Agitators
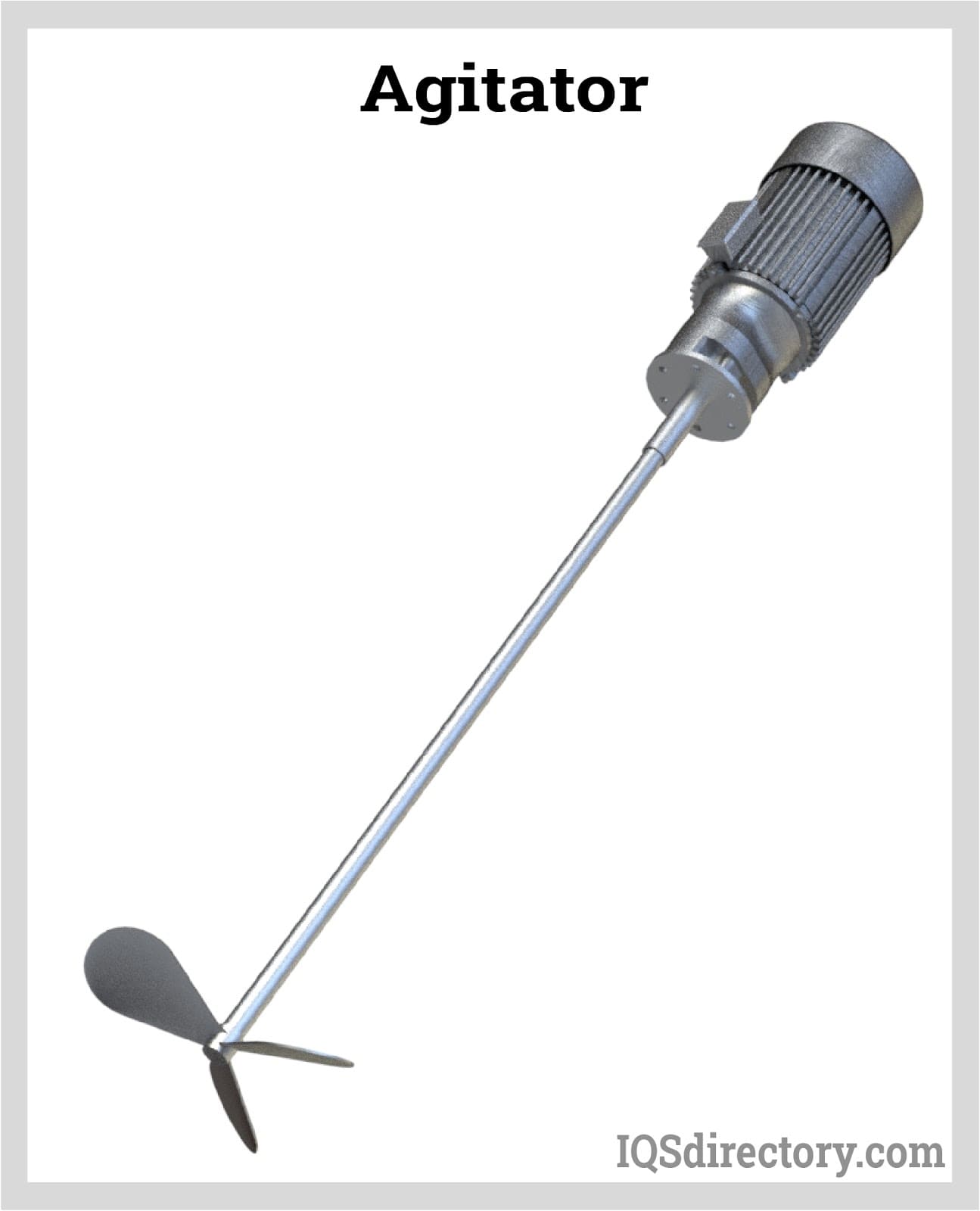
Agitators are equipment used in homogenizing media inside a tank. It works by rotating the impeller at its immersed end at a controlled speed or revolutions per minute (rpm). The work exerted by...
