Aqueous Part Washers
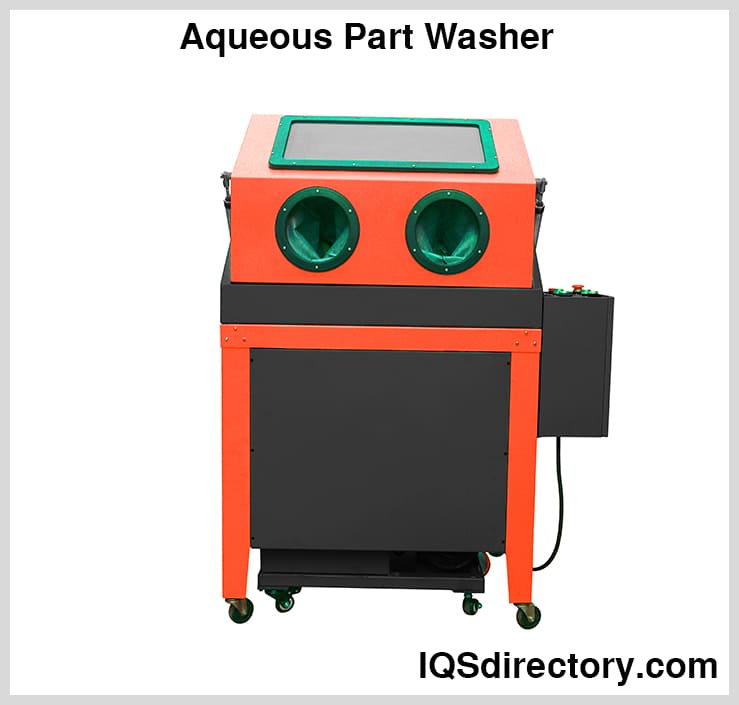
An aqueous part washer is an automated or semi-automated machine manufactured to clean, remove tough grease, and dry large or small parts before distribution or surface treatment. The washing is necessary since...
Please fill out the following form to submit a Request for Quote to any of the following companies listed on Parts Washers .
This Article takes an In-depth look at Types of Parts Washers
You will learn more about topics such as:
Parts washers are specialized devices used in industrial settings to efficiently clean a variety of components, eliminating contaminants such as grit, oil, grease, paint, and other residues. These machines are categorized by the dimensions and nature of the parts they cater to, ranging from tiny millimeter-sized pieces to intricately large instruments. Their function includes cleaning, degreasing, and drying substantial quantities of parts in preparation for surface treatments, assembly processes, inspections, or shipments.
During manufacturing processes, components forged, machined, or fabricated often collect unwanted substances including oils, chemicals, burrs, abrasive particles, and residues. Prior to being coated or used in an assembly line, these parts require meticulous cleaning to ensure that contaminants do not impair surface treatments. Parts washers provide exceptional surface purification, ensuring parts are devoid of impurities for smooth assembly and efficient application of surface treatments.
These washers employ solvents, mechanical motion, and specialized chemicals to thoroughly cleanse surfaces, eradicating debris that could otherwise impede further processing. This is especially vital in processes like electroplating, where a clean and dry surface is essential for optimal coating adhesion. Parts washers prevent potential complications, guaranteeing an effective and smooth coating application.
The fundamental engineering behind a parts washer is centered on effectively and efficiently removing contaminants—such as oils, grease, metal chips, and debris—from industrial and automotive components. The optimal parts washer design is determined by key factors: the size, shape, and material composition of the parts to be cleaned. The term "parts" covers an extensive range, including simple fasteners like nuts and bolts, as well as intricate components featuring varying weights, geometries, blind holes, and confined recesses. As the complexity of parts increases, the parts cleaning process often necessitates automated equipment and advanced cleaning methods to ensure proper contaminant removal and cleanliness standards.
Leading parts washer manufacturers employ expert engineering teams to deliver customized cleaning solutions for every application, from light-duty workshop tasks to large-scale industrial processes. Depending on a user’s requirements, common industrial parts washer systems may incorporate features such as baskets, programmable CNC controls, automated back- and front-loading, trays, conveyor belts, racking configurations, and rotary table mechanisms. The two main categories of parts washers are aqueous (water-based) and solvent-based systems, which differ primarily in the types of cleaning agents used. Aqueous parts washers use water and detergents for safe, eco-friendly cleaning, while solvent parts washers use strong organic solvents to dissolve contaminants.
Despite wide variations in model and design, virtually all industrial parts washers share core components that are essential for optimal operation and reliability. These include a high-efficiency water heater, multi-stage filtration system, industrial-grade pumps, mechanical or spray-action scrubbers and brushes, high-pressure power nozzles, strategically engineered tanks, and a robust enclosure to maintain operator safety and containment. Many modern units also feature automatic controls, programmable wash cycles, and smart sensor technology for energy savings and process optimization.
The water heater is a critical component in both aqueous parts washers and heated solvent systems. Depending on the specific application and available utilities, water heaters may be powered by gas, electricity, or steam. Their primary function is to raise the temperature of the washing solution, significantly enhancing the chemical reaction between detergents, degreasers, surfactants, and contaminants—thus ensuring effective parts cleaning. In high-throughput manufacturing environments, minimizing cycle time is essential, so efficient temperature control can dramatically reduce cleaning time while improving cleanliness outcomes. Advanced digital temperature controls and thermostatic safety features are now common in industrial parts washers, providing precise heat management and process consistency.
