Strain Gauges
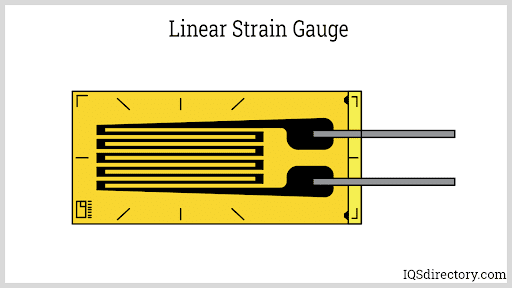
A strain gauge, or strain gage, is a sensing device used for measuring strain experienced by an object. It is made from a long, thin piece of conductor bonded to an elastic backing material called a carrier...
Please fill out the following form to submit a Request for Quote to any of the following companies listed on
This article will take an in-depth look at force sensors.
The article will bring more detail on topics such as:
In this chapter, we will delve into the mechanics of force sensors, discussing their functionality and essential considerations when selecting them for your needs.
Force sensors are instruments that transform various mechanical forces—such as weight, tension, compression, torque, strain, stress, or pressure—into electrical signals. These signals quantify the force's magnitude and can inform operators or function as inputs for machinery and process controls. They often transmit data to indicators, controllers, or computer systems.
While technically different from force transducers, the terms are usually used interchangeably. Force sensors are increasingly critical in power equipment, engineering machinery, various operating machines, and industrial automation. They vary in size, capable of measuring forces from mere grams to several tons.
Applications for force sensors cover a diverse range, from bathroom scales and musical instruments to medical devices, automotive seat occupancy detection, and industry-specific process controls. We'll discuss different force sensor types and elucidate their working principles.
Force sensors function by detecting an applied force and converting it into a quantifiable measurement. Various force sensor types exist, each with unique sensing mechanisms. For instance, some materials like force-sensing resistors alter their resistance when force is applied.
Typically, force sensors comprise electrodes and a sensing material. They determine the applied force by sensing changes in the resistance values of force-sensing resistors, the cornerstone of most force sensor designs.
Force-sensing resistors utilize contact resistance principles. In these resistors, a conductive polymer sheet changes its resistance when force is exerted. This sheet contains a matrix of tiny, electrically conductive, and non-conductive particles.
Applying force to the film's surface causes microscopic particles to make contact with the sensor electrodes, altering the film's resistance. This resistance change indicates the applied force's magnitude, where the mechanical pressure modifies the electrical resistance, providing measurable data.
Force sensors vary in design and applicability. Chapter three will detail the different types of force sensors. Meanwhile, in this section, we highlight critical factors to consider when selecting a sensor, aiding in informed decisions after evaluating your options.
The cost is a vital consideration when choosing a sensor. Depending on the application, expensive sensors could affect the project's financial viability.
It's important to consider if the variable being measured can repeatedly produce the same results under consistent conditions. Repeatability gauges a sensor’s capability to consistently deliver identical results, even if not perfectly accurate, under unchanged settings.
Accuracy and precision are significant specifications. Although sometimes interchanged in sensor advertising, they denote different things. Grasping the variance between them is crucial for deciding which is more pertinent to your needs.
Choose a force sensor based on its operational environment. Factors like temperature and humidity can influence sensor performance in industrial, agricultural, medical, or automotive contexts, potentially affecting accuracy.
Temperature fluctuations can drastically affect sensor outputs, though some sensors are built to withstand such variations. Choosing a resilient sensor is key to dependable performance in its destined environment.
A sensor's durability is crucial. Assess its robustness, lifespan, and resilience to harsh conditions. Every sensor has a limited life span, often defined by its performance over time or during storage.
Factors such as design, materials, manufacturing process, and environmental influences affect sensor longevity. Ensuring sensors are durable helps maintain cost-efficiency and suitability, reducing accuracy drift under disadvantageous conditions.
Choosing a force sensor with an appropriate response time is critical. Rapidly shifting forces require a sensor with a quick response time, whereas steady or slow forces might be sufficiently measured with slower response times.
Comprehending your project's specific needs is vital when selecting a force sensor. Open load sensors are some of the most precise available and can be customized for diverse applications.
The force-sensing technology selection will highly depend on the size and shape the product requires.
This chapter explores in depth the construction, advanced engineering design, and production processes behind force sensors, which are vital components in modern industrial automation, robotics, medical devices, automotive systems, and precision manufacturing. Understanding force sensor manufacturing is key for selecting the ideal product for specific load measurement, material testing, or process control applications.
