Automated Parts Washers
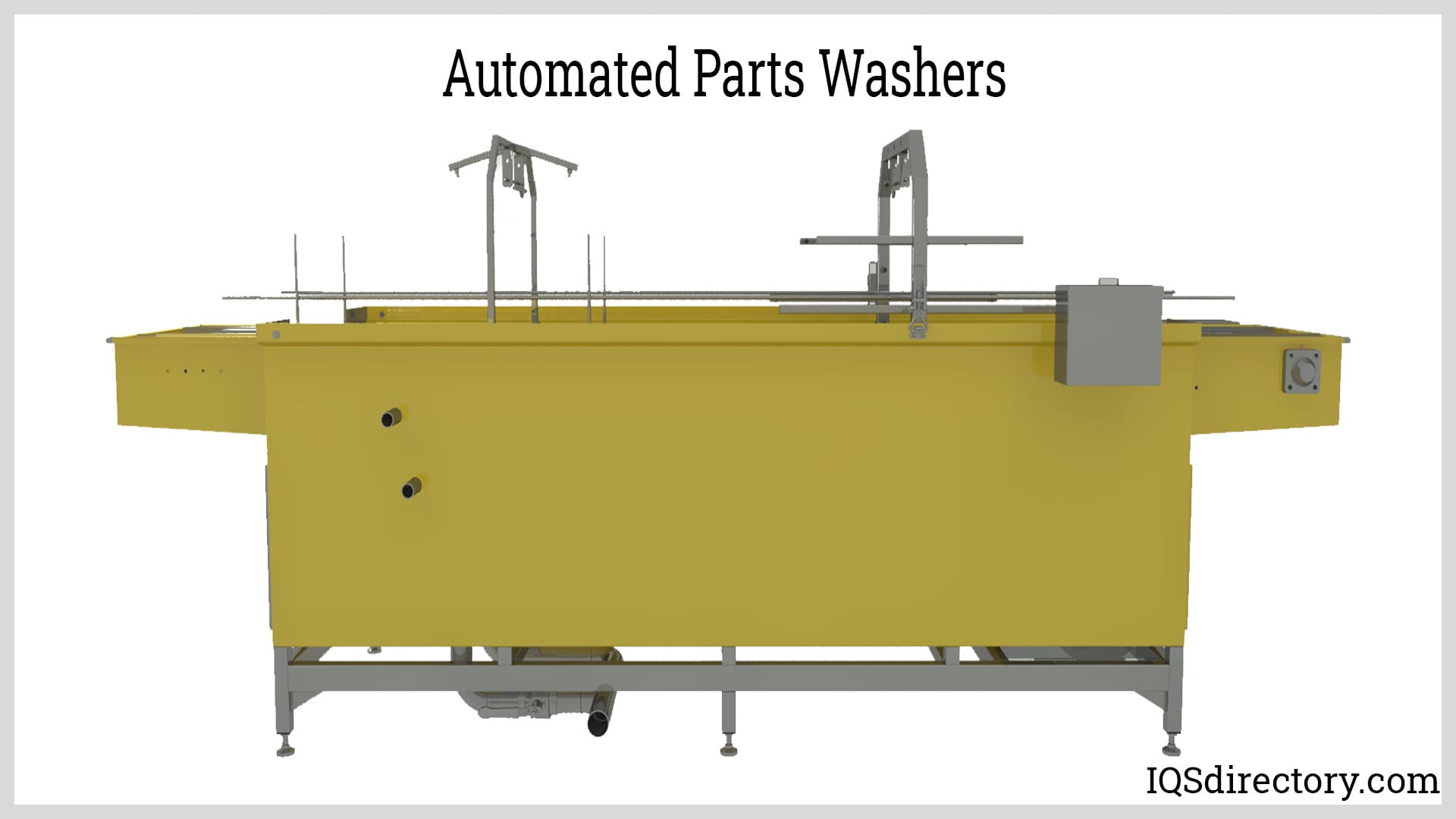
Automated parts washers are mechanical devices designed to efficiently remove grit, oil, grime, dirt, paint and other contaminating substances from parts with minimum manual supervision. These substances are removed...
Please fill out the following form to submit a Request for Quote to any of the following companies listed on
This article will take an in-depth look at aqueous part washers.
The article will bring more detail on topics such as:
This chapter delves into the concept of aqueous part washers, encompassing their design and operational mechanisms.
An aqueous part washer is a device, which can be either fully or semi-automated, crafted to meticulously clean and eliminate tough grease from a variety of parts, regardless of size. These machines not only clean but also dry the components, getting them ready for either shipping or subsequent surface treatments.
