Alnico Magnets
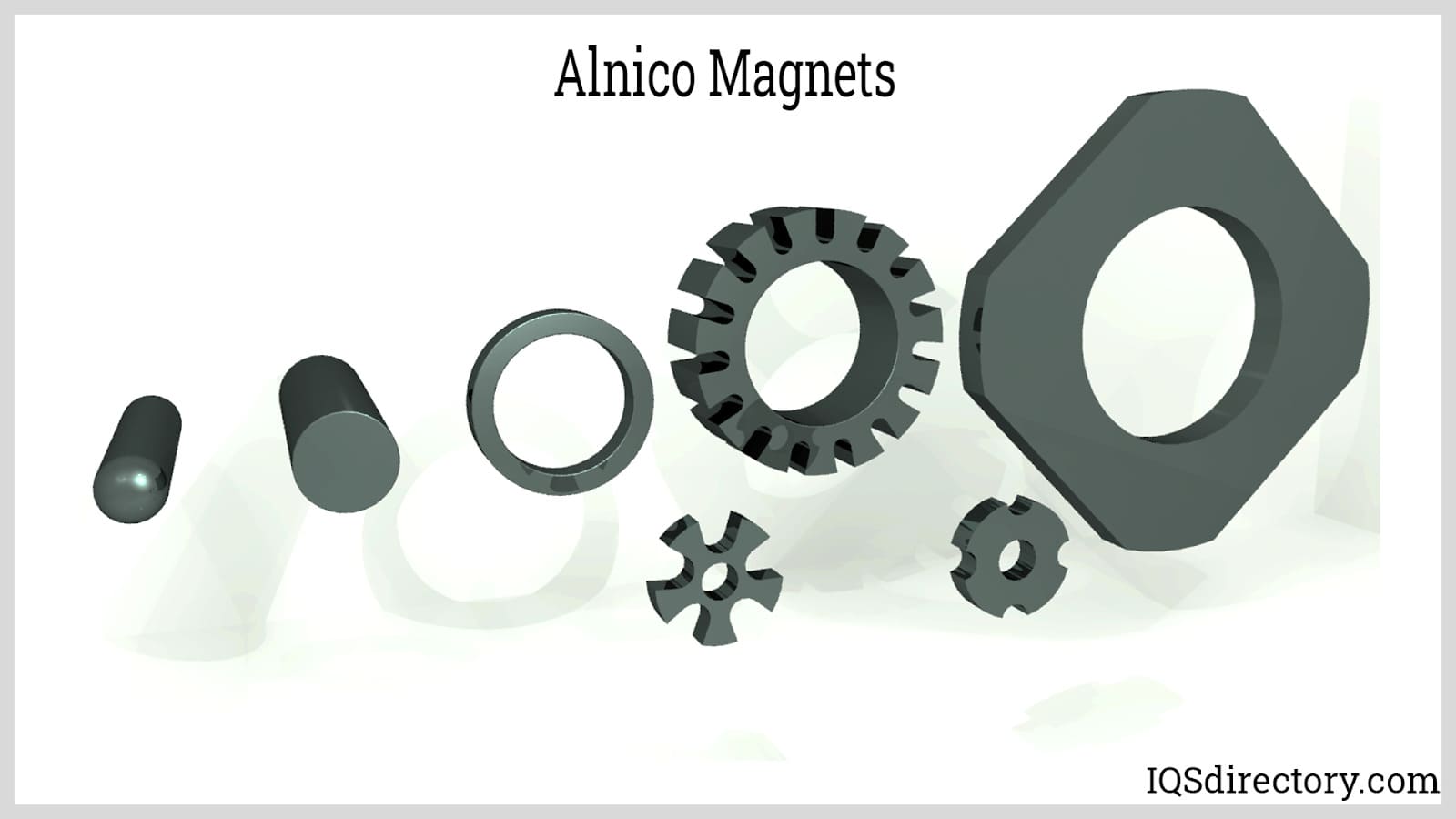
An Alnico magnet is a permanent magnet made by combiming aluminum, nickel, iron, cobalt, and other elements. They come in isotropic, non-directional, or anisotropic, mono-directional, form...
Please fill out the following form to submit a Request for Quote to any of the following companies listed on Neodymium Magnets .
This includes everything you ever wanted to know about neodymium magnets and their use.
