Depalletizers
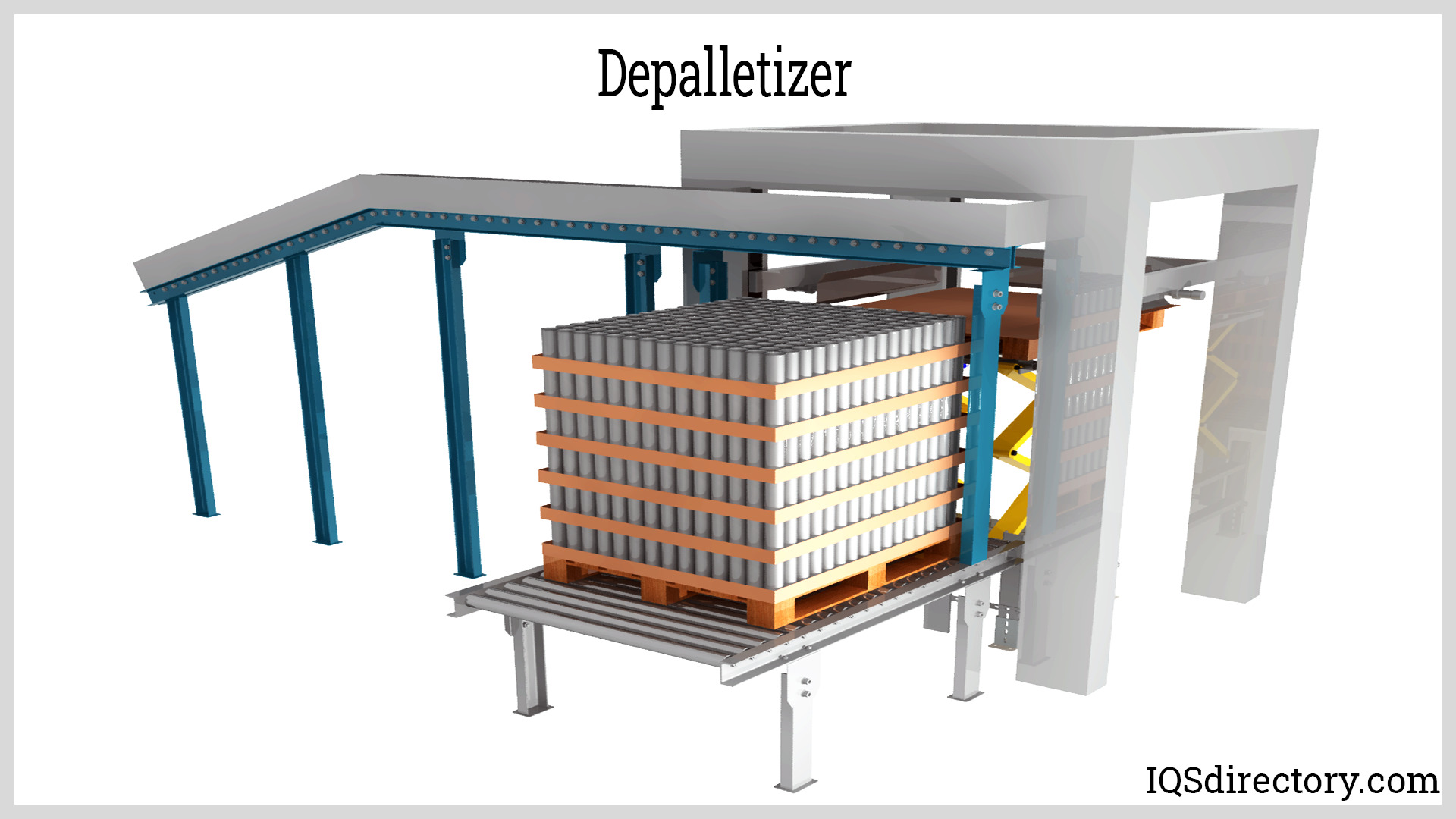
Palletizing is the process of putting items on a pallet. The process of emptying the loaded objects in the reverse pattern is known as depalletizing. A pallet is a flat, square-shaped platform used to transport and...
Please fill out the following form to submit a Request for Quote to any of the following companies listed on Robotic Palletizers .
This article gives all-inclusive details on robotic palletizers.
