Aqueous Part Washers
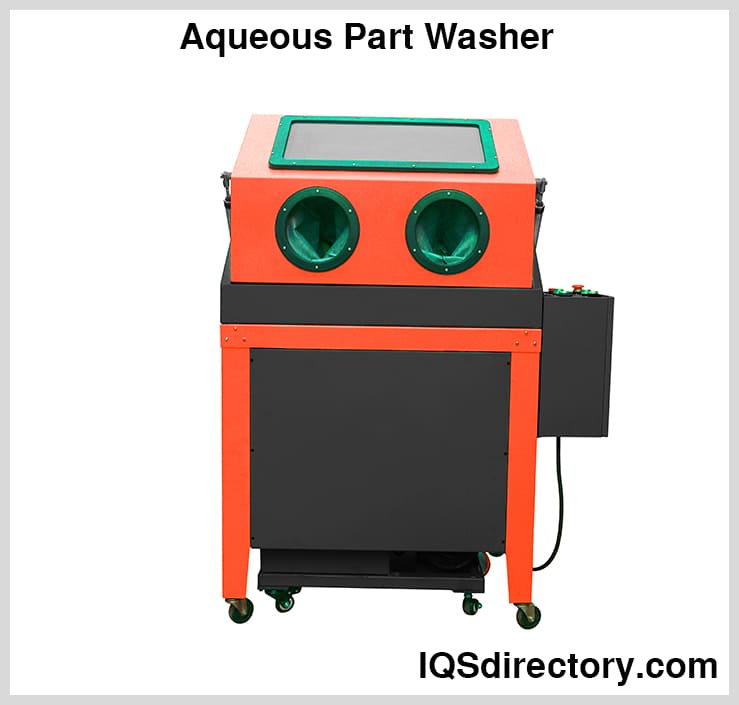
An aqueous part washer is an automated or semi-automated machine manufactured to clean, remove tough grease, and dry large or small parts before distribution or surface treatment. The washing is necessary since...
Please fill out the following form to submit a Request for Quote to any of the following companies listed on
This is the most complete informational guide to parts washers on the internet.
You will learn:
A parts washer is an engineered machine used to thoroughly clean components by effectively removing various contaminants like grit, grime, oil, debris, dirt, and paint. This critical cleaning step is necessary before parts are integrated into assembly lines, packaged, or subjected to coating applications. There are multiple types of parts washers available, including high-pressure washers, cabinet washers, rotary basket washers, and deburring machines, each specialized to meet unique industrial requirements.
Freshly manufactured components, whether they are machined, forged, or fabricated, frequently have leftover residues, such as oils, chemicals, burrs, abrasive particles, debris, and paint from the manufacturing process. These parts need to be meticulously cleaned and decontaminated before they can advance to subsequent stages of operation. This is where parts washers play a crucial role, ensuring that the components are thoroughly cleaned and prepared for the next phases of processing.
When designing an industrial parts washer, key considerations include the size, geometry, and configuration of the components to be cleaned. Additional design factors such as part weight, total surface area, orientation, presence of complex angles, enclosed sections, and blind holes must be thoroughly evaluated. Addressing these variables is crucial for ensuring optimal cleaning efficiency and comprehensive contaminant removal, especially when selecting and purchasing the ideal parts washer system for your application.
Parts washer manufacturers have various options to consider when developing advanced cleaning equipment for diverse industrial applications. These options include automated CNC programming, back or front loading mechanisms, baskets, trays, rack systems, rotary tables, and conveyor belt configurations. Most modern industrial parts washers use aqueous cleaning solutions with water-based solvents, detergents, or specialized degreasers to boil, power wash, or soak contaminated components. Customized systems are often necessary to accommodate the specific requirements of each customer, as part geometries and industry regulations can vary widely. For industries such as automotive, aerospace, medical device manufacturing, and heavy equipment maintenance, tailoring the design ensures compliance with stringent cleanliness standards and improves operational efficiency.
