AC Motors
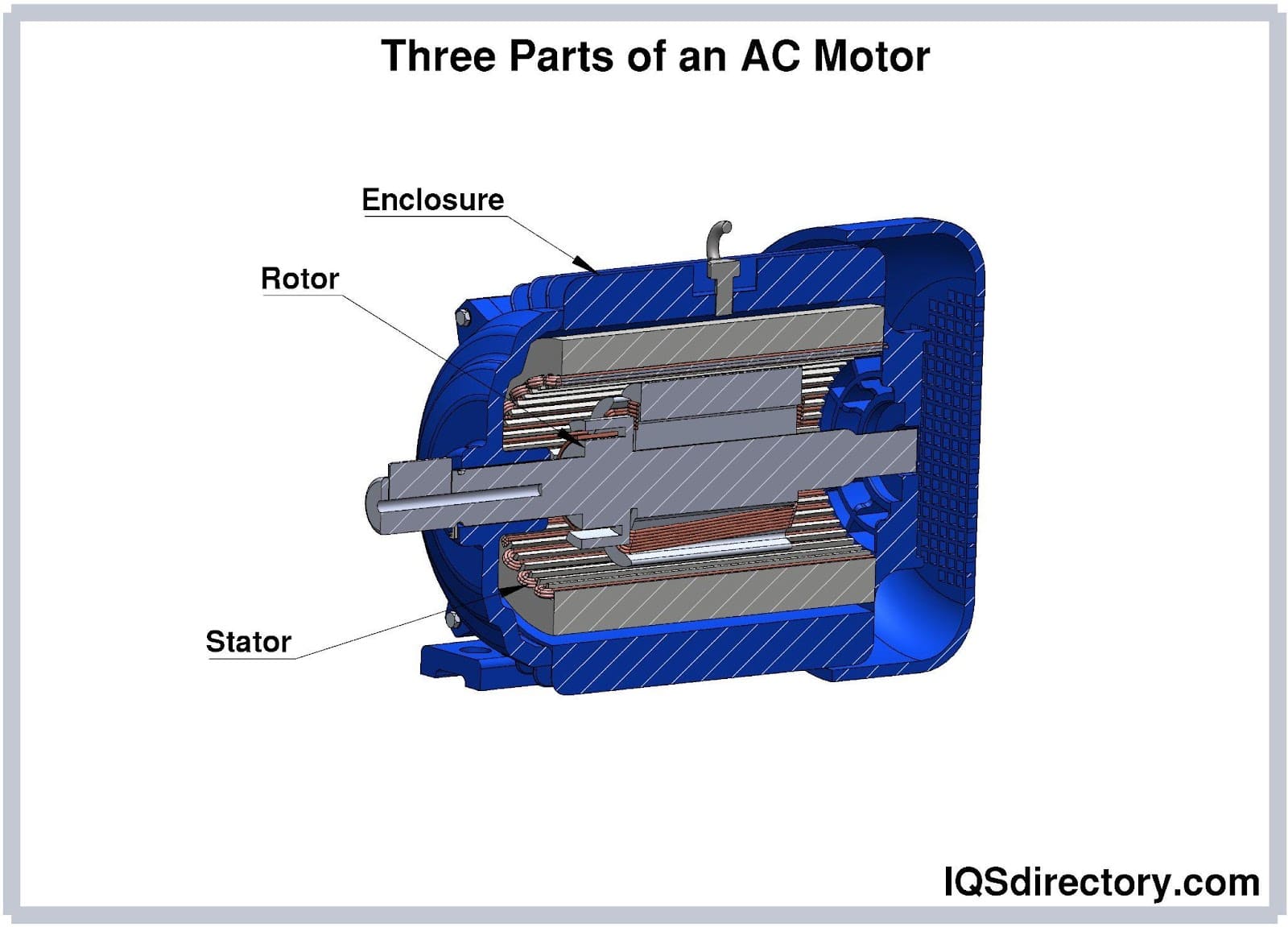
An AC motor is an electric motor that uses alternating current to produce mechanical energy using magnetism blended with alternating current. The structure of an AC motor includes coils that produce a rotating...
Please fill out the following form to submit a Request for Quote to any of the following companies listed on
This article will take an in-depth look at hydraulic motors.
