Agitators
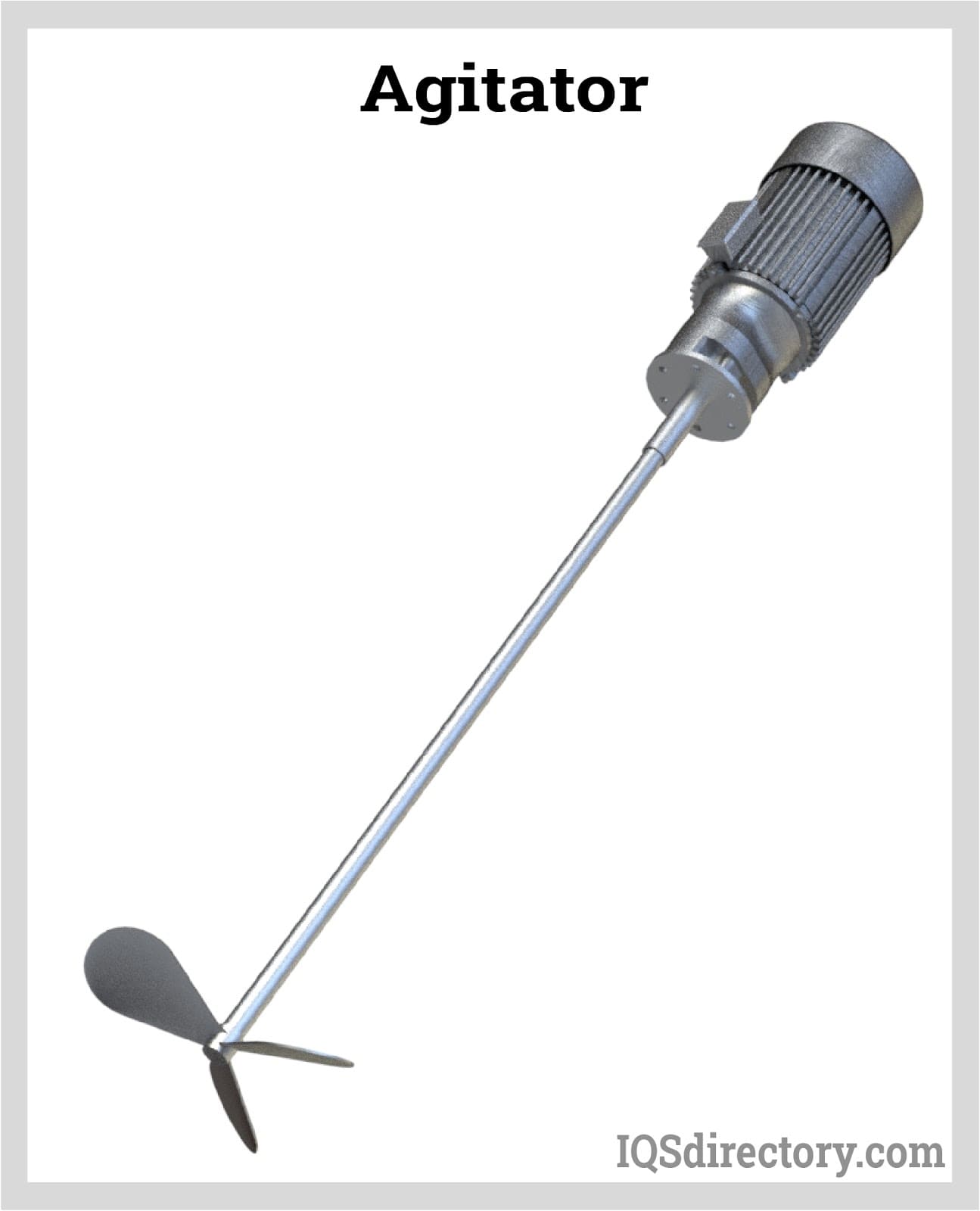
Agitators are equipment used in homogenizing media inside a tank. It works by rotating the impeller at its immersed end at a controlled speed or revolutions per minute (rpm). The work exerted by...