The filtration system is designed to continuously remove suspended solids—such as burrs, chips, metal shavings, and dirt—from the circulating cleaning solution. Positioned strategically between the cleaning tank and solution reservoir, the filter unit greatly extends the lifespan and performance of both detergent and washwater. Regular filtration ensures consistent cleaning effectiveness and minimizes maintenance downtime. Depending on operational requirements, filtration options may include single-pass cartridges, multi-stage filter arrays, bag filters, magnetic traps for ferrous particles, and even oil skimmers or coalescers for oil-water separation. Automated filter monitoring can signal when it is time to replace or clean the filtration media, further enhancing efficiency and process control.
Industrial parts washer pumps provide the necessary force to recirculate cleaning solution from the storage tank through the entire cleaning system. These heavy-duty pumps are constructed from chemically resistant materials such as stainless steel, polypropylene, or specialized alloys, enabling continuous operation at high temperatures (up to 200°F/93°C) and elevated flow rates. Performance ratings may vary, but it is common to find pumps moving over 100 gallons per minute (GPM) at pressures exceeding 65 PSI for commercial-grade applications. A robust pump is vital for maximizing cleaning coverage, whether sending fluid through spray nozzles, agitating bath-style washers, or powering rotary jets. Often, variable speed controls are available to adjust flow for different parts and contamination levels.
Within a parts washer, scrubbers are responsible for the mechanical removal of tough dirt, baked-on oils, carbon deposits, and other industrial residues. Scrubber systems may utilize rotating brushes, oscillating trays, or high-powered spray nozzles to physically dislodge deposits from component surfaces. Selection of the appropriate scrubber technology depends on the size, geometry, and sensitivity of parts—delicate electronics may require soft brushes, while robust castings can withstand more aggressive agitation. In automated wash systems, scrubber position and action are carefully coordinated with tank design and solution flow to reach complex surfaces, internal passages, or hidden recesses and ensure uniform cleaning results for every part.
Nozzles are integral to spray-wash systems and come in a range of designs: fan jets, full-cone, solid stream, and multi-orifice tips. Proper nozzle configuration ensures uniform impingement of the cleaning solution, which is essential for the removal of oils, grease, carbon, and particulate contaminants from the entire surface area. Advanced nozzle designs can deliver solution at variable patterns and pressures, addressing different soil loads and part configurations. In high-performance cabinet parts washers, spray arms equipped with precision nozzles ensure thorough coverage even in dense batches or complicated assemblies. Nozzles in heated aqueous washers typically deliver solution at temperatures from 130°F to 200°F (54°C to 93°C) for optimal soil breakdown.
Parts washer tanks are specifically engineered and sized to hold not just the fluid volume required for cleaning but also accommodate the physical parts load. Tanks may be constructed from stainless steel for maximum corrosion resistance, or coated steel for cost effectiveness. Many installations use compartmentalized tanks for sequential washing, rinsing, and drying phases to ensure no cross-contamination between stages. Cabinet and tunnel washers in industrial environments may feature fully sealed, insulated tanks to sustain uniform temperature and minimize energy consumption. For precision applications, ultrasonic parts washers use tanks designed to efficiently transmit ultrasonic waves for contaminant removal at a microscopic level.
The capacity and access design of each tank is chosen based on whether the parts washer is manual, automated, batch, or continuous flow. Manual benchtop units offer dipping tanks, while industrial cabinet and tunnel parts washers rely on enclosed, automated handling for operator safety and process control.
Parts washer enclosures play a vital role in maintaining safety, environmental compliance, and operational efficiency. Enclosures may vary from simple, open-top tanks with splash guards for light-duty maintenance cleaning to fully enclosed, automated conveyor systems for high-volume industrial applications. In compliance with environmental health and safety regulations, many modern enclosures include integrated ventilation, vapor containment, and access doors with interlocks to prevent operator exposure to cleaning chemicals and high temperatures. The design of the enclosure also helps to capture spent detergent, control splashing, reduce evaporation loss, and minimize workplace hazards from spray and aerosolized cleaning agents.
An essential safety and maintenance feature in both industrial and commercial parts washers is the low water shut-off valve. This device automatically disables the water heater and stops system operation when water or cleaning solution levels fall below a preset threshold, protecting both the heating element and the pump from overheating or dry-run damage. The low water shut-off system consists of a sensor probe, control circuit, and actuator—offering peace of mind for operators running multi-shift or unattended cleaning cycles. Many modern systems also include low fluid level alarms and remote shutdown integration for additional safety and process monitoring. This feature safeguards both equipment longevity and workplace safety, ensuring the parts washer remains reliable and cost-effective over its service life.
Selecting the best parts washer system for your needs involves careful consideration of the specific types of parts, soil loads, cleaning performance requirements, operating costs, and space constraints of your facility. Relevant LSI keywords include: ultrasonic parts washers, solvent-based cleaning machines, automated parts cleaning systems, industrial degreasing equipment, environmental regulations, and maintenance-friendly design. Buyer inquiries may revolve around system throughput, cleaning agent compatibility, energy efficiency, ease of filter maintenance, and available automation or IoT connectivity features. By understanding each basic component and its impact on cleaning efficacy, you can choose, operate, and maintain a parts washing solution that aligns with your application—be it for automotive shops, aerospace maintenance, medical device cleaning, or heavy machinery refurbishment.
For more information about advanced parts washing technologies, regulatory compliance, or to find a supplier of industrial-grade parts washers, explore our comprehensive parts washer buying guides and industry resources.
Parts washer cleaners are specialized systems designed to remove contaminants, grease, oil, and dirt from metal and plastic components in industrial, automotive, manufacturing, and maintenance applications. The types of parts washers are categorized based on the cleaning agents they use, which fall into two main categories: aqueous and solvent-based. Understanding the differences between these cleaning solutions is essential for selecting the optimal parts washer equipment for specific industrial maintenance, auto repair shops, manufacturing production lines, or aerospace component cleaning needs.
