Aluminum 1100
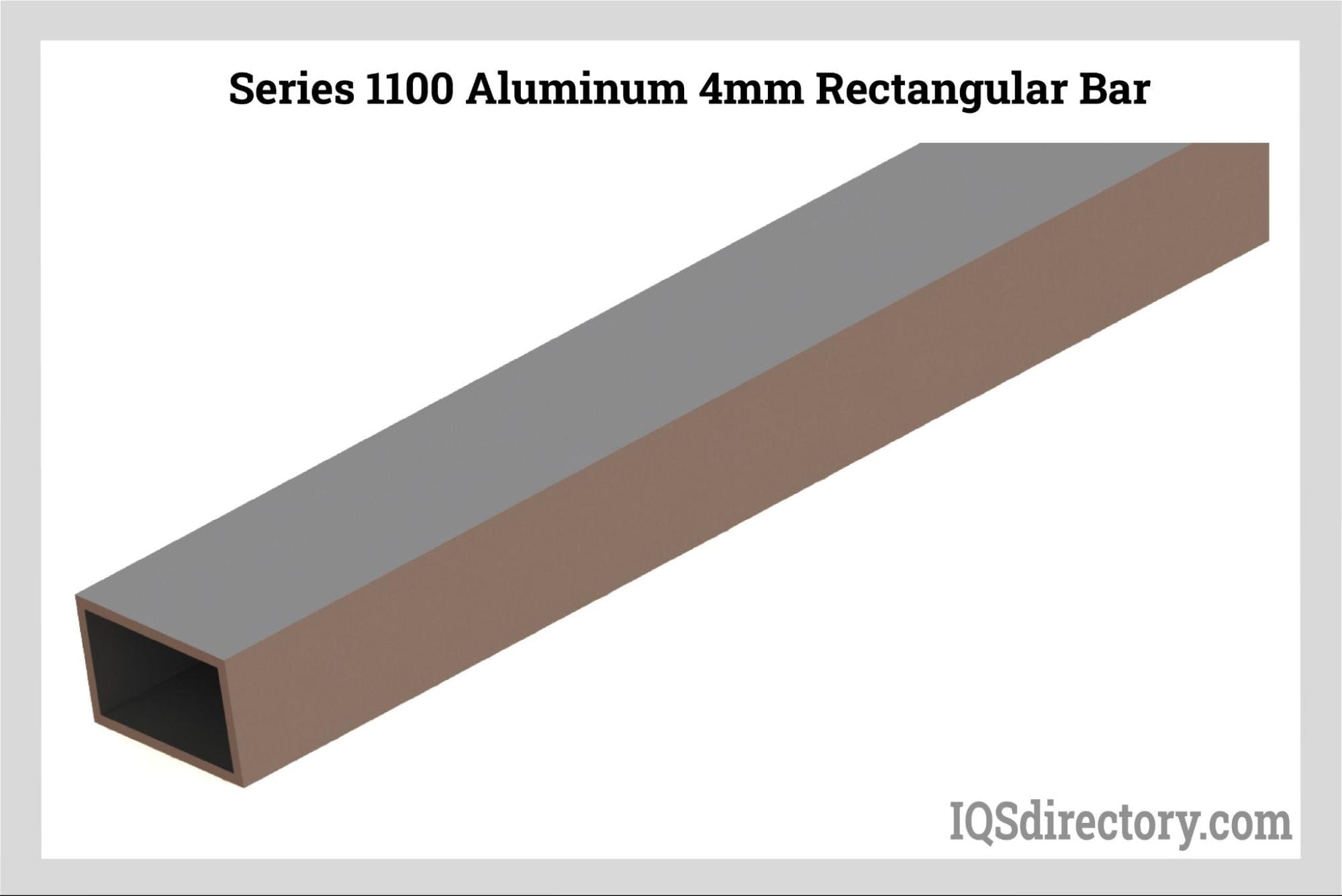
Aluminum 1100 is the softest of the aluminum alloys, which makes it easy to shape and form into a wide range of products for industrial and home use. It can be cold and hot worked but is frequently shaped by...
Please fill out the following form to submit a Request for Quote to any of the following companies listed on
This article will take an in-depth look at metal alloys.
The article will bring more detail on topics such as:
This chapter delves into the essence of metal alloys and their distinctive attributes.
Metal alloys emerge from the fusion of two or more elements to create a novel material. These can wholly consist of metals or a blend of metals and non-metals. Although the combination forms a fresh alloy, it retains inherent properties of the original metals, such as electrical conductivity, opacity, ductility, and luster.
