Agitators
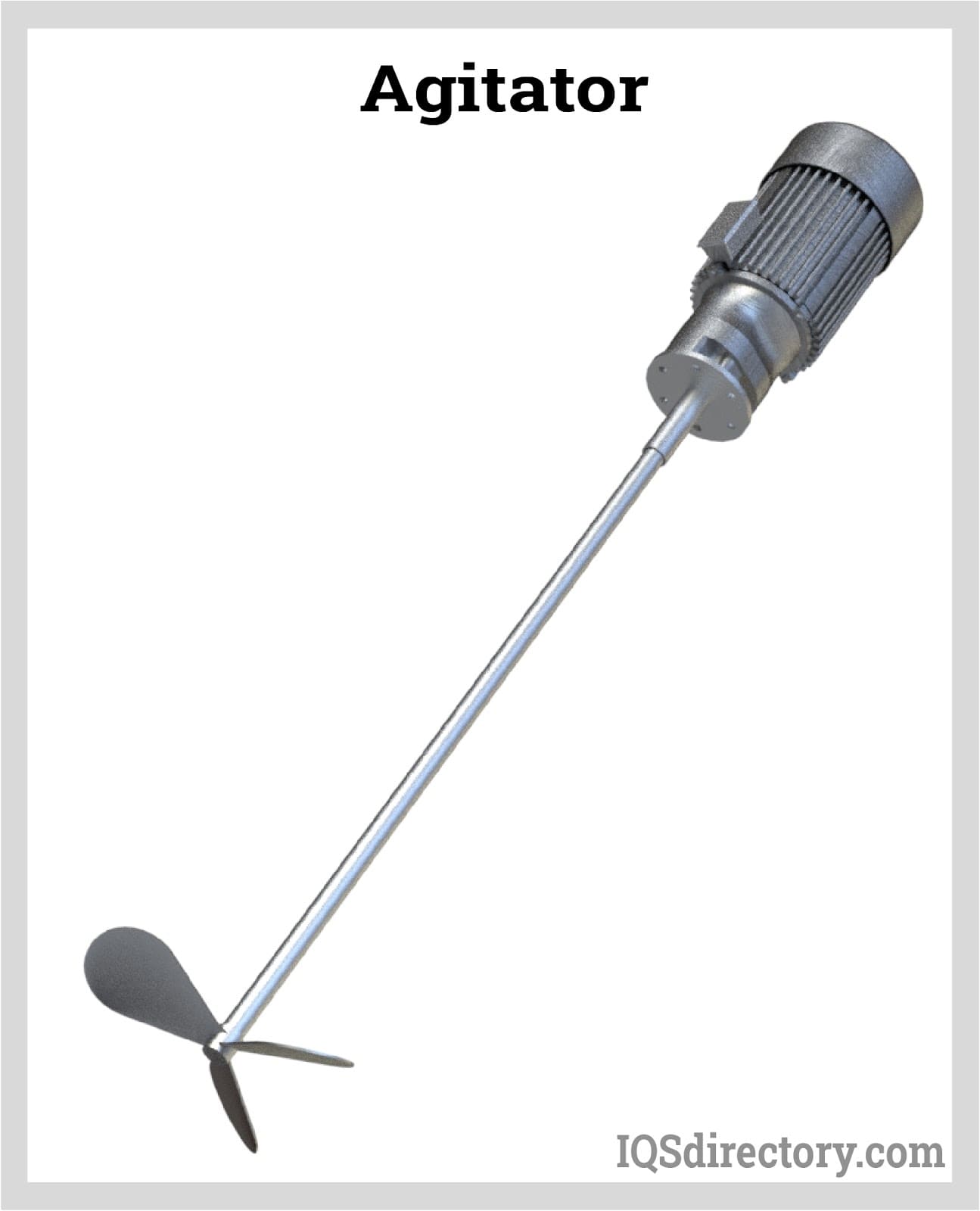
Agitators are equipment used in homogenizing media inside a tank. It works by rotating the impeller at its immersed end at a controlled speed or revolutions per minute (rpm). The work exerted by...
Please fill out the following form to submit a Request for Quote to any of the following companies listed on
This article contains everything you will need to know about drum mixers.