Mineral spirits, a traditional cleaning solvent derived from distilled petroleum, are highly effective for dissolving oils and grease in heavy-duty parts cleaning applications. These hydrocarbon-based solvents clean efficiently without the need for heat, ultrasound, or high-pressure sprays, making them ideal for immersion parts cleaning or manual degreasing. Mineral spirits act quickly, thoroughly cleaning holes, blind spots, and grooves on machinery parts, automotive components, and industrial tools, and they do not require rinsing after application. Additionally, they evaporate rapidly, which reduces drying time and increases throughput in work environments.
However, mineral spirit solvents have notable downsides, primarily their combustibility and high flammability due to their petroleum base. They present occupational health and safety risks, requiring specialized storage and usage precautions in maintenance workshops and industrial plants. The variety of mineral spirit solvents available requires careful selection to match the specific needs of a cleaning process, as solvent strength and VOC (volatile organic compound) emissions can vary greatly. Testing different types for their effectiveness is essential to ensure the best fit for your application, whether you require heavy grease removal or gentle cleaning of sensitive mechanical assemblies.
Despite their degreasing effectiveness, mineral spirits are not considered environmentally friendly and demand exceptionally careful handling and waste disposal to comply with EPA regulations and local hazardous waste statutes. Parts washers using these solvents need to be cleaned, drained, and refilled regularly, often on a monthly basis. Many companies, keen on sustainable cleaning solutions, prefer to avoid the issues associated with mineral spirit solvents due to the associated maintenance, environmental compliance costs, and worker safety concerns. For businesses seeking greener operations, alternative cleaning systems are increasingly preferred.
Fluorinated solvents are advanced industrial cleaning agents prized for their non-flammable, stable, and sustainable characteristics. They offer the unique advantage of multiple reuse cycles, making them an efficient and reliable solution for precision parts cleaning. Fluorinated solvents effectively clean a wide range of materials and delicate surfaces, such as electronics, circuit boards, aerospace components, and medical device parts. These cleaners evaporate quickly without leaving residue, ensuring thorough degreasing and contaminant removal while maximizing throughput in production environments.
The low surface tension of fluorinated solvents allows for deep penetration of tight spaces and micro-contaminants while remaining gentle on substrate surfaces like metals, plastics, polyurethane, and fluoroelastomers. This provides a significant benefit for those needing specialized cleaning for electronics assembly, aerospace maintenance, or medical instrument reprocessing. Despite being the most expensive cleaning products on the market, fluorinated solvents justify their higher cost through shorter cleaning and drying cycles, superior employee safety, lower risk of fire hazard, and their reusability—delivering excellent lifecycle value for advanced parts washing operations.
Aqueous parts cleaners, or water-based cleaning solutions, are gaining popularity due to increasing environmental and employee health concerns among businesses and manufacturers. Unlike mineral solvents that dissolve oil and grease, aqueous-based cleaners rely on surfactants to emulsify these substances and lift them away from mechanical or industrial parts. Surfactants in aqueous cleaner solutions bond with both water and oil, allowing thorough removal of contaminants from automotive, manufacturing, and electronic components. These parts cleaners are typically pH-neutral or mildly alkaline, making them an eco-friendly choice for companies focused on workplace safety and regulatory compliance.
To achieve greater cleaning efficiency, semi-aqueous solutions may incorporate small amounts of solvents and utilize jet sprays, ultrasonic agitation, or power washing techniques. Aqueous-based parts washing equipment offers flexibility for removing light dirt, oil, cured ink, and other challenging contaminants from mechanical assemblies, precision components, and production equipment. Heat, agitation, and adjustable spray pressures ensure a customizable cleaning process for industrial users. Additionally, additive boosters can be mixed with aqueous-based solvents to enhance rust removal, corrosion resistance, and surface brightening for metal parts and tools.
Although aqueous-based systems can be more costly and often require a high pH for optimal removal of stubborn contaminants, they offset these costs through reduced hazardous waste and improved sustainability. Post-cleaning processes such as rinsing and hot air drying might be necessary to prevent residue or corrosion. However, unlike mineral spirits, aqueous parts washer systems typically require less frequent maintenance, can operate longer without cleaning, and adhere to stricter environmental safety regulations, making them an appealing industrial cleaning solution for organizations prioritizing green practices.
Biological parts cleaners, also known as bioremediation parts washer systems, offer a highly sustainable and eco-friendly approach to parts cleaning. These advanced parts washers utilize naturally occurring microorganisms—such as specialized bacteria or enzymes—to break down and digest hydrocarbons, oils, greases, and other contaminants from machinery, automotive, aerospace, and industrial equipment.
These aqueous-based cleaners employ a non-toxic, non-flammable surfactant combined with robust microorganism cultures that continuously purify the cleaning solution. The bioremediation process extends the lifespan of both the cleaning fluid and the parts washing system, resulting in lower overall maintenance costs and minimized liquid waste generation. Biological cleaning systems are biodegradable, ensuring safe handling for both users and the environment, and eliminating exposure to volatile organic compounds (VOCs), solvents, or corrosive chemicals in the workplace.
Biological cleaning liquids—often paired with natural microorganism tablets—provide effective removal of stubborn contaminants such as carbon, heavy grease build-up, gunk, and oils without producing hazardous vapors or toxic by-products. The robust construction of biological parts washers, which often includes non-ferrous metals or durable plastics, also enhances heat retention and minimizes evaporation, leading to improved energy efficiency in your cleaning process. These greener systems often outperform traditional manual solvents and aqueous parts washers in terms of worker safety, regulatory compliance, and overall sustainability. The bioremediation mechanism ensures that both the equipment and cleaning fluids remain consistently ready for use, making biological cleaners a preferred choice across industries aiming to minimize their environmental footprint.
