Alnico Magnets
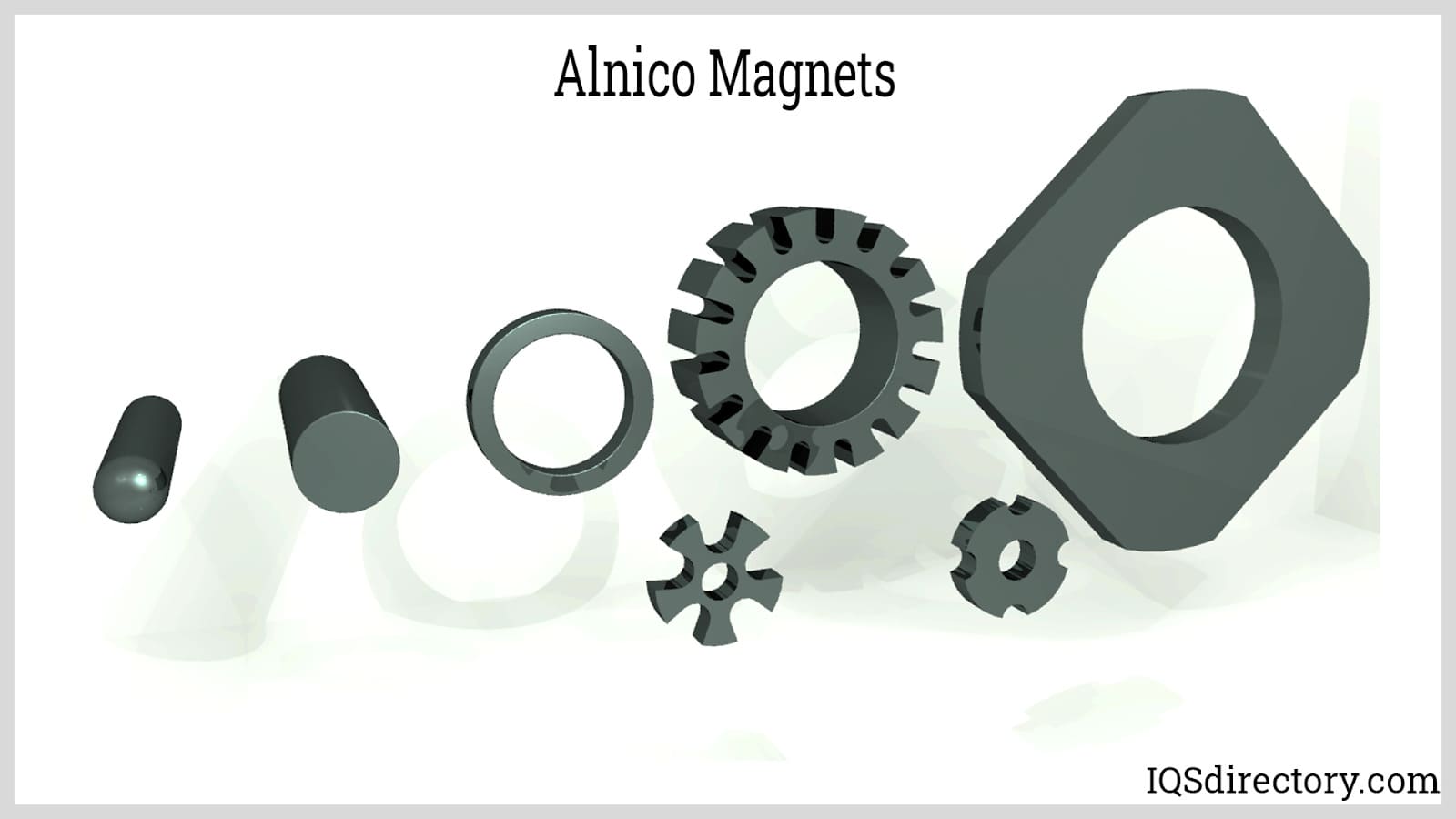
An Alnico magnet is a permanent magnet made by combiming aluminum, nickel, iron, cobalt, and other elements. They come in isotropic, non-directional, or anisotropic, mono-directional, form...
Please fill out the following form to submit a Request for Quote to any of the following companies listed on
This article takes an in depth look at ceramic magnets and their use.
You will learn more about topics such as:
A ceramic magnet, often referred to as a ferrite magnet, is a type of permanent magnet formed by combining iron oxide with strontium carbonate. This human-made magnet is crafted by heating the mixture to temperatures surpassing 2000° F, initiating a chemical transformation that converts the components into a ferrite substance exhibiting a magnetic field.