Please fill out the following form to submit a Request for Quote to any of the following companies listed on Static Mixers .
The content of this article is everything you need to know about static mixers and their use.
You will learn:
A static mixer is a type of device that employs forced flow to merge both miscible and immiscible materials into a uniform mixture. It comprises a tube equipped with mixing blades or elements that alter the flow's direction and movement, ensuring thorough blending of all gases, fluids, and liquids. Fluids can enter a static mixer through various means, with pumps and gravity being two of the most prevalent methods.
In contrast to other mixing methods, static mixers do not incorporate moving components, thereby eliminating the need for maintenance. This design minimizes energy usage and negates the requirement for electrical elements. Featuring helical barriers that compel the flow to integrate, inline mixers, also known as static mixers, are utilized in manufacturing operations and processing lines with a continuous material flow. They ensure the rapid and effective mixing of a constant stream of liquids or gases.
The simple yet highly effective design of static mixers belies their advanced capabilities for continuous mixing, blending, and homogenizing of liquids and gases in industrial process applications. Although most static mixers are manufactured from heavy, sturdy metals designed to withstand high pressure and aggressive chemicals, specialized varieties utilize chemical-resistant plastics, such as polypropylene and polyvinylidene fluoride (PVDF), for less demanding or highly corrosive environments. The main components of these industrial mixing devices—the tube (mixer housing) and internal mixing elements—are manufactured from an assortment of materials including high-quality engineered plastics, 316 stainless steel, as well as more advanced materials like glass-lined steel and exotic alloys to ensure compatibility with critical manufacturing processes in petrochemical, food and beverage, water treatment, and pharmaceutical industries.
The housing for a static mixer serves as the pressure vessel that encases the mixing elements and is crucial for ensuring process safety and performance. Static mixer housings can be fabricated from a range of materials—including metals like stainless steel (304, 316), high-strength aluminum alloys, hastelloy, titanium, as well as thermoplastics such as PVC, CPVC, polyethylene, or specialty fluoropolymers like Teflon (PTFE). The choice of housing material is dictated by several factors: the type of fluids (acids, caustics, high viscosity liquids), operating temperature, process pressure, and industry-specific sanitary regulations. For instance, the chemical processing and water treatment sectors often specify high chemical resistance, while the food and beverage industry demands materials that are hygienic and easy to sanitize, favoring stainless steel for its non-porous, corrosion-resistant surface.
The cylindrical configuration of most static mixer housings is designed to seamlessly integrate into existing pipework or custom inline mixing systems, minimizing pressure drop and ensuring laminar-to-turbulent flow transition as appropriate. Static mixers are commonly installed in-line within process piping, allowing for efficient continuous mixing of fluids in motion without needing external power or moving parts. Features such as flanged ends, threaded connections, or tri-clamp fittings can be specified based on installation requirements. Engineering the housing to exact tolerances is a key part of process equipment design, as factors like flow rate, viscosity, and compatibility must be considered early in the manufacturing process to guarantee maximum mixing efficiency and performance consistency.
The heart of every static mixer lies in its mixing elements—engineered components arranged within the housing to optimize flow dynamics, maximize surface renewal, and induce radial and axial mixing. These elements are custom-made from a wide variety of materials, including chemical-resistant plastics (like PTFE and PVDF), various stainless steels, titanium, and specialty alloys. Selection depends on process compatibility, abrasive wear, fluid toxicity, temperature, and pressure. Static mixer elements can take several forms, including helical blades, baffles, channels, fins, and more, each optimized to achieve a specific type of mixing, dispersion, or emulsification. Advanced CFD (computational fluid dynamics) modeling is often used in the design phase to validate and optimize performance for specialized applications such as polymer blending, gas-liquid mass transfer, and high-viscosity fluid processing.
