Aqueous Part Washers
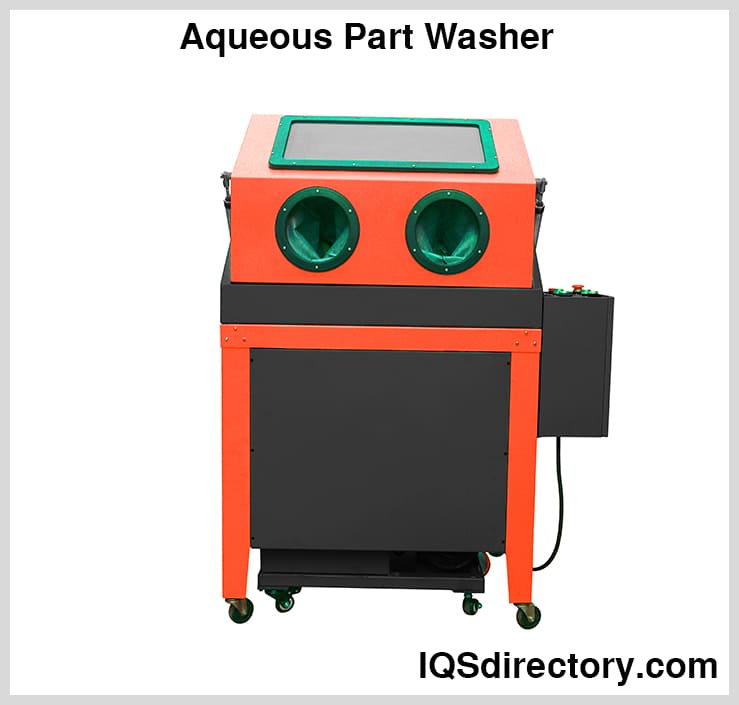
An aqueous part washer is an automated or semi-automated machine manufactured to clean, remove tough grease, and dry large or small parts before distribution or surface treatment. The washing is necessary since...
Please fill out the following form to submit a Request for Quote to any of the following companies listed on
This article will take an in-depth look at automated parts washers.
The article will look at topics such as:
This chapter provides a comprehensive overview of what automated parts washers are and how they function.
Automated parts washers are sophisticated cleaning systems crafted to efficiently eliminate grime, oil, dirt, paint, and other contaminants from parts with minimal manual effort. In the manufacturing phase, substances such as lubricants, oils, and chemicals are essential for enhancing operational efficiency and preventing damage. However, these substances must be effectively cleaned off before incorporating parts into assemblies, packaging them, or sending them for further coating processes.
Since their development, parts washers have seen remarkable evolution, advancing to function autonomously with cutting-edge software that oversees tasks like loading, unloading, washing, rinsing, and drying parts and assemblies. These automated systems reduce labor costs, boost productivity, significantly enhance the quality of cleaning, and efficiently manage large volumes of parts swiftly.
Automated parts washers include a diverse range of equipment such as high-pressure washers, washer cabinets, rotary basket washers, and deburring washers, among others. These adaptable machines are crafted to meticulously clean an extensive variety of parts, regardless of their size or intricacy, enabling manufacturers to achieve top-notch cleaning results, thus improving the quality of their end products.
Within the cleaning process, automated parts washers leverage solvents and chemicals combined with water to effectively eradicate dirt and grime accumulated throughout production. This crucial cleaning stage prepares parts for subsequent processes such as coating and finishing, which demand thoroughly cleaned and dried surfaces for optimal adhesive properties. Various cleaning media are employed to proficiently remove contaminants.
Newly manufactured parts often bear residuals such as burrs, abrasive dust, paint, and others from production processes. The complexity of these parts, with their unique shapes, grooves, blind spots, holes, and passageways, presents a significant cleaning challenge. Automated parts washers are expertly designed to tackle these difficulties, ensuring the complete cleaning of even the most intricate and detailed parts.
When designing parts washers, key factors include the size, shape, and configuration of the parts to be cleaned. Considerations also involve the parts' weight, closed sections, surface area, angles, and blind holes. For parts washer development, options such as CNC programming, front or back loading mechanisms, baskets, trays, rotary tables, and conveyor belts are evaluated. Most parts washers are aqueous, utilizing water-based solvents to soak and clean parts. The design of parts washers is tailored to meet the specific needs of each customer, accommodating unique part designs.