Cleaning is an indispensable step because during the manufacturing process, parts frequently accumulate coatings of chemicals, oils, and residues.
When considering the fundamental design of aqueous part washers, the dimensions, shape, and layout of the parts requiring cleaning come first. Additional considerations include weight distribution, surface area, and hidden cavities. Manufacturers often integrate CNC programming, loading baskets from either side, racks, trays, conveyor belts, and rotary tables for certain washer models.
The majority of parts washers are aqueous in nature, utilizing water-based solvents to efficiently immerse, boil, or blast components covered in grime. Essential parts of these washers include a water heater, pumps, a filtration system, brushes, scrubbers, and an enclosed cabinet.
The water heater is a pivotal element of the cleaning apparatus. It can operate using gas, steam, or electricity to heat the cleaning solution, thereby speeding up the cleaning cycle. Higher temperatures promote quicker chemical reactions among solvents, detergents, and other cleaning agents.
The filtration system purifies the water entering the system. Upon starting, the cleaning agent flows from the cleaning tank to the storage tank, passing through dual filters. The initial filter traps larger debris, while the secondary one captures finer particles that bypass the first.
The pump's role is to circulate the cleaning substances—be it solvent, water, or detergent—through the system. Continually functioning at high temperatures and flow rates, it ensures thorough cleaning by moving solutions from the storage to the cleaning tank. If this process is inefficient, the cleaning suffers in effectiveness.
Scrubbers in parts washers usually consist of sprayers or a series of brushes. The cleaning solution is pumped from the tank to these scrubbers, aiding in the overall cleaning procedure.
Washer cabinets are available in different sizes and capabilities, catering to varied cleaning requirements. The cleaning procedure is carried out using high-pressure aqueous solutions inside the cabinet or across a conveyor belt. Adequate water pressure is crucial for removing contaminants effectively. Cabinets are solidly built to withstand the strain from high-pressure operations and resistant to corrosive materials.
Ensuring the water level in the storage tank is at the correct level is crucial; if it drops too low, heaters may incur damage. An automatic low water shut-off valve prevents this by stopping the parts washer until optimal water levels are restored.
The operation of a parts washer is segmented into timed phases. Initially, parts are placed onto a turntable within the washer, and the door is closed securely. The cleaning cycle activates, spraying high-temperature and high-pressure water-detergent solutions to remove dirt and contaminants.
A closed-loop waste minimization system is integral to the washer's functionality. Key factors influencing operation include:
The cleaning effectiveness of a washer is mainly dictated by its power level—higher power provides a stronger blast for removing residues from parts. This power stems from the solution's pressure and flow rate, which together generate the necessary force to clear soils and residues.
Raising the temperature of the cleaning solution increases the fluidity of oil and grease, thus lowering their viscosity. Grease, which often acts as a binding agent for dirt, becomes easier to manage as the temperature escalates. Heating the solution to approximately 160 °F (71 °C) enhances the cleaning process by effectively breaking down grease.
Higher temperatures also accelerate the chemical reactions within the cleaning solution. Typically, an increase of about 54 °F (12.22 °C) can double the pace of these reactions, yielding quicker and more comprehensive results.
The chemical composition of the cleaning solution is vital for harnessing the washer's industrial strength. Chemicals are added to bolster the solvent's cleaning capability, with some exhibiting abrasive or corrosive traits for more robust stain and grease removal. Alkaline chemicals are frequently used to mitigate environmental impacts.
Aqueous part washers come in various types, primarily categorized by their construction and operational methods.
Spray washers use spray cabinets that clean parts by spraying a jet of heated solutions at moderate to high pressures inside an enclosed cabinet. The cabinets have a range of sizes depending on the parts that need to be cleaned, ranging from small to very large-sized cabinets. The spraying nozzles can clean away the heavy and difficult residues of soil, grease, oil, buffing substances, heat debris, and other contaminants.
In this type of part washer, parts are loaded through a front cabinet door into a perforated basket. Inside the cabinet, the basket rotates periodically while the parts are exposed to a high-pressure spray of cleaning chemicals, detergents, and water. This design allows for the efficient and convenient cleaning of multiple parts simultaneously.
A sink-top aqueous part washer is a straightforward and commonly used type of washer, essentially consisting of a sink mounted atop a drum. It is designed for cleaning individual or a small number of parts. This washer includes a drum that holds the solvent or water, along with a pump and brushes to manage and direct the cleaning solution. The sink-top design allows for hands-on cleaning with controlled application of the solvent.