The fundamental components of a high-performance parts washer include a water heater, multi-stage filtration system, robust pumps, mechanical scrubbers or spray arms, high-pressure power nozzles, and a durable cabinet or enclosure. Integrating these parts washer components ensures thorough cleaning, oil and grease removal, and extended equipment lifespan.
The heating unit—powered by natural gas, electricity, or steam—is designed to rapidly elevate the temperature of the cleaning solution. Higher solution temperatures accelerate the removal of carbon, metal shavings, dirt, and oil, making the wash cycle more effective. Heated aqueous parts washers boost the performance of solvents, detergents, and chemical cleaners by enhancing reaction kinetics, which is especially vital for degreasing engine parts, transmission casings, and precision machinery.
An effective filtration system is the backbone of parts washer cleaning processes. As the cleaning solution circulates between the wash tank and storage reservoir, it passes through multi-stage filters. The initial coarse filter captures larger debris—including metal filings and heavy particles—while subsequent finer filter elements trap remaining particulates, preventing contamination carryover. High-capacity industrial filtration improves wash water longevity, reduces operating costs, and enhances parts cleanliness, making it an essential component in automated or manual parts washers.
Industrial-grade parts washer pumps are engineered for reliable operation, even when submerged in aggressive solvents, hot water, or alkaline detergents. These pumps transfer cleaning solutions from the storage tank to spray nozzles or mechanical brushes. For example, a quality parts washer pump may operate continuously at 185° F, moving 115 gallons per minute (GPM) with a pressure of 65 psi. Maintaining optimal GPM (gallons per minute) and PSI (pounds per square inch) is key to effective contaminant removal—vital for cleaning engines, transmission components, gears, or hydraulic parts in automotive or heavy industrial applications.
The scrubbing action in a parts washer is performed by either automated sprayers, mechanical brushes, or rotary spray arms. The pressurized cleaning solution is delivered via the pump to the scrubber system, which agitates and dislodges contaminants such as grease, lubricants, dirt, and carbon deposits from all surfaces of the parts—even in hard-to-reach areas. In heated spray parts washers, strategically placed nozzles ensure 360-degree coverage within the cabinet, guaranteeing consistent and reliable cleaning results for batches of small parts or large, irregularly-shaped items.
Parts washer cabinets are built in a range of sizes, configurations, and material grades to meet a variety of industrial cleaning needs. Cabinets may be constructed from stainless steel for enhanced chemical resistance and durability. They are engineered to withstand the high pressures and temperatures required to remove stubborn contaminants using water, solvents, or ultrasonic agitation. Parts washer enclosures can feature manual or automatic doors, sealed gaskets to prevent leaks, and advanced safety features. The cabinet design determines maximum load capacity, batch size, and integration with material handling systems such as conveyors or basket lifts, making it an important consideration for high-volume industrial operations.
Maintaining the appropriate water level in the cleaning tank is crucial for protecting washer components—especially the heater, which risks failure if exposed during operation. Automatic low-water shutoff valves monitor fluid levels and initiate a system shutdown if the water drops below a safe threshold. This prevents costly damage and enhances operator safety. Some advanced parts washer models also include digital water level sensors, alarms, and maintenance prompts to ensure reliable long-term operation in demanding industrial, automotive, or aerospace environments.
When selecting or specifying a parts washer, consider factors such as cycle time, energy efficiency, types of contaminants (oil, rust, paint, metal flakes, coolants), volume/throughput requirements, automation level, compatibility with environmentally friendly, biodegradable cleaning agents, and the facility's footprint. Some advanced parts washers offer programmable wash cycles, integrated oil skimmers, wastewater management systems, PLC controls, and remote monitoring for enhanced process control and resource savings. Evaluating these features is crucial for users seeking compliance with environmental regulations, lower operating costs, and maximum process uptime.