Please fill out the following form to submit a Request for Quote to any of the following companies listed on
The article provides in depth and complete information regarding tank mixers and their use.
You will learn:
A tank mixer is an essential tool designed to combine multiple ingredients into one cohesive solution within a storage vessel. This versatile device efficiently blends wettable powders, liquids, emulsifiable concentrates, and surfactants to create a homogeneous and uniform final product. Tank mixers serve a wide range of sectors, including pharmaceuticals, food and beverage industries, water treatment plants, and chemical manufacturing processes.
Known for their dependability and high performance, tank mixers provide cost-efficient solutions for integrating various components within a single blending operation. There are numerous types of tank mixers available, each specifically engineered to cater to unique application requirements.
Tank mixers, vital for efficient industrial mixing and blending processes, feature a set of core components designed to optimize mixing performance, energy efficiency, and operational reliability. The precise assembly and configuration of these components may vary depending on the type of tank mixer—such as static mixers, portable tank mixers, or large industrial agitators—as well as by manufacturer. Tank mixers are available in a broad spectrum of sizes, from compact, portable mixers perfect for small-scale applications, to robust, heavy-duty mixers and agitators mounted on large storage or process tanks. These units can be top-mounted, side-mounted, or plate-mounted to suit specific mixing requirements found in industries such as chemical processing, pharmaceuticals, food and beverage production, water treatment, and more.
The motor is the primary power source that drives the impeller, generating the necessary mixing motion and agitation within the tank. The motor size, horsepower, and power rating are selected based on factors such as the volume and viscosity of the liquid being mixed, desired mixing intensity, and process requirements. High-efficiency electric motors are commonly used to promote consistent agitation, enhance process control, and reduce energy consumption, making them ideal for high-shear mixing or blending viscous fluids. Selection of an appropriately rated industrial mixer motor helps ensure optimal mixing performance and prolonged equipment lifespan.
The impeller is the key rotating element of the tank mixer, responsible for creating mixing action, inducing flow patterns, and promoting proper blending of tank contents. There are several types of impellers, each engineered for specific mixing tasks. Popular options include axial-flow impellers like propellers for bulk flow and circulation, radial-flow turbines for high-shear mixing, and specialized high-shear impellers for rapid emulsification and homogenization. The impeller design and material selection—such as stainless steel for corrosion resistance—directly impact the mixer’s effectiveness in handling different liquid viscosities, solid suspensions, and gas dispersions in chemical processing, water treatment, and biopharmaceutical applications.
The shaft physically connects the impeller to the motor, transmitting torque and rotational motion from the motor to the impeller within the tank. Shafts for industrial tank mixers must be built from corrosion-resistant, high-strength materials such as stainless steel, Hastelloy, or coated alloys to withstand the rigors of aggressive chemicals, abrasive slurries, and continuous operation. Proper shaft alignment and durable bearing assemblies are essential for minimizing wear, reducing vibration, and preventing mechanical failure—critical to the longevity and reliability of top-entry mixers, side-entry mixers, and agitators alike.
The seal forms a crucial barrier, preventing process liquid from leaking out of the tank through the narrow space where the mixing shaft passes through the tank wall. Tank mixer seals must be engineered to handle the specific temperature, pressure, and chemical resistance requirements of the application. Options include mechanical seals, lip seals, or gland packing, each suited to different mixer configurations and process conditions. In industries concerned with contamination—such as pharmaceuticals or food manufacturing—sanitary mixer seals with CIP (Clean-In-Place) compatibility are often required. A robust sealing solution promotes safety, environmental compliance, and long-term equipment effectiveness.