Blades – Blade mixing elements are engineered in various shapes—such as helical, twisted, or spiral—and are precisely positioned to split and redirect the process flow, generating turbulence and maximizing mixing intensity. The specific shape, pitch, and orientation of blades are critical factors in determining how quickly and completely the fluids are homogenized. High-performance blade mixers are essential in processes that require rapid and thorough blending of fluids of different viscosities or concentrations, such as in adhesives, coatings, or chemical dosing.
Baffles – Baffle elements consist of plates or flat sheets, arranged either diagonally or in a crisscross pattern, creating flow division and recombination that enhance radial and axial mixing. Commonly manufactured from twisted metals, corrugated sheets, or parallel rods, baffles are highly effective for blending miscible liquids with similar viscosities (e.g., water and solvents), as well as maintaining uniformity in suspensions. This design is utilized in industries such as wastewater treatment and chemical manufacturing, where consistent and repeatable mixing is required for high-quality end products.
Channels – Channel mixing elements are characterized by rectangular, square, or custom-profiled cross-sections that generate varied velocity profiles and controlled shearing forces within the mixer. By ensuring even distribution of process fluids, channel mixers minimize energy loss, making them ideal for chemical dosing, polymerization, and precise pH adjustment. Their open architecture is beneficial for systems prone to fouling or those requiring low pressure drop, such as in municipal water treatment and liquid fertilizer blending.
Helical – Helical static mixers are designed with alternating elements set at 90° angles, causing a constant inversion and rotation of the fluid stream. This progressive movement effectively eliminates dead zones and ensures comprehensive blending. Helical mixers are frequently available as removable cartridges for easy cleaning, with options for jacketed or heated configurations to handle temperature-sensitive processes—common in pharmaceutical, cosmetic, or food-grade applications. Their high mixing performance makes them the go-to choice for inline static mixing tasks that demand superior homogenization and low maintenance.
Fin – Fin-type static mixers utilize strategically placed, curved fins to promote intensive mixing of gases or low-viscosity fluids, generating secondary flow patterns and additional vortices that accelerate homogenization. Designs often incorporate multiple, staggered sets of fins, amplifying their ability to quickly and efficiently blend immiscible fluids or disperse gases, a key feature in applications such as aeration, chemical injection, and polymer blending.
The configuration and type of static mixing elements used in a mixer are tailored to each application, ensuring optimal dispersion, emulsification, or reaction enhancement—whether blending chemical additives, homogenizing slurries, or achieving uniform heat transfer in process fluids. Many leading static mixer manufacturers offer custom design and engineering services, leveraging years of process expertise and simulation capabilities to resolve challenging mixing applications, reduce downtime, and improve production efficiency.
For those evaluating static mixers for purchase, it is essential to consider: the chemical and physical properties of fluids, operational environment (temperature, pressure), required mixing intensity, ease of maintenance (including CIP—clean-in-place—capability), pressure drop limitations, and regulatory requirements for your specific industry. Consulting with an experienced static mixer supplier can lead to significant improvements in process control, reduced operational costs, and enhanced product quality. As modern processing demands increase, innovative static mixer technology continues to evolve, helping industries achieve better mixing, safer operations, and more sustainable outcomes.
Static mixers are innovative inline mixing devices that rely on fixed internal elements—such as baffles, channels, blades, discs, and various geometries—to blend liquids, gases, or slurries as they flow through a pipe or tube. The arrangement, orientation, and type of these mixing elements determine the static mixer’s efficiency, mixing intensity, and pressure drop. While pipe static mixers are commonly used in many industrial mixing processes, modern engineering has produced several static mixer types to address specific application requirements, ranging from chemical processing and water treatment to food production and pharmaceuticals. Selecting the right static mixer configuration is crucial for achieving homogeneous mixing, optimal residence time, and energy efficiency.
Wafer static mixers are highly compact, space-saving inline mixers designed for pipelines with diameters from 2 to 120 inches (5.08 cm to 304.8 cm). Their slim disc-like profile enables quick drop-in installation and results in minimal pressure loss, which is ideal for retrofitting older systems or optimizing existing process lines. Unlike larger tube or pipe static mixers, wafer mixers provide effective mixing of up to six separate process streams within a restricted footprint, facilitating dosing, dilution, and blending tasks in water treatment, chemical dosing, and other applications demanding rapid and efficient mixing.