Read further to learn more about:
A robotic palletizer is a type of palletizing machine that employs a robotic arm to meticulously pick, orient, and place items into a cohesive stack or load. These next-generation palletizers offer benefits such as reduced initial costs, enhanced versatility, and the capacity to execute varied tasks. However, challenges in speed, accommodation of product dimensions, and durability mean they haven't fully supplanted traditional palletizers in every context.
Similar to other palletizer systems, robotic palletizers utilize the unit load strategy. A unit load involves assembling materials for more efficient handling, benefiting from moving one large entity instead of multiple smaller pieces. Finished products are designed to be part of a larger, consolidated shipment, often packed in boxes, cases, trays, or crates which are further combined into a single unit supported by pallets or roll cages. The initial are known as secondary unit loads, while the latter are termed tertiary unit loads.
Before the advent of automatic palletizing systems, manual hand stacking was the standard method to organize products into pallet loads for warehouse storage and distribution. This process was highly labor-intensive and relatively slow, resulting in limited throughput and increased operational costs. As industries grew and supply chain demands surged, especially in sectors like food and beverage, pharmaceuticals, and consumer goods, the limitations of manual palletizing became more apparent.
Pallets and advanced pallet handling technologies became crucial logistics solutions in the early 20th century. The widespread adoption of pallets was accelerated during World War II, when the efficient transport of heavier loads highlighted the urgent need for improved material handling equipment and streamlined warehouse operations. This period marked a transformative era in industrial automation as organizations sought ways to increase storage efficiency and reduce product handling time.
The development of the first mechanical palletizer by Lamson Corp. in 1948 was a pivotal milestone in the packaging and material handling industry. This early row-forming palletizer arranged products in a dedicated row-forming area and then automatically transferred each layer onto a pallet. By repeating this process until a full pallet load was formed, the system helped companies significantly reduce labor requirements and improve consistency. The conventional palletizer laid the foundation for further advances in automated stacking and palletizing solutions.
The 1980s witnessed the introduction of robotic palletizers, which dramatically improved efficiency and flexibility for various types of production lines. These advanced systems utilize a robotic arm with a specialized end-of-arm tooling (EOAT), such as mechanical, suction, or magnetic grippers, designed to handle diverse products with precision and speed. The robotic palletizing process automates picking products directly from a conveyor, layer table, or accumulation system, and arranges them onto the pallet according to pre-programmed patterns. Modern robotic palletizers are now equipped with vision systems and sensors to further enhance accuracy and accommodate varying product shapes and sizes, making them essential in high-speed packaging lines and smart factories embracing Industry 4.0 technologies.
As enterprises seek greater throughput, lower operational costs, and improved workplace safety, automated palletizing solutions continue to evolve. Manufacturers and distributors evaluating palletizer systems should consider factors such as throughput needs, product variability, facility space, and integration capabilities with existing conveyor or packaging operations. Modern palletizing offers scalable solutions from semi-automatic to fully automated and robotic systems, addressing diverse requirements from small businesses to large-scale distribution centers. Leveraging advanced pallet handling equipment enhances supply chain efficiency, reduces manual labor, and supports seamless logistics in today’s fast-paced market.
Automated and robotic palletizers deliver a wide array of benefits for modern packaging operations and production lines. By integrating advanced robotic automation, manufacturers can dramatically enhance overall manufacturing efficiency and operational productivity. Robotic palletizing systems eliminate much of the variability introduced by manual labor, reducing labor-intensive tasks and preventing slowdowns that can impact plant throughput. While the initial investment in industrial automation may seem significant, the return on investment (ROI) for palletizer technology is consistently positive thanks to the substantial operational improvements and cost savings. Below we outline the core benefits of robotic and automatic palletizers:
Robotic and automated palletizers eliminate the need for human labor in the unitizing and stacking of products, significantly boosting packaging line speeds. With rapid and repeatable motion, these machines efficiently handle heavier and bulkier loads than manual operators can, all while operating at a consistently high speed. Unlike human workers, palletizing robots do not experience fatigue or the risk of workplace injuries, enabling 24/7 operation with minimal downtime. Proper maintenance of these automated systems ensures uninterrupted productivity, which helps avoid bottlenecks and maximizes throughput. As a result, facilities can respond faster to fluctuating customer demands and scale production capacity efficiently.
