Aqueous Part Washers
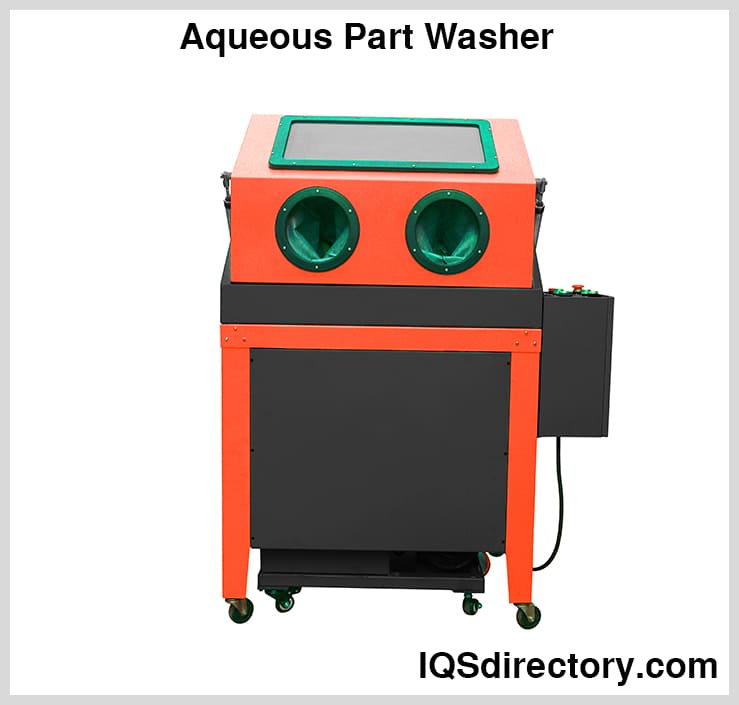
An aqueous part washer is an automated or semi-automated machine manufactured to clean, remove tough grease, and dry large or small parts before distribution or surface treatment. The washing is necessary since...
Please fill out the following form to submit a Request for Quote to any of the following companies listed on Part Cleaner .
This article explores all of the basics of Parts Cleaners.
You will learn more about topics such as:
A parts cleaner is a specialized machine engineered to remove grease, grime, and impurities from manufactured parts before they are dispatched or prepared for further processing. This cleaning operation not only readies the components for subsequent stages but also facilitates quality control by revealing potential flaws, defects, or irregularities.
The parts cleaning process is meticulously designed to efficiently and swiftly decontaminate large batches of components. It employs eco-friendly and biodegradable substances, making it a sustainable and secure method for cleansing.
When planning an effective parts cleaning process, the primary factor to consider is the quantity and size of industrial parts or components that need to be cleaned. The total volume impacts which parts cleaning method and equipment are most suitable for your workflow and operational requirements. For a small batch of machine parts, manual cleaning or hand brushing might deliver satisfactory results. However, larger batches or continuous production lines require specialized industrial parts cleaners such as automated washers, spray cabinets, or ultrasonic parts cleaning systems to ensure efficiency and thorough results.
Regardless of which method is selected, utilizing the appropriate cleaning solvent, degreaser, or chemical agent is essential to remove contaminants like oils, grease, carbon, and metal shavings. Manufacturers of parts cleaning machines offer a wide range of aqueous cleaners, water-based detergents, and solvent-based solutions designed to target specific soils found on automotive, aerospace, and electronic parts. Selecting the right cleaning agent ensures the desired cleanliness standards are met while addressing factors such as material compatibility, environmental regulations, and employee safety.
For manual cleaning, all tasks may be accomplished in one step with physical labor and simple tools. However, automated parts cleaning equipment typically incorporates multiple stages for optimal effectiveness, beginning with pre-cleaning. This initial phase takes place in a designated zone of the machine where incoming parts are prepared and surface contaminants are removed before entering the main cleaning chamber. Pre-cleaning frequently uses a light spray, compressed air, or mechanical agitation to dislodge dirt, loose particles, and machining debris from component surfaces. This step reduces the load placed on subsequent cleaning cycles and maximizes process efficiency.