Choosing the right type of parts washer cleaner—whether it’s solvent-based, aqueous, or biological—requires evaluating your specific cleaning needs, environmental goals, workpiece materials, and industry compliance standards. By understanding the benefits and drawbacks of mineral spirits, fluorinated solvents, aqueous-based cleaners, and biological cleaning systems, you can optimize performance, safety, and cost-efficiency in any industrial or automotive cleaning application.
All parts need washing and cleaning to remove oil, grease, dirt, smut, and contaminants from their surfaces. This process is essential for preparing parts for further finishing, such as applying coatings, painting, and assembly. Proper cleaning is crucial for ensuring the adhesion of coatings and the quality of welding, as most components are subject to secondary processes.
Parts washing and cleaning processes vary widely, including manual washing in specially designed drums and automated systems with long conveyors and baskets. The three most commonly used methods in modern parts washing are auger, ultrasonic, and conveyor systems. The choice of method depends on the volume and complexity of the parts, with more intricate parts often requiring more focused and aggressive cleaning.
Auger or rotary drum parts washers are among the most cost-effective options for high-volume parts cleaning, rinsing, and drying. They operate in three key phases: spray cleaning, immersion, and drying. Spray cleaning removes surface contaminants by scrubbing the exterior of the parts, while immersion ensures thorough cleaning by flushing out contaminants from corners, angles, hollow sections, and tubes. This aqueous process is efficient and quick, making it well-suited for high-volume applications.
In an auger parts washer, parts are first loaded into the drum, and solvents are added. Once activated, the auger moves, causing the parts to spiral through the wash and rinse cycles. This method is highly effective for cleaning large quantities of small components but is not suitable for intricate or delicate parts.
Ultrasonic parts washing is a popular modern method that avoids aggressive agitation or motion to clean parts. Components are placed in baskets and submerged in a tank where ultrasonic waves are generated by a transducer. These waves create cavitation bubbles through high-frequency sound waves, which agitate the liquid solution. The resulting pressure from the agitation and cleaning agent effectively removes oil, grease, and dirt from the parts.
During the ultrasonic cleaning process, ultrasonic waves penetrate into cracks, hollows, angles, and recesses of parts, ensuring thorough cleaning of all surfaces. The absence of aggressive action makes ultrasonic cleaning ideal for delicate and fragile parts, as the sound waves clean without causing damage or harm.
Conveyor parts washers are inline, pass-through systems that feature a conveyor belt and a tunnel. These washers provide continuous cleaning, with the tunnel divided into sections that handle different stages of the cleaning process. Conveyor washers are ideal for high-volume production environments, where cleaned and dried parts seamlessly transition to subsequent operations such as assembly or welding.
Automated conveyor washers help to lower labor costs, boost efficiency, and ensure consistent results. They are capable of handling large volumes of various parts and are tailored to meet the specific cleaning needs of different operations. A key advantage of conveyor washers is their versatility, making them adaptable to a wide range of industries and capable of cleaning various types of parts.
Manual parts washing involves using a vat or drum where individual parts are cleaned by hand with various tools. Workers must wear protective clothing and gloves during this labor-intensive process, which is time-consuming and costly. The inconsistency of manual cleaning often makes it unreliable and inefficient, limiting its use to auto shops and specialized cleaning of delicate parts.
Solution turbulation washing is a spray washing technique where a solvent is circulated over, under, around, and through parts immersed in the solution. A pump agitates the solution, creating turbulence that is directed by manifolds equipped with educators or jets. This method provides higher impingement and increased cleaning power through dynamic spray, turbulence, and agitation, which constantly change the flow for more efficient and thorough cleaning. Although it involves immersion, the multifaceted nature of the process makes it difficult to categorize or define simply.
As technology advances, parts washers have evolved significantly. While manual parts washing remains in use, most operations have shifted to automated or semi-automated systems to boost efficiency. The range of techniques and methods for parts cleaning continues to expand, with ongoing innovations driven by new products and stricter requirements.
Industrial parts washers are employed in various operations, including manufacturing, remanufacturing, assembly, maintenance, and repair. They effectively remove a wide range of contaminants such as dirt, grime, dust, carbon, oil, grease, metal chips, chemicals, ink, paint, residue, burrs, and corrosion. Built for heavy-duty use, these washers are designed for continuous operation in diverse environments. Their cleaning efficiency is bolstered by a variety of cleaners, solvents, solutions, and methods.
Choosing the right industrial parts washer requires thorough research due to the wide variety of models and configurations available. While many people may envision a simple tub or barrel used by mechanics in repair shops for manual cleaning, industrial parts washers extend far beyond this image. They include large-scale machines designed to clean thousands of parts per hour, showcasing their advanced capabilities and high efficiency.
Manufacturers collaborate closely with customers to ensure they have all the necessary information to select the appropriate industrial parts washer for their specific industry, parts, and location. This careful consideration is crucial because some industrial parts washers require special handling and precautions due to their potential toxicity, flammability, or other hazards.
Parts washer cabinets are designed for low-volume batch processing, offering a compact and cost-effective solution for cleaning parts. They fit into various manufacturing processes while avoiding the use of volatile organic compounds (VOCs). Instead, these cabinets use water under pressure to remove contaminants from the surface of parts and are equipped to properly dispose of the removed materials.