The purpose of a parts washer is to help maintain metal and mechanical parts in excellent condition for subsequent processing steps, such as assembly, painting, finishing, or repair. Though there are a variety of parts cleaning systems available to support industrial, automotive, and manufacturing needs, the majority of systems divide into two main types – aqueous or water-based parts cleaners, and solvent parts washers. Understanding the strengths and applications of these primary systems is essential for optimizing your maintenance processes and ensuring regulatory compliance with safety and environmental standards.
Aqueous cleaners have the cleaning power and efficiency of industrial solvents while utilizing cleaning solutions that are both biodegradable and water based. Aqueous parts washers are commonly used for removing oil, grease, dirt, and other contaminants from metal, plastic, and composite components. With the use of heat, agitation, and specialized detergents, these environmentally friendly cleaning systems support a variety of industries seeking to minimize hazardous waste and VOC emissions. Applications often include manufacturing, aerospace, automotive, and electronics industries where eco-friendly cleaning performance is a top priority.
Solvent cleaners work by dissolving stubborn dirt and contaminants through a chemical process, providing deep degreasing and removal of residues that may not be easily broken down by water-based systems. Industrial-grade solvent cleaners include mineral spirits, petroleum naphtha, benzene, trichloroethane, and xylenes, making them particularly effective for heavy-duty cleaning tasks, paint removal, or prepping surfaces for specialized coatings. Due to the flammable nature of many solvents, it is crucial to ensure proper ventilation and to utilize explosion-proof parts washers when handling volatile cleaning fluids, enhancing workplace safety and OSHA compliance.
Parts washers can also be categorized based on their level of automation: manual, semi-automated, or fully automated. This distinction impacts throughput, labor requirements, and suitability for different workflow demands in automotive repair shops, manufacturing plants, or precision engineering facilities.
A sink-on-a-drum is one of the most basic and common types of industrial parts washers, perfect for cleaning small automotive or mechanical parts individually or in limited batches. It features a durable drum with a sink basin mounted on top, equipped with a solvent or aqueous cleaning solution supply line. These models typically include a recirculating pump, replaceable filters, and cleaning brushes for effective spot cleaning. Sink-on-drum washers are favored in maintenance shops and garages for their portability and ease of use.
Immersion parts washers clean components by fully submerging them in a bath of cleaning solvent or water-based degreaser. The system uses agitation, oscillation, or ultrasonic energy to enhance the cleaning process, allowing the cleaning media to reach into crevices, blind holes, and other complex geometries. Once the parts are coated with the solution, a vibrating action generates turbulence in the liquid, ensuring effective removal of oil, grease, and particulate contaminants from industrial, automotive, or aerospace components.
Pull-out sprayers are a crucial component of many manual and semi-automated parts washers. They deliver pressurized streams of cleaning solution to flush away debris and deposits from hard-to-reach areas. Regular maintenance and inspection of spray nozzles is vital, as buildup can reduce cleaning efficiency and nozzle longevity.
Cabinet parts washers utilize a high-pressure, heated aqueous spray within an enclosed cabinet to efficiently clean parts of various sizes, including large and heavy machine components. Parts are loaded into a rotating basket or turntable through a front-access door. Inside the cabinet, parts receive thorough coverage from multiple spray jets that combine water, detergent, and heat to remove grease, cutting oils, and manufacturing residues. Spray cabinet washers are highly effective for automotive rebuilders, metal fabricators, and production facilities needing robust, automated cleaning performance.
The multi-purpose spray cabinet parts washer is an effective and convenient machine for cleaning small batches of diverse metal or plastic parts. Its flexibility allows operators to process different shapes and sizes without manual scrubbing. Features such as programmable cleaning cycles, adjustable spray pressures, and integrated filtration systems maximize productivity and reduce cross-contamination between parts, making these washers popular in engineering and maintenance departments.
Conveyor parts washing systems feature an enclosed, automated transport mechanism that moves baskets or fixtures of parts through each stage of the industrial cleaning process. The design of these industrial washers varies based on functions required at each cleaning stage, including pre-wash, main wash, rinse, and drying. In an immersion conveyor system, parts are transported to the washing station, rinsed, and then subjected to a series of drying cycles for rapid turnaround.