In addition to these primary components, many advanced tank mixer systems incorporate supplementary features to optimize processing and maintenance. These may include:
When selecting a tank mixer for your specific industrial application—be it for blending chemicals, suspending solids, dispersing gases, or homogenizing multi-phase liquids—it is critical to consider the compatibility and quality of each component. Top-performing tank mixer systems balance robust construction, advanced engineering, and process-specific customization to ensure maximum mixing efficiency, compliance with safety standards, and reduced operational downtime.
Tank mixers are essential industrial mixing equipment custom-designed to address the specific requirements of diverse sectors such as chemical processing, food and beverage, water treatment, pharmaceuticals, and cosmetics. Every mixing application has unique operational challenges—including product viscosity, tank size, batch volume, and chemical compatibility—that engineers must consider when selecting and adapting mixer components. This attention to process optimization and fluid dynamics results in a wide variety of industrial tank mixer types, each optimized for a particular set of mixing applications. The optimal tank mixer design is typically determined by factors such as impeller type, rotator speed, batch size, material characteristics, agitation intensity, and the nature of solids suspension or liquid blending required.
Top-entry mixers are designed for blending high-viscosity fluids and are installed on the tank's upper section, making them ideal for large-scale mixing, homogenization, and dissolving solids in liquids. Top-entry agitators utilize a range of impeller options, such as propellers, turbines, and paddles, to enhance tank fluid movement and minimize dead zones. Many models include a variable speed drive for precise control over the agitation process, which is critical for applications involving shear-sensitive ingredients or the gradual addition of powders. Industries such as chemical manufacturing, bioprocessing, fermentation, and oil and gas rely heavily on robust top-entry mixing technology.
Side-mounted mixers are positioned horizontally on the tank’s sidewall and are particularly effective at blending low- to medium-viscosity fluids such as water, juice, or crude oil. These agitators are often used for maintaining product uniformity, suspending settled solids, or preventing stratification in large storage tanks. Options for various impeller types (such as hydrofoils and marine-style propellers) support efficient mixing with reduced power consumption. Clean-in-place (CIP) features help facilitate sanitary operation and easy maintenance, which is important in the food, beverage, and dairy industries.
Bottom-mounted mixers are installed at the base of process tanks or mixing vessels, providing direct contact with settled solids or dense mixtures. This configuration is highly effective for blending high-viscosity fluids, rapidly dispersing powders, or managing high-solids slurries. Many bottom entry mixers incorporate a heating jacket or internal coil, allowing for direct heat transfer and tight temperature control throughout the batch mixing process—key for industries such as cosmetics, coatings, polymer manufacturing, and pharmaceuticals, where melting or cooling is critical for product quality.
Magnetic mixers are engineered with a sealed drive that uses magnetic coupling to transmit power from the motor to the impeller, eliminating the risk of fluid contamination and reducing maintenance associated with traditional shaft seals. Magnetic drive agitation is essential when working with highly corrosive or hazardous chemicals and in sterile processing environments such as biopharmaceutical manufacturing, where GMP compliance and cleanability are paramount. These mixers offer excellent containment and support sterile, hygienic, and leak-free operation.
Portable mixers offer flexibility for small-scale operations or applications where tanks are not dedicated to specific products. These lightweight, moveable units can be clamped or mounted onto multiple batches, supporting short production runs or temporary blending needs. Available with diverse impeller styles (including folding, axial, or pitched-blade), and a range of motor power ratings, portable mixers are frequently used for pilot-scale batch mixes, laboratory blending, paint mixing, and other short-term processes.
Static mixers are non-mechanical mixing devices that use fixed internal baffles, elements, or inserts to blend fluids as they pass through the mixer body. These energy-efficient inline mixers are ideal for low-viscosity applications, continuous blending, or precise dosing tasks where high purity and minimal maintenance are crucial. Static mixers are widely utilized in the chemical processing, water and wastewater treatment, and food processing industries for applications such as pH adjustment, polymer dilution, and the blending of liquid additives.