Typical components of a parts washer include a filtration system, pumps, scrubbers, brushes, a water heater, power nozzles, and a cabinet. These elements are essential for the effective cleaning and maintenance of the parts.
The heating unit's primary role is to rapidly increase the temperature of the cleaning solution, thereby expediting the cleaning process. This unit can be powered by gas, electricity, or steam, depending on the setup. By elevating the temperature, the heating assembly enhances the effectiveness of chemical reactions involving solvents, detergents, and other cleaning agents used in the washing process.
When the parts washer is activated, the cleaning water circulates from the cleaning tank to the storage tank. It first passes through a coarse filter that captures larger particles, followed by a finer filter that removes smaller particles that may have been missed by the initial filter.
Pumps in parts washers are designed to operate while immersed in solvents, water, and detergents. Their primary function is to deliver cleaning solutions to the cleaning tank. These pumps continuously transfer water from the storage tank to the cleaning tank, operating efficiently at temperatures up to 185 °F (85 °C). They can handle a flow rate of 115 gallons per minute (GPM) and operate at a pressure of 65 psi. Both GPM and psi are critical parameters for the effective performance of the pump.
Low GPM and PSI levels can lead to difficulties in fully eliminating the cleaning solution from the parts washer.
The scrubber comes in two types: a sprayer or a set of brushes. The pump delivers the cleaning solution from the storage tank to the scrubber, which then performs the cleaning of the parts.
Parts washer cabinets are available in various sizes, each offering distinct capabilities. The cleaning process involves applying a cleaning solution at high pressure, either within a cabinet or on a conveyor belt. It is essential for the water pressure to be sufficiently strong to effectively remove contaminants.
The cabinet is designed to endure high water pressure, ensuring it remains unaffected by continuous exposure to water or solvents.
The water level is managed in conjunction with the cleaner storage tank. If the water level drops too low, it can potentially damage the heater. To prevent this, an automatic probe detects low or high water levels and shuts off the parts washer when these critical thresholds are reached. The washer will not restart until the storage tank returns to the correct level.
The choice of cleaning agent influences the operation of different types of parts washers. These agents are typically classified as either aqueous or solvent-based. Aqueous cleaners are water-based solutions that combine water and detergent, utilizing mechanical action and heat for cleaning. Solvent cleaners, on the other hand, are petroleum-based compounds that can also be mixed with water-based cleaners.
Solvent-based cleaners are effective for cleaning metal parts by dissolving dirt and grime. It is important for these cleaners to be environmentally friendly and comply with relevant standards.
Aqueous-based cleaners typically maintain a neutral pH or consist of water-based solutions. Semi-aqueous cleaners include small quantities of solvents to enhance their effectiveness. These aqueous-based cleaners often utilize jet sprays for cleaning.
Parts washers have been enhanced and improved due to the advancement in technology. Most parts washers have now become automated and semi-automated to improve efficiency in carrying out assigned work.
Parts washer cabinets are designed for low-volume batch processing and are compact enough to integrate into various manufacturing processes. They offer a cost-effective solution for cleaning parts, avoiding the use of volatile organic compounds (VOCs) by employing high-pressure water to eliminate contaminants. These contaminants are effectively removed from the surfaces of the parts due to the precise engineering of the washers.
Spray angles are engineered to access every nook, cranny, and hole. Some cabinets feature a fixed, non-moving platform for part placement within the cleaning chamber, similar to a traditional household dishwasher. Others have a rotating platform that moves parts past a series of stationary pipe sprayers. Throughout the cleaning process, high-pressure water is used, and the rotating design is particularly efficient in managing water usage within the compact and enclosed cabinet.
Parts washer cabinets can be loaded manually, or by using robots or conveyors. Depending on the design of the washer, parts may be held in baskets, holders, or turntables. When the automated parts washer is activated, water is delivered from pipes at pressures ranging from 100 to 3500 psi. The combination of high-pressure spray and heated water effectively removes material from the surfaces of the parts. These washers are cost-effective, environmentally friendly, and optimize water usage.
Ultrasonic parts cleaners make use of the cavitation effect. In an ultrasonic cleaning tank, vibrating power is generated by transducers and transferred to liquids in the tank to form billions of imploding microscopic bubbles. The process forms a scrubbing action on the surface of parts, crevices, holes, and indentations. The nature of this process cleans the most complex and intricate parts and devices.
