Metal Channel
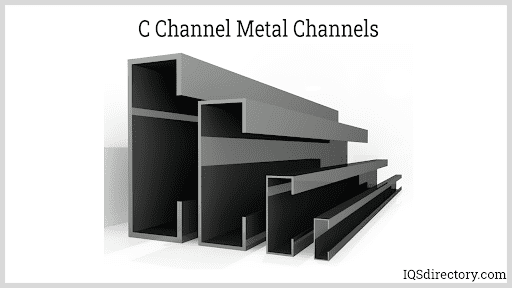
A wire brush is an abrasive tool that has stiff bristles made from a variety of rigid materials designed to clean and prepare metal surfaces. The filaments of wire brushes are small diameter pieces of inflexible material that...
Please fill out the following form to submit a Request for Quote to any of the following companies listed on
This article contains everything you need to know about Metal Spinning.
Read further and learn more about
Metal spinning, also known as spin forming, is a specialized metalworking technique that molds a flat, circular blank or disc into symmetrical round formations. This transformation is achieved through the application of a roller that exerts lateral force against the disc's surface while it spins at high speed on its axis, supported by a mandrel. The mandrel not only stabilizes the workpiece but also determines its final configuration.
Through metal spinning, a sheet of circular metal is contorted into diverse shapes without any material being removed. During this reshaping, tensile and compressive forces are applied to the disc blank over a mandrel. Certain spinning techniques may result in the thinning of the original metal sheet, but such variations are managed with precision to satisfy specific end-product criteria.
Metal spinning is one of humanity's most ancient metalworking techniques, skillfully merging artistic expression and technical knowledge with a lineage extending back to Egyptian times. Through the ages, it has transitioned from a purely manual endeavor to a refined industrial method that includes computer numeric control (CNC) technology.
Even with technological advancements, traditional manual metal spinning remains crucial for crafting products of precise detail and exceptional quality. Gaining proficiency in this method requires significant apprenticeship and distinctive expertise, underscoring the craftsmanship involved.
As a historical reshaping practice, metal spinning’s origins can be traced to ancient Egyptian pottery forming, originally employing a hand-driven potter’s wheel since 3000 BC. While initially used for wood and clay, the technique was adapted by 25 BC for crafting circular iron shields.
During the medieval era, metal spinning became prevalent for making items such as vases, tea kettles, and trophies. These objects were created using a wooden spinning lathe with manual rotational input by an assistant, highlighting the enduring significance and adaptability of this ancient technique across different periods.
A metal spinning operation utilizes a lathe and a roller to shape metal. The lathe is the primary machinery, responsible for spinning the workpiece rapidly around an axis. It also performs other metalworking tasks such as cutting, drilling, and sanding. For metal spinning, the lathe is equipped with a mandrel. The essential components of a metal spinning lathe include:
The mandrel is a forming die used in metal spinning that shapes the metal disc to match the interior form of the finished part. It supports the workpiece during rapid spinning, ensuring even deformation without wrinkles or distortions.
Before the metal disc is mounted on the mandrel and worked by the roller, it is lubricated with grease or wax. This lubrication facilitates easier removal of the workpiece and enhances its surface finish.
Mandrels can be made from materials such as steel, aluminum, plastic, or wood. For prototyping and short production runs, less costly materials are often used. The mandrel must be durable enough to withstand the forces applied by the roller.
The roller in metal spinning machines is a rigid tool that applies localized force in a specific area known as the partial work zone, where plastic deformation occurs. This force helps shape the workpiece as it flows over the mandrel.
To minimize friction and prevent heat buildup and premature wear, the roller tool often includes a ball roller that rotates throughout the process.
While the roller can be manually controlled by an operator, producing flawless parts requires extensive skill and training. To mitigate the risks associated with manual methods, CNC machining has become increasingly popular in metal spinning.
In metal spinning, the localized force applied by the roller is relatively low compared to other metalworking processes. This allows for the formation of high-strength, heavy gauge metals into large diameters using less force and energy, resulting in lower costs.
The work zone creates a slightly spiral path due to the combination of the workpiece's rotation and the forward motion of the roller. This produces a tangential flow in the material, resulting in a slight twist in the finished part.
The tailstock, positioned at the opposite end from the headstock, aligns with it to hold and support the workpiece against the mandrel during rapid spinning. It includes a mechanism that applies the necessary pressure to securely clamp the workpiece in place.
A follower is a pressure pad attached to the end of the tailstock spindle, used to secure the workpiece in place. The surface area of the follower matches the base area of the finished part.
