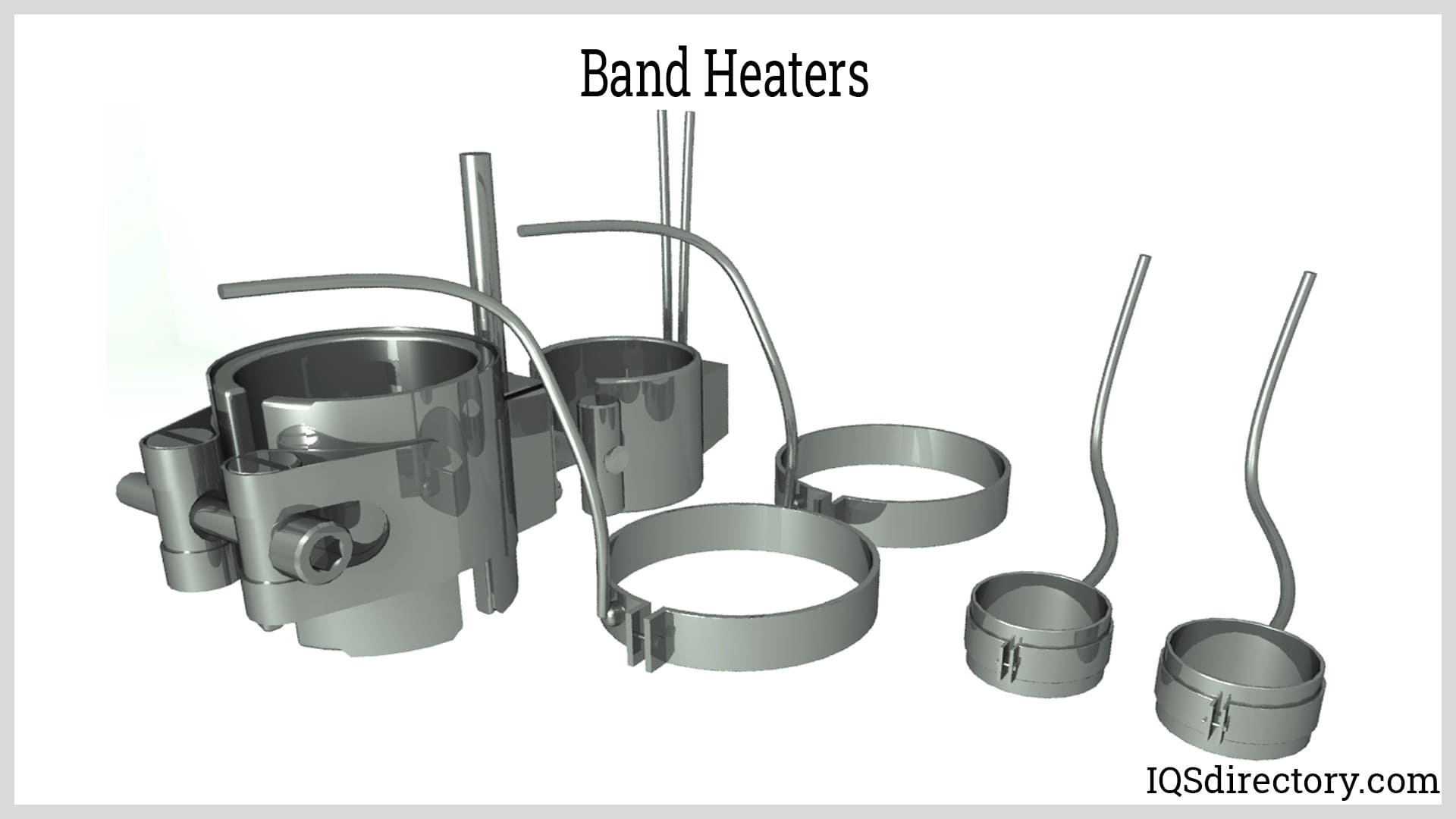
A band heater is a heating device that clamps onto objects to provide external heat using radiant and conductive heating. The different mounting methods of band heaters makes it possible to secure them tightly and...
