Size Reduction Equipment
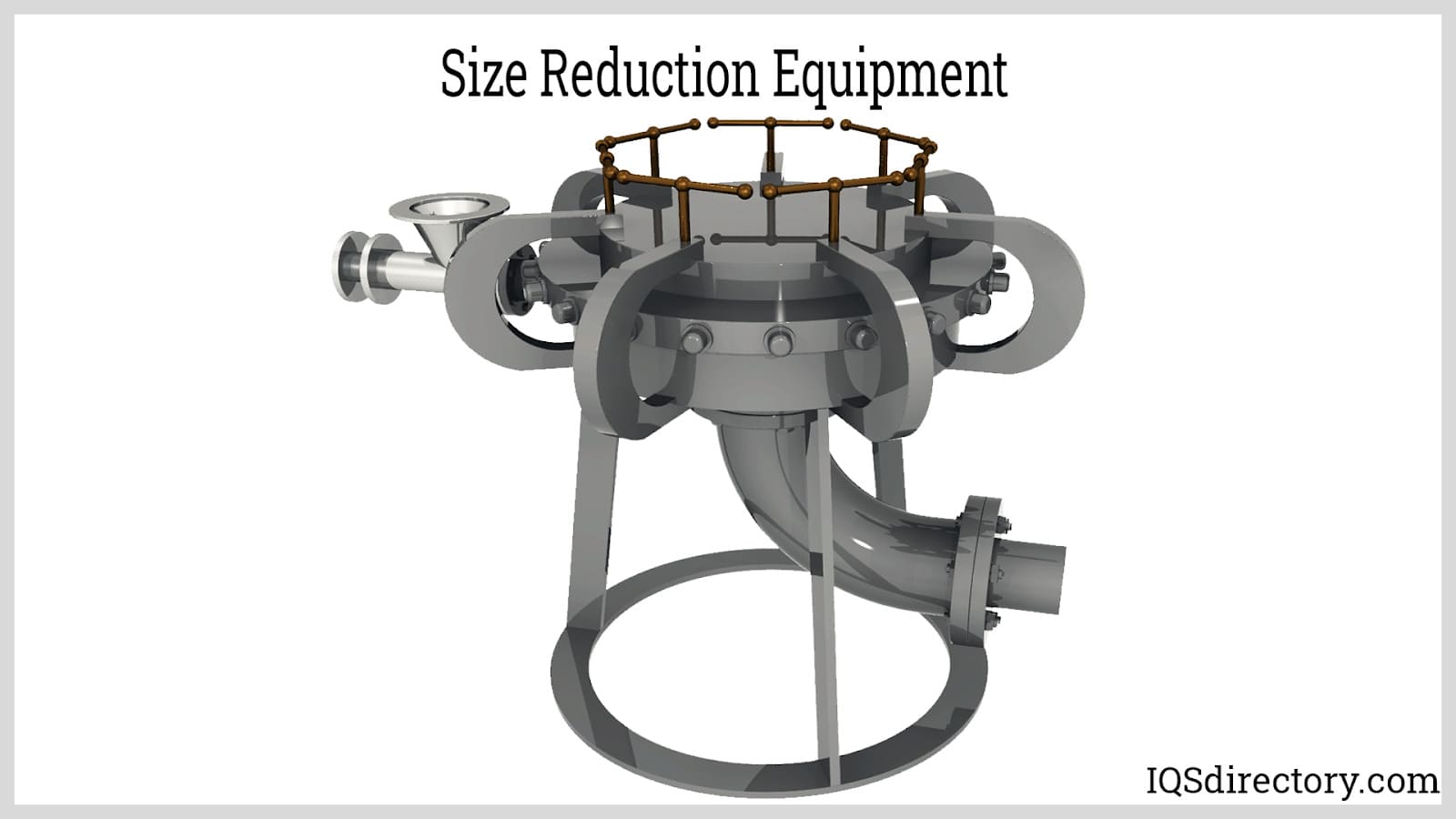
Size reduction equipment refers to machines that crush and grind materials to reduce their size. Pulverizers are a type of size equipment, the names are used interchangeably. Size reduction is an essential...
Please fill out the following form to submit a Request for Quote to any of the following companies listed on
This article will take an in-depth look at types of mills.
The article will bring more detail to topics such as:
In this section, we delve into the workings of mills and identify the typical components that constitute these machines.
