Door Latches
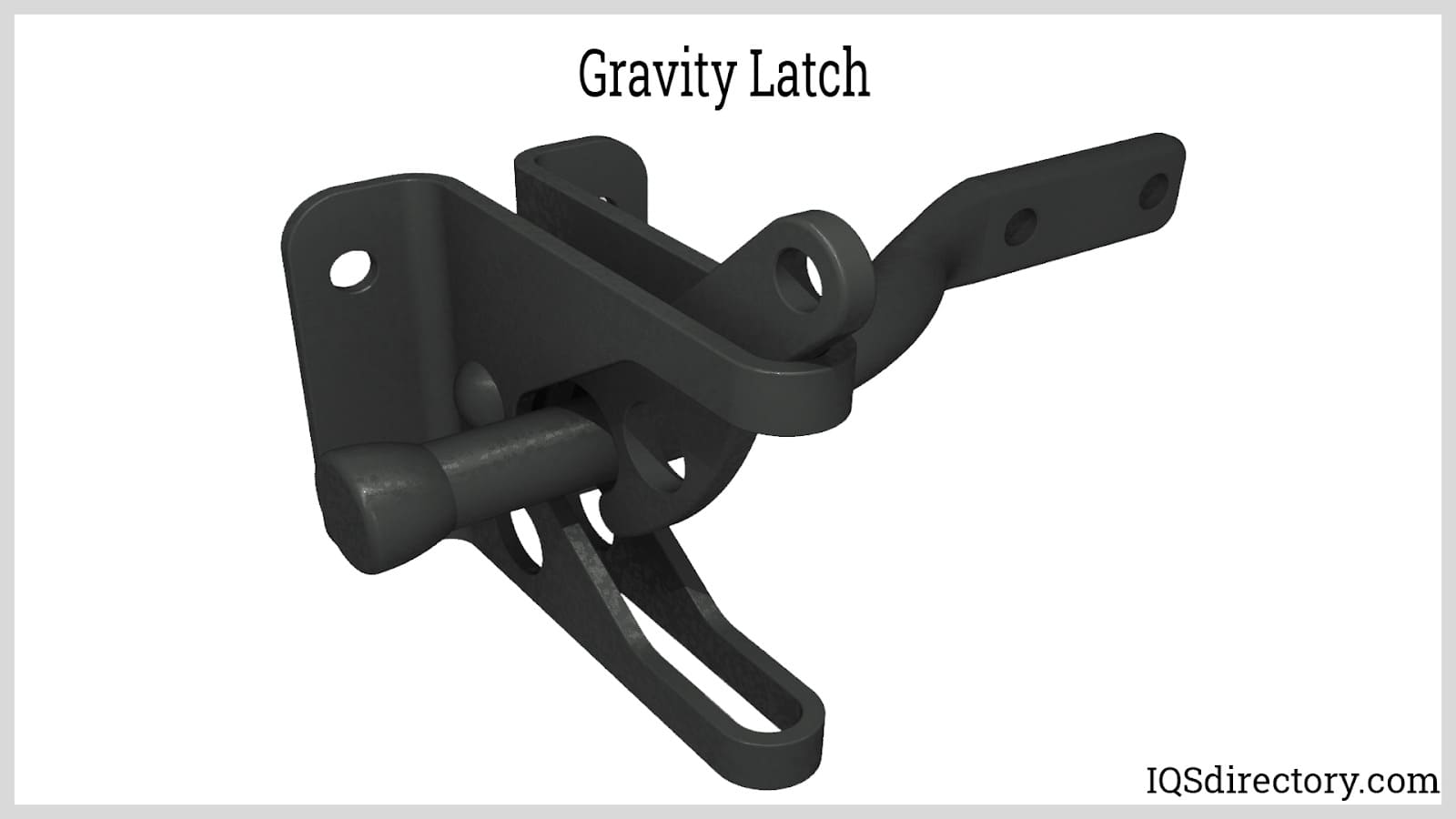
A door latch is a mechanical fastener that connects two surfaces or objects and provides a secure, safe, and strong connection. The latch portion of the mechanism is mounted on a flat surface such that when it meets a...
Please fill out the following form to submit a Request for Quote to any of the following companies listed on
This article contains everything you need to know about rubber latches and their use.