You will learn:
Drum mixers are specialized machines crafted to mix free-flowing materials through a rotational motion both forward and backward. They use welded chutes or flights to create a fluidized mixture, making them ideal for dealing with materials of varying consistencies, from granular substances to powders with diverse densities and particle sizes. A quintessential example of drum mixers is the concrete mixer, commonly known as a tilting mixer, which is used for single-batch concrete mixing.
In a drum mixer, the mixing procedure begins with the introduction of ingredients into the mixer's barrel. As this barrel revolves around its central axis, the materials within it are moved up and down as well as forward and backward. Known under many names, such as dimensional mixer, rotating horizontal mixer, rotary drum blender, and rotary drum mixer, these devices are recognized for their compact size and small footprint. They function quietly and safely, ensuring ease of use, and are especially common in the food and pharmaceutical industries for the gentle combination of powders and granules.
Understanding how a drum mixer operates is crucial for selecting the ideal industrial mixing solution for your application. Various types of drum mixers are available in the market to suit distinct processing requirements in sectors such as chemical manufacturing, pharmaceuticals, food processing, and construction. Some of the most common drum mixer variations include mixers that rotate 55-gallon drums, direct drive mixers, cement mixers, and rotary drum mixers. While each variant delivers unique performance benefits, 55-gallon drum mixers and direct drive mixers remain popular due to their simplified design, minimal components, and ease of integration into production lines. When comparing drum mixers, it’s important to consider the viscosity of your materials, mixing objectives (such as blending, dissolving, or dispersing), batch size, and required mixing speed.
A 55-gallon drum tumbler is a specialized drum mixer engineered for efficiently blending or mixing the contents of a sealed drum. These mixers are commonly utilized for homogenizing powders, granules, liquids, and semi-solids in industries where product consistency and batch uniformity are essential. Operating similarly to rolling a drum across the floor, a 55-gallon drum tumbler ensures even distribution of components without the need for internal agitators. There are two main types of drum tumblers:
Direct drive mixers serve as a robust solution for process industries requiring efficient and high-speed mixing in large drums. These drum top mixers are larger, industrial-grade versions of standard hand mixers, typically designed for mounting onto 55-gallon drums or bulk containers. Their strong electric or pneumatic motors enable mixing of low to medium viscosity fluids, slurries, chemicals, and polymer solutions. Installation can be achieved through various methods, including placements in the drum's bunghole or clamping directly onto the drum lid.
Direct drive drum mixers typically feature a 36-inch mixing shaft that connects securely to a high-performance motor coupler. Multiple impeller designs, fastened with set screws, allow the mixer to be tailored for tasks such as emulsifying, dispersing, and dissolving. Users can choose from a variety of mounting options—plate, cup, clamp, or angle brackets—catering to different drum configurations, process environments, and material characteristics. These secure mounts enhance worker safety and operational flexibility.
Unlike gear drive mixers, direct drive units operate at fixed, typically high rotational speeds around 2000 rpm. This makes them ideal for applications demanding intense shearing, such as the dispersion of additives, incorporation of powders into liquids, or blending of paints and coatings. The specialized impeller designs create high-velocity turbulence, breaking down agglomerates and ensuring thorough homogenization in small batch operations. For processes demanding frequent batch changes or mobile mixing solutions, direct drive drum mixers offer unmatched portability and versatility.
Cement mixers, often synonymous with concrete drum mixers, are engineered for the efficient blending of cement, aggregates, sand, and water. Unlike tumbler mixers and direct drive mixers that function more as blenders or agitators for lighter materials, cement mixers feature a robust internal structure specifically designed for heavy-duty mixing applications. Inside the rotating drum, strategically angled fins or blades lift, tumble, and fold the ingredients, ensuring uniform consistency and preventing clumping of cement and aggregates.
At the top of the drum, a large opening allows for convenient loading of raw materials. Once all components are added, the mixer is activated, and the drum rotates continuously at a controlled speed. This cyclical motion ensures that all elements are thoroughly integrated for optimal hydration and structural integrity in the final concrete product. Industrial cement mixers are indispensable on construction sites for producing large volumes of ready-mix concrete, while portable drum mixers find uses in smaller building projects, repair work, and testing laboratories.
Rotary drum mixers represent some of the most advanced industrial mixing technology available. These continuous or batch mixers are engineered for gentle but thorough blending of granular, powder, and particulate materials. Raw materials are introduced through a top inlet, utilizing gravity to efficiently load the drum. As the vessel rotates slowly, gravity and the drum's internal flights, lifters, or chutes continuously fold, cut, and turn the contents, promoting optimal intermixing while minimizing material degradation and dust generation.
