Cord Reels
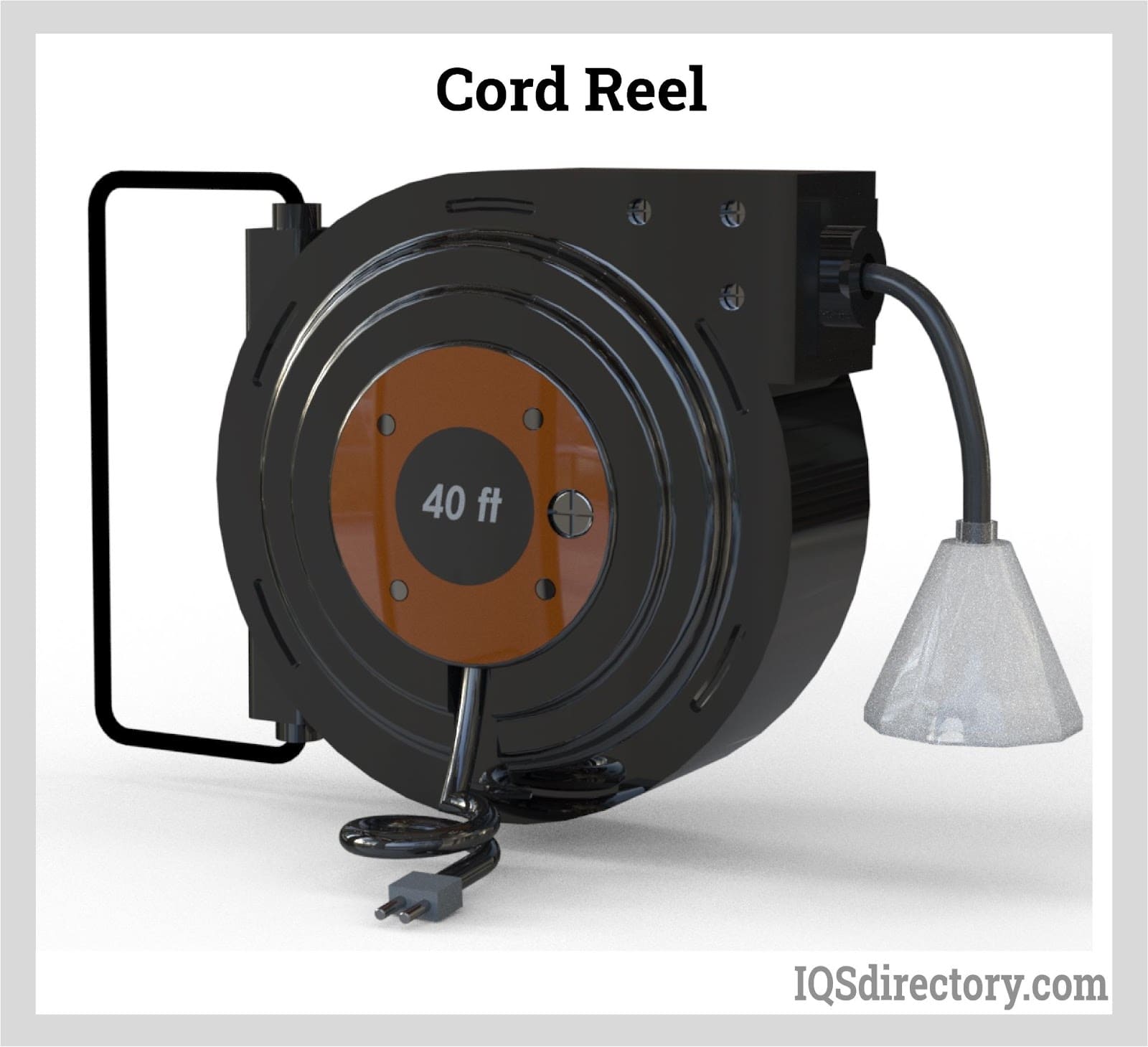
Cord reels are devices that hold extension cords that are used to supply power to electrical equipment or devices located far from the power outlet. They are also used in storing long extension cords properly...
Please fill out the following form to submit a Request for Quote to any of the following companies listed on Cable Reels .
This article will take an in-depth look at cable reels.
