Capacitive Touch Screen
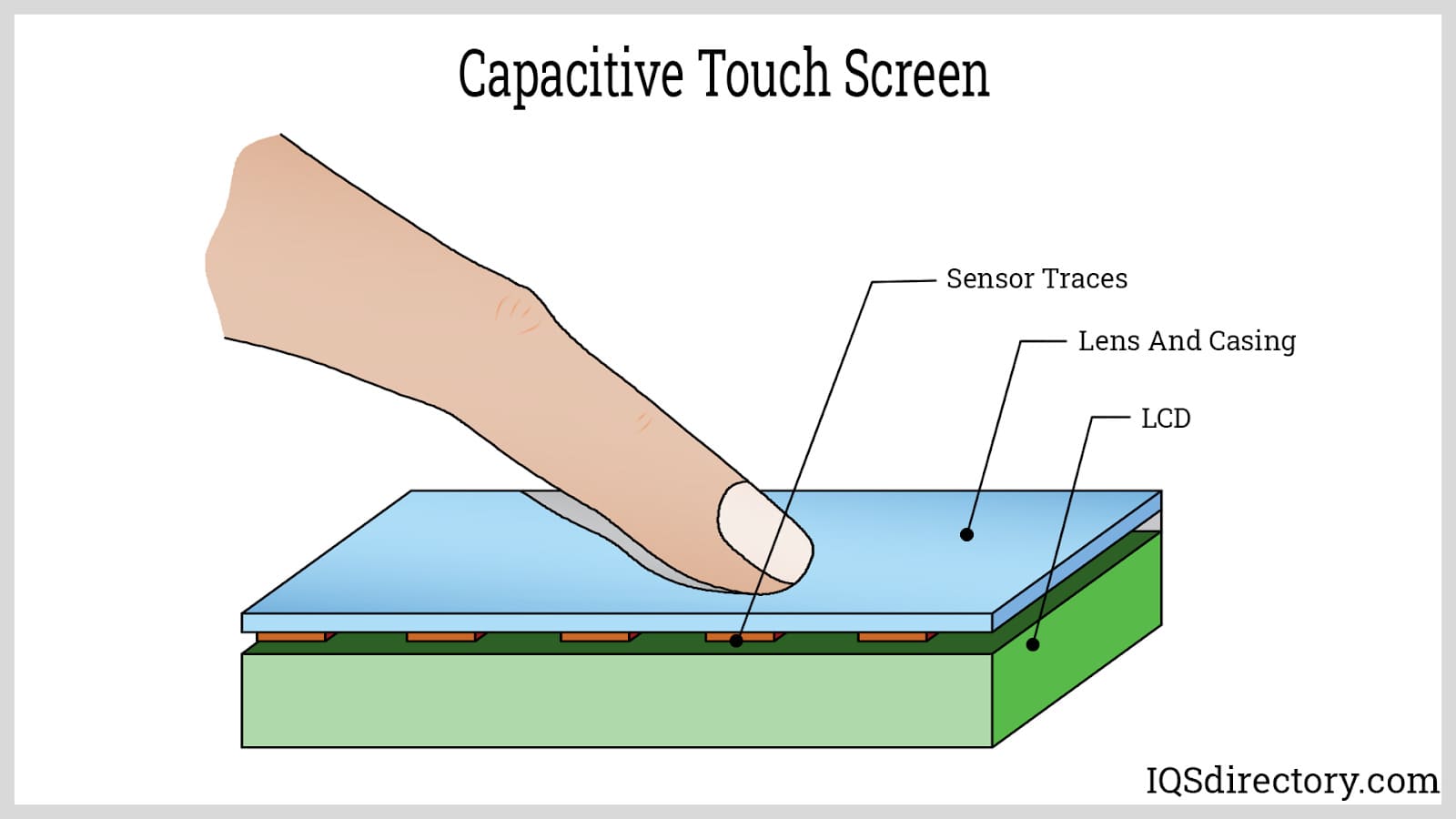
A device's display screen that uses finger pressure for interaction is called a capacitive touch screen. Handheld capacitive touch screen devices generally link to networks or computers using an architecture that can...
