Electric Actuators
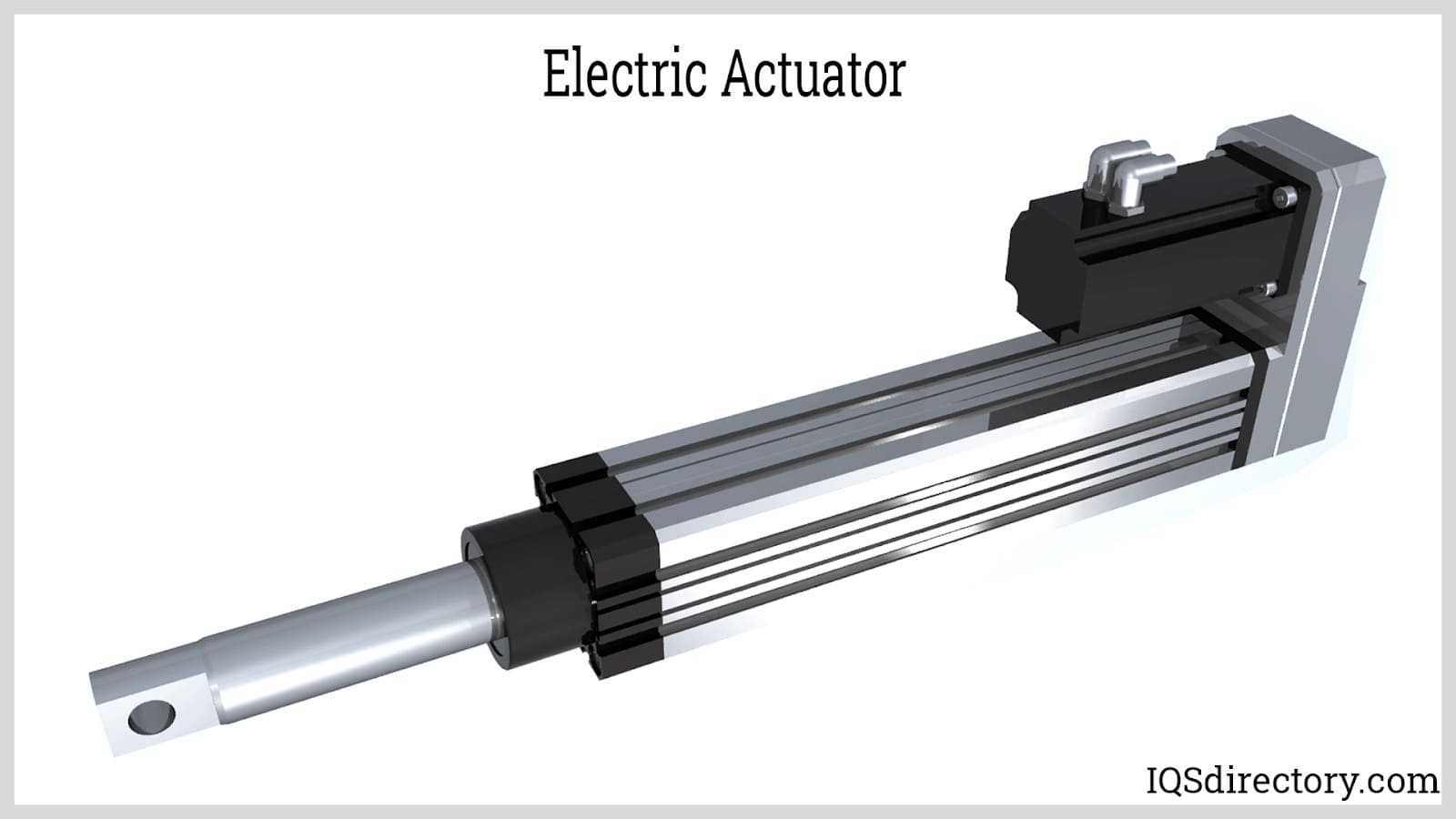
Electric actuators are devices capable of creating motion of a load, or an action that requires a force like clamping, making use of an electric motor to create the force that is necessary...