You will learn:
Neodymium magnets, often abbreviated as Nd-Fe-B magnets, are highly powerful rare earth magnets crafted from an alloy that includes neodymium (Nd), iron (Fe), boron (B), and additional transition metals. They are renowned for their remarkable magnetic field intensity, reaching up to 1.4 teslas (T), which enables exceptional performance across numerous applications due to their significant magnetic flux density.
The manufacture of neodymium magnets involves two primary techniques: sintering and bonding. Since their debut in 1984, these magnets have dominated the market as the most prevalent type due to their impressive strength and efficiency.
In its pure state, neodymium is ferromagnetic, but it only becomes magnetized at temperatures that are exceedingly low. However, when alloyed with metals like iron, neodymium achieves magnetization at room temperature.
The category of rare earth magnets includes neodymium and samarium cobalt types. Before neodymium magnets revolutionized the industry, samarium cobalt magnets (SmCo) were predominant. However, neodymium magnets have largely replaced them due to the high costs associated with producing samarium cobalt magnets.
Despite being less potent than neodymium magnets, samarium cobalt magnets boast a greater tolerance for high temperatures and excellent corrosion resistance, making them ideal for tough environments and situations where robustness is a priority.
Neodymium magnets are renowned for their impressive strength relative to their size. This strength arises from the alignment of atomic dipoles when a magnetic field is applied, creating what is known as the magnetic hysteresis loop. Even after the magnetic field is removed, some alignment remains in the magnetized neodymium.
Grades of neodymium magnets reflect their magnetic strength, with higher grades indicating stronger magnets. These grades are expressed in mega gauss Oersteds (MGOe), representing the peak of their BH Curve.
The "N" grading scale starts at N30 and extends to N52, though N52 is rarely used except in specific applications. A grade may be followed by letters like SH, which denote the magnet's coercivity (Hc). A higher Hc indicates the magnet can withstand higher temperatures without losing its magnetic properties.
Previously, N52 was the strongest neodymium magnet, but it has been surpassed by N55, which is 6% stronger. N55 magnets are used where powerful magnets are needed in compact spaces.
The chart below provides details on the most commonly used grades of neodymium magnets today.
Nxx | NxxM | NxxH | NxxSH | NxxUH | NxxEH |
N30 | N30M | N30H | N30SH | N28UH | N28EH |
N33 | N33M | N33H | N33SH | N30UH | N30EH |
N35 | N35M | N35H | N35SH | N33UH | N33EH |
N38 | N38M | N38H | N38SH | N35UH | N35EH |
N40 | N40M | N40H | N40SH | N38UH | N38EH |
N42 | N42M | N42H | N42SH | N40UH | N33VH |
N45 | N45M | N45H | N45SH | N33AH | |
N48 | N48M | N48H | |||
N50 | N50M | ||||
N52 |
The approximate maximum working temperature for each grade of neodymium magnet is provided below. The "XX" represents the maximum energy product in MGOe.
Neodymium Grade | Max Temp |
Nxx 12000 Oe | 80 C/175 F |
NxxM 14000 Oe | 100 C/212 F |
NxxH 17000 Oe | 120 C/248 F |
NxxSH 20000 Oe | 150 C/302 F |
NxxUH 25000 Oe | 180 C/356 F |
NxxEH 30000 Oe | 200 C/392 F |
NxxVH 35000 Oe | 230 C/446 F |
NxxAH 35000 Oe | 230 C/446 F |
When neodymium is exposed to a magnetic field, its atomic dipoles align. Once the magnetic field is removed, part of this alignment persists, resulting in magnetized neodymium. Remanence refers to the residual flux density that remains when the external magnetic field decreases from saturation to zero. Higher remanence indicates higher flux density. Neodymium magnets typically have a flux density ranging from 1.0 to 1.4 T.
The remanence of neodymium magnets depends on their manufacturing process. Sintered neodymium magnets exhibit a flux density of 1.0 to 1.4 T, whereas bonded neodymium magnets have a flux density of 0.6 to 0.7 T.
Once neodymium magnets are magnetized, they retain some level of magnetization even when the external magnetic field is removed. To return to a state of no magnetization, an opposing magnetic field must be applied. This property is known as coercivity, which measures a magnet’s resistance to being demagnetized. Essentially, coercivity indicates how much external magnetic force is needed to reduce a magnet's magnetization to zero.
