Linear Rails
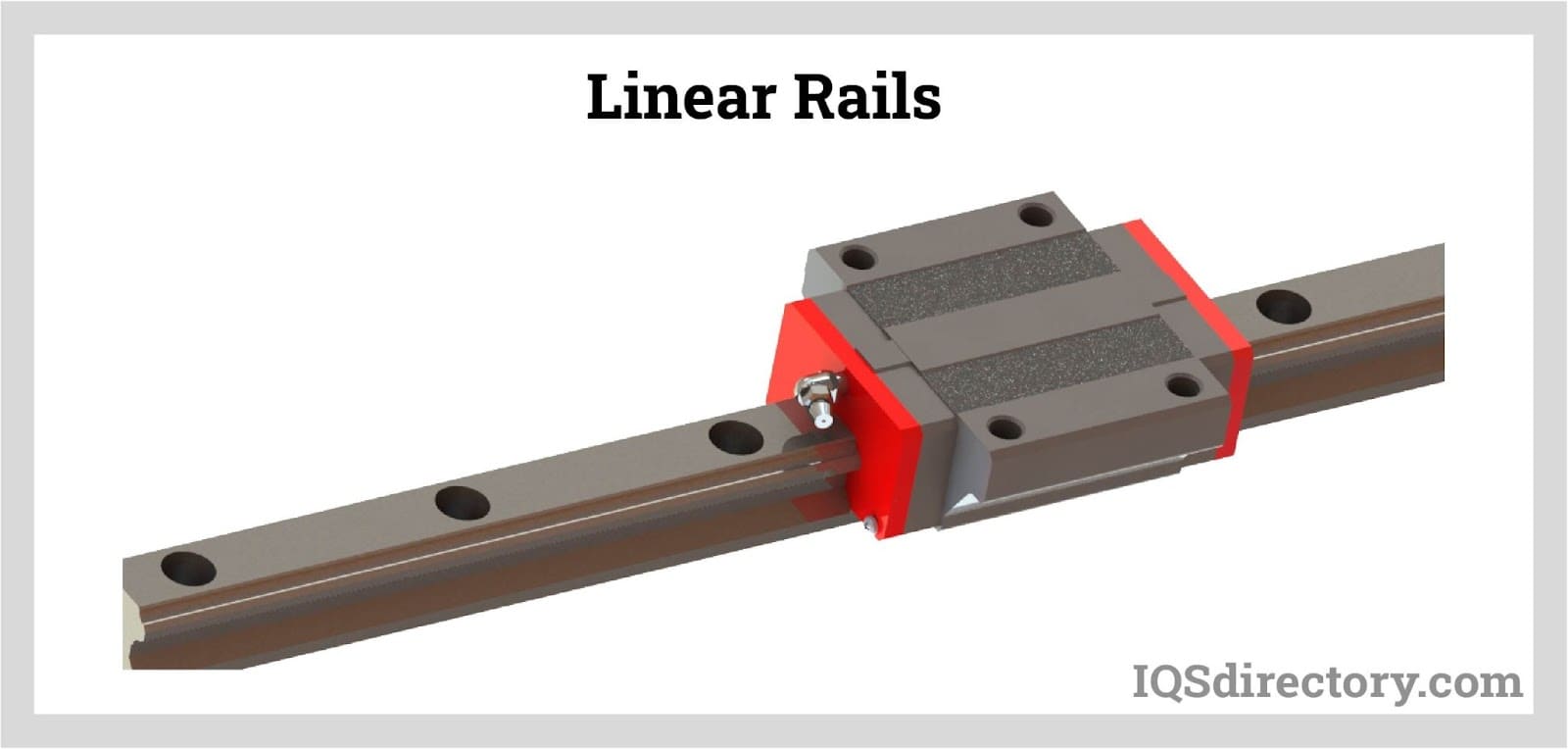
Linear Rails are ideal for moving items through a production process with great precision and as little friction as possible if creating, packing, and distributing products. Linear Rail is a type of gadget that...