You will learn:
Rubber latches find applications in a multitude of industries for the purpose of fastening and securing items, surfaces, and openings. Their combination of flexibility and robustness, alongside their dependable grip, renders them indispensable for various uses. Usually constructed from rubber or incorporating rubber components, these latches are prevalent in sectors such as automotive, aerospace, and medical equipment, thanks to their strength and long-lasting nature. Rubber latches provide a firm and secure closure for doors and lids, effectively sealing the interfaces between surfaces.
A rubber latch includes a stretchable rubber strap attached to a frame, engineered to extend and secure an opening. The defining characteristic of a rubber latch is its elasticity, allowing it to be pulled over hooks, knobs, or anchorage points. The tension exerted by the strap guarantees the latch stays tightly closed and securely in place.
Rubber latches stand out as crucial fastening solutions, renowned for their adaptability, durability, and user-friendliness. Their flexible design and reliable grip make them ideal for stabilizing objects and equipment, even in demanding environments. As technological advancements continue and novel materials emerge, rubber latches are set to progress, preserving their flexibility and significance in the ever-evolving field of fastening systems.
There are several distinct classifications of rubber latches, catering to a wide range of industrial and consumer applications. Latches may be constructed entirely from rubber, made from a combination of rubber and other materials such as stainless steel or zinc-plated alloys, or feature layered designs that enhance their performance in specialized environments. The diverse types of rubber latches are engineered to address unique operational, environmental, and sealing requirements—making them critical components in sectors such as automotive manufacturing, marine hardware, industrial equipment, electronics enclosures, HVAC units, outdoor cabinets, and medical devices.
Toggle latches incorporate a robust metal toggle that works in tandem with a durable rubber catch to deliver a secure, vibration-resistant closure—ideal for cabinets, toolboxes, and marine hardware. Their integrated design is particularly valued in the marine industry, where corrosion resistance and long-term reliability under exposure to saltwater are critical performance factors. These latches often include features such as stainless steel components, reinforced rubber for improved elasticity, and adjustable tension mechanisms for a custom fit, meeting the demanding sealing requirements faced by boats, recreational vehicles, and outdoor enclosures.
Magnetic latches integrate a powerful magnet with a precision-molded rubber catch, resulting in a quick and reliable closure solution often found in cabinets, doors, access panels, and electronic enclosures. The soft rubber minimizes noise and protects surfaces from scratches, making these latches attractive for applications where aesthetics and repeated use are concerns—such as furniture, office panels, and commercial appliances. Their simple operation and consistent holding force make them popular for consumer electronics, laboratory cases, and storage lockers needing rapid access while maintaining secure closure.
Pull latches combine an ergonomic rubber handle with a metal catch or baseplate, delivering a firm and easily operable closure for doors, cabinets, machinery panels, and vehicle compartments. They are frequently used in the automotive industry, where their vibration-dampening properties, tight sealing capabilities, and resistance to environmental factors ensure a dependable, long-lasting fit. Pull latches are essential in heavy-duty trucks, RVs, and utility vehicles, where they prevent accidental openings and minimize rattle, assuring both vehicle safety and equipment integrity.
Snap latches rely on the elastic properties of a rubber catch and a metal spring to close securely with a positive "snap." They are especially prevalent in the medical equipment industry, laboratory cabinetry, and portable instrumentation, where a tactile, audible confirmation of closure is desired. The rubber component helps isolate vibration and reduce noise, while also offering chemical resistance in harsh or sterile environments. Snap latches support frequent access, making them suitable for supply carts, instrument enclosures, and electrical panels.
Over-center latches featuring a rugged rubber catch and a preloaded metal spring deliver robust holding power for doors, enclosures, machinery covers, and transport containers. These latches excel in the transportation sector and with industrial equipment, providing high strength, shock-resistant closures on vehicles and heavy machinery. The over-center action ensures the latch remains tightly closed even under vibration or impact, protecting goods and components from dust, water ingress, and accidental openings during transit.
Rubber draw latches, similar to traditional draw latches, replace metal construction with high-quality, weather-resistant rubber materials. This type of latch is favored in the automotive and marine industries for its superior resistance to environmental exposure—offering watertight and dustproof performance on hatches, storage boxes, and exterior panels. Their inherent flexibility compensates for slight misalignments, which is especially important when sealing against vibration or in outdoor environments.