These industrial conveyor parts washers include several advanced features that enhance the efficiency and throughput of the cleaning process. Similar to robotic-fed washers, many systems incorporate stages with variable speed stainless steel conveyor belts, filtration and recirculation units, moisture blow-off mechanisms, heaters, and exhaust ducts. They offer continuous inline processing with dedicated heated wash zones, rinse zones, and precision drying, tailored to the cleanliness requirements and throughput demands of high-volume production lines.
The primary advantage of conveyorized continuous flow systems is their ability to process large quantities of parts efficiently with minimal operator handling. Conveyor parts washers can differ based on belt configuration, loading capacity, type of cleaning chemistry used, and integration with upstream or downstream automation. These features make conveyor parts washers a top choice for automotive, aerospace, and OEM manufacturers seeking scalable industrial parts cleaning solutions.
Rotary drum parts washers are designed for high-volume cleaning of small to medium-sized parts. Their rotating drum automates cleaning, rinsing, and drying operations, and is ideal for bulk processing of fasteners, stampings, or diecast components. The system employs high-pressure washing, immersion agitation, and tumbling action to reach into tubes, hollow sections, and complex shapes. Rotary drum washers support continuous production and consistent cleanliness results, helping reduce labor costs and maximize throughput in heavy manufacturing settings.
In part manufacturing, most burrs and sharp edges are removed during finishing, but tiny burrs often remain and need further attention. Industrial thermal deburring parts washers address these small defects by placing parts in a chamber filled with flammable gas, such as methane or hydrogen. The gas is pressurized and ignited briefly once the chamber reaches optimal temperature and pressure. The intense heat of the ignition vaporizes the burrs without damaging the base metal parts, ensuring precision and cleanliness for high-tolerance applications like hydraulics, tooling, and aerospace assemblies.
Complex industrial, medical, and automotive parts with embedded contaminants, deposits, and oxidation may not be effectively cleaned using only high-pressure spray or immersion methods. Ultrasonic cleaning systems offer a powerful alternative by using high-frequency ultrasound—typically ranging from 20 to 400 kHz—combined with a specialized aqueous or solvent-based cleaning solution. This process creates microscopic cavitation bubbles that agitate the liquid and generate localized high pressures and temperatures. The resulting agitation penetrates deep into holes, cracks, blind bores, and intricate crevices to thoroughly remove stubborn soils, oxidation, and residues. Ultrasonic parts washers are available in compact bench-top and high-capacity industrial models to suit different parts cleaning requirements in diverse industries.
Green parts washers, also referred to as biomatic or bio-based parts washers, offer an environmentally friendly method for degreasing and cleaning components. In these systems, parts are placed in a heated washer containing a pH-neutral cleaning solution with a colony of microorganisms. These microbes break down hydrocarbons, oils, and greases on the parts, converting contaminants into harmless carbon dioxide and water.
The cleaning process is enhanced by aeration, which increases oxygen to support microbial activity, and integrated filtration mechanisms for solution cleanliness. Thanks to this biomimetic process, the cleaning solution rarely needs replacement, reducing the total cost of ownership and minimizing hazardous waste disposal. Green parts washers are increasingly used in facilities that must meet strict EPA or OSHA requirements for sustainable, VOC-free, and nontoxic cleaning solutions.
Tunnel parts washers are specialized for linear, continuous parts washing—ideal for high-volume industrial production. Parts are automatically conveyed on belts or chain-driven systems through multiple treatment phases. The design of tunnel washers is customized to accommodate the specific dimensions, shapes, and material types of the parts, as well as crucial considerations like cycle time, hourly productivity, cleaning chemistry, and specific process requirements—such as degreasing, phosphating, rinsing, rust prevention, drying, or cooling. These industrial washers facilitate rapid, inline cleaning and are a mainstay in automotive, metalworking, and fabrication industries.
