Capacitive Touch Screen
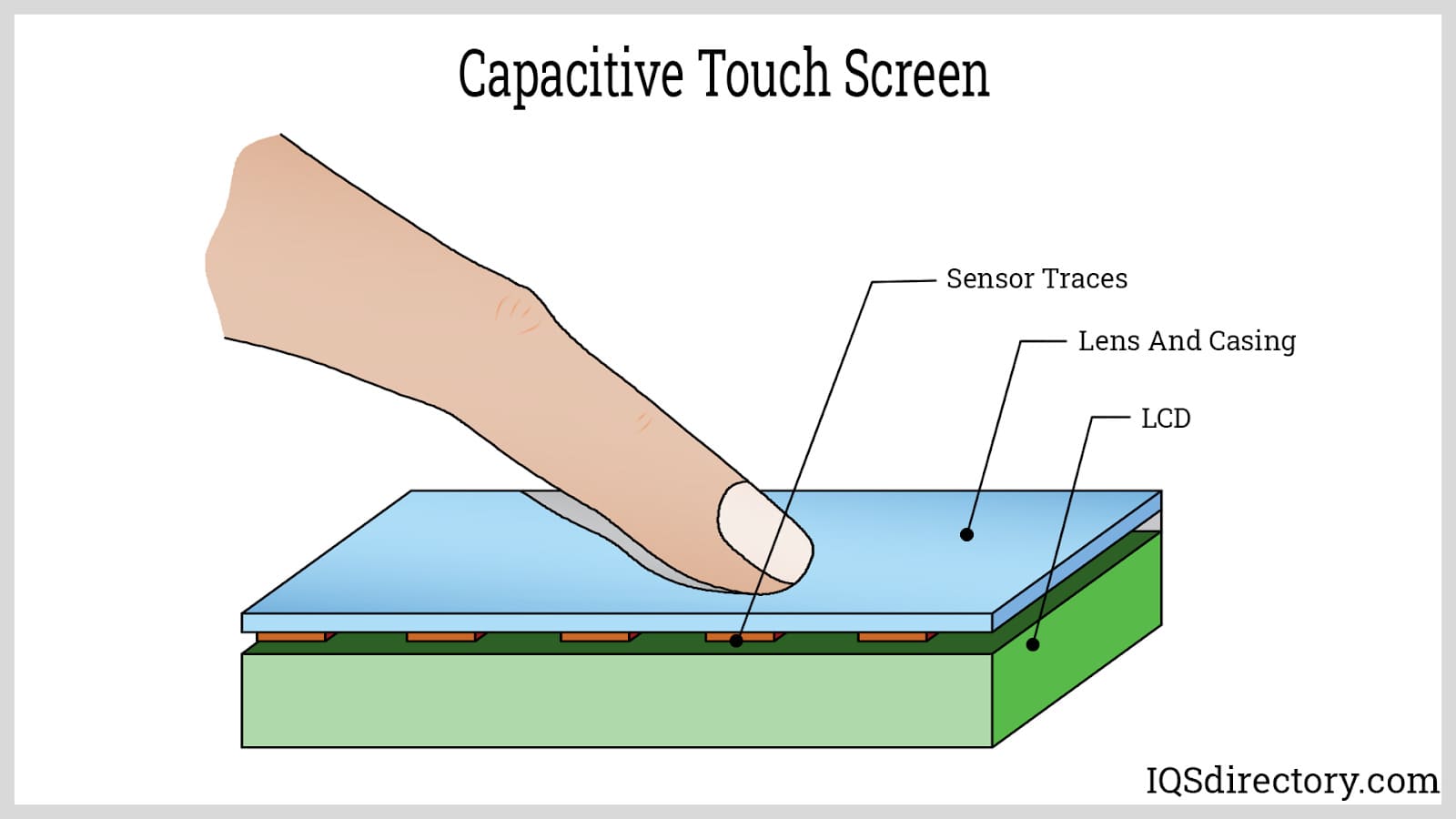
A device's display screen that uses finger pressure for interaction is called a capacitive touch screen. Handheld capacitive touch screen devices generally link to networks or computers using an architecture that can...
Please fill out the following form to submit a Request for Quote to any of the following companies listed on Membrane Switches .