During the cleaning stage, components are processed within the parts cleaning machine using the selected method and cleaning agent. The variety of industrial parts washers ranges from compact benchtop units about four feet tall to expansive conveyor belt washing systems used in high-volume manufacturing settings. In smaller units, the pre-wash and main wash are often combined into a single automated cycle, while larger conveyorized washers are divided into work zones or chambers, each dedicated to a distinct cleaning or rinsing step. These modular zones offer convenient access via service doors for inspection, routine maintenance, and system adjustments.
The rinsing phase is crucial for removing all traces of residual cleaner, degreaser, and embedded particles from part surfaces. The specific rinsing protocol is determined by industry standards and the required level of surface cleanliness — especially critical for manufacturing processes such as precision machining, aerospace assembly, or electronics fabrication where even microscopic residues may impact product performance.
Typically, city or tap water is employed to rinse parts, but for stringent cleanliness criteria, additional purification steps like deionized water or reverse osmosis filtration are implemented to prevent mineral deposits and ensure spot-free results. Thorough rinsing not only improves final part quality but can also reduce warranty claims and assembly defects.
Water usually constitutes around 95% of the total cleaning solution in aqueous-based systems. While standard tap water seems adequate, its mineral content — particularly calcium and magnesium — can cause scaling, streaks, and spots on precision components. Modern industrial rinse systems integrate advanced filtration and purification modules to maintain water purity, protecting critical parts and reducing the need for secondary cleaning steps.
After the main cleaning and rinsing cycle, certain metal or alloy components may feature exposed surfaces that remain prone to oxidation or corrosion. To address this, parts often undergo an additional treatment called a corrosion inhibitor rinse. This specialized rinse coats the surface with a thin, protective layer to prevent rust formation without contaminating or altering the surface finish. Effective corrosion protection is critical for parts destined for storage, further processing, or transport in humid or corrosive environments, safeguarding product integrity and prolonging lifecycle performance.
While solvent and chemical processes remain widely used for removing industrial soils, a variety of alternative parts cleaning technologies are available to meet diverse user requirements. Media blasting with plastic, ceramic, or metal pellets can efficiently dislodge caked-on residues; the dry ice (CO2) blasting technique offers a chemical-free approach suitable for sensitive components.
Ultrasonic cleaning uses high-frequency sound waves to create microscopic cavitation bubbles in a cleaning bath, aggressively scrubbing even the most intricate geometries, including blind holes and crevices — ideal for precision and medical device cleaning. Other popular approaches include vibratory cleaners for deburring and polishing, laser cleaning systems for selective surface treatment, brushes, and high-velocity compressed air blow-off systems. The selected cleaning method must consider part material, geometry, degree of contamination, and industry compliance standards such as ISO 16232, VDA 19, and RoHS regulations.
Understanding the full range of parts cleaning solutions empowers manufacturers, maintenance technicians, and quality assurance teams to optimize process performance and achieve reliable, repeatable cleanliness results. Whether for production, refurbishment, or preventive maintenance, parts cleaning remains an essential step in ensuring operational efficiency, minimizing downtime, and maintaining the integrity of critical components in nearly every manufacturing sector.
When selecting a parts cleaner, evaluating several factors—including part size and geometry, type of contaminants, cleaning cycle duration, throughput requirements, and budget—helps determine the optimal solution. For instance, automated parts washers and ultrasonic cleaners excel in high-throughput environments while manual dip tanks and bench-top cleaners suit low-volume applications. Additionally, consider machine features like filtration systems, programmable wash cycles, safety interlocks, and environmental compliance to ensure long-term, cost-effective performance.
Working with reputable parts cleaning equipment manufacturers ensures access to expert guidance, tailored system design, and reliable parts cleaner maintenance support.
When selecting industrial parts washers for effective component cleaning, it’s essential to understand the concept of power density. Power density is a critical metric in the parts cleaning process, measuring the amount of mechanical power—typically delivered by the pump motor—relative to the internal volume of the cleaner’s cabinet. This power-to-volume ratio significantly impacts parts cleaning efficiency and the washer’s capability to remove contaminants, grease, oil, and debris from a variety of components.
In the context of parts cleaners, power density specifically refers to the cleaning energy—expressed in horsepower (HP) per cubic foot—distributed within the cabinet volume. As the dimensions of the industrial washer, such as its diameter, width, and height, increase, the available power is spread over a larger area, leading to a decrease in power density. This can affect the cleaning action, especially for intricate or densely packed components, making optimal power density essential for deep and consistent cleaning.