Please fill out the following form to submit a Request for Quote to any of the following companies listed on
This article will take an in-depth look at 12V linear actuators
The article will bring more detail on topics such as:
In this chapter, we delve into the mechanics and functioning of 12V linear actuators, examining their operation and various uses.
A linear actuator transforms rotational motion into linear movement, enabling the actuation of machinery or materials through pushing, pulling, lifting, lowering, sliding, or tilting actions. These devices provide dependable, low-maintenance motion control that is both eco-friendly and secure. Powered by a 12-volt DC source, 12V linear actuators are characterized by three main types: screw, wheel and handle, and cam. Screw-type actuators achieve movement as the screw mechanism winds and unwinds.
In wheel and handle actuators, motion results from the tension of a belt or chain attached to a shaft. Meanwhile, cam actuators employ an eccentric circle to shift the shaft. The definition of a linear actuator may vary by industry. Often, it is understood as a device engineered to transform rotary force into linear movement, with initial forces derived from motors or hand cranks.
At the heart of a 12V linear actuator lies a compact DC gear motor that applies a screw-drive mechanism and gears to electromechanically manage heavy loads. Due to their robustness, ease of installation, and compact nature, these 12V DC actuators are exceptionally versatile. Each actuator includes two wires (positive and negative), mounting holes at each extremity, and built-in limit switches. With stroke lengths ranging from 1 inch to 24 inches, these actuators can exert force capabilities of 15 lbs, 50 lbs, or 150 lbs. Customization of these actuators in terms of specific sizes, currents, and speeds is common to meet distinct client needs.
Linear actuators move in a straight trajectory, with various methods achieving such motion. They are integral to numerous applications, from facilitating wheelchair access and toys to complex space technology equipment.
A DC motor powers these actuators, typically using a 12V DC voltage. In brush DC actuators, a switch can reverse the motor’s polarity, altering the actuator's motion. Servo and stepper motors necessitate control electronics to electrically manage current direction within the motor. For proper BLDC and servo motor commutation, rotor feedback is crucial, using devices like Hall effect sensors or encoders.
An actuator's control electronics may be integral or externally accessible. The force applied by an actuator is influenced by its speed, with a trade-off between the two: reducing the actuator's speed through a gearbox enhances the force output. Differentiation among actuators can be seen in the screw and shaft length, which determines stroke length.
The actuator's speed is determined by the gears between the motor and the screw. Stroke length is controlled using devices like limit switches, encoders, linear potentiometers, or LVDT sensors. Microswitches at the shaft's ends may control the stroke, responding to the screw’s movement for precise management.
This chapter will cover the key design considerations for linear actuators, as well as the important factors to consider when selecting the right actuator for your needs.
The duty cycle determines how frequently and for how long the actuator will operate. Since power is lost through heat, the duty cycle is determined by the actuator's temperature while it is in motion. By adhering to the duty cycle recommendations, you can prevent motor overheating and component damage in the actuator. There is variance in the duty cycles of actuators because they are not all created equally. Age, loading characteristics, and ambient temperature are all important variables to consider that might affect duty cycle motors.
Even though speed is crucial when choosing an actuator, it's also crucial to take the weight that needs to be moved into account. An actuator will move more slowly when a lot of force is needed to move a weight. An actuator measures speed in terms of distance traveled per second. By calculating the required duty cycle, you can get information that will assist you when choosing the suitable actuator for the job.
12V linear actuators are available in various types and orientations, including:
The primary function of mechanical or electromechanical linear actuators is to convert rotational motion into linear motion. This conversion is achieved through mechanisms such as screws, wheels and handles, or cams, which are commonly used in linear actuators.
Mechanical linear actuators are powered by either AC or DC motors. In screw-type mechanical linear actuators, various screw designs are utilized, such as ball screws or roller screws. The actuator features a rotating screw shaft that moves linearly along its axis. This linear motion is achieved by the rotation of the shaft, which is controlled by a stator assembly.