However, these alloys might possess characteristics that differ from pure metals, like increased hardness or strength. In some scenarios, an alloy maintains the essential metal properties while lowering the overall material costs. Furthermore, alloys' chemical combination can impart enhanced traits to the component metals, such as improved resistance to corrosion and strengthened mechanical properties.
For practical purposes, the composition of alloys is typically expressed in mass percentage, whereas fundamental scientific research often uses atomic fraction. Alloys are classified by their atomic structure: substitutional alloys, where base metal atoms are replaced by other elements; interstitial alloys, with smaller atoms fitting into the gaps between metal atoms; and heterogeneous alloys consisting of multiple distinct phases. Moreover, alloys can be categorized into intermetallic compounds or homogeneous alloys, characterized by a single phase. An alloy may be a mixture of diverse metallic phases or a solid solution, where all crystalline structures share a uniform composition.
An alloy is a blend of chemical constituents forming a material with metal-like qualities, merging at least one metal with other elements. Unlike impure metals, such as wrought iron, which are less refined yet useful, alloys are meticulously engineered for specific attributes. The primary metal in the alloy is often termed the base or primary metal, and the alloy is usually named after it. The other components, which might be metals or non-metals, dissolve in the molten base metal and integrate into the mixture.
The mechanical features of alloys often significantly differ from their base metals. For instance, alloying a metal like highly malleable aluminum with a softer metal such as copper enhances its strength. Although both metals exhibit ductility and softness, the aluminum alloy becomes more robust.
Introducing a small proportion of non-metallic carbon to iron transforms its excellent ductility into the substantially stronger alloy known as steel. Steel is a highly practical and widely-utilized alloy due to its exceptional strength, notable toughness, and flexibility through heat treatment. Furthermore, steel can be tailored for specific applications: adding chromium boosts its resistance to corrosion, creating stainless steel, or integrating silicon enhances electrical conductivity, producing silicon steel.
Pure metals consist of a single type of atom and exhibit a uniform structure, making them single-phase metals. In contrast, alloyed metals are combinations of pure metals mixed in specific percentages to create a composite with distinct properties. Pure metals have defined mass, melting point, and physical characteristics. However, pure metals, with some exceptions, generally lack the strength, toughness, and durability of alloyed metals, which is why they are often used as components in alloys.
All metal products incorporate a form of pure metal that has been alloyed. While the periodic table lists numerous pure metals, only a few are widely used in commercial products and are present in various metal items. Metals such as iron, aluminum, copper, zinc, titanium, chromium, and nickel are commonly used to manufacture both commercial and industrial products.
Alloys derived from pure metals play a crucial role in modern society. Metallurgists and engineers continually explore innovative methods to blend pure metals, creating alloys that are both strong and durable. During the Bronze Age, early metallurgists developed techniques to mix pure metals, resulting in stronger and more resilient products. To qualify as "pure," a metal must consist of 99% or more of that metal without any alloying.
Copper was among the first metals discovered by humans. Known for its remarkable malleability, it also boasts excellent thermal and electrical conductivity. Copper's resistance to corrosion and its durability make it a valuable material. Unlike many pure metals, copper is frequently utilized in its pure form, especially in electronic products, due to its superior conductivity. Additionally, its resilience in high-moisture environments contributes to its long-lasting nature.
Similar to copper, aluminum is utilized in its pure form because of its excellent thermal and electrical conductivity, ease of workability, and resistance to corrosion. Pure aluminum, which is soft and has a silvery-white appearance, belongs to the boron group of metals and has an atomic number of 13. In addition to its various alloys, pure aluminum is commonly used in power lines, beer kegs, window frames, automobiles, and kitchen utensils. When exposed to oxygen, aluminum develops a protective oxide layer that safeguards its surface from environmental damage.
Iron is a hard, brittle metal that corrodes when exposed to moisture and high temperatures. Most of the iron mined is used to produce steel by alloying it with carbon. Its widespread use is due to its affordability and strength. Iron is a gray, silvery metal with magnetic properties and reacts readily with acids. It rusts easily in the presence of air and water, which is why it is typically alloyed to maintain its strength. Pure iron is 99.8% iron, with small amounts of carbon, manganese, and other elements.
Nickel, similar to aluminum, develops a passivation layer when exposed to oxygen, which safeguards it against corrosion. While both nickel and aluminum are silver-white metals, nickel has a distinct golden hue. Nickel is a hard, ductile metal with chemical reactivity and is magnetic at room temperature. Its corrosion resistance makes it a popular choice for alloys and coatings. Nickel is commonly used in products such as wiring, batteries, and electrodes. Additionally, like copper and aluminum, nickel exhibits excellent thermal conductivity, which is why it is also utilized in heat exchangers.
