Alnico Magnets
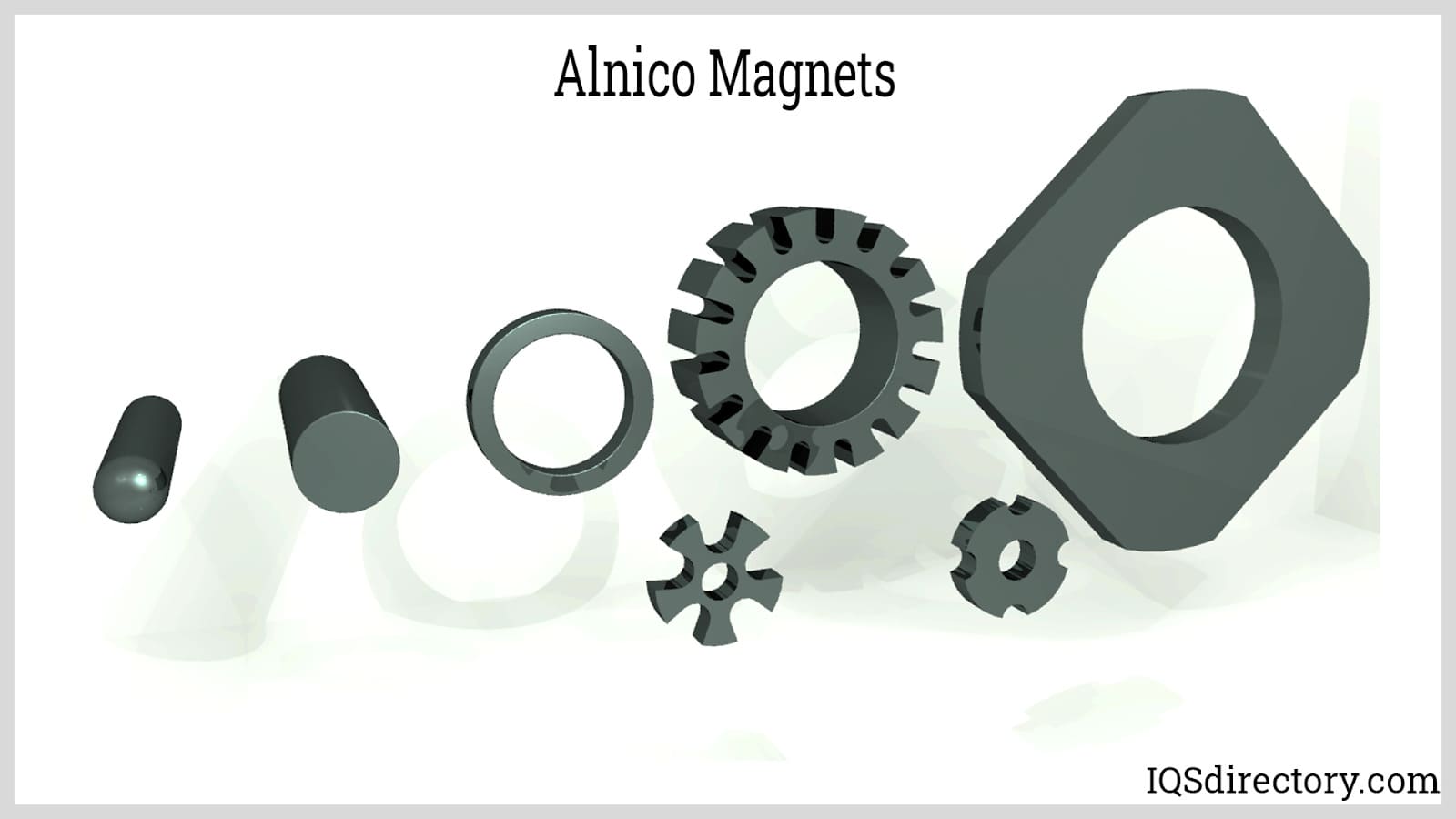
An Alnico magnet is a permanent magnet made by combiming aluminum, nickel, iron, cobalt, and other elements. They come in isotropic, non-directional, or anisotropic, mono-directional, form...
Please fill out the following form to submit a Request for Quote to any of the following companies listed on
This article will take an in-depth look at magnets.
The article will bring more understanding on topics such as:
This chapter delves into the basics of magnets, covering manufacturing techniques and their operative mechanisms.