Spray angles in parts washer cabinets are designed to ensure that every crevice, corner, and hole is thoroughly cleaned. These cabinets can feature either a fixed, non-moving platform for placing parts inside the cleaning chamber or a rotating platform that moves parts past a set of pipe sprayers. The fixed platform resembles a traditional home dishwasher, while the rotating platform provides enhanced coverage. In both configurations, water is applied at high pressure. The compact and enclosed design of parts washer cabinets helps control water usage, making them a more economical choice compared to other types of parts washers.
Loading a cabinet parts washer can be performed manually or with the assistance of a robot or powered conveyor. Parts are typically placed in baskets, on holders, or on turntables, depending on the design of the washer. Once activated, the washer sprays water from pipes at pressures ranging from 100 psi to 3500 psi. The combination of high-pressure spray and heated water effectively removes contaminants from the surface of the items being cleaned.
Cabinet parts washers use aqueous cleaning solutions, which combine detergent, hot water, and alkaline agents. These solutions are environmentally safe, biodegradable, and cost-effective. They help conserve water and improve the efficiency of the parts washing process.
Ultrasonic parts cleaning utilizes the cavitation effect, where transducers in the cleaning tank generate vibrations that create billions of microscopic bubbles in the liquid. These bubbles implode, generating a scrubbing action that cleans the surface of parts, including their most intricate crevices and holes. This thorough and inclusive process allows for effective cleaning of even the most complex and detailed components.
An ultrasonic parts cleaner consists of a bath, transducers, and heaters, all powered by a central source. The transducers and heaters are strategically placed on the bottom and sides of the tank to ensure optimal performance. The size of the bath must be sufficient to accommodate the parts being cleaned, and this is a key consideration during the selection process. Typically, the tanks are constructed from various grades of steel, including 316L or 304 stainless steel.
Transducers in ultrasonic parts cleaners can generate intense vibrations with common frequencies of 20kHz, 80kHz, 100kHz, and 120kHz. Lower frequencies produce more powerful vibrations, with large-capacity ultrasonic washers typically operating at 28kHz and most models functioning between 35kHz and 45kHz. High-frequency ultrasonic cleaners create bubbles that implode with significant cleaning energy, effectively removing abrasives and polishing pastes.
Transducers in ultrasonic parts cleaners require electrical energy to generate the necessary vibrations. The method of power supply varies depending on the design of the parts cleaner and the manufacturer’s proprietary methods. Regardless of the approach, it is crucial to ensure that the power provided is sufficient to complete the cleaning process effectively.
Parts to be cleaned in an ultrasonic parts cleaner can be loaded using various methods, with the most common being baskets suspended from the top or placed on racks. Regardless of the method, it is essential that the parts are fully immersed in the tank and do not come into contact with each other to ensure effective cleaning.
Features of Ultrasonic Parts Cleaners:
Biocycle parts cleaning systems were developed to eliminate the use of hazardous chemicals and solvents. These systems employ water-based immersion, spray, or turbo methods combined with bio-safe chemical solutions for cleaning. The approach integrates biological elements with scientific research, utilizing microbes to decompose grease, oil, and contaminants. The core of this process involves living microorganisms that effectively break down oil, grease, and hydrocarbon materials.
A biocycle system is designed to be self-cleaning using biodegradable formulas, offering a natural and safe method for parts cleaning. The system operates by having microbes clean the materials, with the remaining hydrocarbons being converted into carbon dioxide and water, which are then filtered and reused. Oxygen is continuously supplied to the solution to sustain the microbes. This approach is environmentally beneficial, reusable indefinitely, cost-effective, and eco-friendly.
The major benefits of biocycle systems include reduced costs and the elimination of waste. The cleaning solution remains stable over time, allowing for continuous reuse throughout the process. A control box mounted on the system monitors both the cleaning level and the oxygen supplied to the microorganisms, ensuring optimal performance.
Biocycle parts cleaning systems come in a variety of designs, from simple tubs for manual cleaning to large, sophisticated spray systems. The key component of these systems is the biochemical cleaner and its effective application.
Spray parts washers are cabinet-style aqueous washers that use heated water and solutions applied at high pressure to clean parts. Nozzles within the cabinet spray a jet or swirl of cleaning solution onto the parts. Like other types of parts washers, spray parts washers are enclosed in a steel or stainless steel cabinet and may feature either a fixed table or a turntable, depending on their design.
The cleaning solution is pumped through oscillating nozzles, which continuously blast the parts from multiple angles. A sophisticated control panel manages the solution level, temperature, suction pump filter, various safety devices, and electrical connections. To ensure optimal performance, spray parts washers typically include rinse, steam exhaust, and blow-off cycles.
The efficiency of a spray parts washer hinges on its precisely aligned pumping system, which must operate seamlessly without requiring frequent adjustments. The spray manifold targets the parts from multiple angles—top-down, bottom-up, and from the sides. The oscillating motion of the spray manifold ensures that every part surface is thoroughly cleaned.
Spray parts washers feature various nozzle designs, each crafted to provide precise aiming, spraying, and complete coverage without overlapping spray patterns. Each nozzle delivers its spray in a single plane directly onto the surface of the parts. When choosing a spray parts washer, evaluating the nozzle spray patterns is essential to ensure effective cleaning.
Spray parts washers are available in various designs, including those with a turntable driven by a motor and others with a stationary fixed table. Regardless of the type, the key factor in all spray parts washers is the effectiveness and efficiency of their spraying system.
In mass production facilities, spray parts washers may include a conveyor system that transports batches of parts through various spraying chambers. These inline systems are integrated with other industrial and assembly processes. Due to their complexity, conveyor spray washers often require CNC systems, specialized software, or other forms of automation. The spraying solution is typically heated to temperatures ranging from 130°F to 200°F, with spray pressures ranging from 30 psi to 70 psi.