Rubber T-handle latches feature a molded rubber handle and latch mechanism, allowing operators to achieve a secure and weather-resistant seal on doors, industrial cabinets, toolboxes, and RV storage. Their design enables easy manual operation, even with gloved hands, making them ideal for outdoor equipment, transportation storage, emergency vehicles, and agricultural machinery. The rubber provides excellent grip and shock absorption, further enhancing latch durability and user experience in demanding applications.
These latches utilize a flexible rubber handle and catch mechanism to establish a reliable and weatherproof seal for a wide array of applications, including doors, cabinets, cases, and panels exposed to the elements. In the automotive sector, rubber pull latches are engineered for both interior and exterior use—offering exceptional resistance to UV rays, ozone, and extreme temperatures, while ensuring a vibration-free, secure fit. Their non-marring and corrosion-free properties make them equally valuable in electronics, marine storage, and equipment cases.
Key Advantages and Selection Criteria
Each type of rubber latch—whether a hybrid design or composed fully of rubber—offers a unique set of characteristics to fit a variety of industrial and commercial needs. Key benefits include:
The choice of rubber latch should be informed by factors such as industry standards, load requirements, exposure conditions, frequency of use, and compatibility with surrounding components. Whether you’re seeking a vibration-resistant enclosure latch for a truck, a corrosion-proof closure for marine storage, or a chemical-resistant latch for laboratory equipment, understanding the differences among rubber latch types will help you select the optimal solution for your specific application.
To further compare designs, materials, and suppliers—or to discover custom rubber latch solutions—visit our rubber latch resource page or contact leading rubber latch manufacturers.
Rubber latches are vital components used in a wide variety of industrial, automotive, marine, and electronic applications due to their durability, flexibility, and resistance to harsh environments. The manufacturing of rubber latches utilizes advanced rubber processing techniques that are carefully chosen based on the latch’s intended performance, required mechanical properties, environmental compatibility, and the type of rubber material required (such as EPDM, silicone, or neoprene). When manufacturing rubber latches, engineers and manufacturers must evaluate whether the latch design incorporates metal or plastic inserts, whether it demands chemical or weather resistance, and whether it will be subjected to high or low temperatures.
The production processes for solid rubber latches differ significantly from those for latches with metal-to-rubber bonding or integrated metal hardware. These differences are driven by the intended application—whether the latch must provide strong clamping force, shock absorption, or environmental sealing. The result is a wide spectrum of manufacturing techniques tailored to the exact needs of the end user, the specific latch style (draw latches, toggle latches, or compression latches), and industry requirements.
Rubber injection molding is a popular method for creating rubber latches because it allows for the production of complex shapes and features. The process involves injecting molten rubber material into a mold, where it cools and solidifies to form the desired shape. The resulting part can then be trimmed, cleaned, and assembled into a complete latch. Injection molding is favored for its efficiency in mass production runs, consistent part quality, tight tolerances, and ability to process performance elastomers, which is critical for applications requiring strong, long-lasting latch mechanisms. Common elastomeric compounds used include silicone rubber and nitrile rubber, both valued for their resilience and versatility.
This process, akin to compression molding, offers enhanced control over material flow, making it ideal for complex designs. It is compatible with various rubber materials, including silicone, EPDM, and neoprene. Transfer molding is commonly used for manufacturing rubber latches that require precise dimensions and intricate metal insert encapsulation. The process is ideal for medium-volume production and offers excellent part-to-part consistency. Transfer molding supports the fabrication of custom rubber latches for sensitive industrial or electrical applications where dimensional accuracy and secure bonding between metal and rubber are critical.
Compression molding is a widely used method for producing rubber latches. This process involves placing a pre-cut piece of rubber material, known as the charge, into a heated mold cavity. Pressure is then applied to compress the material into the desired shape. Afterward, the part is cooled and solidified before being removed from the mold. Compression molding is cost-effective for low to medium production quantities and is particularly suited for molding large, simple geometric shapes or heavy-duty latches that require enhanced tear resistance and strength. The technique supports a broad selection of elastomer materials, making it ideal for custom latch designs or replacement parts in maintenance and repair operations.
Liquid injection molding is a process ideal for creating highly precise and detailed rubber components, including rubber latches. It involves injecting liquid rubber material into a heated mold cavity under high pressure, where it solidifies into the desired shape. This method is particularly suited for high-volume production runs. Manufacturers favor this process for applications that demand excellent dimensional stability, repeatable tolerances, and superior surface finish, such as medical, electronics, or food-grade rubber latches. Liquid silicone rubber (LSR) is often selected for its excellent performance in extreme temperature fluctuations and its biocompatibility.