The wheel and handle type of linear actuator utilizes a belt, chain, rack, or cable connected to the shaft. This variant often employs various guide systems, such as recirculating bearings, cam roller guides, and plain bearings. Due to their long strokes and high operating speeds, these actuators are usually enclosed. In the cam variant, linear motion is generated by an eccentrically shaped wheel that rotates, creating thrust that moves the shaft. This type of linear motion is commonly used in automotive applications.
A servo controller is an integral component of a servo linear actuator, responsible for continuously monitoring the actuator's performance and comparing the desired outcomes with the actual results. If discrepancies are detected, the controller adjusts the actuator to correct them. Servo linear actuators are widely used in automated and remote operations, such as flipping switches or adjusting the position and focus of lenses. They are capable of handling a wide range of tasks, from moving large amounts of material to making precise adjustments of just a fraction of an inch. The operation and performance of a servo linear actuator are directly influenced by the data it receives.
The controller assesses the received data against the expected ideal conditions. This data is sourced from a variety of sensors and equipment. Due to their capabilities, servo linear actuators are employed in advanced automation, robotic control, beam steering, remote-controlled vehicles, marine applications, and aerospace manufacturing. As technology advances in manufacturing, servo linear actuators are becoming increasingly prevalent and essential.
Lead screw linear actuators convert rotary motion from a motor into linear motion. They are designed for strength and efficiency, thanks to their thread profile and rolled thread structure. To ensure smooth operation, the nut of a lead screw actuator should be made from low-friction materials or a lubricated metal.
Lead screw actuators can be used for open-loop control with various motor types, including stepper motors. Additionally, linear actuators powered by brushless DC motors are available in multiple sizes, offering excellent speed efficiency at a cost-effective price.
A threaded rod and a corresponding nut are part of the lead screw actuator's construction. The motor turns either the rod or the nut by mounting them directly, connecting them through gears or a belt, or both. The component that has to be moved is connected to the element that is not a part of the motor.
Electric linear actuators are devices that convert electrical energy into mechanical energy to create linear motion. They are commonly used to operate valves powered by external sources. These actuators typically utilize single-phase or three-phase AC motors, as well as DC motors, for their actuation.
The same fundamental elements are found in the majority of electric linear actuators. In many instances, these parts consist of an electric motor, a screw, a nut, and gears. When the nut rotates along the screw in an electric actuator, it enables the conversion of electrical energy to mechanical energy. Electric rotary actuators spin from open to closure using butterfly, ball, and plug valves.
Like hydraulic linear actuators, pneumatic linear actuators use air pressure to move a piston instead of fluid. In a pneumatic linear actuator, the piston is contained within a cylinder and is designed to form a tight seal against the cylinder walls. As pressurized air enters the cylinder, it forces the piston to move. The amount of force exerted by a pneumatic linear actuator is determined by both the size of the piston and the pressure of the compressed air.
The strength of a pneumatic actuator increases as the pressure on the piston rises. This process is straightforward and efficient, allowing pneumatic linear actuators to operate swiftly. They are well-suited for use with electrical and microprocessor components, as they are not affected by magnetic forces. Pneumatic linear actuators can function effectively in a wide temperature range, from -40°F to 250°F, and are adaptable to environments with significant temperature fluctuations. Additionally, because they do not generate magnetic interference, they pose no explosive or incendiary risks.
Ball screw actuators, also known as drive screws, convert rotary motion into linear mechanical energy using a ball screw and ball nut. This mechanism provides highly accurate and precise linear motion due to the tight manufacturing tolerances and the incompressibility of the ball bearings.
These actuators are known for their durability, capable of lasting up to 5,000 kilometers under moderate loads and speeds, or 3,000 kilometers under high loads and speeds. The speed of a ball screw actuator is controlled by its pitch. The screw lead, which defines the linear travel of the ball nut per screw rotation, is calculated by multiplying the screw pitch by the number of threads.
