Industrial Lubricants
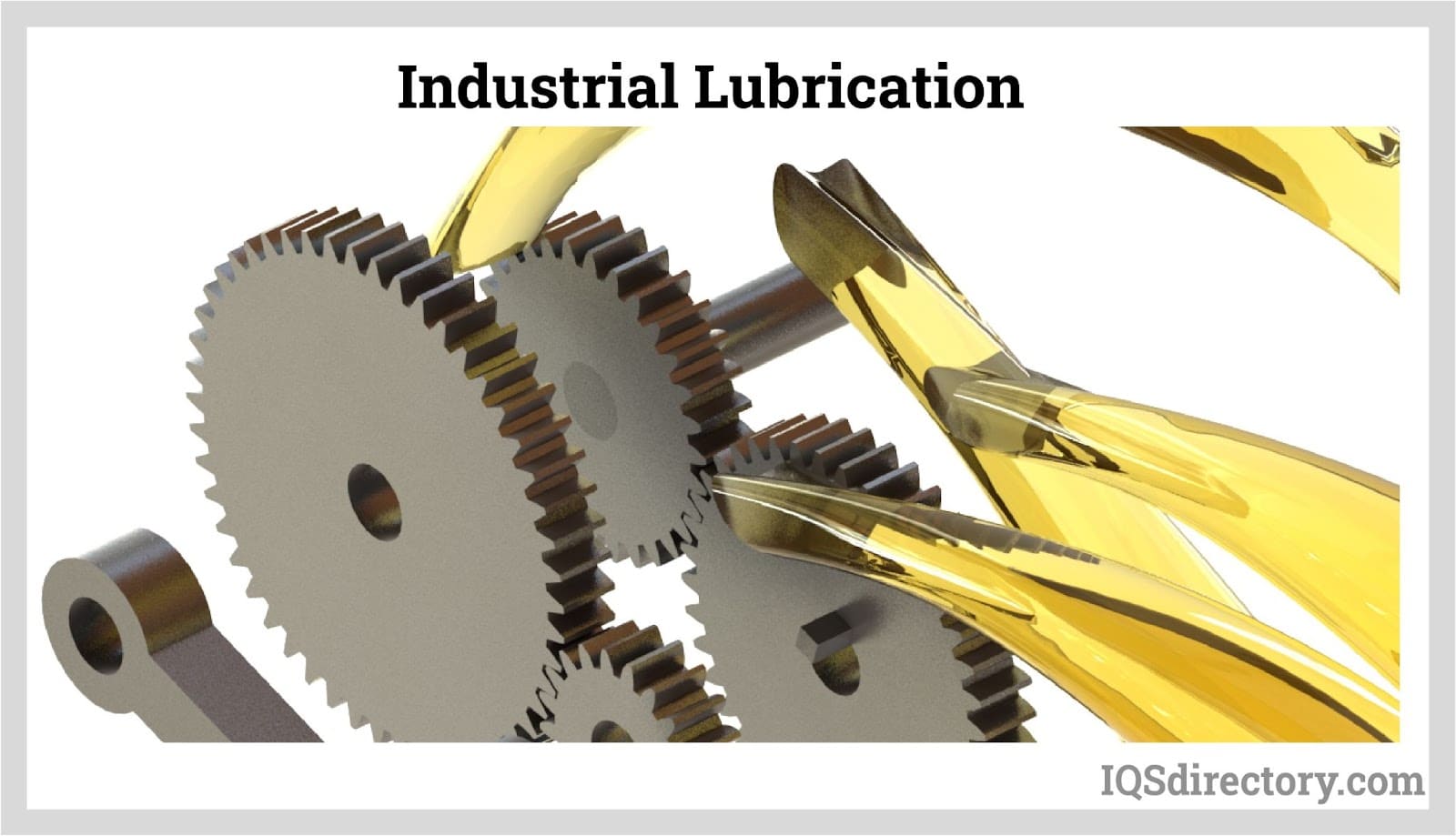
A lubricant is a substance that is applied on surfaces that have relative motion in between them. The lubricant reduces friction and wears between the surfaces. However, the lubricant can have other...
Please fill out the following form to submit a Request for Quote to any of the following companies listed on
This article takes an in-depth look at metering pumps and their use.
