Cable Reels
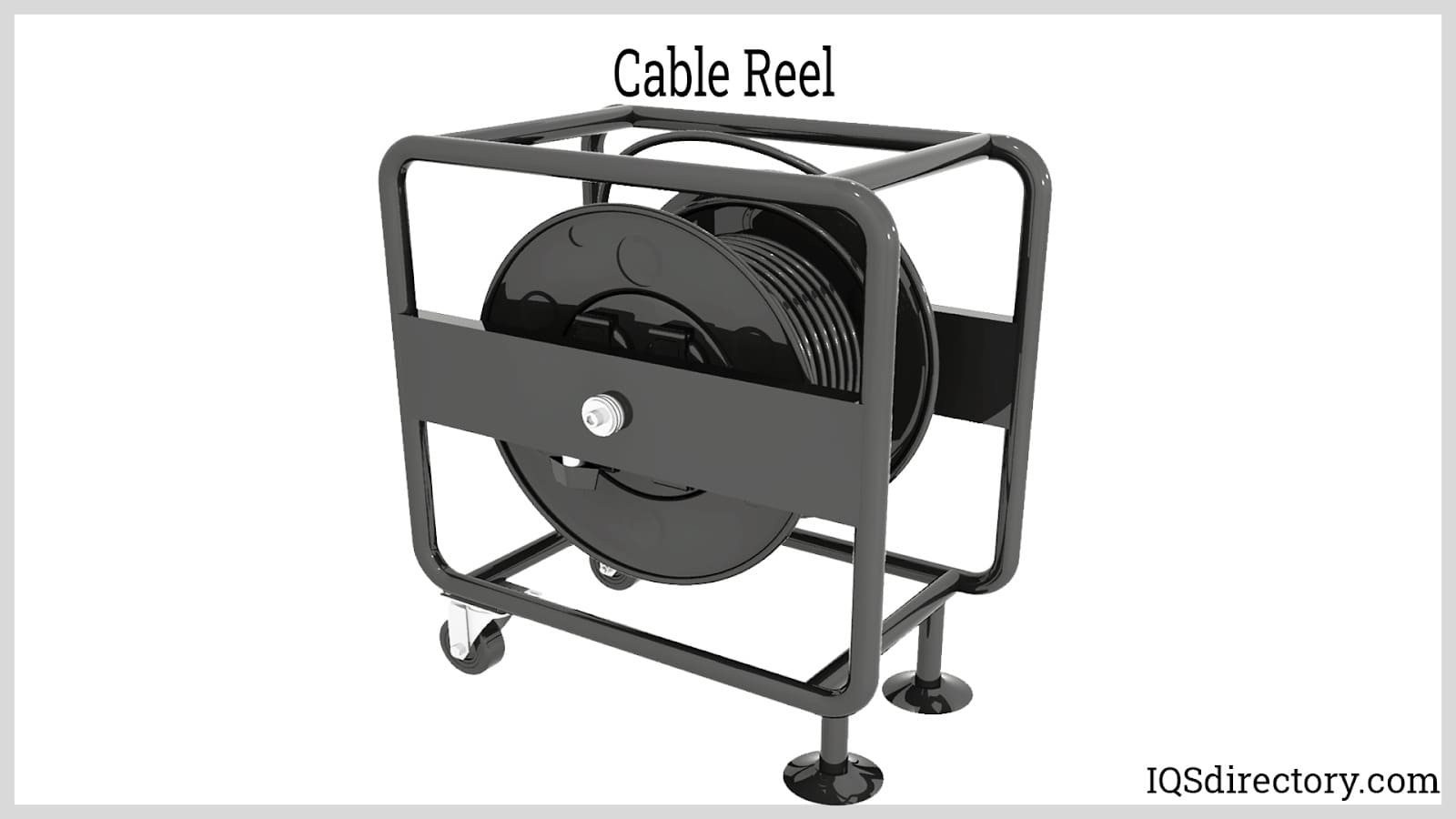
Cable reels hold conductive cable or lifting cable and are used for storage, unwinding, and winding. Contacts on electric cable reels keep the power on while winding. Reels are machines that wrap long, continuous goods like cable...