The carousel parts washer, similar in principle to conveyor models, is optimized for high-volume batch operations in compact spaces. Its circular design enables parts to be loaded and unloaded at a single location, simplifying workflow and allowing integration with automated robotic loading and unloading systems. With programmable cycles, multi-stage cleaning, and streamlined operator controls, carousel washers maximize efficiency and throughput for manufacturers with repetitive cleaning needs.
Certain parts washers may need to be classified as explosion-proof, particularly in industries handling flammable solvents or chemicals. To qualify as explosion-proof by National Fire Protection Association (NFPA) standards, a machine must be engineered with reinforced electrical systems, sealed enclosures, and spark-proof mechanisms to withstand internal explosions from volatile vapors or gases, and to prevent ignition of the surrounding work area. Explosion-proof parts washers are essential in oil and gas, aerospace, and chemical processing facilities where strict safety regulations and hazardous environment certifications are required.
Acid parts washers are built with corrosion-resistant materials and specialized components engineered to endure caustic substances and aggressive chemical exposure. Their robust design is critical for cleaning with acidic or alkaline solutions, supporting industries that must remove scale, rust, and oxidation from metal surfaces. These washers include fume extraction systems, chemical-resistant linings, and high-durability pumps to ensure longevity and operator safety.
Maintenance is crucial for extending the operating life of industrial parts washers and ensuring regulatory compliance with health and safety guidelines. Alliance Manufacturing provides a solution for top-load parts washers featuring a full access canopy. This removable fiberglass canopy grants easy access to the entire washer interior, eliminating the need for full disassembly. As a result, regular cleaning, preventative maintenance, and fast repairs are streamlined, improving overall equipment reliability and minimizing downtime.
Vibratory parts washers are a specific type of immersion washer intended for efficient batch processing and surface finishing in metalworking, aerospace, and automotive applications. Parts are placed in a container filled with cleaning media and solution, then agitated by a motor-driven vibration system. The resulting movement scrubs, polishes, and cleans components while simultaneously removing residues, burrs, and fine particulates from intricate surfaces. Vibratory washers can be configured for automated flow-through operation, continuous or batch use, supporting a wide range of industrial cleaning and deburring requirements.
Robot-fed parts washers integrate multiple washing and drying functions into a flexible, automated cleaning system. These systems perform prewashing, high-pressure washing, blow-off drying, and even deburring with minimal manual intervention. Using coordinated robotics, parts are loaded, moved between various treatment stages, and precisely positioned for multi-angle cleaning and drying. High-pressure nozzles reach deep into complex internal features—cross holes, bores, tapers, and cavities—making robot-fed washers ideal for cleaning precision-engineered components in industries such as automotive, medical device manufacturing, and aerospace.
When selecting an industrial parts washer, factors such as type of contamination (oil, grease, chips, rust), required cleanliness level, part size and material, cleaning chemistry (aqueous, solvent, acid, or bio-based), automation needs, and safety/environmental requirements should all be considered. Evaluating these variables ensures you choose the optimal system for your facility’s production workflow, maintenance goals, and compliance standards.
Parts washers represent a crucial investment and require regular maintenance to ensure optimal performance. For parts washers that are used frequently, weekly checks may be necessary to maintain their efficiency and proper operation. Below are some key steps to follow when assessing the condition of a parts washer.
The first step in effective maintenance is to familiarize yourself with the parts washer's components. Understanding how each part functions helps in identifying potential problem areas that may require closer inspection. Components such as tanks, heaters, pumps, nozzles, filters, and turntables can experience malfunctions or may not perform as expected.
The filter is a crucial component of the parts washer and should be checked regularly for buildup that can lead to clogging. It is generally recommended to replace the filter monthly, or more frequently based on the frequency of use. To prolong the life of the filtration system, consider pre-cleaning parts before placing them in the washer.
In spray-type parts washers, spraying is the most straightforward and cost-effective method for cleaning parts. It is important to regularly check the spray patterns to ensure they provide complete coverage and verify that the water pressure is adequate.