A mill is a machine engineered to fragment solid materials into smaller pieces through methods such as cutting, grinding, or crushing. The milling process involves exerting force on a material to break it down and decrease its size, which improves the effectiveness of the ingredients and enhances the quality of the final products made from them. Milling is generally categorized into two types: dry milling, which involves particle-to-particle collision, and wet milling, where materials are mixed in a slurry.
There are various forms of mills, each tailored to crush or process different materials. Early models were hand-operated, powered by animals, or driven by wind or water. Nowadays, modern mills utilize electricity, providing increased power and decreasing labor expenses.
In milling, solid materials are pulverized using mechanical force that breaches the material's internal structure by surpassing its bonds. This method converts solid substances into smaller particles, grains, or varied shapes. Milling also includes the steps of breaking down, sizing, separating, or classifying materials such as mineral ores. For example, grinding rocks can produce consistent particle sizes for use in construction or separate rock from soil for filler or land reclamation.
Milling is also employed to eliminate or separate impurities or moisture from soil, producing dry fill for use in transportation or construction. The milling process fulfills several critical engineering functions:
Industrial mills are advanced mechanical systems engineered for the grinding, pulverizing, and material size reduction required in a wide range of sectors—including mining, cement production, metallurgy, chemical processing, and aggregate manufacturing. These complex machines are comprised of a series of critical parts and assemblies that must work in concert to deliver reliable, efficient milling performance. While mill designs, such as ball mills, rod mills, SAG mills, and autogenous mills, may vary, all share a core set of vital mill components structured for strength, longevity, and safety. Understanding the primary industrial mill components helps operators select, maintain, and optimize milling equipment for maximum productivity and minimal downtime.
The mill shell is the primary structural element and pressure vessel of any mill, serving as both containment and support for all internal mill components. Constructed from extra-thick, high-quality steel plates, the shell is meticulously welded and sealed into a cylindrical or sometimes conical shape to provide industrial-grade resistance to distortion, vibration, and mechanical fatigue. Automated welding ensures consistent, robust joints for mills exposed to high stresses typical of heavy-duty grinding applications. Engineers also consider shell diameter, length, and thickness based on production capacity and the abrasiveness of bulk materials processed. Holes are precision-drilled into the shell to accommodate liners and bolting systems; wedge-type liners may eliminate the need for bolts. Shell integrity is crucial for mill reliability, particularly for large-scale processing in industries like mining and ore beneficiation.
Mill flanges are precisely engineered to match the unique diameter and operating requirements dictated by the specific application and the bulk solids being processed. These robust, machined elements maintain strict tolerances for flatness, surface finish, and precise fit, preventing material leakage and excessive wear. Flanges often incorporate carefully designed recesses and undercuts to interface seamlessly with the arbor sleeve or drive system. Regular inspection and preventative maintenance of flanges—focusing on balance, surface quality, and tightening sequence—helps safeguard against flange warping, vibration, and premature component failure, all of which are essential for prolonged mill uptime and optimized throughput.
Shell liners function as barrier layers, lining the inside surface of the mill shell to protect against abrasive wear and mechanical damage from grinding media and processed material. Selection of liner materials and profiles—including rubber liners for ball mills and high-manganese steel for heavy-duty SAG mills and AG mills—impacts energy efficiency, throughput rates, and liner life cycle costs. Liner design also shapes the material flow and grinding media action, influencing the mill’s comminution performance. The following are common liner types used in industrial milling:
Mill heads—also called end caps—are critical closure components fabricated from cast or forged steel (or iron) for both strength and rigidity. They are securely affixed to the shell’s flanges, sealing each end of the mill. There are two primary head designs: conical heads, employed in ball and rod mills for improved material discharge and load distribution; and the starfish design, seen in long-run Ballpeb and Compeb mills, leveraging reinforced bracing for extra support. Integral trunnion bearings mounted within the mill head provide rotational support and facilitate the smooth, precise turning of the mill drum, enabling effective grinding media and material motion while reducing mechanical wear.
The pinion shaft is a pivotal component of the mill’s drivetrain system, transmitting mechanical power from the main drive gearbox or motor to the large ring gear affixed to the mill shell. The pinion shaft assembly is positioned using high-performance roller bearings, which offer superior load-handling, minimal rotational friction, and extended operational life. Optimal lubrication—delivered via an oil reservoir or automated lubrication system—prevents heat buildup and supports continuous, energy-efficient operation in demanding industrial environments.