Please fill out the following form to submit a Request for Quote to any of the following companies listed on
This guide provides in-depth insights into linear slides. Read further to learn more about:
Linear slides, frequently referred to as linear motion slides or linear motion guides, are crucial components in mechanical engineering designed to enable accurate and controlled straight-line movement within various industrial and mechanical systems. These devices form the core for achieving seamless and consistent movement of tools or objects along a predetermined path. Machines such as tools, robotic systems, actuators, sensors, and other mechanical apparatuses often need to move components linearly along any of the three-dimensional axes. When two surfaces are in contact, free translational motion is resisted by friction, which is the force opposing the motion of two interacting surfaces. The magnitude of this frictional force is influenced by the load applied on the contacting surfaces and the coefficient of friction—an intrinsic property of the surfaces themselves.
To ensure minimal energy consumption, prolonged tool life, and lower heat output, having low friction and high precision are crucial attributes. A linear slide is one component within linear motion systems, which also encompass power screws, actuated cylinders, linear motors, and rack and pinion setups. The primary function of linear slides is to guide motion, whereas other components focus on the transmission of power.
The main component of linear slides, also known as linear motion guides, is the bearing assembly. Bearings are fundamental to any linear motion system, as they enable smooth, controlled, and repeatable movement along a straight path. Depending on the specific application requirements, linear slides can utilize a variety of bearing types, including rolling-element bearings, plain surface bearings, and magnetic bearings. Understanding the mechanisms behind these bearings is crucial for selecting the ideal linear slide for industrial automation, CNC machinery, robotics, material handling, and precision engineering applications.
A rolling-element bearing reduces friction by using balls or rollers to minimize the surface area of contact between moving parts. The surfaces on which these rolling elements travel are known as races, forming the core paths for linear motion. Rolling-element bearings come in two primary configurations: ball bearings and roller bearings. Ball bearings reduce contact to a small point, enabling exceptionally smooth travel with low friction. While, in theory, the point of contact could become infinitesimally small, material deformation under load creates a finite contact patch. This design limits their load capacity, making ball bearings most suitable for applications prioritizing high-speed travel and precision over heavy load support. To boost load-carrying capacity, manufacturers can incorporate more rows of bearing balls and races, a design feature common in heavy-duty linear guides and industrial slide rails.
Roller bearings are rolling elements engineered to support greater loads and further reduce friction in linear slides. Unlike ball bearings, which create a point contact, rollers establish a line of contact with the raceways. This extended rectangular contact provides a much larger load-bearing area and enables the linear slide to handle higher radial and axial loads with lower surface pressure, enhancing both durability and life cycle. Roller bearing linear guides are frequently specified in CNC machining centers, high-precision cutting equipment, and automated assembly lines, where accuracy, repeatability, and high load capacity are essential.
Plain surface bearings—also known as plain bearings, sleeve bearings, or bushings—use low-friction sliding contact between surfaces instead of rolling elements. These bearings typically feature self-lubricating composites or special surface treatments that deliver a low coefficient of friction, extending the slide’s operating life and reducing maintenance needs. Materials such as PTFE (Polytetrafluoroethylene), graphite, and advanced polymers are commonly used, often with metal backing for improved heat dissipation. Applications that require dry lubrication benefit from these designs, which prevent metal-to-metal contact. As PTFE or graphite layers wear, they form a lubricating film. For plastic-based linear bearings, advantages include corrosion resistance and lightweight properties, though their thermal conductivity is lower.
Some plain surface bearings employ fluids such as lubricating oils, greases, or even pressurized air to sustain linear movement with minimal friction. Hydrostatic lubrication refers to the use of pressurized liquid lubricants, while aerostatic lubrication uses compressed air or gas. In advanced linear guide systems, hydrostatic bearings provide nearly frictionless motion ideal for coordinate measuring machines, optical instruments, and ultra-precise production equipment. Aerostatic linear slides, preferred for their cleanliness and non-contaminating properties, are widely used in semiconductor manufacturing and clean room automation. The drawback of these fluid-film and air bearing systems is the increased cost and complexity associated with pumps and auxiliary equipment.
Magnetic bearings, which operate via electromagnetic forces, are an innovative technology for linear drive systems requiring ultra-low friction and maintenance-free operation. By magnetically levitating the moving component, these bearings eliminate mechanical contact altogether, thus reducing wear and enabling high-speed, high-precision positioning. Magnetic linear slides are commonly applied in medical devices, high-speed transport systems, and highly sensitive laboratory automation, thanks to their ability to support substantial loads and achieve non-contact motion. However, engineers must consider EMI (electromagnetic interference) and higher energy consumption when integrating these systems.