For certain complex equipment parts, intensive cleaning is necessary because some contaminants and oxidation are resistant to standard pressure sprays or immersion methods. Ultrasonic cleaning systems address this by using ultrasound at frequencies ranging from 20 to 400 kHz, combined with a specialized cleaning solution. An ultrasonic system typically comprises three main components: a tank to hold the cleaning liquid and the dirty parts, a generator that converts the line voltage into ultrasonic waves, and transducers that produce the ultrasonic vibrations in the tank.
Transducers play a crucial role in converting ultrasonic electrical signals into kinetic and mechanical energy. During the cleaning process, high-frequency sound waves produce cavitation bubbles that agitate the cleaning liquid, generating heat energy in the process. This agitation energy penetrates deep into small holes, thin cracks, and crevices, effectively removing stubborn contaminants. Ultrasonic parts washers, which are often bench-top units, can vary greatly in size and may occupy substantial amounts of space.
Immersion part washers feature robust and simple tanks equipped with a pneumatically powered, reciprocating mechanism to agitate parts within a water-based fluid. These washers rely on a combination of agitation and oscillation to effectively clean parts immersed in a bath of cleaning solvents.
First, the parts are fully immersed in the solvent. Once the parts are thoroughly coated, an oscillatory vibrating action is applied to create turbulence within the solution, ensuring a thorough cleaning of the parts.
Conveyor parts washing systems utilize an enclosed and automated transport mechanism. These washers feature various belt options, including continuous flat wire, interlocking plastic, wire mesh, roller, and chain belts. The guide rails, which can be either fixed or adjustable, secure the components and contents on the belt during the washing process.
The mechanism in conveyor parts washing systems moves baskets or fixtures through each stage of the cleaning process. The design of the mechanism varies depending on the requirements of each cleaning stage. Conveyor parts washers are equipped with numerous features to streamline the washing process, including robotic and mechanized feeding systems. Some models offer adjustable settings for steel belt speeds, moisture blow-off, precise filtration units, heaters, and exhaust ducts. These systems ensure a continuous inline flow with distinct zones for high-temperature washing, rinsing, and air drying. Custom specifications can be tailored based on the parameters of the parts being cleaned.
Conveyor continuous flow systems are designed to maintain a constant throughput of parts with minimal direct handling. The key differences among systems often relate to whether they have fixed or variable speeds and the types of products they can process. Belt conveyor part washers are noted for their high efficiency and rapid processing speeds.
Rotary drum washers use a rotating drum equipped with an internal helix designed to advance and tumble parts through one or more stages. These washers are particularly effective for cleaning very small parts in high volumes. Similar to conveyor parts washers, rotary drum washers automate the processes of cleaning, rinsing, and drying, utilizing high-pressure sprayers for the cleaning phase. Additionally, an immersion agitation mechanism enhances the cleaning process by thoroughly reaching into tubes and hollows.
The drum sizes usually vary from 12 to up to 72 inches (30.48 to 182.88 cm), and the pitch and height of the inside helix can be altered or custom-made so that it meets the working requirements of part geometry and the optimum feed speeds. The rotary drum washers also allow for spray, immersion, or both, including washing, rinsing, drying, oil separation, and other advanced features.
Aqueous part washers offer various applications and benefits, including:
Aqueous part washers are utilized across a broad range of applications, from industrial settings to everyday commercial activities. If a machine fails, it can disrupt the entire system, potentially damaging products and harming the brand's reputation, which may impact future sales. In particular, part washers are extensively used in the automotive industry for degreasing and cleaning parts and equipment affected by grease and oil.
Parts are cleaned using aqueous part washers to ensure proper reconditioning and servicing, enabling continued, efficient operation. In addition to their use in the aerospace sector, part washers are also employed to clean aeronautical components, providing thorough and reliable cleaning for sustained performance. They are particularly effective for cleaning metal pipes, handling any size, shape, or material with consistent reliability.
Many chemicals used in parts cleaning can be harmful and pose significant health risks. Examples include trichloroethylene, perchloroethylene, and n-propyl bromide, all of which release volatile organic compounds (VOCs). These substances are highly flammable and can lead to severe health issues, such as headaches, dizziness, respiratory problems, and exacerbated allergy symptoms. Part washers are crucial in reducing direct human exposure to these hazardous chemicals. They primarily use water, heat energy, and alkaline detergents, which generally pose fewer health risks.
The chemicals used in parts cleaning not only pose risks to human and animal health but also to the environment. Solvent cleaners contribute to land and air pollution, which can be significantly reduced by using less harmful aqueous part washers. These washers utilize environmentally friendly materials, and residues are carefully managed before disposal.