Mill drive systems are engineered to deliver precise, reliable rotational energy suited to varying mill sizes and processing demands. Smaller mills (under 250 hp) typically implement a V-belt drive for simplicity and cost-efficiency. Larger, heavy-duty mills utilize advanced direct-drive arrangements, featuring wound rotor or synchronous motors coupled directly to the pinion shaft. These configurations offer controlled torque, superior efficiency, and minimal power loss—ideal for high-capacity mining and mineral processing plants. Selection of drive type, gear ratio, and motor specifications depends on mill size, speed, production targets, and the abrasiveness of processed materials.
Feed chutes are engineered for consistent material delivery into the mill, tailored to accommodate the properties of the raw feed (such as particle size, moisture content, and abrasiveness). Mill chutes vary according to application—ranging from mining and aggregate crushing to cement or pharmaceutical powder milling. Key feeder types include:
When choosing a feed system, operators consider factors like clumping, segregation, dust control, and maintenance accessibility to ensure sustained throughput and minimized process interruptions.
After grinding, the processed material exits the mill through the discharge system. The discharge design determines the ultimate particle size distribution and product consistency, directly impacting downstream processing efficiency. Common discharge patterns include:
Optimized discharge mechanisms prevent material buildup, reduce energy waste, and support superior product quality for industries requiring tightly controlled particle size specifications.
Grinding media are the high-impact, energy-transmitting elements responsible for reducing material to finely ground particles, enabling the chemical and physical property changes crucial in industries such as mineral processing, powder metallurgy, cement blending, and ceramics. The optimal selection and maintenance of grinding media—both in terms of shape (balls, rods, cylinders, beads) and material composition—directly influences grinding performance, wear rates, energy efficiency, and contamination risk.
Metallic grinding media are engineered from robust materials such as carbon steel, forged steel, stainless steel, and chrome steel. These media are available in various geometries, including balls (20 mm to 120 mm diameters), cylindrical rods, and short cylinders. Steel balls offer consistent hardness and impact resistance—making them ideal for ball mills engaged in high-throughput ore grinding and mineral liberation. Cylinders suit fine grinding circuits, while cut steel bars, sized to match the mill length (50 mm to 100 mm), are preferred for rod mills due to their uniform particle size reduction. Proper selection of metallic media type and sizing ensures optimal product fineness, mill efficiency, and cost-effectiveness for each specific grinding application.
Non-metallic grinding media are purpose-designed to minimize contamination, wear, and chemical reactivity—especially vital for specialty chemical, pharmaceutical, and ceramic powder production. Common materials include alumina oxide balls, glass beads, silicon carbide and nitride balls, high-purity ceramics, and zirconium oxide spheres. These options are chosen based on media density, hardness, abrasion resistance, and compatibility with processed substances. Using the correct non-metallic media safeguards both process integrity and equipment longevity, preventing costly mill liner or product contamination issues.
Consultation with grinding media and mill manufacturers enables users to select the best media type for each unique milling process, balancing both cost and performance for optimal operational results.
Industrial mills play a vital role in material processing, transforming a wide range of raw materials in manufacturing, chemical processing, pharmaceuticals, food production, and other industries. Generally, mills are classified into four primary categories, each engineered for specific grinding, crushing, milling, or fine-cutting applications. Understanding the unique characteristics of each mill type helps manufacturers and processors select optimal equipment to enhance productivity, product quality, and operational efficiency.
A conical mill, also referred to as a conical screen mill or cone mill, is designed to uniformly reduce particle size through gentle processing. Serving as an alternative to hammer mills, conical mills feature a conical-shaped chamber with a wide feed inlet tapering to a narrower discharge outlet. In operation, bulk material is introduced into the mill by gravity or vacuum transfer, then propelled outward by a high-speed rotating impeller against the perforated conical screen surface, effectively controlling the particle size distribution.
Available in a diverse range of configurations—from benchtop laboratory equipment to high-capacity, industrial-scale machines—conical mills feature customizable impellers and mesh screens for precise control over granule size and throughput. Their versatility extends across multiple applications, including powder deagglomeration, uniform particle sizing, sieving, dry and wet milling, and product homogenization. Common industries using conical mills include food processing (for seasoning powders and flour), cosmetic manufacturing (for creams and gels), specialty chemical production, and pharmaceutical manufacturing (for wet and dry granulation, reprocessing defective tablets, and blend uniformity).
Compared to other milling solutions, conical mills offer significant advantages: they operate with reduced vibration and noise, generate minimal heat and dust emissions, and ensure tight particle size control, minimizing fines and oversize yield. Their modular design allows easy screen and impeller changes, enabling quick adaptation to different processes and compliance with sanitary requirements. Innovation since their inception in 1976 has led to features like mobile hoist-mounted mill heads for easier integration with processing lines, enhanced containment systems for dust control, and tool-free disassembly for efficient cleaning (CIP and SIP capabilities). Today, conical mills are essential for meeting strict compliance standards—such as cGMP and FDA guidelines—in regulated industries.
