Door Latches
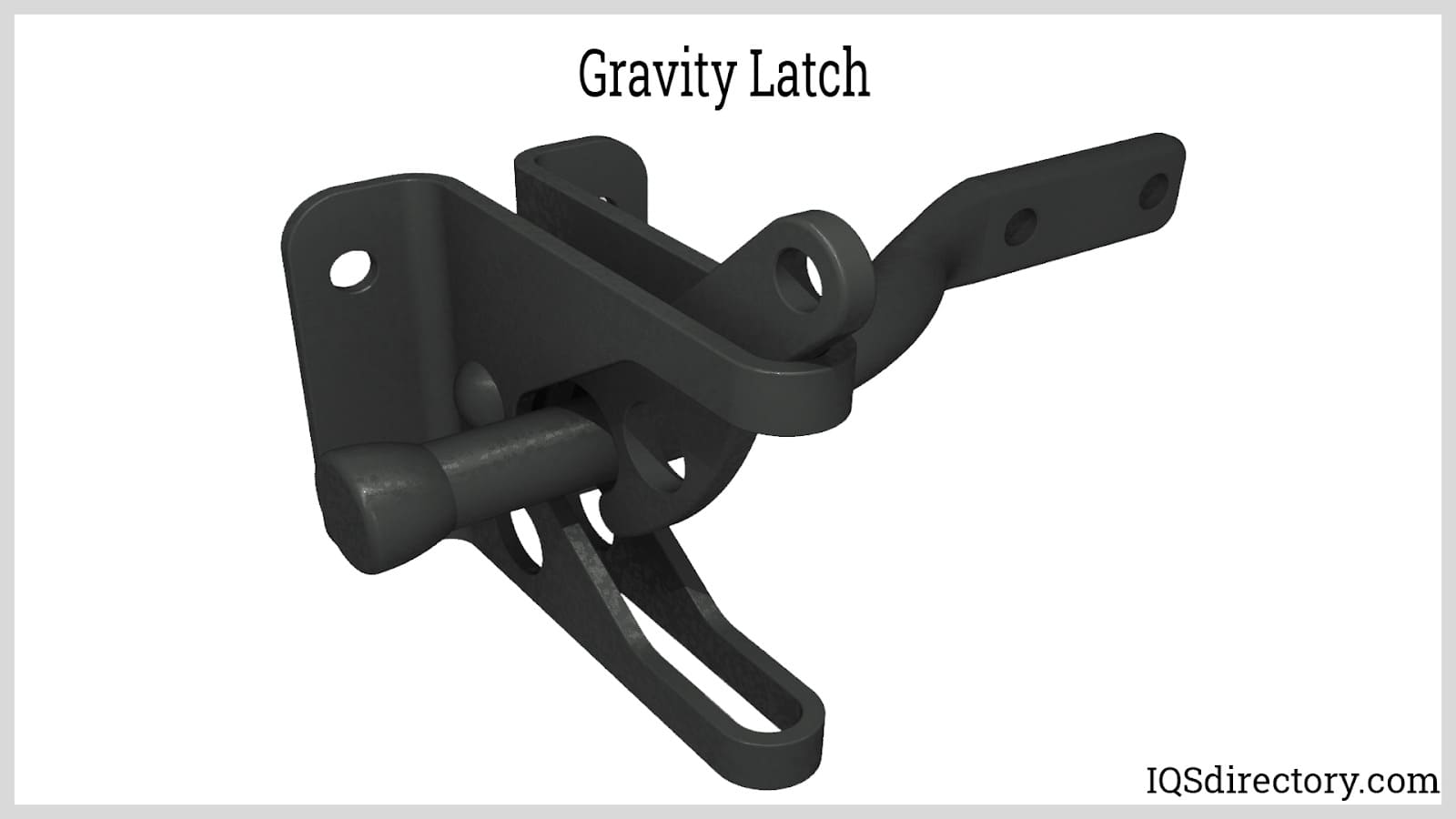
A door latch is a mechanical fastener that connects two surfaces or objects and provides a secure, safe, and strong connection. The latch portion of the mechanism is mounted on a flat surface such that when it meets a...