Ceramic magnets provide an economical substitute for natural magnets and are extensively utilized in both consumer goods and industrial applications. These magnets are the most widely used worldwide, featuring in about 75% of magnet-based products. Their cost-effectiveness is further enhanced by their excellent corrosion resistance.
During the 1960s, there was a push to find a more affordable substitute for metal magnets. This period marked the early days of the rapid expansion in electronics, where metal magnets were driving up the costs of manufacturing recording devices. The introduction of ceramic magnets quickly gained popularity because of their cost-effectiveness, durability against corrosion, and stability in maintaining magnetism.
Ceramic magnets can be found in DC motors, magnetic separators, magnetic resonance imaging scanners, and various forms of sensors. The base element of ceramic magnets is ferrite, which combines iron oxide and strontium carbonate.
The initial stage in creating ceramic magnets involves the calcination of iron oxide powder and strontium carbonate. Calcination is a high-temperature industrial process used to alter the chemical and physical characteristics of solid materials by exposing them to intense heat. This process typically involves minerals, metals, and various ores.
During calcination, materials are heated to temperatures exceeding 1800°F (1000°C). For ceramic magnets, this process yields a metallic oxide compound, SrO-6 (Fe2O3). Depending on the specific type of ceramic magnet, additional elements like cobalt or lanthanum may be included to improve the performance of the final product.
Milling aims to reduce the fine powder into even smaller particles, sometimes as small as two micrometers (µ), which is significantly smaller than a human hair. These minute particles each possess their own magnetic domain.
A common form of milling used to mill the ferrite powder is a ball mill, a type of grinding machine. Traditional milling includes the use of rotary cutters. To transform ferrite powder into finer ferrite powder, a ball mill is used that uses metal balls to grind the powder.
A ball mill consists of a rotating chamber, which can be oriented either vertically or horizontally. Inside this chamber, metal balls collide with the ferrite material, repeatedly striking it and grinding it down to smaller particle sizes.
Before the very fine powder can proceed to the compacting stage, it may be slightly liquefied to create a slurry. This process involves adding water to transform the powder into a mud-like consistency. The slurry is carefully prepared to achieve the precise consistency needed for the compacting process.
Compacting is the stage where the ceramic magnet takes its final shape. This process involves pressing, shaping, and molding the wet slurry into various sizes and configurations of the magnet. During compacting, an external magnetic field is applied to align the anisotropic magnetic properties of the material.
If the material is not processed into a slurry and instead dry-pressed, applying the magnetic field will result in an isotropic material with weaker magnetic properties.
Sintering, or frittage, is a process used to create a solid and durable mass through the application of heat and pressure. During this stage, the shaped magnets are gradually heated from 482°F (250°C) to 1652°F (900°C). The duration of the heating process affects the magnet's quality, with higher-quality magnets requiring a longer heating time, which can range from 20 to 36 hours.
Although sintering involves extremely high temperatures, they are not sufficient to melt or liquefy the material. Instead, the process facilitates the diffusion of atoms across particle boundaries, resulting in a solidified mass.
The goal of sintering is to enhance the strength and integrity of ceramic magnets. As the temperature rises, the tiny gaps between particles are reduced, causing the material to compact tightly together.
In the diagram below, the round red circles illustrate the ferrite particles at various stages: as powder, in the mixture, and after sintering.
Once sintering is complete, the magnets are cooled to room temperature. They are then ground and shaped to meet the required specifications. During grinding, millimeters of material are gradually removed with each pass of the grinding tool until the desired dimensions are reached. For enhanced precision and accuracy, a diamond cutter is used to finalize the cutting process.
Coating or plating ceramic magnets is an additional step taken to protect them and enhance their functionality. Various materials can be used for this coating process to provide different protective and performance benefits.
Nickel-copper coating, or nickel coating, is completed in three layers that include a layer of nickel, a layer of copper, and a layer of nickel.
Epoxy provides a durable coating that offers effective protection against corrosion.
Zinc is a cost-effective coating material that guards against corrosion and serves as a natural barrier to moisture.
PTFE, commonly known as Teflon, enhances the impact resistance of ceramic magnets, making them less likely to break.
Gold is used to protect the skin of users and is typically applied as 22-carat gold. Gold-coated ceramic magnets are often utilized in magnetic therapy.
The five coatings mentioned are just a few options available. The choice of coating usually depends on the specific application for which the ceramic magnet is intended.
Despite their numerous applications, ceramic magnets are generally categorized into a few basic types. The manufacturing process allows for a wide range of shapes and sizes, from small blocks to puck-like forms. This versatility, combined with their affordability, contributes to their widespread use.
