Belt Conveyors
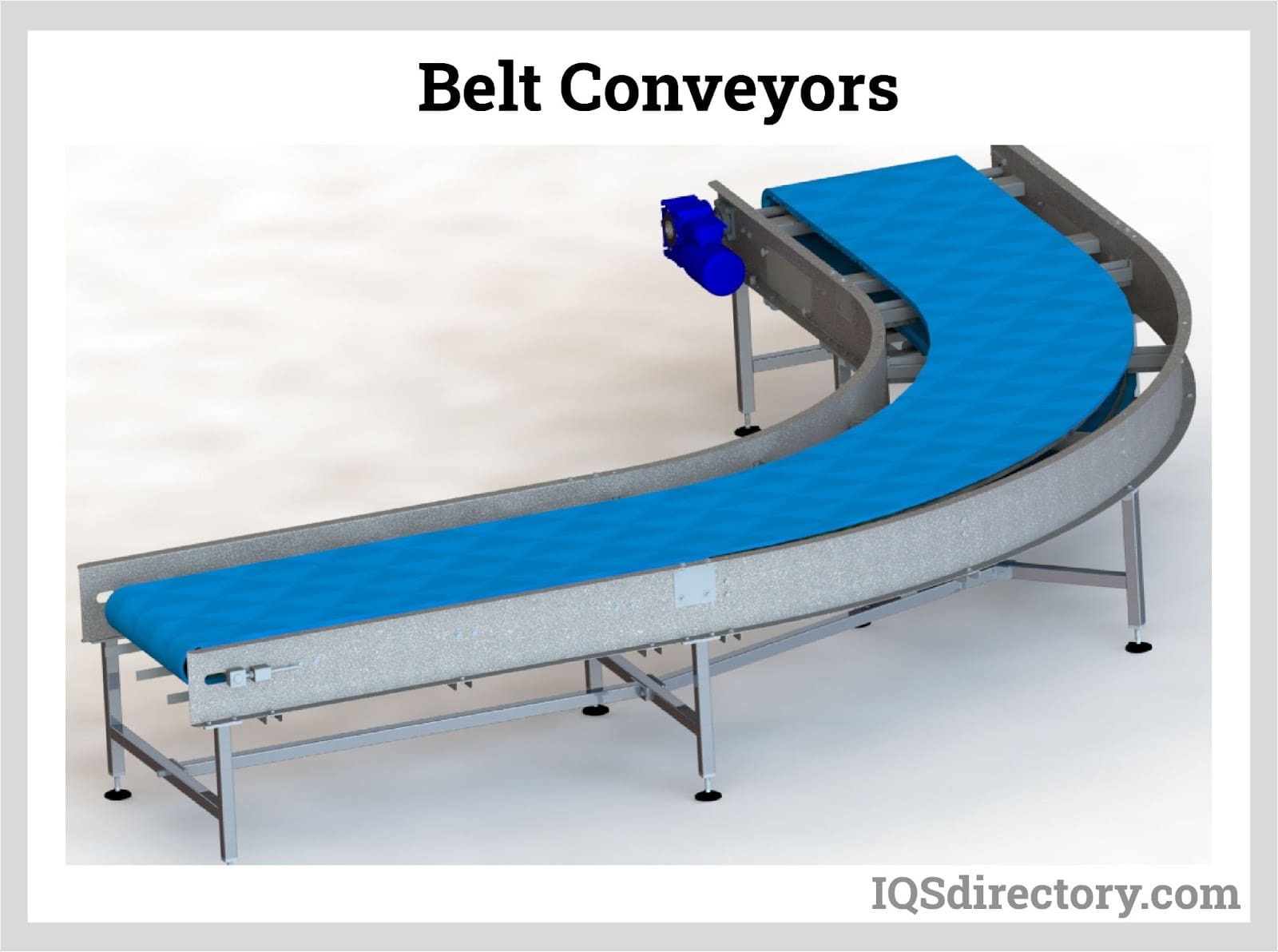
A belt conveyor is a system designed to transport or move physical items like materials, goods, even people from one point to another. Unlike other conveying means that employ chains, spirals, hydraulics, etc...