When evaluating different types of parts washers (including aqueous parts washers, ultrasonic cleaners, and spray cabinet washers), it is paramount to assess the horsepower of the pump relative to the cleaner’s working volume. This relationship is visually represented in the image below, and it allows maintenance professionals and purchasing managers to compare equipment based on cleaning effectiveness, speed, and efficiency.
To accurately measure the performance of an aqueous parts washer or solvent-based parts cleaner, consider these four interrelated factors: mechanical energy, cleaning solution temperature, detergent (cleaning chemistry), and wash/rinse cycle time. A combination of high mechanical energy (i.e., increased power density), elevated operating temperature, and quality detergent enables rapid soil removal and superior results, even for tough industrial residues. The pump motor’s specifications, along with the design and maintenance of the spray nozzles or ultrasonic transducers, directly influence how power density translates to real-world cleaning performance.
As the size and internal volume of a parts washing machine increase—for instance, in large spray cabinet washers or conveyorized systems—the necessary power density changes as well. To sustain effective cleaning, the pump’s horsepower and overall mechanical output must be adjusted to the increased volume. Insufficient power density may result in inadequate cleaning cycles, especially for large, complex, or heavily soiled industrial parts. For proper machine selection and optimized cleaning, always refer to the manufacturer’s power density specifications for each model. Matching the right power-to-volume ratio ensures the equipment delivers consistent, high-quality results and meets industry cleaning standards.
Ultimately, power density is a decisive factor when it comes to maximizing parts cleaning performance and extending equipment life cycles while reducing maintenance costs. A parts cleaner with inadequate horsepower or poorly matched pump capacity can fall short in removing demanding contaminants, especially as the washer’s size increases. To streamline your procurement process or custom equipment design, always consult detailed manufacturer pump motor horsepower charts and power density guidelines. By considering the interplay between cabinet volume, cleaning energy, and specific application requirements, buyers and engineers can confidently select the right industrial parts cleaner for automotive, aerospace, machining, or manufacturing applications.
For those looking to further compare parts washer technologies or evaluate cleaning system upgrades, be sure to assess factors like energy efficiency, system throughput, ease of maintenance, and compatibility with various solvents or aqueous detergents. A well-engineered balance of power density and system design will result in reliable, repeatable, and environmentally responsible cleaning operations that align with both regulatory standards and end-user expectations.
Parts cleaners come in a wide range of models, with new designs continually emerging to address the evolving needs of manufacturers. Specialized cleaners are essential for tackling the challenge of cleaning complex and uniquely designed parts, particularly those with intricate details that require thorough cleaning of hard-to-reach areas.
There is a specific parts cleaner suitable for every task, regardless of its size or volume. For instance, parts cleaners used in auto repair shops tend to be smaller and more affordable compared to those designed for high-volume manufacturing environments. Despite their size differences, each type is engineered to deliver the necessary efficiency and effectiveness for its intended application.
Spray parts cleaners are among the most widely used types. They operate by using nozzles positioned at various angles to apply a combination of cleaning solution and water at high pressure. This pressurized spray effectively removes soil, grime, grease, oil, coolants, and other contaminants from the parts. Spray cleaning systems are commonly integrated into conveyor setups and cleaning cabinets.
The spray cleaning process is automated. Once parts are loaded into the system, the cleaner executes each stage of the cleaning cycle automatically.
Immersion parts cleaners consist of tanks or containers filled with a mixture of water and cleaning solution. This method is ideal for disassembled parts that require a prolonged soak in the solvent. Many immersion cleaners include agitation features, akin to those in household washing machines, to enhance the cleaning action. Additionally, some models combine immersion with ultrasonic cleaning, utilizing high-frequency vibrations produced by transducers. This combination is especially beneficial in the biotech and pharmaceutical industries for thorough cleaning of delicate components.
The rotary drum cleaner can be equipped with either perforated spray nozzles or function as a solid drum for immersion cleaning. As the drum rotates, it keeps the parts in continuous motion, enhancing the cleaning efficiency. The drums can differ in dimensions, rotation speed, and cleaning intensity. Rotary drum cleaners are designed to blend a gentle tumbling action with either immersion or spray methods to ensure thorough cleaning.