Magnets are entities that generate a distinct force on other objects without physical interaction. This magnetic force can either attract or repel. Although many substances exhibit some magnetic force, only a few have a sufficiently strong force to be designated as magnets. The Earth itself is akin to a colossal magnet.
Magnets possess two areas where the magnetic force peaks, known as the poles. These poles are opposite on a rectangular bar magnet, labeled the North Pole (north-seeking) and the South Pole (south-seeking).
Magnetism results from the actions of minuscule particles called electrons. Atoms, which form all matter, consist of electrons, neutrons, and protons. Electrons orbit around the nucleus, generating small-scale magnetic forces. In certain materials, numerous electrons align their spins uniformly, leading to a combined magnetic force that emerges as a significant magnet.
Creating a magnet can be achieved by rubbing metal with an established magnet, ensuring the motion is unidirectional to align electrons. Similarly, electric current can produce magnets. As electricity involves electron flow, electrons moving in a wire create a magnetic field similar to electrons spinning around atomic nuclei. This type of magnet is termed an electromagnet.
Nickel, cobalt, iron, and steel are ideal for creating permanent magnets due to their electron configuration. Once magnetized, these metals maintain their magnetic properties indefinitely, known as hard magnets. Meanwhile, some metals exhibit temporary magnetic behavior when near hard magnets, classifying them as soft magnets.
Most elements, such as wood or water, possess very weak magnetic traits. However, magnets strongly attract objects containing metals like iron, nickel, or cobalt. They can also attract or repel other nearby hard magnets because each has two opposing poles: north and south. Opposite poles attract, while like poles repel each other.
Commonly, magnets are produced through powder metallurgy. Different magnet types have varied manufacturing methods. For example, electromagnets are crafted via metal casting techniques, while flexible magnets are formed by plastic extrusion. In plastic extrusion, raw materials are heated, blended, and forced through an opening under pressure. Below is a general guide on magnet manufacturing procedures.
Iron, boron, and neodymium are melted in a furnace devoid of air to avoid chemical reactions. As the alloy cools, it is fragmented into small metal pieces, later pulverized into a fine powder between 3 to 7 microns in diameter. Because the powder can ignite when exposed to oxygen, it must remain shielded from air.
Isostatic compaction or pressing places powdered metal into a mold, with a magnetic force applied to align particles during compaction. Hydraulic pressure then compresses the material close to its required thickness. Typically, pressures from 10,000 to 15,000 psi are utilized. For diverse designs, the powder is sealed in an evacuated container before shaping with gas pressure.
Post-compaction, the powdered metal is transferred to an oven for sintering, where heat is applied to form solid metal pieces. Sintering includes three key stages. Initially, low heat removes moisture and contaminants. Next, a higher temperature close to the alloy's melting point is sustained, allowing particles to bond. Finally, the material cools gradually to complete sintering.
After heating, the annealing phase begins. This involves controlled heating and cooling to eliminate internal stresses, enhancing the material’s strength.
Typically, the sintered magnets undergo machining, including grinding for smooth surfaces or cutting into smaller segments. Given the material's hardness and brittleness, diamond wheels are preferred for slicing and grinding. Precision slicing often reduces further grinding needs, though caution is required to minimize cracks.
In some cases, a shaped diamond grinding wheel achieves precise dimensions, closely matching the intended final shape, termed "near net shape." Excess material is removed in a final machining step, creating a smooth surface where necessary before a protective coating is applied.
After finishing, magnets undergo magnetization to develop an external magnetic field, achieved using a solenoid, configured for different sizes and shapes. The solenoid can include fixtures for specific patterns. Large assemblies might be magnetized together to reduce handling of charged magnets. Substantial magnetizing field requirements are crucial in this process.
All magnet selection aspects must involve both engineering and production discussions. Up until manufacturing completion, the material is merely compressed metal. Although isostatic pressing aligns the powder, no magnetic effect occurs. Aligning the material with a strong electromagnet while powered creates a permanent magnet.
Magnetic separation utilizes a magnet to extract magnetic materials from a mixture efficiently. Effective in separating ferromagnetic minerals like cobalt, iron, or nickel, this method isn't applicable for non-magnetic metals like silver or gold. Various mechanical approaches aid in isolating magnetic elements; magnets within separator drums capture magnetic particles, forming a concentrate.