While extrusion is not typically used for creating complete rubber latches, it is useful for producing certain components of a latch, such as seals or gaskets. Extrusion involves pushing rubber material through a die to form a continuous length of material with a uniform cross-section. Extruded rubber profiles are frequently integrated with latching mechanisms to offer superior sealing, weatherproofing, or vibration isolation for enclosures, cabinets, or industrial equipment. Custom extruded rubber parts can be co-extruded with multiple materials or designed to match the precise profile requirements of specialized latching solutions.
Overmolding is a process where rubber material is molded over an existing part or substrate to create a rubber coating. This process can be used to create rubber latches that have a hard plastic or metal core for added strength and durability. Overmolded latches are engineered to provide enhanced ergonomics, improved grip, and increased protection against impact, chemicals, or UV exposure. This technique is frequently leveraged in high-performance industries, such as automotive or aerospace, where durability and safety are paramount considerations in latch design.
Choosing the right rubber latch manufacturing method is critical for meeting the functional and performance requirements of the intended application. Injection molding is ideal for crafting small, detailed rubber components at scale, while compression molding is better suited for larger, robust parts with simpler geometries. Transfer molding excels at producing parts with intricate internal features or requiring metal-to-rubber bonding. Liquid injection molding is especially effective for transparent or hygienic components used in medical, food processing, or laboratory equipment. Meanwhile, extrusion creates continuous rubber profiles used in combination with latch assemblies, enhancing sealing and flexibility. Overmolding enables multi-material integration, combining strength and comfort for end-user interfaces. Ultimately, each technique allows manufacturers to custom-engineer rubber latches optimized for longevity, environmental resistance, and precision fit, ensuring optimal performance in even the most demanding environments.
Rubber encompasses a diverse array of materials, ranging from natural rubber sourced from rubber trees to synthetic variants created through polymerization and blending with other substances. For rubber latches, the type of rubber selected can significantly impact both the durability and strength of the latch, as different rubber types offer varying levels of tensile strength and resistance to wear.
Natural rubber is a flexible material known for its tear resistance, durability, and low compression set. It offers excellent tensile strength and resists fatigue, chipping, cutting, and tearing. However, it is vulnerable to damage from heat, light, and ozone. Common applications include seals, gaskets, and shock absorbers. Natural rubber is typically shaped through injection and compression molding processes.
This synthetic rubber material is highly resistant to weathering, ozone, and aging, making it ideal for outdoor applications. It is often used in automotive and marine applications, as well as in electrical insulation. Neoprene can be molded using methods such as injection molding or compression molding.
This rubber material is highly resistant to extreme temperatures and UV radiation, making it perfect for high-temperature environments. It is frequently used in gaskets, seals, and medical devices. Silicone rubber can be molded through liquid injection molding or compression molding.
This synthetic rubber is known for its resistance to weathering, ozone, UV radiation, and various chemicals. It's commonly utilized in automotive and construction industries, as well as in seals and gaskets. EPDM is moldable using injection molding, compression molding, and transfer molding.
This synthetic rubber offers excellent resistance to oil, fuel, and other chemicals, making it ideal for automotive and industrial uses. It is often employed in seals, gaskets, and hoses. Nitrile rubber can be shaped through injection molding, compression molding, and transfer molding.
Rubber materials are compatible with various molding methods, depending on the application and desired characteristics. Natural rubber can be molded through injection, compression, or transfer molding based on factors such as part size, complexity, and production volume. Similarly, silicone rubber is molded using liquid injection or compression molding, depending on part geometry and precision needs. The selection of the rubber latch production process is influenced by the rubber’s properties, part complexity, required volume, and precision level.
Rubber latch design is highly flexible due to the adaptable nature of rubber, allowing it to be molded and shaped to fit any design requirements. Understanding the properties of the chosen rubber material is crucial to creating an effective latch design.
While many standard rubber latches exist, manufacturers often offer custom designs to meet unique or specialized needs. These custom designs often require a high level of craftsmanship and engineering expertise, which rubber latch manufacturers provide.
Selecting the appropriate rubber material depends on the specific application and the required characteristics such as hardness, temperature resistance, and chemical resistance. For instance, silicone rubber might be selected for its high-temperature resistance, while EPDM rubber might be chosen for its superior weather resistance.