You will learn more about topics such as:
A metering pump is a specialized mechanism designed to precisely dispense a predetermined volume of fluid at a desired rate, ensuring controlled volumetric flow. The phrase "metering pump" encompasses a range of pumping technologies, each engineered to fulfill unique application, operational, or process demands. The specific selection of a metering pump is determined by the requirements of the particular application.
In choosing a metering pump, it is crucial to consider factors such as the fluid's viscosity, temperature, discharge pressure, flow rate, and the composition of materials in the wetted path. A metering pump typically consists of a pump head and a motor, which can feature either manual or electronic control systems for adjustments.
Metering pumps often employ piston-driven positive displacement techniques, where the piston transfers the liquid within the reservoir chamber. Although piston-driven pumps are widely used, alternative designs exist to meet specialized requirements.
A metering pump is a type of reciprocating pump that uses positive displacement to deliver a precise volume of liquid with each stroke. The rotary motion is converted into reciprocating motion using a wheel and worm shaft mechanism. These features are general to metering pumps but may vary in their implementation across different types.
The primary function of a metering pump is to control the volume of liquid transferred during a process. Its accuracy ensures that the exact amount is added at the appropriate time.
Piston metering pumps are a type of positive displacement pump that utilize a piston to move fluid within the chamber. The flow rate and volume of liquid dispensed are governed by the size of the pumping chamber. Fluid flows through check valves located at the inlet and outlet. As the piston retracts, it creates a vacuum in the chamber that opens the inlet check valve, allowing the fluid to enter the chamber.
When the chamber is filled, the piston performs a discharge stroke, pushing the liquid out through the outlet check valve.
A diaphragm metering pump uses a diaphragm that flexes to draw liquid into the pumping chamber and then expel it. Similar to a piston pump, the diaphragm's movement generates suction or a vacuum, drawing fluid in through the inlet valve. After the chamber is filled, the diaphragm forces the liquid out through the outlet valve.
In the design shown below, the plunger is connected to the diaphragm and moves it mechanically. In a hydraulic actuated diaphragm metering pump, the mechanism is not connected to the diaphragm, which is driven by hydraulic fluid. In both processes, moving the diaphragm is key for dispensing fluid.
Peristaltic metering pumps operate differently from piston-driven and diaphragm metering pumps. These pumps use a hose or tubing through which the fluid travels. Rollers positioned on a rotating rotor control the flow of the fluid. As the rotor turns, it creates a negative pressure in the tubing that draws in the fluid. When the tubing is filled, the rotor continues to rotate, compressing the tubing and stopping the flow. This rotational action propels the fluid through the tubing in the desired direction.
When the roller completes its cycle, the tubing is released, aligning with the flow. This action generates negative pressure again, allowing the next portion of fluid to enter the tubing.
A gear metering pump operates similarly to a peristaltic pump, but it does not use tubing. The interlocking gears create a vacuum that draws the fluid in. As the gears turn, they transfer the fluid from the inlet to the outlet valve through a rotating motion.
Gear metering pumps are particularly suitable for handling high-viscosity fluids due to their robust design that can manage high pressures. They are commonly employed in hydraulic fluid power systems.
Syringe metering pumps come in two main types: infusion and withdrawal. Both types are designed to handle precise volumes of fluid. Infusion syringe metering pumps deliver small amounts of fluid at controlled pressures and intervals. In contrast, withdrawal syringe metering pumps automatically extract fluid samples for medical and pharmaceutical analysis.
Infusion syringe metering pumps are commonly used in hospitals for dosing and are subject to specific speed and flow rate regulations.
A syringe metering pump operates using a piston to either infuse or withdraw fluid. These pumps typically operate at slower rates and are not suitable for automated systems. They are highly sensitive to pressure variations, especially in systems with multiple syringe pumps. Additionally, their reservoirs have limited capacity, making them suitable for small volume transfers.
A bellows metering pump operates as a positive displacement pump. It utilizes a motor shaft that rotates to drive an up-and-down motion via a lever crank system. This motion compresses and expands the bellows, facilitating the movement of fluids in and out.
During operation, the motor's rotation extends the bellows, generating a vacuum that draws fluid through the inlet valve. As the motor continues to rotate, the bellows contract, pushing the fluid out through the outlet valve.