In a typical rotary drum cleaning cycle, the process starts with agitation to clean complex areas such as blind holes, hollows, and tubes. After cleaning, the parts are rinsed and dried. One of the key advantages of rotary drum cleaners is their durability, primarily attributed to the stainless steel construction of the drum.
Among the diverse range of parts cleaning equipment, part tumblers often don't receive the attention they deserve, despite being a highly efficient and well-engineered solution. Primarily used in the automotive industry, part tumblers excel in removing burrs and polishing parts. There are two main categories of parts tumblers: vibratory and rotary.
Both vibratory and rotary tumblers share a similar construction, featuring a barrel, base, drive system, motor, and gear assembly. The key difference lies in the type of motion they generate during the cleaning process. Both types can be employed for wet or dry deburring and are equipped with speed control features.
Rotary tumblers are equipped with a hexagonal or cylindrical barrel, along with a base, drive mechanism, motor, and gear assembly. The cleaning action in a rotary tumbler involves rotating the barrel with abrasive media inside, which generates a sliding motion. This method is known for its speed and effectiveness in both deburring and polishing parts.
In contrast to rotary tumblers, which rely on rotational movement, vibratory tumblers use a high-frequency side-to-side agitation. This rapid oscillation creates friction that effectively grinds the parts against one another, thoroughly cleaning their surfaces. Vibratory tumblers are particularly suited for processing small to medium-sized parts.
Conveyor parts cleaners are engineered to handle the high-volume cleaning of numerous parts in a streamlined, continuous process. While there are standard conveyor systems available, many are custom-designed to align with specific assembly operations. Common configurations include u-bend, monorail, and in-line systems.
These conveyor systems can be incorporated into existing assembly lines or operate as standalone units, based on operational requirements. Their flexibility allows conveyor parts cleaners to adapt to various applications and processes efficiently.
In a u-bend system, parts are introduced into the cleaning unit, processed, and then returned to the operator in a continuous loop. This setup resembles the conveyor mechanism found in commercial dishwashers.
A monorail system features a traditional conveyor's functionality but differs in that it transports parts using an overhead monorail. Components are mounted on custom supports that guide them through various cleaning stages. Each monorail system is tailored to meet the specific requirements of the parts and their intended application.
In an in-line or tunnel parts cleaner, parts are fed onto a conveyor at the entry point and exit thoroughly cleaned at the end. During their journey from entry to exit, the parts pass through multiple zones or stations, each dedicated to a specific cleaning process.
Ultrasonic parts cleaners use high-frequency sound waves, typically above 20 kHz, to remove contaminants such as dirt and grime. This process involves ultrasonic cavitation, where sound waves create rapid pressure changes that form bubbles in the cleaning solution. These bubbles collapse with force, generating heat and energy that dislodges debris from the surfaces of the parts. This method leverages sound frequencies beyond the range of human hearing to enhance the cleaning action.
Ultrasonic cleaning is highly versatile and can be customized to meet various cleaning requirements, from delicate medical instruments to complex aircraft components. Adjustments can be made to the cleaning temperature, solution, duration, and frequency of the ultrasonic waves to accommodate different cleaning needs.
Agitating parts cleaners are a variation of the immersion cleaning technique. In this method, parts are submerged in a tank filled with a cleaning solution, and both vibration and mixing are used to enhance the cleaning process. The vibrations are generated by impellers, creating a cavitation effect similar to that in ultrasonic cleaning, but at a less intense level. This agitation is further supported by high-pressure spray nozzles, which effectively clean blind holes and complex features of the parts.
Some surfaces need a gentler cleaning method that uses a milder but effective media. While shot blasting, which employs shards or beads, can be too harsh and alter the surface structure, soda blasting offers a more balanced approach.
Soda, rated 2.5 on the Mohs scale, is non-abrasive and will not etch or distort the surface being cleaned. It is particularly effective for cleaning softer, ductile metals like aluminum, and can remove contaminants such as dirt, grease, grime, paint, and carbon deposits. Soda blasting can be performed using either a slurry or a dry blasting method and typically does not require pre-washing of parts.
Specialized equipment is necessary for soda blasting because soda does not flow as easily as other abrasive materials.