Chromium is a pure metal known for its ability to form a protective oxide layer. It is a lustrous, brittle, and hard metal primarily used in producing stainless steel and for plating, thanks to its bright, polished finish. Chromium can exist in various oxidation states ranging from -2 to +6, with the +0, +3, and +6 states being the most stable. Its widespread use stems from its shiny appearance, which enhances the aesthetic appeal of products like cars and household appliances.
Pure zinc is utilized as a protective coating because of its excellent corrosion resistance. This bluish-white metal is commonly used in alloys. In the galvanization process, a layer of zinc is applied to iron and steel, significantly enhancing their resistance to corrosion. Zinc is also alloyed with aluminum and copper to boost their strength, durability, and other properties. As the zinc content increases, copper and aluminum alloys become stronger, more durable, and highly resilient, though they also become more challenging to work with.
Titanium boasts a high strength-to-weight ratio, is highly resistant to rust, and can withstand a wide range of chemicals. The pure titanium grades are 1, 2, 3, and 4. Grade 1 is the softest and most formable, while Grade 2 offers increased strength. Grade 3 provides even more strength, is weldable, and highly resistant to corrosion. Grade 4 is the strongest of the pure titanium grades, though it is the least malleable. It is durable, strong, and weldable, and can be cold worked. Among pure metals, titanium is particularly versatile, as it can be used in its pure form or alloyed with other metals to create exceptionally durable materials.
The different types of metal alloys are:
Steel is an alloy primarily composed of iron with a small amount of carbon, which enhances its strength and resistance to fractures. The temperature of steel affects its crystalline structure, which can be either body-centered cubic or face-centered cubic. The way iron's allotropes interact with other elements in the steel imparts its distinctive and unique properties.
Carbon steel is divided into three types, which are low carbon, medium carbon, and high carbon, with low carbon containing 0.3% carbon, medium 0.6%, and high 1.5%.
Alloy steels are produced by blending carbon steel with additional elements like chromium, cobalt, molybdenum, nickel, tungsten, or vanadium. This combination allows for the creation of steel with a diverse range of properties. While alloy steels can be expensive, their superior resistance to corrosion and wear makes them a valuable choice. The specific mix of alloys used affects the steel's strength and durability.
Tool steel is designed for manufacturing tools and is renowned for its hardness, heat resistance, and durability against abrasion. It comes in six distinct grades, including:
In addition to the various types of steel alloys, steel is categorized based on its intended applications, manufacturing processes, and smelting methods. The production of steel involves processes such as hot and cold rolling, drawing, casting, and forging. Smelting methods further classify steel into categories like rimmed steel, killed steel, and semi-killed steel.
Steel is an alloy primarily composed of iron and carbon. When steel contains at least 10.5% chromium, less than 1.2% carbon, and other alloying elements, it is classified as stainless steel. Additional elements like nickel, molybdenum, titanium, niobium, and manganese can be incorporated to enhance the steel's mechanical properties and resistance to corrosion. The chromium in stainless steel reacts with oxygen to form a thin layer of chromium oxide on the surface. This passive layer is responsible for stainless steel's remarkable resistance to rust and corrosion.
Stainless steel items are easy to clean, as common cleaning agents like detergents and soap powders are effective without scratching the surface. Its durability makes stainless steel ideal for decorative pieces and kitchenware that require frequent and thorough cleaning. Additionally, stainless steel offers various surface textures, including matte, shiny, brushed, and etched.
Stainless Steel Types | Composition |
---|---|
Ferritic | 0.08-0.2% Carbon, 11-18% (17%) Chromium, Iron |
Martensitic | 0.2-1% Molybdenum, Iron, 0.1-1% Carbon, 12-14% Chromium |
Austenitic | 0.15-2% Carbon, Iron, 10-20% Nickel, 17 – 25% Chromium |
Duplex | 1-6% Nickel, Iron, < 5% Molybdenum, 19-28% Chromium |
Stainless steel is a unique and aesthetically pleasing material that can be embossed or colored. Architects often use it for street furniture, interior design, and building exteriors. Its mechanical strength at room temperature surpasses that of most other materials, making it a preferred choice for various applications.
It is notably ductile, elastic, and hard, making it suitable for demanding metal-forming processes such as deep stamping, flat bending, and extrusion. This material also offers high resistance to severe wear, including friction, abrasion, impact, and elasticity, while delivering excellent mechanical performance across both low and high temperatures.