Jet mixers employ a high-velocity stream of liquid or gas to induce turbulence inside tanks, ensuring thorough agitation and rapid mixing without mechanical impellers. These mixers excel in applications requiring significant gas dispersion, liquid blending, homogenization, or where gentle agitation minimizes shear. Jet mixing is especially popular in chemical manufacturing, pharmaceutical formulation, fermentation, and water treatment, where flexibility and ease of cleaning are valued. The absence of internal moving parts also reduces maintenance and wear.
In-line mixers, or pipeline mixers, are installed directly into a processing line, employing rotor-stator assemblies, high-velocity shearing, or static elements to blend product streams on a continuous basis. They are indispensable in processes where seamless, uninterrupted mixing is needed, such as emulsification, dispersion of solids in liquids, or the blending of immiscible fluids for food production, chemical synthesis, and pharmaceutical processing. In-line mixers maximize batch consistency and reduce processing time, promoting product uniformity and production scalability.
High shear mixers are precision-engineered mixing devices that use a combination of rapid rotation, intense turbulence, and fine energy dispersion to achieve highly uniform mixtures. These mixers are critical for breaking up aggregates, dissolving powders, and creating stable emulsions or suspensions in liquids. High shear mixers play a vital role in the chemical, pharmaceutical, cosmetic, food and beverage, and adhesive industries, supporting applications that demand fine particle size reduction, solubilization, and uniform ingredient distribution.
Each of these industrial mixer types is engineered for specific tank mixing processes—ranging from gentle agitation of thin liquids to aggressive blending of highly viscous materials or slurries. When selecting the right tank mixer for your operation, consider fluid viscosity, tank geometry, mixing goals (such as solids suspension, emulsification, or homogenization), energy efficiency, and sanitary requirements. Consulting with a tank mixer manufacturer or process engineer ensures you achieve the ideal level of agitation, mixing speed, and equipment longevity necessary for your application. Proper mixer selection and sizing not only ensures efficient mixing and product quality, but also enhances overall process safety, scalability, and cost-effectiveness across industries.
Selecting the right type of tank mixer is crucial for achieving optimal performance and efficiency. Several factors need to be considered, including the viscosity and specific gravity of the liquid, the tank's volume, and the required mixing speed and intensity. Understanding the specific mixing problem at hand is essential for making the appropriate choice.
Viscosity measures a liquid's resistance to flow, ranging from thin and watery to thick and sticky. Higher viscosity liquids are more challenging to mix effectively. When selecting a tank mixer, it's important to choose one capable of generating sufficient shear force to mix the liquid efficiently based on its viscosity.
Specific gravity is the ratio of a liquid’s density to that of water. Liquids with higher specific gravity typically require more energy to mix than those with lower specific gravity. Therefore, selecting a tank mixer that can deliver adequate mixing energy for the specific gravity of the liquid is crucial.
The tank’s volume influences the choice of mixer. Larger tanks may necessitate more powerful mixers, whereas smaller tanks might be adequately mixed with less powerful equipment. It’s important to choose a mixer that provides sufficient mixing energy for the tank’s volume.
The required mixing speed and intensity affect the mixer selection. Some applications need high-speed, high-intensity mixing, while others require more gentle agitation. Selecting a tank mixer that meets the specific speed and intensity requirements of the application is key to effective mixing.
Each of these factors plays a crucial role in selecting the appropriate tank mixer. For instance, high-viscosity liquids may need mixers with greater shear force capabilities, while low-viscosity liquids can often be mixed effectively with less powerful equipment. Larger tanks typically require more powerful mixers to ensure adequate mixing energy, whereas smaller tanks might be sufficiently mixed with less robust mixers. Additionally, the specific gravity of the liquid affects mixer selection, as higher specific gravity liquids often need more energy to mix thoroughly. Lastly, the desired mixing speed and intensity influence the choice of mixer, as different mixers are designed to deliver varying levels of mixing energy.