An ultrasonic parts cleaner comprises a bath, transducers, heaters, and a power source. Transducers and heaters are strategically positioned on the bottom and sides of the cleaner to optimize efficiency. The size of the bath must accommodate all parts effectively. Tanks are typically constructed from different grades of steel such as 316L and 304 stainless steel.
Contained transducers generate powerful vibrations at frequencies of 20 kHz, 80 kHz, 100 kHz, or 120 kHz. Lower frequencies produce more intense vibrations. Large-capacity ultrasonic parts washers typically operate at 28 kHz, while general ultrasonic cleaners range from 35 kHz to 45 kHz. High-frequency ultrasonic cleaners produce bubbles that release significant cleaning energy, capable of removing abrasives and polishing paste.
Transducers require electrical energy to generate vibrations necessary for effective cleaning. Sufficient power is crucial for optimal cleaning results. Parts are loaded into the cleaner using baskets suspended from the top. Each part must be fully submerged in the tank for thorough cleaning and should not contact other parts.
Biocycle parts cleaning systems are designed to eliminate hazardous chemicals and solvents. These systems use water-based immersion techniques with bio-safe chemical solutions as cleaning agents. Biocycle systems employ biological components and scientific principles, utilizing microbes—microscopic living organisms—to break down grease, oil, and contaminants.
Biocycle systems are self-cleaning through biodegradable formulas, aiming to provide a natural and safe cleaning method. After microbes clean the parts, remaining hydrocarbons are converted into carbon dioxide and water, which are filtered and reused. Oxygen is continuously supplied to maintain microbial activity.
The biocycle system offers environmental benefits and can be reused indefinitely, promoting cost-effectiveness and eco-friendliness. It significantly reduces costs and eliminates waste, with the cleaning solution maintaining stability over time. A control box monitors cleaning levels and oxygen supply to ensure optimal microbial function.
Spray parts washers are aqueous cabinet systems that use heated water and cleaning solutions to clean parts at high pressures. These systems typically feature nozzles that deliver jets of washing solution onto the parts. The washers are housed in stainless steel cabinets and may include either a fixed table or a turntable, depending on their design. The cleaning solution is sprayed through oscillating nozzles that continuously cover the load from various angles. The process is managed via a control panel, which handles rinse cycles, steam exhaust, and blow-off cycles to ensure efficient cleaning results.
The pumping system of the spray washer must be precisely aligned and function effectively without frequent adjustments. The spray manifold is designed to target parts from multiple angles: top-down, bottom-up, and from the sides. The oscillating motion of the spray manifold ensures that the cleaning solution covers every aspect of a part's surface thoroughly.
All nozzles in spray parts washers are designed to aim and spray with complete coverage, ensuring no intersecting spray patterns. Each nozzle directs its blast in a specific plane, providing precise cleaning. Spray parts washers come in various configurations, including models with either a rotating turntable or a fixed, stationary table. The effectiveness and efficiency of the cleaning depend on the nozzle types and their arrangement.
In mass production environments, spray parts washers often include a conveyor system to transport batches of parts through the spraying chambers. These systems may incorporate CNC controls to manage the complexity of the operation. Spray pressures can be adjusted between 30 psi and 70 psi, with temperatures ranging from 130 °F to 200 °F (54 °C to 93 °C) to optimize the cleaning process.
Carousel parts washers are a type of conveyor parts washer designed with multiple cleaning stages. They are particularly effective for parts that require precise, thorough, and complete cleaning. The carousel design is well-suited for high-volume production environments where rapid cleaning is essential and space is limited.
In an automated carousel parts washer, parts are both loaded and unloaded at the same location using a robotic mechanism. The conveyor path transports dirty parts through various cleaning stages before returning them to the loading area. The key advantages of carousel parts washers are their efficiency and speed, making them ideal for continuous, high-throughput operations.
Rotary drum parts washers are cost-effective for high-volume parts cleaning. In this washer, parts are washed using spray and immersion. In this process, the spray cleans the surface of parts as immersion flushes and cleans the insides. Rotary drum parts cleaners are machined to handle small parts in volume.
Rotary drum washers feature a rotating internal helix that tumbles and conveys parts through various stages of the cleaning process. The drum acts like an agitator, moving parts to different cleaning stations. Throughout the washing and rinsing cycles, the tumbling action ensures that all surfaces, edges, and crevices of the parts are thoroughly exposed and cleaned.