Please fill out the following form to submit a Request for Quote to any of the following companies listed on
This article takes an in-depth look at lubrication systems.
Read further and learn more about:
Lubrication systems are engineered to deliver lubricants to moving machine components that contact each other. These lubricants are vital for reducing friction between interacting surfaces, such as gears, spindles, bearings, chains, dies, screws, cylinders, valves, and cables. By minimizing friction, lubricants not only prevent wear and tear but also reduce heat build-up, thereby avoiding premature component failure and extending the lifespan of machine parts. Furthermore, lubricants can act as coolants, counteracting thermal expansion and preserving the precision of the machine elements.
These systems regulate the amount and pressure of the lubricant applied to the surfaces of interacting moving parts, ensuring efficient and consistent operation of the machinery. Lubrication systems are extensively utilized in industries such as automotive, industrial manufacturing, oil and gas, power generation, and steel processing, and are essential components in automotive engines. The sophistication of lubrication systems varies from simple mechanical grease guns to advanced automated and centralized lubricant distribution systems.
The basic components of industrial lubrication systems are as follows:
Pump: The pump distributes the lubricant to the target machine parts to different locations and heights through the lubricating system’s supply and feed lines. The pump must generate enough pressure to push the lubricant through the pipes, fittings, and valves and to compensate for the pressure drop and friction points encountered during transportation. This component must be reliable and efficient in handling the flow properties of the lubricant.
The types of industrial lubrication systems are as follows:
Single line resistance (SLR) lubrication systems use a central pump to direct lubricant through one or more parallel lines. These systems are designed for light to medium-duty machinery and operate at oil pressures between 100 and 250 psi, capable of servicing up to 100 lubrication points. Lubricant flow is carefully managed to target specific machine components during operation.
SLR systems can be either manual or automatic. Manual versions rely on a hand pump for occasional lubrication, while automatic versions, utilizing either timing or mechanical drives, offer continuous or scheduled lubrication, minimizing the need for manual refilling.
With their compact and cost-effective design, SLR lubrication systems are well-suited for closely packed bearing clusters and similar setups.
Single point (SP) lubrication systems deliver lubricant to a single lubrication point, making them ideal for situations with a limited number of lubrication needs dispersed over a large area or in hard-to-reach locations. Although primarily automatic, manual versions of these systems are also available. SP lubrication systems are designed with a compact structure, housing components like the reservoir, metering devices, and supply lines within a protective enclosure. The main categories of single-point lubrication systems include:
Spring-Loaded Lubricators: Spring-loaded lubricators are older designs of SP lubrication systems. These lubricators use a spring-loaded plunger to displace grease. The flow of the grease is dependent on the grease consistency, backpressure, and temperature. The flow can be adjusted by installing a piston O-ring, which creates a varying level of friction as it moves down the tapered reservoir wall. Different orifice sizes can be installed on the lubricator’s nipple to control the grease discharge. The spring-loaded lubricator is installed to deliver grease to a lubrication point by threading it to a port.
Spring-loaded lubricators have chambers commonly constructed from polycarbonate or borosilicate, which can withstand temperatures of up to 2500°F and 4500°F, respectively. Their volumes range from 2 to 18 ounces and can handle lubricant pressure from 2 to 65 psi.
Since grease flow is dependent on temperature, spring-loaded lubricators are not suitable for environments with wide temperature variations. The viscosity of the grease is directly proportional to its temperature. Also, since grease consistency increases with applying shear forces (i.e., thixotropic nature), these lubricators cannot be used in environments with high vibrations.
Gas-Charged Automatic Lubricators: Gas-charged automatic lubricators consist of a cylinder with the pressure generator and lubricant stored in different chambers. The piston, which separates the two chambers, pushes the lubricant to respond to the pressure build-up caused by the pressure generator.