Force sensors, also known as load cells, tension sensors, or pressure transducers, are produced in a variety of sizes and geometries to suit distinct measurement environments and application requirements. Every force sensor is built around three main elements: the sensing element, the conversion element, and the output circuit. The sensing element, typically engineered from durable materials such as aluminum alloy, alloy steel, or stainless steel, translates applied mechanical force into a measurable strain or electrical signal. Selection of the sensing material is critical, as it impacts sensor accuracy, corrosion resistance, and environmental suitability.
The conversion element most often consists of a high-precision strain gauge or a piezoelectric crystal. Strain gauges, frequently made from conductive foil, are bonded to the sensing element and form the heart of resistive force measurement. Alternatively, piezoelectric force sensors exploit the charge generated when a crystal, such as quartz, is mechanically deformed, offering high dynamic response for measuring variable or impulsive forces.
Last but not least, the circuit section is typically formed from enameled wire or advanced PCB layouts. Sensitive strain gauge arrays are linked in circuit configurations, most notably the Wheatstone bridge, to achieve exceptional accuracy and linearity in force measurement. More intricate force sensors may contain up to thirty gauges, exponentially improving signal fidelity, minimizing measurement error, and supporting multi-axis or high-capacity measurement needs.
Force sensors deliver outputs in several standardized formats to suit differing automation and data acquisition system requirements. These output types include raw analog voltage, analog current (such as 4-20 mA for industrial PLC integration), analog frequency, discrete switches or alarms for threshold detection, and both serial and parallel data for digital monitoring systems. Sensor choice depends on factors like required measurement range, sensitivity, linearity, operating environment, and desired output compatibility with signal conditioning electronics and controllers.
To achieve highly precise, repeatable, and stable readings, sensor circuits typically rely on core electrical laws, especially the Wheatstone bridge equation, which balances potential differences and compensates for thermal drift or parasitic resistance changes. Load cell calibration, temperature compensation, and electromagnetic shielding are additional design considerations to maximize reliability and longevity in real-world conditions.
The Wheatstone bridge is a foundational circuit for force and pressure sensor signal processing. With its diamond-shaped configuration and balanced resistors, it precisely measures unknown resistance values, which correlate directly with minute physical deformations in the sensor's strain gauge grid. This circuit is fundamental in converting mechanical load or pressure into highly accurate and linear electrical signals.
With the aid of modern operational amplifiers and digital filtering, Wheatstone bridge circuits are now seamlessly integrated with advanced sensors, including piezoelectric sensors, MEMS-based force sensors, and multi-axis load cells. These setups offer fast, noise-resistant measurement of even extremely small force variations, crucial for research laboratories, industrial weighing systems, robotics, and medical instrumentation.
The Wheatstone bridge design includes:
By precisely calibrating the bridge and using temperature-compensated resistors, force sensors maintain high accuracy in challenging industrial measurement environments, from material testing labs to automated production lines.
Commercial advancements in micro-electromechanical systems (MEMS) technology have revolutionized force sensor miniaturization, durability, and cost-efficiency, especially in consumer electronics, biomedical sensors, and automotive safety devices. MEMS fabrication leverages silicon micromachining and thin-film deposition to produce compact, high-precision sensor arrays.
The process begins with deposition of silicon nitride on a silicon-insulator wafer, followed by precise front-side etching to define the sensor's thin diaphragms. Photolithography and reactive-ion etching carefully pattern nitride to isolate the sensitive membrane area, enhancing mechanical performance and repeatability. Silicon oxide deposition protects the underlying semiconductive substrate, while the remaining nitride is etched on the back side to shape square diaphragm regions for accurate pressure-sensing response.
Anisotropic silicon etching with potassium hydroxide (KOH) creates the suspended structures necessary for force and pressure sensing. These cavities are micro-engineered and sealed with Pyrex wafers, ensuring sensor stability in demanding environments such as medical equipment or automotive control units. Further microchannel and electrode patterning is achieved with hydrofluoric acid and chromium-gold masks, providing precision electrical connectivity for signal processing.
State-of-the-art MEMS manufacturing incorporates techniques such as anodic bonding for hermetic sealing and deposition of thin metal layers (for resistors) via thermal evaporation. Protective coatings like Parylene are applied to ensure waterproofing, chemical resistance, and long-term electrical insulation. The wafers are diced using high-precision die saws to isolate individual sensor cells, which are then packaged, tested, and calibrated for end-use reliability and integration in digital force measurement systems.