Ball screw linear actuators with a lower screw lead generate greater linear thrust, while those with a higher screw pitch move the nut more axially and quickly for a given screw RPM. The ball bearings travel in opposing, hardened rod tracks or grooves carved into the axially moving ball nut, which is designed with a specific helix angle. This motion is facilitated by various drive mechanisms, such as belt, direct, or worm gear drives.
Ball screw linear actuators are widely used in the manufacturing of aircraft, missiles, and laboratory and medical equipment. They are commonly found in dialysis machines and blood separation device pumps. These actuators can handle substantial dynamic loads and efficiently convert a motor's torque into linear thrust.
Hydraulic linear actuators share several components with hydraulic motors, including a cylinder, a piston, and an incompressible fluid that applies uneven pressure on the piston. These actuators are ideal for applications requiring substantial force, as they provide significant mechanical power. They are commonly used in lifting mechanisms of machines designed to handle tons of material.
Hydraulic linear actuators are likely to be found in machinery that requires significant lifting or the transport of heavy loads. These actuators derive their power from hydraulic fluid, and their movement can be adjusted by varying the fluid level. Various types of hydraulic oils are available for this purpose. Like other linear actuators, hydraulic linear actuators offer exceptional accuracy and reliability. They are also versatile and adaptable, allowing them to function like an arm to push and pull machine components.
This chapter will explore the applications and advantages of linear actuators, including 12V linear actuators.
The following applications are ideal for 12V linear actuators:
Linear actuators have a variety of applications, including:
The many applications for a linear actuator have increased workplace automation. It reduces production costs while streamlining manufacturing. For the best material handling, electric linear actuators have evolved into a crucial and essential instrument. Loads are moved from point A to point B via linear actuators. The capacity to halt the action mid-stroke is an additional feature of the electromechanical version. Industrial, high-speed, and micro models are a few of the other kinds of actuators used in material handling.
In order to lift, lower, slide, or tilt machines or materials, a linear actuator converts rotational motion into push or pull linear motion. They provide clean, safe, and effective motion control that doesn't require any maintenance. 12 Volt DC voltage sources are used to power 12 Volt linear actuators. The three different varieties of linear actuators are the screw, wheel and handle, and cam. The kind of screw is determined by the upward and downward motion of the screw winding and unwinding. Benefits, design considerations and applications need to be understood when choosing 12V linear actuators.
Electric actuators are devices capable of creating motion of a load, or an action that requires a force like clamping, making use of an electric motor to create the force that is necessary...
A linear actuator is a means for converting rotational motion into push or pull linear motion, which can be used for lifting, dropping, sliding, or tilting of machines or materials. They provide safe and clean...
High-precision, linear motion goods are essential components at the core of several items which are generally used in machine tools and equipment for manufacturing semiconductors. These items are utilized...
A linear actuator actuates, moves, in a linear, straight, line to complete or start a process. There are a variety of terms used to describe a linear actuator such as ram, piston, or activator. They are very common in...
Ball screws are mechanical linear actuators that consist of a screw shaft and a nut that contain a ball that rolls between their matching helical grooves. The primary function of ball screws is to convert rotational motion to linear motion. Ball nuts are used in...
A lead screw is a kind of mechanical linear actuator that converts rotational motion into linear motion. Its operation relies on the sliding of the screw shaft and the nut threads with no ball bearings between them. The screw shaft and the nut are directly moving against each other on...
Linear bearings are a type of bearing that "bear" or support the load of the carriage during its single-axis linear movement and provide a low friction sliding surface for the guide rails. In a linear guide, the carriage is the component that travels in a straight line, back and forth, along the length of the guide rail...
Linear Rails are ideal for moving items through a production process with great precision and as little friction as possible if creating, packing, and distributing products. Linear Rail is a type of gadget that...
Linear slides, also referred to as linear guides or linear-motion bearings, are types of bearings that allow smooth and near-frictionless motion in a single axis. Machine tools, robots, actuators, sensors, and other...
A roller table is a small, stiff, limited linear guide device with an integrated cross-roller guide. Electrical or mechanical drive systems are frequently used to move a roller table, making it easy to transfer heavy loads...