Traditionally, parts were degreased by placing them in an open-top vapor degreaser (OTVD), initiating the process, and then removing the cleaned part once the solvent had done its job. However, due to concerns over high costs and safety, OTVDs are being gradually replaced by vacuum vapor degreasers (VVDs). VVDs offer the same cleaning capabilities with improved safety and cost-efficiency.
The effectiveness of VVDs lies in their ability to remove air from the cleaning process, which allows uncontaminated vapor to swiftly clean the part's surface. By eliminating air from the chamber, VVDs prevent any obstructions that could impede the vapor’s action. This technology enhances the degreaser's efficiency, enabling it to clean challenging areas such as blind holes and intricate designs. The cleaning solvent can thoroughly reach surfaces that were previously obstructed by air.
Vacuum degreasing addresses many limitations of older equipment, which, despite being effective, produced high emissions and consumed excessive energy. Modern vacuum degreasing systems eliminate these drawbacks, offering a more efficient and environmentally friendly solution.
Robotic arms equipped with six-axis capabilities provide a versatile solution for various manufacturing tasks such as deburring, flash removal, cleaning, and parting line removal. Driven by pneumatic systems, these robotic arms offer rapid, efficient, and safe defect removal in parts production. They can be programmed for extended reach and precise movements, with additional axis options available through turntables and linear tables to further enhance their operational range.
During the cleaning process, robotic arms use grippers to secure and properly position the workpiece for effective access. These robotic systems can be programmed to handle both cleaning and drying tasks. Advanced methods like CO2 or dry ice blasting are employed to remove dust, oil, and sub-micron particles. These non-abrasive techniques are safer and generate no secondary waste. CO2 blasting is suitable for a range of materials, including metals, plastics, and composites.
Modern manufacturing demands high levels of precision and accuracy, requiring parts to be thoroughly cleaned of all contaminants before assembly. While water-based cleaning methods are effective to some extent, they often fall short of meeting the stringent cleanliness standards required for production.
To address these needs, parts cleaner manufacturers collaborate with chemical companies to formulate solvents that are both effective and environmentally friendly. These solvents must be tailored to specific temperature requirements and can include various chemical compositions, such as chlorinated, brominated, fluorinated, or alcohol-based solutions.
When selecting cleaning chemicals, several factors must be evaluated, including health risks, flammability, and overall performance. Low-performing chemicals might necessitate higher temperatures and additional equipment, while fast-drying solvents pose safety hazards and require meticulous handling. Conversely, slow-drying solvents offer excellent performance but generally require supplementary drying processes.
Parts intended for manufacturing must be cleaned thoroughly before final assembly. Contaminants such as cutting oil, grease, and grime from production processes need to be removed to ensure product quality. Solvent-based cleaning methods are commonly used for this purpose, as they offer lower surface tension and viscosity compared to water, allowing them to penetrate into gaps, blind holes, and complex configurations. Solvents effectively wet the surfaces and evaporate from confined spaces.
Solvent based fluids provide lower surface tension and are less viscous than water, allowing them to get into gaps, blind holes, and intricate configurations. Solvents wet the surface of the parts and evaporate out of small tight areas.
Mineral spirits are a popular choice for parts cleaning due to their efficiency in dissolving oil, grease, dirt, grime, burnt carbon, and lubricants. Typically, petroleum-based mineral spirits are used in immersion parts cleaners due to their strong cleaning properties. However, these substances are highly volatile and flammable, making them unsuitable for use in many other types of parts cleaning equipment. Despite their effectiveness, mineral spirits pose significant health and environmental risks due to their toxicity.
Naphtha, a petroleum-based cleaner, is employed in the immersion parts cleaning method due to its potent and aggressive cleaning capabilities. It effectively removes contaminants without harming the surface of the parts. However, naphtha has a more intense odor compared to mineral spirits, which can be a significant drawback.
During the parts cleaning process, naphtha is kept in a reservoir beneath the cleaning unit. It is drawn from the tank under low pressure and applied to the parts through a spray nozzle for effective cleaning.
