Chemical Milling
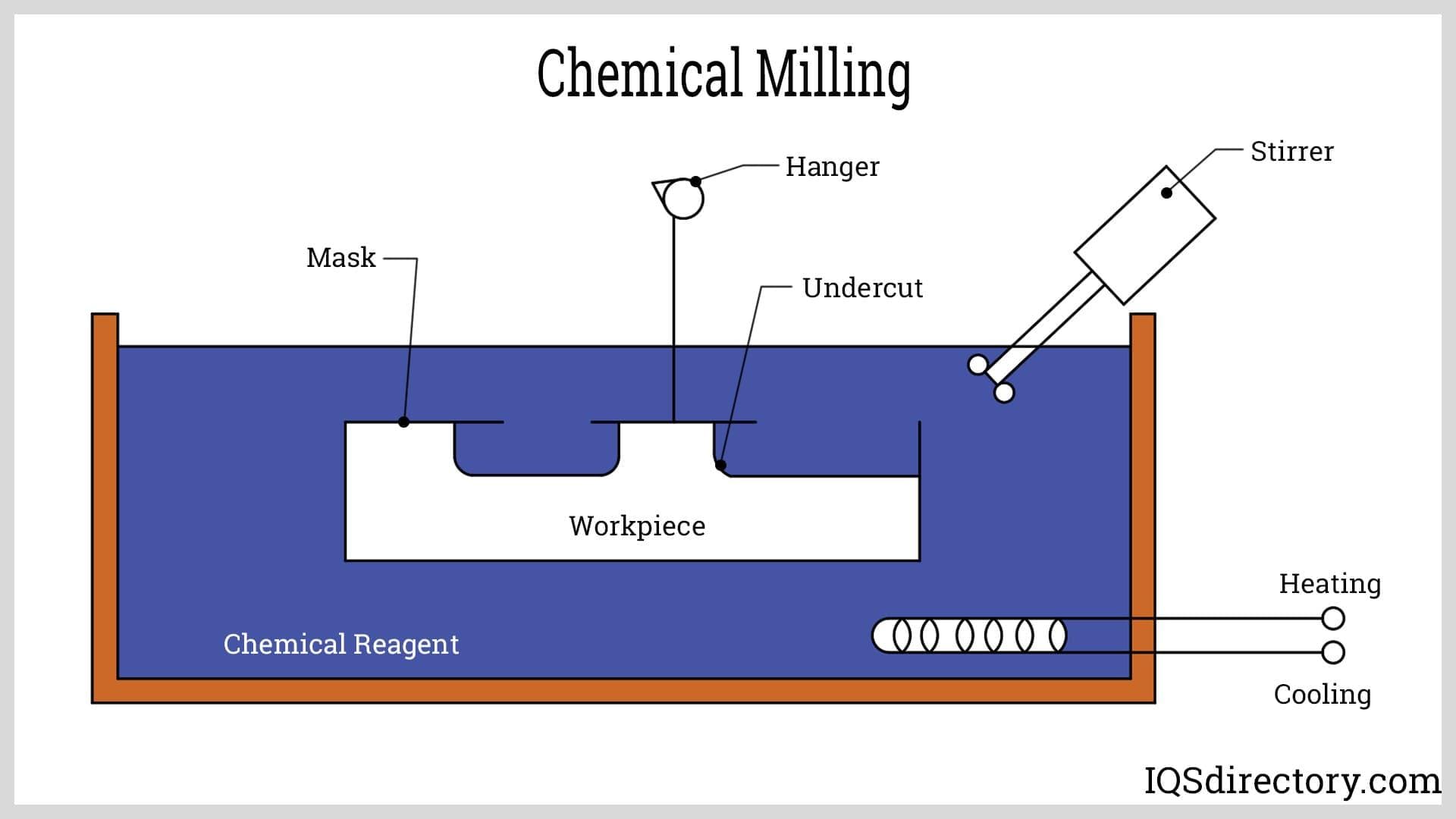
Chemical milling is a subtractive machining process that removes material from a workpiece to achieve a desired shape. Unlike aggressive milling methods that depend on sharp tools to produce a design, chemical...