Rotary drum parts washers are a cost-effective solution for high-volume parts cleaning. They utilize both spray and immersion methods: spray cleaning targets the surface of parts, while immersion removes contaminants from inside. Designed to handle large quantities of small parts, these washers feature a rotating internal helix that tumbles and conveys parts through different stages of the cleaning process.
The drum in a rotary drum parts washer functions as an agitator, moving parts through various cleaning stations. While these washers are designed for small parts, they can continuously clean parts as they travel through the long, cylindrical drum. The screw-like helix mechanism facilitates this movement, ensuring parts are gently tumbled during the washing and rinsing cycles to expose all surfaces, edges, and crevices.
The rotation and spraying in rotary drum parts washers significantly boost cleaning efficiency by removing grime, chemicals, dirt, and debris from both the exterior and interior of parts. The spray force tackles surface oils, dust, and contaminants, while the tumbling immersion process flushes out holes, deep indentations, hollow areas, and blind spots.
Varieties of Rotary Drum Parts Washers by Size:
Conveyor parts washers utilize an inline conveyor system to feed parts directly from stamping presses, CNC machines, and other manufacturing processes. They come in various belt sizes to accommodate different quantities and sizes of parts.
In a standard conveyor parts cleaning system, parts move through various cycles including washing, rinsing, blowing off excess water, and drying. Additional stages can be integrated, such as extra rinsing, rust inhibiting, phosphate application, and sealing, depending on the requirements.
Like other parts cleaning equipment, conveyor parts washers use high-efficiency, maintenance-free pumping systems to ensure a steady flow of water and cleaning solutions. The drying cycle is meticulously engineered to deliver spot-free, flawless drying.
Monorail parts washers operate similarly to conveyor systems but with a distinct difference: instead of using a metal mesh belt, they feature an overhead conveying system. Parts are hung or placed in baskets and transported through the various cleaning cycles.
The conveyance method used in monorail parts washers is well-suited for ultrasonic cleaning, accommodating both small and large parts. To ensure effective ultrasonic cleaning, parts first go through a pre-wash stage before being subjected to the ultrasonic process.
Monorail systems are typically integrated into continuous processing workflows, where parts are cleaned, prepared, and then transferred for additional processing. Similar to conveyor systems, monorail systems can feature multiple stages arranged in closed-loop or inline configurations. In a closed-loop system, operators can load and unload parts at the same station, streamlining the process.
Spray nozzles in monorail systems are mounted on headers to distribute pressurized cleaning solutions over the parts. These systems feature multiple access panels for easy maintenance, monitoring, and servicing. To prevent parts from falling into collection tanks, various protective methods are employed. In large monorail systems, catwalk-style gratings provide personnel with safe access for walking through the monorail tunnel.
Monorail systems are integrated into continuous production lines and are customized to align with existing processes. They are designed with hooks, hangers, fixtures, and other movement devices that match the customer's specific production setup.
Agitating parts washers use an aqueous immersion method to clean parts by generating vibrations and mixing action. This is achieved through impellers or paddles that create cavitation on the surfaces of the parts. Designed for parts that can endure shaking, rapid movement, and bouncing, this method effectively removes surface dirt without causing damage.
The agitation process effectively ensures that the cleaning agent contacts all surfaces of the parts, relying on the chemical action of the surfactant. However, this method can be time-consuming for removing grime and contaminants. It is not ideal for delicate, complex, or intricate parts, which may not withstand the vigorous movement and shaking associated with agitation parts washers.
Agitation parts washers often require extended operation times, which can slow down other processes in an assembly line. They also necessitate manual loading and monitoring during processing. Despite these drawbacks, they tend to be more cost-effective and use less energy compared to other cleaning methods.
Immersion parts washers, also known as dip tank parts washers, clean items by submerging them in a solution of solvents, detergents, and various cleaners. Like agitator parts washers, they are cost-effective and energy-efficient. Immersion parts washers are versatile, able to clean both large, bulky parts and small, intricate items with odd shapes, grooves, holes, and blind spots.
There are several varieties of immersion methods, but all share certain basic features. These include a large washing tank or a series of tanks that churn the cleaning solution. Parts are placed in baskets and undergo one or more of the following cleaning steps:
Small parts washers are specifically designed to clean very small items like screws, bolts, nuts, bullets, pipe fittings, scrap metal, castings, and stampings. These washers are built to handle the intricate cleaning needs of small parts, which often feature blind holes, complex configurations, and both interior and exterior threads that require thorough decontamination.
In the manufacturing of small parts, various oils, lubricants, and solutions are used to facilitate shaping and forming. These lubricants must be thoroughly removed before the parts proceed to subsequent processes. While large parts washers can handle this task, their use can be time-consuming and expensive. To address this, manufacturers have developed small parts washers specifically designed for the unique needs of small parts. These washers are compact, efficient, and tailored to effectively clean intricate components without the drawbacks of larger systems.
Two common methods for cleaning small parts are immersion and rotation. Immersion washers submerge the parts in a cleaning solution, while rotary washers use a rotating system to gently tumble the parts within a basket. Both methods can be designed with small tanks or helixes to accommodate the scale of the components. Small parts washers are often constructed from metals like steel and stainless steel, but due to their smaller size, they can also be made from plastic.
Small parts washers are versatile tools that can handle a range of tasks beyond just cleaning small parts. In repair shops, tools often become coated with grease, oil, lubricants, and dirt. While hand-cleaning with a cleaner may be manageable for a few tools, it quickly becomes labor-intensive when dealing with large quantities. Small parts washers provide an efficient alternative, automating the cleaning process and saving time and effort.