Bromide is utilized for cleaning lightweight metals and alloys due to its strong cleaning capabilities and quick evaporation, which facilitates faster cleaning processes. It operates effectively at moderate temperatures, contributing to reduced energy consumption and cost savings. Unlike petroleum-based solvents, bromides are non-flammable and do not possess a flash point, enhancing safety during use.
Oxygenated solvents, which contain oxygen in their molecular structure, offer high cleaning power while maintaining low toxicity levels. Ensuring the purity of these solvents is crucial, requiring careful purification during processing. Despite their high purity standards, oxygenated solvents are generally cost-effective.
Halogenated solvents contain halogen atoms such as fluorine, bromine, iodine, or chlorine. They are known for their non-flammable nature and rapid evaporation, making them effective cleaners. However, due to their significant environmental impact, their use for parts cleaning has become increasingly discouraged in recent years.
Alkaline cleaners are highly effective when mixed with water. They work best when combined with mechanical action and appropriate temperatures, efficiently removing contaminants and particulate matter. The degree of effectiveness depends on factors such as the type of contaminant, the volume of parts, and the level of automation in the cleaning process.
Alkaline cleaners typically consist of alkaline salts, wetting agents, and sequestrants. They quickly dissolve contaminants from metal surfaces and rinse off easily. Alkaline solutions are effective in dissolving oils and are used across various systems, including immersion tanks, spray cabinets, conveyorized systems, and ultrasonic cleaners.
Fluorinated solvents, also known as fluorosolvents, are used to clean oils, residues, flux, and contaminants from parts in high-volume operations. These solvents are recognized for their environmental benefits as they do not possess a flash point or contribute to ozone depletion. Additionally, they have a low global warming potential and minimal surface tension effects. Fluorinated solvents effectively penetrate contaminants without causing damage to the underlying materials.
The primary distinction between aqueous and solvent parts cleaners lies in their chemical composition. Solvent-based cleaners typically utilize petroleum-derived chemicals such as alcohols, chlorinated hydrocarbons, and terpenes. These solvents can be flammable and reactive, posing safety risks under certain conditions.
In contrast, aqueous cleaners are water-based solutions containing natural chemicals. They often include additives like surfactants, solvents, acids, alkaline agents, and inhibitors to improve their cleaning efficiency and address specific needs.
Aqueous cleaners are praised for their environmental safety, as they contain no volatile organic compounds (VOCs), hazardous pollutants, or flammable materials, and have minimal global warming potential. They dilute easily in water and rinse thoroughly after use. Various aqueous cleaners are available that work well with different cleaning methods, including spray, immersion, and ultrasonic cleaning.
The aqueous cleaning process is both quick and efficient, allowing parts to be loaded directly into the cleaning system without the need for pre-washing, soaking, or scrubbing. This simplicity makes aqueous cleaners cost-effective and reduces labor requirements.
Aqueous cleaners use hot water, a cleaner, and mechanical energy to remove dirt, grime, contaminants, and soil from parts. Their main benefit is their safety since they do not use any form of petroleum or flammable products that can produce harmful odors and be environmentally unsafe.
One significant concern for society is the volume of industrial waste generated during manufacturing processes. A notable advantage of aqueous cleaners is their ability to produce minimal waste, making them an environmentally friendly option.
Additionally, aqueous cleaners help reduce scrap and material waste. Their gentle cleaning action prevents damage to the parts being cleaned, which means fewer parts are discarded due to scratches or blemishes. This not only lowers waste but also contributes to overall material conservation.
One major issue with mineral and other petroleum-based solvents is the significant air pollution they generate, which poses risks to both workers and the surrounding community. Aqueous parts cleaners address this problem by providing a cleaner alternative that does not contribute to air pollution.
In the parts cleaning process, it's crucial to filter and clean the water to remove any residual cleaning agents, addressing both safety and environmental concerns. For aqueous cleaners, the cleaning solution can often be recovered and reused, minimizing contamination risks and enhancing sustainability.
Cost is a significant consideration in manufacturing, and aqueous cleaners often present a more economical option due to their reduced pollution potential. Their setup and operational footprint are generally less expensive and more efficient compared to other systems.
By eliminating petroleum-based cleaners, you also reduce the risk of damage to parts cleaning equipment. Petroleum solvents can degrade equipment surfaces over time, leading to increased maintenance and reduced equipment lifespan.