Please fill out the following form to submit a Request for Quote to any of the following companies listed on
This article will take an in-depth look at acid etching.
The article will bring more detail on topics such as:
In this chapter, you will explore the concept of acid etching, delving into its applications, elements, and methodologies.
Acid etching is a chemical technique whereby a potent acid, known as an etchant, is applied to a metal's surface to strip away a portion of the material. This process is utilized to craft patterns, designs, or detailed components on metal surfaces.
Importantly, acid etching does not alter the core properties of the metal, such as its grain structure and tensile strength. This versatile method is applicable to various metal types and is particularly effective for thin materials at risk from other processes.
As a precision metalworking technology, acid etching utilizes acidic etchants to fabricate intricate and highly precise metal components. It is also employed to replicate artworks with high fidelity. Initially, acid etching was developed to make an artist’s creations accessible to a broader audience.
During the acid etching process, the artisan begins with a copper or mild steel plate and coats its surface with a waxy, acid-resistant ground. The engraver meticulously etches the image onto the ground, using a variety of tools to achieve an exact reproduction of the original artwork. Subsequently, the plate is submerged in a mordant bath for a set time before being rinsed and the ground removed, revealing a distinct image replicating the engraver’s original creation. This technique necessitates extensive skill, time, and resources to produce top-tier artworks.
Acid etching effectively works on various substrates, including stainless steel profiles, sheets, and plates, as well as other metals such as aluminum and brass. The process modifies the surface texture of stainless steel, turning it matte compared to the original finish. This texturing enhances the non-slip grip, adding safety to hand tools. Furthermore, acid etching is implemented to produce decorative motifs, contrast textures, and textual elements.
Several acids, such as nitric acid, hydrochloric acid, and sulfuric acid, can be employed for etching steel and stainless steel. These powerful acids require careful handling as they can dissolve stainless steel and pose severe risks to the skin.
Chemicals like ferric chloride or copper sulfate, which yield acids when mixed with water, are also suitable for etching. These compounds usually work more quickly than conventional acids. The etching speed of steel is influenced by the acid's strength: more potent acids accelerate the etching process.
Etching acids and chemical compounds are available through online chemical supply retailers.
The choice of metal affects the acid etching process since some metals etch faster than others. For example, steels and nickel require more time than softer metals like bronze, copper, and aluminum.
Although most metals can undergo acid etching, those with unique characteristics are typically favored. Frequently used metals in acid etching include:
Aluminum – This lightweight, strong metal offers superior weight-to-strength ratio and corrosion resistance.
Bronze – With greater hardness than copper, bronze is ductile, firm, and stiff.
This chapter will explore the various types of acid etching techniques applied to different metals. It will also provide examples of procedures used for executing these etching methods.
The following procedure was used for acid etching a steel folding knife.
The most critical step in the acid etching process is preparation. Inadequate preparation can lead to poor and frustrating results.
Ensure that no acid comes into contact with the scales, washers, or liners. Store all small screws in a safe container or magnetic tray. If you are not comfortable disassembling the knife, make sure to mask off any parts you want to protect from the acid.
This step ensures a clean surface for the etch resist to adhere to. Avoid touching the blade with bare hands after cleaning, as the oil from your fingers can damage the etch.
Apply the etch resist to create a pattern on the steel. The goal is to form a barrier that prevents the acid from contacting certain areas of the steel, leaving behind a design once the resist is removed. Areas of the metal exposed to the acid will be darkened and marked. Take care to avoid overexposure, as excessive etching can damage the knife.
Using a bright color nail polish helps by making it clear where the etch resistance has been applied. You can experiment with sharpie markers, nail polish, vinyl, electrical tape, stickers, and different stenciling materials. If you need to black out the whole blade, then use very little etch resist on only the pivot and lock face. If you need only a small logo, you must protect most parts of the blade with tape or even nail polish. If you are etching a folding knife, you will want to protect the detent, pivot, and lock face area in order to avoid messing with the tolerances of those areas. Similarly, if you are etching liners and scales, protect the ball detent and the same pivot area.