Small parts washers are designed to clean both tools and parts effectively. They typically feature a basket or tank where tools are immersed in a cleaning solvent. Using methods such as helix rotation, agitation, or spray nozzles, these washers apply solvents and detergents to remove contaminants from tools efficiently and with minimal effort. Compared to manual cleaning, small parts washers offer a far superior level of cleanliness and convenience.
Most parts washers are automatic or semi-automatic, operated by computer systems that manage the loading, washing, rinsing, drying, and unloading processes. This automation enhances convenience and efficiency, allowing personnel to focus on other tasks while the parts are being cleaned.
Automatic parts washers come in various configurations, including those integrated into assembly lines and standalone models. Production line washers differ in size based on cleanliness requirements and the number of processing stations. Parts are introduced into the system via metal mesh conveyors or monorail systems, where they are placed in baskets, hung from hooks, or transported using other methods.
Automatic parts washers incorporate various cleaning methods, including immersion, agitation, rotary, and spray, with spray being the most prevalent. These automated systems are designed to integrate seamlessly into manufacturing processes, allowing parts to be mechanically machined and transferred directly into the washer without manual intervention. This design enhances efficiency and reduces production time.
The introduction of CNC systems and PC software has significantly boosted production efficiency by synchronizing machining and cleaning processes. Previously, cleaning procedures were conducted separately, but modern automated parts washing systems can be designed to handle multiple processes in a single unit. These advanced systems integrate various cleaning stages into one machine, allowing for a seamless workflow with multiple stations.
Automated parts washing systems do have size limitations for the parts they can handle. Typically, parts are loaded into the system using gantry or robotic delivery methods, and then transported through the various computer-controlled stations via a conveying system. Similarly, unloading is managed by automated mechanisms that move the parts to their next processing stage.
Despite its seeming obsolescence, manual parts washing remains essential in certain situations. A key consideration in manual parts washing is safety, as the chemicals used can be hazardous. Essential safety measures include wearing safety glasses that fully protect the eyes and durable, heavy-duty rubber gloves to safeguard the hands.
Modern manual parts washing has evolved from the traditional basin and drum methods, incorporating high-pressure sprayers that greatly reduce cleaning time. Despite these advancements, safety remains a critical concern. Modern setups often include dedicated cabinets or enclosures designed to contain overspray and protect users.
Most chemicals used in manual parts washing are water-based and biodegradable, minimizing environmental impact and damage. However, safety precautions remain essential. Regardless of the cleaning method—spray, immersion, or agitation—proper training and preparation are crucial to ensure safe and effective operation.
Manual parts washers are the most cost-effective type of parts washing equipment, typically used for occasional cleaning of complex or intricate parts. Manual methods include soaking, brushing, heated fluids, spraying, directed streams, and fluid agitation. Immersion is commonly used in manual parts washing to ensure thorough cleaning.
Aqueous parts washers use water combined with various water-soluble cleaners as their primary cleaning agents. They are widely used due to their environmentally friendly nature. Unlike petroleum-based cleaners, aqueous solutions are non-flammable, making the washing process safer and less hazardous. These washers use heat, agitation, and pressurized water to break down dirt and contaminants into small particles for easier removal.
Aqueous parts washers come in various types, including immersion, spray, conveyor belt, and ultrasonic washers. Each type features a filtration system to remove dirt particles broken down during the cleaning process. For oil removal, oil skimmers are used to extract free-floating oil from the cleaning solution, enhancing its effectiveness and prolonging the life of the parts washer.
Carousel parts washers use a cleaning system similar to conveyor parts washers but are designed with a smaller footprint. They are ideal for production operations requiring precision cleaning at higher production rates. In a carousel parts washer, parts are both loaded and unloaded at the same location, in contrast to conveyor systems where parts are loaded at one end and unloaded at the opposite end.
Carousel parts washers operate on a design similar to a rotating barrel. The open side of the barrel allows for easy loading of parts, while the interior features a rotating carousel that moves parts through each step of the cleaning process. Depending on the design, the carousel may include anywhere from 3 to 16 steps, each indexed to ensure sequential processing for optimal cleaning and drying. Users can adjust the rotation speed, timing, number of steps, and treatment durations to tailor the system to the specific cleaning requirements of the parts being processed.
One design of carousel parts washers integrates the conveyor system with the carousel process. In this design, the enclosure maintains the barrel shape, but parts are loaded and unloaded onto a conveyor that moves through each stage of the carousel cleaning process. This hybrid approach combines the efficiency of a conveyor system with the multi-stage cleaning capabilities of a carousel, allowing for continuous and streamlined processing of parts.
A chain mesh parts washer is a type of conveyor parts washer that continuously cleans parts as they move through multiple stages. Parts are transported on a chain mesh belt and cleaned by high-pressure jet sprayers that apply a cleaning solution to effectively remove dirt and grime. Typically used in assembly processes, chain mesh parts washers are engineered to handle specific parts and are particularly well-suited for aqueous cleaning because the cleaning solution can flow through the mesh, allowing for efficient recirculation and retrieval. Designed for high-volume cleaning, these washers can be easily customized to accommodate different parts and cleaning requirements.
Chain mesh parts washers come in various styles, including those with fixtures and those designed to transport pallets through the cleaning process. Pallet chain mesh parts washers enhance assembly operations by efficiently shuttling pallets of parts between workstations. These systems can be integrated to not only clean palletized parts but also flush empty pallets, improving overall efficiency and workflow in the production environment.