The spindle of the headstock is a shaft on which the mandrel is mounted. It rotates both the mandrel and the workpiece during the forming process. Additionally, the tailstock has its own rotating spindle where the follower is mounted.
The headstock is a structural unit that houses the power transmission system needed to drive the spindles. It manages the rotational speed of the spindles and provides support for both the spindle and the attached mandrel.
The lathe bed serves as the foundation, providing support for the headstock, tailstock, and other components of the metal spinning machine.
CNC metal spinning utilizes a lathe to automate and control the metal spinning process. Initially, the steps resemble those of manual spinning, where the operator places the workpiece on the CNC lathe and secures it with a pressure pad.
The CNC machine is programmed with the necessary parameters for the forming process. Once activated, the CNC lathe rotates and applies pressure to the workpiece, shaping it according to the mold. The rotational force of the CNC lathe, similar to manual lathes, molds the metal to the desired form.
CNC metal spinning is favored for its cost-effectiveness, enhanced tensile strength of the finished products, high-quality surface finishes, and refined grain structures. It achieves dimensional accuracy within 0.001 inches or 0.01 millimeters.
In PNC metal spinning, the operator manually shapes the workpiece using a joystick. Once the desired shape is achieved, the programmed motions are saved and can be replicated multiple times. To ensure accuracy, the program may need adjustments, such as refining or optimizing inefficient aspects.
PNC metal spinning is well-suited for high-volume production. In playback mode, the lathe reproduces the forming process to create precise duplicates of the original part. The operator simply places the blank on the lathe and starts the playback cycle.
In the United States and Canada, there is a wide range of machines available for metal spinning. These machines play a crucial role in modern industry by facilitating the cost-effective and efficient production of metal components used across various sectors, including aerospace, automotive, electronics, and more. They contribute significantly to technological progress and economic development. Below, we explore several leading machines and their features.
The Leifeld PNC350-800 is a well-regarded CNC metal spinning machine recognized for its advanced automation, precision, and reliability. It is designed to accommodate large workpieces, making it ideal for manufacturing metal components for industries such as aerospace and automotive. The CNC control system enables programmable setups, enhancing both efficiency and versatility.
The MJC Engineering E-400 is a popular option for metal spinning, known for its user-friendly interface and CNC control that simplify programming and operation. Its robust construction and powerful performance allow it to tackle heavy-duty spinning tasks with exceptional accuracy and repeatability.
The Baileigh R-M10 is a manually operated metal spinning machine, perfect for smaller workshops and hobbyists. Although it lacks the automation of CNC models, it is favored for its affordability, compact design, and ease of use. It is well-suited for small-scale projects and prototype development.
The PNC-CNC series includes a range of models equipped with CNC controls to meet diverse metal spinning requirements. Renowned for their durable construction, intuitive interfaces, and outstanding performance, these machines are engineered to excel in both precision and productivity for metal forming tasks.
The LNSpin LS-250 is a highly versatile automatic metal spinning machine, ideal for high-volume production. It features automatic loading and unloading, which minimizes manual handling and boosts efficiency. Known for its reliability and quick cycle times, the LS-250 is a favored choice among manufacturers.
Keep in mind that the availability and popularity of specific models may have changed since this update. When selecting metal spinning machines, it's crucial to review current offerings from manufacturers and evaluate factors such as features, production capacity, automation, and budget to find the best option for your needs.
Spinning is categorized as compressive draw forming due to the radial, tensile, and compressive stresses that affect the metal flow within the localized roller work zone and nearby regions. Tensile stresses arise when the roller makes contact with the workpiece, increasing with the axial feed of the roller, which causes volumetric displacement in a plane radial to the mandrel.
As the metal volume decreases towards the center, compressive stresses form between the metal volumes. These stresses contribute to increased thickness at the open end and may lead to buckling and wrinkling. Adjustments in the direction of the feed can help mitigate these issues.
In conventional spinning, the roller directs the workpiece over the mandrel's contour, maintaining a constant material thickness throughout the process. After shaping, the workpiece's depth increases while its diameter decreases. This method is regarded as the most basic form of metal spinning and involves less complex tooling and machinery.
In shear spinning, the rollers apply a downward force as the workpiece is shaped over the mandrel's contour. This process results in a final part with a reduced material thickness compared to the original blank, while maintaining a constant diameter. The depth of the workpiece increases, and the increased compressive forces enhance the part's mechanical properties, such as strength and hardness.
Shear spinning demands a more robust tooling design and precise machining to ensure dimensional accuracy and a good surface finish. The process creates significant friction and wear on both the workpiece and mandrel, necessitating the use of coolant to manage the heat generated.