Before mixing the etching solution, always wear protective gloves. Mix ferric chloride with distilled water in a 1:1 ratio by pouring equal amounts of each into a plastic container. Full-strength solutions are not necessary for good results. Ensure you leave some space in the container to accommodate the blade's displacement.
Always add acid to water, not the other way around, to prevent violent reactions or splashing. Use a container with a secure lid, preferably a snap-on type, as screw lids may trap dried acid in the threads, and metal containers can be damaged by the acid. While a small amount of this acid mixture can be effective for etching, the quantity needed depends on the type of metal and the extent of material being removed.
Before beginning the etching process, ensure you are in a well-ventilated area. The acid will produce vapors as a by-product of the chemical reaction. Safe locations for performing this procedure include outdoors or under a ventilation hood or stove hood.
The two acid etching processes are detailed below:
Short dips with quick rinses under the tap yield the best etching results, as they allow for better control over the final outcome. Use a paper clip or dental floss to submerge the knife in the acid, repeating the process until the desired effect is achieved. The recommended procedure is to dip the knife in the bath for 10-60 seconds, rinse it under the tap for 10 seconds, let it air dry for 10 seconds, and then repeat. This method also helps preserve any factory laser markings on the blade.
It is also advisable to move the blade around in the acid to ensure an even etch and reduce pitting. Some advanced systems use fish tank aerators to agitate the acid.
Alternatively, some processes involve a single, long bath in the acid rather than multiple short dips. This method removes more metal at once and can make it challenging to gauge when the etching is complete. Recommended bath duration is about 10 minutes.
Take care to avoid touching the blade with bare hands during rinsing, as fingerprints can leave marks on the surface.
This method is effective for applying a small mark or etching just one side of the steel. Start by protecting the steel with electrical tape, nail polish, or vinyl. Use a cotton Q-tip to apply a small amount of acid to the desired area.
Next, apply the acid to the stenciled steel using the same timing as before, or monitor the Q-tip to detect when the acid starts to react with the steel. Rub the Q-tip around the stencil, working the acid into the steel. The Q-tip will turn black as the metal is removed.
Depending on your goals, you may consider the following finishing options:
Once the desired results are achieved, use acetone and cotton swabs to remove the etch resist, including any Sharpie marker or nail polish from the blade, pivot, and lock face areas. The knife can then be reassembled.
If you no longer need the acid, it should be taken to a hazardous waste disposal facility. To neutralize the acid, you can use baking soda. Even after neutralization, it is advisable to dispose of the solution at a hazardous waste facility, as it may still contain concentrations of metals harmful to the environment.
Here are a few final considerations to keep in mind:
The etching of aluminum with copper sulfate is a less toxic, safer, simpler and cheaper kind of electro-chemical metal etching. Aluminum etching is less toxic and is also a lot of fun to mess around with.
An example of the step-by-step process for aluminum etching is outlined below:
Once the salt and copper sulfate have dissolved and the solution has cooled slightly, it is ready for etching. Copper sulfate is toxic in large quantities, so always wear gloves, a mask, and eye protection. If the solution is not cooled, it can be more aggressive and may even produce smoke during etching, so be sure to let it cool before use.
The proportions of copper sulfate and salt can be adjusted to create a weaker or stronger solution. While it's possible to etch without salt, doing so will reduce the etchant's reactivity. This solution is also suitable for etching zinc and steel, but not copper.
The etching process is relatively quick. With the proportions specified, it takes about 4 minutes to etch a line, an additional 10 seconds to achieve a light gray tone, and around 4 minutes for a deep black. However, unlike copper and zinc etching, the lines may not be as crisp. The shorter etching time and more erratic etch make it challenging to achieve different line thicknesses.