Please fill out the following form to submit a Request for Quote to any of the following companies listed on
This article is a thorough examination of rotary latches and their use.
You will learn:
A rotary latch refers to a locking mechanism designed to secure openings such as doors, enclosures, cabinets, and panels, preventing them from unintentionally opening. Also known as slam latches, these devices engage with a striker to lock when pushed into place. The fundamental components of a rotary latch typically include a housing, jaw, lever, and spring, where the housing supports the latch components and enables mounting. Rotary latches belong to a broader category of latches, often called slam latches, named for the action required to lock a door or lid securely.
There are several types of rotary latches available, mainly classified as single, double, and two-stage versions. A single rotary latch features a solitary rotating mechanism, whereas a double rotary latch includes two rotating mechanisms. The two-stage rotary latch operates in two segments to secure itself. An actuator, linked via a rod or cable, releases the latch to allow for the opening of doors or panels.
Rotary latches are straightforward to install and have been in use for securing vehicle doors, storage compartments, and industrial machinery doors for many years. They offer remarkable holding strength that remains reliable despite exposure to vibrations, stress, or harsh environmental conditions. Rotary latch systems are highly favored for their user-friendly nature, enabling disengagement with a single button press, unlike other latching systems that may require multiple actions to unlock and open an enclosure.
Rotary latches serve a straightforward purpose: they are built to secure and keep openings closed. Choosing the appropriate size and strength of a rotary latch is crucial for the effective operation of a mechanical system and its intended use. Selecting the right rotary latch involves understanding the different types available in terms of their function, strength, and suitability for the application.
Rotary latches are typically categorized into single, double, and one and two-stage types. Within these broad categories, rotary latches can be further classified based on materials, actuators, load capacities, and other factors to help choose the most suitable latch for a given application.
Each rotary latch offers various options that impact its performance and suitability. The primary factor in choosing a rotary latch is the type of opening and whether it is rigid or flexible. More complex systems may require multiple triggering options and adjustments to integrate the latch effectively into the overall system.
A single-stage rotary latch features a single rotor and can be configured for either right- or left-hand closing. This rotor engages directly with the striker. As the most basic type of rotary latch, it is suited for light to medium-duty applications. Despite its straightforward design, single-stage rotary latches offer various trip levers and mounting options. For optimal performance, they should be paired with a door that matches their weight capacity.
Single-stage rotary latches are favored for their compact design, which offers flexibility in various applications. Typically, these latches feature multiple actuation points and stacked actuator levers, making them highly configurable compared to other rotary latch types.
Two stage rotary latches are designed for heavy workloads and are commonly used in car doors. They come with built-in bumpers that trap the striker between rubber bumpers and the rotor, which eliminates noise and vibrations during the latch’s operation. Two stage rotary latches are similar to single stage latches in their appearance but differ in how they attach to the striker.
Two-stage rotary latches are chosen for their enhanced security features, including a secondary latching position that helps prevent false latching and accommodates misalignments. Like single-stage rotary latches, two-stage models can also include multiple actuator points, offering designers a range of configuration options.
Two-stage rotary latches feature a single rotor that connects to the striker. Similar to single-stage latches, these are suitable for light to medium loads. Their compact design, even with multiple actuators, allows them to fit into various spaces. However, their use is constrained by the thickness and weight of the door they are installed on.
Double rotor rotary latches enhance strength and offer greater tolerance for misalignment compared to other types. Designed to handle extremely high workloads, they feature two single rotors that provide a wider catch opening, improving their ability to manage misalignments. Suitable for medium to heavy-duty applications, these latches also include linkage for direct handle actuation. Like other rotary latches, double rotor models support both left- and right-hand mounting as well as push or remote release options.