The thickness of the final material in a shear spinning process is theoretically governed by the Sine Law. According to this law, the final thickness of the part is calculated by multiplying the original thickness of the flat metal sheet by the sine of the semi-apex angle of the cone. This principle is applicable when the part has a conical profile achieved through a single-pass shear spinning process. The metal that remains perpendicular to the spinning axis will retain its initial thickness.
Hot spinning involves heating the workpiece to forging temperatures using a heating torch, which is applied while the workpiece is pressed over the mandrel. This technique is employed when the material exhibits low ductility and malleability or if the metal sheet is excessively thick and hard to deform at room temperature. Cold spinning, performed at ambient temperatures, is suitable for a wide range of metals.
During hot spinning, the metal is deformed in its plastic state, which allows for substantial deformation and refinement of the grain structure, enhancing physical properties such as strength. However, the process leads to rapid oxidation of the heated metal, making it harder to control and more costly overall.
Tube spinning is a variant of shear spinning designed to elongate and reduce the wall thickness of hollow cylindrical tubes. The process begins with the tube being mounted and secured on the mandrel. The elongation is achieved by drawing the tube over the mandrel's length using three or more rollers positioned equidistantly around the tube. The axial flow of the material follows the direction of the roller movement.
Tube spinning can be carried out externally or internally relative to the mandrel. In external tube spinning, the tube is stretched over the mandrel's outer surface. Conversely, in internal tube spinning, the tube is spun and elongated inside a hollow mandrel.
This method is effective for creating tubes with varying diameters, provided that wall thickness is not a critical factor. Similar to shear spinning, tube spinning demands a complex tooling design and enhances the mechanical properties of the tube.
To achieve the desired thickness and finish of the workpiece, adjustments can be made to various parameters, including RPM, roller shape and diameter, pressure, attack angle, and feed rates. In some cases, a second pass may be required to reduce the outside diameter near the edge of the workpiece.
Adjusting the edge of the workpiece can be challenging, as it may result in edges that need trimming or become excessively sharp. Careful adjustments are necessary, as each pass of the roller can make the material increasingly brittle and prone to spring back from the tool.
Necking and expanding are additional techniques used in metal spinning. Necking involves the gradual reduction of the diameter in a specific section of the part, while expanding refers to the increase in diameter in a particular section.
After metal spinning, two common post-processes are planishing and trimming. Planishing is used to smooth out wrinkles and marks left by the tool on the finished part. This step involves using a planishing tool to apply force while the workpiece is spun at a slower RPM. Trimming involves cutting away any excess material from the edges of the finished part to achieve the desired shape and dimensions.
Metal spinning is versatile and can be used with various types of metals. If a metal can be processed by metal stamping, it can also be spun. Additionally, some metals that are challenging to form through stamping can be successfully shaped by spinning. However, metal spinning lathes typically operate at pressures up to 15,000 psi, which limits their ability to deform metals such as carbon steel and tool steel.
Aluminum is a favored material for metal spinning due to its excellent strength-to-weight ratio, ductility, and malleability. These properties make it a preferred choice in the metal spinning industry. Aluminum is widely used because of its high resistance to corrosion and chemicals, as well as its thermal stability. It serves as a cost-effective and lightweight alternative to steel.
Commonly used aluminum alloys for metal spinning include 1100, 2024, 3003, 5052, 6061, and 7075.
Spun aluminum parts can be found in a variety of applications, including cooking utensils, kitchenware, drums, funnels, decorative elements, electronic device components, appliances, and furniture.
Steel, an alloy primarily composed of iron and carbon along with other elements, exhibits varying properties based on its specific composition and the manufacturing methods used. These properties influence its workability and performance during metal spinning.
Stainless steel, defined by its chromium content of at least 10.5%, along with additional elements like nickel, molybdenum, and manganese, is renowned for its superior resistance to chemicals and corrosion. It offers exceptional strength, toughness, and rigidity, which are preserved even under high pressures and temperatures.
Carbon steel primarily consists of iron and up to 2% carbon. This composition enhances strength and rigidity but also increases brittleness, reducing malleability and ductility. The higher carbon content diminishes corrosion and chemical resistance, though carbon steel remains a cost-effective choice.
Carbon steel is categorized into low carbon or mild steel (less than 0.3% carbon), medium carbon steel (0.3 - 0.6% carbon), and high carbon steel (more than 0.6% carbon).
The steel's manufacturing process affects its workability in metal spinning. Hot-rolled steel, processed at temperatures exceeding its recrystallization point, is more ductile and malleable but prone to oxidation, which can weaken it. Cold-rolled steel, rolled at room temperature, is less flexible but maintains strength and is also suitable for metal spinning.