The pressure generator of the gas-charged automatic lubricator is composed of an electrolytic solution and a galvanic strip contained in a plastic tube. The activating screw breaks the plastic tube after the injector is installed, which exposes the galvanic strip to the electrolytic solution. This exposure results in an electrochemical reaction that produces hydrogen gas. As more hydrogen gas is produced, the internal pressure within the generator increases, which pushes the piston. The piston then ejects the lubricant out of its chamber. The rate of lubricant discharge can be designed or set by the manufacturer depending on the nature of the customer’s application.
The electrochemical reaction inside the pressure generator is dependent on temperature. As the ambient temperature increases, consequently increasing the lubricant discharge rate. The flow properties of the lubricant also vary with the ambient temperature.
Since hydrogen gas is flammable, gas-charged automatic lubricators should not be used in areas with ignition sources.
Positive Displacement Single Point Lubricators: Positive displacement single point (PDSP) lubricators are electromechanical single point lubricators consisting of a follower plate that ejects the grease from its canister. The follower plate is powered by a battery or an electric motor. The rate of grease ejection can be precisely controlled and is not dependent on ambient temperature. PDSP lubricators can be controlled such that a specific volume of grease is dispensed at regular time intervals. The capacity of PDSP lubricators ranges from 60 cc to 600 cc.
Dual-line lubrication systems, sometimes referred to as "dualine" or double line systems, function through an alternating two-phase cycle. During the initial phase, lubricant is drawn from the reservoir and directed through the first supply line, activating the inlet and discharge pistons of all injectors in a single direction. The injectors, which are modular and shared between the two lines, release lubricant accordingly. When the pressure reaches a set level on the end-line pressure switch, the system shifts, allowing lubricant to flow through the second supply line, reversing the piston movement and distribution direction.
These systems are designed for continuous lubrication of multiple points and are prevalent in various industries with ongoing lubrication needs. They are well-suited for medium to large machinery and operate effectively in demanding environments. Cost-effective for setups with over 20 lubrication points, dual-line systems can be expanded without overhauling the entire setup. In case of blockages, the system ensures that remaining points continue receiving lubrication. Additionally, dual-line systems accommodate a broad spectrum of lubricants, including light oils and grade-2 greases.
Here are the types of small-scale or manual lubrication systems. These systems are generally used to supply lubricant to a single point within a specific application and are best suited for occasional or intermittent use.
Chain Oiler: Chain oilers are devices used to supply oil lubricant automatically to the bicycle and motorcycle chain and sprocket assembly. These devices replace the traditional chain spray, which dispenses sticky and tacky lubricant, causing the chain to pick up excessive dirt from the road and fail prematurely. Moreover, chain sprays are also time-consuming and messy to apply.
Like industrial lubrication systems, automatic chain oilers are composed of a reservoir, pump, metering device, and an injector; these components are installed in bicycles and motorcycles which do not appear bulky. These integrated components are connected to a controller in which the release of the lubricant can be set or adjusted. The lubricant is usually released when the bicycle or motorcycle is running.
Grease Gun: Grease guns are one of the commonly found tools in machine shops and garages. They are used to inject grease to a lubrication point. They are also used in maintaining light to heavy machinery and equipment in industrial plants. The lubricant is contained in a canister and is dispensed through an aperture by the following methods:
Grease Pump: Grease pumps are devices used to deliver grease lubricants with wide viscosity ranges. These devices operate pneumatically or electrically. They are suitable for pumping high volumes of highly viscous and dense grease lubricants because their pumps have a high compression ratio. The delivery of specific volumes of grease can be controlled precisely.
Positive displacement injector (PDI) lubrication systems utilize a central pump to create high pressure (over 55 bars) that delivers lubricant through multiple supply lines. The lubricant is conveyed to feed lines where PDIs are installed. When the desired pressure is achieved, the piston within the PDI, which is fixed in displacement, moves hydraulically against spring force to release a specific quantity of lubricant at each lubrication point. These systems are ideal for small to medium machinery requiring precise lubricant delivery at various points and can be set to dispense at regular intervals.