Rotary drum mixers are highly valued in bulk material handling, mineral processing, pharmaceutical compounding, fertilizer blending, and biomass mixing due to their energy-efficient operation and gentle handling of fragile or abrasive products. Once the mixing cycle is completed, the homogeneous mixture is discharged via a gravity-operated gate or a screw auger to facilitate fast, controlled outflow for packaging or further processing. Automated feeding, precise weighing, and customizable mixing parameters further enhance process efficiency and product quality in industrial drum mixing systems.
Choosing the Right Drum Mixer: When evaluating and purchasing industrial drum mixers, consider essential factors such as material compatibility, drum size, required level of agitation, energy efficiency, ease of cleaning, and compliance with safety standards. Renowned drum mixer manufacturers offer a range of features including explosion-proof motors for hazardous environments, variable speed controls, interchangeable impellers, and washdown-capable designs. By identifying your process requirements and budget, you can select a drum mixer that delivers optimal mixing performance, product consistency, and long-term value.
Drum mixers, also known as barrel mixers or drum blenders, come in a diverse array of types designed to accommodate the broad spectrum of industrial mixing needs. Their widespread adoption is due to key advantages such as versatility, user-friendliness, rugged construction, and consistent mixing efficiency. Drum mixers are essential equipment for processing bulk materials in industries like construction, pharmaceuticals, chemicals, food & beverage, and manufacturing. This comprehensive guide explores the main types of drum mixers—including compact, portable drum mixers and large-scale horizontal rotary drum mixers—clarifying how each is engineered for specific applications and material types.
Within the drum mixer category, mixers are often classified by the type of container used, typically 55-gallon drums or barrels, and the method used to blend ingredients that may settle or separate during storage and transportation. Specialized drum mixers ensure thorough mixing, homogenizing, and suspension of materials such as powders, liquids, slurries, and granular substances.
Prominent categories among drum mixers include drum concrete mixers, 55-gallon drum mixers, direct drive drum mixers, and rotary drum mixers. Concrete drum mixers—further divided into tilting, non-tilting, and reversing models—are vital to construction sites and ready-mix operations. Horizontal rotary drum mixers, recognized for their continuous, large-scale mixing capabilities, play a pivotal role in industrial batch processing and production lines.
Barrel drum mixers are engineered to thoroughly blend loose and granular materials, such as powders, pellets, and dry chemicals, within a rotating barrel or drum. Each mixer uses a rigid hoop to secure the barrel during mixing, which relies on smooth rotation, allowing contents to mix thoroughly without the friction or mechanical breakdown that can occur with impeller or blade mixers.
The frictionless mixing action eliminates dead zones and prevents material degradation or cross-contamination due to heat, making barrel drum mixers particularly effective for sensitive applications like food processing, pharmaceuticals, and pigment blending. Available with pneumatic or electric drives, and offering a variety of drum capacities and configurations, these mixers combine precision control with adaptability to suit any operational scale.
The reliability and adaptability of barrel drum mixers have fueled their popularity across many industries. They provide an economical solution for low-volume batch mixing and are frequently used for blending powders, dyeing, homogenizing, granule mixing, and specialty product formulations. Their roll on/roll off design further supports rapid batch changes, ideal for research labs, pilot plants, and small-scale production. For an overview of how batch mixers can be used to streamline your mixing processes, review our resource on batch mixers.
55-gallon drum mixers, sometimes referred to as industrial drum agitators, are specifically designed to mix, agitate, or reblend the contents of standard 55-gallon drums. These mixers address sedimentation issues by redistributing solids and liquids that have separated during extended storage or shipment, ensuring product consistency and quality control. Drum agitators are also used to dissolve powders, disperse pigments, and maintain emulsions within drums.
There are several configurations including closed head (bung entry) mixers, open head (removable lid) mixers, and direct drive drum mixers. Most feature a long mixing shaft and impeller assembly powered by an electric or air motor, with some models utilizing ribbon impellers or collapsible blades for optimal blending and material circulation.
Closed head mixers allow for mixing without opening the drum, minimizing operator exposure to hazardous materials and reducing the risk of contamination or spillage. They are inserted through the drum’s bunghole and are ideal for mixing volatile, sensitive, or hazardous chemicals. Open head drum mixers, conversely, offer greater flexibility for adding or inspecting materials during mixing, using a dedicated mixer lid and accommodating a wider range of impeller designs and capacities.