Magnetic separation is essential in electromagnetic cranes for waste management and shipping, efficiently extracting unwanted metals. Commonly utilized in recycling facilities, this method removes metal impurities and purifies ores. Traditionally, magnetic pulleys, overhead magnets, and drums were prevalent in the industry.
It is particularly beneficial in mining iron due to its magnetic attraction. Within food and pharmaceutical sectors, it removes metal contaminants and enhances product purity, contributing to effective recycling techniques.
Magnets are essential in numerous industries, devices, and technologies, and understanding the different types of magnets helps you choose the best one for your specific use case. Here, we outline the main types of magnets—including both permanent and temporary magnets—as well as their unique properties, manufacturing processes, and common applications. Enhancing your knowledge of magnet types is crucial whether you’re searching for industrial magnets, rare earth magnets, or specialty magnetic solutions for engineering and electronics.
Alnico magnets come in cast, sintered, and bonded forms, with cast alnico magnets being the most common. They are an essential category of permanent magnet alloys composed of nickel (Ni), aluminum (Al), iron (Fe), and cobalt (Co), with minor additions of titanium (Ti) and copper (Cu). Alnico magnets exhibit relatively high coercivity and strong magnetic stability due to the shape anisotropy of the iron (Fe) or cobalt (Co) particles, which are precipitated within a weakly ferromagnetic or non-ferromagnetic nickel-aluminum matrix. After cooling, isotropic alnico magnets are tempered at high temperatures for several hours, enhancing their durability and performance in demanding environments.
Spinodal decomposition is a phase separation process where the final sizes and shapes of particles are determined early in the process. Alnico magnets are known for their excellent temperature coefficients, meaning they experience minimal changes in field output with temperature variations. These magnets can operate at the highest temperatures of any magnet type, making them ideal for high-temperature industrial applications, sensors, and electric guitar pickups.
Demagnetization of the alnicos can be reduced if the working point is improved, such as for making use of a longer magnet than before in order to increase the length to diameter ratio—which is a good rule of thumb guide for Alnico magnets. All external demagnetizing factors must be taken into consideration, however. A large length-to-diameter ratio and a good magnetic circuit may also be required to optimize magnetic performance, especially in magnetic assemblies and custom magnetic solutions.
Bar magnets are rectangular objects made from steel, iron, or other ferromagnetic materials with strong magnetic properties. They are classic examples of permanent magnets and are popular in educational demonstrations and DIY science experiments. They feature two magnetic poles: north and south.
When a bar magnet is suspended freely, it aligns itself such that its north pole points towards the Earth's magnetic north pole, making it an essential tool for simple compasses. Bar magnets can be used to illustrate the concept of magnetic fields and magnetic flux lines, which can be visualized with iron filings.
There are two main types of bar magnets. Cylindrical bar magnets, also known as rod magnets, have a high thickness in diameter, which enhances their magnetic properties. The second type is rectangular bar magnets, which are commonly used in manufacturing and engineering applications due to their greater magnetic strength and consistent field compared to other shapes.
When a bar magnet is broken in half, each piece will still have both a north and a south pole, even if broken into smaller parts multiple times—a property known as magnetic dipole. The magnetic force of a bar magnet is most intense at its poles. When two bar magnets are brought near each other, opposite poles attract, while like poles repel. Bar magnets are effective at attracting ferromagnetic materials like cobalt, nickel, and iron, and are widely used for scientific research, crafts, and small-scale magnetic separation.
Bonded magnets consist of two primary components: a non-magnetic polymer (such as epoxy or nylon) and hard magnetic powder. The powder can be derived from various magnetic materials such as alnico, ferrite, neodymium-iron-boron (NdFeB), cobalt, and iron. Additionally, multiple types of magnetic powders can be combined to create hybrid mixtures for enhanced performance tailored to particular needs. The properties of these powders are meticulously optimized through precise chemical processes and step-by-step manufacturing, ensuring that bonded magnets perform effectively regardless of the materials used.
Bonded magnets provide numerous advantages, as the near net shape manufacturing requires no or minimal finishing operations compared to other metallurgical processes. Value-added assemblies can be made economically in one operation, and these magnets are highly versatile in both shape and function. Some advantages of bonded magnets are that they have excellent mechanical properties and great electrical resistivity when compared with sintered materials. Bonded magnets are available in different sizes, shapes, magnetic orientations, and can achieve multipole magnetization.
Common applications for bonded magnets include motors, sensors, actuators, magnetic couplings, and medical devices. Their ability to be molded into intricate geometries while maintaining reliable magnetic performance makes them ideal for compact or complex electronic assemblies.