Please fill out the following form to submit a Request for Quote to any of the following companies listed on
This article will take an in-depth look at machine guards.
The article will bring more detail on topics such as:
This chapter explores the definition, design, and operating principles of machine guards, detailing their critical importance in safety.
A machine guard is a crucial safety component crafted to form a protective wall between workers and machinery within environments like manufacturing plants, warehouses, and factories. These barriers also limit vehicular access, manage traffic, and keep debris in check. Nearly all machinery types rely on safety guards.
Machinery posing threats due to impacts, rotations, shearing, reciprocating actions, meshing gears, belts, or cutting tools requires suitable barriers to ensure operator safety.
Manufacturers typically construct machine guards through a combination of CNC machining, extrusion, and post-extrusion techniques (using rivets, bolts, nuts, screws, etc.). More details on these methods below.
Extrusion involves shaping materials like aluminum by forcing them through a die with a specific opening. This process results in a shape that mirrors the die, emerging as an extended piece. The procedure involves pushing aluminum through the die with a strong ram, creating shapes pulled along a runout table. Aluminum extrusion is relatively simple to grasp at a basic level.
Extrusion typically yields three shape types: solid forms without enclosed areas (angles, rods, beams), hollow forms with one or more voids (like rectangular or square tubes), and semi-hollow shapes with partially enclosed voids ("C" channels with narrow gaps). These forms are vital for machine guard production, described in the following ten steps.
The pliable billet goes into the press, experiencing up to 15,000 tons of ram pressure.
As pressure is applied, the billet fills the extrusion container. Walls constrain the increasing volume.
Post-extrusion involves shaping a flat, warm extruded sheet into a form. This procedure, often occurring during extrusion, is common with rigid PVC. It balances extrusion's cost-effectiveness with injection molding's shaping benefits.
CNC machining employs sophisticated computer programs to autonomously design and produce precise parts. This technology is foundational in diverse industries, including creating machine guards. CNC, symbolizing Computer Numerical Control, highlights its computerized accuracy.
This CNC umbrella covers various techniques ensuring swift, precise, and efficient part production, whether for small or large volumes.
Choosing the right CNC machine shop involves assessing specific processes for guard design and production. Important aspects include dimensional capabilities, material suitability, production volume, software compatibility, and types of available machinery. CNC providers differ significantly in terms of materials and dimensions. Diameter capacities have set ranges, and volume specifications follow suit. Material options should be exact, generally favoring metals for durability, though plastic is a viable alternative.
Once suitable facilities, materials, and software are determined, the machining process begins with client-manufacturer collaboration. Employing computer-aided design (CAD) and manufacturing (CAM), alongside advanced photo imaging techniques, designs are produced in-house. These programs convert dimensions into machine-readable code. Raw materials, typically metal or plastic in billets, are loaded into machinery.
Pre-extruded materials can be sourced from either the machining shop or the client. In environments with multiple machines, manual material movement between steps may occur, though automation is possible. Once materials are ready, software initiates their transformation, guiding machinery operations.
The computerized system executes commands sequentially, manipulating positioning, pressure, depth, and other actions for precise part creation, enabling rapid, accurate duplications—far swifter than manual efforts.
Machine guards can be made from various materials, with metal as the standard due to its strength and durability. Metal is often shaped into bars, pipes, mesh, panels, or sheets. For visibility-driven applications, polycarbonate, a strong and shatter-resistant plastic, is preferred over glass due to its impact tolerance and durability. Wood is feasible for environments lacking high temperatures or corrosive exposure.
Industrial machine guards serve to secure equipment using various methods. Notable examples include point of operation guarding, point guarding, and fixed perimeter guarding.