Please fill out the following form to submit a Request for Quote to any of the following companies listed on Membrane Switches .
This article will give a detailed discussion of flexible printed circuits.
It is expected that after reading this article, one should understand the following:
And much more…
A flexible printed circuit (FPC) involves conductive tracks on a thin, pliable base material. Unlike traditional rigid PCBs, these "flexible printed circuits" are engineered to bend or twist. They may incorporate surface-mounted parts such as resistors and LEDs and typically feature connectors or terminations for integration with other systems. The choice of substrate is vital, differing from standard PCBs in design, production methods, and functionality. Materials like polyimide are frequently used for their distinct properties in constructing these circuits. An FPC is created by laminating a copper foil onto a resin substrate, with layers joined through adhesive, heat, or pressure to create a unified board. The construction includes conductive, insulating, and adhesive layers to ensure proper operation and insulation.
Flexible PCBs are perfect for applications requiring lightweight, slender, and high-density circuitry. As companies aim to maximize functionality with minimal resources, flexible PCBs offer the benefits of three-dimensional wiring and the ability to conform to specific spaces and uses. Moreover, they generally provide superior heat dissipation compared to traditional PCBs, thereby enhancing the longevity and performance of electronic devices.
Flexible printed circuits and conventional PCBs share similar electrical roles, yet they differ substantially in design and structure. The primary difference is the ability of flexible circuits to bend or twist, unlike their rigid counterparts. This flexibility necessitates diverse manufacturing approaches, materials, and designs.
Standard PCBs focus on thermal and chemical properties of adhesives irrelevant to flexibility. In contrast, flexible circuits require adhesives that stretch and offer flexibility. Therefore, the adhesive in flexible circuits must possess distinct thermal, mechanical, and chemical characteristics compared to those used in rigid PCBs.
The foundational layer in a PCB needs strength and is typically reinforced with glass. The most common material used is a flame retardant epoxy resin and glass fabric composite, providing crucial stability, mechanical, and thermal resistance. However, it's rigid and inelastic. Conversely, flexible circuits commonly use polyimide for its flexibility, although this material offers limited mechanical support and dimensional stability.
Regarding copper film, there are two varieties. The first uses electrodeposition, while the second involves rolling and annealing. The rolled and annealed type is more flexible, ideal for FPC applications, whereas PCBs typically use electro-deposited copper with limited flexibility. Thus, the performance of a flexible circuit heavily relies on the copper type used.
Designing flexible PCBs requires a distinct approach compared to rigid ones. Consider these guidelines and factors when creating flexible printed circuits.
Choosing a manufacturer for flexible PCBs necessitates ensuring they employ current technology to address material characteristics, movement, and thermal coefficients vital for crafting robust circuits that meet specifications.
Additional considerations when selecting a manufacturer include guaranteeing product quality, as the investment is significant. Circuit boards should feature high-density designs, effective communication paths, and good conductivity to enhance thermal dissipation. Moreover, the manufacturer must be capable of producing flexible PCBs to any required shape, ensuring they meet essential criteria:
Bend radius characteristics are crucial for flexible circuit manufacturers. Establishing the bend radius early in the design process ensures the circuit can withstand bending without damaging copper traces. The bend radius defines the minimum curvature of a flexible section and should avoid features like slots or cutouts that could weaken it.
Selecting cover materials during PCB fabrication significantly affects durability and performance. Choosing materials suited to the PCB's specific application is essential. Quality matters whether flexible printed circuit boards are for personal or commercial use. Manufacturers should choose cover materials based on performance, specifications, and the board's operating environment.
In PCB design, "wire routing" describes the path electrical connections follow. This step is critical for PCB design, especially for flex PCBs, as the growing bend radius increases strain. Routing traces through low-stress areas enhances PCB safety, helping prevent short circuits and reducing electrostatic discharge risks.
Attention must be paid to features that might cause discontinuities, especially in bending zones. Internal stress when twisting or stretching flexible circuits can lead to insulation or conductor fractures. Avoiding features like beams and reducing copper thinning minimizes these risks.
Layer stacking in flexible PCBs is pivotal due to multiple layers being stacked. Position the most pliable layers centrally to mitigate movement and maintain flexibility.