The pump generates the necessary pressure for the system and should be inspected for proper alignment and any required adjustments. Regular maintenance should include checking the pump’s bearings, depending on their location, and ensuring they are properly lubricated.
Certain cabinet parts washers feature a turntable that rotates parts for thorough cleaning. The turntable is driven by a set of gears, so it's crucial to ensure it operates correctly. Regularly check the bearings for proper lubrication and ensure the gears are aligned to prevent slippage. Additionally, monitor the turntable's weight capacity to avoid overloading. While washing more parts at once can reduce the overall cleaning time, the pump must have a high gallons-per-minute capacity to adequately cover all surfaces.
The turntable cleaning method can also incorporate indexing, where parts are washed individually. In an indexing system, parts are loaded onto a rotating fixture either manually or robotically. The fixture then indexes through timed cycles, typically ranging from three seconds or longer, moving the parts into high-pressure spray zones to effectively remove chips and oils.
Proper leveling of a parts washer is crucial for its optimal performance. Leveling is typically part of the installation process. Although rare, it is advisable to check the washer’s level if a malfunction occurs. For small, portable parts washers, ensuring the device is level during setup is essential and usually outlined in the manufacturer’s instructions.
Parts washers produce waste during the cleaning process, and proper disposal is essential. This waste should not be disposed of in onsite septic systems, as it can cause contamination. Waste may be managed by evaporation in some systems, but local regulations vary. Some municipalities allow waste to be discharged into the sewer system, so it is important to check with local regulatory agencies to ensure compliance with disposal guidelines.
When preparing parts for cleaning, avoid overfilling or tightly packing the cleaning basket, as this can result in inadequate cleaning and may require re-cleaning. To ensure parts are thoroughly cleaned, use methods such as visual inspection, particle counting, and other testing techniques.
Parts with burrs, cleaned using solvent or aqueous methods, can present challenges during the cleaning process. Thermal deburring is the most effective method for ensuring complete removal of these burrs.
Choosing the right solvent or cleaner is crucial for effective parts cleaning. Parts that are coated with oil-based coolants from machining processes require solvents specifically designed for hydrocarbon removal. For parts cleaned from grinding or lapping operations, an aqueous cleaning method is typically more suitable. Selecting the correct cleaner and cleaning process can significantly improve efficiency and reduce the time needed for parts washing.
When the cleaning solution becomes saturated with grime, dirt, and other contaminants, its ability to effectively clean diminishes, as the solution can no longer handle the volume of grease and oil. While using a skimmer or sludge scraper can help manage this issue, they do not completely eliminate the need for periodic cleaning of the parts washer tank.
A key component of a parts washer is the type of chemical or detergent used for cleaning. The choice depends on the type of parts being cleaned and the cleaning method. Chemicals and detergents for immersion cleaners differ from those used in ultrasonic or spray parts washers.
Parts cleaning often involves detergents and solvents that can be hazardous, dangerous, and toxic. Effective parts washer management includes monitoring the workplace environment to ensure proper control of these materials, thereby preventing potential injury and illness.
Washing parts is a complex process that requires specialized materials to effectively remove grease, grime, oil, chemicals, and soil from high-volume parts production. In response to growing environmental concerns, manufacturers are increasingly using biodegradable ingredients. For example, the detergent shown in the image below from TEMCO highlights this shift towards more eco-friendly cleaning solutions.
Oil eater detergents are an effective solution for cleaning industrial parts. They serve as degreasers without containing any acids.
Water-based detergents are high-quality parts cleaners that are pH-neutral, non-toxic, non-irritating, and non-flammable. They can also be used with bioremediating systems.
Detergents for aqueous parts washers are specifically formulated for use in jet sprayers and power washers. To enhance their effectiveness, these detergent solvents often include a defoamer, which floats on the surface of the washing solution to prevent foaming.
There are several different types of cleaning solutions designed to be used with ultrasonic parts cleaners. The different types include acidic solutions, alkaline solutions, high caustic solutions, deionized water, enzymatic solution, neutral solution, and mildly alkaline solutions.