With a critical temperature above 1472°F (800°C), stainless steel offers the best fire resistance of all metallic materials when employed in structural applications. Stainless steel has a fire resistance rating of A2S1D0 and emits no harmful fumes.
Alloys made of aluminum are very robust, reliable, and adaptable. They are one of the most popular metal materials, along with steel, and are highly sought-after in engineering, construction, and automotive applications. Iron, copper, magnesium, silicon, and zinc are elements commonly used in aluminum alloys. When aluminum is molten (liquid), the alloy components are combined, and when it cools, a homogeneous solid solution is created. These other elements could account for up to 15% of the alloy's bulk.
Alloys containing aluminum are often valued for their lightweight nature and corrosion resistance. While pure aluminum has notable properties, it lacks the strength needed for many high-durability applications. To address this, aluminum is alloyed with other elements to enhance its robustness and suitability for industrial uses. Aluminum alloys are particularly advantageous when engineers need to reduce the weight of a product, such as an airplane, without compromising its strength.
With the right combination of components, aluminum can become significantly stronger and, in some cases, even surpass steel. Many aluminum alloys offer the benefits of pure aluminum while being more cost-effective, thanks to their lower melting points.
Nickel readily alloys with various metals like chromium, iron, molybdenum, and copper, allowing for the creation of diverse alloys with remarkable properties. These alloys often display exceptional high-temperature strength, excellent corrosion resistance, and resistance to high-temperature scaling. Additionally, they may feature unique properties such as shape memory, where the metal returns to its original shape upon heating, and a low coefficient of expansion, which measures how much the material expands when heated.
The chemical industry relies on pure nickel for its excellent corrosion resistance, particularly against alkalis. Additionally, its ability to shield against electromagnetic interference makes it valuable for use in transducers.
Nickel-iron alloys are chosen for glass-to-metal seals and soft magnetic materials due to their thermal expansion properties. Invar (UNS K93600), with 36% nickel and the remainder iron, is particularly notable for its minimal thermal expansion at room temperature. This characteristic makes Invar ideal for applications requiring high dimensional stability, such as precision measuring instruments and thermostat rods.
Due to its exceptionally low thermal expansion rates, this material is also suitable for cryogenic temperatures. Alloys containing 72–83 percent nickel exhibit the best soft magnetic properties and are commonly used in transformers, inductors, magnetic amplifiers, magnetic shields, and memory storage devices. Nickel-copper alloys, such as the widely used Alloy 400, are highly resistant to corrosion from seawater, non-oxidizing salts, and alkaline solutions.
Without the presence of oxidizing ions such as cupric (copper-based) and ferric (iron-based), or dissolved oxygen, nickel-molybdenum alloys exhibit significant resistance to reducing acids. On the other hand, nickel-chromium alloys are noted for their exceptional electrical resistance, robust high-temperature strength, and impressive corrosion resistance at both standard and elevated temperatures, including resistance to scaling.
Modern bronze typically consists of 88% copper and 12% tin. Historically significant, bronze remains widely used due to its unique properties. Compared to pure copper, bronze is more durable because it is alloyed with tin or other metals. It also melts more easily, facilitating casting. Moreover, bronze is more corrosion-resistant and tougher than pure iron. Although iron eventually replaced bronze in tools and weapons due to its greater availability, rather than superior strength, bronze continues to be valued for its durability and historical significance.
Aluminum bronze contains between 6% and 12% aluminum, iron, and nickel. This robust alloy is known for its excellent wear and corrosion resistance, making it an ideal choice for applications such as pumps, valves, and other hardware subjected to corrosive fluids.
Cupronickel is a bronze alloy composed of copper and 2% to 30% nickel. It is renowned for its excellent thermal stability and corrosion resistance, particularly in steam or moist air environments. Cupronickel outperforms other bronze types in seawater, making it ideal for use in ship hulls, pumps, valves, electronics, and marine equipment.
Cupronickel is a bronze alloy composed of copper and 2% to 30% nickel. It is renowned for its excellent thermal stability and corrosion resistance, particularly in steam or moist air environments. Cupronickel outperforms other bronze types in seawater, making it ideal for use in ship hulls, pumps, valves, electronics, and marine equipment.
Despite its name, nickel silver contains no actual silver. The name comes from its silvery appearance. Nickel silver is composed of zinc, nickel, and copper. It offers moderate strength and fair corrosion resistance. This versatile material is commonly used in dinnerware, decorative items, optical devices, and musical instruments.
Tin bronze, also referred to as phosphor bronze, contains 0.01% to 0.035% phosphorus and 0.5% to 1.0% tin. This alloy is known for its fine grain, low friction coefficient, and excellent fatigue resistance, making it both durable and strong. Phosphor bronze is commonly used in applications such as bellows, washers, electrical equipment, and springs.