These industrial drum mixers support a full spectrum of mixing tasks—from blending adhesives and coatings to preparing slurries and processing viscous fluids—making them essential in paints, coatings, chemical, and food manufacturing. Specialty drum mixers are available for high-viscosity mixing, heating and blending with drum heaters, and integration with automation systems.
Drum rollers, or rotary drum mixers, offer an alternative approach by agitating the contents of the drum through gentle rolling motion, minimizing the risk of contamination and reducing cleaning requirements. These mixers are used to shake, blend, and suspend materials inside fully sealed 55-gallon plastic or steel drums, promoting workplace safety and reducing direct contact with chemicals or hazardous materials.
Operation involves placing the drum horizontally on rollers, where controlled rotation agitates the ingredients. Drum rotators are highly portable and adaptable, allowing the use of individual drums for batch processing and enabling seamless movement across warehouse or production environments. Adjustable roller systems can accommodate various drum sizes, making these mixers suitable for powders, liquids, viscous slurries, coatings, paints, adhesives, and resins.
Drum rotators are favored for rapid batch blending, premixing of additives, ball milling applications, and situations where minimizing cross-contamination and downtime is crucial. These devices are commonly used in the chemical, pharmaceutical, and coating industries for efficient drum handling and safe, thorough agitation of bulk materials.
Tilting drum mixers are a principal style of concrete drum mixer, pivotal in construction, precast, and infrastructure projects requiring high-speed mixing and fast, efficient discharge. This mixer discharges its blended contents by tilting, allowing for easy, controlled unloading—reducing cycle times and supporting rapid batching for concrete pours and mortar production.
The blades within the tilting drum mixer are engineered to lift, turn, and tumble aggregates, water, and admixtures. Horizontal tilting drum mixer variants provide both side and bottom discharge options, ensuring flexibility in charging and unloading. Users can select models with single or double tilting mechanisms to suit project requirements.
These mixers are commonly found on construction sites and in precast concrete manufacturing plants, delivering uniform mixes while minimizing labor. They handle large aggregate efficiently, providing consistent batch quality for roads, bridges, floors, and structural components.
The non-tilting drum mixer, or reversing drum mixer, features a continuously rotating drum loaded through a charge chute and unloaded via a discharge chute. With fixed internal mixing blades, these mixers repeatedly lift and cascade materials for thorough blending. Upon completion, the drum reverses rotation to move the mixture toward the discharge outlet, facilitating rapid unloading.
Ideal for mixing concrete, these mixers guarantee batch consistency, especially when large volumes and continuous operation are required. Their robust design, with capacities commonly reaching up to 1 cubic yard (0.76 cubic meters), makes them staples in ready-mix concrete plants and large construction projects.
Continuous drum mixers facilitate seamless, high-throughput mixing for industrial production lines. By gravity feeding raw materials from one end and discharging finished blends from the other, these mixers excel in bulk processing environments, where consistency and speed are critical. Integrated screw conveyors, augers, or feeders regulate ingredient flow, ensure even distribution, and eliminate batch-to-batch variation.
The low-speed tumbling action, combined with carefully engineered internal flights, achieves homogeneous mixing of powders, granules, or wet materials without excessive energy consumption or residence time. Continuous drum mixers are indispensable in asphalt production, dry mortar blending, fertilizer granulation, animal feed preparation, and bulk solids processing—delivering reliable, efficient, and scalable results for high-demand operations.
Flotti mortar drum mixers are specialized mixing machines designed for precision blending of ready-mix dry mortar products, including cement, plaster, tile adhesives, and screeds. Their compact size, low maintenance needs, and energy-efficient 220V motor make them excellent for small-scale or satellite construction sites, masonry, and remodeling projects where rapid, portable mixing is needed.
Engineered for both continuous and batch production, Flotti mixers provide automation-friendly operation, and their portability ensures they can be deployed wherever fresh mortar is needed. This versatility helps tradespeople maintain high-quality mortar consistency, reduce waste, and minimize downtime between batches.
Two-dimensional rotary drum mixers leverage both rotary and swinging movements, providing multidirectional agitation for rapid, uniform blending. These mixers move the drum along two axes, mixing sensitive or high-value materials gently and thoroughly. Key features include an oscillating support frame, adjustable speed controls, and precision bearings for quiet, vibration-free operation.
