Capacitive Touch Screen
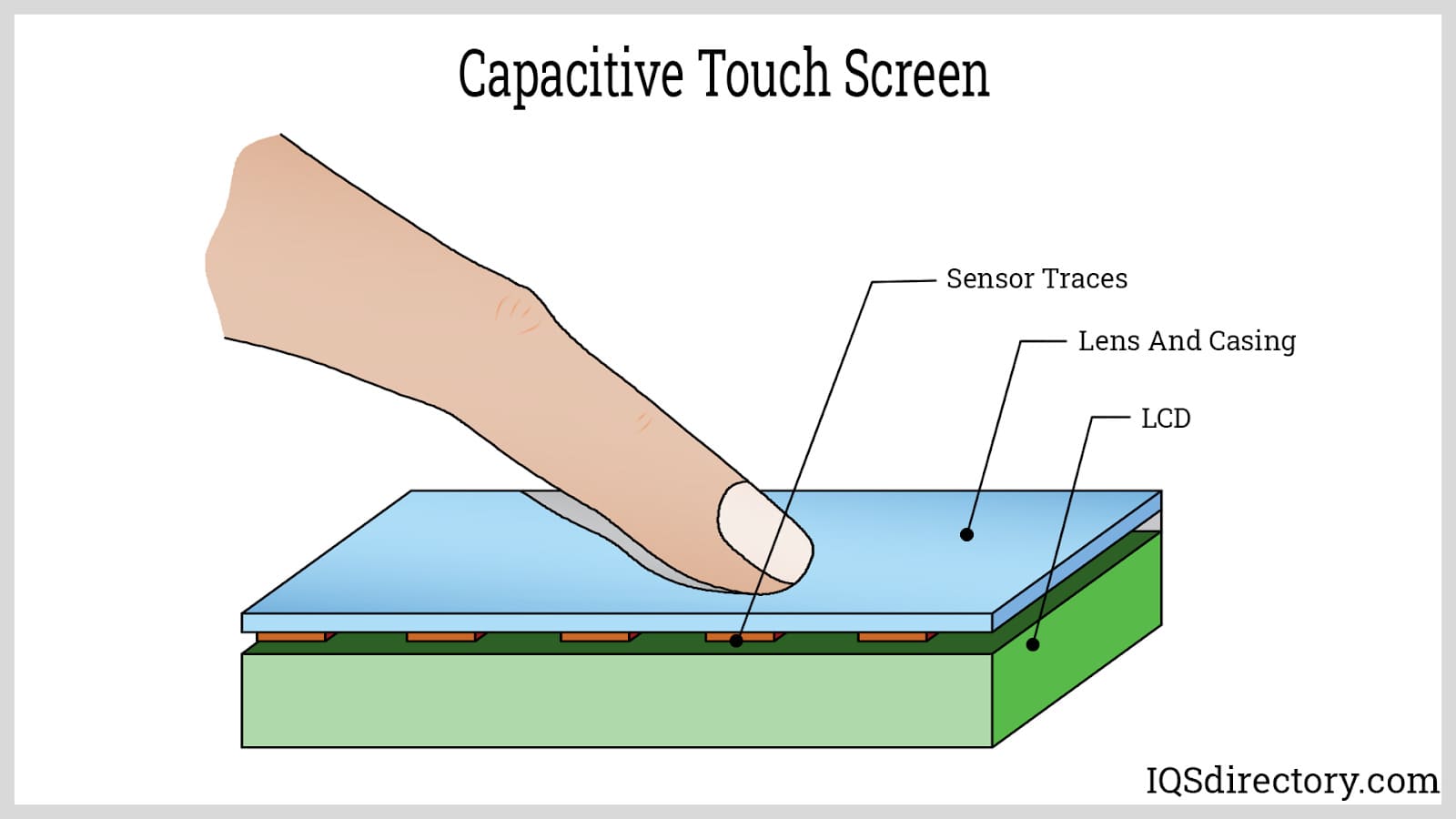
A device's display screen that uses finger pressure for interaction is called a capacitive touch screen. Handheld capacitive touch screen devices generally link to networks or computers using an architecture that can...