Ceramic magnets, also known as ferrite magnets, are a widely used type of permanent magnet and are the most cost-effective compared to other magnet types. Made from iron oxide and strontium carbonate (sometimes barium ferrite), these magnets offer medium magnetic strength and can operate at high temperatures, making them suitable for many industrial and commercial applications. Their key advantages include high corrosion resistance, ease of magnetization, and affordability, making them a popular choice for a wide range of applications, including industrial, technical, and commercial uses. Ceramic magnets come in various grades, with Grade 5 (C5) being commonly used for motors and loudspeakers, and they are available in different shapes such as blocks, rings, discs, and custom-formed parts.
Ferrite magnets can operate at high temperatures, although their magnetic properties decrease as the temperature rises. They require specialized machining skills for precision shaping and must be handled carefully as they are brittle. An advantage of ceramic magnets is their resistance to surface rust, thanks to a protective film of magnetic powder on their surface. They are typically bonded to products using strong adhesives like superglue. However, ceramic magnets are very brittle and can easily break if dropped or subjected to impact, so they require careful handling to avoid damage.
Ceramic magnets are widely used in electrical motors, refrigerator magnets, loudspeakers, magnetic separators, magnetic holding devices, and as components in automotive sensors, anti-theft systems, and measuring instruments due to their balance of performance and low cost.
Electromagnets are magnets whose magnetic field is generated by an electric current. Typically, they consist of a wire wound into a coil of copper or aluminum. When current flows through the wire, it creates a powerful, adjustable magnetic field. This magnetic field vanishes when the current is turned off, classifying electromagnets as temporary magnets. Electromagnets are usually composed of wire turns wound around a magnetic core made from ferromagnetic materials such as iron, nickel, or silicon steel. The core serves to concentrate and direct the magnetic flux, resulting in a more powerful magnet than air-core electromagnets.
Electromagnets offer the advantage of quickly adjusting the magnetic field strength by regulating the electric current, unlike permanent magnets whose magnetic field is constant. However, they require a continuous current supply to maintain their magnetic field and may heat up rapidly, consuming significant amounts of energy. Safety precautions are necessary in high-powered electromagnet systems, as they can discharge large amounts of energy if current is interrupted. Despite these challenges, electromagnets are essential in a wide range of applications: generators, relays, electro-mechanical solenoids, motors, loudspeakers, magnetic separation equipment, maglev trains, MRI machines, transformers, magnetic locks, and in industry for lifting heavy ferromagnetic materials such as iron and steel scrap. Electromagnets attract ferromagnetic materials like nickel, cobalt, and iron. As with most magnets, similar poles repel and opposite poles attract.
Flexible magnets are designed to bend and flex without breaking or sustaining damage. Unlike rigid magnets, these magnets can be deformed, rolled, or bent without losing their magnetic properties, making them ideal for applications where conformability and versatility are key. The flexible magnet shown in Figure 2:6 illustrates this capability. Typically, flexible magnets consist of a synthetic substrate, such as vinyl or rubber, combined with a thin layer of ferromagnetic powder made from ferrite. The substrate is made from a highly pliable material, and when the ferromagnetic powder is applied, it imparts magnetic properties to the entire surface.
Various production methods are used to manufacture flexible magnets, but most involve mixing ferromagnetic powder with a binding agent and then calendaring or extruding the compound to create flexible magnetic sheets and strips. Flexible magnets come in various forms, including sheets of different designs, shapes, and sizes, as well as strips that are thinner and longer than the sheets. These magnets are commonly used in applications such as refrigerator magnets, advertising signage, business card magnets, flexible closures for doors and cabinets, and crafts. They are also widely used in the automotive and construction industries for gaskets, seals, and labeling.
On the market, they are usually sold and packaged in rolls, making them easy to cut and customize. Flexible magnets are versatile with their bendable properties and they can wrap around machines and other surfaces or components, even if the surfaces are not perfectly smooth or flat. Flexible magnets can be cut and shaped into desired forms and sizes—most can be cut with standard scissors or utility knives. Flexible magnets are not affected by drilling; they will not crack but will form holes without damaging the surrounding magnet structure, further enhancing their versatility and ease of installation.
