Depalletizers
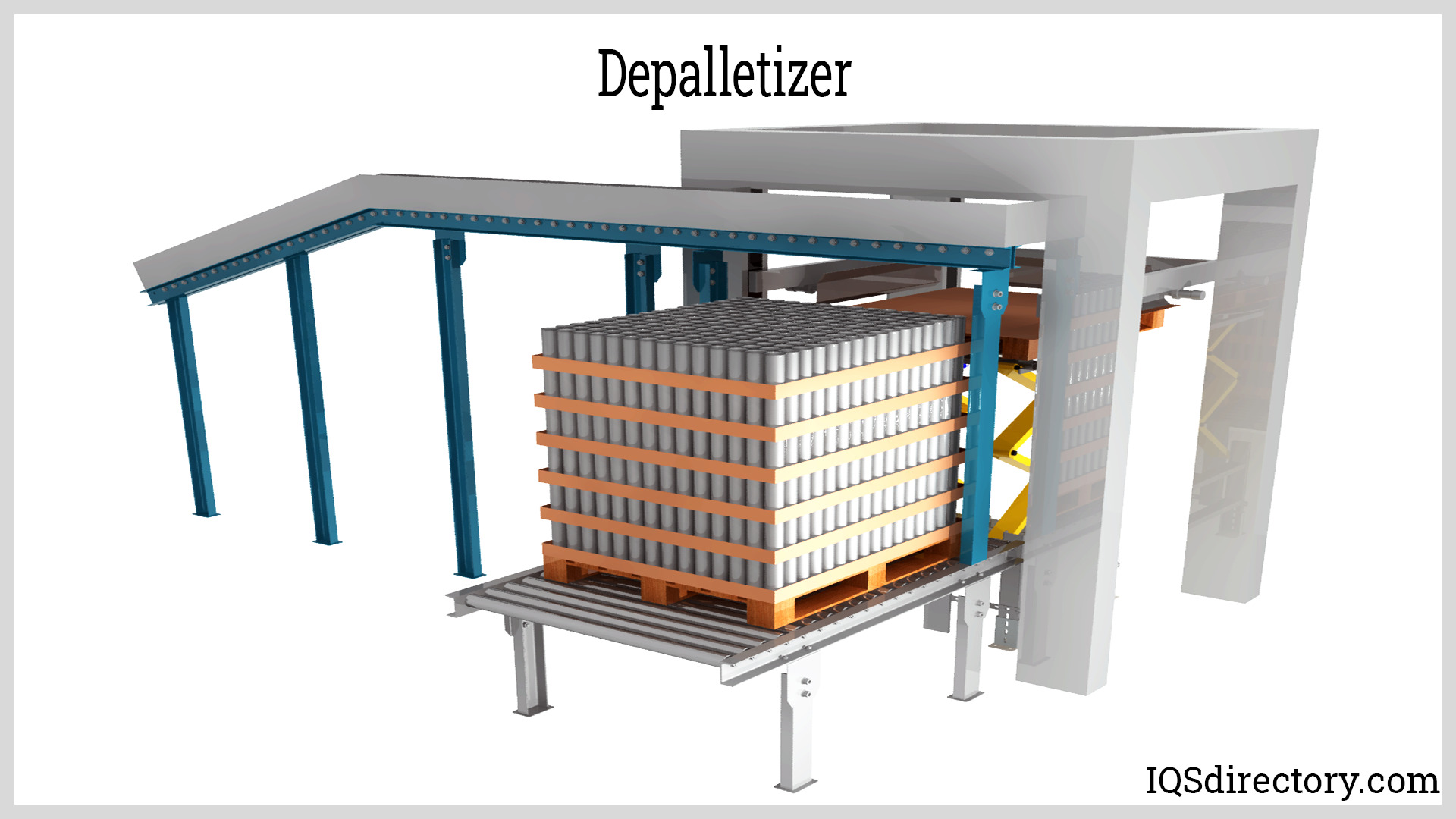
Palletizing is the process of putting items on a pallet. The process of emptying the loaded objects in the reverse pattern is known as depalletizing. A pallet is a flat, square-shaped platform used to transport and...
Please fill out the following form to submit a Request for Quote to any of the following companies listed on
This article provides comprehensive knowledge about palletizers. Read further and learn about:
A palletizer is a mechanical system used to stack and organize various products into one cohesive load, thus improving efficiency in handling, storage, and transportation. Often, it is part of a larger packaging operation, which might include functions like weighing, counting, sorting, labeling, metal detection, and wrapping. These additional processes can sometimes be included within the palletizer or handled with different equipment.