Ceramic magnets are classified based on their magnetic properties and intended applications. They are typically grouped into five categories: soft, permanent, spin, moment, and piezomagnetic magnets.
Hard ceramic magnets have high coercivity, making them resistant to demagnetization and ensuring their magnetic properties remain stable. Their strong and permanent magnetic field makes them well-suited for applications where durability and reliability are crucial. Due to their robustness, hard ceramic magnets are often used in critical telecommunications equipment where failure is not an option.
Ceramic moment magnets exhibit rectangular hysteresis loops. They become magnetized and reach saturation when exposed to a small magnetic field. After the external field is removed, these magnets retain their magnetization. Made from magnesium manganese ferrite and lithium manganese ferrite, moment magnets are crucial components in the memory cores of computers.
Permanent ceramic magnets possess a uniaxial anisotropic hexagonal structure that allows them to maintain strong magnetic properties over long periods. Their hardness contributes to their enduring and consistent strength. These magnets are commonly used in refrigerators, microphones, automotive applications, and cordless devices due to their reliable and long-lasting magnetic field.
Piezomagnetic ceramic magnets exhibit a change in dimensions along the direction of the magnetic field when magnetized. These materials generate a magnetic field in response to mechanical stress or deformation. This effect occurs due to deficiencies or distortions in the material's crystal structure.
Piezomagnetic ceramic magnets are utilized in transducers and magnetostrictive components for ultrasound applications.
Soft ceramic magnets are ferrimagnetic and feature a cubic crystal structure, making them easy to magnetize and demagnetize. These magnets have a wide range of applications, are produced in large quantities, and offer high performance. They are commonly used in filters, transformers, radio cores, and tape and video heads.
Soft ceramic magnets are primarily classified by their low coercivity. Coercivity is assessed through their magnetic hysteresis loop or magnetization curve, which measures the ease with which the magnet can be magnetized and demagnetized.
Spin ceramic magnets operate on the principle of rotary magnetism, involving two perpendicular stable magnetic fields and an electromagnetic wave magnetic field. The interaction of these fields results in continuous rotation. While some metal magnets exhibit spin magnetism, their performance is limited by eddy current losses, making ceramic magnets a more viable option for sustaining spin magnetism.
Ceramic magnets are utilized in a diverse range of products, including speakers, recorders, and large communication systems. Their affordability and versatility make them an excellent choice for providing magnetism. Ceramic magnets are primarily categorized into soft and hard types, with hard magnets exhibiting high coercivity and soft magnets having low coercivity.
Before the advent of ceramic magnets in the 1960s, cost-effective options for generating a magnetic field were limited, as most magnets were metal-based. The introduction of ceramic magnets significantly reduced the cost of many products and made them widely accessible.
In a speaker, the voice coil moves in and out in response to the audio signal, generating a magnetic field. A ceramic magnet positioned near the voice coil helps regulate its movement, influencing the overall sound quality of the speaker. To achieve superior sound quality, ceramic magnet speakers are often heavier, which enhances their punch and clarity.
Direct current (DC) motors utilize the magnetic field's force to generate rotational motion. An armature within the magnetic field rotates due to this force, producing DC current. In a permanent ceramic magnet DC motor, a permanent ceramic magnet creates the necessary magnetic field.
Permanent ceramic magnet motors are commonly found in automobile starters, windshield wipers, washers, and air conditioners. These motors are ideal for applications where speed control is not required, as speed regulation typically involves adjusting the magnetic field.
MRI scanners utilize magnetic fields and radio waves to create detailed images of the human body, aiding in medical diagnoses. They come in different sizes and configurations, with some models featuring side openings to alleviate feelings of claustrophobia.
The core component of an MRI system is its extremely strong magnet, which generates a stable magnetic field along the length of the MRI tube. This uniform magnetic field ensures clear and high-quality imaging of the internal structures of a patient's body.
Small motors do not require a battery. They generate power for the spark plugs using a magneto. The voltage from the magneto creates a spark that jumps the spark plug gap that ignites the engine’s fuel. The function of the magneto is to supply current to the ignition system and produce voltage for the spark plugs. For the motor to work properly, the magneto must be precisely placed in relation to the flywheel to generate the correct magnetic field.
A magneto integrates the functions of a distributor and a generator, differing from a traditional distributor by generating its own spark without requiring external voltage. In this system, rotating ceramic magnets disrupt the electrical field, which induces current in the primary windings, as illustrated in the image below.
The term "ceramic magnet" refers to a broad category of 27 different types, each designed for specific applications, from operating MRI scanners to starting lawnmowers. Their resistance to high temperatures and corrosion, combined with their affordability, makes them a popular choice.