Coercivity is quantified in units such as oersteds (Oe) or ampere turns per meter (A/m), denoted as Hc. The coercivity levels of neodymium magnets vary based on their manufacturing method. For sintered neodymium magnets, the coercivity ranges from 750 Oe to 2000 Oe, whereas bonded neodymium magnets have coercivity values between 600 Oe and 1200 Oe.
Magnetic energy density is defined as the product of the peak flux density and the magnetic field strength. This represents the quantity of magnetic flux per unit area. It is measured in teslas in the SI system and in gauss, with flux density denoted by the symbol B. In SI units, magnetic flux density is the combined effect of the external magnetic field H and the magnetic polarization J of the material.
Permanent magnets have a B field in their core and surroundings. The direction of the B field‘s strength is attributed to the points inside and outside the magnet. A compass needle in a B field of a magnet points itself toward the field direction.
Determining the flux density for various magnetic shapes isn't straightforward. While complex calculations require specialized computer software, simpler shapes can be evaluated using basic formulas.
The strength of a magnetic field is typically gauged in Gauss or Teslas, which reflect the field's density. A gaussmeter is used to measure the flux density of a magnet. For neodymium magnets, the flux density is generally up to 6000 Gauss or lower due to their linear demagnetization curve.
The Curie temperature, or Curie point, refers to the specific temperature at which a magnetic material transitions to a paramagnetic state, altering its magnetic characteristics. In ferromagnetic materials, the magnetic atoms align to enhance each other's magnetic fields. As the Curie temperature is approached, this alignment is disrupted, affecting the material's magnetic properties.
Coercivity tends to rise with temperature, but for neodymium magnets, it decreases as the temperature approaches the Curie point, typically around 320°C or 608°F. Beyond this temperature, neodymium magnets lose their magnetism, which differs from simply surpassing their maximum operating temperature.
Despite their strength, neodymium magnets can experience significant changes in atomic structure when exposed to extreme temperatures. Prolonged high temperatures, starting at about 80°C or 176°F, can lead to a total loss of their magnetic properties.
Neodymium magnets are produced through two primary methods: sintering and bonding. The final characteristics of the magnets depend on the manufacturing process used, with sintering generally providing superior properties compared to bonding.
To create neodymium magnets, Neodymium, Iron, and Boron are carefully measured and placed in a vacuum induction furnace to form an alloy. Additional elements like cobalt, copper, gadolinium, and dysprosium may be included to enhance specific properties such as corrosion resistance. The alloy is heated using electrical eddy currents in a vacuum environment to prevent contamination. The composition of the neodymium alloy can vary depending on the manufacturer and the grade of the magnet.
The molten metal is solidified into blocks, which are then processed through jet milling in a nitrogen and argon environment to produce a fine micron-sized powder. This neodymium powder is subsequently loaded into a hopper for compression.
The powder is compacted into a mold that is slightly oversized compared to the final shape using a technique called upsetting, conducted at approximately 725°C. The extra size of the mold accommodates for material contraction during the sintering phase. During this compaction process, the material is subjected to a magnetic field and then placed into a secondary mold to be shaped further, ensuring that the magnetization aligns with the pressing direction. Some techniques involve using fixtures that generate magnetic fields during pressing to better orient the particles.
Prior to removing the pressed magnet, it is exposed to a demagnetizing pulse to ensure it remains in a demagnetized state, resulting in a "green" magnet that is fragile and exhibits suboptimal magnetic characteristics.
Sintering, also known as frittage, consolidates and shapes the green magnet by applying heat below its melting point, thus imparting the final magnetic characteristics. This process is conducted under strict control in an inert, oxygen-free environment to prevent oxidation, which could impair the magnet's performance. The material is heated up to 1080°C, just shy of its melting point, to encourage the particles to bond together.
A rapid cooling process, or quenching, is then employed to quickly lower the temperature of the magnet. This helps to minimize the formation of phases that could degrade the alloy's magnetic properties.
After sintering, the magnets are shaped to precise specifications using diamond or wire cutting tools for grinding.
Neodymium is highly susceptible to oxidation and corrosion, which can impair its magnetic properties. To safeguard against this, the magnets are coated with materials such as plastic, nickel, copper, zinc, or tin.
Even though the magnet has a specific direction of magnetization, it remains unmagnetized until it is briefly subjected to a powerful magnetic field generated by a wire coil surrounding it. This magnetization process utilizes capacitors and high voltage to create a strong current.