A pawl rotary latch operates similarly to a two-stage rotary latch but includes a rotating cam that shifts between latch and unlatch positions. The cam mechanism is designed to engage with the striker. Initially, the pawl rotates a quarter turn to secure the striker. As the striker approaches the latch body, the pawl turns another quarter turn to fully engage the striker. Pawl latches allow movement in one direction and prevent reverse motion. They are often used in conjunction with a ratchet wheel.
Pawl latches come in two main types: fixed grip and adjustable grip. Fixed grip latches are designed to fit any door frame and rotate to compress against it. Adjustable grip pawl latches engage with the door frame or keeper as the handle turns. They feature a long shaft or bolt that separates the handle from the cam, allowing the grip length to be adjusted to match the door frame dimensions.
Quarter turn spring latches operate by rotating 90° to lock or unlock. This rotation moves a cross pin through a curved section at the bottom of the latch, which tensions the spring. The cross pin engages with a recessed section at the curve's end, ensuring a secure connection. The spring tension maintains a tight fit despite movement or vibrations. The locking bolt, retaining washer, and base of the latch are attached to the opening frame and can be installed in an enclosure without the need for tools.
Quarter turn spring latches are cost-effective and do not need fasteners or bolts for installation. To install, a thin loop is threaded through a vertical slit perpendicular to the pull. The latch is then twisted a quarter turn, pulled, and twisted another quarter turn to finish the installation. Folding down the latch lever secures the panels and engages the spring tension.
Quarter turn spring latches are commonly used in shrouds, riding lawn mower housings, water heater control panel doors, and electrical enclosures. They are the most cost-effective rotary latch available, with millions used by engineers annually.
Typically, rotary latches are operated with a key, handle, or lever. A special type, the rotary draw latch, requires a tool such as a screwdriver to open or close. This latch, like other draw latches, features a keeper and catch plate. The keeper hooks onto the catch plate and is drawn toward the latch as the locking mechanism is rotated using the tool.
The tension between the keeper and catch plate ensures that an opening or enclosure remains securely closed. Tool-operated rotary draw latches are commonly used in agriculture, especially for safety shield panels near moving parts or hydraulics. These latches feature mounting holes and are operated by rotating their head, which has a notch for inserting a tool. They can handle several hundred pounds of tension.
Rotary latches are widely used because of their longevity, strength, durability, and reliable performance under various conditions. They serve as locking mechanisms for cabinets, panels, doors, enclosures, and cages. A rotary latch system typically includes one or more actuators, a housing, rotors, a lever, and a spring. The complete system is made up of the actuator, connector, and the rotary latch itself.
The latch is the core component of a rotary latch system, and its strength depends on its size and durability. There is a wide range of latches available to meet various application needs. Choosing between a one-stage or two-stage latch depends on the required security level. Two-stage latches offer greater security and can prevent accidental opening of secured doors.
The rotor is a key component of a rotary latch, with most systems featuring a single rotor to engage the striker. While single rotor latches are more common, double rotor latches offer better tolerance for misalignments and provide greater strength. These factors are crucial in the selection process when configuring a rotary latch system.
Actuators in a rotary latch system come in various forms, configurations, and mechanisms and are the only visible part of the system. They act as the interface between the user and the latching mechanism. Besides functioning as the release mechanism, selecting the right actuator can also improve the strength and security of the system.
Choosing an actuator starts with deciding whether it will be placed on the inside or outside of the application. Interior actuators, such as finger pulls or push buttons, are designed to be flush with the surface of the opening. Actuators are available in various materials, including plastics, zinc, and aluminum, providing a range of options for different applications.
Exterior actuators offer a wide range of sizes, shapes, and designs, similar to interior options. They can be flush mounted, surface mounted, or available as push handles and push buttons. Additionally, exterior actuators may include keys or key codes. Mechanical inputs, such as cables, are commonly used to activate actuators, providing quick and convenient access. Alternatively, rods can be used instead of cables for transferring mechanical energy.
