Cable Reels
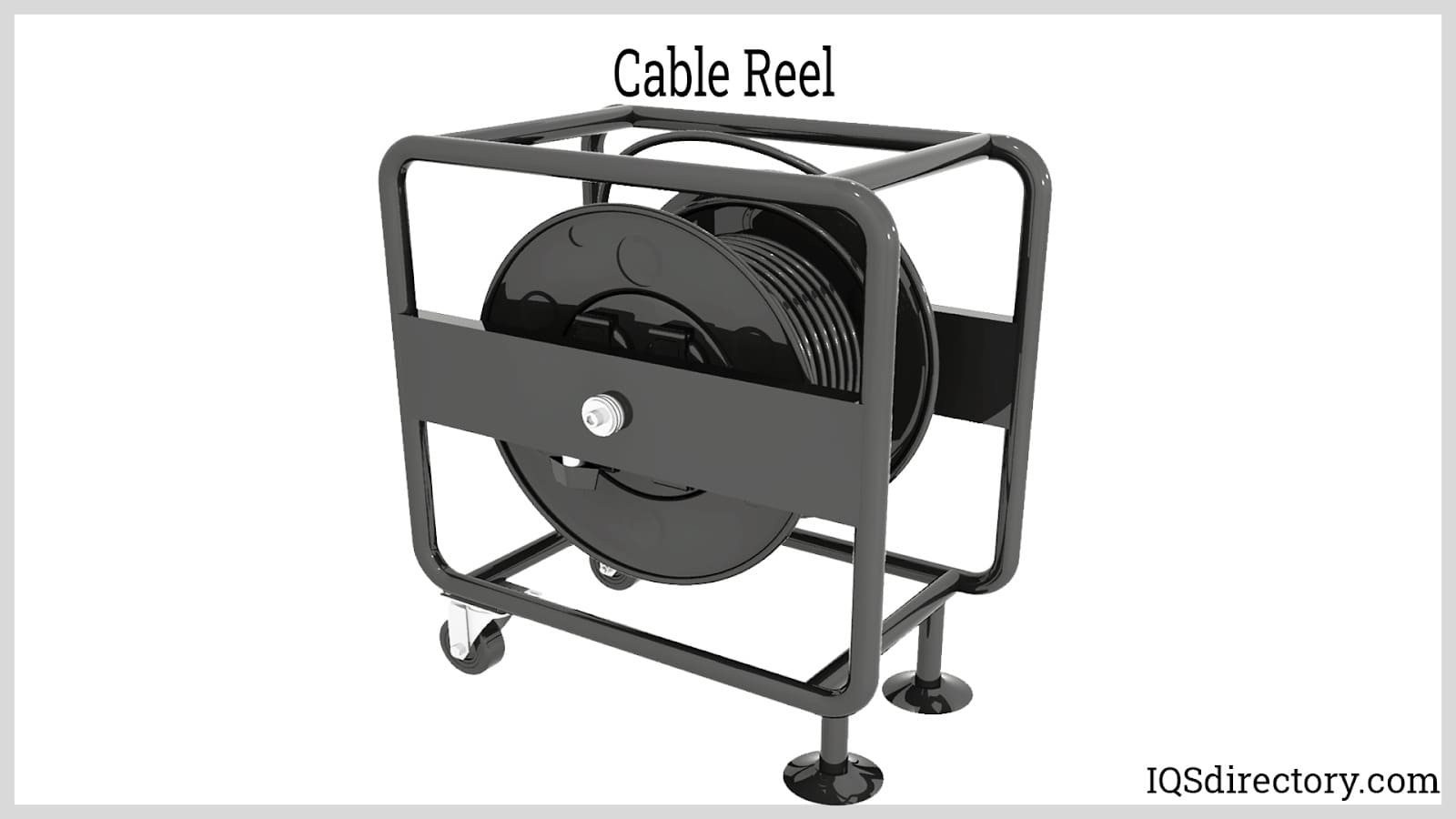
Cable reels hold conductive cable or lifting cable and are used for storage, unwinding, and winding. Contacts on electric cable reels keep the power on while winding. Reels are machines that wrap long, continuous goods like cable...