Modern hammer mills are robust machines engineered for aggressive and high-throughput size reduction, comminution, and grinding of diverse raw materials. Driven by a powerful industrial motor, hammer mills use rapidly swinging blades—hammers—to break down materials against a robust mill casing. This kinetic impact efficiently fragments fibrous, tough, or brittle materials into smaller particles, which are then filtered through customizable sieves or screens. Hammer mills are commonly used for pulverizing grains, biomass, dried herbs, plastics, minerals, and more, making them indispensable in agricultural, chemical, recycling, and pharmaceutical industries.
These mills feature distinct blade configurations—flat or serrated, stirrup-shaped for fine milling or bar-shaped for coarse reduction—optimized for specific material properties and desired final product characteristics. Pharmaceutical hammer mills use stainless steel contact parts to ensure product integrity and minimize cross-contamination, while industrial-grade models often have abrasion-resistant coatings for processing harder stock. The hammer assembly may be rigid or swinging; swing hammers adapt to varying feed loads, while rigid hammers provide consistent clearance for higher consistency in particle reduction.
Material feed systems can be gravity-fed for simple operation or utilize pneumatic metering to maintain consistent flow and quality control, particularly crucial for achieving uniform granules or powders. Some advanced hammer mills feature integrated control boxes for real-time process monitoring, adjustable speed settings (ranging from 2,500 to 60,000 RPM), and display panels that allow operators to customize performance according to raw material characteristics and target particle size. The electric motor ensures high energy efficiency and reliability, supporting continuous production cycles. For precise pharmaceutical milling and other specialized requirements, hammer mills offer flexibility to change mesh hole sizes, optimize air flow, and minimize downtime through modular construction.
Fine-cut mills are precision machines designed for producing exceptionally fine powders and highly controlled granule sizes. Feed materials, typically 4 to 8mm, enter the grinding chamber via an intake chute. Inside, particle size reduction is accomplished by the shearing action between an adjustable disc stator and a high-speed rotating grinding disc. The staged grinding process moves material from the innermost point of the disc outward, achieving progressive reduction and uniformity. Integrated screening systems or inline classifiers can be added to further optimize particle size and improve product consistency.
Oversized particles are automatically recirculated to ensure pass-through of only correctly sized product. Fine-cut mills are widely used in the plastics industry for micronizing resins and polymers, pigment dispersion in chemical manufacturing, and laboratory or pilot plant applications. Their cryogenic milling option allows for temperature-sensitive materials—such as thermoplastics or certain food ingredients—to be ground without heat buildup, preventing degradation and preserving material properties. By efficiently producing ultra-fine, uniform powders with minimal contamination risk, fine-cut mills meet the stringent requirements of advanced manufacturing and research environments.
Coarse-cut mills are industrial machines engineered for applications requiring moderate particle size reduction without over-grinding. Designed for relatively gentle processing, these mills utilize robust rotating cutting tools and specialized screens to shear and trim materials into coarser fractions. By adjusting cutting speed, screen size, and rotor design, operators can tailor output particle sizes for distinct end uses.
These mills excel in the food processing industry for producing granulated sugar, rock salt, chopped spices, and feedstock, but also serve mineral, biomass, and recycling plants where controlled particle size is necessary for efficient downstream processing. Coarse-cut mills operate via electric motors to increase productivity while minimizing manual labor, but hand-crank models are available for small-scale or home-based operations. Lower rotational speeds and specialized rotary screens help minimize fines generation and prevent material overheating—important for maintaining the sensory and physical properties of food and specialty chemicals. Their durable construction ensures reliable, long-lasting operation in high-volume production environments.
Grinding mills are core to industrial material processing, designed to transform large raw inputs into fine powders suitable for downstream processes. Unlike mills focused on cutting or crushing, grinding mills operate by attrition, abrasion, or impact to achieve finely ground powders. Major variants include rod mills, ball mills, and attrition mills, each optimized for specific materials and production goals.
The choice of grinding mill and its configuration depends on a wide spectrum of material characteristics: hardness, brittleness, abrasiveness, elasticity, moisture content, particle shape, melting behavior, and chemical stability. Hard materials often require specialized ceramic or alloy liners and precisely engineered grinding media to prevent excessive wear and maximize product purity. Grinding mills provide highly controlled comminution, making them indispensable in cement production, mineral ore processing, paint and pigment manufacturing, ceramics, and pharmaceutical powder blending.