The green washer utilizes Bio-Matic, a blend of biological and scientific methods for cleaning. Parts are immersed in a heated washer with a pH-neutral solution mixed with a colony of microbes. These microbes operate in an environmentally safe manner. The rotary drum parts washer enhances cleaning efficiency through a combination of rotation and spraying, effectively removing chemicals, dirt, and grime from both the exterior and interior of parts. The high-pressure spray eliminates surface oils, dust, and contaminants, while the tumbling action flushes out holes, hollow areas, and blind spots.
Rotary drum washers come in various sizes, including mini, large, and dual configurations. Mini versions are designed for small parts and delicate components. Large versions offer greater cleaning power and are suited for high-volume cleaning. Dual types feature drums that operate at different speeds and can clean separate batches of parts simultaneously. These washers are designed to be space-efficient, making them ideal for environments with limited floor space.
This type of automated parts washer utilizes an inline parts conveying system, designed to integrate seamlessly with stamping presses, CNC machines, and other manufacturing processes. The system accommodates various belt sizes to handle different numbers and sizes of parts. It is programmed to perform multiple cycles, including washing, rinsing, blowing off, and drying, as parts move along the conveyor. A continuous flow of water is essential for effective operation.
Monorail systems, similar to conveyor systems, utilize an overhead conveying mechanism to move parts, in contrast to conveyor systems that use metal mesh belts. Monorail systems are integral to continuous processes, where parts are transported for cleaning, prepared, and then directed to further processing stages. These systems can feature closed-loop configurations, allowing for loading and unloading at the same station, or inline stages for streamlined operations. Pressurized cleaning solutions are sprayed onto parts via nozzles mounted on headers. Multiple control panels are included for maintenance, monitoring, and servicing.
Agitation-based parts cleaning utilizes an aqueous immersion method that relies on energy to generate vibrations and mixing actions, effectively removing surface dirt from parts. This vibration is produced by impellers and paddles that create cavitation on the part surfaces. The process is designed for parts that can endure rapid shaking and bouncing without sustaining damage.
The effectiveness of the agitation process is influenced by the chemical action of the surfactant, which ensures the cleaning agent thoroughly contacts the part surfaces. However, one drawback is the time required to remove grime and contaminants, making it less efficient for complex or heavily soiled parts. While agitation parts washers are cost-effective and consume less energy, they generally require more time to complete the cleaning process.
Immersion parts washers submerge parts in a cleaning solution. Immersion parts washers are also referred to as dip tank parts washers. These reveal items to be cleaned with a mixture of solvents, detergents, and other cleaners. Immersion parts washers are a cost-effective method for cleaning parts and saving energy. These washers can cater to large bulky parts and very small parts in batches with odd shapes, grooves, and blind spots.
To clean parts, they are placed in baskets and subjected to various processes, including soaking, ultrasonic cleaning, heat immersion, and agitation. Soaking is used for parts that are relatively easy to clean, preparing them for subsequent intensive cleaning steps. Agitation can take two forms: lift platform agitation and turbo agitation.
In lift platform agitation, parts are moved up and down within the cleaning solution, scrubbing and agitating their surfaces. Turbo agitation involves a pump that continuously circulates the cleaning solution to enhance cleaning effectiveness. Combining these two agitation methods often results in more thorough cleaning. Heat immersion uses water heated to high temperatures in conjunction with water-based cleaners, providing an eco-friendly alternative for parts washing.
Small parts washers are specifically designed to clean very small components such as screws, bullets, pipe fittings, scrap metal, castings, and bolts. These washers address the unique challenges of cleaning parts with blind holes, complex configurations, and both interior and exterior threads. Various oils, lubricants, and solutions are used in the manufacturing of these small parts to enhance shaping and forming efficiency. Before moving on to the next process, it is crucial to remove these lubricants. Small parts washers are generally less costly and more time-efficient compared to larger washers, due to their specialized design and application.
Immersion and rotation are popular methods for cleaning small parts. Rotary washers, for example, use a rotating mechanism to gently tumble parts within a basket. These washers can be constructed from stainless steel or plastic and are designed to clean both tools and other components. They typically feature a basket or a tank for immersing parts in cleaning solvents. The cleaning process involves solvents and detergents that are applied through helix rotation, agitation, and sprayers, ensuring effective removal of substances. Small parts washers can complement manual cleaning techniques to achieve optimal cleaning results.