Extensively employed in pharmaceuticals, food blending, dye processing, animal feed manufacturing, fertilizer production, and specialty chemical applications, these mixers are valued for their gentle action, efficiency, and capacity for processing a wide range of material types—from fine powders to granular and pelleted bulk solids.
Three-dimensional rotary drum mixers incorporate a third axis of motion—introducing a pulsing, twisting action in addition to swinging and rolling—to achieve exceptional homogeneity and particle distribution. This advanced motion simulates manual bottle shaking, redistributing ingredients from center to ends and top to bottom, making these mixers ideal for blending complex multi-component or sensitive products.
With batch sizes ranging from 1.3 to 79 gallons (5 to 300 liters), three-dimensional mixers are optimized for pharmaceuticals, nutraceuticals, advanced ceramics, and specialty composites. Quick-change drum mounting systems and ergonomic designs minimize labor and increase productivity, making them ideal for pilot-scale manufacturing and agile production settings.
Horizontal rotary drum mixers are engineered for gentle, yet thorough blending of sensitive, fragile, or temperature-sensitive materials—such as pharmaceuticals, food ingredients, specialty polymers, and composite powders. These mixers rely on gravity and internal flights or chutes to thoroughly tumble, cut, and fold materials during rotation, preserving product integrity and minimizing heat build-up.
Stainless steel or carbon steel construction ensures sanitary operation, while customizable inlets, outlets, and interior configurations accommodate even the most demanding batch processing or continuous mixing requirements. Adjustable rotation speeds (around 15 rpm) and auger-fed loading make these mixers highly efficient for blending, granulating, or coating operations. Moisture addition through spray nozzles or in-line injection supports the processing of hydrated or coated products.
Widely adopted in industries requiring contamination-free, precision blending and reduced cleaning frequency, horizontal drum mixers streamline workflow, increase throughput, and deliver consistently high-quality blends ideal for packaging, further processing, or direct end-use.
Rotary drum mixers are efficient devices that use minimal power for mixing. They offer a cost-effective solution for blending powders, granular materials, and substances that need a slow, gentle mixing process.
The simple design of rotary drum mixers makes them ideal for the blending process. Their rotating motion that continuously moves ingredients upwards and downwards evenly distributes the ingredients into a homogeneous mixture. The constant motion provides full contact and exchange between a material’s particles for fast and uniform mixing.
The slow rotation of a rotary drum mixer requires minimal energy, operating at just 5 rpm to 15 rpm. The electric motors used consume very little power and operate nearly silently. The slow and controlled process also produces minimal dust, which helps reduce environmental pollution and issues with airborne dust.
Rotary drum mixers come in various types that can blend a wide range of ingredients. Some models allow for quick changes between different materials with minimal effort. This adaptability is a key reason many industries rely on them. They are effective for mixing a broad spectrum of granular and powdered ingredients, including those needing additives or moisture.
The operation of a rotary drum mixer is straightforward and uncomplicated, requiring no complex controls or monitoring. Its simple structure includes a drum of various sizes, support rollers, an electric motor, and inlets and outlets. Operators can initiate mixing with minimal training.
While industrial rotary drum mixers may occupy a large space, their overall footprint is generally quite compact. Their simple design contributes to their small size, saving both electricity and space.
Rotary drum mixers ensure thorough mixing by evenly distributing ingredients. This leads to improved uniformity and solubility of dry materials, making the final mixture more consistent and effective.
Among the different mixing solutions available, rotary drum mixers stand out for their durability and longevity. Constructed from premium stainless steel and carbon steel, these mixers are designed to handle a variety of mixing tasks efficiently over an extended period.
The minimal number of moving parts in a rotary drum mixer reduces the risk of wear and tear, contributing to its longevity. Additionally, the corrosion-resistant metals used in the construction of these mixers make them suitable for use in challenging and aggressive environments.
Rotary drum mixers have short mixing times due to the absence of friction, rising temperatures, and hot spots. This ensures efficient and quick mixing.
The flights or chutes in a rotary drum mixer gently lift and transfer the product throughout the mixer. Powders and granules of varying densities and particle sizes mix quickly and gently.