An industrial magnet is a powerful magnet designed for heavy-duty applications across various sectors including manufacturing, recycling, mining, and material handling. These magnets come in multiple shapes and configurations, including electromagnets, permanent magnets, and rare earth magnets, and are known for their diverse grades, pull strengths, and retained residual magnetism. Industrial permanent magnets can be made from materials like alnico, rare earth elements (neodymium or samarium cobalt), or ceramic ferrite. They are crafted from ferromagnetic substances that are magnetized by an external magnetic field and can retain their magnetized state over an extended period, ensuring reliable long-term operation in demanding environments. Industrial magnets feature clearly defined north and south poles where magnetic intensity is strongest.
Samarium-cobalt industrial magnets are known for their ability to withstand high temperatures up to 250 °C. These magnets are highly resistant to corrosion due to their lack of iron content. However, their production is costly because of the high price of cobalt. Despite the expense, samarium-cobalt magnets are valued for their ability to produce extremely strong magnetic fields and are commonly used in applications involving high operating temperatures, such as in industrial motors, sensors, medical equipment, generators, and aerospace technology where stability and precision are crucial.
Alnico industrial magnets are made from a combination of aluminum, cobalt, and nickel, with possible additions of copper, iron, and titanium. Compared to samarium-cobalt magnets, alnico magnets can endure even higher temperatures, up to 525 °C, making them highly heat-resistant. However, they are more susceptible to demagnetization due to their sensitivity to external demagnetizing fields. Industrial electromagnets, on the other hand, are adjustable and can be switched on and off, suitable for applications where controllable magnetic fields are needed, such as electromagnetic cranes and conveyor systems.
Industrial magnets serve a variety of critical functions, such as:
The range of industrial magnet solutions ensures that it’s possible to find the right magnetic technology for your business, whether you need automated handling, increased throughput, or advanced separation efficiency.
Rare earth magnets, especially neodymium magnets (NdFeB), are the strongest type of permanent magnets available. These high-performance magnets are composed of neodymium, iron, and boron, allowing them to produce exceptionally strong magnetic fields—often exceeding 1.4 teslas. Their compact size and powerful attraction make them indispensable for modern industries.
Neodymium magnets are widely used in high-tech and consumer electronics, such as hard disk drives, which leverage their high magnetic energy product for data storage. They are also key in electric motors (EVs, robotics, and power tools), MRI equipment, wind turbine generators, magnetic resonance imaging, and portable electronics. Acoustics benefit from neodymium in loudspeakers, headphones, microphones, and earphones, where small yet powerful magnets deliver superior sound quality. The medical field uses neodymium magnets for magnetic therapy jewelry and precision placement of dental prostheses.
Other applications include anti-lock braking systems (ABS) for vehicles, magnetic closures in security devices, magnetic sensors, and in industrial automation where precise magnetic actuation is needed. Their strength enables miniaturization of components in advanced engineering designs. However, neodymium magnets are sensitive to corrosion and should be coated or plated for long-term durability. For additional insights, visit Neodymium magnets.
This chapter will explore various applications of magnets across different industries and technologies.
Magnets are employed in a wide range of applications across various contexts and purposes. They come in sizes ranging from tiny components to large structures. In everyday life, magnets are integral to many devices; for instance, hard disks in computers use magnetic elements to store and retrieve data. Additionally, magnets are found in televisions, radios, and speakers, playing a crucial role in their operation.
Magnetic stripe technology enables data storage on plastic cards by encoding information into tiny magnetic bits along a stripe on the card. This technology underpins credit and debit cards, significantly reducing cash transactions globally. Known as magstripe technology, it has led to the creation of highly durable cards with robust data integrity. Thanks to magnetic stripe cards, financial institutions and banks can efficiently handle a wide range of card-based transactions and processes.
Magnetic stripes are integral to countless transactions daily and are widely used in various identification cards. Card readers can quickly extract details from these magnetic cards, which are then sent to banks for authorization. However, in recent years, a new technology has increasingly rivaled magnetic card transactions: contactless payment systems. This modern method uses signals from a small chip to transfer transaction details, eliminating the need for a magnetic stripe. Apple Inc. has been a pioneer in advancing contactless payment systems.
In speakers, a small coil of wire and a magnet work together to convert electronic signals into sound vibrations. Similarly, generators utilize magnets to transform mechanical energy into electrical energy. Magnets are also crucial in various mechanical and electrical motors, where they convert electrical energy into mechanical motion.