Point guarding emphasizes shielding moving machine parts that pose risks to operators or nearby personnel. According to OSHA standard 1910.212(a)(2), such guards should be securely attached to the machine or placed nearby where direct attachment is impractical.
"Point of operation guarding" targets the specific machine areas engaged by the operator, aiming to preempt operator-machine contact and maintain a safe zone during operations.
Fixed perimeter guarding involves constructing complete enclosures or boundaries around a machine's workspace, ensuring full area security to prevent unintended contact with moving parts.
Key factors for choosing machine guards include:
Safety risks and regulations can vary widely between organizations, regardless of similar machinery usage. Evaluating each workplace's conditions is critical for implementing correct safety guard setups.
Determine the distance between the machine and operator to pinpoint risks, guiding the guard type—be it wire mesh or solid panels. Additionally, consult standards from MSHA, OSHA, and CSA to grasp unique machine risks encountered.
While expertise in guard design and manufacture isn't mandatory, basic awareness is beneficial. Understanding core MSHA, OSHA, and CSA regulations aids in recognizing quality standards.
For example, delving into wire mesh guard production helps identify optimal materials, wire gauges, and weaving methods, which guide informed choice-making.
To comply with regulations and uphold safety standards, companies with machinery must correctly install guards. Given varying machine sizes, custom guards from manufacturers may be necessary when standard sizes are incompatible. Wire mesh guards offer flexible solutions due to their adaptability.
When selecting machine guard panels, assess the manufacturer for their support and service level. Partner with reliable suppliers offering comprehensive guidance during purchase. Also, opt for manufacturers providing post-sale support to address subsequent inquiries or issues.
Machine guards come in four main types: fixed, adjustable, interlocked, and self-adjusting. These categories encompass various subtypes of machine guards, each tailored to specific safety needs.
Chuck guards are crucial safety devices designed to shield workers from flying debris such as shards, shavings, and tool bits produced during machining processes. Typically, these guards are curved panels mounted to machinery with brackets and screws. They are predominantly used on lathes, which operate at high RPMs (revolutions per minute) to shape various materials like metal, wood, and glass. The chuck, a clamping mechanism that secures rotating materials and tools, is a central feature of these lathes. Chuck guards are attached to the chuck itself, allowing them to be easily swung or lifted for convenient access to the lathe while providing protection.
Chuck guards are widely utilized in factories and manufacturing settings to enhance worker safety during processes like glass blowing, metal spinning, shearing, and sanding. These guards, along with protective clothing and goggles, help prevent injuries from debris ejected by high-speed lathes. Although the debris is typically small, its high velocity makes it a significant hazard. Chuck guards offer a straightforward and effective solution to mitigate these risks. Similar to chuck guards, other machine guards include milling machine guards, lathe guards, and drill press guards, each designed to address specific hazards associated with their respective machines.
Drill press guards are designed to shield operators from potential injuries during the use of drill presses. These guards help protect personnel from contaminants, moving parts, flying debris, and excessive noise generated by the equipment, ensuring a safer working environment.
Drill press guards, a subcategory of machine guards, shield operators' eyes and hands from cutting blades, cutting tools, hot chips, grease, splash coolants, and oil. Drill presses, according to the OSHA list, need guarding where work is done when the material is in an ongoing process. Drill press guards come in a variety of styles.
Fixed machine guards are securely attached to a machine or tool and do not have any moving parts, making them immovable during operation. These guards are typically employed to cover areas of the machine that pose hazards and do not require operator interaction, such as flywheels or fan blades. Since they are a permanent part of the machinery, they must be disassembled and removed before any maintenance or adjustments can be made.
Interlocking guards, also referred to as barrier guards, are designed to automatically cut off or disengage the power source when they are opened or removed. They are particularly beneficial in situations where operators need to access guarded machine components, such as for clearing jams, while ensuring that the machine is safely shut down during these activities.
Interlocking guards allow safe entry to the machine's interior without the need for complete disassembly. However, they can be inadvertently opened, so regular maintenance and careful adjustment are necessary to ensure their proper function.