A plunger metering pump functions similarly to a piston metering pump but uses a plunger for its reciprocating motion. As a single-acting pump, it expels fluid during the forward stroke. Fluid is drawn in through a suction check valve, and as the plunger moves forward, the fluid is pushed out through a discharge check valve.
Plunger metering pumps are designed to handle higher pressures than piston metering pumps, capable of withstanding pressures over 50,000 psi. They also operate at higher speeds, making them suitable for high-pressure applications that piston pumps may not be able to manage.
Small metering pumps are scaled-down versions of their larger counterparts, operating on the same principles. They feature a compact pump head, driver, and motor, making them suitable for handling various liquid media. These pumps offer adaptability, as their motors can be replaced or adjusted to meet specific application needs.
Large metering pumps can be miniaturized into smaller models, and multiple small metering pumps can be used together to manage the flow of several fluids concurrently within a single process.
The mobility of small metering pumps makes them easy to install and configure. Their size makes it possible to adjust their flow rate, stroke length, and the frequency of their cycles. Small metering pumps can weigh as little as 1.6 ounces (46 g).
Chemical metering pumps are specifically designed to introduce chemicals into processes with high precision. Consistency is crucial due to the nature of the materials they handle. Although these pumps are engineered for accuracy, they are not infallible; metering is based on averages over time. These pumps are also highly sensitive to pressure, which requires careful monitoring during operation.
Incorrect chemical dosing can alter a substance’s pH, making it either too acidic or too alkaline, potentially compromising the intended application of the chemical fluid. Piston and diaphragm metering pumps are commonly used for chemical applications due to their reliability.
Chemical metering pumps are employed in various applications, including:
pH Control: In water treatment, metering pumps are used to regulate pH levels, which indicate the acidity of the water. These pumps dispense chemicals like sulfuric acid or caustic soda to adjust and maintain balanced pH levels.
Coagulation and Flocculation: To remove impurities from water, coagulation and flocculation processes are employed. These chemical treatments cause particles and impurities to clump together and settle at the bottom of a container, making them easier to remove.
Water Enhancement: This stage involves adding substances to the water to halt unwanted processes, improve its purity, or eliminate microorganisms.
Fuel Additives: Chemical metering pumps are used to inject various fuel additives into oil and gas, enhancing performance and stability.
Mining: In mining, chemical metering pumps facilitate the extraction of precious metals from ore by introducing different chemicals. Each mining operation may use a unique method tailored to its specific needs.
Electronic metering pumps use either direct current (DC) or alternating current (AC) to operate. They offer enhanced control over fluid dispensing accuracy, with their pumping action regulated by electrical current. This setup allows precise monitoring of the pump’s stroke and performance.
Historically, metering pumps were powered using methods common to other types of pumps, such as pneumatic, hydraulic, manual, or fuel-driven systems.
Electronic metering pumps have largely replaced these traditional powering methods. They can be integrated with digital and computerized systems, allowing for advanced control features like touch screens to adjust flow rates, volumes, and operating cycles.
Automatic adjustments can be input to electronic metering pumps to ensure accuracy of the set point regardless of the discharge pressure. The use of electronic metering pumps makes it possible for operators to set metering pumps to a desired discharge rate without the need to calculate capacity due to the changes in stroke length settings.
A solenoid metering pump operates using electromagnetic force. When the electromagnet is activated, it draws the plunger of the solenoid, creating a reciprocating motion that moves a diaphragm to draw in and dispense the fluid.
Solenoid metering pumps are valued for their user-friendly operation, featuring an LED display and intuitive button controls for easy adjustments. Their advantages include adjustable stroke lengths, minimal maintenance requirements, simplified operation, high efficiency, and a well-designed pump head, all contributing to their widespread use.
These pumps are commonly employed to control discharge volumes or for external regulation purposes.
A metering pump, also known as a dosing pump, is designed to accurately dispense various fluids, including acids, bases, corrosives, viscous liquids, and other materials, to fulfill specific process or application needs. These pumps perform repetitive dispensing tasks automatically.
The driver supplies power to the pump through various systems, including AC, DC, pneumatic, or hydraulic power sources.
The power delivered by the driver is initially in rotary motion, which must be converted into reciprocating motion for the pump mechanism to function. The drive mechanism handles this conversion, transforming the rotary motion from the driver into reciprocating movement. Under demanding conditions, this component is often submerged in a lubricant or oil bath to maintain reliability and ensure consistent performance.