Digital measuring projectors are used to check the dimensions, while x-ray fluorescence technology is employed to verify the thickness of the coating. Additional tests are performed to assess the coating's quality and durability. The BH curve is analyzed using a hysteresis graph to ensure that the magnet achieves full magnetization.
Bonding, also known as compression bonding, involves pressing a blend of neodymium powder and an epoxy binder. This mixture consists of 97% magnetic material and 3% epoxy.
The blend is either compressed in a press or extruded and then cured in an oven. This method allows for the creation of magnets in intricate shapes and configurations due to the pressing or extrusion process. Compression bonding results in magnets with precise tolerances and eliminates the need for further processing.
Compression bonded magnets are isotropic and can be magnetized in any direction, which includes multi-polar configurations. The epoxy binding makes the magnets strong enough to be milled or lathed but not be drilled or tapped.
Radially oriented neodymium magnets represent the latest advancement in magnet technology. Although the technique for creating radially aligned magnets has been known for years, it was previously not cost-effective. Recent technological advancements have optimized the production process, making these magnets more accessible to manufacture.
There are three primary methods for producing radially aligned neodymium magnets: anisotropic pressure molding, hot pressing with backward extrusion, and radial rotating field alignment.
The sintering process plays a crucial role in ensuring the magnet's structure is free from weak points.
A distinctive feature of radially oriented magnets is their magnetic field direction, which extends around the magnet's perimeter. In this arrangement, the south pole is located on the inner side of the ring, while the north pole is positioned on the outer edge.
Radially oriented neodymium magnets exhibit anisotropic properties, with magnetization extending from the center of the ring outward. This radial magnetization enhances the magnet's strength and allows for various configurations.
These radially aligned neodymium ring magnets find applications in synchronous motors, stepping motors, and DC brushless motors across industries such as automotive, computing, electronics, and communications.
Since their introduction in the early 1980s, neodymium magnets have become the most prevalent type among various magnets. They are utilized in numerous everyday items, including disk drives and magnetic components in cars and airplanes. Neodymium magnets can be manufactured in a range of sizes while maintaining their original magnetic strength.
In the demonstration shown below, the conveyor belt is equipped with neodymium magnets arranged with alternating poles facing outward. This configuration provides a strong magnetic grip. Objects that are not magnetic will fall off, while ferromagnetic materials are attracted and collected in a bin.
Hard drives contain tracks and sectors filled with magnetic cells. These cells are magnetized to store data when information is written to the drive.
Neodymium magnets are employed in water treatment systems to help mitigate scaling caused by hard water, which contains high levels of calcium and magnesium. In magnetic water treatment, water flows through a magnetic field that aims to capture and reduce scale buildup. While this technology has not yet been universally accepted as fully effective, there have been some promising results.
A reed switch is an electrical switch operated by a magnetic field. They have two contacts and metal reeds in a glass envelope. The contacts of the switch are open until activated by a magnet.
Reed switches are employed in various mechanical systems as proximity sensors, such as in doors and windows for burglar alarms and tamper-proofing. In laptops, reed switches trigger sleep mode when the lid is closed. Additionally, pedal keyboards for pipe organs utilize reed switches enclosed in glass to shield the contacts from dirt, dust, and debris.
Neodymium sew-in magnets are commonly used for magnetic clasps on purses, clothing, and folders or binders. These sewing magnets are sold in pairs, with one magnet being positive (+) and the other negative (–).
Magnets embedded in a patient's jaw can help secure dentures in place. To protect the magnets from corrosion caused by saliva, they are coated with stainless steel plating. Additionally, a layer of ceramic titanium nitride is applied to prevent abrasion and minimize exposure to nickel.
Magnetic doorstops are mechanical devices designed to keep a door open. When the door swings open and makes contact with the magnet, it remains in place until it is manually pulled away from the magnet.
Magnetic jewelry clasps consist of two halves sold as a pair. Each half features a magnet encased in a non-magnetic housing. A metal loop on each half allows attachment to the chain of a bracelet or necklace. The housings are designed to interlock, which prevents side-to-side or shearing movement between the magnets, ensuring a secure connection.
Speakers transform electrical energy into mechanical energy or motion. This motion compresses air and converts it into sound energy or sound pressure levels. An electric current passing through a wire coil generates a magnetic field within a permanent magnet attached to the speaker. The voice coil interacts with this magnetic field, causing the cone to move back and forth. This movement creates pressure waves in the air, which we perceive as sound.