The article will bring more detail on topics such as:
In this chapter, we delve into the fundamentals of cable reels by examining their definition, design, essential features, and the factors to consider when selecting the right cable reels.
Cable reels are crafted to store, wind, and unwind conductive or lifting cables efficiently. Electric cable reels are equipped with contacts that ensure power continuity during the winding process. These devices are essential for coiling long, continuous materials such as cables, wires, paper, and other items for storage or transit purposes. The designs of reels vary from basic storage solutions to sophisticated self-winding models, some of which support live connections, allowing hoses or electrical wires to be utilized directly from the reel.
Cable reels can be rewound using several techniques, such as manual crank, electric power, hydraulic systems, pneumatic force, and spring technology.
The five principal configurations for cable reels include collapsible, portable, live connection, reel and cable assemblies, and storage reels.
Critical attributes of cable reels include the flange diameter, core diameter, inside traverse, the external diameter of the cable intended for the reel, and the cable length.
Essential considerations in choosing cable reels are:
Safety – Roller systems reduce operator fatigue and promote ergonomic handling, maintaining a consistent cable length with each draw. They are safer compared to reel jack stands when used with optional tie-down kits.
Specifications for Cable Length:
Various types of cable reels include:
Wooden cable reels, as the name suggests, are made from wood and are designed for applications requiring the transportation of heavy loads. These reels are used to spool wires, ropes, and electrical cables. They can be customized with various traverse lengths and flange diameters to accommodate different types of products.
The process begins with the creation of the flanges. These are the circular portions located at each end of the core. Two layers of lumber are attached perpendicularly to form a solid piece, resulting in a square flange. The square flange is then shaped into a circular form using a bandsaw, which trims away the edges. Lastly, the circular flange is smoothed to ensure a flat surface along the newly cut edges.
Next, the flanges are customized according to user needs. Common adjustments include the diameters of the start hole and arbor hole, the number of bolt holes, and the angles of various holes.
Thirdly, the staves for the reel's core are made from lumber. The core, also known as the drum, requires straight-edged lumber that must be rounded before use in the reel. Regular lumber is fed into a machine that shaves the edges and creates curved boards, called staves, which will form the drum of the reel. Finally, the flanges and staves are bolted together.
The process begins with logs being soaked and heated to soften the wood, a step necessary before cutting veneers into suitable shapes and sizes. Depending on the wood type, this process can take anywhere from 12 to 40 hours. Each treated log is individually placed on a peeler lathe, where it is fed into a full-length knife blade. This reduces the log's diameter to approximately 3 to 4 inches, and any remaining wood is removed from the lathe and replaced with a fresh log. The veneer is then cut into usable widths according to industry standards for plywood sheets.
The veneer is often sorted by grade, a process that can be done manually or with optical scanners. To reduce moisture content and shrink the veneer to the desired size, it is stored in a low-humidity environment known as a dryer. The appropriate pieces of veneer are assembled using a waterproof adhesive, typically done manually. The plywood sheets are then transferred to a hot press, capable of handling around 20 to 40 sheets at a time, after the adhesive has been properly applied. The hot press applies extreme temperatures and pressures, reaching approximately 200 psi and 310 °F, ensuring thorough contact between the veneer layers and allowing the adhesive to achieve its maximum bonding potential.
Subsequently, the plywood sheets are cut to exact dimensions using specialized saws. Each finished sheet is marked with details such as grade, mill number, and additional pertinent information. Cable reels may be constructed from either marine-grade or shuttering plywood.
Plywood has several notable features, including:
Despite its name suggesting inherent water resistance, marine plywood is not naturally waterproof. Without chemical treatment, it remains susceptible to water damage. Marine plywood is crafted from premium hardwood and bonded with waterproof adhesives to enhance durability.
Selecting higher-quality grades ensures you receive plywood that is both strong and lightweight, free of defects. These properties make marine plywood ideal for applications exposed to moisture, such as on boats. Additionally, marine plywood reels can be repurposed into durable outdoor furniture. After applying a robust protective finish, these products become well-suited for coastal environments. The available grades of marine plywood include: A, A-B, B, high-density overlay, and medium-density overlay.