Choosing the right materials for tank mixers is crucial as it impacts the equipment's performance, durability, and safety. Key factors to consider include the chemical compatibility of the material with the liquids being mixed, as well as the temperature and pressure conditions the mixer will endure. Common materials for constructing mixing tanks include plastics, glass, rubber, steel, and copper.
It's essential that the material used for the mixer is compatible with the chemicals being processed. Certain chemicals can react with specific materials, causing issues like corrosion, contamination, or equipment degradation. Reviewing a chemical compatibility chart for any materials used in the mixer is an important step in the selection process.
The material chosen for the mixer must be able to withstand the pressure and temperature conditions of the application. Some materials may become brittle or fail under extreme pressure or temperature, while others may not provide adequate insulation for applications requiring heat or cold.
Based on these considerations, commonly used materials for tank mixers include stainless steel, carbon steel, and various plastics such as polyethylene and polypropylene. Each material offers different benefits and limitations, which are explained below.
Stainless steel is a popular choice for tank mixers because it is corrosion-resistant, durable, and easy to clean. It is commonly used in food and beverage, pharmaceutical, and chemical processing applications.
Carbon steel is a cost-effective choice compared to stainless steel, but it offers less resistance to corrosion. It is typically used in applications where corrosion is not a major concern.
Plastics such as polypropylene and polyethylene are lightweight, resistant to corrosion, and economically viable. They are commonly utilized in chemical processing and water treatment applications.
For added protection against corrosion and wear in high-stress environments, coatings like epoxy and ceramic can be applied. When selecting materials for tank mixers, it's essential to consider the specific requirements of the application. Consulting with a supplier or manufacturer can provide valuable guidance on choosing the most appropriate materials to ensure reliable and safe operation.
Scheduled maintenance is crucial for ensuring the optimal performance and longevity of a tank mixer, just like with any industrial equipment. Regular upkeep helps identify potential issues early and prevents more significant damage or failure. Manufacturers recommend following a maintenance schedule to monitor performance variations. Among the various maintenance tasks, lubrication is particularly important due to the constant use of tank mixers.
Regular inspections are essential to identify signs of wear and tear, damage, or corrosion. These inspections should also verify proper alignment, adequate lubrication, and the tightness of bolts and fasteners.
Lubrication of bearings, gears, and other moving parts should be performed regularly to ensure proper operation and reduce the risk of premature failure.
Regularly cleaning the mixer is crucial to eliminate any material buildup that could disrupt the mixer's operation or lead to contamination.
Sensors and control systems in the mixer should be calibrated regularly to ensure they provide accurate readings and to avoid potential errors.
Worn or damaged parts should be replaced promptly to prevent further damage or malfunction of the mixer.
If repairs become necessary, follow these recommended steps:
The initial step in repairing a mixer is to identify the problem, which may involve troubleshooting to determine the cause. Once the issue is identified, disassemble the mixer to access the damaged or faulty parts. Repair or replace these parts based on the extent of the damage. After the repairs or replacements are completed, reassemble the mixer and test it to ensure it operates correctly.
Post-repair, the mixer should be tested and calibrated to confirm it operates properly and within the correct parameters.
Using high-quality replacement parts and having repairs performed by a qualified technician is essential. Neglecting repairs can result in reduced performance, increased risk of damage or injury, and even equipment failure.
Custom designs and the adaptability of tank mixers make them a valuable asset for various industrial processes. Their most valuable feature is their durability, which is crucial for production and assembly operations. Consistently performing equipment helps avoid downtime and production delays.
Tank mixers enhance product quality by ensuring thorough mixing and blending of ingredients. This leads to a more consistent product with fewer defects and inconsistencies. Additionally, tank mixers prevent sedimentation and ensure even distribution of ingredients throughout the mixture.
Tank mixers boost efficiency by reducing mixing times and minimizing manual labor. Automated tank mixers can be programmed to mix batches regularly, streamlining production processes and reducing downtime.