Ultrasonic parts cleaners utilize high-frequency sound waves to generate cavitation bubbles that break down contaminants at a molecular level. This process, enhanced by the use of aqueous cleaning solutions, accelerates and amplifies the cleaning action.
In response to environmental concerns, parts cleaner manufacturers are increasingly adopting aqueous cleaners as a safer alternative to traditional solvents. As a result, there has been a significant increase in the integration of aqueous solutions with ultrasonic cleaning, as well as with spray and immersion methods.
In today's manufacturing landscape, technology plays a crucial role in producing products and components quickly and efficiently. As demands for speed and precision rise, every stage of the process must be executed flawlessly, minimizing the need for reprocessing and reducing waste. Essential to this efficiency are parts cleaners, which prepare components for integration into final products.
The performance of parts cleaners is pivotal in ensuring that components meet the required quality standards and customer expectations. Dirty or defective parts can lead to production delays and increased costs.
Cleaning parts by hand is both time-consuming and inefficient, especially in a fast-paced production environment. As the demand for quicker turnaround times increases, relying on manual cleaning becomes impractical. It lacks the efficiency and capacity of modern parts cleaners. Utilizing pressure washing and agitation-based parts washers not only enhances cleaning effectiveness but also allows labor to be redirected towards more critical tasks.
Removing various types of lubricants, oils, grease, and other contaminants from part surfaces can be highly challenging. Parts cleaners are designed to tackle these tough residues, ensuring that grime is removed efficiently and safely.
Cleaning agents and solvents used to remove contaminants from parts can be aggressive and potentially hazardous. Parts cleaners mitigate these risks, promoting a safer working environment by handling the cleaning process efficiently and effectively.
Parts cleaners swiftly and effectively clean parts, ensuring they are ready for use. In the competitive landscape of today’s market, the speed of processing enhances productivity and optimizes the use of time and resources.
In addition to lowering labor costs, modern parts cleaning equipment is designed to use less power and water, thanks to its advanced technology. These machines also offer a longer operational lifespan, which helps to minimize equipment costs. Parts cleaners are durable and require infrequent repairs, allowing them to operate continuously with high efficiency.
Parts cleaners are available to suit every type of manufacturing operation. Whether it's a compact unit for automotive repair or an extensive conveyor system for large-scale assembly lines, parts cleaners can be customized and engineered to fit any specific space or configuration.
Efficiency and time management are crucial in manufacturing operations. Producing high-quality products quickly is essential to staying competitive in the market. Parts cleaners meet these demands by effectively preparing parts without escalating costs or utilizing additional resources.
Growing environmental concerns have heightened awareness among producers, particularly those working with solvents and chemicals. Today’s parts cleaner manufacturers are increasingly focused on creating equipment that cleans parts effectively while minimizing environmental impact. This shift has led to the development of parts cleaners designed to leave a minimal ecological footprint, utilizing recyclable and reusable materials.
Efficiency is crucial for every industrial operation, forming the foundation of effective production and customer satisfaction. As a result, parts cleaners have become indispensable across various industries, from small-scale toy manufacturers to major automobile producers.
In today’s competitive market, the quality of the final product sets companies apart. Consumers are increasingly demanding higher value from their purchases, prompting producers to refine their processes to ensure superior product quality. Consequently, parts cleaners have emerged as a vital component in maintaining high standards throughout production.
Medical instruments require flawless cleanliness and precision. In the production of medical equipment, a closed-loop cleaning system is employed, which integrates washing, rinsing, and drying into a single streamlined process. For enhanced cleanliness, a multi-step process is used, including cleaning, rinsing, passivation, additional rinsing, and drying, often utilizing ultrasonic technology. Parts cleaning equipment in the medical instrument industry is designed with precision engineering to meet these stringent requirements.
The aerospace industry demands exceptional cleaning for sensitive parts and aircraft sensors, which require precision engineering and machining. Ensuring the highest quality of parts is critical due to the need for accuracy and safety in aircraft operations. This heightened requirement places significant demands on parts cleaners to deliver superior cleaning performance, effectively removing all contaminants and particulate matter.
The cleaning process for automobile parts falls into two main categories: manufacturing and repair. In the repair category, individuals and repair shops use parts cleaners to remove accumulated materials from used parts to assess their reusability. In manufacturing, the focus is on ensuring the precision and quality of parts to meet the demanding conditions of vehicle use, thus guaranteeing the final product's reliability and performance.