Delamination, or "layer detachment," is a common issue in PCB manufacturing, potentially damaging circuits or causing faults. Using appropriate solder paste and considering flexibility requirements can help prevent delamination. Incorporating features that counteract delamination is essential in the design.
In flexible printed circuit board design, don't solely rely on drawings for adhesive width. Design should specify overall PCB width, including dielectric materials affecting impedance. Designers should prepare comprehensive drawing packages, focusing on critical features while omitting unnecessary details to balance accuracy and cost efficiency.
Flexible printed circuits (FPCs), also known as flex circuits or flexible PCB boards, are engineered with a diverse array of high-performance materials to meet the demanding requirements of modern electronics. Copper is the most widely used conductive material due to its superior electrical conductivity and reliability. Other advanced conductors employed in flexible printed circuit manufacturing include silver ink, Constantan°, and aluminum, each selected based on specific circuit performance needs such as signal integrity or thermal management. Polyimide film is a standard choice as the insulating substrate, offering excellent flexibility, high thermal resistance, and durability. Compared to traditional rigid printed circuit boards (PCBs), these materials enable flexible PCBs to accommodate bending, folding, and complex electronic packaging, making them ideal for applications in medical devices, consumer electronics, automotive systems, and aerospace technology.
The production of flexible printed circuits is a precise, multi-step process, optimized for high yield, repeatability, and quality control. Leading flex PCB manufacturers follow four main stages, each with rigorous protocols and advanced process technologies to ensure compliance with industry standards such as IPC-6013 and RoHS directives. These stages are designed to address all design and engineering requirements — from prototype development to mass production of custom flexible circuit solutions.
The initial phase of manufacturing focuses on the careful preparation of the substrate material, primarily high-grade polyimide, for ultimate flexibility and mechanical strength. To maximize space utilization and reduce manufacturing costs, engineers employ nesting techniques that optimize circuit placement. The following critical steps are integral to robust, reliable flexible PCB fabrication:
To further optimize signal performance and reduce electromagnetic interference (EMI), engineers frequently implement cross-hatched ground planes and tailor circuit board weight to boost flexibility and minimize substrate fatigue over repetitive bending cycles.
With substrates prepared, the next phase centers on the actual fabrication of the flexible circuit board layers. Key design parameters—such as minimum conductor width, spacing, and the use of thin polymer films—are determined to optimize current-carrying capacity and voltage isolation. Flexible PCB manufacturing standards typically require a minimum conductor width of 375 micrometers, though high-density applications may demand even finer lines. The use of specialized adhesives and copper-clad laminates ensures thermal stability and reliability in extreme environments encountered by military, medical, and automotive electronics.
Maintaining optimal edge clearance between circuit traces and the outer edge of the PCB is essential for mechanical fit and to prevent dielectric breakdown. Advanced design software tools are used to analyze laminate layer spacing and enable precise filleting of pads, distributing mechanical stress, enhancing solder joint robustness, and promoting overall longevity. Plating through holes and via structures is a standard practice to achieve strong, reliable interconnects in multilayer flex PCB assemblies.
Surface treatment processes improve mechanical stability, dielectric properties, and solderability of flexible PCBs. Plasma chemical vapor deposition and vacuum-assisted plasma (PVD) techniques are commonly employed to activate surfaces prior to lamination or bonding. For circuits using FR4 or other flame-retardant substrates, these treatments optimize electrical performance, improve adhesion, and protect against moisture ingress, further extending the lifespan of the final electronic product.
Button plating is a refined electroplating process that enhances the durability of plated through-holes (PTH) in flexible PCBs. By depositing additional copper into hole walls, manufacturers produce highly reliable via connections capable of withstanding thermal and mechanical stress, which is especially important for flex-rigid PCB hybrids and multilayer designs.
Advancements in PCB fabrication allow for exceptionally small holes and densely populated layouts, maximizing use of available space. Technologies such as micro-via drilling enable the production of holes down to 30 micrometers, opening up possibilities for compact, lightweight designs with intricate circuitry for medical implants, mobile devices, and IoT sensors.
