Force Sensors
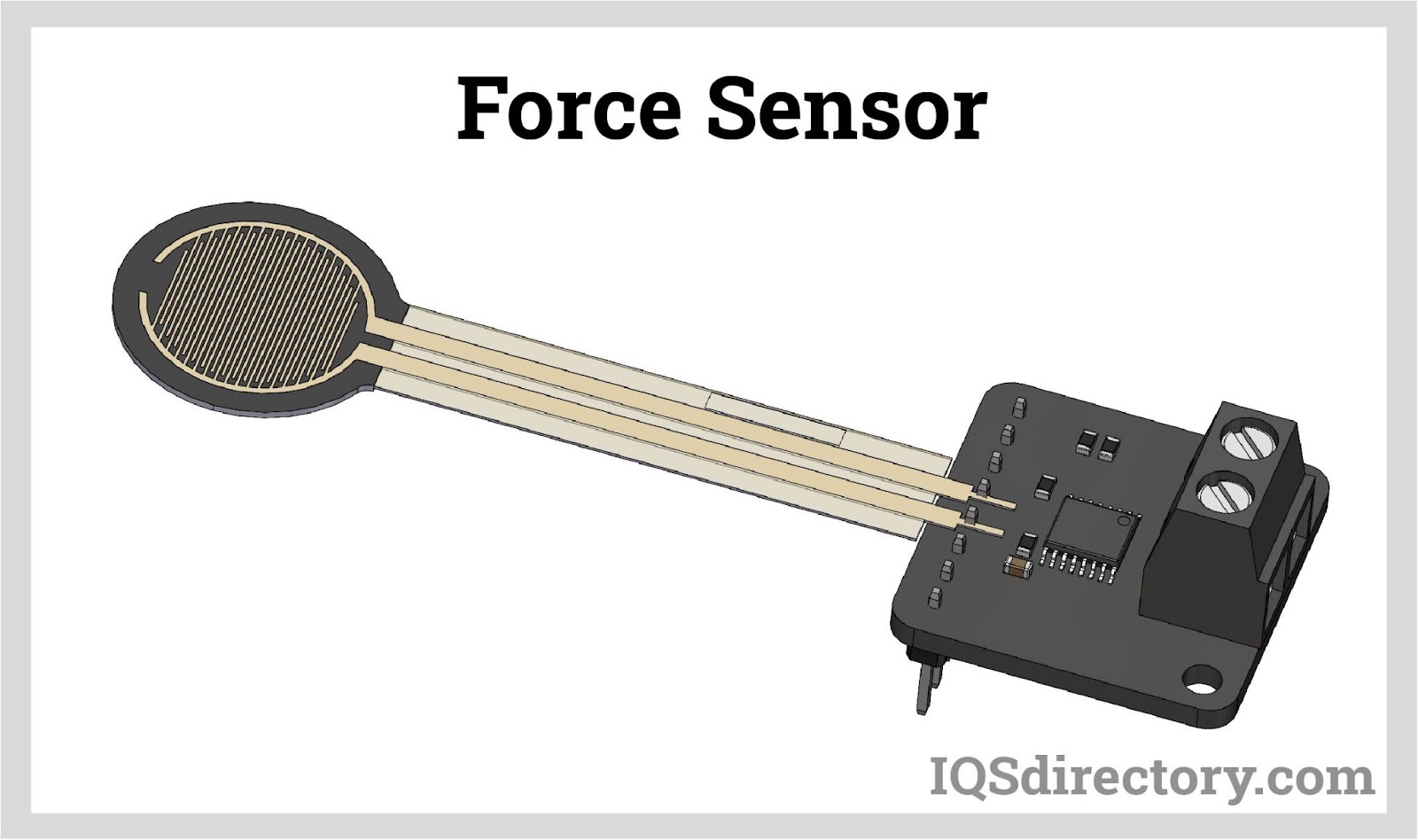
Force sensors are devices that convert mechanical forces such as weight, tension, compression, torque, strain, stress, or pressure into an electrical signal. This output signal can then be used to...