Initially developed to meet the stringent requirements of the desalination industry—removing salt and impurities from seawater—wafer static mixers now serve a broad array of industries including municipal water treatment, power generation, and petrochemicals. Recent innovations in wafer mixer design enable excellent mixing in both laminar and turbulent flow regimes, optimizing mixing performance for additives, disinfectants, polymers, and reagents commonly used in process industries.
The venturi static mixer combination is engineered for high-efficiency gas-liquid mixing, most notably for dissolving gases such as ozone, chlorine, or carbon dioxide into water streams. In this application, a venturi tube raises the fluid velocity and reduces pressure to draw in gas, forming bubbles. The subsequent static mixer, installed downstream, uses its internal mixing elements to break down the gas bubbles into smaller sizes, significantly increasing the surface area for gas transfer and solubility. This targeted mixing maximizes ozone dissolution for advanced oxidation, water disinfection, and industrial effluent treatment applications.
By leveraging the pressure differential created by the venturi and the turbulence induced by the static mixer, this hybrid system ensures reliable dosing, superior mass transfer, and minimized chemical waste. Venturi-static mixer systems are vital in municipal water purification, aquaculture, food processing, and pulp and paper manufacturing where precise gas-liquid mixing is critical for process performance.
Jet static mixers utilize the kinetic energy of a high-velocity jet stream to achieve inline mixing of liquids or to disperse solids and gases. The continuous mixing process is tailored to specific process conditions and fluid properties, providing a solution for quick, energy-efficient homogenization. Jet mixers ensure low pressure drop and high mixing efficiency, efficiently handling both miscible and immiscible fluids and producing uniform blends for downstream processing.
In jet mixing, a fast-moving liquid is injected tangentially or axially into a slower-moving stream, and the resulting velocity gradient initiates intensive mixing as the flow passes through the static mixing elements. This method is suitable for applications involving laminar or turbulent flow, such as chemical blending, wastewater treatment, pH adjustment, polymer preparation, and slurry suspension. Factors like flow rate, viscosity, and pipe diameter influence the selection and number of mixing elements, with advanced CFD modeling often used to optimize static mixer design for critical industries.
The Kenics static mixer, a classic helical inline mixer, is renowned for delivering predictable, repeatable, and energy-efficient mixing in process piping. It employs alternating right- and left-handed helical mixing elements that continuously split, stretch, and reorient product streams, significantly improving radial mixing and eliminating gradients in temperature, concentration, and velocity.
Kenics mixers feature a non-clogging, open-channel design—minimizing material buildup and allowing them to handle high-viscosity fluids, fiber-laden slurries, and polymer melts. Their proven efficiency in blending, dispersion, heat transfer, and emulsification applications makes them a trusted choice for the chemical, pharmaceutical, petroleum, and food processing sectors. Whether installed in laminar or turbulent flow regimes, Kenics static mixers offer precise mixing metrics and low maintenance, optimizing both batch and continuous operations.
Spiral static mixers (also known as disposable or one-time-use mixers) cater to two-part adhesives, resins, coatings, and sealants. Their hallmark is a sequence of 180° alternating helical elements, precisely joined with perpendicular leading and trailing edges. This configuration progressively splits and recombines product streams, ensuring optimal blending in cartridge and tube applications prior to dispensing.
Spiral static mixer assemblies are commonly constructed of high-strength plastics and feature a bell-shaped inlet for easy, clean product loading. For high-pressure applications exceeding 150 psi, spiral mixers can be reinforced with metal jackets or mounted inside durable stainless steel housings. This allows them to withstand industrial-grade mixing tasks, including those in automotive assembly, electronics, construction adhesives, and dental materials.
The wide selection of element diameters, tip styles, and housing types makes spiral static mixers extremely versatile. Their low cost and ease of disposal make them the preferred solution for small-batch and rapid-cure reactive materials that require perfect mixing at the point of application.