Palletized products form a unit load by bundling materials for streamlined handling. It is generally quicker and more economical to move a single large unit rather than numerous smaller items. Typically, finished goods aren't made for individual shipping but are placed in boxes, cases, trays, or crates, then consolidated into a single load supported by pallets or roll cages. The packaging forms represent secondary unit loads, with roll cages identified as tertiary unit loads.
The palletizer arranges products onto a pallet, hence the term. Pallets are level, sturdy platforms crafted from wood, plastic, paper, or metal featuring notches or openings. These features accommodate forklifts and hand pallet trucks for lifting and relocating the load. These openings designate a pallet as either two-way or four-way, indicating forklift entry directions. Most pallets can support loads up to one metric ton over an area close to one square meter. Below are examples of standard pallet dimensions.
Dimensions (W x L) in millimeters |
Dimensions (W x L) in inches |
Unused Floor Space (ISO Container) |
Region |
1016 x 1219 | 40.0 x 48.00 | 3.7% | North America |
1000 x 1200 | 39.37 x 47.24 | 6.7% | Europe, Asia |
1165 x 1165 | 45.9 x 45.9 | 8.1% | Australia |
1067 x 1067 | 42.00 x 42.00 | 11.5% | North America, Europe, Asia |
1100 x 1100 | 43.30 x 43.30 | 14% | Asia |
800 x 1200 | 31.50 x 47.24 | 15.2% | Europe |
Some palletizers are equipped to stack products using slip sheets or conveyor surfaces and are called unitizers. These unitized loads eliminate the need for a pallet. In some instances, "palletizers" and "unitizers" are interchangeably used terms.
There are three main types of pallets made from wood or plastic, and one type made from cardboard.
The most prevalent is the GMA pallet, typically measuring 40x48 inches, with notches on the sides facilitating side lifting access.
The CHEP pallet ranks as the second most used. This design, also usually sized 40x48 inches, incorporates blocks on every side, making handling possible from any direction. These pallets are easily recognized by their distinctive blue color.
PECO pallets are emerging in the industry, providing similar services as CHEP. They are known for their red paint identifiers.
The Pull Board is characterized by a corrugated sheet with dual 3-inch tabs generally located on adjacent sides. Forklifts equipped with special attachments can use these tabs to push or pull loads on or off the prongs. Pull Boards are favored for their hygiene benefits and space efficiency, allowing up to an additional 5 inches of space per load, potentially saving significant costs by accommodating additional layers in a transport vehicle.
Certain palletizers are engineered to stack items on slip sheets or conveying surfaces, termed unitizers. With unitized loads, there's no requirement for a pallet, and in some applications, the terms "palletizers" and "unitizers" are used interchangeably.
Diverse companies may demand various pallet arrangements tailored to their specific requirements.
This stacking arrangement strengthens load integrity with a foundational column that bolsters the whole pile. In warehouses, pallets can be stacked up to four units high, leveraging load strength from the vertically aligned box corners. The top interlocked section adds further stability, ensuring unwrapped loads can be safely maneuvered with a forklift to a wrapping station.
Before the advent of automatic palletizing, manual hand stacking was used to organize products into pallet loads for storage and distribution. This method was labor-intensive and slow, requiring considerable effort for relatively low output. Pallets and pallet handling became crucial logistics tools in the early 20th century, particularly during World War II. As the demand for transporting heavier loads more quickly increased, there was a growing need for improved material handling and storage solutions.
The first mechanical palletizer was developed by Lamson Corp. in 1948. This early palletizer was a row-forming type, which arranged materials into rows. These rows were then transferred to another section where layers were stacked. This process was repeated until a complete stack of materials was formed, ready to be placed on a pallet.
In 1970, the need for faster logistics led to the introduction of the in-line palletizer. Unlike the row-forming palletizer's intermittent motion, the in-line palletizer operates with continuous motion, guiding and orienting products onto a layer forming platform until the layer is complete. The finished layer is then placed onto a pallet.
The 1980s saw the emergence of robotic palletizers. These systems use a robotic arm equipped with an end effector or product gripper to pick up products from a conveyor or layer table and place them onto a pallet. The end-of-arm tools can be mechanical, suction-based, or magnetic grippers, depending on the requirements of the handling process.
Palletizers are mainly divided into two categories: conventional and robotic palletizers. Both can receive products at high and low elevations. High elevations typically range between 84" to 124", while low elevations are 30" to 36". Conventional palletizers are then divided into floor- (low-) level and high-level palletizers.