Please fill out the following form to submit a Request for Quote to any of the following companies listed on
A load pin is a sensor utilized to measure force or weight in various research, control, measurement and testing applications. The load pin force sensor converts a force into an electrical signal. The load pins provide durable and accurate measurement, even in extreme environments such as space, oceans, mines, and deserts, amongst others. An example of the value of load pins, due to their design, is identifying applied forces, and measuring and preventing overloads transferred through the pin joints.
A key benefit of force sensors, especially load pins, is the use of internal strain gauges. Developed by Strainsert and patented, this internal gauge technology significantly expands the applications of load pins. This proven technology has demonstrated its reliability and effectiveness for more than six decades.
This functionality is achieved through the pin's design, which includes a small internal cavity along its neutral axis to accommodate and safeguard the internal components, keeping the gauges isolated from external conditions. Additionally, load pins are crafted from high-strength stainless or alloy steel to enhance their linearity and ensure consistent performance.
While standard load pins are suitable for many uses, the growing diversity of applications has made custom load pins increasingly essential. The option to acquire load pins tailored to specific requirements offers a significant benefit. Strainsert has streamlined the custom design process, enabling efficient and cost-effective production to meet tight deadlines.
Load pin strain gauges are usually arranged in a Wheatstone bridge setup. With a constant voltage supply, this configuration produces a changing output voltage that corresponds to the force applied to the elastic element. Therefore, a load pin converts mechanical input into an electrical signal by undergoing several physical transformations.
In essence, when a force is exerted on the Load Pin, it causes deformation. This deformation is sensed by the strain gauges and is subsequently converted into an electrical signal that is measurable via the Wheatstone bridge.
Quantifying forces on a structure often requires costly and complex equipment. Load pins address this issue by being integrated directly into assemblies, replacing standard, non-instrumented pins or shafts within the load path. When force is applied to these instrumented load pins, the strain gauges generate a signal that enables precise load measurement, including under high stress and overload conditions.
Load pins find use in a variety of applications. Here are a few examples:
Constructed from durable stainless steel or other high-strength alloy steels, load pins offer excellent corrosion resistance. This makes them suitable for deployment in extremely challenging environments.
Many load pin systems come with built-in thermal compensation. They are designed for straightforward installation and upkeep, offering a cost-effective solution for challenging load measurement scenarios. An optional wireless transmitter for these load pins features integrated electronics, allowing for cable-free monitoring. When correctly installed and calibrated, load pins can serve as direct replacements, reducing installation expenses and eliminating the need for extra hardware components in the load path.
Load pins play a vital role across various sectors such as aerospace, marine, oil and gas exploration, military, aviation, and automotive industries. Ensuring accurate force measurements is essential for addressing product liability and safety concerns. Adhering to traceability standards aligned with NIST is often necessary to meet ISO and AS certification requirements.
Load pins can experience degradation over time due to factors such as usage, mishandling, drift, or aging. To maintain accuracy, it is essential to calibrate them periodically. Wear and tear can affect the load pin’s reliability, potentially causing issues from electrical interference, mechanical effects, instrumentation faults, or loose connections. Additionally, neglecting to inspect or clean load pins can lead to operational problems, as even in clean settings, particulate matter can accumulate. Conducting regular annual calibrations ensures that the load pins continue to perform at their best.
Ştefănescu, D. M. (2020). *Handbook of Force Transducers: Features and Uses*. Springer Nature.
Ştefănescu, D. M. (2011). *Handbook of Force Transducers: Fundamentals and Parts*. Springer-Verlag.
Force sensors are devices that convert mechanical forces such as weight, tension, compression, torque, strain, stress, or pressure into an electrical signal. This output signal can then be used to...
A load cell is a type of transducer that changes mechanical energy, such as tensile and compressive forces, into electrical signals. Various operating principles can be employed by these transducers to measure forces...
A strain gauge, also known as a strain gage, is a device designed to measure the deformation or strain on an object. It consists of a fine conductor attached to a flexible backing material, referred to as a carrier...
Central to all weighing instruments is a component known as a load cell. When an object is placed on a load cell, it detects the gravitational force exerted by the weight. This force is then processed by an electronic circuit to present the measurement...
A platform scale is designed to weigh items placed on a horizontal platform. Its role is to transfer the weight of the item to the internal measurement system while providing support for the object throughout the weighing process...