The article will bring more detail on topics such as:
This chapter delves into the definition of hydraulic motors, exploring their unique terminology, the fundamental principles of their operation, and what sets them apart from hydraulic pumps.
Hydraulic motors are specialized devices that transform hydraulic pressure or the energy from fluid into rotational force and angular motion.
Some critical terminology associated with hydraulic motors includes:
Motor displacement indicates the amount of fluid necessary to complete one complete revolution of the motor’s output shaft. This measurement is expressed in cubic inches or cubic centimeters per revolution. Depending on whether the motor features fixed or variable displacement, its torque can either remain consistent or change. Fixed displacement motors maintain stable torque, whereas variable displacement motors have variable torque and speed based on input flow.
The output torque, measured in foot-pounds or inch-pounds, is influenced by the system's pressure and the motor’s displacement. Manufacturers offer specific torque ratings to evaluate pressure differentials across the motor.
Starting torque represents the force a hydraulic motor must exert to initiate the movement of a load. It is the torque required to start turning a stationary load and is often a percentage of the theoretical torque. For common hydraulic motors like piston, vane, and gear types, starting torque usually varies from 70% to 80% of the theoretical torque value.
Breakaway torque is defined as the torque necessary to overcome inertia and initiate the rotation of a stationary load. It typically exceeds the torque needed to keep the load in motion.
Running torque pertains to the torque needed to sustain the rotation of the motor or its load. For motors, it signifies the actual torque produced to keep the load rotating. Typical vane, piston, and gear motors offer running torque around 90% of the theoretical value.
Mechanical efficiency evaluates the effectiveness of a mechanical system in transforming input into output. In hydraulic motors, it is the ratio of actual torque delivered relative to the theoretical torque, indicating the motor's performance efficiency.
Slippage is a condition whereby fluid moves through the internal components of the motor without effectively contributing to the intended work.
Hydraulic motors convert hydraulic pressure or fluid energy into torque and angular displacement. These motors consist of various components working in unison to achieve their desired functionality. Below is an overview of key components commonly found in hydraulic motors and their respective functions:
The stator generates a force acting on the piston, creating a tangential component that propels the rotation of both the piston and the rotor.
The rotor is the part of the hydraulic motor that spins once triggered by an internal mechanism. This mechanism varies with motor types; for example, in gear-type motors, the rotor rotates as gears engage and fluid flows. Conversely, in vane-type motors, rotor motion is induced by vane pressure.
The driveshaft, also known as a propeller, is a part of a hydraulic motor that transmits the internally generated torque to external applications, such as lifting loads. Typically made of metal, driveshafts have gear teeth on their ends to transfer power efficiently.
Hydraulic motors operate by controlling the flow of fluid within them. Directional control valves play a pivotal role in managing this fluid flow. These valves regulate how fluids—like oil, water, or air—navigate through different system parts, based on operational control mechanisms and patterns.
A protective housing encases hydraulic motors, safeguarding and containing internal components. These casings can be made from various materials, including stainless steel, titanium, cast iron, low carbon steel, and nickel. The casing's shape changes based on the motor's internal component arrangement.
A piston rod is a precisely machined bar used to transfer force within a hydraulic or pneumatic setup to another machine part that performs work. In hydraulic motors, piston rods mainly function in piston-type motors to produce rotational movement.
Hydraulic motors use fluids to transmit energy across points. These fluids typically range from water-based and petroleum-based to synthetic. Mineral-based, or petroleum-based fluids, are the most common, with variability stemming from the additives and crude oil quality. Common additives include anti-corrosion agents, demulsifiers, extreme pressure agents, rust inhibitors, oxidation inhibitors, and defoamants.
Water-based fluids are predominantly used in fire-resistant applications due to their high water content. High temperatures should be avoided as they can cause evaporation issues. Constant monitoring is vital since water loss might lead to lubrication complications.
Synthetic-based lubricants, although costly, deliver superior properties compared to other fluid types.
Bearings are essential mechanical parts developed to minimize friction and support loads for rotation. In hydraulic motors, they are especially crucial for the driveshaft, ensuring smooth, efficient shaft movement. The bearing type is selected based on factors including rotational speed, load capacity, load direction, and the specific fluid used.