Jacketed static mixers are designed to maintain precise process temperatures during mixing by incorporating external heating or cooling jackets around the mixer body. These mixers are especially valuable when handling heat-sensitive fluids, viscous polymers, food products, or temperature-dependent reactive chemicals. The temperature control ensures that product quality, viscosity, and process outcomes meet stringent industry standards while preventing premature curing, fouling, or degradation.
Jacketed static mixers are widely used in polymer blending, resins manufacturing, oil and gas processing, and pharmaceutical applications that demand continuous temperature regulation during mixing.
Teflon (PTFE) lined static mixers are engineered to resist corrosion, chemical attack, and fouling when handling aggressive industrial chemicals, high-purity acids, caustics, or hazardous process fluids. The PTFE lining safeguards both the mixer and the process stream from contamination, ensuring safe, reliable mixing and long equipment lifespan in harsh chemical processing environments.
The high chemical resistance of Teflon coating extends to all internal surfaces, including flanged ends, threaded ports, and static mixing elements—often produced with glass-filled PTFE for added strength. Teflon-lined mixers are an industry standard for mixing concentrated acids, alkaline solutions, oxidizers, and other potentially damaging substances within the pharmaceutical, water treatment, semiconductor, and specialty chemical sectors.
Heat exchanger static mixers are specifically optimized for enhancing heat transfer in laminar flow scenarios—an operational challenge for conventional heat exchangers. By redistributing fluid from the walls to the pipe center and vice versa, static mixer elements promote uniform temperature profiles and efficient energy exchange. This makes heat exchanger static mixers invaluable for processing viscous fluids, thermal-sensitive materials, or products with poor thermal conductivity.
The geometry of the mixing elements, particularly helical and bowtie twists, influences the extent of heat transfer and pressure drop. Monotube or multi-tube configurations can be tailored to process requirements, allowing for enhanced performance in food pasteurization, polymer production, and chemical processing where precise temperature control and mixing uniformity are critical for product quality and process efficiency.
Static mixers, also referred to as motionless mixers, are one of the least expensive but highly effective types of industrial mixing tools. The first static mixers were developed in Germany by Bayer AG, a chemical and pharmaceutical company, that used the mixers in their polymer plants. The process was further developed by a chemical company in Switzerland.
The simple structure of static mixers makes them highly efficient and capable of mixing several types of fluids. They are engineered and designed to mix a wide array of materials by adjustments to their material structure, element design, and size, which can vary according to the size of a pipeline. In most cases, the simple process of a static mixer has been a cost saving for industrial mixing operations and removes the need for more complex mixing methods.
When discussing the process of a static mixer, it is important to understand the different types of flow, which influences the type of static mixer and its elements. There are many characteristics to fluid flow with turbulent and laminar being the most common but not the only types. When clients are working with manufacturers in the selection and design of a static mixer, the type of fluid, such as its viscosity and velocity, are two of the initial factors. What is considered next is the type of flow, since flow movement determines the effectiveness of the mixing process of a static mixer.
Static mixers have no moving parts and rely on the placement of the various types of mixing elements to blend and mix liquids, fluids, and gasses that pass through the mixer. The placement of the mixing elements causes the material flow to move in certain ways to initiate the mixing process. For turbulent flow patterns, the mixing process is splitting and radial while the process for a laminar flow is splitting.
Although static mixers operate without the need of power, they do cause a pressure drop, which is compensated for by an upstream pump. In the majority of cases, static mixers provide efficient mixing with a very small pressure drop.
The laminar mixing process involves repeated division, transposition, and recombining of the liquid flow. The identical mixing elements of the static mixer are spread into several layers. An increase in the number of mixing elements makes each layer finer creating a more homogenous mix.
Turbulent mixing is very common in industrial applications. Mixing is achieved by rotating and shearing the layers in the flow, which happens with the reversal of the rotation of the liquid. Small shearing is necessary when the pitch between the rotations can be adjusted. As the pitch slows the rotation, extra mixing occurs in the static mixer. The mixing elements in a static mixer generates eddy currents in the flow. Inhomogeneity is removed by cross currents created by the mixing elements.