The complexity of the latch design influences the manufacturing process. Injection molding is suitable for intricate designs with detailed features, whereas compression molding might be more appropriate for simpler designs with larger dimensions.
Tight tolerance requirements affect the choice of manufacturing process and material. For example, liquid injection molding may be preferred for parts requiring precise tolerances, while extrusion could be used for larger parts where tolerances are less critical.
The design should ensure adequate strength and durability for the intended application. This might involve opting for a thicker or more robust design, or selecting a stronger material like neoprene or natural rubber.
Environmental factors that could impact the rubber latch, such as exposure to extreme temperatures, UV radiation, or chemicals, must be considered in the design. The selected material and design need to withstand these conditions to ensure long-term reliability.
Having covered the basic design and engineering principles for rubber latches, let's connect this information with our previous discussions on rubber types and the processes used to create rubber latches. For example:
In designing silicone rubber latches, considerations might include accommodating its high durometer and lower tear strength. Compression molding could be an effective process for producing silicone rubber latches due to its ability to work with high-durometer materials.
When working with EPDM rubber, design considerations might include its low compression set and excellent weather resistance. The extrusion process could be ideal for creating EPDM rubber latches, particularly for applications requiring long lengths of uniform cross-section, such as sealing.
For natural rubber, design considerations might focus on its high elongation and tear strength. Compression molding is a suitable method for creating natural rubber latches, as it handles materials with high elongation and tear strength well.
Designing neoprene rubber latches might involve considering its resistance to oils, chemicals, and weathering. Injection molding could be the best choice for neoprene rubber latches, especially for producing complex shapes and small parts with tight tolerances.
In the case of nitrile rubber, design considerations could include its resistance to oils, fuels, and chemicals. Transfer molding might be the preferred process for nitrile rubber latches, as it handles materials with good flow properties and produces parts with stable dimensions.
Rubber latches are versatile and can be applied in a broad spectrum of industries, including industrial, commercial, and residential sectors, with marine applications being particularly prevalent. The resilience of different rubber types makes them ideal for securely fastening doors and preventing panel movement.
In the automotive industry, rubber latches are commonly found on doors, hatches, and various compartments. They provide secure closure, reduce rattling, and mitigate noise thanks to their durability and ability to withstand vibration and impact.
Within the aerospace industry, rubber latches are employed in aircraft doors, panels, and hatches to ensure secure closure and minimize cabin noise.
Rubber latches are integral to medical equipment, such as cabinets and carts, where they ensure secure closure and help prevent contaminants from entering.
In industrial settings, rubber latches are used in machinery and tools to provide secure closures and to help reduce noise and vibration.
Rubber latches are often utilized in outdoor settings, including enclosures, sheds, and cabinets, due to their ability to withstand harsh weather conditions.
In the electronics industry, rubber latches are employed on equipment enclosures due to their effectiveness in safeguarding against dust, moisture, and other environmental hazards.
Rubber latches are a common feature in sports equipment like backpacks and bags, valued for their flexibility and reliable fastening capabilities.
Rubber latches are widely used in military applications on cases and containers, where their durability, weather resistance, and ability to withstand harsh conditions are critical.
Rubber latches are particularly suited for electrical applications due to their non-conductive properties, which prevent issues related to conductivity. Their strength, durability, and impact resistance make them ideal for securing components in extreme environments. Additionally, rubber latches are highly resistant to rust, corrosion, and UV exposure, making them a perfect choice for outdoor control and electrical panels.
For thousands of years, civilization has relied on rubber as a robust and enduring material. The material's journey into modern applications began with Charles Goodyear's invention of the vulcanization process during the early stages of the first industrial revolution. Since then, the versatile properties of rubber have captivated manufacturers and expanded its use in various industries.
One of the key advantages of rubber latches is their ability to flex and adapt to irregular shapes and sizes, making them perfect for situations where a tight seal is crucial, such as on enclosures or containers. Their capacity to absorb shock and vibration further enhances their suitability for applications requiring a dependable hold in dynamic conditions.
Moreover, rubber latches offer resistance to various chemicals and adverse weather conditions, making them versatile for use across numerous industries, including automotive, marine, and aerospace. This combination of flexibility and resilience ensures that rubber latches provide a reliable and secure solution for many applications.