Understanding the differences between hydraulic pumps and motors is crucial. Although hydraulic pumps and motors operate in similar fashions, they have distinct characteristics that sometimes lead to confusion. People often interchange the terms pump and motor.
Some key distinctions between hydraulic motors and pumps include:
Hydraulic motors are designed to rotate in both directions. They possess internal symmetry to accommodate both positive and negative rotation, unlike hydraulic pumps, which generally rotate in a single direction.
For instance, a vane motor must have blades arranged radially and not inclined like a vane pump, as the latter would damage retracting blades. The distribution plate in the axial plunger motor is symmetrical, unlike the axial plunger pump.
This section will cover the different categories and varieties of hydraulic motors, providing an in-depth overview for users seeking to understand the diverse options available for hydraulic power transmission in industrial applications.
Hydraulic motors are typically categorized into two main types based on their speed and torque characteristics: low speed and high torque (LSHT) motors, and high-speed low torque (HSLT) motors. These classifications help users select the appropriate hydraulic drive system for their specific fluid power and motion control requirements.
Low-speed high torque (LSHT) motors, also known as high torque low RPM motors, are designed for heavy-duty hydraulic applications requiring slow, controlled operation. These motors can operate at speeds ranging from 0.1 rpm to approximately 1000 rpm, delivering substantial, continuous torque at low speeds. Typical industrial uses for LSHT motors include operating gates, doors, elevators, presses, and winches. They are ideal for environments where machinery must lift or move substantial weights in a precise, secure manner and are critical in hydraulic systems that require high force output with low rotational speed.
Their slow speeds ensure heavy objects are manipulated with optimal accuracy, minimizing risk and maximizing control. LSHT hydraulic motors play an essential role in a variety of industries, such as public infrastructure, automotive and aerospace systems, conveyors, robotic feeding mechanisms, textile manufacturing, mining equipment, metalworking machinery, agricultural systems, food processing, material handling, and other automated transportation solutions. These motors are instrumental in modern mechanization, industrial automation, and high-load applications, providing the robust performance required for demanding tasks.
The advantages of using low-speed high torque (LSHT) motors are:
With their durability, energy efficiency, and ability to operate under extreme hydraulic pressures, LSHT motors are a preferred choice for operators seeking reliability, minimal maintenance, and customizability for complex industrial projects.
High-speed low torque (HSLT) hydraulic motors, often called high RPM motors or rotary actuators, are engineered to function at speeds between 1,000 rpm and 14,000 rpm. These hydraulic drive units are suitable for applications requiring rapid rotation with lower torque output, making them ideal for lighter load scenarios. HSLT hydraulic motors are commonly found in utility equipment, earthmoving machinery, forestry operations, material handling systems, and other industrial processes where speed is prioritized over maximum force.
Benefits of employing high-speed low torque (HSLT) motors include:
HSLT motors are crucial when fluid power systems require rapid cycling, high throughput, and smooth, continuous rotation. Their adaptability ensures optimized hydraulic system design for a wide range of industrial and mobile hydraulic applications.
The different types of hydraulic motors are categorized based on their design, operating principle, and suitability for specific tasks within hydraulic power transmission systems. Selecting the appropriate type of hydraulic motor is essential for maximizing productivity, reliability, and efficiency in any fluid power application.
This gear mechanism employs a hydraulic motor with two intermeshing gears: a driven gear and an idler gear. The driven gear is connected to the output shaft via a key, allowing power transmission from hydraulic pressure to mechanical rotation. Pressurized oil flows around the gear tips inside the housing, enters through specially designed side ports, and exits through the outlet port. The meshing action of the gears creates a seal, which prevents backflow from the outlet to the inlet side, ensuring efficient fluid transfer and torque generation.
A small fraction of the hydraulic oil is diverted for gear lubrication, flowing through the hydrodynamically lubricated bearings located on the pressure side. The spur gears, commonly found in these external gear hydraulic motors, must be manufactured to high precision standards to avoid operational vibration and excessive noise under load.
The features of external gear hydraulic motors are:
These motors are frequently chosen for mobile machinery, industrial automation, agricultural equipment, and conveyor drives, where consistent torque and affordability are important.