Static mixers are designed to mix fluids or gasses since the mixing elements would block powders or solids and become clogged with material build up. The mixing process of a static mixer causes turbulence in the liquids or gasses that enter it. The materials being mixed are divided, recombined, and divided again multiple times such that the stream exiting the mixer is homogeneous in regard to its concentration, temperature, velocity, and is equalized.
The many variations in static mixer design are due to the need to meet the requirements of a manufacturer’s application. In general, helical element static mixers are used by the chemical, pharmaceutical, and food industries while Kenics, tab, and wafer static mixers are used by the water industry.
There are variations as to how liquids, fluids, and gasses enter a static mixer. In some cases, blowers or pumps are used to move materials along to the mixing elements at the necessary volumetric flow rate and pressure. The sizes of static mixers vary in accordance with the application for which they are used.
Static mixers can be installed horizontally, vertically, on an angle, or any other type of configuration since they do not have any moving parts and do not require any form of power supply. As with other factors that govern the use of static mixers, their positioning is in regard to the type of fluids or gasses that will be mixed.
Modern industrial applications require the blending and mixing of fluids and gasses to ensure the quality of products. The two most used methods of mixing are dynamic and static, which can achieve the same mixing results using different methods. Although both methods are productive and advantageous, they have their drawbacks and disadvantages.
Static mixers are immobile mixers with baffles, blades, and other forms of elements that are arranged in a pipe or tube that cause turbulence in fluids or gasses for continuous mixing. They are simple inline devices that are capable of mixing and blending miscible and immiscible fluids.
Advantages of Static Mixers
The most notable difference between static mixers and dynamic mixers is the electrical power that is used to power dynamic mixers. Electrical power is required by a dynamic mixer in order for it to be able to create the turbulence of the mixing process. They have a rotating shaft with various forms of impellers that blend and mix materials as they spin at high speed. The mixing process for dynamic mixers is very aggressive due to the fast rotation of the impellers. In addition, dynamic mixers, unlike static mixers, require more space and have a larger footprint.
When examining static mixers and dynamic mixers, it is important to understand that static mixers rely on the design of the elements of the mixer in order to achieve optimal mixing without the use of any form of mechanical force. The lack of power and mechanical force is the aspect of static mixers that differentiates them from dynamic mixers, which rely on mechanical force and motion to complete the mixing process.
In addition, static mixers cost less, have a smaller footprint, have a simple design, and require very little maintenance. Dynamic mixers are large complex devices that are subject to mechanical failure. They have motors that rotate a shaft that is attached to impellers and are capable of completing demanding mixing applications. Unlike static mixers, dynamic mixers are capable of mixing powders, dry materials, and solids that would clog or block a static mixer.
The many advantages of static mixers make them an ideal tool for several industries. Their simple design, ease of installation, and reliability enables users to apply them to various forms of fluids, liquids, and gases. The fact that all forms of static mixers can be adapted to a variety of conditions has enhanced their use and made them an attractive, money saving investment.
Static mixers are used in the chemical, wastewater treatment, food and beverage, and pharmaceutical industries due to their ability to blend and mix miscible and immiscible fluids with varying viscosities. The flexibility and adaptability of static mixers are characteristics that make them ideal for modern manufacturing.
It can be easily assumed that static mixers would be a perfect fit for the chemical industry, which has to blend and mix chemicals, additives, and dyes as part of chemical production. Static mixers ensure consistent mixing during polymerization, emulsification, and reaction kinetics. The precision of static mixers improves product quality, decreases reaction times, and improves overall efficiency.
One of the primary uses of static mixers is in the wastewater treatment industry and was one of the initial uses of wafer static mixers. In the water and wastewater industry, static mixers are used for chemical dosing, pH adjustments, coagulation, and flocculation. They ensure proper blending and effective treatment processing as well as the removal of contaminants.