As precision-driven, programmable machines, robotic palletizers are designed with advanced end-of-arm tooling and vision systems to gently and accurately handle a variety of packaging materials—ranging from cases and cartons to bags and shrink-wrapped bundles. Automation eliminates human error, reduces variability, and ensures more uniform stacking. Consistent product handling minimizes the risk of product damage, defects, or misaligned pallets, which is essential for industries like food and beverage, pharmaceuticals, and consumer goods where packaging integrity is paramount.
The integration of palletizer robots into production and warehouse environments significantly improves workplace safety. Manual palletizing exposes workers to hazards such as repetitive motion injuries, slips, trips, falls, and the potential for musculoskeletal disorders, particularly lower back injuries from frequent lifting, reaching, and stacking. Automated palletizing systems are engineered to eliminate or reduce these occupational risks, supporting compliance with Occupational Safety and Health Administration (OSHA) standards and fostering a safer work environment. As a result, companies often experience decreased injury-related costs and improved employee morale.
Deploying robotic and automatic palletizing systems reduces labor costs by minimizing the number of operators needed on the packaging line. Additionally, the increased efficiency and accuracy of automated palletizing reduces product waste, shrinkage, and rework associated with manual errors. For high-volume operations, the long-term savings in labor and minimized downtime create a compelling ROI. Automation also enables better use of warehouse space and lowers utility expenses by optimizing product stacking and load stability.
Beyond these core advantages, the specific features of robotic palletizers offer unique value in automated material handling and logistics operations. As businesses weigh the choice between robotic palletizing systems and conventional (mechanical) palletizers, it’s essential to match each option to the facility’s individual needs—including product types, required throughput, flexibility, and footprint. The comparative table below helps clarify the strengths and capabilities of each palletizing solution for various industrial applications.
Robotic Palletizer | Conventional Palletizer |
---|---|
Low investment cost for simple applications: For straightforward palletizing solutions, a robotic arm can be utilized where high speeds are not critical. By deploying a robotic arm, facilities can eliminate the complexity and expense of multiple conveyor systems, turning stations, stoppers, and gating equipment. As a result, robotic palletizers represent a cost-effective automation solution where their cycle times meet application requirements. | Better tolerance with varying packaging types: Conventional palletizers assemble unit loads by turning and pushing products to exact locations and orientations—no pick-and-place required. This allows them to handle a broad range of case sizes and packaging formats with minimal adjustment required. If product specifications change, modifications can be made through software programming, with no hardware upgrades needed. |
Ability to serve multiple lines: A single robotic palletizer can be positioned between several packaging lines, accepting various product SKUs carried by separate production streams. This minimizes floor space and capital investment while streamlining complex operations. In contrast, mechanical palletizers often need separate accumulation areas or supplemental conveyors to accommodate multiple lines, adding expense and complexity. | Higher throughput: Conventional palletizers excel at high-speed operations due to the simplicity and directness of their actuators. With the ability to move several products simultaneously, they achieve significantly higher throughput rates, making them ideal for large-scale, continuous production environments. Robotic palletizers can increase speed by using multi-pick end effectors, but generally operate at slightly reduced speeds when individually picking and placing products. |
Versatile pattern forming: Robotic palletizers are exceptionally flexible for changing palletizing patterns. New stacking formations, layer configurations, or product orientations can be introduced simply by updating programming and re-configuring end-of-arm tools—no major hardware changes required. However, highly complex or irregular patterns may reduce overall cycle times and throughput. | More robust and reliable: Conventional palletizers are engineered for longevity and can safely palletize heavier loads with robust conveyor-based systems. The mechanical structure distributes weight evenly, reducing wear and tear. By contrast, the articulating joints of robotic palletizers bear concentrated loads, which can contribute to accelerated maintenance needs depending on application. |
Ability to perform secondary tasks: Equipped with vacuum grippers, magnetic heads, or custom end effectors, robotic palletizers can perform additional functions such as placing slip sheets, interleaving cardboard, depalletizing, or even integrating pallet wrapping stations. This multi-functionality increases the overall automation potential within a packaging cell, providing transformative value for materials handling and logistics. | Easy maintenance and servicing: With distinct, easily accessible actuators and modular components, conventional palletizers are straightforward to troubleshoot. Maintenance personnel can quickly isolate and address mechanical failures, minimizing production disruptions. Their purely mechanical architecture often means less technical specialization is required for repairs and spares management. |