For both piezoresistive and strain-gauge MEMS sensors, the Wheatstone bridge circuit provides unsurpassed performance in the detection of minute resistance changes. This allows for the precise measurement and control required in critical force sensing applications, including medical devices, industrial automation, robotics, and aerospace systems.
As force sensor technology evolves, manufacturers increasingly integrate advanced features such as temperature compensation, overload protection, self-diagnostics, and digital signal conversion to meet the demands of Industry 4.0 environments. When evaluating force sensor vendors or placing orders for specialized applications, it is essential to consider these manufacturing and design choices for optimal performance, precision, and cost-effectiveness.
Force sensors are critical components in modern industrial automation, manufacturing, robotics, automotive engineering, and medical devices. Generally, there are four main types of force sensor technologies, each classified by the underlying behavior of their sensing elements. These dominant sensing methods—capacitive, inductive, piezoelectric, and piezoresistive—deliver high accuracy and reliability in a diverse range of applications and environmental conditions. Additional emerging force sensor types, such as optical and magnetoresistive, further enrich the field by meeting increasingly specific measurement needs.
An inductive force sensor operates on the principle of electromagnetic induction to detect or measure metallic objects and applied mechanical forces. When the magnetic field around an inductor changes (for example, due to the proximity of a metal target or a mechanical displacement), a current is induced in the circuit containing the inductor. Unlike techniques based solely on load cells, inductive sensors offer contactless measurement, contributing to longer service life and minimal drift.
This effect enables the detection of metallic objects interacting with a magnetic field, making inductive force sensors ideal for environments exposed to moisture, dust, oil, and non-conductive contaminants, since non-metallic substances such as liquids, plastics, or airborne particles do not interfere with the magnetic field. Various sensor designs utilize self-inductance, mutual inductance, or Eddy current generation to translate mechanical deformation or displacement into a precise electrical output, enabling accurate force measurement. These features make inductive sensors highly applicable in automotive assembly, materials testing, and structural monitoring.
Inductive force sensors excel at low-force detection and displacement measurement. Recent advancements, such as bi-directional inductive force sensors, enable both amplitude and vector direction measurement of applied forces within a single plane—critical for precise automation and robotic feedback systems. In such sensors, Eddy currents induced in a conductor surface by the alternating current (AC) magnetic field of an LC circuit create a back-emf that counteracts the primary magnetic field, reducing sensor inductance. Changes in this inductance directly correspond to mechanical deformation or displacement, forming the basis for quantitatively accurate force sensing.
A high-frequency oscillator within the sensor generates a robust electromagnetic field at the sensing face. When a conductive metal object enters this field, Eddy currents are induced in the metal, thus altering the amplitude of the field oscillations. This amplitude change produces a measurable voltage variation at the oscillator output, which in turn triggers the sensor output state. High-frequency oscillating sensors are widely used in automation, conveyor systems, and precision metalworking—industries where high-speed and non-contact force or proximity sensing is critical for maintaining efficiency and product quality.
Magnetic inductive sensors, including magnetic proximity switches and reed sensors, are activated by a permanent magnet and function based on reed contacts—thin, magnetically responsive plates enclosed within a hermetic glass bulb filled with inert gas. When exposed to a magnetic field, these contacts close, forming an electrical connection. The precision surface treatment of contact plates ensures optimal performance in both low-current and high-inductive circuit environments.
Key advantages of magnetic force sensors over mechanical switches include immunity to dust, oxidation, and corrosion, due to the hermetic seal, and longer operational lifetimes resulting from contactless actuation. These sensors are widely used in position sensing, door interlocks, and industrial safety applications, where reliability and resilience in harsh environments are crucial performance criteria.
Capacitive force sensors function by measuring the change in electrical capacitance between two conductive plates separated by a dielectric material. Any applied force, pressure, or displacement alters the physical gap between these plates, resulting in a corresponding change in capacitance. This method delivers high sensitivity and linearity, making capacitive sensors ideal for detecting small mechanical displacements, vibrations, and pressures in both static and dynamic conditions. They are commonly integrated into robotics, semiconductor manufacturing, material thickness gauging, level sensing, touch screen interfaces, and medical diagnostics.