Positive Displacement Injector (PDI) systems operate with a central pump that generates high pressure (over 55 bars) to push lubricant through several supply lines. The lubricant reaches the feed lines where PDIs are situated. Once the necessary pressure is achieved, the fixed displacement piston within each PDI moves against a spring to release a precise amount of lubricant at each lubrication point. These systems are ideal for small to medium machinery where exact and precise lubrication at multiple points is required. PDIs can be set to dispense lubricant at scheduled intervals.
The types of industrial lubricants are the following:
Oil serves as the primary substance in lubricants, minimizing friction and wear between interacting machine parts. Oil-based lubricants come in various viscosities and can be derived from synthetic, vegetable, or mineral sources.
While oil lubricants are considered the most refined type, they often include additives. For instance, antioxidants and corrosion inhibitors are used to prevent oxidation and rust, while detergents help avoid deposit buildup. Viscosity index improvers like polyacrylates and butadiene are added to maintain the oil's viscosity at elevated temperatures.
Oil lubricants are frequently applied to hinges, bearings, and blades for sharpening. However, they are not suitable for use on surfaces that are dirty, dusty, or wet.
Grease consists of a blend of oil, a thickening agent, and additives with inherent lubricating properties such as PTFE, graphite, and molybdenum disulfide. The additional stickiness of grease allows it to adhere effectively to surfaces, providing enhanced protection against corrosion and wear.
Grease lubricants are ideal for applications where lubrication is infrequent, as they have the ability to remain in place for extended periods. Due to their higher viscosities and densities, they create more resistance, making them less suitable for use on small or rapidly moving components.
Penetrating lubricants are specifically designed to address rusted or debris-covered machine parts. They work by infiltrating small crevices in the metal, effectively loosening and disintegrating rust. Despite their effectiveness in breaking down rust, they do not provide long-lasting lubrication and should not replace other lubricant types in regular maintenance.
Dry lubricants are made up of tiny particles with self-lubricating properties such as PTFE, graphite, and molybdenum disulfide. These particles create a microscopic, slippery film when they are sprayed onto the surface of the machine part. Dry lubricants can be mixed and sprayed together with water, alcohol, or solvent, eventually evaporating, leaving the thin lubricating film on the surface. Unlike oil and grease, dry lubricants do not attract dust and dirt.
Dry lubricants are ideal for precision components like ball screws, lead screws, and gears, as well as for threaded rods, locks, bearings, and hinges. They excel in high-temperature environments where oils may degrade, but they are less effective in environments exposed to liquids and solvents, as these can wash away the lubricant.
Gear lubricants are designed to safeguard gears and their teeth from wear and tear. They need to be thermally stable to avoid sludge buildup. Additives are often included to prevent pitting and localized corrosion on gear teeth. Some formulations incorporate extreme pressure (EP) additives to shield surfaces from high pressures, especially in gearboxes under significant load.
Compressor oils are crucial for lubricating rotating components to minimize friction and wear. In addition to their lubricating function, these oils act as coolants by dissipating heat produced during air compression and serve as sealants for the compression chamber. It is essential to use compressor oils specifically designed for this purpose, as other types of lubricants are not suitable replacements.
Cable reels hold conductive cable or lifting cable and are used for storage, unwinding, and winding. Contacts on electric cable reels keep the power on while winding. Reels are machines that wrap long, continuous goods like cable...
A conveyor system is a method for moving packages, products, supplies, parts, and equipment for production, shipping, or relocation. The different types of conveying systems include pneumatic, screw, belt, and roller. The construction of individual systems depends on the materials...
Cord reels are devices that hold extension cords that are used to supply power to electrical equipment or devices located far from the power outlet. They are also used in storing long extension cords properly...
A hose reel is a mechanism for storing and use of a hose on a barrel for easy access. It is a system designed to make hoses, cords, flexible tubing, and wire conveniently available for immediate use...
A lubricant is a substance that is applied on surfaces that have relative motion in between them. The lubricant reduces friction and wears between the surfaces. However, the lubricant can have other...
A metering pump is a precision mechanical device that moves or pumps a measured amount of a fluid or liquid in a predetermined time period to create an accurate and exact volumetric flow...