These palletizers typically have an infeed level of 30" to 36". As products travel through the infeed conveyor, they are oriented by a turning device or conveyor before being moved to the row-forming area. Products are arranged into rows until a row is complete. This row is then transferred to the layer-forming area. Once a full layer is formed, it is pushed forward to the stripper plate, where the products are adjusted in height and placed onto the pallet or the previous layer. The stack remains stationary during the load-building process, which continues until the pallet is fully loaded. The finished pallet is then transferred to the discharge conveyor, usually set at an 18" discharge level.
Floor-level palletizers are generally less expensive and simpler to construct compared to high-level palletizers, and they require less floor space. With most components positioned at floor level, maintenance is quicker and more straightforward due to easy access to the parts. Additionally, operators can easily monitor the machine’s operation since most moving parts are at eye level. When integrating with other equipment in the packaging line, floor-level palletizers are ideal because they do not require elevation changes for the infeed conveyor, making them well-suited for pairing with packers and sealers.
High-level palletizers typically have an infeed level ranging from 84" to 124" or more. Like floor-level palletizers, products are transported by the infeed conveyor to a turning device or conveyor that rotates them into the correct orientation before moving them to the row-forming area. Products are arranged into rows until a row is complete, then transferred to the layer-forming area. Once a layer is formed, it is moved into position on the pallet or stack. The main distinction from floor-level palletizers is the ability of high-level palletizers to raise and lower the stack with each layer added. After the stack is completed, it is lowered onto the discharge conveyor, which is usually set between 18" to 30". In many installations, a raised operator platform is built alongside the machine for easier operation and monitoring.
High-level palletizers are ideal when there is sufficient space for an inclined conveyor, allowing the packer and sealer to be positioned at a distance from the palletizer. Compared to floor-level palletizers, high-level machines offer higher throughput relative to their size, making floor space utilization more efficient. They are capable of handling throughputs of approximately 40 to 50 items per minute, regardless of the discharge elevation of the packer or sealer.
A conventional palletizer consists of various components, including both static and moving parts. Some of these components may be integrated directly into the palletizer, while others can be installed as separate pieces of equipment.
Bags exiting the packaging units and sewing machines are typically in an upright position. They are then positioned or flattened by the knockdown conveyor to prepare them for palletizing.
This can be either an integrated or separate machine used to ensure the accuracy of the weights of bagged products prior to storage and distribution.
Similar to the checkweigher, this device can be integrated with the palletizer or operate as a separate machine. The metal detector identifies any ferrous, non-ferrous, or stainless-steel contaminants in the product.
Products that are detected as either being off-weight or containing metal contaminants are diverted by the reject conveyor to a staging area or platform.
Products can enter a palletizer from different sides, including the side, rear, or front. These infeed types apply to both floor-level and high-level palletizers.
To ensure the pattern is formed correctly, the bag flattener adjusts and shapes the bags to the proper height.
As products are fed onto the palletizing machine via the conveyor, they are oriented into the correct position before entering the row-forming area. Various turning devices are used for this purpose, including turn shoes, cushioned turns, turntables, and soft turn devices. Turn shoes and cushioned turns gently nudge the product to rotate it by 90°. Turntables lift and rotate products by +90°, -90°, or 180°. Soft turn devices utilize two sets of rollers driven by variable frequency drives (VFDs) to achieve rotations of +90°, -90°, or 180° by varying roller speeds.
These mechanical devices are used to create the desired pattern in the row-forming area by establishing side-to-side gaps. Stops are activated by pneumatic valves and cylinders, which are controlled by programmable logic controllers (PLCs). To alter forming patterns, only software controls need to be adjusted, eliminating the need for hardware changes.
These mechanical devices, similar to stops, assist in pattern formation by creating front and back gaps. Once a layer is complete, it is transferred onto a stripper plate or apron, which then moves it onto the pallet. When the stripper plate is in place on top of the pallet or stack, a gate descends to block the layer's movement. The stripper plate is then retracted, leaving the layer in position on the stack. A pusher gate holds the layer in place until it is released.
This component enables the creation of front and back gaps without the need for a pusher gate. As the stripper apron opens in the middle, it forms gaps while the layer is placed onto the stack below.
As the name suggests, this component dispenses and conveys pallets to ensure the continuous operation of the palletizer. When one unit load is completed, the pallet dispenser feeds a new pallet. Typically, a pallet dispenser holds 10 to 20 pallets in its pallet magazine.
For some materials, such as bagged products, slip sheets are needed between layers. A slip sheet dispenser uses a venturi vacuum system to efficiently place these slip sheets.