Granule fineness is defined by application-specific requirements: for instance, pharmaceutical grade powders often require a d90 below 75 μm (microns), while construction materials may be ground to 100 mesh or coarser. Moisture management and feedstock consistency are vital, as sticky or wet materials may lead to clogging and reduced efficiency. Closed-circuit grinding systems utilize classifiers or separators to continually recycle oversize particles, maximizing throughput and energy efficiency. Open circuits produce product in a single pass, often suitable for simpler, low-precision applications.
Grinding mills come in tumbling, rolling, and high-speed variants, with options like vibrating mills, pin mills, turbo mills, and fluid energy mills ensuring processors can match operational needs with technical performance. These systems typically include integrated feed mechanisms, separation/classification solutions, and product collection systems, all designed to optimize output quality, maximize yield, and minimize operational downtime.
As advancements in powder processing and materials science continue, the proper selection and operation of industrial mills are more critical than ever for businesses seeking to improve product uniformity, meet regulatory requirements, and remain competitive in an evolving manufacturing landscape. A thorough understanding of industrial milling equipment, from conical and hammer mills to fine-cut, coarse-cut, and grinding mills, is essential for selecting the ideal solution for your specific process requirements and production goals.
Various types of mills fall into the categories mentioned earlier, including:
Wet grinding, also referred to as wet milling, involves processing materials in a liquid state or as a slurry. This method is commonly used to break down agglomerates. Historically, mills designed for damp materials have been produced, but as demands shifted towards finer particles, existing equipment became insufficient. As a result, advancements were made in both the machinery and processing techniques to meet the evolving needs for finer materials.
The first stage in wet grinding involves de-agglomeration, where clumped materials, such as paint molecules, are processed to break up lumps and prevent the formation of agglomerates. This is achieved by passing the product through a machine with close-tolerance settings that force the particles apart. To avoid the reformation of agglomerates, it is crucial to have an optimal formulation that coats each particle adequately.
Following de-agglomeration, the next step is to shear the particles to the desired size. Mills equipped with specialized components handle this task, including fluidizing disks, spacers, and other materials inside the chamber that are agitated by a rotating shaft. The narrow gaps between the medium, disks, and shaft create high pressure that breaks the particles into smaller sizes. Multiple passes through the machine are often necessary to achieve the desired sub-micro particle size.
Rotor-stator wet milling is predominantly utilized in the pharmaceutical sector to achieve finer particle sizes. This technique involves breaking down strongly bonded particles for subsequent processing. The rotor, rotating within the stator, generates a force that draws the material through the stator's openings. As the particles move through the tight spaces between the rotor and stator, they are progressively reduced in size.
The underlying concept of rotor-stator wet milling is to break down substances by suspending them in a liquid medium. The process involves shear forces acting within the confined spaces between the stationary stator and the rapidly spinning rotor. Typically constructed from resilient materials like steel or corundum, the rotor and stator come in various sizes depending on the specific needs of the milling process. Each manufacturer of rotor-stator mills customizes their equipment to achieve the desired level of material refinement.
The term “ball mill” refers to a type of grinding apparatus that contains spherical grinding media. The mill's length is typically the same as its diameter. Ball mills are extensively used in fields such as metallurgy, power generation, and mining. They offer high versatility and can process a diverse range of materials with impressive efficiency. One of the key attributes of ball mills is their ability to handle both wet and dry grinding operations effectively.
In ball mills, spherical media are employed to crush and grind materials. When the mill is activated, it rotates either horizontally or vertically. The material is loaded into the mill's chamber, where it is subjected to the action of the moving balls. As the mill rotates, the balls collide with the material, exerting sufficient force to break it down into finer particles. This mechanical action, driven by the mill's rotation, transforms the material into a fine powder.
For a ball mill to operate effectively, it must achieve its critical speed. This is the speed at which the balls within the mill begin to move along the interior walls. If the mill does not reach this critical speed, the balls will remain at the bottom and exert minimal impact on the material, resulting in inefficient grinding.
Ball mills differ significantly from traditional milling machinery. Unlike conventional mills, which rely on cutting tools for material removal, ball mills utilize the motion of spherical balls. There is no cutting tool involved in the ball mill process; instead, the grinding action is provided by the movement and collisions of the balls within the mill.