Please fill out the following form to submit a Request for Quote to any of the following companies listed on
This article will discuss industrial lubricants.
This article will give a better understanding of the topics below:
Industrial lubricants are materials designed to coat surfaces that are in motion relative to each other. Their primary function is to reduce friction and mitigate wear between these surfaces. Besides these main purposes, lubricants can also fulfill other critical functions, such as:
Lubricants can be found in a variety of forms, such as liquids, semi-solids, dry substances, and gases. Oils and gases are among the most commonly utilized types. In mechanical systems, it is vital to achieve a balance between the lubricant’s ability to minimize friction and wear and its other functions. Following manufacturer's guidelines is crucial for ensuring peak performance.
Lubricants come in several types, with the most prevalent being liquids, solids, and greases.
Industrial grease consists of a liquid lubricant mixed with a thickening agent, often soap along with additives to enhance properties like tackiness and resistance to corrosion. This grease generally becomes liquid at a dropping point temperature ranging from 200 to 500°F, although it can be higher depending on the thickening agent used. For instance, greases thickened with lime or calcium soaps have lower dropping points, while those with clay thickening agents remain solid at higher temperatures.
The National Lubricating Grease Institute (NLGI) classifies grease consistency on a scale from semifluid (000) to very hard (5), with block type (6) also included. This rating is determined through penetration tests where standard objects are pressed into the grease at specific times and temperatures. The depth of penetration is measured to assess consistency. For example, bearings lubricated with grease typically use an NLGI 2 grade.
One of the key benefits of industrial grease is its ability to lubricate hard-to-reach or enclosed surfaces more effectively than oil. Unlike oil, the consistency rating of grease does not directly reflect its viscosity. Instead, the rating is determined by the viscosity of the base lubricant. Consequently, different greases can share the same NLGI rating but exhibit varying performance characteristics. Manufacturers typically provide detailed specifications for their products.
Industrial grease can be enhanced with extreme pressure (EP) additives to protect against damage from heavy loads, shock loads, frequent starts and stops, and static loads. However, EP additives should be used judiciously, as they may increase wear on bearing surfaces, especially under extreme temperature conditions.
The types of industrial grease applied across industries are:
Lubricants are primarily derived from synthetic and petroleum-based fluids. Petroleum oils are more cost-effective due to their widespread availability, whereas synthetic oils, though pricier, often provide superior performance that can justify the higher cost in certain applications. A key characteristic of liquid lubricants is their viscosity, which comes in two main types: dynamic and absolute viscosity. Typically measured in lb-sec/ft², viscosity describes the rate of deformation between moving and stationary layers of a fluid. Kinematic viscosity, calculated by dividing dynamic viscosity by the lubricant's density, is often measured in Saybolt Seconds Universal (SSU). This measurement is determined by observing the flow of the lubricant through a capillary-tube viscometer under Newtonian flow conditions. The centipoise is the standard unit for dynamic viscosity in the cgs system. It's important to note that viscosity can be influenced by factors such as shear, temperature, and high pressure.
The viscosity index (VI) measures how a lubricant's viscosity changes with temperature, with values ranging from 0 to 100. A higher VI indicates that the lubricant's viscosity remains more stable as the temperature varies.
The pour point is the lowest temperature at which a lubricant remains fluid enough to flow. This is particularly important for applications like gravity-fed lubricators or engines that start in cold conditions. Pour point depressants can be added to reduce the pour point. Conversely, the cloud point is the temperature at which wax in the lubricant begins to visibly separate. This temperature is typically higher than the solidification point and is important because wax can cause filter blockages.
Additional characteristics of lubricants include:
Extreme pressure (EP) lubricants are specially designed to prevent metal-to-metal wear in heavily loaded gears. However, under very high pressure, these lubricants experience an increase in viscosity. Therefore, machines subjected to high loads are often recommended to use fluids with relatively low viscosity, which may not be ideal for applications with lower pressure requirements.