As with the chemical industry, the pharmaceutical industry involves a great deal of mixing and blending of chemicals, which necessitates precision and accurate processing. Pharmaceutical products require homogeneous mixing of ingredients (APIs), excipients, and other substances. Errors in the mixing process can lead to catastrophic results and danger to the general population. Consistent blending results in the proper texture, taste, quality, and appearance of a final product.
For the pharmaceutical industry, static mixers are made of stainless steel due to government regulations regarding hygiene and uncontaminated conditions. Since static mixers are sealed in a pipeline, they do not require the type of cleaning that is related to dynamic mixers due to being isolated from the environment.
The types of mixing that is related to the pharmaceutical industry also applies to the food and beverage industry as well as the regulations relating to hygiene and sterility. Since products produced by the food and beverage industry are used by the public, the quality and appearance of the products has to meet the highest standards. This factor has led to the wide use of static mixers that are capable of blending and mixing any form of fluid or liquid to create a flavorful and homogeneous product.
Static mixers are ideal for the petrochemical industry that deals with volatile and combustible chemicals. Since static mixers are contained in a pipeline away from equipment and workers, the blending and mixing process is isolated, safe, and contained. Fuels, additives, and lubricants are mixed safely, completely, and efficiently to ensure conformity with product parameters. The use of static mixers ensures the proper performance, stability, and quality of fluids and components.
Manufacturers are motivated to produce quality products at a reasonable price. In order to achieve these goals, it is necessary for producers to evaluate their processes to ensure they are producing their products with the utmost efficiency and quality. Static mixers have found a place in a wide range of industries for three reasons.
Agitators are equipment used in homogenizing media inside a tank. It works by rotating the impeller at its immersed end at a controlled speed or revolutions per minute (rpm). The work exerted by...
Drum mixers are mixers that are used for mixing free flowing materials by rotating them forward and reverse with welded chutes or flights that fluidize the mixture. The design of drum mixers gives them...
An emulsifier is an emulsion device used for colloidal dispersion of liquid droplets of immiscible liquids in the presence of an emulsifying agent. It enables the combining of non-soluble solutions or liquids...
High shear mixers, also known as high shear reactors (HSRs), rotor-stator mixers, and high shear homogenizers, are used to emulsify, homogenize, disperse, grind and/or dissolve immiscible mixtures with components of the same or different phases...
An industrial blender is a machine for large-scale production that consists of a large tank capable of mixing and blending batches of manufacturing materials to create a reaction between the materials. The many uses for industrial blenders are due to their capacity and...
A mill is a mechanical device that is often a structure, appliance, or machine that is used to break down solid materials into smaller pieces by cutting, grinding, or crushing them. Many industrial processes involve...
A tank mixer is a mixing device that blends several different ingredients in a single tank to make a single solution. It is a mixing process capable of mixing wettable powders, liquids, emulsifiable concentrates, and surfactants. They mix and blend...
A mixer is a complex and precise tool that is used in combining and mixing of substances and chemicals for manufacturing, production, and industrial use. There are many types of industrial mixers including...
A plastic tank is a large capacity liquid or granular storage unit that can be vertical, horizontal, below or above ground, as well as movable. They are designed to hold several gallons of a variety of substances for long periods without experiencing wear, weathering, or deterioration...
A plastic water tank is a large capacity container designed to store water for household, agricultural, irrigation, and industrial manufacturing use. There are various types of water tanks produced to meet the needs of specific applications, with...
A poly tank is a plastic storage tank used to store, transport, and collect water, other liquids, and granular or powder materials. They are made of polyethylene or polypropylene and are a cost effective, lightweight, and easy to handle...
Pressure tanks are vessels that are used to store, hold, and/or convey gasses, vapors and fluids at pressures greater than atmospheric pressure, also known as high pressures...
Pressure vessels are enclosed containers used to hold liquids, vapors, and gases at a pressure significantly higher or lower than the ambient pressure. They are widely used in various industries such as...
Stainless steel tanks are widely used in food, beverage, dairy, medicine, cosmetics, and other manufacturing processes where cleanliness and purity are important. These are also used in industrial plants for storing chemicals and gases where strong resistance from chemical degradation is required...