This component transfers completed unit loads onto a platform, where they can be picked up by forklifts or hand pallet trucks for storage.
This is the control area where operators troubleshoot, adjust, or reprogram the palletizer and its automated components. The main element of the control panel is the PLC, which controls circuit functions according to the machine’s programming.
These palletizers utilize robotic arms to maneuver the end effector and perform pattern formation. Robotic palletizers are categorized into Cartesian, gantry, SCARA, and articulated types. Each type varies in flexibility and range of movement.
This type of palletizer has an end of arm tool that can move in three directions of space, or the Cartesian axes X, Y, and Z, hence the name Cartesian. Its mechanical structure consists of beams and a telescopic mast usually actuated by servo motors. This type of robotic palletizer is slow and is used for products with consistent weight and sizes. This is generally the cheapest type of robotic palletizer suiting single line speeds of up to 10 items per minute.
A gantry palletizer features an end effector assembly mounted on a beam that moves along one axis. The beam itself moves along a perpendicular axis, allowing for movement in the X-Y plane. To move vertically along the Z-axis, the end effector assembly uses a telescopic or articulated arm that can extend or retract. Gantry palletizers are often categorized as Cartesian palletizers due to their linear movement along Cartesian axes. While they perform pick-and-place operations, they are generally slower than Cartesian robots and tend to be larger and more expensive. However, they offer the advantage of lifting heavier loads.
A SCARA robot features an arm that is flexible in the X-Y plane (left, right, forward, and backward) but rigid along the Z-axis (up and down). This "Selective Compliant" characteristic is what defines its name. The "Articulated Robot Arm" of a SCARA resembles a human arm, consisting of two linked segments connected by a joint, allowing for extension and folding. SCARA robots are faster than Cartesian palletizers and can handle multiple palletizing lines, operating at speeds of around 20 items per minute.
This type of palletizer offers two additional degrees of freedom compared to SCARA palletizers. Articulated palletizers feature arms connected by a simple joint at one end, similar to SCARA models, but they lack a mast. Instead, one arm is mounted on a swivel joint with a fixed base, allowing for greater flexibility in movement. Articulated palletizers are faster than SCARAs and can handle multiple production lines, typically processing around 25 items per minute.
Robotic palletizers vary in their approach to pattern formation and use distinct components based on their design. While elements such as check weighers and metal detectors are utilized, they are typically installed as separate pieces of equipment. Below are the common components of a robotic palletizer.
This component supports the end effector and allows linear movement along a single axis. Motion is provided by servo motors through mechanisms such as rollers and rails, rack and pinion gearing systems, or chain and sprocket drives. Beams are commonly found in Cartesian and gantry palletizers.
Mounted on a fixed base, this part supports the beam or arm and end effector assembly. It uses hydraulics, servo motors, or chain drives to enable vertical movement, allowing the connected components to move up and down.
Typically consisting of two linked segments, arms enable the end effector to move horizontally by rotating, extending, or folding.
These components provide rotational movement between various parts of the palletizer system. The number of joints can vary depending on the required versatility of the system.
Often referred to as end-of-arm tools, end effectors are crucial in robotic palletizer assemblies due to their versatility compared to conventional palletizers. They are responsible for picking up and placing products in the correct location and orientation on the stack. Designed to handle a variety of products with a single tool, they can also be equipped to retrieve pallets from a pallet rack or to pick slip sheets, tier sheets, or top caps from a dispensing rack. These features enhance the robot's functionality and efficiency.
Following are the most common types of end effectors.
Clamps lift products by gripping the sides, enabling the handling of multiple items with the same orientation simultaneously, which speeds up throughput. They are particularly useful for stable products or those not suited for vacuum handling, such as HSC (cases with no top) or display cases.
Fork tools are used for delicate, unstable, or special cases like HSC (cases with no top) or warm/hot shrink-wrapped products where gentle handling is necessary. The tool features cutouts that allow it to slide underneath the product for lifting and cradling. A clamp can be added to the fork tool for added stability during movement.
Finger end effectors are mechanical tools that open and close in two directions, providing support underneath the product. They are commonly used for handling bags.
Vacuum end effectors are commonly used for picking up RSC cases and can be configured to handle multiple cases simultaneously. They use a blower to generate a high volume of vacuum necessary to lift thin, porous corrugated boxes made from recycled materials. This approach is often preferred over venturi systems, which rely on plant air that may be unreliable or insufficient for the required air volume.
Bag end-of-arm tools are designed to pick up large bags of product one at a time. They can be equipped to add slip sheets or tier sheets between layers, depending on the speed requirements.