Ball mills and conventional milling machines differ from one another in their distinct functions. Ball mills and conventional milling equipment are both used to grind materials into smaller pieces. Ball bills can handle materials like ore, ceramics, and paint, whereas conventional milling machines can handle huge workpieces.
A tube mill features spherical grinding media, but its length is significantly greater than its diameter. It consists of rotating cylinders with smooth interiors filled with hard, round balls. The interior lining of these mills is typically constructed from durable materials such as hardwood or iron alloys, including steel and manganese steel.
Tube mills are characterized by their elongated cylinders with simple, smooth interiors. Inside these cylinders, numerous round grinding balls are arranged. Unlike roller mills, tube mills lack a dedicated cooling system for welded arcs, often requiring an additional cooling method. They may also utilize advanced welding techniques, including modern laser welding. To improve the quality of the final product, some tube mills incorporate hand-woven tubes. These mills are commonly used for manufacturing plumbing pipes or tubes, which are typically found in plumbing and construction supply stores. The design of tube mills allows them to operate at high speeds, providing the necessary hardness for applications such as drainage systems.
Tube mills function similarly to belt grinders. The material, whether it be wire or sheet metal, is loaded into the drum, which then initiates the grinding process. The "grinders" inside the drum move back and forth to cut the material to the desired diameter. Some tube mills use a manual crank, while others are powered by electric motors. This process can involve either feeding the wire from within or grinding from the outside to achieve a consistent diameter and profile for ease of fitting and finishing.
In ore grinding applications, tube mills combine rotating discs with grinding wheels. The material, often steel, is placed inside the mill and then spun around the spindle over the grinding surface. As the balls in the disc rotate, they chip away at the material, forming sharp edges for cutting purposes. This method is akin to the operation of most belt grinders.
Unlike ball mills, rod mills utilize long rods as the grinding medium. These rods, similar to grinding balls, tumble within the mill to crush materials such as limestone and various ores. The rod mills are designed with a length-to-diameter ratio between 1.4 and 1.6 to prevent rod entanglement. They can handle feed sizes as large as 50 mm and produce output sizes ranging from 3000 mm to 270 mm. The grinding action is generated through line contact between the rods, which extend the full length of the mill. The rods rotate and tumble in parallel, mimicking the action of a series of roll crushers. This design minimizes the production of slimes and enhances the grinding of coarse materials.
Among the three main types of rod mills—overflow, end peripheral discharge, and center peripheral discharge—the overflow mill is the most commonly used. In the mineral processing industry, wet grinding with rod mills is preferred, although dry grinding is occasionally used despite its limitations. Rod mills operate at a slower speed compared to ball mills because the rods are rolled rather than cascaded. This slower speed leads to less steel consumption while achieving similar grinding efficiency due to better contact between the media and ore. Regular maintenance is required to remove broken or damaged rods and ensure optimal performance. Rod mills need careful monitoring as the rods must remain nearly parallel to avoid tangling and reduced grinding efficiency. The maximum rod length typically reaches around 6.1 meters (20 feet), which limits the length, diameter, and capacity of rod mills. Additionally, larger rods can lead to increased wear on mill liners and loaders.
Pebble mills, a variation of ball mills, utilize natural pebbles rather than spherical balls for grinding. These pebbles roll through the mill, effectively crushing materials contained within. They are particularly suited for grinding hard substances such as minerals, glass, advanced ceramics, and semiconductor materials to very fine sizes, often down to 1 micron or less. Pebble mills are sometimes known as ceramic-lined mills due to their use of ceramic linings. The extended residence time within the mill ensures that each particle undergoes consistent treatment, resulting in a narrow range of particle sizes and a more uniform product.
Historically, flint rocks were commonly used as the grinding media in pebble mills. However, modern industries now favor grinding materials made of aluminum oxide, with a composition ranging from 90% to 96%, and high-alumina bricks. These aluminum oxide (alumina) bricks are highly durable and provide excellent protection against contamination of the processed materials, making them ideal for lining contemporary pebble mills.
In the operation of pebble mills, small alumina grinding media are typically used to fill the rotating containers to about half their capacity. As the container turns slowly, the grinding media are lifted and then allowed to cascade down, continuously impacting the particles within. This process effectively grinds the material. The self-contained design of pebble mills offers the advantage of reducing worker exposure to the milled product. Pebble mills can be used for both dry and wet grinding, with wet grinding involving the dispersion of particles in a liquid medium.