The majority of titanium alloys feature titanium as the primary metal while also containing small amounts of other metals or substances. Like other alloys, titanium alloys are created by combining titanium in a certain proportion to other metals and chemical components. The mixture is allowed to cool after the ideal ratio has been reached. The titanium alloy material is then sold, transported, or used in another way.
Pure titanium is primarily used for orthopedic and dental implants, while titanium alloys find applications in a variety of fields including aerospace engineering, high-temperature engines, medical and marine processing, and athletic equipment. Although titanium appears in trace amounts in many other metal alloys, they are not classified as titanium alloys unless titanium constitutes a significant portion of the mixture.
Titanium alloys come in various types, each consisting of pure titanium combined with other metals or elements. For example, alpha titanium alloys incorporate alpha stabilizers such as oxygen or aluminum, which impart their unique properties.
Conversely, near-alpha titanium alloys contain a limited amount of beta-stage stabilizers. Grade 1 titanium alloy, known for its softness and ductility, is the most manageable for cold-forming metalworking techniques. In contrast, Grade 38 titanium alloy offers significantly higher tensile strength.
There are 38 common types of titanium alloys, with Grade 5 being the most prevalent. This particular alloy consists of 90% titanium, 6% aluminum, and 4% vanadium. While titanium alloys range from Grades 1 to 38, with Grade 38 being the latest development, these grades are listed in chronological order of creation and do not indicate the strength or other characteristics of the alloys.
Titanium Grade 5, also known as Titanium 6AL-4V, is considered suitable for military applications. This titanium alloy, stable at temperatures up to 752°F (400°C), is commonly used in high-temperature, rapidly rotating aircraft turbines.
Columbium, also known as niobium, is a shiny, ductile metal primarily used in alloys to improve the properties of steel. It is commonly employed in structural applications, jet engines, and gas pipelines. Due to its corrosion resistance and high-temperature performance, niobium metal plates, rods, and sheets are used as sputtering targets and in chemical processing equipment. At extremely low temperatures, niobium becomes a superconductor, which is essential for creating powerful electromagnets used in particle accelerators and magnetic resonance imaging (MRI).
Niobium alloys are known for their high-temperature strength and resistance to creep and cold flow, although not as pronounced as molybdenum. They offer excellent thermal conductivity due to their high melting points and exceptional chemical resistance, including against liquid lead alloys. These properties make them ideal for use as structural materials in fuel assemblies and rod coatings in commercial high-temperature Liquid Metal Fast Reactors (LFRs). While niobium alloys, such as C-103 (89 wt% Nb, 10 wt% Hf, 1 wt% Ti) and Nb-1Zr (99 wt% Nb, 1 wt% Zr), have slightly lower strength compared to molybdenum alloys, they are generally easier to fabricate and work with. Niobium alloys, like other refractory materials, can be produced through powder metallurgy to achieve properties similar to those of wrought products. They are also readily weldable using TIG or other welding techniques.
Tantalum is a refractory blue-gray metal known for its ability to endure high temperatures while retaining essential physical and chemical properties. Tantalum-tungsten alloys are characterized by their high melting point and exceptional stress resistance. These alloys combine tantalum's high corrosion resistance with tungsten's extreme melting point, the highest among elements on the periodic table. Initially, tantalum's chemical inertness and high melting point made it ideal for use in dental equipment and incandescent light bulb filaments.
Tantalum has long been prized for its exceptional corrosion resistance in conditions that are harsh for most metals. Known for its durability, tantalum's corrosion resistance is often likened to that of glass, yet it remains both ductile and strong, comparable to steel. When exposed to oxygen, tantalum forms a passive oxide layer on its surface, enhancing its corrosion resistance. Currently, the bulk of tantalum produced is utilized in the electronics industry, primarily for capacitors. Tantalum powders are pressed and sintered to create porous anodes used in various electronic applications.
Tantalum oxide forms anodically on tantalum, creating a layer that provides tantalum capacitors with exceptional stability and dielectric properties. This layer’s performance makes tantalum capacitors ideal for applications that require compact sizes and high reliability across a broad spectrum of operating voltages and temperatures. Consequently, tantalum capacitors are widely used in critical sectors such as military, aerospace, and healthcare.
Tungsten alloys, commonly referred to as heavy alloys, generally contain 90–97% tungsten, with the remaining metals serving as a matrix to enhance the alloy's ductility and machinability. Unlike steel or aluminum alloys, which have standardized names, tungsten alloys are often custom-produced by different manufacturers for specific applications, resulting in no uniform naming convention.