Parts cleaners for the pharmaceutical industry must adhere to stringent cleanroom standards. The production of labware, instruments, and tools is meticulously monitored to ensure the highest levels of cleanliness and hygiene. Consequently, the processes for manufacturing pharmaceutical parts require precision-engineered cleaning equipment to meet these rigorous standards.
While the standards for food processing may not be as stringent as those for medical and pharmaceutical industries, producers must still comply with the Food and Drug Administration (FDA) regulations. The FDA provides comprehensive guidelines for the equipment, parts, and machines used in food production. These requirements necessitate the use of parts cleaning tools that integrate seamlessly into production processes and deliver thorough cleaning.
The energy industry shares similar concerns with the aerospace sector due to the harsh and hazardous conditions involved in energy production. The volatile nature of energy production requires that components and parts be free from residues or potential contaminants that could pose risks. Parts cleaners play a crucial role in ensuring that components are thoroughly cleansed of any potential hazards, meeting the stringent requirements of the industry.
The optics industry demands meticulous pre-sanitization of its components, such as fiber optic glass, microscope lenses, telescope lenses, and lighting instruments. Parts cleaners are essential for removing oil, burrs, fine metal particles, and soil from glass and quartz surfaces. A critical aspect of this process is the thorough rinsing, which ensures that no residue or product buildup remains, maintaining the high standards required for optical clarity and performance.
An aqueous part washer is an automated or semi-automated machine manufactured to clean, remove tough grease, and dry large or small parts before distribution or surface treatment. The washing is necessary since...
Automated parts washers are mechanical devices designed to efficiently remove grit, oil, grime, dirt, paint and other contaminating substances from parts with minimum manual supervision. These substances are removed...
A parts washer is a mechanical device designed to remove grit, grime, oil, miscellaneous debris, dirt, paint, and other contaminating substances from parts in preparation for their use in assembly operations, packaging, or coating...
A wastewater evaporator is a method of removing water from water-based waste by converting the water in the waste to a vapor and leaving contaminants. The function of a wastewater evaporator is to reduce the volume of waste materials...
Parts washers are designed for cleaning, degreasing of equipment, and drying of mass quantities of small or large parts in preparation for surface treatment, assembly, inspection, or shipment...
Industries worldwide utilize abrasive blasting for various purposes, including cleaning rust and oil, removing surface coatings like paint and pollutants, preparing surfaces for paint and coatings, reinforcing metal surfaces and...
Deburring is a secondary operation of a machining process that enhances the final quality of the product by removing raised edges and unwanted pieces of material, known as burrs, left by the initial...
Finishing machines are machines used for metal finishing, which is the last stage of the metal fabrication process; the stage encompasses the use of machines in finishing the metal surface...
Sandblast cabinets include systems or machinery and components for projecting blast media against a part's surface to abrade, clean, or modify the surface. Sand, abrasive, metal shot, and other blast media are driven or propelled using pressurized water, compressed air, or a blast wheel...
Sandblasting equipment includes systems or machinery, and components for projecting blast media against a part's surface to abrade, clean, or modify the surface. Sand, abrasive, metal shot, and other blast media are driven or propelled using pressurized water, compressed air, or a blast wheel...
Shot peening equipment includes systems or machinery and components for projecting shot peening media against a part's surface to modify the surface or surface engineer the part...
A tumbling machine is a durable deburring and metal-polishing machine designed for finishing large parts or batches of smaller parts. A tumbling machine is also known as a barreling machine or a mass-finishing...
An ultrasonic cleaner is a type of sonic cleaner or sonic cleaning machine that uses cavitation to remove unwanted material. The cleaning effect is created by the compression and refraction of a cleaning medium. Miniscule vibrations propagate throughout the...
Ultrasonic cleaning is a type of cleaning process which uses cavitation induced by alternating compression and rarefaction cycles at ultrasonic frequencies. Ultrasonic frequencies are sound waves vibrating at 20 kHz or higher...
Vibratory tumbler is the equipment used in a vibratory finishing process, one of the most common methods in mass finishing. But how does a vibratory tumbler work...