This article provides comprehensive insights into membrane switches. Read further to learn more about:
Membrane switches are a type of interface between humans and machines, composed of layers of plastic films or other flexible substrates. These layers are typically printed or laminated with conductive materials and graphic inks. When pressed, the switches function by temporarily closing or opening an electrical circuit. Their compact and efficient design makes them ideal for a broad range of uses, such as in consumer electronics and industrial machinery.
Membrane switches are advanced user interface solutions widely utilized in modern electronic devices, industrial control panels, medical equipment, and consumer appliances. Constructed from multiple flexible layers—including a durable top graphic overlay with printed icons or symbols, an insulating spacer, and a lower membrane with printed conductive traces—membrane switches enable efficient, reliable user input. By pressing the surface of a membrane switch keypad, the overlay flexes to close an electrical circuit, allowing for seamless data entry and control. Thanks to their low profile, cost-effective manufacturing, and superior reliability, membrane switch panels have become the preferred choice for high-performance electronic interface applications.
Understanding the various types of membrane switches is crucial when selecting the optimal solution for your specific project needs. Below are the most common types, each with unique features that cater to different industries and environmental requirements:
Non-tactile membrane switches lack physical feedback or a "click" sensation when pressed, making them ideal for industries where a gentle touch operation is preferred, such as in medical devices or laboratory equipment. Their silent, low-force activation supports streamlined, ergonomic design without mechanical noise interference—a feature valued in healthcare, cleanroom environments, and sensitive control systems. The absence of tactile feedback allows for higher switch density and longer operational life, reducing wear and tear on user interface components.
Tactile membrane switches are engineered to deliver mechanical feedback through a noticeable "snap" action when pressed. This tactile response is typically achieved by integrating domes or other actuating mechanisms beneath the graphic overlay. The definitive tactile sensation assures users that an actuation has occurred, enhancing usability and operational accuracy in applications such as industrial machinery, household appliances, and consumer electronics. By combining tactile feedback with customizable overlays, designers can create intuitive and reliable membrane switch keyboards for virtually any industry.
Metal dome membrane switches utilize precision-engineered stainless steel domes as tactile elements. When depressed, these domes provide not only a sharp tactile sensation but also audible feedback—essential in applications demanding confirmation of input signals in environments with ambient noise. Metal dome switches are a popular choice for commercial-grade control panels, instrumentation, and rugged wearable devices, thanks to their high durability, consistent actuation force, and resistance to environmental stressors.
Polydome membrane switches incorporate molded plastic domes (polyester or polycarbonate) to create the tactile response. These polymer domes deliver cost-effective tactile feedback, making polydome switches especially desirable for networking equipment, point-of-sale terminals, and budget-sensitive consumer products. The design flexibility of poly domes allows for a range of actuation forces and lifespans, supporting custom membrane switch manufacturing for specialized uses.
LED backlit membrane switches are equipped with integrated Light Emitting Diodes (LEDs) below the graphic layer, providing illuminated buttons or labels. This backlighting technology increases switch visibility in low-light or dark environments, ensuring accurate operation for medical devices, aerospace controls, automotive dashboards, and marine equipment. High-brightness LED backlighting can be further customized with diffusers and color options, delivering enhanced visual cues and brand consistency within user interface design.
Capacitive membrane switches are based on capacitive touch sensing technology rather than traditional physical actuation. They detect changes in the electrical field when a finger approaches or touches the interface, enabling sleek, touch-sensitive controls with no moving parts. Capacitive touch membrane switches are preferred for high-end consumer electronics, touchscreen kiosks, wearable devices, and smart home products due to their modern appearance, customizable sensitivity, and ease of cleaning and maintenance.
Sealed or waterproof membrane switches are designed with environmental sealing to block moisture, dust, chemicals, and other contaminants. Using advanced sealing technologies, such as perimeter gaskets, adhesives, and protective overlays, these switches are tested to meet rigorous IP65, IP67, or NEMA standards. They are essential for outdoor controls, agriculture machinery, food processing equipment, and industrial automation systems where maximum durability and reliability are critical for safety and operational efficiency.
Custom membrane switches are engineered to fulfill unique project requirements and can be designed with a wide range of options, including multi-color printing, EMI/RFI shielding, integrated display windows, variable switch layouts, and specialized actuator shapes. Manufacturers collaborate with clients to develop switches tailored to application-specific criteria such as ergonomic preferences, user interface complexity, environmental exposure, and regulatory compliance, ensuring optimal performance and branding alignment across sectors like healthcare, defense, transportation, and consumer electronics.