Synthetic oils are mostly used to increase the VI or thermal stability. This typically happens at the expense of another characteristic, e.g., pour point. Synthetic lubricants are much more expensive than mineral-based lubricants. They are thus used in industrial settings only, in which case the performance gains outweigh the extra expense. Examples of such industrial environments include instruments and heat transfer systems.
Synthetic lubricants can be formulated from a range of fluids, such as phosphate esters for fire-resistant hydraulic fluids, polyglycols for brake fluids, and silicones for use with plastics and rubbers. Engine oils, for instance, may perform additional functions beyond lubrication, including cooling, corrosion prevention, and sealing. To enhance their performance, manufacturers often blend these base fluids with various additives, including viscosity index (VI) improvers, detergents, pour point depressants, and extreme pressure (EP) agents, to achieve a range of benefits.
Solid lubricants, also known as dry film lubricants, include materials like natural graphite, synthetic compounds, and molybdenum disulfide, often combined with binders or applied directly to sliding surfaces. They are particularly useful in scenarios where liquid lubricants are unsuitable due to extreme pressures or temperatures. For instance, molybdenum disulfide is ideal for high-vacuum environments, unlike graphite, which requires water vapor to function effectively under similar conditions. Both molybdenum disulfide and graphite feature low coefficients of friction due to their layered molecular structures, which result in relatively weak interplate bonding.
Polytetrafluoroethylene (PTFE) lacks the layered structure found in lubricants like molybdenum disulfide and graphite. As a result, PTFE is often used as an additive in greases, oils, and other lubricants. It can also serve as an anti-friction coating or film on various machine parts and can be combined with aluminum to produce a hard-coat anodizing effect.
Additionally, solid lubricants can be combined with both inorganic and organic binders or applied as loose granules or powders to create curable coatings on surfaces. For example, molybdenum disulfide can be vapor-deposited onto compression fittings to function as an anti-seize agent.
When selecting a lubrication method, whether oil or grease, it's crucial to address key factors such as viscosity, oil distribution, and heat impact. These considerations include:
For applications like bearing lubrication, it's important to use high-quality synthetic or mineral oils. The choice of oil type depends on factors such as the type of bearing, load, speed, lubrication method, and operating temperature. The benefits and features of oil lubrication include:
Oil can be introduced into the bearing housing through several methods. The common approaches include:
In some bearing housing designs, the rolling bearing elements can move through an oil sump. Generally, the oil level should be kept below the center point of the lowest rolling element. To reduce churning, especially at high speeds, it’s advisable to maintain a lower oil level. Proper oil levels can be regulated and monitored using elevation drains or gauges.
Typically, a pressurized circulating oil system has a pump, oil reservoir, filter, and piping. In some cases, a heat exchanger is used. The pressurized circulating oil system provides the following advantages:
Oil-mist lubrication systems are ideal for continuous, high-speed operations. These systems allow for precise control over the lubrication reaching the bearings. Oil is either metered and atomized before being mixed with air or drawn from the reservoir using the Venturi effect. In either method, the air is filtered and delivered to the bearings to ensure adequate lubrication.
Monitoring operating temperatures is crucial for effective control of the lubrication system. Labyrinth seals help prevent contaminants from entering the system by providing a continuous pathway for the oil and pressurized air.
Key factors contributing to the success of such a system include:
The oil-mist system should be activated a few minutes before the equipment starts to ensure that the bearings are properly lubricated. This pre-lubrication helps prevent potential damage to the rolling elements and rings.
The lubricating oils are available in various forms across aircraft, automotive, industrial, etc. These oils can be synthetic type, i.e., made from chemical synthesis, or petroleum type, i.e., made from refined crude oil.
When selecting the appropriate oil viscosity for bearing applications, several factors must be taken into account, including speed, load, type of oil, bearing configuration, and environmental conditions. Oil viscosity usually decreases as temperature increases, so viscosity values should be specified with their corresponding temperatures. Generally, high-viscosity oils are used in high ambient temperatures and low-speed applications, while oils with more common viscosities are suited for low ambient temperatures and high-speed conditions.