Cables for actuators are typically coated to enhance their appearance and durability. They are made from resilient materials that withstand various weather conditions. Designed to endure thousands of cycles, these cables must resist stretching and deformation. Actuator cable liners enable the cable to flex and move without significant wear over time.
In high-security environments, an electromechanical actuator can be utilized to remotely release the rotary latch while also monitoring who is operating the locking system.
Just as there are many types of actuators, there are also numerous end fittings for cable connections, each compatible with different latch styles. Manufacturers offer a variety of cable end fittings, including barrels, L, Z, eyelet, ball, and bare cable. The choice of end fitting depends on the specific needs of the application. Barrel fittings are versatile and can connect to any actuator, while L fittings are specifically designed for rotary latches and are installed with a retaining clip to avoid metal-to-metal contact.
The striker in a rotary latch system attaches to the latch and connects to the door or opening. It may be a short rod or shaft or have a U shape, resembling a U-shaped bracket. Made from highly durable materials, strikers are designed to endure numerous cycles of opening and closing. As the door closes, the striker engages with the rotor or rotors of the latch, which encircle and secure it, ensuring a firm hold through the locking mechanism.
The striker must fit securely into the rotor and rotary latch to prevent any movement or potential for the opening to be jostled open. Despite its simple design, the striker is a crucial component of the rotary latch system, as it locks the opening to prevent unauthorized access. Strikers are typically made from steel, stainless steel, or other hardened metals to ensure durability and strength.
The strength, longevity, and durability of a rotary latch are influenced by the materials used in its production. The choice of metals depends on the latch's intended use. Critical and high-security latches require hardened metals for increased strength, while latches subjected to less stress can be made from softer, less durable metals.
Rotary latches are manufactured from metals such as carbon steel, alloy steel, stainless steel, aluminum alloys, and copper alloys, selected for their formability, machinability, and strength. After forming, latches may undergo secondary processes like polishing or coating to improve their appearance. The type of coating applied is chosen based on the expected number of cycles the latch will endure.
Aluminum is chosen for manufacturing rotary latches due to its positive properties, such as resistance to impact, moisture, and corrosion. The 6000 series aluminum alloys are selected for their strength and ability to endure frequent use. While softer alloys may look better, they lack the strength needed to secure a latch effectively. Aluminum is an ideal material because it can be easily cast, forged, shaped, and molded into the complex forms required for rotary latches.
Brass has historically been used in the production of latches, but its use has declined with the rise of more durable metals. Brass, an alloy of copper and zinc, is castable, moldable, and strong. However, its appearance can deteriorate over time and may require regular cleaning. Despite these drawbacks, brass remains a choice in some regions for its decorative qualities and strength in rotary latch manufacturing.
Bronze latches are used in various environments due to the high copper and tin content of bronze. Although it is one of the more expensive metals for latch manufacturing, bronze offers an excellent appearance. The copper content in bronze makes it both moldable and castable, resulting in harder and more durable latches that can withstand multiple cycles.
Carbon steel is the toughest and most durable metal used in rotary latch production. Although it can be challenging to work with, it is one of the least expensive options and is typically forged or cast into the desired shape. Carbon steel latches are ideal for demanding conditions that involve frequent use. To combat rust and corrosion, carbon steel rotary latches are usually coated, metal-plated, or painted.
Stainless steel is a popular choice for manufacturing rotary latches due to its cost-effectiveness and protective coating, which ensures excellent appearance and durability. Unlike carbon steel, stainless steel can be cast, forged, molded, or stamped from sheets, offering greater workability while maintaining comparable strength. Its appearance makes it suitable for both residential and industrial applications. Users often prefer stainless steel latches over aluminum and carbon steel for their superior longevity.
The manufacturing processes for producing latches can stress the metal, leading to marks and scratches. To enhance their appearance, rotary latches undergo finishing methods that address surface imperfections. Common finishing techniques include painting, polishing, powder coating, and plating, each designed to improve the latch’s look and surface quality.