In anti-lock braking systems, neodymium magnets are embedded within copper coils in the brake sensors. The system manages wheel acceleration and deceleration by adjusting the brake line pressure. Control signals, generated by the system's controller and sent to the brake pressure modulating unit, are derived from wheel speed sensors.
As the sensor ring's teeth pass by the magnetic sensor, they cause changes in the magnetic field's polarity, generating a frequency signal that corresponds to the axle's angular velocity. This signal is then used to determine the wheels' acceleration.
Neodymium magnets, being among the most powerful and strongest magnets available, can pose significant risks if not handled properly. It is crucial to manage these magnets with care to avoid potential harm. Below are descriptions of some of the negative effects associated with neodymium magnets.
Neodymium magnets are capable of snapping together with great force, potentially pinching skin or causing serious injuries. They can attract from several inches to even feet apart, and if a finger is caught between them, it can result in severe harm or fractures. Due to their immense strength, the force between neodymium magnets can be unexpectedly intense compared to other types of magnets.
Neodymium magnets are brittle and can easily peel, chip, crack, or shatter if they collide with force, potentially sending sharp metal fragments flying at high speeds. Although they are made from metal and have a shiny appearance, their hardness makes them quite fragile. It is important to wear eye protection when handling neodymium magnets to prevent injury from these flying fragments.
Neodymium magnets are not toys and should not be handled by children. Small magnets pose a choking hazard, and if multiple magnets are swallowed, they can attract to each other through the intestinal walls, leading to severe health problems that necessitate immediate emergency surgery.
A magnetic field strength of ten gauss can affect pacemakers or defibrillators, as neodymium magnets generate powerful magnetic fields. These fields can interfere with pacemakers, implantable cardioverter-defibrillators (ICDs), and other implanted medical devices, potentially causing them to deactivate when exposed to magnetic fields.
The intense magnetic fields produced by neodymium magnets can damage magnetic media, including floppy disks, credit cards, magnetic ID cards, cassette tapes, and video tapes. They can also adversely affect older electronic devices such as televisions, VCRs, computer monitors, and CRT displays. Therefore, neodymium magnets should be kept away from electronic appliances to avoid potential damage.
Magnetic fields can disrupt the operation of compasses, magnetometers, and the internal compasses found in smartphones and GPS devices. The International Air Transport Association (IATA) and U.S. federal regulations govern the shipping of magnets to ensure safe handling and transportation.
If you have a nickel allergy, your immune system treats nickel as a harmful substance and produces chemicals to combat it, leading to symptoms such as redness and skin rashes. Nickel allergies are more prevalent in women and girls, with about 36 percent of women under 18 affected. To prevent an allergic reaction, it is best to avoid neodymium magnets that are coated with nickel.
Neodymium magnets maintain their effectiveness up to 80°C (175°F). However, the temperature at which they start to lose their magnetic properties can vary depending on the grade, shape, and specific application of the magnets.
Neodymium magnets should not be drilled or machined, as the dust and powder generated during grinding are flammable.
Neodymium magnets are coated or plated to protect them from environmental damage. However, they are not waterproof and can rust or corrode if exposed to wet or moist conditions.
Despite their powerful magnetic fields, neodymium magnets are very brittle and require careful handling. Various industrial monitoring agencies have established regulations for their handling, manufacture, and shipping. Below is a brief overview of some of these regulations.
The American Society of Mechanical Engineers (ASME) sets standards for Below-The-Hook Lifting Devices. ASME Standard B30.20 covers the installation, inspection, testing, maintenance, and operation of lifting devices, including lifting magnets where the operator positions and guides the load. ASME Standard BTH-1 is applied in conjunction with ASME B30.20 to provide additional guidelines.
Hazard Analysis and Critical Control Points (HACCP) is an internationally recognized preventive risk management system focused on food safety. It addresses biological, chemical, and physical hazards by requiring the identification and control of risks at specific points in the production process. HACCP also provides certification for equipment used in food facilities, including separation magnets that have been specifically identified and certified for use in the food industry.
Magnetic separation equipment has been approved by the United States Department of Agriculture Agricultural Marketing Service as being in compliance for use with two food processing programs:
Certification is based on the following two standards or guidelines:
The Restriction of Hazardous Substances (RoHS) regulations restrict the use of lead, cadmium, polybrominated biphenyl (PBB), mercury, hexavalent chromium, and polybrominated diphenyl ether (PBDE) flame retardants in electronic equipment. Because neodymium magnets can pose hazards, RoHS has established standards for their handling and use.