Steel, in its various forms, is ideal for heavy-duty applications and is widely used in automotive, construction, manufacturing, and aerospace sectors. It is commonly employed in the fabrication of pressure vessels, tanks, and processing equipment.
Brass is an alloy of copper and zinc known for its excellent thermal and electrical conductivity. Its copper content imparts resistance to corrosion, microbial growth, and biofouling. Brass is also valued for its attractive color, ranging from dull yellow to reddish hues, which makes it ideal for decorative applications.
With its good ductility and malleability, brass is highly workable during metal spinning. Common applications for spun brass parts include musical instruments, pipes and fittings, structural elements, furniture, and various electronic devices.
Bronze is an alloy primarily composed of copper and tin, with additional elements like manganese and phosphorus. It is known for its distinctive yellowish-brown color and offers higher strength and rigidity compared to brass. Although heavier than brass and stainless steel, bronze maintains many of the beneficial properties of copper, including good weldability.
Parts made from spun bronze are highly durable and exhibit superior strength. Common applications include sculptures, musical instruments, trophies, engine components, and structural elements. However, bronze is less malleable and harder than brass.
Hastelloy is a specialized metal alloy composed of nickel, chromium, and molybdenum. Renowned for its superior resistance to chemicals, oxidation, and corrosion, this alloy is frequently employed in demanding environments. It is commonly used for manufacturing tank heads in pressure vessels found in oil refineries, power generation facilities, and chemical plants, as well as in various automotive and aerospace components. With its impressive strength and durability, Hastelloy performs exceptionally well under high temperatures and pressures.
Titanium is a metal known for its excellent strength-to-weight ratio and resistance to chemicals and corrosion. It's both lightweight and flexible, which makes it ideal for metal spinning applications. Despite these advantages, titanium is quite costly and less commonly used for spinning compared to other metals.
Metal spinning is an effective technique for producing concentric and symmetric parts in low to medium production volumes, especially when the expense of metal stamping dies is too high. For larger production runs, metal stamping becomes more cost-efficient and faster compared to metal spinning.
Certain metal shapes are too intricate for metal stamping to handle efficiently and are best created through metal spinning due to their unique design requirements.
Metal hemispheres are versatile components used in a variety of applications, including lighting fixtures, reflectors, mixing bowls, satellite dishes, tank heads, covers, caps, and domes. They can feature either straight or curved walls and are crafted from materials such as cold rolled steel, stainless steel (grades 304 and 316), aluminum, copper, and brass.
Funnel shapes, hopper designs, and cone-shaped pendants.
Venturi tubes used in dust collectors, fans, blowers, and air scrubbers.
Bells, antenna reflectors, satellite dishes, lighting fixtures, and supports for columns and stands.
Tubes, vessel and tank casings, gas containers, and canisters.
Hopper lids and bases are crafted through hand spinning to handle different materials. These components are made from premium aluminum, spun and trimmed to meet specific customer requirements. Occasionally, additional processing is needed, such as incorporating holes and slots.
Metal spinning is a fabrication technique used to manufacture tank heads for pressure vessels, storage tanks, and various process equipment. Given that these vessels often endure high pressures and challenging conditions, the goal is to produce seamless, robust, and resilient tank heads through metal spinning. This process demands meticulous control to meet stringent regulations regarding dimensions, strength, and material composition.
Typical shapes of tank heads include:
The benefits of the metal spinning process include:
The drawbacks and constraints of the metal spinning process are as follows:
A wire brush is an abrasive tool that has stiff bristles made from a variety of rigid materials designed to clean and prepare metal surfaces. The filaments of wire brushes are small diameter pieces of inflexible material that...
Precision sheet metal fabrication is a common manufacturing process where the structure of a metal workpiece is cut, bent, and assembled by machining. There are any number of operations that are performed in the creation of a finished sheet metal product...
Roll forming is a gradual process of bending a flat sheet of metal to obtain a longitudinal and uniform profile by processing it through a set of mated tool dies. The process is carried out until a uniform shape is obtained....
Roll forming is a process that uses a set of precisely placed rollers to perform incremental bending to a continuously fed strip of metal. The rollers are mounted in sets on a consecutive stand with each roller...
Steel channels are "C"-shaped hot-rolled carbon steel built with vertical web and inside radius corners on the top and bottom horizontal flanges. Steel channels consist of a wide web and two flanges, which can...
Secondary manufacturing processes, or fabrication, work on products from primary processes to create a metal part or structure that is suitable for end-use. In these processes, semi-finished metal products are reshaped and joined...