In a grate-discharge mill, the diaphragm is designed as a grate, which controls the discharge of the grinding balls to the end of the mill. This grating system ensures that the ground material is retained in the space between the diaphragm and the opposite end of the mill, where it is collected by a scoop.
An air-swept mill utilizes a strong airflow to carry away the finer particles generated during the grinding process. This airstream passes through a classifier, which separates the fine particles from the coarser ones. The larger, rejected materials are then redirected back into the mill for further grinding. The mill features balls within a horizontally rotating drum, which is driven by an external gear mechanism.
Mixing involves the systematic combination of two or more different ingredients or particles to create a uniform material. Typically, ingredients are introduced into a rotating impeller via a trailing edge. The flow of material within the vessel is influenced by both the particle size and type, as well as the impeller's rotational speed. There are several types of mixers, including horizontal mixers, spiral mixers, and planetary mixers. Horizontal mixers are designed to handle large volumes of material, mixing them thoroughly before transferring the mixture to a trough for convenient transport. In contrast, spiral mixers use rotating spiral blades to achieve highly efficient mixing, ensuring thorough blending of ingredients.
A planetary mixer is a common kitchen appliance designed for mixing various food ingredients. It features a stationary bowl and rotating blades at the base that cut, crush, and blend the materials into a uniform mixture. Mixing, akin to dispersion, involves combining particles, with both processes using flow-driven methods to achieve the desired outcome. In mixing, two or more liquids are combined, and any applicable soluble solids are dissolved. The choice of impeller size in mixing depends on the properties of the ingredients, such as their viscosity and texture.
The milling process differs from mixing and dispersion as it focuses on particle-size reduction. After an initial dispersion, a blend requiring further size reduction is processed in a mill. Mills utilize various mechanical forces, including the medium, pegs, and screens, to break down particles to the desired size. This process maximizes ingredient yield and enhances product functionality. For coatings and inks, it contributes to color development, film properties, and flow characteristics.
To achieve the desired particle size, mills can be adjusted, and environmental conditions such as temperature can be controlled. With numerous types of mills available, selecting the right one can be challenging. Equipment suppliers often provide experimental services to help match the appropriate mill to specific needs and ensure optimal results.
This chapter will cover the various applications and advantages of milling machines. Additionally, it will address the maintenance practices necessary to keep these machines in optimal condition.
Mills are employed across numerous industries, including in many basic home applications. This section outlines some of the primary uses of mills.
In the pharmaceutical and chemical manufacturing sectors, mills are essential for grinding and reducing large particles into powders or fine-grained substances. Hammer mills are commonly employed to achieve an intermediate powder consistency. They are designed to produce a nearly precise particle size. However, hammer mills have limitations, such as their inability to handle sticky materials, which can clog the perforated screens.
In the food processing industry, mills are utilized for crushing and grinding various legumes. They are effective for processing nutshells, soybeans, certain seeds, and different types of beans. For removing hard shells, a hammer mill with lower hammer blows is typically employed, which helps in breaking down the tough outer layers.
In the medicinal and pharmaceutical industries, mills are crucial for micronization. They finely grind medicine particles to ensure precise dosage measurements for capsule packaging. By reducing the particle size, mills facilitate the accurate filling of capsules with the necessary quantities of medication.
Mills play a crucial role in breaking down large particles into smaller ones, enhancing their dissolution rate in solvents. Smaller particles dissolve more quickly, which can lead to time and cost savings in resource utilization.
Industrial mills are also used to mix various solid powders. They help create a uniform blend of dissimilar compounds, resulting in a well-integrated fibrous solid mixture.
Some ingredients require a boost in their chemical reactivity when added to formulations. Mills slightly crush these ingredients to enhance their activity, improving the overall effectiveness of the formulation.
In the automotive and mechanical industries, mills are employed for efficient scrapping processes. They crush surplus and spent metals, which are then melted down and repurposed for manufacturing new components or recycling.
Modern milling machines offer significant advantages in both industrial and home settings. Their robust construction and large size provide strong support, allowing them to handle heavy and bulky parts without damage. Additionally, these mills are designed with interchangeable components that can be replaced, ensuring continued operation even if parts become damaged.
Modern milling machines are often computer-controlled, which enhances their flexibility and precision. Computers allow for adjustments in grinding rates and cutting tools, optimizing machine efficiency and reducing the likelihood of human error. Automated systems ensure precise and consistent cuts that would be challenging to achieve manually. The integration of computer programs also facilitates full automation of the milling processes.