Facility owners should prioritize worker safety alongside business needs. Aqueous part washers offer short run times, resulting in lower electricity costs and reduced labor requirements. They are highly economical due to their efficient mechanical performance.
In the manufacturing process, maintaining clean and well-maintained industrial machines is essential for uninterrupted operations. Regular upkeep ensures that equipment remains in optimal condition with minimal downtime. Aqueous part washers and other cleaning equipment are crucial for ensuring the safety, longevity, and quality of machinery and, consequently, the final products. The following sections detail how aqueous part washers benefit the manufacturing industry.
Incorrect components can compromise the entire product and damage the brand's reputation. They can also affect machine performance, leading to breakdowns and interruptions. Parts cleaners help remove residues and ensure smooth machine operation. Regular maintenance prevents surface damage, a major issue for industrial machines. Utilizing stock resource baskets and ultrasonic baskets can help prevent part damage.
Scrap production is an inevitable part of any manufacturing process and contributes to increased production costs. However, aligning maintenance with parts washing can significantly reduce scrap. Addressing part damages and removing debris and grease helps minimize waste and improve efficiency.
Production delays can severely impact output, sales, and brand reputation. Using parts cleaning machines helps prevent unforeseen machinery breakdowns, thereby reducing the likelihood of production delays.
Machines that lack regular maintenance are prone to frequent breakdowns, leading to higher repair and maintenance costs. Investing in reliable equipment like conveyor parts cleaners, part cleaning systems, and industrial cleaners can reduce the need for frequent repairs and replacements, offering long-term cost savings.
Aqueous part cleaners involve a moderate to high initial investment. Setting up these systems requires technical expertise to ensure reliability and efficiency. They use electrical energy for heating and energy conversion, making them more expensive compared to traditional solvent units. Additionally, aqueous part washers can be vulnerable to corrosion from oxygen or water. To mitigate rusting, rust inhibitors and additional drying mechanisms should be used to prevent moisture accumulation. Some stains and residues can be particularly stubborn and challenging to clean.
Chemical residues can be difficult to remove, even with ultrasonic part washers. Aqueous part washers require significant attention and intensive maintenance to prevent blockages, clogs, or damage caused by residual dirt from cleaned parts. Additionally, some part washers have a compact design that limits their ability to clean very large components. Their cleaning compartments may be too small to accommodate larger parts effectively.
Aqueous part washers operate similarly to other industrial part washers, with the primary goal of removing dust, oil, and grease from machine surfaces. However, these devices use different methods compared to other types of washers. Aqueous cleaners employ detergents, water, corrosive agents, and heat energy to remove debris from mechanical parts. While they are generally safe to operate, these washers can become hazardous if contaminated beyond their operational limits. Excessive contamination can lead to flash points exceeding 140 °F (60 °C), increasing the risk of flammability during the cleaning process.
In addition to increased heat output, aqueous cleaning systems can present other serious safety concerns. Without proper monitoring, these systems can reach pH levels below 2.0 (highly acidic) or above 12.5 (highly alkaline), both of which can have detrimental effects on the environment.
Aqueous cleaning machines use water to clean and rinse machine parts. Businesses must manage their water usage to comply with regulations and control costs. Facilities using aqueous cleaning systems should implement strategies to minimize water consumption while maintaining effective cleaning processes.
To protect both final products and employees during production and cleaning, operators must monitor the hazard levels of cleaning solutions. While some part washing systems are marketed as non-toxic or non-hazardous, these solutions can become hazardous over time. As they accumulate metal-bearing oils and grease, their toxicity and potency can increase. The following techniques can help control toxin levels in the cleaning solution:
Another critical factor in part washing is the choice of chemical or detergent used. The selection of detergent depends on the nature of the parts being cleaned and the cleaning method employed, whether ultrasonic or spray.
Parts cleaning often involves hazardous and toxic detergents and chemicals. Therefore, it is crucial to monitor the workplace environment to ensure proper control over these chemicals to prevent illness and injuries.
Detergents and chemicals used in parts cleaning generally include:
Cleaning parts effectively requires materials designed to remove grease, oil, grime, chemical residues, and soil from high volumes of parts. Due to growing environmental concerns, manufacturers are increasingly using biodegradable ingredients in their cleaning solutions.
Oil-eating detergents are highly effective for cleaning industrial parts and can serve as acid-free degreasers.
Water-based cleaning chemicals typically have a neutral pH and are non-toxic, non-flammable, and non-irritating. They are also suitable for use in bioremediation systems.