The most frequently used grades of ceramic magnets are C1, C5, and C8, known for their straightforward construction due to their manufacturing process. The variations between these grades are based on their ferromagnetic properties.
The traditional “C” labeling system for ceramic magnet grades has been replaced by a “Y” system. In this new system, grades are indicated by the letter Y followed by a number or a combination of numbers and letters. The numbers after the "Y" denote the magnet’s energy, while the letters provide additional details about its characteristics.
The “Y” labeling system is gradually becoming the standard for ceramic magnets and is now widely adopted in most countries. However, the transition has been gradual, so the “C” labeling system remains common in the United States.
C1 ceramic magnets are small and relatively weak, designed to fit into compact spaces. With an operating temperature of up to 480°F (249°C), they are well-suited for high-temperature environments. These magnets are commonly used in speakers, small motors, and reed switches.
C5 ceramic magnets are among the most commonly used ceramic magnets and are magnetized according to their orientation. While they offer broad applicability, they can be demagnetized, which limits their use in certain applications.
C8 ceramic magnets are valued for their high energy and strong resistance to demagnetization. They are frequently employed in applications where the magnet's length could be an issue or where there is a risk of demagnetization.
Ceramic magnets C1, C5, and C8 are among the most commonly used and can be found in a wide range of products. However, they are just a few of the 27 different types available from manufacturers. The list below highlights some of the more popular ceramic magnets, along with their properties and characteristics.
Grades of Ceramic Magnets | |||||
---|---|---|---|---|---|
Grade | Br (Kg) | HcB (KOe) | Hci (KOe) | BHmax (MGOe) | T max |
C | 2.30 | 1.86 | 3.50 | 1.00 | 250C / 482F |
C | 3.30 | 2.40 | 2.50 | 3.40 | 250C / 482F |
C7 | 4.30 | 3.23 | 4.00 | 2.75 | 250C / 482F |
C8 | 5.30 | 2.95 | 3.05 | 3.50 | 250C / 482F |
C8B | 6.30 | 2.91 | 2.96 | 4.12 | 250C / 482F |
C9 | 7.30 | 3.52 | 4.01 | 3.32 | 250C / 482F |
C10 | 8.30 | 3.62 | 3.51 | 3.82 | 250C / 482F |
C11 | 9.30 | 2.51 | 2.56 | 4.32 | 250C / 482F |
The magnetic field describes the force exerted by a magnet and is characterized by its poles, which are either attracting or repelling. The vector method represents a magnetic field with dots on a grid, where each vector points in the direction of the magnetic force and its length corresponds to the strength of the field. Alternatively, the field lines method visualizes the magnetic force pattern using smooth, curved lines to illustrate the field's behavior.
Two key parameters used to measure a magnetic field are its strength and direction. Among these, direction is the simpler parameter to measure. Determining the strength of a magnetic field is more challenging and has been possible for only about 30 years.
A magnetic field arises when a charge is in motion. The stronger the charge and its movement, the more intense the magnetic field. Electromagnetic force, which includes magnetism and magnetic fields, is one of the four fundamental forces of nature.
Magnetization directions vary and are primarily limited by the magnet's size. As illustrated in the images below, magnetization can be axial, running along the axis of the magnet, or diametrical, extending across its length. Additionally, there are multiple pole configurations, including multipole axial and multipole diametrical magnetizations.
The terms axial and diametrical describe magnetization directions in cylindrical, disk, ring, and arc-shaped magnets. In axial magnetization, the magnetic force aligns with the end planes of the magnet, whereas in diametrical magnetization, the field is oriented along the inner and outer arcs.
Magnetic fields are classified into two categories: isotropic and anisotropic. Isotropic magnets have a random magnetization direction, resulting in generally weaker magnetic fields. In contrast, anisotropic magnets have a specific, predetermined magnetization direction, which provides them with a stronger magnetic force.
The distinction between isotropic and anisotropic magnets is clearly illustrated in the image below. Isotropic magnetization appears scattered and random, while anisotropic magnetization is more directional and uniform.
Since their invention, ceramic magnets have found a growing number of applications. They are permanent magnets known for their durability and strength, largely due to their high magnetic permeability.
Approximately 75% of all magnets globally are ceramic magnets. Their widespread use can be attributed to several factors, with their low cost being a primary reason.
The most frequently highlighted advantage of ceramic magnets is their cost, which is significantly lower compared to other types of magnets. The production process for ceramic magnets is more efficient, and their magnetic field strength often exceeds that of natural magnets. Their affordability primarily stems from their composition, as they are made from nonmetallic materials.