Furthermore, mills can be customized to meet specific user needs or to accommodate transportation and packaging constraints. They come equipped with various types of cutters designed for different applications, and can perform multiple cuts simultaneously, saving time and energy. The ability to produce complex shapes using multi-teeth and single-cutting tools, along with their capability to handle large batch productions, enhances their versatility.
Despite their advantages, milling machines have several drawbacks. They are often expensive to purchase, requiring a significant initial investment. Additionally, they consume a lot of electricity or fuel, leading to high operational costs. Their various sizes and weights make transportation challenging. Furthermore, milling machines are complex and require skilled operators, making them unsuitable for inexperienced users.
Early detection of issues such as a defective bearing seal can prevent costly repairs, as addressing minor problems early is cheaper than a full bearing replacement. Accumulation of waste material can obscure signs of damage, making regular cleaning and inspection crucial. Routine checks for equipment damage, protective covering integrity, and grout cracking are essential to avoid extensive issues.
While cleaning mills may seem straightforward, it requires careful handling. For instance, pressure hosing hot castings can cause cracks or deformation, and high-pressure sprays can lead to water ingress and premature bearing failure. It is important that staff are properly trained in cleaning procedures and that maintenance guidelines provided by the equipment supplier are followed to ensure proper care.
In conclusion, mills are devices that may be used in households or in an industrial setting to grind, crush, or cut huge materials into smaller, more manageable components. The mills are divided into many varieties according to their intended usage. Some mills are utilized in the mining sector where they are used to crush mineral ores from stones in order to separate them from the pure metal. To ensure that the mill lasts its whole lifespan and continues to function properly and efficiently, it is also crucial to have it cleaned and maintained.
Size reduction equipment refers to machines that crush and grind materials to reduce their size. Pulverizers are a type of size equipment, the names are used interchangeably. Size reduction is an essential...
Agitators are equipment used in homogenizing media inside a tank. It works by rotating the impeller at its immersed end at a controlled speed or revolutions per minute (rpm). The work exerted by...
Drum mixers are mixers that are used for mixing free flowing materials by rotating them forward and reverse with welded chutes or flights that fluidize the mixture. The design of drum mixers gives them...
An emulsifier is an emulsion device used for colloidal dispersion of liquid droplets of immiscible liquids in the presence of an emulsifying agent. It enables the combining of non-soluble solutions or liquids...
High shear mixers, also known as high shear reactors (HSRs), rotor-stator mixers, and high shear homogenizers, are used to emulsify, homogenize, disperse, grind and/or dissolve immiscible mixtures with components of the same or different phases...
A homogenizer is a type of mixing equipment used to create a uniform and consistent mixture. It works by breaking the components and evenly distributing them throughout the solution. The components are either immiscible, have varying sizes, or are in different phases from each other...
An industrial blender is a machine for large-scale production that consists of a large tank capable of mixing and blending batches of manufacturing materials to create a reaction between the materials. The many uses for industrial blenders are due to their capacity and...
A tank mixer is a mixing device that blends several different ingredients in a single tank to make a single solution. It is a mixing process capable of mixing wettable powders, liquids, emulsifiable concentrates, and surfactants. They mix and blend...
A mixer is a complex and precise tool that is used in combining and mixing of substances and chemicals for manufacturing, production, and industrial use. There are many types of industrial mixers including...
A plastic tank is a large capacity liquid or granular storage unit that can be vertical, horizontal, below or above ground, as well as movable. They are designed to hold several gallons of a variety of substances for long periods without experiencing wear, weathering, or deterioration...
A plastic water tank is a large capacity container designed to store water for household, agricultural, irrigation, and industrial manufacturing use. There are various types of water tanks produced to meet the needs of specific applications, with...
A poly tank is a plastic storage tank used to store, transport, and collect water, other liquids, and granular or powder materials. They are made of polyethylene or polypropylene and are a cost effective, lightweight, and easy to handle...
Pressure tanks are vessels that are used to store, hold, and/or convey gasses, vapors and fluids at pressures greater than atmospheric pressure, also known as high pressures...
Pressure vessels are enclosed containers used to hold liquids, vapors, and gases at a pressure significantly higher or lower than the ambient pressure. They are widely used in various industries such as...
Stainless steel tanks are widely used in food, beverage, dairy, medicine, cosmetics, and other manufacturing processes where cleanliness and purity are important. These are also used in industrial plants for storing chemicals and gases where strong resistance from chemical degradation is required...
A vertical conveyor is an engineered mechanical method for moving goods, products, supplies, parts, and components from a lower level to a higher level or from a higher level to a lower level. They are...