Tank mixers are versatile and suitable for a wide range of applications across different industries. They can mix liquids and solids, as well as dissolve, disperse, and emulsify ingredients.
Tank mixers offer a cost-effective solution for mixing and blending processes. They reduce the need for manual labor and minimize material waste. Additionally, they can be designed to be energy-efficient, which helps lower operational costs.
Tank mixers enhance safety by reducing the need for manual mixing, thus lowering the risk of workplace injuries. They can also be designed to be explosion-proof, helping to prevent accidents in hazardous environments.
Tank mixers can be easily scaled up or down to accommodate different production needs. This makes them a flexible solution for companies that need to adjust their production processes according to changing demand.
Tank mixers are designed for easy maintenance, which helps minimize downtime and reduce maintenance costs. Many models are easy to clean, preventing contamination and ensuring consistent product quality.
Tank mixers provide consistent results across various batches, which is crucial for companies needing to adhere to strict quality standards.
Tank mixers help reduce waste by ensuring thorough mixing and blending of ingredients, which minimizes material waste. They can also be designed to be energy-efficient, further reducing waste associated with energy consumption.
Tank mixers can be tailored to meet specific application needs. They can handle different volumes and viscosities of liquids and accommodate various types of impellers and mixers.
Tank mixers are integral to any production process involving the mixing or blending of products or materials. In the pharmaceutical industry, they are crucial for combining ingredients into a smooth and uniform mixture. Similarly, in food production, tank mixers play a key role in achieving the desired flavor and taste by effectively blending and mixing ingredients.
Tank mixers are extensively utilized in the food and beverage industry for mixing ingredients, homogenizing, blending, and emulsifying food products. They are commonly employed in the production of dairy products, baked goods, beverages, sauces, and other food items.
In chemical processing, tank mixers are employed for blending various chemical compounds, including adhesives, paints, coatings, resins, and polymers. They are also effective for dissolving solids into liquids and mixing liquids with different viscosities.
In the pharmaceutical industry, tank mixers facilitate the blending of active pharmaceutical ingredients (APIs) with excipients, as well as the production of suspensions, emulsions, and creams. They are also used for preparing sterile solutions and injectables.
In water treatment, tank mixers are used to combine chemicals and coagulants with water to aid in removing impurities such as bacteria, viruses, and other contaminants. They are also crucial for mixing chemicals used in pH adjustment, flocculation, and disinfection.
In cosmetics manufacturing, tank mixers are essential for blending ingredients like oils, emulsifiers, thickeners, and fragrances. They are commonly utilized in the production of creams, lotions, and gels.
In biotechnology, tank mixers are employed to mix and blend biological materials such as cell cultures, fermentation media, and protein solutions. They are commonly used in the production of vaccines, antibodies, and other biopharmaceuticals.
In the petrochemical industry, tank mixers facilitate the blending of various petroleum products, including fuels, lubricants, and additives. They are also used in producing specialty chemicals like surfactants and solvents.
In mining, tank mixers are used for blending chemicals involved in the extraction of minerals from ores. They are also essential for producing slurry solutions, which are used to transport minerals through pipelines.
Tank mixers are utilized in the pulp and paper industry to blend chemicals for pulping, bleaching, and de-inking paper products. They are also used for mixing adhesives, coatings, and other chemicals involved in paper manufacturing.
In waste management, tank mixers are crucial for blending chemicals used in treating waste streams, including municipal wastewater and industrial effluent. They are also used in producing biofuels and other renewable energy sources.
Both international and national governments and organizations have established regulations, guidelines, and standards for the use of tank mixers. As with any industrial equipment, tank mixers require oversight to protect processes, the environment, and workers. These regulations are continually updated to align with technological advancements.
OSHA sets and enforces workplace safety standards, including those for tank mixers. Specific regulations include requirements for lockout/tagout procedures, guarding, and personal protective equipment.