How to Choose the Right Linear Slide for Your Application
Selecting the optimal linear slide depends on several user-driven factors, including load capacity, travel length, required accuracy, installation environment, and service life. Key considerations include the type of bearing (e.g., ball, roller, plain), required maintenance schedule, protection against contaminants, alignment tolerance, and compatibility with automation systems. Assess whether your process benefits more from high speed and smooth motion (ball bearings), high load support (roller bearings), minimal maintenance (plain or dry-lube bearings), or specialized environments (air, hydrostatic, or maglev slides). For assistance in sourcing high-quality linear slides, linear motion guides, and linear actuator systems, consult reputable linear slide manufacturers and suppliers that offer technical support and customization options for your specific industry or project.
This section explores the fundamental elements of linear slide systems, a critical component in automation, precision engineering, and industrial machinery. Understanding the structure and function of each linear slide component enables users to select, maintain, and optimize these devices for a variety of linear motion applications. From slide mechanisms to advanced actuation parts and positional regulation features, linear slides come in diverse designs tailored to specific use cases. Depending on the application requirements and the manufacturer, additional specialized parts—such as air bearings, precision positioners, or integrated feedback systems—may also be included for enhanced performance and accuracy.
The most commonly used classification among the three is rolling element bearings. Compared to lubricated and magnetic bearings, rolling element designs—such as those in ball bearing slides—are more robust and highly versatile. They perform effectively under both dynamic and static loads and boast predictable service life due to well-established industry standards and lifecycle engineering. By contrast, hydrostatic and magnetic bearings are reserved primarily for specialized applications in research labs and niche precision instruments, where their unique properties outweigh their higher complexity and cost.
Rolling element bearings in linear slides are further classified by the method of rolling element recirculation. Non-recirculating designs restrict the travel distance to the length of the rolling element row; the rolling elements rotate within the carriage but do not travel with it, covering only half the overall stroke range. Conversely, recirculating ball bearings feature a return path engineered into the carriage or linear motion guide block, allowing the balls to circulate continuously along the looped pathway with the carriage. This results in virtually unlimited stroke lengths, making recirculating ball bearing slides ideal for applications demanding extended linear travel and smooth, consistent movement along the guide rail—such as automated assembly lines and conveyor systems.
Carriage: The carriage, or slide block, is the primary load-carrying component guided by the linear bearings. It supports the tooling, sensors, workpieces, or subassemblies requiring controlled linear positioning. While most carriages facilitate movement within the X-Y plane, advanced systems can achieve multi-axis motion—including Z-axis translation—using power screws, lead screws, or precision rack and pinion drives. A drive unit is typically integrated or coupled to the carriage to generate adequate force and optimize the mechanical efficiency required for reliable operation.
Guide Rail: Guide rails, or linear guideways, serve as the fixed reference surfaces for both plain and rolling element bearings. For plain surface bearings, guide rails typically comprise highly polished or coated flat surfaces—or, for shaft-style slides, cylindrical rails. In rolling element systems, the race profiles are engineered to optimize area contact and load transmission while controlling deformation and wear. Linear guide rails in precision motion systems are frequently classified by their race geometries, with circular arch and gothic arch profiles being most common for ball bearings.
Circular and gothic arch raceways both contain two tracks for ball bearings. In circular arches, each ball only contacts the rail at two points, offering low friction and predictable motion. Gothic arches, on the other hand, feature four-point contact, accommodating greater load capacity and improved moment resistance. However, the increased contact leads to differential slip—an effect caused by varying rolling diameters—resulting in sliding friction and potential wear, especially at higher speeds. Because of this, circular arches are generally favored for applications prioritizing repeatability and minimal wear, while gothic arch profiles are reserved for compact linear guides with higher load demands.
The construction of roller guides includes linear rails fitted with precisely machined rollers, a moving slide element (block or runner), and a durable mounting bracket. Common raw materials for roller guides include aluminum alloys or cast iron, which provide the necessary rigidity and load-carrying capability. Stainless steel construction is employed in corrosive or washdown environments, further enhancing service life and reliability for precision linear motion applications. The required rail spacing is determined by load and application conditions; as the weight increases, the rails must be spaced appropriately to maintain system rigidity and accuracy.