The mordant depletes quickly compared to other acids, but it can be recycled. While etching, copper sediments rapidly cover the plate; regularly removing these sediments with a soft brush or feather helps maintain the etching quality. Fine-grain salt and copper sulfate are recommended for better dissolution, though coarse salt can create interesting textures in the aquatint.
For etching lines, you can use Charbonnel Ultra Flex. Ensure that you draw your lines firmly, scratching the metal slightly. Note that the lines may not be as consistent as those achieved with copper or zinc.
Aluminum feels quite greasy compared to other metals because of its softness, which can cause ink to stick and make cleaning more difficult. Adding about 10% softener to the ink can help make the plate easier to clean and result in a finer, more even aquatint texture. Using a softener significantly improves both the printing process and the final result.
Proper treatment of a ceramic bonding surface is essential to ensure a durable bond between orthodontic brackets and the composite material used for repair, as well as with ceramic materials and tooth structures. These treatments fall into three categories based on their mechanism of action: chemical, mechanical, and chemical-mechanical surface treatments.
The choice of surface conditioning method depends on the chemical composition of the ceramic restoration. Surface acid etching is typically used for mechanical alteration, while universal or ceramic primers are applied for chemical treatment.
Ceramics containing silicon dioxide, such as conventional or glass-ceramics, are recommended for acid etching. This includes materials like leucite-reinforced, feldspar-based, zirconia-reinforced lithium silicate ceramics, lithium disilicate, and fluorapatite ceramics.
The acids commonly used as ceramic etchants include acidulated phosphate fluoride (APF), hydrofluoric acid (HF), and ammonium hydrogen fluoride. Hydrofluoric acid is the most frequently used. When applied to the ceramic surface, it reacts with the silica matrix to release silicon tetrafluoride and water. Silicon tetrafluoride then reacts with additional hydrofluoric acid molecules, forming a soluble complex ion known as hexafluorosilicate.
Subsequently, hydrogen ions interact with the hexafluorosilicate complex to form fluorosilicic acid, which can be rinsed off. This process dissolves and removes the surface layer of the glassy matrix, including silica, silicates, and leucite crystals, leaving the surface porous with pore sizes of 3 to 4 micrometers. Acidulated phosphate fluoride consists of 1.23% fluoride ions from sodium fluoride and hydrofluoric acid, acidified with 0.1 M phosphoric acid.
Ammonium hydrogen difluoride (NH4HF2) reacts with the silica matrix to produce silicon tetrafluoride and ammonium fluoride. This acid is suitable for use as a glass etchant or as an intermediate in the production of hydrofluoric acid. While these products are effective, their high toxicity means they may be restricted or banned in some countries.
The IPS ceramic etching gel from Ivoclar Vivadent is an aqueous solution containing 4% hydrofluoric acid. In contrast, VITA ceramics etch is an alcoholic solution composed of 5% hydrofluoric acid and 10% sulfuric acid. Porcelain Etch by Ultradent contains 9% hydrofluoric acid gel, noted for its high viscosity. According to the manufacturer's instructions, it can be used for intraoral repairs of fractured porcelain, porcelain-fused-to-metal or all-ceramic restorations, and surface treatment of porcelain before placing orthodontic brackets.
BISCO offers porcelain etchants in two concentrations: 4% and 9.5% hydrofluoric acid gel. Additionally, Mirage provides two types of porcelain etchants: a 9.6% hydrofluoric acid gel and a 4% acidulated phosphate fluoride (APF) gel. The APF gel is suitable for intraoral use and for the luting of orthodontic brackets to porcelain crowns.
The effectiveness of acid etching depends on several factors, including the type and concentration of the acid, the etching time, and the type of ceramic being treated. Hydrofluoric acid is particularly effective; its increased concentration and prolonged etching time enhance the etching effect.