More compact: Robotic palletizers are space-efficient, needing only a footprint large enough for the robotic arm and the staging area for palletized loads. This compact design is ideal where manufacturing or warehouse space is at a premium. Mechanical palletizers, with their multiple rollers, pushers, and stacking zones, typically require greater floor space and ceiling height to accommodate various subsystems. | Easy part replacement and sparing: Conventional palletizer components—including actuators and conveyors—are widely standardized and readily available in the industrial equipment market, making replacement and procurement simple. With robotic palletizers, replacement parts are often proprietary, requiring sourcing from specific manufacturers or approved resellers, which can marginally affect uptime depending on local availability. |
When evaluating palletizer solutions, key considerations include production throughput requirements, product dimensions, packaging types, available floor space, anticipated SKUs, and integration with other material handling equipment, such as automated guided vehicles (AGVs) and conveyor systems. By analyzing these factors, operations managers can determine whether a robotic palletizer, a conventional palletizer, or a hybrid solution best meets their needs. Selecting the right palletizing automation delivers measurable benefits for warehouse management, supply chain efficiency, and order fulfillment accuracy, positioning your facility for sustained growth and operational excellence.
For businesses aiming to optimize palletizing processes and future-proof their production lines, partnering with experienced integrators or OEMs specializing in custom robotic palletizing solutions can ensure a tailored system that integrates seamlessly with existing packaging machinery, warehouse management systems, and overall logistics strategies.
Robotic palletizers can be classified based on their configuration and construction. Different configurations are characterized by the palletizer's mode of operation. Robotic palletizers can operate individually or in conjunction with other units and may also perform tasks beyond palletizing. Below are some types of robotic palletizers categorized by their configuration.
This configuration is the most straightforward and widely used, featuring a single robotic palletizer. This single unit handles the palletizing task and may also incorporate additional functions, such as slip sheet and pallet dispensing, as well as stretch wrapping.
Single in-line palletizers can handle one or multiple palletizing lines, which may contain either the same or different product SKUs, depending on the design. They are typically equipped with articulated arms and custom end-of-arm tools.
Although this type of palletizer offers significant versatility, it tends to have a lower throughput.
This palletizer type adds another layer of versatility—depalletizing. Depalletizing is the inverse process—the individual items are disassembled and separated from the unitized or palletized load. This feature is useful in applications that require the unloading of products from mixed pallets. The depalletizing robot also sorts the goods according to the product SKU.
Generally, a robotic palletizer is designed to handle either palletizing or depalletizing, but not both functions simultaneously. A machine labeled as a palletizer-depalletizer indicates it can be programmed for both tasks. Palletizers are typically used in end-of-line processes for packaging and storage, whereas depalletizers are used for unloading and distributing raw materials like empty bottles, boxes, and cases. The advantages provided by palletizers are similarly realized with depalletizers.
This robotic palletizer configuration uses multiple robots. In a layer-forming system, each robot is assigned a specific task. For example, a basic layer-forming setup includes two robots: one for assembling layers and another for stacking them. This division of labor enhances the overall throughput of the palletizing system.
The specifics of robotic palletizers, including the number and types of robots, programmed tasks, and additional features, vary between manufacturers. Some systems combine conventional and robotic palletizers into what are known as hybrid palletizers. In these setups, a conventional palletizer is used for layer forming, as it effectively handles incoming products from conveyor belts. Once the layers are formed, a robotic palletizer takes over to stack them. Robotic palletizers are particularly efficient in stacking due to their optimized pick-and-place movements.
Mixed palletizing describes the capability of robotic palletizers to handle various products and consolidate them into a single pallet. Mixed configuration robotic palletizers are typically high-end models equipped with advanced programming, custom end-of-arm tools, and sensors. They are highly versatile, able to make precise adjustments to their arm and tooling movements without requiring reprogramming. This adaptability allows them to accommodate different product profiles and determine their positions on the stack. Mixed configuration palletizers are particularly valuable in environments with high SKU diversity, including packaging, storage, and distribution lines.
Robotic palletizers can also be classified based on their construction, with each type distinguished by its range of allowable movements. These types vary in complexity, with more advanced models offering greater freedom of movement. Below are the four primary types of robotic palletizers categorized by their construction.