Please fill out the following form to submit a Request for Quote to any of the following companies listed on
Descriptions of graphic overlays, their use, and a list of graphic overlay manufacturers
You will learn:
Terms like graphic overlays, faceplates, dead front panels, and user interfaces describe relatively robust printed items affixed to equipment. They offer critical information about machine controls and switches, facilitating human-machine interaction. Installed on machinery, these overlays serve as essential guides for workers and contribute to workplace safety. By design, graphic overlays are crafted from durable materials such as polycarbonate, vinyl, or polyester. They may feature display windows, embossed buttons, vibrant colors, graphics, and various shielding types to enhance functionality.
In today's tech-driven world, graphic overlays play a crucial role in offering users straightforward and clear operating instructions. They are fundamental components that enable users to interface with electronic circuits and machinery. Early overlays were simply paper or plastic labels positioned near equipment controls, indicating switch or button functions. However, these primitive versions lacked durability and practicality for repeated use, prompting the evolution of more sophisticated and robust overlays.
Graphic overlays have been integral to a diverse array of machinery, tools, and products for decades, providing an appealing visual while serving crucial operational purposes. The explosive growth in commercial and industrial electronics has driven the creation of versatile overlay graphics to align with specific customer and product needs.
An essential part of the planning of a graphic overly is the design phase, which involves several factors. The functions of graphic overlays include protection of circuitry, guidance, product appearance, ease of operation, and information. Each of these factors, and others, are included in the design process.
The first step in the design process is a determination of the dimensions of a graphic overlay, which includes size, shape, thickness, and placement. Where a graphic overlay will be placed is dependent on the available space and how it is connected to circuitry. With modern equipment, ergonomics plays an important role to ensure user comfort, efficiency, and access.
Included in the basic specs of a graphic overlay are considerations regarding user interface. Graphic overlays provide access to the operation of equipment but must be placed in accordance with circuitry. In essence, graphic overlays provide the connection between the operator of equipment and the electrical circuits that send signals to various components of equipment.
The endless number of graphic overlays are used in a wide range of conditions from welding shops to schools to music production. Since the introduction of the computer age, there has been a need for keypads, buttons, directions, and information to direct users in the use of highly technical devices. The wide assortment of working environments necessitates choosing materials capable of enduring a variety of conditions. Temperatures, chemicals, moisture, UV rays, debris, impacts, and continuous use can damage the functions of a graphic overlay.
During the design phase, designers use data from users to determine the types of materials and printing method that will best fit the circumstances under which a graphic overlay will be used. As with many products, longevity is one of the main concerns since clients and customers expect products to endure.
Part of environmental factors is exterior lighting that provides visibility for a graphic overlay. Intense, extreme, and high-powered lighting may make a graphic overlay hard to see while dim light has the same effect. Such conditions necessitate the addition of backlighting to a graphic overlay, referred to as internal lighting.
Graphic overlay lighting is added as part of graphic overlay design, which can take the form of backlighting. The application of lighting requires the addition of components that will illuminate a graphic overlay’s surface. The types of lighting are diodes (LED), fiber optic, electroluminescence, and light guide film. Each type of lighting enhances the visibility of a graphic overlay and makes its operation more efficient.
Although the basic material of a graphic overlay may be highly durable and long lasting, manufacturers further enhance durability by adding various types of finishes, coatings, and treatments. This is especially true for hostile and stressful conditions where a graphic overlay has to endure impacts, heavy use, or other damaging factors.
The use of different finishing methods improves the looks, durability, convenience, and life expectancy of a graphic overlay. Some of the types of typical finishes include glossy, textured, metallic, anti-glare, protective, and sanitary anti-microbial.
The type of information on a graphic overlay is normally very brief and to the point. This is due to the limited space that is available. Such limitations require careful consideration of a graphic overlay’s information, which can include symbols, letters, and numbers. In many cases, the images printed on a graphic overlay are specific to the industry for which a device is manufactured. The typical on and off switch can take different forms.
The number of symbols is endless and ever growing as new equipment and processes are developed. Designers work closely with clients to ensure that the image placed on a graphic overlay has sufficient meaning to assist operators. As equipment and machines become more complex, their symbols become more difficult to decipher.
Of the many features of a graphic overlay, the color of an overlay is the first aspect that people respond to. Color is a critical part of the design phase since it plays a significant role in the appearance and appeal of equipment. Properly chosen colors have a positive effect on the function of machinery as well as providing aesthetic appeal.