The type of ceramic being treated influences the surface roughness and etching pattern. Acids do not affect polycrystalline ceramics with glassy matrices. In contrast, glass-ceramics, which contain a matrix of silica and leucite crystals, undergo selective dissolution, creating a three-dimensional porous structure. This process cleanses the bonded surface by removing unwanted oxides, debris, and grease, and increases surface roughness, which enhances bonding area and wettability. It also creates micro-retention that can be easily infiltrated by uncured flowable composite cement, thereby significantly improving resin adhesion. The following factors further impact this effect:
Acid Type: The type of acid determines the degree of surface micromorphology achieved after etching. Hydrofluoric acid creates more pronounced ceramic roughness compared to other acids.
Acid Concentration: The concentration of the acid also affects the etching outcome. Higher concentrations of hydrofluoric acid (e.g., 52%) result in greater microroughness and a uniform crystal structure due to the dissolution of the glassy phase. Lower concentrations (e.g., 20%) may produce an amorphous structure with larger porosity as more crystalline phase is dissolved.
Etching Time: The duration of etching with hydrofluoric acid influences the extent of micro-morphological changes and surface microroughness. Extended etching times increase the depth of the pores.
Photochemical etching can be used to achieve excellent accuracy. Minimum standard etching tolerances are plus or minus 10% of the thickness of the metal that is being etched, to a minimum of plus or minus 0.025 mm. Greater accuracy can be achieved with development.
Numerous companies in the United States and Canada provide specialized acid etching services, offering expertise and equipment for precision etching on various materials. These companies are distinguished by their positive traits, characteristics, and factors that contribute to their success. Below, we discuss some of these companies and the traits that have led to their achievements.
Metal Etch Services is a well-regarded company specializing in acid etching for metal components. Their success can be attributed to several key factors:
Expertise and Experience: The company has earned a strong reputation through their deep knowledge of acid etching techniques and extensive industry experience.
Customization: They provide tailored acid etching solutions to meet specific customer needs.
Quality Control: Their rigorous quality control processes ensure high-quality results, contributing to their success and customer satisfaction.
Qualitetch Components is a leading name in the Canadian acid etching market. Their success can be attributed to:
Diverse Capabilities: Qualitetch offers acid etching services for a broad range of materials and industries, establishing themselves as a versatile solution provider.
Innovative Approaches: They employ advanced techniques and technologies in their acid etching processes, resulting in unique and high-quality outcomes.
Customer Focus: Their strong commitment to customer satisfaction and addressing client needs has played a significant role in their success.
Newcut Inc. is renowned for its precision acid etching services. Their success can be attributed to:
State-of-the-Art Equipment: By investing in advanced acid etching machinery, Newcut is able to handle complex projects with both precision and efficiency.
High-Quality Standards: Their commitment to maintaining rigorous quality standards has earned them a strong reputation in the industry.
Diverse Clientele: Serving a wide range of clients across various industries has contributed to their success and stability.
Metal Etching Technology specializes in chemical and electrochemical etching. Their success can be attributed to:
Technological Advancements: By adopting the latest technologies and methods in acid etching, they have distinguished themselves from competitors.
Strong Partnerships: Their collaborations with key industry players and strategic partnerships have broadened their reach and expanded their customer base.
Advanced Metal Etching is a leading company in acid etching services. Their success can be attributed to:
Customization and Prototyping: Their ability to offer rapid prototyping and customized solutions has attracted clients looking for quick and tailored acid etching services.
Quality Assurance: Their strong emphasis on quality assurance and precision has contributed to their reputation for delivering high-quality products.
Please note that the information about these companies is based on data available up until September 2021. Market dynamics and leading companies in the acid etching industry may have changed since then. For the most current information, it is recommended to conduct up-to-date research to identify the top acid etching companies in the United States and Canada.
Industrial acid etching is a technique used to manufacture high-precision parts and components with complex and intricate details. This sophisticated process relies on computer-aided design (CAD) to define the parameters for the production of each part.
Computer-generated drawings and sketches are plotted and transferred onto photographic film in a process known as phototooling. The number of images on the film depends on the size of the part, ranging from one to thousands. The film features black and clear areas, with the black areas representing the desired part.
During the initial phototooling process, customers have the opportunity to adjust and modify the CAD design. This flexibility helps keep the process more cost-effective compared to other metal-shaping methods.