The EPA enforces regulations related to the handling and disposal of hazardous waste, including waste produced by tank mixers.
The FDA regulates the safety of food, drugs, and medical devices, including tank mixers used in their production. The FDA has specific guidelines for the design and construction of mixers in these sectors.
At the state and local levels, there may be additional laws, regulations, and regulatory agencies governing the use of tank mixers. These can vary by state or locality and may include:
Many states have their own occupational safety and health agencies that enforce standards similar to OSHA's, including those for tank mixers.
State departments of environmental protection enforce regulations related to hazardous waste handling and disposal, including waste generated by tank mixers.
In states with significant agricultural activity, the Department of Agriculture may have specific regulations for the use of tank mixers in agricultural production.
Additionally, local fire departments may have regulations regarding the storage and use of hazardous materials involved in tank mixing operations. Companies must be aware of all applicable federal, state, and local regulations to ensure compliance and avoid workplace injuries or environmental hazards.
As with all heavy-duty equipment, tank mixers require careful monitoring and control for safety reasons. Regardless of their function, tank mixers are production tools that can be dangerous if not properly handled and respected. It is crucial to be aware of conditions that could be harmful or hazardous when operating them.
Air pockets can lead to inconsistencies in the final product in various ways. For example, in liquid mixing, air pockets may cause foaming, affecting product quality and consistency. When mixing with gases or air, air pockets can hinder proper blending and cause variations in the end product. Designing tank mixers with features to minimize air pockets, such as specialized impellers or advanced agitation techniques, is essential.
The presence of air pockets can result in excessive noise and vibration as the mixer tries to eliminate them. These conditions can be hazardous to workers, potentially causing injuries or hearing loss. To mitigate these risks, tank mixers should be designed to reduce air pocket formation, and workers should be equipped with personal protective equipment like ear protection to prevent hearing damage.
The viscosity of the product being mixed influences the design and effectiveness of the tank mixer. High-viscosity products may require more powerful mixers or impellers to ensure thorough mixing.
Some products are sensitive to shear, which can cause damage or degradation. Choosing a tank mixer that matches the product's characteristics is crucial to avoid damage and maintain product quality.
The time required to achieve thorough blending can vary based on the product and mixer design. Monitoring mixing times is important to ensure that products are blended effectively and efficiently.
The size and design of the tank affect mixer performance. The tank must be designed to accommodate the mixer properly to ensure thorough and efficient mixing.
Regular cleaning and maintenance of the mixer and tank are vital to ensure product quality and prevent contamination. The design of the mixer and tank should facilitate easy cleaning and maintenance.
Power requirements impact operational costs. It is important to select a mixer that is energy-efficient and suitable for the product being mixed to manage these costs effectively.
Tank mixers can pose safety risks if not used correctly. Adhering to safety protocols and using appropriate personal protective equipment is essential when operating tank mixers.
Material compatibility is critical to avoid adverse reactions between the product and the tank or mixer materials. Selecting a mixer and tank that are compatible with the chemicals involved is necessary to maintain product quality and prevent reactions.
In industries such as food and beverage, pharmaceuticals, and others where hygiene is crucial, the tank mixer should be designed to prevent contamination and facilitate easy cleaning to ensure that products remain safe for consumption.
Tank mixers can apply high shear to products depending on the impeller and mixing speed, potentially affecting the final product's quality. Careful selection of the impeller type and speed is required to minimize unwanted shear.
Choosing the right materials for constructing the tank mixer is essential for its durability. The materials should be resistant to corrosion, wear, and tear from the mixed products. Inappropriate material selection can lead to premature mixer failure.
Proper installation and maintenance are crucial for optimal mixer performance. Improper installation can result in misalignment and premature failure, while inadequate maintenance can lead to equipment breakdown and contamination.