Please fill out the following form to submit a Request for Quote to any of the following companies listed on
This article presents a comprehensive guide about heating elements. Read further to learn more about:
A heating element is a component or material designed to transform electrical energy into heat through a phenomenon known as Joule heating. This process happens when an electric current travels through a conductor, with electrons or charge carriers interacting with the atoms or ions within the conductor. These interactions create friction on an atomic scale, which manifests as heat. The heat produced is quantified by Joule's first law (or the Joule-Lenz law), which states:
P = IV or P = I²R
These formulas indicate that the heat generated is influenced by the current, voltage, and the conductor's resistance. The resistance of the conductor is a key consideration in the design of heating elements.
Joule heating happens across all conductive materials, with the exception of superconductors, albeit to varying extents. Materials with lower electrical resistance emit less heat as charge carriers pass through them with ease, whereas materials with higher resistance generate greater heat. Superconductors are unique in that they allow current to pass without producing heat. Generally, the heat generated in conductors is seen as energy loss. For instance, when powering equipment, some electrical energy results in unwanted heating, known as copper loss, which is not beneficial for practical work.
Electrical heating elements are close to 100% efficient in converting electrical energy into thermal energy since nearly all the energy supplied is turned into heat. These elements might also emit energy as light and radiation. However, this level of efficiency is particularly true for resistors. Minor losses occur due to the intrinsic capacitance and inductance of materials, transforming electrical energy into electric and magnetic fields, respectively. Moreover, the overall efficiency can decrease due to heat escaping into the surroundings from the heater or the process fluid. Therefore, to ensure optimal use of generated heat, the heating system should be insulated effectively.
Nearly all conductors generate heat when an electric current passes through them, but not all are optimal for use as heating elements. To ensure efficient performance and long-term durability, the preferred heating element materials must have a precise balance of electrical, thermal, mechanical, and chemical properties. These make them suitable for a variety of industrial heating applications such as furnaces, electric ovens, kilns, and water heaters. Below are the key properties critical to effective heating element design and selection:
When evaluating and purchasing heating elements, industrial buyers and engineers often consider additional factors such as cost-effectiveness, energy efficiency, compatibility with specific voltage and wattage requirements, and ease of integration with existing heating systems. Custom heating elements—whether cartridge heaters, band heaters, or infrared heating elements—can be designed to address unique environmental conditions and process specifications, making them suitable for industries including manufacturing, food processing, and laboratory equipment. Understanding these properties allows buyers to choose between electric heating element types (e.g., metallic vs. ceramic) and ensures compliance with safety certifications and industry standards.
In summary, the right choice of heating element material and configuration directly impacts overall system performance, safety, and operational lifetime. For expert guidance or specific product recommendations, contacting leading heating element manufacturers and suppliers is highly recommended.
The selection of materials for heating elements is determined by thermal stability, electrical resistivity, oxidation resistance, and operating environment. The most commonly utilized heating element materials in industrial and commercial applications include nickel-chromium (nichrome) alloy, iron-chromium-aluminum (FeCrAl) alloy, molybdenum disilicide, and silicon carbide. These materials are ideal for electric heating elements because they withstand high temperatures, offer reliable performance under electrical load, and resist oxidation, making them suitable for open-air and industrial furnace environments.
Another category of heating element materials includes graphite, molybdenum, tungsten, and tantalum—refractory elements that excel in ultra-high-temperature conditions. However, because these advanced materials are prone to oxidation at elevated temperatures, they are predominately used in vacuum furnaces or controlled-atmosphere applications where oxygen is absent or minimized. This critical property is essential in applications such as metallurgy, crystal growth, and specialty material processing.
Nickel-chromium alloys, often referred to as nichrome wire, are among the leading electrical heating element materials due to their outstanding combination of ductility, high resistivity, corrosion resistance, and superior oxidation resistance at elevated temperatures. Standard compositions, such as 80% nickel and 20% chromium, provide a balance of high electrical resistance and mechanical flexibility, allowing these alloys to be easily shaped into coils and wires. Applications include home appliances (toasters, hair dryers, space heaters), laboratory heating, and industrial kiln heating elements. Nichrome wires can reach maximum operating temperatures of approximately 1,100 to 1,200°C, making them suitable for medium- to high-temperature heating solutions with long service life.