Rubber latches are renowned for their durability, as the resilient nature of rubber enables it to withstand significant wear and tear. This quality makes rubber latches ideal for applications requiring repeated use or a secure seal, particularly in automotive, marine, or industrial environments.
Engineered to resist harsh weather conditions, rubber latches can endure extreme temperatures, rain, snow, and sunlight. This weather resilience makes them suitable for outdoor applications where other materials might deteriorate due to exposure.
Compared to latches made from metal or plastic, rubber latches offer the added benefit of noise reduction. The natural dampening properties of rubber help minimize the noise produced when the latch is engaged or disengaged, enhancing the overall user experience.
Rubber latches exhibit strong resistance to corrosion, making them ideal for environments exposed to corrosive substances like saltwater or chemicals. This resistance ensures their longevity in marine, industrial, or chemical processing applications, where other materials might corrode or degrade.
As a cost-effective alternative to metal or plastic, rubber latches offer significant savings. Rubber's relatively low production costs and its ability to be molded into various shapes and sizes make it a versatile option for a wide array of applications.
There have been notable instances where innovative rubber designs and concepts have revolutionized approaches to manufacturing challenges. These breakthroughs have redefined how rubber is perceived and utilized. Designers, engineers, and developers have found that rubber can be tailored to meet requirements that surpass the capabilities of other materials.
In one instance, a major automobile manufacturer incorporated rubber latches into a new vehicle design featuring a motorized arm that extended to open the door. The rubber latch securely held the door in place when closed, offering a tight seal and absorbing shock and vibration. This application exemplifies the flexibility of rubber latches in providing a secure and comfortable ride.
This application underscores the versatility of rubber latches, which adapt to dynamic environments by offering a secure hold and mitigating shock and vibration.
An off-road vehicle manufacturer sought a latch that could endure the rigorous conditions of off-road environments. They opted for rubber latches, which demonstrated superior durability and longevity compared to their previous metal latches. The rubber material effectively withstood impacts and vibrations without failure.
A company specializing in outdoor electronics enclosures required a latch capable of withstanding severe weather conditions, including high winds and heavy rain. They transitioned to rubber latches, which proved resilient against weather-related damage, effectively handling moisture and temperature variations without deterioration.
An automotive parts manufacturer needed a latch that could minimize noise and vibration inside a vehicle. By adopting rubber latches, they achieved significant noise reduction, as the rubber material dampened the impact when the latch engaged or disengaged.
A marine equipment manufacturer required a latch resistant to saltwater and other corrosive substances. They switched to rubber latches, which offered excellent corrosion resistance, maintaining performance despite exposure to harsh marine environments.
An industrial equipment manufacturer sought a durable and cost-effective latch. Rubber latches proved to be a more economical alternative to metal latches, as the rubber material is less expensive to produce and can be molded into various shapes and sizes, reducing the need for expensive machining and fabrication.
Manufacturers and users of rubber latches are guided by laws, regulations, and agencies that ensure adherence to safety and environmental standards. Oversight of industrial products is crucial for the safety of both rubber latch users and manufacturers. Compliance with these regulations is essential to ensure the safety and effectiveness of rubber latches while minimizing their environmental impact.
The CPSC is an independent federal agency that monitors the safety of consumer products sold in the United States. It has the authority to issue recalls, ban products, and set safety standards for consumer goods, including rubber latches.
OSHA is a federal agency that regulates the use, production, and disposal of chemicals and substances that could impact the environment. This includes overseeing the chemical substances involved in rubber latch production and the disposal of manufacturing waste.
The EPA enforces federal environmental laws and regulations governing the use, production, and disposal of chemicals and substances that could affect the environment. This includes the regulation of chemicals used in rubber latch production and the management of waste products from manufacturing.
The FDA is a federal agency responsible for regulating food, drugs, medical devices, and other products. Rubber latches used in medical devices or food packaging may need to comply with FDA regulations.
The NHTSA oversees motor vehicle safety in the United States. Rubber latches used in automotive applications, such as in car trunks or hoods, may be regulated by NHTSA standards.
The FAA regulates the use of rubber latches in aircraft to ensure they meet specific safety standards.
The TSCA is a federal law that governs the production, importation, and use of chemicals in the United States. Rubber materials used in rubber latches may be subject to TSCA regulations.
The CAA is a federal law that regulates air emissions from industrial sources. Facilities involved in rubber production may be subject to CAA regulations.