The effectiveness of a magnet is assessed by its ability to retain magnetism under challenging conditions. While many magnets can demagnetize due to vibrations or high temperatures, ceramic magnets are notably more resilient. They can endure extreme temperatures and still maintain their magnetization.
Ceramic magnets exhibit remarkable magnetic permanence even in the harshest environments. Their resistance to electrical exposure makes them particularly suitable for use in DC motors.
The combination of iron oxide and strontium carbonate in ceramic magnets provides inherent corrosion resistance. The natural properties of these materials are retained in the magnets, making them highly resistant to corrosion. This quality is essential for their use in industrial and manufacturing settings.
Once a ceramic magnet is magnetized, it remains nearly impossible to demagnetize. This durability is crucial for applications that rely on the consistent performance of magnets.
Beyond their ease of magnetization, ceramic magnets can be magnetized in various directions, making them versatile for a wide range of applications.
Because ceramic magnets are made from compacted powdered materials, they can be manufactured in virtually any shape, size, or configuration. This versatility allows ceramic magnets to be used in a diverse range of applications, from small toys to large MRI scanners.
An Alnico magnet is a permanent magnet made by combiming aluminum, nickel, iron, cobalt, and other elements. They come in isotropic, non-directional, or anisotropic, mono-directional, form...
Flexible magnets are composite materials with magnetic components arranged in an elastomer matrix. They are made from a combination of rubber polymer resin and ferrite powder by forming it through...
Magnets are materials that exert a noticeable force on other materials without physically contacting them. This force is called a magnetic force. The magnetic force can either attract or repel. Most known materials...
A Neodymium (Nd-Fe-B) magnet is a common rare earth magnet composed of neodymium (Nd), iron (Fe), boron (B), and transition metals. They have superior performance in applications because of their strong...
Power supplies are electrical circuits and devices that are designed to convert mains power or electricity from any electric source to specific values of voltage and current for the target device...
An AC power supply is a type of power supply used to supply alternating current (AC) power to a load. The power input may be in an AC or DC form. The power supplied from wall outlets (mains supply) and...
A bowl feeder is a mechanism for supplying small parts and components to a production line or for sorting bulk items for rapid use. A self contained bowl feeder system has a bowl that sets on a spring loaded base that moves vertically...
A DC DC power supply (also known as DC DC Converter) is a kind of DC power supply that uses DC voltage as input instead of AC/DC power supplies that rely on AC mains supply voltage as an input...
A DC power supply is a type of power supply that gives direct current (DC) voltage to power a device. Because DC power supply is commonly used on an engineer‘s or technician‘s bench for a ton of power tests...
Electric transformers are static electrical machines that transform electric power from one circuit to the other without changing the frequency. An electrical transformer can increase or decrease the voltage with...
An electromagnetic interference or EMI Filter is an electrical device or circuit that filters specific unwanted frequencies in power lines or offending frequencies that are detrimental to a system. They receive AC or main power...
By definition a power supply is a device that is designed to supply electric power to an electrical load. An electrical load refers to an electrical device that uses up electric power. Such a device can be anything from...
An isolation transformer, just like typical transformers, is a non-moving device that transmits electrical energy from one circuit to another without requiring any physical contact. It works on the idea of magnetic...
Power transformers are electrical instruments used in transmitting electrical power from one circuit to another without changing the frequency. They operate by the principle of electromagnetic induction. They are used in transmitting electrical power between...
A programmable power supply is a method for controlling output voltage using an analog or digitally controlled signal using a keypad or rotary switch from the front panel of the power supply...
An electrical transformer is a passive machine that transfers electrical energy from one circuit to another using a magnetic flux to induce an electromotive force. Transformers are used to increase (step-up) or decrease (step-down) voltages without changing the frequency of the electric current...
A toroidal transformer is a type of electrical transformer constructed with a torus or donut-shaped core. Its primary and secondary windings are wound across the entire surface of the torus core separated by an insulating material...
Vibratory conveyors are material-handling equipment used to transport fine to coarse-grained bulk materials. These vibratory conveyors are strong conveying equipment utilized for bulk commodities with fine to coarse graininess...
Vibratory feeders are short conveyors used to transport bulk materials utilizing a controlled vibratory force system and gravity. The vibrations impart a combination of horizontal and vertical acceleration through tossing, hopping, or sliding-type of action to the materials being handled...
A vibratory screening is a process that separates bulk solid materials from solids and slurries using inertial vibration that causes various sizes of particles to pass through openings in a screen or...
Electronically operated equipment depends on power transformers to convert electrical currents into voltage. Current transformers store and transport energy through power lines and grids...