Post-lamination, precise routing, cutting, and trimming processes remove excess material from the flexible circuit panel. Automated laser cutters or mechanical routers ensure edge quality and dimensional accuracy, which are vital for ensuring the PCB perfectly fits within enclosures and maintains consistent assembly tolerances.
During this stage, critical attention is given to defining the physical and protective layers of the flexible printed circuit. Applying robust cover layers and solder masks shields the delicate circuitry from environmental hazards such as moisture, dust, and corrosion. The cover layer also acts as an electrical insulator, safeguarding against accidental short circuits and improving the safety of electronic assemblies. The selection of coverlay materials—including polyimide, screen-printable liquid overcoats, or UV-cured resins—depends on the intended use case, bendability requirements, and cost considerations. Custom solutions are often utilized for circuits exposed to continuous flexing, such as medical catheter PCBs or automotive harnesses.
Some common cover layers used in this process include:
Quality assurance is a critical component of modern flexible PCB manufacturing, ensuring each circuit meets rigorous standards for electrical performance, reliability, and safety. Industry-leading manufacturers integrate advanced computer-aided inspection technologies and standardized test protocols into their process flow to achieve high production yields and minimize defects.
These inspection and test measures ensure that finished flexible circuit boards are free from defects, properly functioning, and fully compliant with industry standards—critical requirements for high-reliability electronics in aerospace, automotive, and medical device markets. Comprehensive documentation, traceability, and ongoing process monitoring further reinforce the delivery of quality-assured, high-performance flexible printed circuits to end users, OEMs, and contract manufacturers worldwide.
Flexible printed circuits (FPCs), also known as flex circuits or flexible PCBs, come in a diverse range of types and configurations tailored to meet the needs of advanced electronics, wearable technology, aerospace, automotive, industrial, and medical device applications. These flexible circuit boards can be categorized based on layer count, circuit complexity, and compliance with established industry standards such as IPC-6013. Understanding the different types of flexible PCBs is crucial for selecting the optimal solution for your specific electronic design, ensuring both reliability and performance in environments where space saving, bendability, and lightweight construction are paramount.
High-density interconnect (HDI) flexible printed circuit boards represent the cutting edge in flexible PCB technology. Characterized by their microvia technology, advanced connectors, and ability to support higher circuit density, HDI flex circuits outperform conventional flexible circuits in demanding applications. These boards feature intricate designs and can accommodate a greater number of components while maintaining superior signal integrity. By utilizing ultra-thin polyimide substrates and fine-line copper traces, HDI flexible circuit boards offer excellent electrical performance, enhanced reliability, and maximum miniaturization—attributes essential for today's consumer electronics, high-speed communication devices, and IoT products.
The single-sided flexible circuit is the most basic type of flexible printed circuit board (FPCB), featuring a single layer of polyimide or polyester insulating film bonded to a thin copper foil. The copper surface is etched (using precise photolithography) to create the desired circuit pattern and is usually protected by a cover layer of polyimide (PI) or polyester (PET) for increased insulation and environmental protection. These flexible PCB types are cost-effective solutions ideal for dynamic flexing applications, LED strip lighting, and simple interconnections due to their light weight, bendability, and ability to fit into tight spaces.
Dual-access single-sided flexible circuits offer unique design flexibility within a thin, lightweight package. While these FPCs feature only a single conductor layer (typically copper), specialized laser and processing methodologies allow for access to the conductor layer from both sides of the circuit board. This provides increased versatility for top and bottom component mounting or for making test pad connections. For designers seeking affordable solutions with accessible conductive layers, dual-access flexible PCBs are used in membrane switch assemblies, touch sensor panels, and complex interconnects relying on copper sheet technology.
Double-sided flexible circuits are manufactured with copper conductor layers on both sides of a central polyimide substrate, forming a dual-layered structure. Plated through-holes (PTH), or vias, electrically interconnect the two conductive layers, enabling more intricate routing and denser trace layouts crucial for advanced electronics assembly. These flexible PCB solutions support higher circuit complexity, enable crossover connections, and allow for surface mount device (SMD) integration on both sides. Double-sided flexible circuits are popular in automotive electronics, medical instrumentation, and portable consumer products requiring robust mechanical reliability and improved signal routing.