Aside from the highly durable materials used to construct rotary drum mixers, the lack of stress and wear removes the need for regular maintenance. Without drive parts or bearings being exposed to ingredients and low power requirement, rotary drum mixers are maintenance free, even after running continuously for long periods of time.
The straight forward design and easy access makes rotary drum mixers very easy to clean, which is especially necessary in food production and the pharmaceutical industry.
Drum mixers are extensively utilized in both the pharmaceutical and food industries due to their ability to handle ingredients with care. In the pharmaceutical sector, rapid mixing can harm sensitive ingredients, while in the food industry, fast blending might compromise the flavor of certain components.
In the food industry, drum mixers play a crucial role in specialized processes such as vitamin-enriching rice, mixing soup components, and blending various teas. These applications require a gentle mixing approach, often involving the use of a spray. For example, gourmet teas flavored with mango and dried peach blend effectively in a drum mixer. Additionally, drum mixers are commonly employed in the production of powdered nutritional drinks.
Drum mixers are widely used in the animal feed industry to mix ingredients for large-scale storage. Given the high volume and precision required in feed production, drum mixers are engineered to blend grains and powders efficiently, ensuring consistent quality for bulk storage systems.
In the pharmaceutical field, drum mixers are ideal for blending delicate powders to produce medicinal products. The absence of moving parts such as impellers and blades allows for a gentle mixing process, minimizing friction that could damage sensitive chemicals. This design feature ensures that ingredients can be mixed and then transferred into barrels or drums without compromising their quality.
Drum mixers are integral to concrete production, providing a reliable method for efficiently mixing concrete materials. They ensure a consistent texture, which is critical for high-quality concrete. Due to their durability and ability to endure the rigors of construction environments, drum mixers are a staple in the industry. Their mobility, ease of use, and various sizes make them suitable for diverse construction projects.
Agitators are equipment used in homogenizing media inside a tank. It works by rotating the impeller at its immersed end at a controlled speed or revolutions per minute (rpm). The work exerted by...
An emulsifier is an emulsion device used for colloidal dispersion of liquid droplets of immiscible liquids in the presence of an emulsifying agent. It enables the combining of non-soluble solutions or liquids...
High shear mixers, also known as high shear reactors (HSRs), rotor-stator mixers, and high shear homogenizers, are used to emulsify, homogenize, disperse, grind and/or dissolve immiscible mixtures with components of the same or different phases...
A homogenizer is a type of mixing equipment used to create a uniform and consistent mixture. It works by breaking the components and evenly distributing them throughout the solution. The components are either immiscible, have varying sizes, or are in different phases from each other...
An industrial blender is a machine for large-scale production that consists of a large tank capable of mixing and blending batches of manufacturing materials to create a reaction between the materials. The many uses for industrial blenders are due to their capacity and...
A mill is a mechanical device that is often a structure, appliance, or machine that is used to break down solid materials into smaller pieces by cutting, grinding, or crushing them. Many industrial processes involve...
A tank mixer is a mixing device that blends several different ingredients in a single tank to make a single solution. It is a mixing process capable of mixing wettable powders, liquids, emulsifiable concentrates, and surfactants. They mix and blend...
A mixer is a complex and precise tool that is used in combining and mixing of substances and chemicals for manufacturing, production, and industrial use. There are many types of industrial mixers including...
A plastic tank is a large capacity liquid or granular storage unit that can be vertical, horizontal, below or above ground, as well as movable. They are designed to hold several gallons of a variety of substances for long periods without experiencing wear, weathering, or deterioration...
A plastic water tank is a large capacity container designed to store water for household, agricultural, irrigation, and industrial manufacturing use. There are various types of water tanks produced to meet the needs of specific applications, with...
A poly tank is a plastic storage tank used to store, transport, and collect water, other liquids, and granular or powder materials. They are made of polyethylene or polypropylene and are a cost effective, lightweight, and easy to handle...
Pressure tanks are vessels that are used to store, hold, and/or convey gasses, vapors and fluids at pressures greater than atmospheric pressure, also known as high pressures...
Pressure vessels are enclosed containers used to hold liquids, vapors, and gases at a pressure significantly higher or lower than the ambient pressure. They are widely used in various industries such as...
Stainless steel tanks are widely used in food, beverage, dairy, medicine, cosmetics, and other manufacturing processes where cleanliness and purity are important. These are also used in industrial plants for storing chemicals and gases where strong resistance from chemical degradation is required...