Detergents for aqueous parts cleaners are formulated for use in jet sprayers and power stream washers. To maximize efficiency, these detergent solvents include defoamers that rise to the surface of the cleaning solution to prevent foaming.
Numerous types of washing solutions are designed to be used in ultrasonic parts cleaners. The different types include acidic chemicals, alkaline chemicals, high caustic solutions, deionized water, enzymatic chemicals, neutral solution, and mildly alkaline chemicals.
Ultrasonic washing solutions are classified as either demulsifying or emulsifying. Demulsifying solutions are used to remove oily contaminants and should be drained from the tank promptly after cleaning. Emulsifying solutions, in contrast, suspend contaminants within the tank. If used over multiple cleaning cycles, debris may adhere to the parts upon removal.
Effective parts cleaning often requires strong abrasive chemicals for superior performance. Powerful cleaning agents, such as Trichloroethylene, Sodium Hydroxide, Butyl Cellosolve, Acetone, Toluene, and Benzene, are commonly used. Each of these chemicals serves a specific purpose:
Trichloroethylene is a water-like solvent used in various cleaning solutions. Sodium Hydroxide is a caustic agent that can dissolve grease, oil, fatty acids, and protein deposits. Butyl Cellosolve is frequently used in both industrial and household cleaners. Acetone is a versatile cleaner often used to prepare metals for painting.
Toluene, a solvent less potent than acetone and butanone, is primarily used in paint thinners and can dissolve adhesives, rubbers, and sealants. Bacteria, employed in part cleaners, offer a natural method of stain and soil removal through bioremediation. Benzene is widely used in manufacturing but requires careful handling due to its hazardous effects.
In summation, aqueous part washers are a form of machinery used to clean small to medium parts of industrial machines through the use of water-based solvents and temperature controls.
Automated parts washers are mechanical devices designed to efficiently remove grit, oil, grime, dirt, paint and other contaminating substances from parts with minimum manual supervision. These substances are removed...
A parts cleaner is a cleaning device that uses various types of solvents, cleaning agents, and processes to remove grease, grime, and contaminating materials from manufactured parts prior to shipment or movement for further processing...
A parts washer is a mechanical device designed to remove grit, grime, oil, miscellaneous debris, dirt, paint, and other contaminating substances from parts in preparation for their use in assembly operations, packaging, or coating...
A wastewater evaporator is a method of removing water from water-based waste by converting the water in the waste to a vapor and leaving contaminants. The function of a wastewater evaporator is to reduce the volume of waste materials...
Parts washers are designed for cleaning, degreasing of equipment, and drying of mass quantities of small or large parts in preparation for surface treatment, assembly, inspection, or shipment...
Industries worldwide utilize abrasive blasting for various purposes, including cleaning rust and oil, removing surface coatings like paint and pollutants, preparing surfaces for paint and coatings, reinforcing metal surfaces and...
Deburring is a secondary operation of a machining process that enhances the final quality of the product by removing raised edges and unwanted pieces of material, known as burrs, left by the initial...
Finishing machines are machines used for metal finishing, which is the last stage of the metal fabrication process; the stage encompasses the use of machines in finishing the metal surface...
Sandblast cabinets include systems or machinery and components for projecting blast media against a part‘s surface to abrade, clean, or modify the surface. Sand, abrasive, metal shot, and other blast media are driven or propelled using pressurized water, compressed air, or a blast wheel...
Sandblasting equipment includes systems or machinery, and components for projecting blast media against a part‘s surface to abrade, clean, or modify the surface. Sand, abrasive, metal shot, and other blast media are driven or propelled using pressurized water, compressed air, or a blast wheel...
Shot peening equipment includes systems or machinery and components for projecting shot peening media against a part‘s surface to modify the surface or surface engineer the part...
A tumbling machine is a durable deburring and metal-polishing machine designed for finishing large parts or batches of smaller parts. A tumbling machine is also known as a barreling machine or a mass-finishing...
An ultrasonic cleaner is a type of sonic cleaner or sonic cleaning machine that uses cavitation to remove unwanted material. The cleaning effect is created by the compression and refraction of a cleaning medium. Miniscule vibrations propagate throughout the...
Ultrasonic cleaning is a type of cleaning process which uses cavitation induced by alternating compression and rarefaction cycles at ultrasonic frequencies. Ultrasonic frequencies are sound waves vibrating at 20 kHz or higher...
Vibratory tumbler is the equipment used in a vibratory finishing process, one of the most common methods in mass finishing. But how does a vibratory tumbler work...