When choosing a membrane switch, it's important to evaluate not only the basic electromechanical requirements but also factors like tactile vs. non-tactile feedback, waterproofing capabilities, backlighting features, and compatibility with existing electronic equipment. Reliable suppliers and experienced membrane switch manufacturers can guide you through the design process, helping you select the best materials, overlay graphics, and actuation methods for superior user experience, long-term durability, and cost-effectiveness. For more details or to request a custom quote, consider reaching out to trusted membrane switch suppliers who can support you from prototyping to large-scale production.
Membrane switches are increasingly favored in a wide array of applications—including domestic, commercial, medical, and industrial sectors—due to their unique blend of cost-effectiveness, durability, and design flexibility. While user interfaces such as touchscreens, mechanical keypads, push-button switches, and rotary selector knobs are all viable options, membrane switches stand out for their compact form factor, robust construction, high reliability, resistance to harsh environments, and low production costs. These qualities together make membrane switches an optimal solution for industries seeking reliable and customizable user interface technology. Explore the core advantages of membrane switches explained in detail below to understand why they are so widely implemented in modern equipment and electronics.
Membrane switches are renowned for their ultra-slim and compact design, an important advantage for devices where space is at a premium. Constructed from multiple micro-thin layers—including the graphic overlay (usually durable polyester or polycarbonate), insulating spacer layers, tactile domes, and a printed circuit layer—the overall thickness can be less than 1 millimeter. This allows for seamless integration into sleek product designs without adding bulk, which is particularly critical in medical devices, portable instrumentation, consumer electronics, and industrial control panels. Their low-profile form also supports contemporary aesthetic requirements and simplifies installation in confined spaces—boosting both space efficiency and product reliability. For manufacturers and engineers, space-saving membrane switch panels are ideal when every millimeter matters.
Designing the graphic interface for membrane switches is streamlined and highly customizable. The process typically starts with professional CAD or graphic design software such as AutoCAD, SolidWorks, or Adobe Illustrator, enabling engineers and designers to create visually appealing and intuitive icons, text, and layouts. Once designs are finalized, overlays are digitally printed, which allows for high-resolution graphics, precise color matching, and brand consistency. Some applications may leverage additional processes like embossing, engraving, or tactile marking to enhance user experience and visual impact, although digital and screen printing remain industry standards for membrane keypad overlays. This ease of design translates into faster development time, greater product differentiation, and the ability to handle both high-volume and low-volume production efficiently.
One of the primary advantages of membrane switches is their robust defense against environmental contaminants. Sealed construction using pressure-sensitive adhesives, heat sealing, or laser bonding prevents dust, moisture, corrosive chemicals, and gases from penetrating sensitive circuit areas. Materials such as polyester (PET) and polycarbonate offer superior chemical resistance and excellent optical clarity, while advanced UV protective coatings increase resistance to sunlight and fading. The absence of exposed mechanical components means these user interfaces can meet rigorous IP (Ingress Protection) ratings—crucial for industrial control interfaces, food processing equipment, medical instrumentation, and outdoor electronic devices. This makes membrane switches highly suitable for applications demanding consistent functionality in challenging or sterile environments.
The flat, sealed surfaces of membrane switches make them exceptionally straightforward to clean and sanitize, a highly valued attribute in sectors like healthcare, pharmaceuticals, and food production where hygiene is paramount. Their rugged overlays are engineered to resist abrasion, scratching, and repeated exposure to cleaning agents. Users simply wipe down the membrane keypad or interface with a damp cloth, alcohol-based cleaner, or mild disinfectant, ensuring safe, reliable operation without risk to underlying circuitry. This low-maintenance design not only reduces downtime and routine servicing expenses, but also extends the lifespan and functional reliability of the equipment in demanding applications.
Despite their low profile, membrane switches are engineered to deliver satisfying tactile response, enhancing both usability and operational confidence. Tactile feedback is commonly achieved through metal domes, poly domes, or other dome arrays integrated into the switch layer, providing users with a distinct “click” or actuation feel. This sensory feedback reduces input errors and accidental keystrokes—important for operator safety and process accuracy in critical applications like medical devices, test instruments, and control consoles. For touch-based interface solutions, having tactile feedback on a membrane keypad or panel provides a user experience closer to traditional mechanical keypads, but with a much thinner footprint and increased reliability.