Roller guide technology eliminates much of the lubrication required in traditional sliding linear motion products, reducing maintenance and operational downtime. Consistent rolling contact supports high-speed operation and exceptional repeatability in factory automation, electronics manufacturing, and other demanding industries.
End Cap: The end cap, or linear slide cover, acts as a critical protective element at the ends of the assembly. Its primary function is to seal the linear motion system against external contaminants (such as dust, metal chips, and moisture), thus protecting bearings, rails, and moving parts from premature wear or failure. High-quality end caps help prolong the operational lifespan and reliability of linear slide systems in challenging industrial environments.
Bellows and Covers: For linear guideways operating in especially harsh or dusty industrial settings, bellows and protective covers provide an essential layer of defense. These accordion-style or rigid enclosures prevent intrusion of debris, cutting fluids, or corrosive agents, all while allowing full linear movement. By preserving the cleanliness and integrity of bearings and guides, bellows and covers help maintain consistent positioning accuracy and ensure system longevity.
When choosing or evaluating a linear slide for your industrial automation, robotics, machine tool, or precision positioning application, consider factors such as load rating, environmental conditions, expected service life, accuracy, and ease of maintenance. A well-configured linear slide assembly—with optimized bearings, robust guide rails, integrated drive units, and advanced feedback sensors—ensures reliable performance, high throughput, and minimized downtime in even the most demanding environments.
For more information on sizing, selection criteria, or custom linear slide system integration, consult a trusted motion control specialist or review industry standards for best practices.
There are numerous combinations of bearings, including recirculating and non-recirculating designs, contact types, raceway profiles, drive mechanisms, and precision controls, each tailored to specific applications. Certain combinations are particularly notable for their simplicity, load capacity, rigidity, or versatility. These are constantly being developed to match their intended purposes. Listed below are some of the commonly used linear slides in the market.
Dovetail Slides: These are linear slides that employ plain surface bearings that rely on a low coefficient of friction and lubrication. Their names originate from dovetail-shaped protrusions that fit into identical negative geometry. The protrusion is usually on the stationary rail or base while the negative is constructed into the carriage. This configuration is sometimes referred to as a dovetail table. Dovetail slides are robust and can withstand both radial and lateral loads. These are typically used for large machine tools such as lathes, shapers, and milling machines.
Boxway Slides: Like the dovetail slides, boxway slides are plain surface bearings. But instead of a dovetail-shaped protrusion, these have a square gib with flanges at the top forming a T shape. They can handle heavier loads than dovetail slides due to the larger projected surface area in contact between the carriage and the rail.
Sleeve Bearing Slides: This type uses cylindrical surfaces instead of mating tongue and groove geometry. These surfaces are called bushings and journals. The bushing is like a hollow cylinder constructed into the carriage, while the journal is a long shaft that acts as the guide rail mounted on the base. Advantages of using sleeve bearing slides are its simple construction and its ability to handle loads applied in any direction. However, they are not as strong as dovetail and boxway slides and can only be used for light to medium load applications.
The bushings can also be classified according to their form, which can be closed or open. Closed bushings have a shaft that is supported only at the ends, while open bushings allow shaft supports directly underneath. Having support underneath the shaft eliminates deflection from carrying high loads.
Linear Ball Slides: This is one of the most common types of rolling element slides. Linear ball slides are similar to linear ball bushings, but a runner block is used instead of bushings. The runner block can also be constructed with a return path for recirculation. Linear ball slides are better than linear bushings since they offer better versatility and load capacity. Since the races sit directly on the base, there is guide rail deflection. Also, several design variations are available for the race profiles that can favor either load capacity or compactness.
Crossed Roller Slides: As the name suggests, this type utilizes rollers that are oriented at 45° and 135° relative to the horizontal. The rollers can be arranged into a single row with 90° alternating orientations, or into multiple rows where each row is oriented perpendicular relative to the other rows. This type has better load capacity than similarly sized ball slides due to the larger contact area inherent to roller bearings.