Shuttering plywood consists of sturdy hardwood and features a smooth film coating on both surfaces. It is primarily utilized in construction settings. This type of plywood is exceptionally dense, comprising at least nine layers of tightly packed core veneers that are bonded using high-pressure machinery at elevated temperatures. The result is a highly durable plywood with a density of 750 kg per cubic meter and a thickness of 12 mm, designed to handle substantial loads in demanding applications.
Plastic reels offer a robust and lightweight packaging option for manufacturers of monofilament and insulated wires. These reels are fully recyclable. They are used across various industries, including those producing electrical wiring, data transmission cables, ribbons, tapes, and monofilaments for both recreational and medical purposes.
Plastic flanges come in diameters ranging from 6 1/2 inches to 24 inches, with customization available for any size. They can also be produced at home using a 3D printer, which significantly reduces the overall weight. Additionally, plastic reels are the only type of cable caps that meet the stringent health and cleanliness standards required in medical technology.
Steel drums have largely replaced traditional wooden drums in the cable and wire business, particularly in the offshore sector. Steel drums are usually welded as fixed drums, however there are also collapsible steel drums. Steel reels or drums are made in an environmentally responsible manner and are more durable than wooden drums, although at a much greater price. Steel reels are more difficult to steal. Steel reels or drums are chosen by the offshore business nowadays over hardwood, plywood, or plastic reels or drums, although the previous land-based industry favored wooden drums due to reduced costs. Steel reels can be loaded with a variety of cables and wires, ranging from the heaviest to the lightest. These steel coils are more durable than wooden coils and are made in an environmentally sustainable manner. Cable drums that are spring loaded and can be mounted in various ways. These cable retractors, also known as spring coils, are a quick and cost-effective option for applications requiring counterbalance, recovery, or return operations.
Spring cable reels are used on a variety of moving machinery to automatically reel in cables. Most hoisting and material handling devices, such as portal cranes, grabs, magnets, lift and working platforms, machines, excavators, mobile cranes, transfer vehicles, transport systems, and skimmers in purifying plants, fall into this category. These devices are usually track-based and run in a straight line. These applications for the transmission of electric power and control signals via reeling might be horizontal or vertical in orientation.
Motor springs are designed for long extension and can handle numerous revolutions, making them ideal for applications involving retrieval and return. They can be directly connected to a reel for retracting cords, cables, and hoses. Spirator springs, which allow for long deflections, are used in reels like 100-foot cable reels to optimize weight and space. In negator spring motor assemblies, single or double negator constant force springs are mounted on one or two storage drums, with an output drum incorporating an integrated cable reel. The entire assembly is supported by a metal base plate. For custom applications, materials such as Inconel, Elgiloy, or high-carbon steel can be used.
Spirator prestressed power springs are created by reverse-winding a negator spring around an arbor and enclosing it in a retaining ring or case. To achieve linear motion, a pulley and cable attachment can be used to convert rotational energy from the arbor or case. Compared to standard power springs, spirator springs occupy 20% less space and offer a flatter torque gradient when deflection and torque are matched. These springs are used for winding, counterbalancing, and retrieval tasks across various applications. They are compact and lightweight, capable of delivering more than twice the number of rotations of conventional power springs. The increased pre-stressing enables the use of thinner materials, resulting in a more compact package size compared to traditional power springs.
Mobile machinery, including gantry cranes, indoor cranes, diverse loading devices, expansive open-pit mining equipment, longitudinal scraper bridges in purification plants, and traveling platforms, play a crucial role in transferring energy and data. Effective transmission maintenance requires a system that continuously stores and deploys cables while synchronizing with the movement of the equipment. The specifics of the equipment's application—such as movement distance, direction, acceleration, speed, and load—define the fundamental pattern of cable handling.
Motor-driven cable reels are designed to meet these needs. They consist of a reel body, a drive mechanism, and a slip ring assembly. These reels are also known by various names, including motorized hose reels, motor-driven hose reels, air hose reels, electric hose reels, and motorized cable reels.
Unlike take-apart reels, this type of reel is permanently assembled. It is designed for winding and unwinding steel wire ropes and power cables and is commonly used in lifting and hauling equipment such as cranes, elevators, and ropeways.