Modern electronics face constant threats from electromagnetic interference (EMI) and electrostatic discharge (ESD), which can compromise equipment operation or damage control systems. Membrane switches can be engineered with dedicated EMI shielding, a feature achieved by integrating conductive inks or mesh layers (such as silver or carbon-based grids) within the switch assembly. Consistent, gap-free shielding ensures optimum attenuation of unwanted RF signals and reliable performance in sensitive environments. This capability is especially essential in medical instrumentation, aerospace electronics, and industrial automation where signal integrity and electrical safety are non-negotiable.
Membrane switches are highly cost-effective compared to traditional mechanical switches or touchscreen interfaces, thanks to their lightweight materials, simplified construction, and compatibility with high-volume automated manufacturing. The use of plastics like polyester (PET), polycarbonate, or polyimide and printed conductive inks reduces material and fabrication costs. Design adaptability means that custom layouts, backlighting (LED illumination), and integrated features such as flexible circuits or resistive touch technology can be incorporated without significant increases in production costs. This makes membrane keypads and custom membrane panels a preferred solution for OEMs seeking reliable, scalable, and affordable human-machine interface (HMI) options.
Membrane switches are inherently customizable and can be tailored precisely to meet end-user requirements. Options include integrating surface-mount LEDs for backlighting, tactile and non-tactile feedback, transparent display windows, antimicrobial coatings for medical keypads, and even multilayer circuits for capacitive touch interfaces. This level of design flexibility enables seamless integration with printed circuit boards (PCBs), flexible circuits, or touchscreens—supporting unique branding, functional requirements, and even strict regulatory compliance.
When evaluating the best membrane switch or control panel for your application, consider key specifications such as life cycle ratings, actuation force, IP and NEMA ratings, chemical resistance, and available customization. Many leading suppliers and manufacturers provide engineering support, rapid prototyping, and value-added services to ensure your membrane switch assembly meets exact performance criteria.
Membrane switches are made up of multiple layers assembled using pressure-sensitive adhesives or heat sealing films. The main components include: an overlay with graphic elements; a circuit layer that contains conductive tracks, metal domes, circuit tail, and terminals; and a spacer that maintains separation between the switch contacts.
Also known as top or graphic overlay, the overlay is the outermost layer of the membrane switch. Since this layer is on the exposed side of the membrane switch, it is made from materials that have good flexibility, clarity, durability, chemical resistance, and barrier properties. There are two common materials used for making the overlay.
Other materials suitable for overlays include acrylic, vinyl, and PVC.
Graphics can be printed either on the reverse side or the front side of the overlay. Reverse side or sub-surface printing is more commonly used as it results in more durable prints, with the overlay plastic film providing protection against abrasion and chemical damage. Front side or top-surface printing, however, allows for the addition of various features such as selective textures and transparent windows.
Domes are the components that provide tactile feedback. They can be made from metal or plastic. The size of the keys of the membrane switch determines what size the dome will be, with sizes ranging from 0.24 to 0.79 inches (6 to 20 mm). Additionally, the dome’s height is closely related to the size of the dome and can be 0.010 to 0.057 inches (0.25 to 1.45 mm).
A critical aspect of using domes in membrane switches is the actuation force, or trip force, required to compress the dome and activate the switch. This force can range from 1.41 oz to 80 oz (40 to 2250 g). Domes are available in a variety of shapes and sizes, including:
Metal domes are constructed from stainless steel or copper alloys and are typically secured by a dome retainer layer or spacer layer. In addition to providing tactile feedback, metal domes also serve as integral components of the circuit. When pressed, the metal dome completes the circuit by closing the open contacts of the switch. These domes feature a low profile and are highly durable, with life ratings of up to 10 million presses, making them well-suited for a wide range of applications.
Plastic domes, often made from polyester, are known for their flexibility and are commonly referred to as “poly” domes. These domes usually include their own layer, which in some designs can also function as the overlay or graphics layer. The poly dome layer is a polyester film featuring dome or blister-like shapes. On the concave side of the dome, a layer of printed conductive ink completes the circuit when the button is pressed.
The retainer layer's primary function is to hold the metal domes in place. It is typically made from polyester film, similar to the material used for poly domes. This layer secures the domes without the need for an adhesive layer.