Ultrasonic cleaning solutions can be either demulsifying or emulsifying. Demulsifying solutions are used to remove oily contaminants but must be drained from the tank after use. Emulsifying solutions suspend contaminants within the tank, which can lead to residues clinging to parts if the solution is used over multiple cleaning cycles.
Powerful and aggressive chemicals are essential for ensuring thorough cleaning and optimal performance of a parts washer. Regardless of the cleaning method employed, strong cleaning agents are necessary. Examples include Trichloroethylene, Butyl Cellosolve, bacteria-based cleaners, Sodium Hydroxide, Toluene, Benzene, and Acetone, among others.
Trichloroethylene: Trichloroethylene is a colorless chemical commonly used in cleaners and solvents.
Butyl Cellosolve: Butyl Cellosolve is present in a variety of cleaners, ranging from industrial to household products.
Bacteria: Bacteria and enzymes used in parts washers offer a natural method for removing soil and stains through a process known as bioremediation.
Sodium Hydroxide: Sodium Hydroxide is a caustic agent that effectively dissolves grease, oils, fats, and protein deposits.
Toluene: Toluene, which is less potent than acetone and butanone, is primarily used in paint thinners and dissolves adhesives, rubber, and sealants.
Benzene: Benzene is extensively used in manufacturing but must be handled with caution due to its harmful effects.
Acetone: Acetone serves multiple purposes, including cleaning and preparing metals for painting.
The chemicals listed above are among many used for parts cleaning. Due to their toxicity, they must be handled with great care. Proper storage and management are essential to ensure the safety of workers and the integrity of materials.
There are a variety of methods used to assess the cleanliness of parts. These methods range from simple visual inspections, such as wiping a part with a cloth, to more sophisticated tests involving chemical reactions. Because there are no universal cleanliness standards, the evaluation of cleanliness can be somewhat subjective. Below are some commonly used tests for determining part cleanliness.
The cotton swab test is a straightforward method where the surface of a part is wiped with a white glove or cotton swab. The glove or swab is then inspected for any residual contaminants. This visual inspection determines whether the part meets cleanliness standards based on the presence or absence of residues.
The dyne test measures the surface wetness or tension of a part. This simple test involves marking a flat area of the part with a pen, marker, or ink. If the ink beads up instead of spreading out, it indicates that the part's surface is contaminated.
The gravimetric test quantifies particulate matter on a part by measuring different levels of microns (μm), from as low as 2 μm to several microns. Initially, the part is washed with a solvent to determine its level of contamination. After cleaning with a chemical like acetone, the solvent is filtered to separate non-soluble contaminants. These contaminants are then analyzed for amount, weight, size, and type.
FTIR is used to assess organic cleanliness by scanning the infrared spectrum absorption rate of a part. The part is first rinsed in a solvent and then scanned to evaluate the organic residues before and after cleaning.
The TOC test measures the total, organic, and inorganic carbon content in dissolved carbon dioxide and carbonic acid salts. This test is performed before and after cleaning to gauge the efficiency of the cleaning process and to check for any remaining alkaline content.
This test checks for the presence of oil and hydrophobic films on freshly cleaned metals such as stainless steel, titanium, steel, aluminum, and brass. The part is immersed in clean water at an angle. The formation of water droplets that do not spread evenly indicates the presence of residues or oils.
The conductivity rinse test is conducted before, during, and after the rinsing process. Changes in the conductivity of the rinse water are used to evaluate the effectiveness of the rinsing process.
The ROSE test detects ionic contamination by using solvent solutions to extract ions from the part's substrate. The resistivity of the solution is analyzed before and after cleaning to determine the level of ionic contamination in units per square inch.
Similar to the ROSE test, ion chromatography uses thermal extraction to collect ionic species into a solution, which is then analyzed using an ion chromatograph. The test measures the level and type of ionic species and the conductivity of the extracted solution.