In addition to enhancing the appearance, these finishing processes provide a protective layer that helps prevent rust, corrosion, wear, and damage from impacts.
The primary methods for fabricating latches are die casting, stamping, and forging, which shape metals into latch components. After forming plates, discs, and sheets into various parts, these components are assembled using techniques such as spot welding or screwing. Despite the durability of the materials, proper assembly is crucial, as any loose or improperly connected components can lead to latch failure.
Stamping encompasses several processes, including blanking, punching, embossing, and die stamping of metal sheets. This method deforms the metal under force to achieve the desired shape for latch components. Stamping is favored for its speed and efficiency, allowing large volumes of parts to be produced in a single run.
Metals commonly used for rotary latches, such as stainless steel, steel alloys, aluminum, brass, and copper alloys, are well-suited for stamping. This method not only boosts productivity but also achieves precise tolerances, essential for accurately fitting latch components into small spaces.
Forging, like stamping, involves shaping metal discs, sheets, or plates using force and hammering. The main forging methods are open die, closed die, and upset, and can be performed as hot forging or cold working. These processes apply substantial pressure repeatedly to form and shape rotary latch components. Forging enhances the strength of parts by altering their grain structure. However, parts produced by forging often require additional finishing to remove waste or flash from the shaping process.
Forging, like stamping, achieves precise tolerances that meet industry standards. It is used to produce nearly all components of a rotary latch, including the striker. Achieving the desired shape may require multiple passes through the forge. In addition to trimming the finished parts, secondary processing might involve adding holes, bending, or cutting shapes into the workpiece.
Stamping and forging are forms of cold working processes that pound, hammer, and force metal sheets and billets into a mold or specific shape. They are based on applying pressure to a workpiece in order to achieve a necessary shape. During stamping or forging, the workpiece is a solid form even though it may be heated to make shaping it easier. With casting, the metal is melted and poured into a mold or die.
Casting involves using either permanent or temporary molds to shape molten metal. Metal ingots, billets, or slabs are melted in a furnace and transferred to a mold via a crucible. The molten metal is poured into the mold through a sprue or riser. Permanent molds consist of two tightly fitted halves, whereas nonpermanent molds can be made from materials such as sand, wax, or other substances.
Unlike stamping and forging, casting molds must account for shrinkage that happens as the metal cools. This factor is crucial as it affects the final part's tolerance. The casting process is favored for its ability to produce latch components with intricate details and precise shapes that match the design specifications of the latch.
Regardless of the production method used for rotary latch components, each part undergoes secondary processing. This can involve adding holes, smoothing surfaces, bending, shaping, and configuring components to ensure a precise fit. Despite achieving excellent tolerances, every component must fit accurately to ensure the latch's strength and durability. Secondary processes shape and form each piece to ensure proper assembly. Often, welding and screws are employed to connect and secure the components.
For many years, rotary latches have been employed in diverse applications, from securing cupboards to ensuring car doors are tightly sealed. Their strength and reliability make them a crucial component in engineering designs. Rotary latches are preferred over cam latches and push-to-close latches due to their superior performance and dependability.
Unlike other latches that require multiple actions to disengage, rotary latches can be released with a simple push of a button or pull of a switch. This feature allows for quick access to an enclosure. Additionally, engaging the locking mechanism is straightforward, requiring only a push or slam of a door or lid to securely close the opening.
One reason for the popularity of rotary latches is their secure engagement, which helps prevent accidental entry. They can be designed with no visible means of access, reducing the risk of break-ins or theft. This security makes rotary latches a preferred choice for auto manufacturers to secure compartments. Additionally, specialty rotary latches can be operated by an interior button or switch for convenience.