Iron-chromium-aluminum alloys, widely recognized under the Kanthal brand, represent a major advancement in heating technology for industrial furnaces, tubular heating elements, and electric ovens. Typical Fe-Cr-Al compositions consist of 20–24% chromium, 4–6% aluminum, with iron as the base metal. These alloys offer higher operating temperatures—up to 1,300 to 1,400°C—compared to nickel-chromium counterparts and feature excellent resistance to oxidation and sulfur attack. Fe-Cr-Al heating elements are commonly used in glass kilns, ceramic manufacturing, and process heating, as well as high-temperature dryers and heat treat furnaces. Economically, they are favored for their lower cost due to iron's price stability.
Advanced Fe-Cr-Al alloys can be manufactured via powder metallurgy processes, which finely grind the alloy into powder, compress it into a die, and then sinter or hot-press it in a controlled atmosphere. The incorporation of oxide dispersoids during this process enhances high-temperature strength, creep resistance, and mechanical durability, extending the lifespan in harsh operating environments.
Molybdenum disilicide (MoSi₂) is a premium refractory cermet material recognized for its exceptional oxidation resistance, high melting point (over 2,000°C), and electrical conductivity. MoSi₂ heating elements are indispensable in laboratory and industrial high-temperature furnaces, glass processing, and sintering of advanced ceramics. Common fabrication methods include mechanical alloying, combustion synthesis, shock synthesis, and advanced hot isostatic pressing to achieve optimal density and material purity. MoSi₂ elements are capable of reaching continuous operating temperatures up to 1,900°C, making them ideal for demanding high-temperature electric heating solutions.
Despite their extraordinary temperature capabilities, MoSi₂ elements are relatively brittle at ambient temperature and susceptible to thermal shock. Their strength and toughness increase dramatically above 1,000°C, at the material's brittle–ductile transition point. The most widely used MoSi₂ element design is the U-shaped (2-shank) hairpin form, suspended in both vertical and horizontal furnace arrangements to maximize thermal efficiency and process uniformity. To further optimize performance, these elements are often paired with ceramic insulation which helps to minimize heat loss and improve energy efficiency in high-temperature processing environments.
Silicon carbide heating elements, fabricated from high-purity SiC grains by recrystallizing or reaction bonding above 2,100°C, are widely used for electric furnaces operating at temperatures up to 1,600–1,700°C. As a robust ceramic, silicon carbide exhibits excellent thermal conductivity, corrosion resistance, and mechanical strength. SiC heaters are inherently porous, enabling interaction with furnace atmospheres, which can influence element aging and resistance changes over time—a factor mitigated by adjustable power supplies that maintain constant heating performance throughout the element's service life. Silicon carbide's ability to sublimate at 2,700°C, combined with its low thermal expansion and resistance to chemical attack, make it especially valuable for heat treatment, metallurgy, laboratory muffle furnaces, and semiconductors manufacturing.
SiC heating rods do not sag under their own weight at elevated temperatures, eliminating the need for internal supports, even in large-scale furnace designs. This, along with their excellent thermal shock resistance and longevity, contributes to their popularity in high-temperature industrial process heating and thermal oxidation environments.
Graphite heating elements, composed of high-purity carbon, are essential for applications requiring operation above 2,000°C, including vacuum heat treatment, high-temperature sintering, and crystal growth. The unique crystalline structure of graphite provides high thermal and electrical conductivity, minimal thermal expansion, and exceptional resistance to thermal shock. However, graphite is prone to oxidation at temperatures above 500°C, limiting its use in atmospheres where oxygen or moisture is present. As a result, it is the material of choice for vacuum and inert-gas furnace systems, where it achieves extended service life and maintains dimensional stability without degradation or embrittlement.