This type of palletizer, known as a Cartesian palletizer, features an end-of-arm tool that moves along three Cartesian axes—x, y, and z. Its structure includes beams and a telescopic mast driven by servo motors, geared rollers, rack and pinion, chain and sprocket, or lead screw mechanisms. Cartesian palletizers are relatively slow and best suited for products with consistent weights and sizes. Their end-of-arm tools are typically basic, making them ideal for straightforward pick-and-place tasks. As one of the more cost-effective options, Cartesian palletizers are suitable for single line speeds of up to 10 items per minute.
A gantry palletizer features an end-of-arm tool or end effector mounted on a beam that moves along one axis. This beam, in turn, moves on a second axis, enabling movement within the horizontal plane. For vertical motion, the end effector assembly often includes a telescopic or articulated arm that can extend or retract. Gantry palletizers are a subset of Cartesian palletizers, as they provide linear movement along the three Cartesian axes. While they are typically slower than Cartesian robots and tend to be larger and more expensive, they offer the advantage of handling heavier loads.
A SCARA-type palletizer features an arm that is flexible in the horizontal plane but rigid in the vertical direction, which is its "Selective Compliant" characteristic. Its articulated robot arm, resembling a human arm, consists of two links connected by a joint at their ends. This joint typically has a single degree of freedom, allowing the arm to extend or fold. SCARA palletizers are generally faster than Cartesian models and can handle multiple palletizing lines, achieving speeds of approximately 20 items per minute.
Articulated palletizers offer two additional degrees of freedom compared to SCARA palletizers, making them the most advanced type with a design closest to a human arm. Their end-of-arm tool is mounted on a wrist with one or two degrees of freedom. Unlike SCARA palletizers, articulated palletizers do not have a mast; instead, one arm is mounted on a swivel joint with a fixed base, allowing for greater flexibility in movement. Articulated palletizers are faster than SCARA models and can manage multiple production lines, handling approximately 25 items per minute.
End-of-arm-tools, columns, arms, and joints are some of the terms used in the previous chapters to describe the different types of robotic palletizers. Robotic palletizer components are more similar to robots used in automated assembly and manufacturing systems than those found in conventional palletizers. From a mechanical point of view, a robotic palletizer is an assembly of links and joints. These links and joints are specifically denoted by their role in the robotic system and their position in the assembly.
The columns and masts are the vertical components mounted on either a fixed base (in Cartesian, gantry, and SCARA types) or a rotating base (in articulated types). These columns support the weight of the load and the palletizer assembly. They serve as the attachment points for the beam, arm, and end effector assemblies. Movement up and down is facilitated by hydraulics, servo motors, lead screws, or chain drives, which raise or lower the connected parts.
Beams are horizontal load-bearing components that support the end effector assembly or end-of-arm tool. They feature guided rails that enable the translational movement of a trolley carrying the tool. A single beam allows movement along a single axis, while a two-beam assembly enables movement within the horizontal plane. Beams are commonly found in simpler robotic palletizers like Cartesian and gantry types. However, an exception is the gantry palletizer that utilizes a robotic arm as its end effector.
Arms are two-link mechanisms that allow the end-of-arm tool to move within two- or three-dimensional space through rotation, extension, or folding. The links are connected by joints that provide one or two degrees of freedom. The range of motion of the palletizer is determined by the length of the arms and the movement capabilities of the joints. Arms are specific to SCARA and articulated palletizer types.
Joints facilitate rotational or translational movement between the links of an arm. The number of joints in a palletizer system varies based on the level of versatility required. An arm with full, unrestricted motion generally includes six joints, each offering a single degree of freedom.
The wrist is the joint in a robotic arm that supports the end-of-arm tool. It typically allows for rotational movement to position the tool. Some designs also permit additional rotational adjustments, providing a two-degree of freedom movement for more versatile tool positioning.
Often called end effectors (EOAT), these are the most crucial components of a robotic palletizer, contributing significantly to the machine's versatility. EOATs are responsible for picking up and placing products in their correct location and orientation within the stack. They can be designed to handle not only finished products but also various other materials, including packaging materials, wrappers, slip sheets, and pallets.