Magnets play a key role in lifting large metal objects that are too heavy for manual handling, such as in crane operations. They are also used in the separation and filtering of metallic ores from crushed rocks, and in the food processing industry to remove small metal contaminants from grains. These are just a few examples of the diverse applications of magnets.
Several significant drawbacks are associated with different types of magnets. Ferrite magnets, for instance, are produced through molding and sintering, making them challenging to machine. As a result, ferrite magnets typically have simple shapes and large dimensional tolerances. Samarium Cobalt magnets are quite brittle, which complicates the processing of small-sized products. Additionally, many magnets suffer from degradation at very high temperatures. Neodymium magnets, on the other hand, are prone to corrosion and thus require protective coatings to maintain their durability.
Magnets come in different forms, from simple bar magnets to very large permanent industrial magnets. Every type of magnet has two poles and even if they are cut in half, they will still have these two poles. Magnets are of great importance to the human community, but however they can be demagnetized at excessive temperatures and pressure.
An Alnico magnet is a permanent magnet made by combiming aluminum, nickel, iron, cobalt, and other elements. They come in isotropic, non-directional, or anisotropic, mono-directional, form...
A ceramic magnet, also known as a ferrite magnet, is a permanent magnet made by combining iron oxide and strontium carbonate. They are a man made magnet produced by heating the two elements to...
Flexible magnets are composite materials with magnetic components arranged in an elastomer matrix. They are made from a combination of rubber polymer resin and ferrite powder by forming it through...
A Neodymium (Nd-Fe-B) magnet is a common rare earth magnet composed of neodymium (Nd), iron (Fe), boron (B), and transition metals. They have superior performance in applications because of their strong...
Power supplies are electrical circuits and devices that are designed to convert mains power or electricity from any electric source to specific values of voltage and current for the target device...
An AC power supply is a type of power supply used to supply alternating current (AC) power to a load. The power input may be in an AC or DC form. The power supplied from wall outlets (mains supply) and...
A bowl feeder is a mechanism for supplying small parts and components to a production line or for sorting bulk items for rapid use. A self contained bowl feeder system has a bowl that sets on a spring loaded base that moves vertically...
A DC DC power supply (also known as DC DC Converter) is a kind of DC power supply that uses DC voltage as input instead of AC/DC power supplies that rely on AC mains supply voltage as an input...
A DC power supply is a type of power supply that gives direct current (DC) voltage to power a device. Because DC power supply is commonly used on an engineer‘s or technician‘s bench for a ton of power tests...
Electric transformers are static electrical machines that transform electric power from one circuit to the other without changing the frequency. An electrical transformer can increase or decrease the voltage with...
An electromagnetic interference or EMI Filter is an electrical device or circuit that filters specific unwanted frequencies in power lines or offending frequencies that are detrimental to a system. They receive AC or main power...
By definition a power supply is a device that is designed to supply electric power to an electrical load. An electrical load refers to an electrical device that uses up electric power. Such a device can be anything from...
An isolation transformer, just like typical transformers, is a non-moving device that transmits electrical energy from one circuit to another without requiring any physical contact. It works on the idea of magnetic...
Power transformers are electrical instruments used in transmitting electrical power from one circuit to another without changing the frequency. They operate by the principle of electromagnetic induction. They are used in transmitting electrical power between...
A programmable power supply is a method for controlling output voltage using an analog or digitally controlled signal using a keypad or rotary switch from the front panel of the power supply...
An electrical transformer is a passive machine that transfers electrical energy from one circuit to another using a magnetic flux to induce an electromotive force. Transformers are used to increase (step-up) or decrease (step-down) voltages without changing the frequency of the electric current...
A toroidal transformer is a type of electrical transformer constructed with a torus or donut-shaped core. Its primary and secondary windings are wound across the entire surface of the torus core separated by an insulating material...
Vibratory conveyors are material-handling equipment used to transport fine to coarse-grained bulk materials. These vibratory conveyors are strong conveying equipment utilized for bulk commodities with fine to coarse graininess...
Vibratory feeders are short conveyors used to transport bulk materials utilizing a controlled vibratory force system and gravity. The vibrations impart a combination of horizontal and vertical acceleration through tossing, hopping, or sliding-type of action to the materials being handled...
A vibratory screening is a process that separates bulk solid materials from solids and slurries using inertial vibration that causes various sizes of particles to pass through openings in a screen or...
Electronically operated equipment depends on power transformers to convert electrical currents into voltage. Current transformers store and transport energy through power lines and grids...