At one point, there were a limited number of colors that could be printed on graphic overlay materials. In recent years, the numbers of available colors have expanded into the thousands giving engineers a wide range of choices. Colors for graphic overlays are printed from darkest to lightest. The specification of colors involves the use of the Pantone Matching System (PMS), which indicates how a color will appear on coated or uncoated material.
Cut outs are used for access to display screens and can take several forms. In some cases, the screen of a cut out may not display until activated due to the nature of the information it provides. Cut outs add an additional texture to graphic overlays creating an illusion of separate windows or access panels. Although the purpose of cut outs may be for additional display information, they can also be holes for fasteners and hardware.
The use of cut outs may not be necessary depending on the design of a graphic overlay. Cut outs are normally used with complex equipment as a method for offering alternatives and equipment operating instructions. During the design phase, engineers carefully walk customers through the use of cut outs since their determination is essential prior to graphic overlay construction.
The process for manufacturing graphic overlays involves several steps to ensure their quality and durability. Although all of the steps are essential and critical, material selection and printing are the most important since they provide information and determine the quality of a graphic overlay. During the design phase, engineers explain the qualities of graphic overlay materials and the printing process. This assists clients in choosing a proper match of a graphic overlay to its function.
Different printing methods are used to produce graphic overlays. In most cases, the type of material selected dictates the printing method. Although the types of printing methods are similar, some manufacturers specialize in one method while others offer a choice of methods. In most cases, the images to be printed determine how they will be printed. As the intricacy and number of details, images, and symbols increases, printing methods require more precision and craftsmanship.
The choice of materials for a graphic overlay are made in accordance with the nature and type of application for which the graphic overlay is produced. The first consideration for materials is endurance since different types of applications place stress on graphic overlay materials. After the consideration of endurance, a pleasing aesthetic appearance is necessary due to graphic overlays being the face of instruments and equipment.
Materials used to manufacture graphic overlays are polyester (PET), polycarbonate (PC), acrylic (PMMA), and vinyl, each of which have distinguishing characteristics and properties that make them ideal for different scenarios. There are specific mils, a measurement that equals 0.001 in or 0.0254 mm, of plastics that make them more desirable for the manufacture of graphic overlays. Most materials have a thickness between 5 mils and 20 mils. The deciding factor for any material is its ability to be cut with thicknesses over 20 mils being difficult to cut, although such materials can be cut but at an additional cost.
Printing techniques used to apply the graphics, text, and symbols to graphic overlays are of exceptionally high quality, due to the practical function of graphic overlays. The different forms of graphic overlay printing include screen printing, digital printing, thermal transfer, laser marking, UV printing, and laminate printing. Since a graphic overlay is the “face” of a product, its printing has to be inviting, pleasant, functional, and practical. Each part of a graphic overlay is carefully planned to ensure it properly adheres to its purpose.
Screen printing is a traditional printing method that has been used for many years to print images and text on clothing, cloth, paper, and plastic. Also referred to as silk screen printing, screen printing involves placing the desired graphics onto a screen that is secured tightly to a frame. The traditional method of screen printing, which is still used today to print T-shirts and sweatshirts, involves applying ink to the screen and transferring the inked image to the surface of the material.
For the mass printing of graphic overlays, the traditional method is too time consuming and labor intensive. Modern screen printing is automated and produces multiple images. The image for screen printing is imprinted on the screen through a developing process that makes the image transferable but prevents ink from seeping through non-pattern parts of the screen. Screen printing can be used on all types of graphic overlay materials and provides clear sharp printed images.
Digital printing was introduced in the early 1990s and went through various technological advancements before it became a viable printing method for high volume production. The process replaced the use of printing plates and made it possible to print images directly onto graphic overlays from digital files. Digital printing is a highly flexible printing method that allows design changes, corrections, and customization while providing exceptionally high image resolution for detailed and complex graphics.
The designs for digital printing are created using computer graphics software, which are downloaded into a computer-controlled printer. The printing process uses the same four-color printing method of CMYK as that of copy machines with greater accuracy and allows for the production of complex patterns and gradient effects. The digital process allows for printing text and images on dark, black, or transparent surfaces with exceptional clarity. As with screen printing, digital printing can apply text, images, and graphics to any type of graphic overlay material.