Hose reels are used to wind, unwind, and store hose lengths used to transfer gasses and liquids in industrial settings. Hose reels come in a variety of materials, including steel, stainless steel, plastic, and wood. The majority of goods contain ports to keep fluid flowing during rewinding. Hose reels come in a variety of shapes and sizes.
Collapsible devices are designed for easy disassembly, making them convenient for storage or transport. Portable hose reels, which typically come with a handle, are meant for manual handling. Live connection reels feature mechanisms that keep the material flowing while the hose remains attached. Storage reels are used for holding continuous items like cables, hoses, paper, or ropes over long durations. A complete assembly generally includes the reel, hose, and essential components such as nozzles.
Hose reels can be rewound using different mechanisms. Manual models require a hand crank, whereas others may be powered by electric motors, hydraulic motors, pneumatic motors, or internal springs. Electric motors are described by their shaft speed, terminal voltage, continuous current, torque, and power output. Hydraulic motors are evaluated based on factors such as operating torque, pressure, speed, temperature, power, fluid flow capacity, viscosity, and displacement per revolution. Air motors are assessed by torque, maximum air pressure, air consumption, free speed rating, and noise level during operation.
Hose reels are useful for winding, unwinding, and storing a variety of industrial hoses. Reinforced hose comes in a variety of types, including textile braid, wire braid, wire helix, and other multi-ply or multi-layer arrangements, and is suited for heavy-duty applications. Industrial hose that has been coiled is flexible, elastic, and relatively easy to store. Corrugations, pleats, or spiral convolutions are used in corrugated hoses to promote flexibility, compression, and elongation capacity. Articulated industrial hose is made up of rigid hose sections with movable "joints" that can swivel, position, or articulate. Multiple hoses are created or glued together in a flat, ribbon, or bundled arrangement in a multi-element hose. Hose reels for pneumatic hoses and hydraulic hoses are also available.
Some cable reels feature a retractable mechanism. While these reels are commonly used for transmitting mains electricity, a similar approach is employed for air hoses. Retractable cable reels are highly useful in environments where electricity or air needs to be accessible at multiple locations. These reels use a constant force spring to provide torsion to the spool, and a ratcheting mechanism ensures that the cable remains extended during use, preventing unwanted retraction.
This chapter will explore the various applications and advantages of cable reels.
Cable reels are designed for winding and unwinding the following materials:
Some of the benefits of using cable reels are:
Cable reel rollers, unlike reel jack stands, are a single, stationary piece of equipment. The reel rotates thanks to a low base with steel rollers smoothly. Workers may swiftly disburse cable after installing the reel in place without worrying about serious safety hazards caused by poor setup.
There may be limitations in terms of space for proper installation. Compared to trench rollers, cable rollers are relatively easy to install. You simply need to identify a suitable spot at the edge of the building, lay out the cable, and position the rollers correctly. If a suitable location isn’t available, you might need to dig into the ground to place the rollers. For managing cables around corners and curves, you might need a cable roller designed with specialized curved ends.
Cable reels hold conductive cable or lifting cable and are used for storage, unwinding, and winding. Contacts on electric cable reels keep the power on while winding. Reels are machines that wrap long, continuous goods like cable, wires, paper, and other materials for transport or storage. Simple storage systems such as reels are available, while more advanced versions are self-winding. They can also be ordered with live connections, allowing you to utilize a hose or electrical wire while it's still on the reel. The choice of a cable reel has to be cognizant of the different types, applications, and benefits of each one.
Cord reels are devices that hold extension cords that are used to supply power to electrical equipment or devices located far from the power outlet. They are also used in storing long extension cords properly...
A hose reel is a mechanism for storing and use of a hose on a barrel for easy access. It is a system designed to make hoses, cords, flexible tubing, and wire conveniently available for immediate use...
A lubricant is a substance that is applied on surfaces that have relative motion in between them. The lubricant reduces friction and wears between the surfaces. However, the lubricant can have other...
Lubrication systems distribute the lubricant to the moving machine parts in contact. Lubricants reduce the friction between sliding or rolling machine elements, such as gears, spindles, bearings, chains, dies, screws, cylinders, valves, and...
A metering pump is a precision mechanical device that moves or pumps a measured amount of a fluid or liquid in a predetermined time period to create an accurate and exact volumetric flow...