The RCRA is a federal law that manages the disposal of hazardous waste. Rubber production facilities may need to comply with RCRA regulations regarding the disposal of rubber waste.
As with any industrial material, rubber latches have their drawbacks, which can be mitigated through proper precautions and adherence to established standards and regulations. The negative aspects of rubber depend on the type of rubber, its application, and the conditions to which it is exposed.
Rubber latches can degrade over time due to environmental factors such as temperature, humidity, and UV exposure. This degradation can lead to a loss of elasticity and potential failure of the latch.
Some rubber latches may not resist certain chemicals, which can weaken or compromise the latch. Choosing a rubber material suited for the specific environmental conditions is crucial.
Rubber latches might not be compatible with the material of the component they are securing. This incompatibility can result in insufficient retention force or damage to the component.
Rubber latches may have restricted temperature ranges within which they operate effectively. Extreme temperatures can cause the rubber to lose elasticity or crack.
Rubber latches may not endure heavy use or abrasion, potentially leading to premature wear or failure.
Rubber latches, like other rubber products, have environmental impacts associated with their production and disposal. Rubber manufacturing can be resource-intensive and may contribute to deforestation and habitat loss, while disposal can result in rubber waste that decomposes slowly.
Considering these negative aspects is essential when choosing a rubber latch for a specific application. While rubber latches offer advantages such as flexibility and durability, these factors can influence their performance and lifespan. Additional considerations include the latch's size and shape, the material it interacts with, and the environmental conditions it will face.
The future of rubber latches looks promising due to several exciting trends. These trends, combined with other factors, suggest an increased use of rubber latches going forward. While the exact trajectory and growth of rubber latches can only be speculated based on current data, technological advances are expected to significantly influence their future designs and applications.
With ongoing technological advancements, the properties and capabilities of rubber latches are expected to improve. Innovations such as 3D printing and additive manufacturing are enabling the production of more complex and customized rubber latch designs. Additionally, new rubber materials are being developed to offer enhanced strength, durability, and flexibility.
Industries such as automotive, aerospace, and medical equipment are anticipated to continue growing, likely leading to higher demand for rubber latches.
As environmental concerns regarding manufacturing and production processes rise, there is an increasing demand for sustainable and eco-friendly products. Rubber latches, which are often recyclable and made from renewable resources, are well-positioned to meet this demand. Furthermore, the development of new sustainable materials and manufacturing processes is expected to enhance the eco-friendliness of rubber latches.
As the versatility and durability of rubber latches become more recognized, their application is expected to expand into new areas and industries. For instance, rubber latches could be used in home appliances like refrigerators and washing machines to provide secure and durable latching solutions. Additionally, the growth of the e-commerce sector is creating opportunities for rubber latches in packaging and shipping applications.
A door latch is a mechanical fastener that connects two surfaces or objects and provides a secure, safe, and strong connection. The latch portion of the mechanism is mounted on a flat surface such that when it meets a...
A gate latch is a locking mechanism that is used to secure gates on fences or stakes on truck beds using a metal bar and lever that is raised to open the latch and lowered to close it. Although they do not have...
Latches are mechanical components that allow the temporary joining of parts that are moving relative to each other. They are actuated to release the coupling and allow the two parts to separate. Latches are mostly seen on doors and enclosure...
A magnetic door latch is a type of latch that consists of a striking pad and a magnet and is used to keep doors and gates closed. Magnetic door latches are also known as magnetic door stops, magnetic door catches, and door magnets...
A rotary latch is a locking mechanism that secures openings such as doors, enclosures, cabinets, and panels so that they are locked and unable to accidentally open. They are referred to as slam latches since...
A spring latch is a mechanical device that is utilized in the joining of two separate components in order to prevent movement or opening. A spring latch is locked with a spring compression so that it will not be released...
A hinge is a movable joint or mechanism that joins two items together. The hinge is one of the most popular categories of mechanical bearings. Butt hinges are a particular kind of hinge that have rectangular pieces that...
A concealed hinge, also known as a hidden or European hinge, is a type of hinge that has parts invisible to the onlooker when the door is closed. They are commonly used in cabinet doors to add an aesthetically pleasing and...
A continuous hinge is an extended single unit hinge that spans the full length of a door, cabinet, lid, or enclosure entrance. They are made of lightweight metals and can be cut to fit the size of any opening...