Thermal transfer printers have ribbons of wax or resin-based ink that melts onto the graphic overlay surface. The printhead for thermal transfer is an essential part of the printing process. It has heating elements that transfer heat through the thermal transfer ribbon (TTR) and onto the surface of the graphic overlay. Combined with pressure, the printhead heating process completes the printing process. The wax or resin ribbon is fed from an unwinder to the printhead and pulled through by a take up ribbon. The graphic overlay material is simultaneously fed through by a platen roller positioned just below the printhead.
The advantage of thermal transfer printing is the resilience and durability of the graphic overlays the process produces. Graphic overlays produced by thermal transfer are capable of withstanding hazardous and harsh conditions and are unaffected by direct sunlight or extreme temperatures.
Laser marking is a non-contact etching process that creates a permanent image. A laser beam etches the desired image, pattern, or text onto the surface of the material to create a meticulously crafted printed image. The concentrated light of the laser beam creates marks on the surface of the material using heat to alter the properties and appearance of the material. Regardless of the power of laser printing, it is ideal for the manufacture of graphic overlays since the wavelengths of the laser beam are adjustable.
Different types of laser beams with different levels of wavelengths are used to match the type of material. The two basic types of laser beams are fiber and CO2. Of the two methods, CO2 is used to print graphic overlays while fiber lasers are used with metals. Laser marking is a high precision process that produces exceptionally clear images and symbols. Markings are permanent and resistant to exposure to chemicals, abrasions, impact, and extremes of temperature.
UV printing is a form of digital printing that uses UV light to cure and dry the ink as it is printed. The purpose of adding UV printing to digital printing is to enhance the durability of the printed images and to keep the images from fading, scratching, and exposure to chemicals. The use of UV printing offers exceptional colors, unequaled accuracy, and uniformity. UV printing can be combined with 3D printing to create layers for raised images and graphics and can print on all types of graphic overlay materials.
With UV printing, images are printed onto the substrate after which the ink is exposed to UV light. The application of the UV light prevents the wet ink from spreading, which results in more detailed and higher resolution images. As the UV light shines on the ink, the ink immediately solidifies. The photomechanical process of UV printing differentiates it from other forms of printing that rely on solvent evaporation and heat to dry ink. UV printing is cleaner, safer, and eco friendly.
The benefits of UV printing include faster output, increased efficiency, higher durability, color sharpness, instant drying, consistency, and the ability to print on any type of material. A key characteristic of UV printed graphic overlays is their longevity, which is one of the main reasons that the use of UV printing is so rapidly growing.
Lamination printing is a protective process that applies gloss, matt, or silk to a printed graphic overlay during the printing process. The application of the laminate protects against tears and enhances the durability of graphic overlays and seals them against water damage. Like other forms of sealing materials, the added strength of laminates increases the life expectancy of a graphic overlay.
The laminate process is used in combination with a method of printing as an additional layer of protection. The essence of the process is to press a protective layer over the surface of a graphic overlay.
The printing methods outlined above are a sampling of the many methods used to produce graphic overlays. In addition, manufacturers are continually developing new and innovative methods that enhance their products, improve performance, and have exceptionally high quality. The graphic overlay industry is widely varied and includes the use of multiple manufacturing techniques. When looking for a producer, it is wise to thoroughly investigate a company’s techniques and methods in order to choose a process that fits an application.
The in mold decoration method for manufacturing graphic overlays is unlike the methods described above. The process of in mold decoration includes graphic overlay in the production of plastic products. Graphic elements are included in the molding process and the structure of plastic components. Instead of being applied to the surface of a product, graphics are baked into a product.
The process for in mold decoration is somewhat similar to other production methods. As with other graphic overlays, the overlay is printed on material using a special film. After being cut to the proper dimensions, it is placed in an injection mold, and resin is added. It is a labor-saving process that is versatile and efficient.
The process for in mold decorating:
The purpose of the adhesive backing is to securely attach a graphic overlay to a piece of equipment or control panel. The adhesive is designed to bond to a surface through the application of pressure. The configuration of the adhesive allows for cut outs and areas where adhesive is not necessary. During the application of a graphic overlay, the shape of the adhesive backing and its application is dictated by the technician that applies it.
Adhesive backings that are applied to graphic overlay materials are designed to match the substrate and take into consideration environmental conditions. Graphic overlays are interfaces, brand identifiers, and protective layers that are securely attached to equipment. They are carefully planned, designed, and created to provide information and directions. The key to their successful use is the adhesive that unites them with the surface of a control panel.