Magnetic end effectors use electromagnets to handle products and are typically employed for stacking and palletizing canned goods.
While conventional palletizers represent the earlier generation of palletizing technology, they are not fully superseded by newer robotic models. Each type of palletizer offers distinct benefits tailored to specific applications. Given the wide variety of industries that utilize palletizers, no single design fits all needs. Below are the advantages of using conventional palletizers compared to robotic ones.
Merits of Using Conventional Palletizers:
Conventional palletizers build the unit load by turning and pushing products into their designated positions and orientations, eliminating the need to pick up and place each item. This method allows for flexibility in handling different packaging dimensions or types without affecting the palletizer's operation. Any necessary adjustments can be made through control program changes, without requiring hardware modifications.
Robotic palletizers can be slow when operating by picking and placing individual products. To improve throughput, they often collect and handle multiple products simultaneously. However, this approach typically offers less flexibility compared to conventional palletizers, which can be easily adjusted to change pattern configurations without impacting throughput.
Benefits of Robotic Palletizers:
For straightforward palletizing tasks where speed is less critical, a robotic arm can be a cost-effective choice. It eliminates the need for additional systems such as conveyors, turning mechanisms, stoppers, and gates. As long as the robotic arm meets the required throughput, it presents a more economical solution.
A single robotic palletizer can be positioned between several packaging lines and handle multiple product types simultaneously. In contrast, conventional palletizers require separate upstream product accumulation systems to manage multiple lines. By eliminating the need for these additional systems, robotic palletizers reduce overall investment costs.
Robotic palletizers offer greater flexibility in changing pattern formations compared to conventional systems. However, it’s important to note that modifying the pattern may impact the palletizer's throughput.
Hybrid palletizers combine the speed and reliability of conventional palletizers with the flexibility of robotic systems. They use traditional row-forming methods, such as turning devices and stoppers, but employ a robotic arm to pick up and place entire layers onto the pallet or stack. This design overcomes the limitation of high-level palletizers, which require products to be moved up by a conveyor, while retaining the advantage of higher throughput.
Another type of hybrid palletizer features robotic pattern forming. In this setup, a robotic arm handles the orientation and positioning of products in the layer-forming area. Once the layer is complete, a conventional palletizer takes over to place it on the stack and manage additional tasks, such as feeding pallets and slip sheets.
Palletizing is the process of putting items on a pallet. The process of emptying the loaded objects in the reverse pattern is known as depalletizing. A pallet is a flat, square-shaped platform used to transport and...
A robotic palletizer is a type of palletizer that employs a robotic arm to pick, orient, and place individual products and arrange them into a single stack of load. They are the next generation of palletizers, and they will supersede conventional palletizers...
An AGV forklift is a driverless self-operating robotic device that has the ability to carry, lift, retrieve, and place loads for easy transfer from one location to another. An automatic guided vehicle (AGV) forklift is a computer controlled mechanism that...
Automated guided vehicles (AGV) or mobile robots are types of guided robotic systems that are not bounded by a fixed range of motion. Rather, it is self-contained and can move along a line, surface, or space...
An autonomous mobile robot (AMR) is a self-propelled self-powered mechanism designed to perform repetitive tasks or organizational functions using an internal guidance system. They are able to navigate their...
Processing equipment for holding and moving bulk bags is known as bulk bag equipment. This bulk bag equipment is typically used at the front end of the production process to hand off product to...
Packaging equipment is utilized throughout all packaging processes, concerning primary packs to distribution packages. This involves many packaging operations: cleaning, fabrication, filling, sealing, labeling...
A pallet stacker is a machine designed to assist the user in lifting, moving and handling palletized materials with ease. A pallet itself is a flat and horizontal structure used to support goods in a sturdy fashion...
Pneumatic conveying is a method for transferring bulk materials, like powders and granules, using compressed gas or air, from one processing center to another. Material is moved through an enclosed conveying line or tube using a combination of pressure differential and airflow from a blower or fan...
Screw conveyors, or auger conveyors, are industrial equipment used in transporting bulk quantities of granular solids (e.g., powder, grains, granules), semi-solids, liquids, and even non-flowing materials from one point to another...
Vacuum conveyors are suctioning machines that utilize air pressure in order to move materials through an enclosed pipeline. Vacuum conveyors have broad applications throughout the industrial and...
In 1954, when Arthur "Mac" Barrett, of Barrett Electronics Corporation, unveiled the first AGV, he named it Guide-o-Matic and described it as a driverless vehicle...