Magnets are classified as dangerous goods for shipments outside the Continental United States to international destinations. For air transport, any packaged material must have a magnetic field strength of 0.002 Gauss or more at a distance of seven feet from any point on the surface of the package.
Packages containing magnets shipped by air must be tested to ensure they meet established standards. The magnetic field strength must be less than 0.00525 Gauss at a distance of 15 feet from the package. For powerful magnets, appropriate shielding is required. Due to potential safety hazards, there are numerous regulations and requirements governing the air shipment of magnets.
The Restriction, Evaluation, and Authorization of Chemicals (REACH) is an international regulation within the European Union that sets standards for hazardous materials. It provides guidelines and documentation for the proper use, handling, and manufacture of magnets, with a focus on their application in medical devices and electronic components.
An Alnico magnet is a permanent magnet made by combiming aluminum, nickel, iron, cobalt, and other elements. They come in isotropic, non-directional, or anisotropic, mono-directional, form...
A ceramic magnet, also known as a ferrite magnet, is a permanent magnet made by combining iron oxide and strontium carbonate. They are a man made magnet produced by heating the two elements to...
Flexible magnets are composite materials with magnetic components arranged in an elastomer matrix. They are made from a combination of rubber polymer resin and ferrite powder by forming it through...
Magnets are materials that exert a noticeable force on other materials without physically contacting them. This force is called a magnetic force. The magnetic force can either attract or repel. Most known materials...
Power supplies are electrical circuits and devices that are designed to convert mains power or electricity from any electric source to specific values of voltage and current for the target device...
An AC power supply is a type of power supply used to supply alternating current (AC) power to a load. The power input may be in an AC or DC form. The power supplied from wall outlets (mains supply) and...
A bowl feeder is a mechanism for supplying small parts and components to a production line or for sorting bulk items for rapid use. A self contained bowl feeder system has a bowl that sets on a spring loaded base that moves vertically...
A DC DC power supply (also known as DC DC Converter) is a kind of DC power supply that uses DC voltage as input instead of AC/DC power supplies that rely on AC mains supply voltage as an input...
A DC power supply is a type of power supply that gives direct current (DC) voltage to power a device. Because DC power supply is commonly used on an engineer‘s or technician‘s bench for a ton of power tests...
Electric transformers are static electrical machines that transform electric power from one circuit to the other without changing the frequency. An electrical transformer can increase or decrease the voltage with...
An electromagnetic interference or EMI Filter is an electrical device or circuit that filters specific unwanted frequencies in power lines or offending frequencies that are detrimental to a system. They receive AC or main power...
By definition a power supply is a device that is designed to supply electric power to an electrical load. An electrical load refers to an electrical device that uses up electric power. Such a device can be anything from...
An isolation transformer, just like typical transformers, is a non-moving device that transmits electrical energy from one circuit to another without requiring any physical contact. It works on the idea of magnetic...
Power transformers are electrical instruments used in transmitting electrical power from one circuit to another without changing the frequency. They operate by the principle of electromagnetic induction. They are used in transmitting electrical power between...
A programmable power supply is a method for controlling output voltage using an analog or digitally controlled signal using a keypad or rotary switch from the front panel of the power supply...
An electrical transformer is a passive machine that transfers electrical energy from one circuit to another using a magnetic flux to induce an electromotive force. Transformers are used to increase (step-up) or decrease (step-down) voltages without changing the frequency of the electric current...
A toroidal transformer is a type of electrical transformer constructed with a torus or donut-shaped core. Its primary and secondary windings are wound across the entire surface of the torus core separated by an insulating material...
Vibratory conveyors are material-handling equipment used to transport fine to coarse-grained bulk materials. These vibratory conveyors are strong conveying equipment utilized for bulk commodities with fine to coarse graininess...
Vibratory feeders are short conveyors used to transport bulk materials utilizing a controlled vibratory force system and gravity. The vibrations impart a combination of horizontal and vertical acceleration through tossing, hopping, or sliding-type of action to the materials being handled...
A vibratory screening is a process that separates bulk solid materials from solids and slurries using inertial vibration that causes various sizes of particles to pass through openings in a screen or...
Electronically operated equipment depends on power transformers to convert electrical currents into voltage. Current transformers store and transport energy through power lines and grids...