The end-of-arm tool (EOAT) distinguishes robotic palletizers from conventional types. As discussed in the previous chapter, it is the key element that provides robotic palletizers with their versatility. Below are some of the most commonly used EOATs in the palletizing industry.
These EOATs lift products by clamping and gripping their sides. In this design, one part of the clamp remains stationary while the other moves. The gripping action is achieved by bringing the movable part closer to the stationary part, securely holding the product. Clamps can simultaneously handle and place multiple products with the same orientation, enabling faster throughput.
These end effectors are ideal for products that need support from underneath. By providing additional support, they can handle heavier loads without damaging the sides of the products. Their operation is similar to that of clamp types, involving a pushing action to load the products onto the fork. Like clamps, forks can also collect and place multiple products simultaneously.
Finger end effectors are mechanical tools that operate by opening and closing in two directions. They not only grip products at their sides but also provide support from underneath, offering a more advanced solution compared to clamps and forks. Fingers are particularly useful for handling delicate items or products packed in fragile materials such as paper or sheet plastic.
Vacuum end effectors utilize pneumatic systems with a venturi device to create vacuum pressure. These types use multiple suction cups to hold products from their top surface, which minimizes damage to packaging materials compared to mechanical types. They are also more reliable due to having fewer moving parts. However, vacuum end effectors have weight limitations and tend to palletize at lower speeds, as they can lose grip when accelerating the product quickly.
This type of EOAT uses magnetic devices for lifting magnetic products or products with magnetic casing or packaging. Permanent magnets can be used since they do not continuously consume power; however, they need a mechanical device for removing the collected object. Electromagnets are preferred due to their simple operation, as the object can be lifted or dropped simply by supplying or cutting power to the electromagnet. Their suitability as a palletizer EOAT is limited since only a few products are completely magnetic. The number of applications is further reduced since magnetism can damage products or cause them to be magnetic.
Custom EOATs are uniquely fabricated tools for handling odd-shaped products. They can be equipped with a combination of mechanical, pneumatic, or magnetic actuators. This further increases the flexibility of the palletizer. Custom EOATs also allow the robotic palletizer to execute secondary tasks such as dispensing and wrapping.
Palletizing is the process of putting items on a pallet. The process of emptying the loaded objects in the reverse pattern is known as depalletizing. A pallet is a flat, square-shaped platform used to transport and...
A palletizer is an automated material handling machine used to stack and orient several individual products into a single load for a more convenient and economical method of handling, storage, and shipment. Palletizers are usually part of a bigger packaging process...
An AGV forklift is a driverless self-operating robotic device that has the ability to carry, lift, retrieve, and place loads for easy transfer from one location to another. An automatic guided vehicle (AGV) forklift is a computer controlled mechanism that...
Automated guided vehicles (AGV) or mobile robots are types of guided robotic systems that are not bounded by a fixed range of motion. Rather, it is self-contained and can move along a line, surface, or space...
An autonomous mobile robot (AMR) is a self-propelled self-powered mechanism designed to perform repetitive tasks or organizational functions using an internal guidance system. They are able to navigate their...
Processing equipment for holding and moving bulk bags is known as bulk bag equipment. This bulk bag equipment is typically used at the front end of the production process to hand off product to...
Packaging equipment is utilized throughout all packaging processes, concerning primary packs to distribution packages. This involves many packaging operations: cleaning, fabrication, filling, sealing, labeling...
A pallet stacker is a machine designed to assist the user in lifting, moving and handling palletized materials with ease. A pallet itself is a flat and horizontal structure used to support goods in a sturdy fashion...
Pneumatic conveying is a method for transferring bulk materials, like powders and granules, using compressed gas or air, from one processing center to another. Material is moved through an enclosed conveying line or tube using a combination of pressure differential and airflow from a blower or fan...
Screw conveyors, or auger conveyors, are industrial equipment used in transporting bulk quantities of granular solids (e.g., powder, grains, granules), semi-solids, liquids, and even non-flowing materials from one point to another...
Vacuum conveyors are suctioning machines that utilize air pressure in order to move materials through an enclosed pipeline. Vacuum conveyors have broad applications throughout the industrial and...
In 1954, when Arthur "Mac" Barrett, of Barrett Electronics Corporation, unveiled the first AGV, he named it Guide-o-Matic and described it as a driverless vehicle...