Analog capacitive sensors deliver continuous, analog output proportional to the detected force or displacement. Compared to digital or basic capacitive proximity sensors, they excel in applications demanding high-resolution monitoring—such as process control, fluid-level sensing, non-contact thickness measurement, and materials analysis. Their flexibility supports integration into automated manufacturing, laboratory research, and real-time quality assurance systems.
Miniature, or micro-capacitive force sensors, are engineered to fit within extremely confined environments while maintaining precise force or pressure detection capabilities. These compact sensors are vital for OEM equipment, portable medical devices, and applications where high density and spatial efficiency are required. Often, external amplification circuits are used to boost sensitivity, and adjustable potentiometers allow users to fine-tune signal amplification and sensor response according to the target application. Miniature capacitive sensors are critical for industrial machinery monitoring, laboratory automation, and fine process control.
Designed for demanding environments, high-temperature capacitive sensors maintain performance under extreme thermal conditions. These are frequently used in process industries, chemical plants, and energy sector applications where temperature fluctuations or direct exposure to heated materials would defeat conventional sensors. Their specialized construction ensures accurate measurement of force, pressure, and material levels in ovens, kilns, foundries, and engine monitoring systems.
A piezoelectric force sensor relies on the piezoelectric effect: the ability of certain crystalline materials (such as quartz, PZT, or tourmaline) to generate an electrical charge in response to applied mechanical stress. When a force, pressure, or vibration acts upon the piezoelectric element, an output voltage proportional to the stress is produced. Piezoelectric sensors are highly valued for their fast dynamic response, high-frequency bandwidth, and wide operating temperature range, making them ideal for dynamic load monitoring, vibration analysis, acoustic emission testing, and impact detection across automotive crash studies, structural health monitoring, and industrial process control.
Piezoresistive force sensors function through changes in their electrical resistance in response to externally applied force, pressure, or strain. These sensors utilize a strain gauge—either bonded onto or integrated within the sensor substrate—to translate mechanical deformation into an electrical signal. As force is exerted, the resistive element changes shape, causing a measurable alteration in resistance. This allows precise monitoring of static and dynamic loads, pressure, and strain. Piezoresistive sensing technology is a cornerstone of load cell design and is widely used in digital weight scales, force feedback controls, and structural testing.
Flexiforce sensors are ultra-thin, flexible printed circuits that serve as tactile force and pressure sensors. They detect and quantify the force applied between two surfaces and can also measure bending using the flex sensor principle. The resistance of the sensor changes with the extent of bending, providing real-time forces, load distribution, and bending feedback data. Flexiforce sensors stand out for their easy integration with microcontrollers and data acquisition systems and are heavily featured in robotics, biomechanics, wearable technology, and human-machine interface (HMI) designs for interactive control.
A strain gauge sensor leverages the elastic deformation of the strain gauge element to convert mechanical force into a measurable electrical signal. Applications range from static force measurement, such as in weighing scales and industrial load cells, to dynamic force monitoring in structural testing, aerospace engineering, civil infrastructure, and automotive crash detection. The material and geometry of the strain gauge are critical for optimizing sensor linearity, resolution, and reliability in demanding load measurement tasks.
When tensile force is applied parallel to the thin wiring of the gauge, the wire stretches and narrows—increasing resistance, similar to stretching a rubber band. In contrast, compressive force causes the wire to shorten and widen, decreasing resistance. The resulting change in electrical resistance is directly proportional to the magnitude of the applied force, enabling highly accurate, linear output suitable for integration into force measurement transducers, instrumented bearings, and test fixtures.
Optical force sensors employ light-based measurement principles to detect changes in force, pressure, or displacement. The simplest devices function by correlating increased pressure with reduced light transmission, such as a mechanical vane blocking an LED’s output. More advanced fiber-optic force sensors use phase-shift or interferometric techniques for high-precision measurement of minimal pressure changes, with immunity to electromagnetic interference and suitability for hazardous or explosive environments.
In intensity-based optical force sensors, force or pressure shifts a diaphragm and movable obstruction (vane), reducing the light received by a photodiode. The photodiode output varies in direct relation to the applied load, providing a highly sensitive measurement unaffected by electrical noise or contact wear. Optical force sensors are essential in biomedical diagnostics, industrial automation, and research settings where electrical isolation, miniaturization, and reliability are critical.