Flow adjustments for a metering pump involve modifying the stroke length and the frequency of strokes per minute. These adjustments can be made manually, through axial displacement, or automatically.
Manual: Manual adjustment typically involves using a screw mechanism to turn the pump on or off.
Axial Displacement: Axial displacement can be adjusted while the pump is running, using mechanisms such as an N or L-shaped crankshaft adjustment or an eccentric cam adjustment.
Automatic: Automatic adjustments are made using pneumatic or electronic controls. Pneumatic controls alter the stroke by adjusting the air pressure signal, whereas electronic controls modify the electrical signal to adjust the stroke.
Check valves can be located at the suction end of a metering pump or at its discharge end. The designs of check valves permit the liquid flow to enter the chamber of the metering pump and allow the flow to be discharged. Aside from peristaltic pumps, most metering pumps have ball check valves with one or two balls.
Poppet check valves are frequently used in metering pumps due to their ability to ensure unidirectional flow, similar to ball check valves. The mechanism of a poppet check valve resembles that of a sink or bathtub drain plug, where a poppet opens and closes to regulate the flow of fluid.
Metering pumps are essential for various manufacturing processes, including blending, purifying, and managing fluid operations and applications. Enhancing a metering pump with the right accessories can boost its accuracy and reliability in dosing, help prevent downstream issues, and lower maintenance costs.
Each component is designed to enhance specific features of the metering pump, improving its overall performance. Chemical dosing systems often benefit from a range of accessories, such as pressure relief valves, back pressure valves, calibration cylinders, pulsation dampeners, pressure gauges, injection quills, and strainers.
When the discharge side of the pump is obstructed during operation, pressure within the pump can rise continuously, potentially leading to damage. To prevent this, a relief valve is used to release excess pressure, protecting the pump, piping, and other components from harm.
Back pressure valves are installed near the discharge side of the pump to maintain pressure on the discharge side, ensuring that the pump's internal check valves seat correctly. These valves release fluid when a predetermined pressure is achieved, thereby optimizing the pump's performance and the flow within the pipeline.
A back pressure valve functions as a control valve, maintaining pressure when the suction pressure exceeds the discharge pressure. Without it, a metering pump might experience overfeed and inaccuracies. The valve provides enough pressure to counteract the inertia of the discharged liquid, ensuring proper operation.
Injection quills are equipped with built-in check valves to prevent backflow of the dosed chemical. They are designed to introduce the chemical into the center of the flow stream, ensuring uniform distribution and thorough mixing. These quills also include flow calculations to determine the natural frequency. Beveled end injection quills enhance dispersion and reduce the risk of corrosion or fouling from concentrated chemicals.
An anti-syphon check valve combines back pressure and check valve functions to prevent siphoning, which occurs when fluid continues to flow and be drawn out after the pump stops. This issue arises when the pressure on the discharge side of the pump is lower than on the suction side. Anti-syphon check valves are designed to prevent overfeeding and backflow in the mainline, ensuring proper fluid management.
An air chamber is a device used to dampen vibrations and pulsations generated by a reciprocating pump, leading to a more stable liquid flow. By releasing air, the chamber helps minimize pulsations within the pipeline.
Air chambers function in conjunction with throttle valves, through which the liquid flows after leaving the air chamber. The liquid accumulates in the air chamber based on the pressure loss relative to the air pressure.
A pulsation damper serves a similar purpose to an air chamber, aimed at reducing pulsations and vibrations from a metering pump. As fluid is discharged, it enters the damper, which compresses a gas-filled bladder or diaphragm to absorb and mitigate system vibrations. Pulsation dampers promote a smooth and steady flow, and they are compatible with all types of metering pumps.
Calibration cylinders are used to measure the flow rate of a fluid, taking into account factors such as fluid viscosity, the pump’s position relative to the fluid source, and wear on pump components. They are installed on the suction side of the pump, where the drawdown of the fluid column is timed to determine the flow rate and ensure accurate dosing. Calibration should be performed whenever there is a change in fluid properties or alterations in the pump's operation.
The image below illustrates the placement of a calibration cylinder in relation to the valves and the pump within a metering pump system.
Like all pumps, a pressure gauge is used to measure the pressure of a liquid and ensure it remains within specified limits. It acts as a safety device to protect the pumping system from potential damage or explosion due to excessive pressure levels.