Tungsten is an excellent alloying component and can also serve as the foundation for other alloys; in the alloying process, tungsten has become a crucial component. Tungsten’s unique characteristics help endow base metals with high strength, corrosion resistance, and other beneficial qualities. Common alloys of tungsten include:
In the heavy metals sector, tungsten-nickel-iron alloys are the most popular alloys. Because they are generally unmatched by almost any other metal alloy in terms of density, ductility, and strength, tungsten-nickel-iron alloys are very common.
In the metals industry, nickel-copper alloys play a crucial role in certain applications. Copper alloys are essential when magnetic permeability is a factor. Although copper has lower tensile strength and ductility, it remains valuable for various applications such as cancer treatment systems, shielding electrical sensors, and components in rotational inertia systems due to its non-magnetic properties.
Tungsten carbide stands out as the most important tungsten compound due to its beneficial characteristics. On the Mohs scale of mineral hardness, it ranks between 8.5 and 9, just below diamonds, which score a solid 10. Tungsten carbide’s density and stiffness fall between lead and gold, and it is nearly twice as rigid as steel. This compound is created through a chemical reaction between carbon powder and tungsten metal powder. Tungsten carbide inlays are highly resistant to chemical corrosion and damage, while retaining the inherent strengths of pure tungsten. Remarkably, 60% of all tungsten applications use tungsten carbide.
Molybdenum (Mo) is generally produced through powder metallurgy techniques. The process involves hydrostatically compacting Mo powder and sintering it at approximately 3812°F (2100°C) to form molybdenum metal. Hot working is performed at temperatures between 1598 and 2300°F (870-1260°C). Molybdenum is suitable for use only in non-oxidizing environments or vacuum conditions at high temperatures, as it forms a volatile oxide when heated in air above around 1112°F (600°C).
At temperatures reaching up to 3452°F (1900°C), molybdenum alloys exhibit excellent mechanical stability and strength. Unlike ceramics, molybdenum's high ductility and hardness provide a greater resistance to flaws and brittleness. Its superior thermal conductivity, low thermal expansion, and exceptional mechanical strength at high temperatures make molybdenum ideal for challenging thermal applications. It is the preferred material for heat sinks in electronic chips and for use in vacuum and inert furnaces.
Molybdenum's superior electrical properties have made it a valuable material in microelectronics, where it serves as an electrode in photovoltaics and as a thin-film transistor in flat-panel displays. Additionally, molybdenum is frequently utilized as an alloying element in stainless steels, tool steels, and high-strength, low-alloy steels to enhance their corrosion resistance.
Molybdenum, a glossy, silvery metal, has a melting point of 4,748°F (2,620°C) and a boiling point of 10,040°F (5,560°C). It is renowned for its exceptional performance in refractory applications due to its high strength, stiffness, and resistance to softening at elevated temperatures. Its excellent heat conductivity and low thermal expansion rate enhance these outstanding properties.
Brass, an alloy of copper and zinc, has had a profound historical impact due to its durability and workability. The earliest form of brass, called calamine brass, was likely produced by reducing mixtures of copper and zinc ores and dates back to the Neolithic period. In ancient texts, brass was often referred to as bronze, which is actually an alloy of copper and tin. The malleability of brass depends on its zinc content; brass alloys with more than 45% zinc are challenging to work with, whether hot or cold.
Brass Alloy Type | Composition |
---|---|
Manganese Brass | 1.3% Manganese, 29% Zinc, and 70% Copper |
Red Brass | 5% Zinc, Copper, 5% Lead, and 5% Tin |
Yellow Brass | 33% Zinc, Copper |
Admiralty Brass | 1% Tin, Copper, 28% Zinc |
White Brass | >50% Zinc, Copper |
Aluminum Brass | 2% Aluminum, 22% Zinc, 76% Copper |
Lead-free Brass | Zinc, Copper, and < 0.25% Lead |
Nickel Brass | 5.5% Nickel, 24.5% Zinc, and 70% Copper |
While a granulated form is used in brazing (soldering), these brasses, often referred to as white brasses, are economically insignificant. They also form the basis for various alloys used in die casting. Malleable brasses can be divided into those that can be worked cold—typically containing less than 40% zinc—and those that require hot working, usually with a higher zinc content.
Malleable brasses, also known as alpha brasses, are commonly used for making pins, bolts, screws, and cartridge casings. Beta brasses, containing 50-55% copper, are less ductile but stronger, making them suitable for producing window and door fittings, faucet handles, sprinkler heads, and other fixtures. Besides copper and zinc, additional elements are often included in brasses to improve physical and mechanical properties, enhance corrosion resistance, increase machinability, or alter color.