A lathe guard functions as a protective shield or visor designed to safeguard operators and nearby workers from hazards associated with a spinning lathe. It helps prevent injuries from flying debris, chips, broken tool pieces, and shavings, and also keeps fingers clear of the high-speed rotating lathe.
Lathe guards come in pre-engineered sizes or are custom made to fit the particular dimensions of the machine. They are easily attached to the chuck or cross-slide by a bracket on screws, though others are attached to other lathe devices. Lathe guards can be curved and thus shaped as a half circle, or they can be flat and have three sides. The most common design consists of an aluminum die-cast frame and a big polycarbonate vision panel, a see-through plastic material which behaves like glass but is lightweight, has high impact strength, shatter resistance, and flexibility.
Milling machine guards are protective enclosures, typically consisting of two or three sides, designed to cover and protect dangerous milling machinery. They shield operators and machinists from hazards such as flying coolant, swarf, broken tools, and loose material fragments. These guards help maintain a clean work environment and enhance safety without compromising productivity.
Constructed from panels set within an aluminum frame or steel tubing, milling machine guards often feature transparent panels to allow visibility of the machining process. Milling machines are versatile tools used to cut and shape materials such as wood, plastic, and metals.
Milling machine guards are commonly found in manufacturing settings, workshops, and educational shop classes. Whether static (non-moving) or traversing (able to move without removal), these guards are securely locked in place whenever the milling machine is operating. They can either be pre-engineered in various standard sizes or custom-built to meet specific design requirements. Typically, milling machine guards are larger than other types of machine guards, reflecting the size of the milling machinery they protect.
There are two main types of milling machine guards: sliding and stationary. Both types are securely locked during operation to ensure worker safety. Sliding guards can move back and forth along a cross-slide, while stationary guards may need to be removed or swung aside to access the machining area. All panels used in milling machine guards are made from polycarbonate, a durable and shatter-resistant plastic that allows visibility while providing robust protection.
In industrial settings, safety barriers serve as physical partitions designed to prevent accidents and injuries. They protect operating personnel and employees from hazardous machinery, restrict vehicle access to designated areas, and manage traffic flow. These barriers enclose robotic and automated systems, safeguard heavy machinery that poses a risk of injury, and secure storage areas such as racks and shelving systems.
Safety barriers come in two main types designed to shield workers from injury and prevent costly vehicle accidents. Wire mesh and fencing barriers, for instance, restrict unauthorized access to dangerous areas and enclose automated machinery. Often equipped with interlocked electrical doors that shut off power when opened, these barriers are generally over six feet tall and easy to assemble. They are installed using a series of ground-mounted posts, and the doors can be customized as either panel or swing types to suit specific company needs.
Safety guards are physical barriers designed to encase potentially dangerous machinery and moving parts. They vary widely in size and shape, tailored to shield employees from preventable injuries related to machine operation. Many safety guards are custom-built to fit the specific safety needs of a particular machine or device. These guards can be made from various materials, including metals, wood, and plastics, with the choice of material depending on the type of machinery being protected.
The types of safety guards are self-adjusting, adjustable, fixed, and interlocked. Self-adjusting guards can automatically adjust themselves, whereas conventional adjusting machine guards should be shifted by hand. Fixed guards are permanently affixed to a part of the machinery, whereas interlocked guards are by electronic means connected to the machinery and thus capable of shutting down the machine if the barrier is crossed.
Self-adjusting machine guards automatically modify their positions when new materials are fed into the machines. Commonly used with saws, these guards move away from the cutting area to accommodate material entry and then cover the blade when it is not in operation, ensuring protection while maintaining accessibility.
In addition to the aforementioned types, there are numerous specialized machine guards designed for specific equipment. Examples include chuck guards, lathe guards, drill press guards, milling machine guards, wire guards, brake monitors, and safety light curtains, each tailored to address particular safety needs and machine types.