The spacer layer is used to create a gap between the two conductors of the switch, allowing the switch to remain in its open position. In some tactile-type membrane switch designs, it also functions as a retainer for holding the metal dome in place. The spacer layer typically features channels or vents that allow air to escape from the cavity when the key is pressed, preventing air compression that could affect the switch's performance.
This layer contains the conductive paths of the switch, which can be created using methods such as screen printing or photochemical etching.
Depending on the type of membrane switch, the circuit can be designed and constructed in two primary ways.
The circuit tail is the component of the membrane switch that connects it to the machine’s control unit. It consists of a flat, flexible ribbon with multiple conductive tracks printed on a polyester strip. At the end of the circuit tail are connectors that interface with the control unit’s termination block. Common connector types include plain headers, latching headers, or solder tabs. Additionally, the circuit tail may use a ZIF (zero insertion force) style connector, which minimizes the force required to connect the tail to the control unit terminals. ZIF connectors are particularly useful for delicate circuits where the control unit terminals are fragile and prone to damage.
Mounting adhesive is applied to the back of the membrane switch to securely bond it to the mounting surface. The choice of adhesive depends on factors such as bonding strength, thickness, and operating temperature. Typically, mounting adhesives are elastomeric compounds made from high-strength or modified acrylic materials.
Acrylic adhesives are the industry standard for bonding due to their excellent adhesion to both metal and plastic surfaces. They also allow for repositioning, which enhances placement accuracy when working with plastics. The advantages of acrylic adhesives include:
The thickness of the mounting adhesive is an important consideration for ensuring a proper bond between the membrane switch and the surface. For smooth surfaces, a thickness of 0.079 inches (2 mm) is typically sufficient. However, for textured surfaces, a thicker adhesive, around 0.2 inches (5 mm), is recommended to maximize the adhesive's contact area and ensure a strong bond.
When selecting a membrane switch and supplier, it's crucial to understand the switch's specifications and features. Like any electronic or electrical component, the membrane switch must be compatible with the system where it will be installed. This ensures that the electrical specifications of the switch align with the system's requirements, preventing issues such as electrical shorting or premature failure. Additionally, consider other features such as coatings, backlighting, and precision cutting to ensure the switch meets your needs.
These data outline the characteristics and performance of the electrical circuit. Some of the key specifications are listed below.
Certifications confirm that a product meets the general safety standards set by national and international organizations. Commonly recognized certifications include Underwriter Laboratories (UL Listed or Recognized) and CE.
Membrane switches operate with low voltages and currents, making them susceptible to stray electrostatic discharges (ESD) and electromagnetic interference (EMI), which can short the circuit or disrupt the electrical current. To mitigate these issues, an ESD/EMI shield is included in the membrane switch assembly. This shield is typically a layer of conductive material positioned either above or below the circuit. Some designs feature a complete wrap around the circuit layer. Common shield materials include a thin polyester layer with conductive ink printed in a grid or mesh pattern, or copper or aluminum foil, which may or may not be laminated with polyester. The shielding is often grounded by connecting it to the metal enclosure, metal backer, or a grounding connection from the circuit tail.
Tactile feedback in membrane switches is achieved through metal or plastic domes, which help operators confirm that a keypress has been registered. Different dome designs offer varying actuation forces to suit different needs. In contrast, non-tactile membrane switches are preferred in applications where a slim profile is more important than providing feedback.
A backing layer adds rigidity to the membrane switch and can be omitted based on the application, especially if the keypad is supported by the device's panel itself. This layer typically has a pressure-sensitive adhesive on its underside to facilitate mounting.
Selective texturing involves applying a transparent, scratch-resistant matte finish to specific areas of the overlay to highlight graphic elements and enhance aesthetics. This finish helps reduce visible scratches that commonly occur on glossy surfaces, making it ideal for heavy-duty applications such as industrial equipment interfaces.
Hard coating is a common surface treatment applied to materials with lower durability, such as plastics, paper, wood, and glass. This process involves applying a layer of ultraviolet-curable polymer resin using various deposition methods. The specific composition of the polymer and the deposition technique can vary between manufacturers. The hard coating provides enhanced durability and chemical resistance compared to the underlying polyester or polycarbonate film.
Embossing enhances both the aesthetics and tactile feel of the overlay by raising certain areas. The main types of embossing include pad, dome, and rim.