These include lead brasses, which are easier to machine; naval and admiralty brasses, which gain improved seawater corrosion resistance from a small amount of tin; and aluminum brasses, which provide enhanced strength and corrosion resistance in environments where naval brasses might be less effective.
Brass alloys include:
It contains 1.64% iron, 1.02% tin, 60.66% copper, and 36.58% zinc. This composition makes it ideal for marine applications, offering exceptional toughness, hardness, and resistance to corrosion.
A malleable metal containing less than 35% zinc, suitable for pressing, forging, and similar applications. Alpha brasses feature a face-centered cubic crystal structure and consist of a single phase.
This brass is composed of 60% to 85% copper and zinc. It is commonly used to imitate gold in more affordable jewelry pieces.
Alpha-beta brass, commonly referred to as duplex brass, contains 35–45% zinc. It includes both the β'-phase, which is body-centered cubic and known for its toughness and strength, and the α-phase. Alpha-beta brasses are typically produced through hot working processes. Additionally, Muntz metal, a type of alpha-beta brass, contains a small amount of iron.
Iron-carbon alloys with a carbon content exceeding 2% are melted to produce cast iron. Once melted, the metal is poured into a mold. Unlike wrought iron, which can be shaped with hammers and tools, cast iron is not malleable. It typically contains 2-4% carbon and additional alloys, along with 1-3% silicon, which improves the casting properties of the liquid metal.
Cast iron alloys can vary in composition, with elements like manganese and trace contaminants such as sulfur and phosphorus also present. Additionally, the specific chemical composition and physical properties can be used to further differentiate between wrought iron and cast iron.
Here are a few examples of cast iron alloys:
Gray iron gets its name from the flake-shaped graphite molecules embedded within it. When the metal fractures, these graphite flakes break apart, resulting in the gray color of the fractured surface. The name "gray iron" reflects this characteristic. By adjusting the graphite content and controlling the cooling rate during production, it is possible to influence the size of the graphite flakes and the overall composition of the matrix.
Gray iron has a lower tensile strength and is less ductile than other types of cast iron. However, it provides a higher amount of vibration damping (the ability to reduce energy by absorbing vibration) and is a superior heat conductor. It is superior to all other cast irons in its damping capacity; it is 20–25 times greater than that of steel.
Iron carbide forms when carbon atoms combine with iron under specific carbon concentrations and rapid cooling conditions. This results in a solidified substance with little to no free graphite molecules. As a result, the fractured surface of white iron appears white due to the absence of graphite. The cementite microcrystalline structure of iron carbide provides high compressive strength, excellent wear resistance, and significant hardness, though it is also brittle.
While the brittleness of white iron limits its use as a standalone manufacturing material, its abrasion resistance makes it valuable as a coating in specific applications, such as shell liners, pipe fittings, or cement mixers. This is achieved by incorporating a heat-conductive material into a part of the mold. This localized cooling method rapidly draws heat away from the molten metal at that spot, leading to a harder surface. Ni-Hard Iron, a popular grade of white iron, is particularly effective for low-impact, sliding abrasion applications due to its chromium and nickel alloy content, which enhances its durability.
Duralumin is an alloy composed of 90% to 94% aluminum, 4% copper, 1% magnesium, and 0.5% to 1% manganese. Known for its exceptional toughness, Duralumin is used in demanding applications that require durable materials, including vehicle armor in the defense industry.
Duralumin is a lightweight and durable aluminum alloy known for its toughness. It was one of the first deformable aluminum alloys widely used. Several minor variants exist, differing in composition, type, and temper, with an average yield strength of approximately 450 MPa.
Duralumin is a durable, lightweight, and strong aluminum alloy known for its impermeability and reflectivity. Its malleability makes it easy to shape, and it is an excellent conductor of both heat and electricity. Duralumin is odorless and reacts with nearby oxygen to form aluminum oxide. Additionally, it boasts excellent corrosion resistance.
Duralumin has a sleek, corrosion-resistant outer layer of pure aluminum that encases its core. In their standard state, duralumin alloys are quite flexible and manageable. They can be easily rolled, folded, and forged, and can also be shaped into various forms.
This chapter will explore the applications and advantages of metal alloys.