Wire guards are used to control traffic flow, establish secure areas, and contain large debris from escaping the work area. These guards are easy to install and are not reliant on electrical power, unlike safety light curtains. They are frequently employed to protect robotic systems, automated machinery, heavy equipment, tanks, spiral HVAC fans, and motors. Suitable for both indoor and outdoor use, wire guards are generally over six feet tall to deter individuals from climbing over them.
Wire guards serve to shield workers from accidents and injuries, prevent unauthorized access to restricted areas, and help reduce risks of tampering and vandalism. Unlike other machine guards, wire guards provide a visual warning of potential hazards. They are often brightly colored, such as yellow or orange, and are typically equipped with warning signs to enhance visibility and caution.
One widely used type of guard is the tiered guard, which attaches to the drill press's quill and encloses the rotating components. This design allows operators to maintain a clear view of the drilling process while ensuring safety. Although these guards generally do not pose significant issues, they can sometimes interfere with the task. In such cases, a safety protocol should be established to manage potential hazards, allowing the guard to be temporarily removed for task completion when necessary.
Safety guards come in various types, including self-adjusting, adjustable, fixed, and interlocked. Self-adjusting guards automatically modify their position, while adjustable guards require manual adjustment. Fixed guards are permanently attached to the machinery, and interlocked guards are electronically connected to the machine, enabling automatic shutdown if the guard is tampered with or removed.
This chapter will explore the applications and advantages of machine guards.
Machines such as presses, automated assembly lines, milling machines, roll formers, saws, feeders, and robotics have dangerous parts that require machine guards for safe operation. These safeguards are essential to prevent injuries like crushed hands, burns, blindness, limb loss, or fatalities. While many machines come with built-in guards, others may need custom-built guards tailored to specific operations. Proper machine guarding is also necessary for robotic systems.
Machine guards are crucial for ensuring worker safety, maintaining orderly operations, and promoting efficient workflow. They not only protect employees but also foster a sense of confidence and well-being in the workplace.
OSHA requirements for machine guards include:
Guards must be inspected regularly as part of the machine guard maintenance schedule.
A guard should be replaced if:
Guards should be cleaned using a non-abrasive plastic cleaner. Avoid cleaning products based on ammonia, such as glass cleaner. Yellowing of transparent guards is generally not a major issue since they are made from PETG plastic rather than polycarbonate.
A machine guard is a device whose role is to act as a safety barrier between a worker and machines used in manufacturing facilities, factories, plants, and warehouses. They are manufactured from extrusion, CNC machining, and post extrusion process. Metal is usually the preferred material for making machine guards though plastic and wood are used as well. Machine guards play a vital role in protecting operators and employees from workplace hazards.
A belt conveyor is a system designed to transport or move physical items like materials, goods, even people from one point to another. Unlike other conveying means that employ chains, spirals, hydraulics, etc...
A conveyor system is a method for moving packages, products, supplies, parts, and equipment for production, shipping, or relocation. The different types of conveying systems include pneumatic, screw, belt, and roller. The construction of individual systems depends on the materials...
A forging press is a process that uses a vertical ram to apply gradual controlled pressure to a die holding a workpiece. The process is similar to drop forging but uses slow pressure instead of a series of blows. The slow movement of the ram penetrates deeper into the workpiece...
A hydraulic press is a mechanical device that uses the static pressure of a liquid, as defined by Pascal‘s principle, to shape, deform, and configure various types of metals, plastics, rubber, and wood. The mechanism of a hydraulic press consists of a mainframe, power system, and controls...
A power press machine is a hydraulic machine used to cut, bend, shape, and press any metal sheet into a required shape. A power press is a multi-faceted machine for shaping metal sheets in order to...
Roller conveyors are a type of conveyor belt that allows objects to skate on its surface by using rollers, which are equally spaced revolving cylinders. They transport stuff from one location to another...
A vertical conveyor is an engineered mechanical method for moving goods, products, supplies, parts, and components from a lower level to a higher level or from a higher level to a lower level. They are...