Internal gear motors resemble external gear motors in basic operation but are distinguished by superior smoothness and quieter performance. Their unique construction includes a smaller external gear meshing with a larger internal gear, enabling near-silent running with minimal vibration. Internal gear motors are available in two primary designs, notably the gerotor motor, widely utilized in mobile hydraulics and compact hydraulic systems, as well as the more advanced geroller motor.
Utilizing a crescent-shaped vane to divide the intake and discharge volumes, these gear motors allow pressurized hydraulic fluid to enter the inlet port, increase pressure and volume, and actively drive gear rotation. The resulting fluid flow is expelled through the discharge port, generating rotational motion.
The features of internal gear hydraulic motors are:
Due to their efficiency, reliability, and low-maintenance operation, internal gear motors are prevalent in industrial processes involving food and beverage, chemical transfer, plastics, and mobile hydraulic systems requiring long life and minimal downtime.
Hydraulic motors in the vane category generate output torque by creating an internal pressure imbalance within the housing, which causes the rotor and shaft to rotate. In hydraulic vane motors, this force difference is produced across sliding vanes extending from a rotor, with the pressure differential causing the rotor to spin. Vane motors feature internal hydraulic balancing to prevent side loading and shaft wear, making them well-suited for continuous duty cycles and critical automation systems.
Typically constructed with a cartridge-style housing, vane hydraulic motors resemble hydraulic vane pumps in design—featuring port plates that divide inlet from outlet, a precision cam, and a rotor ring. The vanes, mounted in radial slots, maintain contact with the cylindrical internal wall, propelled outward by centrifugal force to maintain optimal sealing and efficiency. This ensures steady, pulsation-free flow and even torque characteristics critical for smooth industrial operation.
Key characteristics of vane hydraulic motors include:
Vane motors are commonly used for machine tools, injection molding, plastic processing, and drive applications requiring both efficiency and quiet operation.
The radial piston hydraulic motor is a high-torque, low-speed hydraulic actuator that converts hydraulic energy into mechanical rotation. Central to its design is a directional valve with dedicated intake and return lines, with a rotor featuring radial bores housing free-floating pistons. As high-pressure hydraulic fluid enters the bores, it presses the pistons outward, applying force to a fixed cam ring or track, which in turn causes the rotor and main shaft to rotate. The use of an odd number of cylinders ensures consistent torque output.
To ensure continuous, smooth power delivery, radial piston hydraulic motors may incorporate rollers that reduce friction losses between pistons and the stationary track. Their ruggedness and ability to operate under extremely high system pressures make them indispensable for heavy-duty applications like injection molding machinery, offshore winches, heavy construction equipment, tunnel boring, and other hydrostatic drive systems demanding massive torque at low speeds.
The features of radial piston hydraulic motors are:
Operators select radial piston motors for their energy efficiency, compactness for mobile equipment, and superior reliability in high-impact environments.
Axial piston hydraulic motors, also known as barrel or swashplate motors, are designed for variable displacement and high-speed operations. Their construction includes a series of pistons arranged parallel (axially) within a rotating barrel, with a drive shaft plate set at an angle. Pressurized hydraulic fluid entering the cylinders causes the pistons to move, generating an axial force on the plate, which is then converted into rotational motion by the swashplate design.
The inclination angle of the swashplate is key; adjusting it allows for control over displacement and output speed, providing essential flexibility in variable-flow hydraulic systems. Axial piston motors are often equipped for bidirectional flow and speed regulation, making them ideal for closed-circuit hydrostatic drives in mobile equipment, marine propulsion, and industrial power units. Their inherent efficiency and high power-to-weight ratio make them a top choice for dynamic, demanding hydraulic drive applications.
The features of axial piston motors are:
Axial piston motors continue to dominate technology-driven industries where compactness, speed, and energy efficiency are prioritized, including marine engineering, injection molding, hydraulic presses, and renewable energy systems. When selecting a hydraulic motor, factors such as operating pressure, fluid compatibility, required speed, torque output, and space constraints should guide your decision to ensure optimal performance and system longevity.