During the design process, the appropriate type of metal for the part is selected. In the manufacturing area, the chosen metal is cut into sheets and meticulously cleaned to remove contaminants. This cleaning ensures a smooth, even surface for etching, allowing the applied resist to adhere uniformly to the metal sheet.
After the metal sheets are selected, they are coated with a photoresist, a polymer material that is sensitive to ultraviolet (UV) light and resistant to acids. The phototool images are then placed on the top and bottom of the metal sheet and vacuum sealed to its surface.
The phototool, photoresist, and metal sheet are exposed to UV light to transfer the engineered image onto the coated metal. The UV light hardens and firms the resist in the areas where it shines through the clear sections of the phototool. Conversely, the resist remains soft in the areas where it is blocked from the UV light.
In the developing process, a solution washes away the unexposed coating, leaving behind only the areas that will be etched. This reveals the configuration, shape, and pattern of the part to be produced, while the areas protected by the hardened resist remain intact.
During the etching process, the etchant is applied to the metal sheet. The acid solution, sprayed onto both sides of the sheet, dissolves the metal in the uncoated areas. The regions covered by the coating or resist are shielded from the etchant and remain intact.
After the metal sheet exits the etching machine, the remaining resist must be removed. This is accomplished using a specially formulated resist solution, which may include an alkaline mixture in some cases.
Once the resist is cleaned off, the finished part is ready for delivery or additional processing. This may involve plating, forming, electropolishing, or machining, each tailored to meet the specific requirements of the application.
This chapter explores the diverse uses and advantages of acid etching.
Acid etching finds applications in the following areas:
Acid etching utilizes digital tooling, allowing for rapid setup and optimization of component designs without incurring additional costs. The process is performed without heat or mechanical force, preserving the material properties and ensuring components are free from burrs and stress. This method supports nearly limitless complexity in parts, achieving precision with an accuracy of ±0.025 mm.
Chemical etching is capable of simultaneously producing very accurate engraved features during the profiling of the material, like fluidic channels, part numbers, or logos. These features come without any additional cost.
Additional advantages include:
Acid etching is the process of cutting a hard surface like metal by means of a specially formulated acid for the process of etching in order to allow for the creation of a design onto the metal. It is also known as chemical etching or photo etching. Acid etching can be applied on ceramic components as well as in dentistry. There are different types of acid etching techniques including total etching, selective etching, and self-etching. The effects of acid etching are affected by several parameters such as the acid type, the acid concentration, and the etching time. Therefore when performing acid etching, one must consider the type of acid going to be used, the concentration as well as the time it is going to take to finish the process of etching. It must be noted that even though the acid can also be neutralized with baking soda after etching, if there is no need to keep the acid, it is recommended to take it to a hazardous waste disposal
Chemical milling is a subtractive machining process that removes material from a workpiece to achieve a desired shape. Unlike aggressive milling methods that depend on sharp tools to produce a design, chemical...
Metal etching is a metal removal process that uses various methods to configure complex, intricate, and highly accurate components and shapes. Its flexibility allows for instantaneous changes during processing...
Photochemical etching, also known as photochemical machining or metal etching, is a non-traditional, subtractive machining process in which photographic and chemical techniques are used to shape the metal workpiece...
EMI shielding is a technique of creating a barrier that prevents leakage of strong electromagnetic fields that can interfere with sensitive devices and signals. They can be installed to isolate the electromagnetic field source or as an enclosure of the device that needs protection...
Laser cutting is a non-traditional machining method that uses an intensely focused, coherent stream of light called lasers to cut through the material. This is a type of subtractive machining process where the material is continuously removed during the cutting process...
Radiofrequency (RF) shielding is the practice of blocking radiofrequency electromagnetic signals that cause radio frequency interference (RFI). RFI can disrupt the electrical circuits of a device from working normally...
Water jet cutting is a manufacturing process that uses high pressure jets of water provided by pressurizing pumps that deliver a supersonic stream of water to cut and shape various types of materials. The water in water jet cutting is...