Despite their extensive current applications, the future of tank mixers is even more promising. The role of tank mixers is expected to grow with advancements in technology and innovation. Here are some potential developments that could enhance the role of tank mixers in the future:
Smart technology is becoming more prevalent in industrial equipment, including tank mixers. Future mixers may feature sensors that monitor variables such as temperature, pressure, and flow rate, along with software that adjusts mixing parameters in real-time based on this data.
With increasing demand for sustainable and energy-efficient equipment, advancements in tank mixer design may focus on enhancing efficiency and reducing energy consumption. Innovations might include more efficient motors and new mixing techniques that consume less energy.
To maximize equipment utility, future tank mixers may become more versatile, capable of handling a broader range of viscosities and adaptable to various tank sizes and geometries.
As industrial equipment becomes more interconnected, tank mixers may be designed to integrate seamlessly with other machinery such as pumps, filters, and sensors. This integration could enhance processing efficiency and enable better data collection and analysis.
Advances in materials science and manufacturing techniques could lead to the development of new materials that are more suitable for tank mixers. This might include materials with enhanced resistance to corrosion, wear, and extreme temperatures and pressures.
Overall, the future of tank mixers will likely be shaped by technological advancements, evolving customer needs, and environmental considerations. As the industry progresses, we can anticipate new and innovative solutions for mixing a diverse range of fluids across various applications.
Agitators are equipment used in homogenizing media inside a tank. It works by rotating the impeller at its immersed end at a controlled speed or revolutions per minute (rpm). The work exerted by...
Drum mixers are mixers that are used for mixing free flowing materials by rotating them forward and reverse with welded chutes or flights that fluidize the mixture. The design of drum mixers gives them...
An emulsifier is an emulsion device used for colloidal dispersion of liquid droplets of immiscible liquids in the presence of an emulsifying agent. It enables the combining of non-soluble solutions or liquids...
High shear mixers, also known as high shear reactors (HSRs), rotor-stator mixers, and high shear homogenizers, are used to emulsify, homogenize, disperse, grind and/or dissolve immiscible mixtures with components of the same or different phases...
A homogenizer is a type of mixing equipment used to create a uniform and consistent mixture. It works by breaking the components and evenly distributing them throughout the solution. The components are either immiscible, have varying sizes, or are in different phases from each other...
An industrial blender is a machine for large-scale production that consists of a large tank capable of mixing and blending batches of manufacturing materials to create a reaction between the materials. The many uses for industrial blenders are due to their capacity and...
A mill is a mechanical device that is often a structure, appliance, or machine that is used to break down solid materials into smaller pieces by cutting, grinding, or crushing them. Many industrial processes involve...
A mixer is a complex and precise tool that is used in combining and mixing of substances and chemicals for manufacturing, production, and industrial use. There are many types of industrial mixers including...
A plastic tank is a large capacity liquid or granular storage unit that can be vertical, horizontal, below or above ground, as well as movable. They are designed to hold several gallons of a variety of substances for long periods without experiencing wear, weathering, or deterioration...
A plastic water tank is a large capacity container designed to store water for household, agricultural, irrigation, and industrial manufacturing use. There are various types of water tanks produced to meet the needs of specific applications, with...
A poly tank is a plastic storage tank used to store, transport, and collect water, other liquids, and granular or powder materials. They are made of polyethylene or polypropylene and are a cost effective, lightweight, and easy to handle...
Pressure tanks are vessels that are used to store, hold, and/or convey gasses, vapors and fluids at pressures greater than atmospheric pressure, also known as high pressures...
Pressure vessels are enclosed containers used to hold liquids, vapors, and gases at a pressure significantly higher or lower than the ambient pressure. They are widely used in various industries such as...
Stainless steel tanks are widely used in food, beverage, dairy, medicine, cosmetics, and other manufacturing processes where cleanliness and purity are important. These are also used in industrial plants for storing chemicals and gases where strong resistance from chemical degradation is required...