In addition to the three common types of embossing—pad, dome, and rim—custom raised patterns can include shapes such as Braille, text, and logos. The height of the embossing can also be varied to create multi-level effects, enhancing the visual appeal and tactile experience of the graphics.
Windows in membrane switches are transparent or translucent areas designed to accommodate light crystal displays (LCDs) or light-emitting diode (LED) displays. The design of these windows ensures optimal readability based on the display type. LCDs typically require clear windows with minimal filtering, while LED segment displays benefit from optical filtering to enhance readability in bright conditions. To improve contrast between the LED segments and their background, a gray or amber filter is printed on the display window, with varying levels of transmission. The choice of filter color depends on the color of the LED.
Indicators highlight activated keys, while backlighting enhances the readability and aesthetics of the interface. The four main types of backlighting are:
Backlighting is an optional feature for membrane switches that illuminates the front surface of the switch. It can be applied in various ways, such as lighting a specific area, the entire surface, or selected sections. Although not essential, backlighting offers several benefits, including:
The term "dead front" refers to a user interface that remains unobtrusive until activated. In this design, switches are concealed beneath a smooth, unmarked surface, giving the panel a clean and minimalist look. When touched, the flexible membrane switches provide tactile feedback, ensuring ease of use and a satisfying user experience. This technology is commonly used across various industries, from consumer electronics to industrial control systems, where a discreet and intuitive interface is crucial. Dead front membrane switches not only enhance the visual appeal of products but also offer a durable and reliable solution for user interaction, achieving a harmonious balance between form and function.
Membrane switches are designed to fit into a plastic molding or metal panel assembled with the control unit. Specific dimensional tolerances must be complied with to ensure proper mounting and sealing of the electrical components. This is influenced by the type of cutting method used. The most popular methods are steel rule die cutting and laser cutting. Steel rule die tooling is used due to its low capital cost and high cutting speed. On the other hand, laser cutting is preferred in applications where precision and burr-free cutting is necessary.
Membrane switches are commonly used in car dashboards for functions such as climate control, audio systems, and navigation. They are also employed in steering wheel controls and other interior components of vehicles.
Aircraft cockpit controls and instrument panels frequently use membrane switches because of their reliability and compact design. These switches are well-suited to endure the challenging environmental conditions found in aviation.
Membrane switches are used in military control systems, communication equipment, and vehicle consoles. They can be engineered to meet stringent military specifications, including resistance to shock, vibration, and extreme temperatures.
Membrane switches are commonly used in keyboards and control panels for telecommunication devices, including smartphones, landline phones, and network equipment.
Home automation systems frequently use membrane switches to control lighting, security systems, and climate control. They are also commonly found in kitchen appliances such as ovens, microwave ovens, and coffee makers.
Membrane switches are utilized in laboratory devices and scientific instruments for controlling settings and inputting data.
Control panels and navigation systems on boats and ships often use membrane switches because of their resistance to water and harsh marine conditions.
Membrane switches are commonly found in cash registers, barcode scanners, and other point-of-sale (POS) equipment.
Membrane switches are frequently used during the prototyping phase of product development due to their ease of customization and cost-effectiveness.
Membrane switches are commonly used in access control panels and security systems for user interaction.
Membrane switches can be customized with specific graphics, icons, and tactile feedback to suit specialized applications, including industrial machinery, scientific instruments, and more.
A device's display screen that uses finger pressure for interaction is called a capacitive touch screen. Handheld capacitive touch screen devices generally link to networks or computers using an architecture that can...
Simply put, a flexible printed circuit (abbreviated FPC) has conductive traces on a thin, flexible substrate. "Flexible printed circuits." are circuit boards that can twist or bend. This claim makes it clear that they can be distinguished by...
A membrane keyboard is a type of keyboard technology found in many electronic gadgets and appliances. A keyboard, as we all know, is essential hardware that...
Die cutting is the mass fabrication of cut-out shapes by shearing a stock material such as paper and chipboard using tooling called a die. A die is a specialized tool used in manufacturing to cut or shape a material fitted into a press...
Kiss cutting is a method for cutting into a material where the upper layers are pierced, but the back layer is left intact. The term "kiss" refers to the way the blade touches the upper layers of the material and leaves a pattern or cut with a sufficient amount of force to leave an impression...
A name plate is a method for displaying the name of a person, logo, product, or mechanism and is made from a variety of materials to serve as a long term identifier...