The long lifespan of rotary latches reduces overall costs and makes them an ideal locking mechanism. Their simple structure allows for installation in a wide range of applications. With a maintenance-free design, rotary latches do not need replacement during their service life. Made from exceptionally strong and durable materials, they resist damage from wear and tear as well as external factors like impacts and abrasions. This sturdiness makes them suitable for both indoor and outdoor use.
Rotary latches come in a wide variety, making it possible to find one suited for any condition or environment. Over the years, these latches have been adapted and engineered to meet diverse requirements, with custom options continually emerging to address new and unique challenges. Manufacturers collaborate closely with customers to ensure that each latch perfectly matches the application and needs. The compact design of rotary latches is a key advantage, allowing them to fit seamlessly into any environment, even under stressful or harsh conditions.
A door latch is a mechanical fastener that connects two surfaces or objects and provides a secure, safe, and strong connection. The latch portion of the mechanism is mounted on a flat surface such that when it meets a...
A gate latch is a locking mechanism that is used to secure gates on fences or stakes on truck beds using a metal bar and lever that is raised to open the latch and lowered to close it. Although they do not have...
Latches are mechanical components that allow the temporary joining of parts that are moving relative to each other. They are actuated to release the coupling and allow the two parts to separate. Latches are mostly seen on doors and enclosure...
A magnetic door latch is a type of latch that consists of a striking pad and a magnet and is used to keep doors and gates closed. Magnetic door latches are also known as magnetic door stops, magnetic door catches, and door magnets...
Rubber latches are latches made of rubber or are composed of rubber components. They are used in the automotive, aerospace, and medical equipment industries due to their flexibility, durability, and non-abrasive properties...
A spring latch is a mechanical device that is utilized in the joining of two separate components in order to prevent movement or opening. A spring latch is locked with a spring compression so that it will not be released...
A hinge is a movable joint or mechanism that joins two items together. The hinge is one of the most popular categories of mechanical bearings. Butt hinges are a particular kind of hinge that have rectangular pieces that...
A concealed hinge, also known as a hidden or European hinge, is a type of hinge that has parts invisible to the onlooker when the door is closed. They are commonly used in cabinet doors to add an aesthetically pleasing and...
A continuous hinge is an extended single unit hinge that spans the full length of a door, cabinet, lid, or enclosure entrance. They are made of lightweight metals and can be cut to fit the size of any opening...
An eyelet is a metal, rubber, or plastic ring with flanges are used to strengthen or reinforce holes punched in thin fabrics. It is a smaller counterpart of a grommet that is bigger in size and used for more heavy duty materials...
A hinge is a machine element that connects two bodies allowing angular movement about a fixed axis of rotation, all the while preventing translations and rotations on the remaining two axes. A hinge can be...
A fastener is a non-permanent or permanent mechanical tool that rigidly connects or affixes two surfaces or objects together. Non-permanent fasteners can easily be removed without damaging the joined materials...
A friction hinge works by creating a specific tolerance in between the mechanical components. It works based on the principle of torque that can be achieved by applying a desired amount of force. Some other additions to these hinges such as...
A lock is a mechanism designed to connect an opening to its frame using a latch, solid cylinder, bolt, or some other form of a solid metal plunger that extends into the strike. They are metal devices that prevent entry or access for privacy, security, or...
A metal washer is a small flat piece of metal that has a hole in the center and is used as a spacer, a method for absorbing shock, or distributing the load of a fastener. The hole in the middle of a metal washer allows for a bolt or screw to pass through...
A self-drilling screw is a type of tool that has the same design features as a drill bit or cutting tool. As the name implies, self-drilling screws do not require a pilot hole in order to perform as a fastener...
A spring hinge is a self-closing hinge that automatically closes two connected workpieces using the action of a spring that is loaded into the hinge's barrel. They can be found in a wide variety of products such as...
Stainless steel hinges connect two components while allowing them to move in relation to one another. They can have various leafs shaped like rectangles and other forms depending on the type of stainless steel hinge. Stainless steel hinge leafs are...