When evaluating hydraulic motor suppliers and manufacturers, consider key factors such as industry reputation, support for custom hydraulic solutions, inventory of standard and specialty replacement parts, industry certifications, and customer support capabilities. Compare technical datasheets, performance curves, and warranties to make informed purchasing decisions and ensure you select the right hydraulic motor for your system requirements and budget.
This section will explore the different applications of various hydraulic motor types.
Below are the different applications of hydraulic motors.
External gear motors are used in the following applications:
The applications of internal gear motors are:
The applications of vane hydraulic motors are:
The applications of radial piston hydraulic motors are:
The applications of axial piston hydraulic motors are:
When selecting a hydraulic motor, several factors must be considered to ensure the system operates efficiently. The chosen motor must meet the system's requirements; otherwise, it could impact the overall performance. Below are key factors and questions to consider:
Understanding load requirements is crucial, as it defines the system's purpose. Designers should start by assessing the load size, whether large or small. Once the load requirements are clear, other system specifications can be designed accordingly.
Different motor types have varying operational characteristics based on their applications. Selecting the appropriate motor involves understanding the ratings and specifications provided by the manufacturer.
For instance, using a motor designed for high speeds in a slow-speed application can overstress the motor, potentially reducing its lifespan. It's important to match motor ratings with load requirements.
Motors operate with either fixed or adjustable displacements, depending on the application. Understanding the application will guide the selection of the appropriate motor. Additionally, consider the operating pressure and flow, as high pressures result in greater torque.
Leakage refers to fluid escaping through gaps such as holes or cracks. A motor with high leakage potential poses a risk, making it unsuitable for sensitive material handling due to the increased likelihood of failure.
Hydraulic motors are used in various applications, with materials affecting their response to operating conditions. Some motors are robust enough to handle vibrations and harsh conditions, making them suitable for industrial use.
Motor designs vary, with some operating with broad tolerances and suitable for multiple purposes, while others are specific in terms of pressure, speed, and temperature. Understanding these aspects helps in system design and motor selection.
Motor controls can be mechanical or electronic, depending on user preferences and considerations like power consumption and automation benefits.
While some motors are highly efficient, they may require significant maintenance. For instance, axial piston motors often need more frequent maintenance compared to gear motors to maintain their lifespan.
Knowing the expected lifespan of a motor and its bearings is crucial for application and maintenance planning. For complex machines, choosing a motor with a short lifespan may not be practical. Various bearings can be used based on the forces and torque involved, as they are selected according to the stress on their surface area.
Before choosing a motor, gather installation details as some types require specialized expertise and complex installation. Consulting with professionals about associated costs is essential before purchasing a hydraulic motor.
A closed-loop hydraulic system, or hydrostatic drive, is commonly used in mobile systems and industrial machines like conveyors. In this setup, fluid circulates directly from the pump to the motor and back without a reservoir. Fluid flow determines motor speed. In an open-loop system, fluid moves from the motor to the pump through a reservoir. Understanding the loop type is crucial for selecting the right motor for the system.
Contamination risks vary based on the motor's application. Contaminants like dirt, dust, chemicals, or water can affect motor performance. Motors exposed to water may rust, and contaminants can lead to leakage, cracking, or unwanted vibrations.
Motors may need to meet various standards, including international, workshop, or engineering approvals. Considering these requirements is crucial to avoid safety issues and ensure compliance with engineering standards.
Proper maintenance is key to optimal motor performance. Below are considerations for maintaining hydraulic motors.
Hydraulic motors play a vital role in the engineering and automation of many systems in our everyday lives. Although some of them are complex, most of these motors use simple operating principles which are easy to understand and are user-friendly.
An AC motor is an electric motor that uses alternating current to produce mechanical energy using magnetism blended with alternating current. The structure of an AC motor includes coils that produce a rotating...
A DC motor or direct current motor is an electrical machine that transforms electrical energy into mechanical energy by creating a magnetic field that is powered by direct current. When a DC motor is powered, a magnetic field is created...
An electric motor is an electric machine that converts electrical energy to mechanical energy. Most electric motors work via the interaction of the motor magnetic field and electrical current in a wound wire to...
A hydraulic cylinder is a tube that produces linear actuation utilizing hydraulic pressure. Basically, the pressure of a hydraulic fluid forces a piston to move in either a pushing or pulling motion...