Ball Screw: This is a special type of linear slide that combines ball bearings with power screws. A typical power screw drive has an Acme profile that engages the nut integrated into the carriage through sliding contact. A ball screw further lowers friction by introducing balls as rolling element bearings. The nut is constructed to have a return path for recirculation.
A linear slide serves to guide the movement of a machine tool or instrument but does not provide the force needed for this motion. Instead, a drive unit, which can be mechanical or electromagnetic, supplies the necessary force. Basic linear slides often rely on manual actuation, which can be accomplished through methods like pushing, pulling, or using devices such as a hand crank leadscrew. The following are various types of powered drive units commonly used with linear slides.
Belt Drive: In this type, the carriage is attached to both ends of a toothed belt. A toothed or timing belt is used instead of a flat or V-belt to prevent slippage. This toothed belt is wrapped around two pulleys located at the ends of the guide rails. One pulley is connected to a motor known as the drive end, while the other pulley is only for providing tension known as the tail end.
Pneumatic Systems: Pneumatic systems are piston and cylinder assemblies where compressed air is supplied on one or both ends. Introducing compressed air causes increased pressure inside the cylinder, moving the piston. A rod is attached to one side of the piston and is extended or retracted according to the piston‘s action. A pneumatic cylinder can be classified as single-acting or double-acting. A single-acting cylinder has only one inlet port. One stroke is pneumatically powered, while the return stroke is caused by other countering forces, such as spring force. In a double-acting cylinder, there is one inlet port at both ends of the cylinder. This makes the return stroke pneumatically powered also. The simplest pneumatic actuators have the tool or part of the carriage attached to the end of the rod. However, this requires an overall length twice that of the stroke. The rod is then replaced with other modes of coupling such as cables, bands, and magnets. Pneumatic systems have high operating speeds. Also, since there are no mounted electrical components, they are suited for explosion-proof devices. However, unlike the other types, the carriage cannot stop at an intermediate position. The travel is only from end-to-end positions.
While the previous chapter focused on machines responsible for carriage actuation, it’s equally important to consider the devices that monitor these movements. Actuation can be either manually controlled by an operator or automated. To facilitate this, sensors are required to provide feedback signals that the controller uses to activate, deactivate, or adjust the force generated by the drive units. The following are some common sensors employed in linear slide systems.
Linear slides offer numerous benefits across various applications, such as in manufacturing, automation, and precision machinery. Below are some of the primary advantages and benefits associated with using linear slides:
Linear Rails are ideal for moving items through a production process with great precision and as little friction as possible if creating, packing, and distributing products. Linear Rail is a type of gadget that...
A roller table is a small, stiff, limited linear guide device with an integrated cross-roller guide. Electrical or mechanical drive systems are frequently used to move a roller table, making it easy to transfer heavy loads...
A linear actuator is a device that transforms rotational motion into push or pull linear motion, which can then be used to lift, lower, slide, or tilt machinery or materials. They offer effective, maintenance-free motion control...
Ball screws are mechanical linear actuators that consist of a screw shaft and a nut that contain a ball that rolls between their matching helical grooves. The primary function of ball screws is to convert rotational motion to linear motion. Ball nuts are used in...
Electric actuators are devices capable of creating motion of a load, or an action that requires a force like clamping, making use of an electric motor to create the force that is necessary...
A lead screw is a kind of mechanical linear actuator that converts rotational motion into linear motion. Its operation relies on the sliding of the screw shaft and the nut threads with no ball bearings between them. The screw shaft and the nut are directly moving against each other on...
A linear actuator is a means for converting rotational motion into push or pull linear motion, which can be used for lifting, dropping, sliding, or tilting of machines or materials. They provide safe and clean...
Linear bearings are a type of bearing that "bear" or support the load of the carriage during its single-axis linear movement and provide a low friction sliding surface for the guide rails. In a linear guide, the carriage is the component that travels in a straight line, back and forth, along the length of the guide rail...
High-precision, linear motion goods are essential components at the core of several items which are generally used in machine tools and equipment for manufacturing semiconductors. These items are utilized...
A linear actuator actuates, moves, in a linear, straight, line to complete or start a process. There are a variety of terms used to describe a linear actuator such as ram, piston, or activator. They are very common in...