The spring of a pressure gauge reacts to compression or expansion to provide a reading in compliance with Hooke’s law of force. Modern pressure gauges are digital and supply numerical readings. They are completely automated and provide readings that can be sent to laptops or desktop computers.
Strainers in metering pumps serve the same purpose as those used in other applications: they filter out particles and debris that could disrupt the pump’s operation. For metering pumps, strainers are positioned before the suction side of the piping. They are particularly useful when drawing materials from the top of a tank, vat, or container where debris might accumulate.
Strainers help remove impurities or potential contaminants from the fluid. The Y configuration is the most common type of strainer used for this purpose.
A degassing valve is used to expel dissolved gases such as oxygen and carbon dioxide from the liquid flow. These trapped gases are vented back to the supply tank. Installed at the highest point in the piping system, degassing valves help prevent gas accumulation that could lead to vapor lock. Degassing connectors are crucial for ensuring the valve system and metering pump function correctly.
Chemical dosing processes often generate gases, including those from substances like sodium hypochlorite, hydrogen peroxide, or sulfuric acid. Movement or compression of these chemicals produces vapors that need to be properly vented.
The images below illustrate examples of installed metering pump systems.
Control volume pumps, injection pumps, feed pumps, dosing pumps, and metering pumps are utilized for injecting chemical additives, proportional blending, and transferring liquids. Their key advantage lies in their ability to precisely control and adjust the flow rate. The efficiency of metering pumps is influenced by their suction and discharge capabilities, which can be fine-tuned by adjusting the stroke length and speed.
Detergent dosing metering pumps are specifically engineered for use in commercial washing machines. They dispense the precise amount of detergent needed for each washing cycle, helping to minimize waste. By preventing blockages in machines, enhancing the efficiency of the laundry process, and safeguarding workers from exposure to detergents and chemicals, these pumps play a crucial role in maintaining operational efficiency and safety.
Automated dispensing of raw materials for packaging represents a streamlined production operation that requires no human intervention. Today, automated packaging systems integrate all stages of the packaging process into a single set of operations, enhancing efficiency.
Challenges with automated dispensing often arise when transitioning between different products. This issue has been addressed with digitally controlled volumetric adjustments, which significantly reduce the time required to switch from one product to another.
Metering pumps are utilized for dispensing chemical mixtures in municipal water supplies and wastewater treatment applications. They are selected for their energy efficiency, which is crucial for optimizing production and controlling energy costs in water treatment plants. By providing precise chemical dosing, metering pumps help water treatment facilities achieve and surpass their operational goals.
Metering pumps are used to inject chemicals such as methanol, monoethylene glycol, and corrosion inhibitors into gas and oil flows. This helps prevent issues like hydrate formation, wax and scale buildup, and corrosion, which can obstruct flow and reduce production efficiency. Additionally, using corrosion inhibitors enhances safety by minimizing the risk of leaks and spills.
Durability is a key requirement for metering pumps in the oil and gas industry. These pumps are designed to be highly resilient, with an estimated lifespan of up to 20 years without needing repairs or replacements.
Center pivot irrigation systems often require the injection of nitrogen into the water supply as it is drawn from a pond, river, or other local sources. The water is directed through pivoting points and applied to crops. Metering pumps are installed at these pivot points to manage the injection process. These pumps can be either portable, allowing them to be used with multiple irrigation systems, or compact enough to remain a permanent fixture at the pivot point.
For irrigation purposes, metering pumps are typically connected to 55-gallon drums containing nitrogen. As the nitrogen is drawn from the tanks, it is mixed with the water and distributed through the sprinkler heads. This system ensures that the nitrogen is effectively applied to the crops while minimizing the risk of it contaminating the groundwater supply.
A metering pump system is engineered to precisely distribute, transfer, and inject specific quantities of fluid into various processes, applications, or operations. The fundamental component of this system is the metering pump, which regulates the fluid volume according to the system’s requirements.
These systems are integral to a wide range of industries, including chemical manufacturing, pharmaceuticals, food and beverage production, water treatment, healthcare, commercial dispensing, irrigation, oil and gas, milling, wastewater management, plastic processing, metal fabrication, automotive, and analytical fields.
There are four primary categories of metering pump systems: diaphragm, bellows, peristaltic, and piston.