Precision cleaning is crucial for removing contaminants, meeting cleanliness parameters, and adhering to industry standards. While the concept of cleanliness might seem straightforward, each industry has its own interpretation, parameters, and requirements for cleanliness. Additionally, companies set their own cleanliness goals that must be met before a part is approved for use or shipment.
Parts washer manufacturers produce equipment that cleans parts to precise micron (µ) or micrometer levels, which are significantly smaller than inches or millimeters. This precision is critical due to the specific nature and use of the parts. Some parts washers clean to as low as 2 µm, while others may clean to 50 µm.
Accurate and precise cleaning is essential for ensuring the proper functioning of parts and preventing damage to equipment and components.
Precision cleaning is increasingly essential for enhancing the usability, safety, and longevity of parts. Modern manufacturing processes introduce various contaminants and unnecessary materials that must be removed through multiple cleaning methods. Effective precision cleaning ensures adherence to required cleanliness standards.
Contaminants are typically categorized into solid and residual types. Solid contaminants include fibers, particles, and fragments that attach to the part's surface, while residues are substances like oil or grease left behind after manufacturing.
Ensuring part cleanliness involves proper inspection following the cleaning process, using various testing methods to detect any remaining substances or materials.
An aqueous part washer is an automated or semi-automated machine manufactured to clean, remove tough grease, and dry large or small parts before distribution or surface treatment. The washing is necessary since...
Automated parts washers are mechanical devices designed to efficiently remove grit, oil, grime, dirt, paint and other contaminating substances from parts with minimum manual supervision. These substances are removed...
A parts cleaner is a cleaning device that uses various types of solvents, cleaning agents, and processes to remove grease, grime, and contaminating materials from manufactured parts prior to shipment or movement for further processing...
A wastewater evaporator is a method of removing water from water-based waste by converting the water in the waste to a vapor and leaving contaminants. The function of a wastewater evaporator is to reduce the volume of waste materials...
Parts washers are designed for cleaning, degreasing of equipment, and drying of mass quantities of small or large parts in preparation for surface treatment, assembly, inspection, or shipment...
Industries worldwide utilize abrasive blasting for various purposes, including cleaning rust and oil, removing surface coatings like paint and pollutants, preparing surfaces for paint and coatings, reinforcing metal surfaces and...
Deburring is a secondary operation of a machining process that enhances the final quality of the product by removing raised edges and unwanted pieces of material, known as burrs, left by the initial...
Finishing machines are machines used for metal finishing, which is the last stage of the metal fabrication process; the stage encompasses the use of machines in finishing the metal surface...
Sandblast cabinets include systems or machinery and components for projecting blast media against a part‘s surface to abrade, clean, or modify the surface. Sand, abrasive, metal shot, and other blast media are driven or propelled using pressurized water, compressed air, or a blast wheel...
Sandblasting equipment includes systems or machinery, and components for projecting blast media against a part‘s surface to abrade, clean, or modify the surface. Sand, abrasive, metal shot, and other blast media are driven or propelled using pressurized water, compressed air, or a blast wheel...
Shot peening equipment includes systems or machinery and components for projecting shot peening media against a part‘s surface to modify the surface or surface engineer the part...
A tumbling machine is a durable deburring and metal-polishing machine designed for finishing large parts or batches of smaller parts. A tumbling machine is also known as a barreling machine or a mass-finishing...
An ultrasonic cleaner is a type of sonic cleaner or sonic cleaning machine that uses cavitation to remove unwanted material. The cleaning effect is created by the compression and refraction of a cleaning medium. Miniscule vibrations propagate throughout the...
Ultrasonic cleaning is a type of cleaning process which uses cavitation induced by alternating compression and rarefaction cycles at ultrasonic frequencies. Ultrasonic frequencies are sound waves vibrating at 20 kHz or higher...
Vibratory tumbler is the equipment used in a vibratory finishing process, one of the most common methods in mass finishing. But how does a vibratory tumbler work...