This chapter will explore the diverse applications and benefits of automated parts washers, highlighting their efficiency, versatility, and impact on modern manufacturing processes.
Automated parts washers are essential in various industries. In automotive manufacturing, they clean both newly formed vehicle parts and used components covered in grease, road dirt, and grime. Hardware factories utilize these washers for high-volume cleaning of small tools and fasteners. In the medical sector, automated parts washers sanitize large quantities of reusable instruments and supplies. Recycling facilities also rely on these washers to clean and sanitize items like plastic bottles and drums before they are melted down and repurposed into new products.
Parts washers provide a safe and efficient method for cleaning components using elements such as water, heat, agitation, and environmentally friendly chemicals. They are cost-effective as they minimize the need for manual labor, with some cleaning processes operating without human intervention, thereby reducing labor costs. Parts washers are versatile, capable of cleaning parts of any size or complexity, including intricate and hard-to-reach areas. Manufacturers can efficiently control these machines using automated control panels, ensuring consistent and high-quality cleaning results.
Automated parts washers are mechanical devices designed to efficiently remove grit, oil, grime, dirt, paint, and other contaminating substances with minimum manual supervision. In short, the common use of an automated parts washer is to clean and prepare parts. Certain computer software is used to control the parts. In this design process, the first option to consider is the size, shape, and configuration of the parts to be cleaned. Some elements include weight, closed sections, surface area, angles, and blind holes. The standard components of a parts washer are the filtration system, pumps, scrubbers, brushes, a water heater, power nozzle, and cabinet. Types of automated parts washers include small parts washers, agitation parts washers, immersion parts washers, and conveyors parts washers. They can be used in the automotive, medical, and recycling sectors.
An aqueous part washer is an automated or semi-automated machine manufactured to clean, remove tough grease, and dry large or small parts before distribution or surface treatment. The washing is necessary since...
A parts cleaner is a cleaning device that uses various types of solvents, cleaning agents, and processes to remove grease, grime, and contaminating materials from manufactured parts prior to shipment or movement for further processing...
A parts washer is a mechanical device designed to remove grit, grime, oil, miscellaneous debris, dirt, paint, and other contaminating substances from parts in preparation for their use in assembly operations, packaging, or coating...
A wastewater evaporator is a method of removing water from water-based waste by converting the water in the waste to a vapor and leaving contaminants. The function of a wastewater evaporator is to reduce the volume of waste materials...
Parts washers are designed for cleaning, degreasing of equipment, and drying of mass quantities of small or large parts in preparation for surface treatment, assembly, inspection, or shipment...
Industries worldwide utilize abrasive blasting for various purposes, including cleaning rust and oil, removing surface coatings like paint and pollutants, preparing surfaces for paint and coatings, reinforcing metal surfaces and...
Deburring is a secondary operation of a machining process that enhances the final quality of the product by removing raised edges and unwanted pieces of material, known as burrs, left by the initial...
Finishing machines are machines used for metal finishing, which is the last stage of the metal fabrication process; the stage encompasses the use of machines in finishing the metal surface...
Sandblast cabinets include systems or machinery and components for projecting blast media against a part‘s surface to abrade, clean, or modify the surface. Sand, abrasive, metal shot, and other blast media are driven or propelled using pressurized water, compressed air, or a blast wheel...
Sandblasting equipment includes systems or machinery, and components for projecting blast media against a part‘s surface to abrade, clean, or modify the surface. Sand, abrasive, metal shot, and other blast media are driven or propelled using pressurized water, compressed air, or a blast wheel...
Shot peening equipment includes systems or machinery and components for projecting shot peening media against a part‘s surface to modify the surface or surface engineer the part...
A tumbling machine is a durable deburring and metal-polishing machine designed for finishing large parts or batches of smaller parts. A tumbling machine is also known as a barreling machine or a mass-finishing...
An ultrasonic cleaner is a type of sonic cleaner or sonic cleaning machine that uses cavitation to remove unwanted material. The cleaning effect is created by the compression and refraction of a cleaning medium. Miniscule vibrations propagate throughout the...
Ultrasonic cleaning is a type of cleaning process which uses cavitation induced by alternating compression and rarefaction cycles at ultrasonic frequencies. Ultrasonic frequencies are sound waves vibrating at 20 kHz or higher...
Vibratory tumbler is the equipment used in a vibratory finishing process, one of the most common methods in mass finishing. But how does a vibratory tumbler work...