Many optical force sensors feature a reference photodiode—unobstructed by the vane—to compensate for fluctuations in the light source or power supply, improving measurement stability and repeatability. Fiber-optic force sensors further extend the operational range by allowing remote sensing across extended distances or in environments exposed to radio frequency (RF) or electromagnetic interference.
Choosing the Right Force Sensor Technology:
When selecting a force sensor for your application, it is important to consider key performance parameters, including measurement range, sensitivity, accuracy, environmental tolerance (temperature, humidity, corrosive atmospheres), and installation constraints. Each sensor type—capacitive, inductive, piezoelectric, piezoresistive, and optical—offers unique advantages and tradeoffs depending on user intent, such as whether you require contactless operation, dynamic/high-frequency response, miniaturization, or extreme environmental robustness. Evaluating specifications from different manufacturers for features like overload protection, repeatability, resolution, and integration options can greatly impact the long-term reliability and performance of your measurement system.
For more details on applications, sensor integration, and best practices in selecting force transducers, always consult with technical specialists or request datasheets from experienced vendors in the force measurement and sensor industry.
This chapter will explore the applications of force sensors, along with their benefits and limitations.
In industrial settings, force measurement is crucial, with force transducers frequently used to gauge forces for weight measurement or during production processes. These transducers are essential for metering forces in industrial machinery and systems, including presses, assembly lines, and end-of-line inspections.
Scales are among the most typical applications for force sensors. Scales come in a wide variety of designs, including counting scales, bench scales, hopper scales, platform scales, truck scales, belt scales, and more. In order to provide accurate results when weighing different materials, force sensors are used.
Onboard weighing involves measuring the load of heavy goods or industrial vehicles while they are still loaded. This method ensures that vehicles operate at their optimal capacity—neither under-loaded, which could lead to inefficiency, nor over-loaded, which could be hazardous.
In grocery stores, scales integrated into self-service checkout counters use force sensors to weigh items during the scanning process.
Luggage scales at airports are another common application of force sensors. In the medical field, force sensors are vital for various functions, including monitoring fluid levels, operating MRI and dialysis machines, performing endoscopic procedures, and supporting physical therapy equipment. These sensors used in medical contexts must comply with specific regulatory standards. In the automotive industry, force sensors are crucial for accurately measuring truck axle loads, which ensures effective and timely load management.
Automobiles utilize numerous force sensors. For example, sensors located near trailer couplings can provide important data regarding static weight relative to dynamic driving conditions. This capability allows vehicle control systems to adjust more efficiently and effectively. In the railway sector, force sensors are used in several applications.
Force sensors measure cargo and passenger weights, as well as tractive forces on drawbars. This data is crucial for ensuring safe and efficient operations within the prescribed limits. Additionally, force sensors are employed in railway track systems.
In aerospace, force sensors are used for various purposes, including providing feedback, detecting flap positions, supporting autopilot functions, and recording flight data.
Force sensors assess the forces exerted on objects, such as in testing the impact of an accident on a motorcycle helmet.
Reference measurements are used to ensure consistency in measured values across different regions. Metrological institutes worldwide test systems using high-precision force transducers and provide standardized reference values for both domestic and international contexts.
Test benches frequently utilize force transducers to verify that materials receive the appropriate load during testing.
This section will outline the pros and cons of the various force sensor types discussed in Chapter Three. Understanding these can assist in selecting the most suitable force sensor for specific applications by providing a comparative overview.
Due to the need for force measurements in numerous sectors, including instrumentation, robotics, medicine, artificial intelligence, vehicles, and wireless transmission, to name a few, force sensing technology is of great interest to researchers. Additionally, force sensing is a difficult task since the measured force has been in a range of different scales and is affected by outside factors including noise, the environment, and material qualities. This study effectively presented a variety of force sensing technologies and its optimization approaches, and also assessed a variety of force sensor applications in diverse fields.
A strain gauge, or strain gage, is a sensing device used for measuring strain experienced by an object. It is made from a long, thin piece of conductor bonded to an elastic backing material called a carrier...
A load pin is a sensor utilized to measure force or weight in various research, control, measurement and testing applications. The load pin force sensor converts a force into an electrical signal. The load pins provide durable and...
At the heart of every weighing device is a sensor called a load cell. When an item is put on a load cell, it senses the force of the gravitational pull of the weight, which an electronic circuit processes to display as data...
A platform scale is a scale that measures the weight of objects loaded on a flat platform. The function of the platform is to transmit the weight of the object to the internal measuring device and to support the object during weighing...