A diaphragm system operates with a flexible membrane that oscillates to transfer fluids. When the membrane moves back, it creates a vacuum that draws fluid into the chamber. The volume of fluid is controlled by the stroke length of the diaphragm mechanism. After the desired volume is reached, the membrane moves forward, pushing the fluid out through the outlet valve.
A bellows metering system features a series of interlinked circular membranes that are sealed together. One end of the bellows is connected to the fluid source, while the other end is equipped with a mechanical arm operated by a motor.
As the bellows extend, they draw in fluid until the desired volume is reached. Once the volume is achieved, the bellows compress to expel the fluid through the outlet valve. These systems are ideal for applications needing a constant flow rate at low flow and pressure levels.
A peristaltic metering system utilizes a rotor, tubing, and rollers to manage fluid flow. The fluid travels through the tubing, which is pressed by rollers connected to the rotor inside a sealed housing. As the tubing fills with the fluid, the flow is temporarily halted until the desired volume is reached. The rotor’s rotation then discharges the measured fluid, and the cycle repeats with new fluid entering the tubing. This mechanism allows for efficient and precise fluid transfer.
One key benefit of peristaltic metering systems is their capability to handle dirty or contaminated fluids, which is challenging for other systems. The fluid remains confined within the tubing, which is made from materials resistant to corrosive or harmful substances, thereby avoiding direct contact with the internal components.
The piston metering pump system operates by using the piston’s motion to generate a vacuum that draws in fluid. The volume of fluid pulled into the pumping chamber is directly related to the piston’s stroke length. Once the desired volume is reached, the piston moves forward to expel the fluid through the outlet valve.
In a piston metering pump, the inlet and outlet valves function as check valves, allowing fluid to move in only one direction. As the piston retracts to create a vacuum, the inlet check valve opens, permitting fluid to enter. When the piston advances to discharge the fluid, the inlet valve closes while the outlet valve opens to release the fluid, ensuring a controlled flow.
Metering pumps play a crucial role in dispensing systems. Choosing the right metering pump requires thoughtful evaluation to ensure it meets the specific requirements of the application.
The flow rate is central to the operation of a metering pump and must align with the specific needs of the application. Fluid viscosity affects the flow rate and dictates the stroke force required to transfer the fluid. Flow rate refers to the speed at which the fluid is dispensed, and accurate calculation is crucial for optimal pump performance.
Turndown ratios indicate a metering pump's ability to handle low flow rates while maintaining accuracy. Variations in temperature and pressure during operation can affect pump performance. A well-selected metering pump allows for adjustments to both stroke and drive mechanisms to ensure the desired flow rate is achieved.
Different applications demand varying pressure levels from metering pumps. For example, water treatment typically requires pressures below 100 psi, whereas industries like oil and gas may need pumps that handle pressures exceeding 20,000 psi. Metering pumps are specifically designed to accommodate these diverse pressure needs.
A pump's capacity is influenced by factors such as gear ratio, piston diameter, and motor RPMs. As the piston diameter increases and stroke speed rises, the pressure capabilities of the metering pump generally decrease.
The adaptability of metering pumps is crucial in production environments where dispensing of raw materials and finished products occurs. When product specifications change, the metering pump system must be capable of adjusting and being reconfigured to fit the new requirements.
Metering pumps must be designed to handle varying demands in production settings. While small metering pumps can easily accommodate these changes, larger and more complex systems require careful planning. The specific needs of a production environment significantly impact the choice of metering pump.
In industrial and production settings, metering pumps must be robust, reliable, and durable to handle various operational demands. For applications involving chemicals, corrosives, and toxic substances, it’s essential to select pumps made from materials compatible with these agents. This careful selection process guarantees the pump's longevity and the safety of personnel.
When used under optimal conditions, metering pumps can provide reliable performance for up to twenty years without requiring repairs or replacement. This durability has solidified their role as a critical component in manufacturing processes.
A lubricant is a substance that is applied on surfaces that have relative motion in between them. The lubricant reduces friction and wears between the surfaces. However, the lubricant can have other...
Lubrication systems distribute the lubricant to the moving machine parts in contact. Lubricants reduce the friction between sliding or rolling machine elements, such as gears, spindles, bearings, chains, dies, screws, cylinders, valves, and...