Multilayer flexible circuits incorporate three or more conductive layers, alternating between insulating dielectric substrates, to accommodate complex designs with high component density and advanced functionality. These multilayer FPCs leverage stacked designs, intricate interconnections, and strategic shielding to manage signal integrity, reduce crosstalk, achieve controlled impedance, and support electromagnetic interference (EMI) reduction. By incorporating ground planes and power distribution networks, multilayer flexible PCBs are the go-to choice for high-speed data transmission, military avionics, and medical imaging equipment where both space constraints and electrical performance are mission-critical.
Rigid-flex printed circuit boards combine the attributes of rigid PCBs and flexible circuits within a single unified structure—merging stiff, multi-layer rigid sections with one or more flexible interconnect zones. Electrical connections across these regions are typically accomplished with plated through-holes, allowing for three-dimensional configuration and robust mechanical stability. Rigid-flex PCBs are essential in mission-critical sectors such as aerospace, medical devices (like implantable electronics), and compact consumer electronics, as they reduce the need for connectors and cables, increase reliability, and enable innovative product designs. Components can be strategically mounted on the rigid segments for strength and support, while the flexible areas provide resistance to vibration, shock, and repeated bending cycles, ensuring durability and longevity.
When selecting the appropriate flexible printed circuit type for your project, consider critical factors such as flexural endurance, conductor trace width, application environment, assembly methods, and total cost of ownership. By matching your application's functional needs with the right FPC design—be it single-sided, double-sided, multilayer, HDI, or rigid-flex—you optimize product performance, enhance reliability, and achieve a lighter, more compact form factor. To explore supplier capabilities or request engineering support for custom flexible board manufacturing, consult with an experienced flex circuit manufacturer to ensure your product meets all design and industry compliance standards.
The automotive industry has greatly benefited from flexible electronics, which expand the design possibilities for dash panels, infotainment systems, and other vehicle electronics. Unlike traditional flat and boxy displays, flexible electronics offer a wide range of design options.
Furthermore, flexible electronics allow for more compact packaging, enabling components to fit into smaller engine compartments compared to conventional rectangular boxes that occupy more space. This flexibility allows car designers to prioritize making the vehicle more fuel-efficient, comfortable, and aerodynamic, and then adapt the electronics to fit the available space.
Flexible circuits are employed in various computer peripherals, such as connecting signals to the moving print heads of printers and the read/write heads of disk drives. They are also widely used in consumer electronics, including cameras, portable entertainment systems, calculators, and fitness trackers. In manufacturing and medical equipment, flexible printed circuits are essential for managing numerous interconnections within compact spaces. Cellular phones are another prominent example of devices that utilize flexible circuits.
Flexible circuits play a crucial role in the expanding industry of wearable technology, including devices like fitness trackers, smartwatches, and compact real-time medical monitors.
Because every human body has unique contours, flexible electronics are particularly well-suited for this application. Sensors can now adapt to the natural curves of the skin, eliminating the need for equipment to be worn tightly to ensure proper contact.
Recent research in flexible electronics has focused on medical applications. Beyond step trackers and calorie counters, advancements are being made in developing flexible devices for monitoring blood pressure, oxygen levels, glucose, and even blood alcohol content.
A device's display screen that uses finger pressure for interaction is called a capacitive touch screen. Handheld capacitive touch screen devices generally link to networks or computers using an architecture that can...
A membrane keyboard is a type of keyboard technology found in many electronic gadgets and appliances. A keyboard, as we all know, is essential hardware that...
Membrane switches are a type of human-machine interface characterized by being constructed from several layers of plastic films or other flexible materials...
Die cutting is the mass fabrication of cut-out shapes by shearing a stock material such as paper and chipboard using tooling called a die. A die is a specialized tool used in manufacturing to cut or shape a material fitted into a press...
Kiss cutting is a method for cutting into a material where the upper layers are pierced, but the back layer is left intact. The term "kiss" refers to the way the blade touches the upper layers of the material and leaves a pattern or cut with a sufficient amount of force to leave an impression...
A name plate is a method for displaying the name of a person, logo, product, or mechanism and is made from a variety of materials to serve as a long term identifier...