Refractory metals—molybdenum, tungsten, and tantalum—are renowned for their exceptional melting points, high thermal and electrical conductivity, and chemical stability in oxygen-free environments. Tungsten heating elements, found in vacuum furnaces and electron-beam systems, can operate at temperatures exceeding 2,500°C, making them indispensable for advanced material processing and high-temperature heat treatment. Molybdenum and tantalum are valuable for similar applications, offering optimal performance in vacuum or reducing atmospheres due to their reactivity with oxygen, nitrogen, and hydrogen at moderate temperatures (300 to 500°C). Cost and material availability often drive the selection among these refractory metals, as tungsten tends to be the most expensive, while molybdenum strikes a balance between performance and affordability.
These metals are typically specified for sensitive thermal processing, semiconductor manufacturing, and specialty glass production, where precision, consistency, and extreme temperature capability are paramount.
Positive Temperature Coefficient (PTC) materials represent a class of self-regulating heating elements widely used in safety-critical or low-wattage applications. Standard PTC materials include conductive rubbers and ceramics, such as barium titanate or PDMS infused with carbon nanoparticles. PTC heaters deliver rapid warm-up due to their low initial resistance and inherently limit power draw as their resistance rises with increasing temperature, stabilizing output and preventing overheating. This makes them ideal for wearable heating, automotive seat warmers, underfloor heating systems, and medical device heating solutions.
The technology behind PTC heating elements reduces the need for external thermal controls, as the material itself ensures precise and automatic temperature regulation. This feature enhances safety and simplifies design in consumer appliances and industrial systems where temperature uniformity, efficiency, and protection from thermal runaway are essential considerations.
Choosing the right heating element material depends on the specific industrial application, required temperature range, environmental conditions (such as exposure to air, vacuum, or process gases), and cost considerations. For further technical data or assistance in selecting optimal heating element materials for your industrial furnace, electric heating system, or custom thermal processing application, consult with experienced manufacturers or refer to comprehensive industry resources.
A heating system includes more than just the heating element. It also comprises terminations, leads, insulation, packing, sheath, and seals. Heaters come in various forms and configurations to meet specific application needs. Below are some of the most common types of heaters and their applications.
While heating elements generally operate on the same principle, their performance and service life are influenced by several factors. Key specifications for heaters include power or wattage, maximum operating temperature, type of process fluid, sheath material, and power supply (voltage and frequency). Additionally, factors such as fluid flow and temperature control must also be considered to optimize performance.
A band heater is a heating device that clamps onto objects to provide external heat using radiant and conductive heating. The different mounting methods of band heaters makes it possible to secure them tightly and...
A cartridge heater is a cylindrical tubular heating device that provides concise and precise heating for various forms of materials, machinery, and equipment. Unlike an immersion heater, a cartridge heater is inserted into a hole in the item to be heated to furnish internal radiant heat...
Ceramic heaters are electric heaters that utilize a positive temperature coefficient (PTC) ceramic heating element and generate heat through the principle of resistive heating. Ceramic materials possess sufficient electrical resistance and...
Electric heating is produced by using a known resistance in an electric circuit. This placed resistance has very few free electrons in it so it does not conduct electric current easily through it. When there is resistance in...
A flexible heater is a heater made of material that can bend, stretch, and conform to a surface that requires heating. The various forms of flexible heaters include polyimide film, silicone rubber, tape...
An immersion heater is a fast, economical, and efficient method for heating liquids in tanks, vats, or equipment. Known as bayonet heaters, they have heating elements that can be directly inserted into a container of water, oil, or other material in order to heat the entire contents...
Infrared heating is a heating method used to warm surrounding bodies by infrared radiation. Thermal energy is transferred directly to a body with a lower temperature through electromagnetic waves in the infrared region...
Radiant heaters are systems that generate heat internally and then radiate it to the nearby objects and people. The sun is a basic example of a radiant heater. When we feel warm on our bodies on a sunny day...
The idea of an electric heater seems to be out of place in modern society since most buildings have a sophisticated central heating system. That may be true, but electric heaters can be a helpful way of saving energy while providing efficient heating...