The four purposes of the adhesive are to provide secure attachment, environmental protection, easy equipment assembly, and exceptional performance and durability. They keep an overlay in place, tightly sealing its underside while simplifying the assembly process.
The choice of adhesive depends on an equipment’s surface energy, which is the surface metal or plastic, smooth or textured, flat or curved, and any powder coatings that have been used. Industrial strength adhesives provide exceptional bonding strength and durability. They are available as pressure sensitive, structural, and instant types. In the majority of cases, adhesives for graphic overlays are die cut for simple assembly and prevention of blurring or creeping into cut outs.
After the adhesive is attached to the back of a graphic overlay, it is cut, trimmed, and shaped to fit the space for which it was designed. The methods for cutting graphic overlays takes several forms with new forms being introduced using advanced technology. The traditional method used to cut a graphic overlay is a steel metal die that has the shape and dimensions of the overlay. Using pressure and force, the steel metal die punches a graphic overlay to remove excess material and shape the overlay. The punching shapes and forms a graphic overlay to the dimensions of its design and the graphics of the substrate. The process ensures a perfect fit for the space for which a graphic overlay has been designed.
Other methods used to cut out a graphic overlay are digital cutting and class 1 die sets, which are used for thin graphic overlays. Thicker graphic overlays of 20 mils or greater are cut using digital routing, laser, or water jet. Steel dies are a physical method of cutting while other cutting processes use computer programming to guide cutting tools. The design of steel dies various and can include a block of wood into which the blades in the shape of a graphic overlay are mounted. Technologically advanced methods have complex and intricate mechanisms with a unique structure.
The differentiating factor between the different die cutting methods is the volume of graphic overlays being made. High volume production is best served by steel dies mounted on a drum that rapidly rotates to cut graphic overlays from the base material. More complicated low volume graphic overlays are normally cut with great precision using a computer technology.
Regardless of the method chosen to shape a graphic overlay, it is essential that it maintain high accuracy and tight tolerances for dimensional alignment. A key aspect of the cutting process is an examination of the final product. This includes placement of buttons, displays, and images and compliance with design parameters. As with all industrial products, quality check of a graphic overlay ensures that it meets the standards established by the customer.
The many features and uses of graphic overlays is contingent on the materials from which they are made. The base material serves as the foundation for graphic overlays and is where the functions of a graphic overlay are imprinted. Materials have to be robust enough to endure constant use and be durable enough to last, as well as provide a pleasing and practical appearance.
The selection of materials for graphic overlays includes polyester (PET), polycarbonate (PC), vinyl, polyvinyl chloride (PVC), acrylic, and aluminum. Since the impressions for graphic overlays are printed on clear material on its backside in reverse, the ink of the graphics is never exposed. The thickness of the base material protects the graphics and serves as a strong support. In essence, the images, displays, and visuals are encapsulated between the base material and the adhesive backing, a configuration that adds durability, strength, protection, and a long life.
Polyester is used for the manufacture of graphic overlays due to its exceptional durability. The chemical resistance of polyester is one of the main reasons that it is so widely used. Although not true of all forms of polyester, most polyester materials are resistant to UV rays, which makes them applicable for outdoor applications. A common practice with polyester overlays is to coat them with anti-bacterial compounds so that they can be applied to equipment used in cleanrooms, medical facilities, and pharmaceutical laboratories.
The material used to produce polyester is a synthetic thermoplastic polymer made from the polymerization of terephthalic acid and ethylene glycol. Polyester was introduced to the public in the 1950s after being researched for over thirty years. Activation switches and buttons produced using polyester can endure millions of actuations without splitting, cracking, or deteriorating. Polyester is considered to be the toughest, most durable material available.
Polyester comes in thicknesses of 0.005 in up to 0.010 in for indoor use and 0.006 in and 0.008 in for outdoor use. It is not flame retardant and comes in a limited range of textures. Polycarbonate offers clearer images and graphics.
The outstanding feature of polycarbonate is its excellent appearance that provides sharp clarity. It is made from the polymerization of bisphenol A (BPA) and phosgene. The main characteristics of polycarbonate is its impact resistance, high temperature stability, and exceptional optical transparency. In comparison to polyester, polycarbonate comes in a wider selection of textures and colors.