Metal alloys are blends of different metals designed to enhance desirable properties while minimizing drawbacks. These mixtures often result in materials that are more durable than their pure metal counterparts. Pure metals can be brittle, so alloys are created to combine strength with improved workability. Unlike pure metals, where all atoms are identical, metal alloys contain a variety of atoms. This variation makes it more difficult for atoms to move, resulting in alloys that are generally stronger and harder than pure metals. Utilizing alloys allows for the construction of more robust structures and the creation of more resilient products. For example, stainless steel is a particularly strong alloy.
Metal alloys are combinations of various metals and non-metals. Unlike pure metals, which are prone to chemical reactivity and corrosion, alloys can be engineered to resist these effects. Corrosion can rapidly degrade pure metals, leading to costly repairs. Metal alloys, with their enhanced resistance to corrosion, help mitigate and delay this persistent issue, making them more durable and cost-effective over time.
Metal alloys offer greater adaptability compared to pure metals. They can be tailored to enhance specific properties suited for various applications, whereas pure metals only exhibit their inherent qualities, for better or worse. By combining the best characteristics of different materials, metal alloys provide a broader range of possibilities for diverse projects.
Metal is combined with either another metal or nonmetal ingredient to form an alloy. In order to create a metal alloy, the components are typically melted, mixed together, and allowed to cool to room temperature. Many pure metals, such as gold’s softness, contain inherent traits which makes them unsuitable for some applications. However, metals can gain strength and other improved chemical characteristics by combining them to form an alloy. By making an alloy, other desired qualities may be improved or added like hardness, machinability, and corrosion resistance.
Aluminum 1100 is the softest of the aluminum alloys, which makes it easy to shape and form into a wide range of products for industrial and home use. It can be cold and hot worked but is frequently shaped by...
The term "aluminum coil" describes aluminum that has been flattened into sheets where their width is significantly higher than their thickness and then "coiled" into a roll. Stacks of individual aluminum sheets are difficult to...
Aluminized steels are steels that have been hot-dip coated with pure aluminum or aluminum-silicon alloys. This hot-dip coating process is termed hot-dip aluminizing (HAD)...
Aluminum piping and tubing is silvery-white, soft, and ductile. The metal belongs to the boron group. Aluminum is the third most abundant element present on earth. Aluminum has low density. When exposed...
Beryllium Copper is a versatile copper alloy that is valued for its high strength and hardness, combined with good electrical and thermal conductivity. It is a non-ferrous, non-magnetic, and non-sparking metal alloy...
A variety of copper-zinc alloys are referred to together as brass. Different ratios of brass and zinc can be used to create alloys, which produce materials with various mechanical, corrosion, and thermal properties...
Copper is a ductile, malleable, and reddish-gold metal with the capacity to effectively conduct heat and electricity. Brass and bronze, two commonly used alloys, are created when copper is combined with...
The copper sheet is a highly malleable and workable metal with outstanding electrical and thermal conductivity and corrosion resistance. Copper (Cu) is a reddish, very ductile metal that belongs to Group 11 of the periodic table...
Metals are a group of substances that are malleable, ductile, and have high heat and electrical conductivity. They can be grouped into five categories with nickel falling in the category known as transition metals...
Stainless steel grade 304 is an austenite stainless steel that is the most widely used and versatile of the various grades of stainless steel. It is a part of the T300 series stainless steels with...
Stainless steel is a type of steel alloy containing a minimum of 10.5% chromium. Chromium imparts corrosion resistance to the metal. Corrosion resistance is achieved by creating a thin film of metal...
Stainless steel grades each consist of carbon, iron, 10.5%-30% chromium, nickel, molybdenum, and other alloying elements. It is a popular metal used in various products, tools, equipment, and structures that serve in many industrial, commercial, and domestic applications...
Stainless steel can be fabricated using any of the traditional forming and shaping methods. Austenitic stainless steel can be rolled, spun, deep drawn, cold forged, hot forged, or stippled using force and stress...
Stainless steel tubing is a multifaceted product that is commonly utilized in structural applications. Stainless steel tubing diameters and variations vary greatly based on the application requirements and are...
Steel service centers are companies that specialize in procuring steel directly from mills and manufacturers and supplying them to the customers. They are fundamental to the steel supply chain...
Titanium metal, with the symbol Ti, is the ninth most abundant element in the earth‘s crust. It does not occur in large deposits, yet small amounts of titanium are found in almost every rock...
Tungsten is a rare naturally occurring chemical element on earth. It is known to be one of the toughest metals on the earth. It is usually a tin white or a steel gray metal. Tungsten is common for its high tensile...
Aluminum is the most abundant metal on the Earth’s crust, but it rarely exists as an elemental form. Aluminum and its alloys are valued because of their low density and high strength-to-weight ratio, durability, and corrosion resistance...