When evaluating viscosity classes, synthetic oils offer the advantage of functioning well at both extremely cold and hot temperatures and are less susceptible to oxidation. Different types of oils have varying pressure-viscosity coefficients, so careful selection is essential. Polyalphaolefins (PAO) possess pressure-viscosity coefficients and chemical structures akin to those of petroleum hydrocarbons. Consequently, PAO oils are commonly used in bearings operating under extreme temperature conditions.
In contrast, ester, silicone, and polyglycol oils have different oxygen-based chemical structures compared to PAO and petroleum oils. This structural difference results in lower pressure-viscosity coefficients. As a result, these synthetic oils form a thinner elastohydrodynamic film compared to PAO or mineral oils with the same viscosity at operating temperatures. This reduced film thickness can increase bearing wear and shorten bearing fatigue life.
This graphical representation depicts the relationship between friction and variables such as speed, load, and fluid viscosity. The Stribeck curve illustrates how the coefficient of friction varies under different operating conditions. The x-axis represents the lubrication parameter, which is influenced by fluid film thickness, viscosity, load, and speed. As viscosity increases, an increase in speed or a decrease in load results in a larger lubrication parameter and greater fluid film thickness.
In contrast, ester, silicone, and polyglycol oils have distinct oxygen-based chemical structures compared to PAO and petroleum oils. This structural variation results in lower pressure-viscosity coefficients for these synthetic oils. Consequently, they tend to produce a thinner elastohydrodynamic film than PAO or mineral oils with the same viscosity at operating temperatures. This reduction in film thickness can lead to increased wear and reduced fatigue life of bearings.
Grease lubrication is commonly used for low to moderate speed applications with specific temperature limits. Since no single grease is universally suitable for all bearings, each type of grease has unique characteristics and limitations. Typically, greases are formulated from a base oil, various additives, and a thickening agent. Polyurea is increasingly used as a thickener due to its excellent performance in lubricating fluids.
Grease thickeners are typically categorized into complex and simple soaps. Complex soaps are formed by the reaction of a long-chain fatty acid with a difunctional acid and a shorter-chain fatty acid with a single alkaline metal. In contrast, simple soaps result from the reaction of a single fatty acid with a single alkaline metal. Common metal forms used for these thickeners include calcium, lithium, and aluminum hydroxides.
Other examples of grease thickeners include calcium sulfonate, polyurea, fumed silica, and PTFE.
Accurate grease specifications are crucial for ensuring consistent performance. These specifications typically encompass physical properties that depend on the manufacturing process, such as mechanical stability, low-temperature flow, water resistance, consistency, and oil separation. The concentration of the thickener in the grease influences each of these properties. Therefore, variations in the manufacturing process can impact these specifications. Effective control of these process variables helps maintain the grease specifications and ensures reliable performance.
Starting torque at low temperatures is a crucial factor for grease-lubricated bearings, as resistance to initial movement can be significant depending on the application. Some machinery may have difficulty starting in very cold conditions and therefore requires greases formulated with low-temperature oils that offer a wide operating temperature range. For applications where water ingress is a concern, aluminum and calcium-based greases are preferred due to their water resistance. Additionally, lithium-based greases, known for their multipurpose capabilities, are commonly used in various wheel bearings and industrial applications.
As previously noted, synthetic base oils generally have a higher maximum temperature tolerance compared to petroleum-based greases. Synthetic base oils, including organic esters, esters, and silicones, are often used with traditional additives and thickeners. These synthetic greases can function effectively within a temperature range of -100°F to 550°F.
However, the starting torque of lubricating grease is not directly related to the grease's channel properties or consistency. Instead, it depends on the grease's rheological properties.
In lubricating greases, the high-temperature limit is influenced by the effectiveness of oxidation inhibitors and the oxidation stability of the fluid. The temperature range of the grease is determined by the composition of the base oil and the dropping point of the grease thickener. Generally, the lifespan of the grease is reduced by half for every 50°F increase in operating temperature.
Therefore, selecting grease for high-temperature applications requires consideration of temperature limits, oxidation resistance, and thermal stability. For applications where lubrication is needed at temperatures above 250°F, chemically stable synthetic fluids or highly refined mineral oils are often used as the base oil in the grease.