Included in the characteristics of polycarbonate are its UV resistance, chemical resistance, formability, and thermal stability. The flexible formability of polycarbonate enables designers to produce intricate and complex shapes using polycarbonate’s exceptional printability. Precise and vibrant graphics are easily displayed on its surface. Its UV resistance prevents it from yellowing or degrading over time.
The outstanding feature of vinyl is its flexibility, compared to the other graphic overlay materials. It can be bent, curved, configured, and contoured into regular and irregular shapes. Vinyl can be applied directly due to its natural static cling or be mounted using an adhesive backing.
One of the main reasons for choosing vinyl is its low cost in comparison to polycarbonate and polyester, which is due to vinyl’s low durability and inability to withstand abrasions, weather, or chemicals. Vinyl is widely used in less stressful conditions and normally has a glossy, matt, or clear finish as protection.
Vinyl overlays have a printed design or solid color. They are commonly used for applications where information is constantly changing, since they can be easily removed and replaced. Vinyl overlays are not designed to last and must be treated with care when in use. Cleaning and upkeep for vinyl overlays is completed using non-toxic cleaning products such as dish or hand soap.
Acrylic is a transparent thermoplastic polymer that is lightweight and made by the polymerization of the liquid monomer methyl methacrylate. It has the greatest clarity of all of the graphic overlay materials, which is similar to that of glass. Acrylic is commonly used for transparent overlays and backlit control panels. The resistance of acrylic to UV rays makes it ideal for outdoor use and applications where equipment is constantly exposed to UV rays.
The scratch resistance of acrylic helps it maintain its aesthetic appearance. It can be scratched when subjected to materials with high hardness, which can be overcome with the application of a protective coating. Since acrylic can be printed on using any of the recommended methods, graphic overlays will have high quality graphics with sharp vibrant colors. The clarity, versatility, and durability of acrylic has made it a highly sought after graphic overlay material.
As with vinyl graphic overlays, PVC overlays are less expensive than polycarbonate and polyester graphic overlays. The strength of PVC overlays makes them suitable for any environment due to their resistance to abrasions and scratches, chemicals, and the effects of corrosive materials. PVC overlays have low to medium strength and durability properties that give PVC overlays a shorter life. The surface hardness of PVC graphic overlays limits their use to applications that do not have membrane switches or touch panels.
The properties of PVC are somewhere between polyester and vinyl. It is not as strong as polyester but can be adjusted and textured to increase its strength to match polyester. A broad range of colors, finishes, and textures are available for the design of PVC graphic overlays. The characteristic that has increased the use of PVC graphic overlays is their exceptionally pleasing appearance.
Embossing and backlighting are special features that are added to graphic overlays during production. They enhance and simplify the user experience and are customized to fit a client’s specifications. These additional features are designed to increase the efficient use of equipment and provide a direct interface with the electronics of a device.
Graphic overlays are vital and important components for manufacturers. They clarify equipment, machine, and device operations to ensure quick and efficient performance. Several features are added to graphic overlays to make users more comfortable. Although the list of features contains a long list of proprietary and custom enhancements, embossing and backlighting are two commonly used ones.
Embossing is raised areas on a graphic overlay that provides a physical response to user touch. The process of embossing accentuates key areas of a graphic overlay and can be included to raise LEDs to offer a decorative effect. The embossing of keys helps operators to quickly find a key, enhances the feel of buttons, and provides a three-dimensional appearance. The process of embossing pushes the plastic material upward from its surface.
The presence of embossing is an indication of the presence of a switch, which is usually a membrane switch that has a conductive layer covering a domed shaped actuator. The pushing of the embossed button connects it with the conductive layer and actuator. Although it is a simple tactile layer to the user, in actuality, it is a connection to the functions of a device.
Two ways to emboss graphics are hard tooled and print. With hard tooled embossing, a male or female die is used to make an impression on the substrate. It is a mechanical process that is selectively and carefully administered. Embossing raises the substrate to heights 0.005 in up to 0.015 in with widths of 0.04 in up to 0.07 in. The height of embossing is limited to six times the thickness of the graphic overlay material.
Print embossing is a non-mechanical process that involves adding layers to the surface of the substrate by passing ink multiple times over the surface. It is a stressless process that does not deform the surface of a graphic overlay. Since the embossing process leaves the graphic overlay flat, the overlay has greater adhesion. The height of print embossing is limited to 0.006 in up to 0.010 in.