An eyelet is a metal, rubber, or plastic ring with flanges are used to strengthen or reinforce holes punched in thin fabrics. It is a smaller counterpart of a grommet that is bigger in size and used for more heavy duty materials...
A fastener is a non-permanent or permanent mechanical tool that rigidly connects or affixes two surfaces or objects together. Non-permanent fasteners can easily be removed without damaging the joined materials...
A hinge is a machine element that connects two bodies allowing angular movement about a fixed axis of rotation, all the while preventing translations and rotations on the remaining two axes. A hinge can be...
A friction hinge works by creating a specific tolerance in between the mechanical components. It works based on the principle of torque that can be achieved by applying a desired amount of force. Some other additions to these hinges such as...
A lock is a mechanism designed to connect an opening to its frame using a latch, solid cylinder, bolt, or some other form of a solid metal plunger that extends into the strike. They are metal devices that prevent entry or access for privacy, security, or...
A metal washer is a small flat piece of metal that has a hole in the center and is used as a spacer, a method for absorbing shock, or distributing the load of a fastener. The hole in the middle of a metal washer allows for a bolt or screw to pass through...
A self-drilling screw is a type of tool that has the same design features as a drill bit or cutting tool. As the name implies, self-drilling screws do not require a pilot hole in order to perform as a fastener...
A spring hinge is a self-closing hinge that automatically closes two connected workpieces using the action of a spring that is loaded into the hinge's barrel. They can be found in a wide variety of products such as...
Stainless steel hinges connect two components while allowing them to move in relation to one another. They can have various leafs shaped like rectangles and other forms depending on the type of stainless steel hinge. Stainless steel hinge leafs are...
Molding is a manufacturing process that uses a mold - the latter being a solid container used to give shape to a piece of material. It is a forming process. The form is transferred from the mold to the material by...
Rubber injection molding is when uncured rubber is transformed into a usable product by injecting raw rubber material into a mold cavity made of metal. The applied pressure produces a chemical reaction like...
Rubber latches are latches made of rubber or are composed of rubber components. They are used in the automotive, aerospace, and medical equipment industries due to their flexibility, durability, and non-abrasive properties...
Rubber molding is a process of transforming uncured rubber or an elastomer into a usable product by transferring, compressing, or injecting raw rubber material into a metal mold cavity...
There are several methods to perform rubber overmolding, and each method has its own unique advantages and disadvantages. The choice of method typically depends on the design and material requirements of the product being...
Silicone rubber molding is a method for shaping, forming, and fabricating silicone rubber parts and products using a heated mold. The process involves compressing or injecting silicone rubber into a mold...
A rubber bushing is a form of vibration isolator that is placed between two parts to limit the motion between them and absorb, mollify, and buffer the energy produced by their interaction. They are very...
Extruded rubber is a group of products made by softening and pressurizing an elastomeric compound and forcing it to flow through a hard tool called a die. The resulting product is a continuous piece of material that has the same cross-section throughout its length...
Rubber gaskets are elastic components used for mechanically sealing the microscopic gap between two mating surfaces or joints. Examples of these surfaces are flange faces of piping and fittings, mating surfaces of an...
A rubber O ring is a mechanical gasket in the shape of a torus or donut and is used for static and dynamic applications where there is relative motion between parts and the possibility of friction. Some of the benefits of rubber O rings are...
A rubber roller is a machine part that is composed of an inner round shaft or tube covered by an outer layer of elastomer compounds. The inner shaft is made of steel, aluminum alloys, or other strong and rigid material composites...
Rubber sheets are basically sheets made of rubber or cloth that are coated with rubber to improve the mechanical properties of rubber sheeting such as increased tensile strength and reduced elongation...
Rubber to metal bonding is when a rubber part has to be adhered to a metal part, a metal component is chemically prepared and is attached or encapsulated as part of the process to become a bonded rubber part...
Rubber trim is an extruded, sometimes molded, elastomer that is used to protect the edges or surfaces of objects from sudden impacts. They are usually found on panels, windows, doors, removable covers, and hatches...
Rubber tubing, also known as rubber hose or rubber piping, is made of natural and synthetic rubber and is used to circulate and transport liquids and gases for household and industrial uses. The natural or synthetic rubber materials used for the manufacture of rubber tubing...
Urethane casting is the process of injecting polyurethane and additive resins into a soft mold usually made of silicone elastomer. The casting process is similar to injection molding; injection molding differs by using hard, metal molds...