Moisture and water can contribute to bearing damage. To address this, lubricating greases can be evaluated for their resistance to contamination. As previously mentioned, aluminum and calcium complex greases exhibit good water resistance. In contrast, sodium soap greases are water-soluble and should be avoided in applications where water exposure is a concern.
Suspended or dissolved water in lubricating oils can affect the bearing fatigue life negatively as the water can cause etching of the bearing. As much as it is unknown how water lowers fatigue life, it permeates through bearing rings' microcracks caused by the stress cycles. This causes hydrogen embrittlement and corrosion in the microcracks, thereby quickening these cracks' propagation.
Water-based fluids, such as inverted emulsions and water-glycol solutions, can also reduce bearing fatigue. Although these fluids differ from contaminants, they still contribute to the challenges associated with water-contaminated lubricants.
Grease is typically supplied in 35-pound kegs, while oil is generally available in 5-gallon pails and 55-gallon drums. The shelf life of lubricants is often determined by the additives they contain. To ensure freshness, it's recommended to use the oldest stock first, following the first-in, first-out (FIFO) principle. To maximize shelf life, store lubricants in dry, clean environments with minimal temperature fluctuations. If drums must be stored outdoors, they should be placed on their sides and covered with shelters or tarps for protection.
When handling drums, they can be rolled on their sides but should not be dropped. Forklift blades are unsuitable for gripping drum sides; instead, use drum handling jaws on forklifts, which can securely grasp the drum's perimeter.
Oil cleanliness is crucial for extending equipment life. The International Standards Organization (ISO) rates oil cleanliness based on the size and number of particles per millimeter. However, new oils can sometimes contain high particle counts, making them unsuitable for use without prior filtration to avoid reducing equipment life.
Proper handling of lubricants is vital to prevent contamination and avoid mixing different formulations. This careful handling should be a key component of any lubrication program. Additionally, used lubricants should be disposed of or recovered following environmental safety practices.
Maintaining the condition of lubricants over an extended period can help save on both purchase and disposal costs. The service life of oils can be prolonged by adding solubility enhancers, which are synthetic base oils with high solubility. These enhancers help keep particles in solution, preventing them from causing premature filter fouling and reducing varnish formation.
Filter manufacturers are increasingly designing their casings to be more environmentally friendly, with options for recycling or reuse, thus reducing waste and disposal costs. Fiber or paper inserts can be easily removed and disposed of, while components such as wire meshes and end caps can be reused, leading to an 80-90% reduction in waste.
In larger manufacturing operations, oil intended for waste can be reclaimed. Since oil leaks are inevitable, even in well-designed systems, the leaked oil is collected via drainage sumps. Each type of lubricant is separately collected, dried, and filtered for reuse. This reclaimed oil helps mitigate environmental impact and can reduce lubrication costs by cutting down on disposal expenses and waste.
A lubricant can be used as a substance applied on surfaces with relative motion in between them. The lubricant would aim to reduce friction and wear between the surfaces. However, the lubricant can have other functions apart from these primary functions. These additional functions include serving as a sealing agent, heat transfer agent, corrosion preventative agent, and an agent for trapping and expelling mechanical systems contaminants. Regardless of the system is automated or manual, the objective is to apply the right lubricant type at the right time in the right amount.
Cable reels hold conductive cable or lifting cable and are used for storage, unwinding, and winding. Contacts on electric cable reels keep the power on while winding. Reels are machines that wrap long, continuous goods like cable...
Cord reels are devices that hold extension cords that are used to supply power to electrical equipment or devices located far from the power outlet. They are also used in storing long extension cords properly...
A hose reel is a mechanism for storing and use of a hose on a barrel for easy access. It is a system designed to make hoses, cords, flexible tubing, and wire conveniently available for immediate use...
Lubrication systems distribute the lubricant to the moving machine parts in contact. Lubricants reduce the friction between sliding or rolling machine elements, such as gears, spindles, bearings, chains, dies, screws, cylinders, valves, and...
A metering pump is a precision mechanical device that moves or pumps a measured amount of a fluid or liquid in a predetermined time period to create an accurate and exact volumetric flow...