Two forms of graphic overlay buttons are rim and pillow. Rim embossing creates a border around buttons, which differentiates the buttons from the surface of a graphic overlay. It is commonly used in applications where precision control is necessary. Pillow embossing is the raised surface type of embossing that creates a domed appearance. The configuration of pillow embossing ensures contact and provides tactile feedback regarding the activation process. The domed surface highlights a button and makes the activation process distinguishable. As part of the inclusion directive, embossing may have tactile letters, such as braille.
Since graphic overlays are a small portion of equipment, they can necessitate the use of light to enhance their readability. It is an optional feature that can be added to a graphic overlay to make switches, instructions, displays, and images more visible. Backlighting creates a dramatic effect in different environments and is a vital part of instruments on motorized equipment.
The traditional forms of backlighting are incandescent and LED lights that are attached to a subpanel. The use of backlighting influences the functionality of a graphic overlay and improves its aesthetic appearance. The choice of backlighting affects graphic overlay design, material, and color.
Backlighting choices include:
Light-Emitting Diodes (LED) – LED lights are widely used due to their reliability, longevity, and low cost. Combined with other light sources, LED lights can be designed to light the entire surface of a graphic overlay.
The use of graphic overlays covers a wide spectrum of devices from kitchen appliances to space craft. In the modern era, graphic overlays have become an essential part of manufacturing as a method of providing users with an easy interface. What used to require weeks of training to operate complex equipment has been simplified into several days. The purpose of a graphic overlay is to provide an interface for users to interact with products.
The instructions provided by a graphic overlay provides guidance for the operation of a device. As the complexity of equipment increases, clear and concise instructions become crucial to the safety of operators. Certain types of equipment require graphic overlays that meet the standards of the National Fire Protection Association (NFPA) regarding the protection of operators and hazardous conditions under NFPA standard 79.
The more practical aspect of graphic overlays is their ability to prevent dirt, moisture, debris, chemicals, and other matter from contaminating electrical circuits. The film material combined with the adhesive backing create a solid impenetrable barrier from outside elements. The most crucial component of a graphic overlay’s protection is providing a layer of protection for mechanical electrical components.
The quality of graphic overlay protection is dependent on certain design factors. Cut outs have to be sized and installed correctly. During the cutting and shaping phase of production, graphic overlays must be cut to dimensional tolerances.
Not considered to be a necessary part of graphic overlay functions, the promotion of brand image has become one of their major components. The crisp sharp colors and strategically placed images promote the manufacture of equipment and devices. They are printed in brand colors and may contain a brand's tagline or slogan. The strength and durability of a graphic overlay supports the principles of the brand it displays.
Graphic overlay manufacturers take pride in the stability and strength of their products. Activation switches and buttons are guaranteed to be protected under the layers of a graphic overlay for the lifetime of a piece of equipment. The inclusion of a graphic overlay ensures the life expectancy of equipment controls and circuits. The layer of coverage prevents accidental activation, breakage, and accidental offs. Embossed buttons and switches cannot be pushed too far or fail at a critical time.
Common Types of Graphic Overlays:
Industries that use Graphic Overlays:
Machinery That Use Graphic Overlays:
A device's display screen that uses finger pressure for interaction is called a capacitive touch screen. Handheld capacitive touch screen devices generally link to networks or computers using an architecture that can...
Simply put, a flexible printed circuit (abbreviated FPC) has conductive traces on a thin, flexible substrate. "Flexible printed circuits." are circuit boards that can twist or bend. This claim makes it clear that they can be distinguished by...
Membrane switches are a type of human-machine interface characterized by being constructed from several layers of plastic films or other flexible materials...
Die cutting is the mass fabrication of cut-out shapes by shearing a stock material such as paper and chipboard using tooling called a die. A die is a specialized tool used in manufacturing to cut or shape a material fitted into a press...
Kiss cutting is a method for cutting into a material where the upper layers are pierced, but the back layer is left intact. The term "kiss" refers to the way the blade touches the upper layers of the material and leaves a pattern or cut with a sufficient amount of force to leave an impression...
A name plate is a method for displaying the name of a person, logo, product, or mechanism and is made from a variety of materials to serve as a long term identifier...