Planning a chain mesh parts washing system involves careful consideration of cell layout, cycle times, and methods for transferring pallets, which may include forklifts or automated systems. The effectiveness of a chain mesh parts washer hinges on the precise transfer of parts and alignment of line speed with production operations to ensure seamless integration and efficiency.
Tumble parts washers are designed to handle large volumes of small parts efficiently. The tumbling action, combined with jet sprayers that blast tempered water, effectively cleans dirt, grime, and reaches hollow areas and hidden corners. While tumbling is a key feature, these washers can also accommodate parts in covered racks or specialized fixtures, offering flexibility and adaptability for varying cleaning needs.
Tumble parts washers incorporate features common to other parts washing systems, such as storage tanks for recirculating water and rinse tanks. Some models also include an additional tank for heavily soiled parts needing extra cleaning. These washers can integrate multiple cleaning stages, including spraying, immersion, and ultrasonic cleaning, which can be used in any sequence to optimize the cleaning process.
Metal parts washers are essential for industries handling metal components, offering a convenient and effective way to clean parts. This not only enhances their appearance but also protects them from environmental degradation. Metal parts washers come in a variety of types, including cabinet-style and long conveyor models, each providing an economical and efficient solution for cleaning metal parts.
Petroleum-based solvent parts washers are widely used for metal parts cleaning due to their exceptional ability to remove tough grease, grime, dirt, and contaminants. However, despite their effective cleaning performance, these washers are hazardous and toxic. Their use requires careful consideration and stringent safety precautions to mitigate the associated risks.
Water-based cleaners have become increasingly popular for metal parts cleaning due to their safety, non-toxicity, and non-flammability. They provide effective cleaning similar to petroleum-based solvents but with fewer hazards. Various types of water-based parts washers are available, including ultrasonic parts washers, which are particularly well-suited for delicate or fragile parts.
In essence, there is a suitable metal parts cleaner for every application. Choosing the right metal parts washer requires careful consideration of several factors: the type of parts to be cleaned, the available space for the parts cleaner, the desired cleaning quality, and how the cleaner will integrate into the existing operation or process.
Industries that work with various types of parts rely on parts washers, particularly those dealing with metal parts. In fabrication processes where parts can become contaminated, parts washers are essential for cleaning items such as fasteners, bolts, nuts, screws, bearings, gearboxes, and assemblies.
The automotive industry relies heavily on parts washers due to the nature of their products. Essential automobile components involve oil, gas, grease, and various lubricants that can contaminate and dirty parts. To effectively assemble and repair vehicles, parts washers are crucial for cleaning components during assembly and diagnosing issues during repairs.
In various industrial environments, equipment is often exposed to dirt and contaminants, making regular maintenance crucial for successful operation. This includes examining, checking, and cleaning parts, components, and assemblies. Parts washers play a key role in this process by allowing for the thorough inspection of defective parts to determine if they need replacement or repair. Efficient parts washers help ensure that repairs are performed properly, aiding in getting equipment back into optimal working condition.
The effectiveness of an army hinges on the rapid and reliable movement of troops, necessitating a fleet of vehicles ready for immediate action. To maintain operational readiness, every vehicle in the motor pool—whether trucks, Humvees, troop carriers, or jeeps—must be in peak condition. Parts washers are crucial in ensuring that all vehicles are thoroughly cleaned and maintained, keeping them ready for any situation.
Cabinet parts washers are widely utilized in the food industry for cleaning equipment, dishes, tools, and bowls. They enable the loading of various cooking items into a single washer and complete the cleaning process in one cycle. Ideal for low-volume needs, cabinet parts washers efficiently serve the food industry by streamlining the cleaning of kitchenware and utensils.
Parts washers are highly efficient for the medical instrument industry, which demands rigorous cleaning standards and regulations. Various types of parts washers, including immersion, spray cabinets, and ultrasonic models, are employed to meet these stringent requirements. Each type is well-suited for the delicate cleaning needs of medical devices and instruments.
What are some common accessories for parts washers, and how do they enhance the functionality of different types of parts washers? Are these accessories necessary from the beginning, or are they typically added after extended use?
Solvent filters are designed to extend the life of cleaning solvents by removing oil, grease, and other contaminants from them. This filtration process allows solvents to be reused multiple times, reducing costs and ensuring a continuous supply of clean solvents.
Parts washers are typically equipped with containers such as baskets and racks to organize and separate parts during cleaning. However, these containers can wear out or become damaged with extended use. Fortunately, manufacturers offer a wide range of replacement baskets and racks to ensure continued effective operation.
Work shelves serve multiple purposes in parts washers, including the storage of parts, providing extra space in certain models, and acting as replacements for worn shelves. Constructed from heavy-gauge steel, these shelves feature a robust metal frame for durability.
Sludge trays are designed to collect and contain residue such as grime, oil, and grease that settles at the bottom of the washing tank. This keeps the sludge away from cleaned parts, ensuring a more efficient cleaning process.
A degreaser is a powerful solvent cleaning system used with parts washers to effectively cut through grease and oil buildup. The term "degreaser" encompasses a range of products, including precision cleaners, maintenance cleaners, and carb cleaners, all designed to remove contaminants quickly and efficiently without mechanical devices or scrubbing. While petroleum-based degreasers are common, water-based degreasers are often preferred for their safety and ease of use. Degreasers are suitable for use with immersion cleaning systems and batch cleaners. Specialized types, such as ultrasonic and vapor degreasers, offer automated, repeatable cleaning processes ideal for critical applications like medical equipment and aerospace components.
A wastewater evaporator transforms water into vapor, leaving contaminants behind. This process utilizes thermodynamics by heating the wastewater to convert it into vapor. A blower then removes the water vapor from the system. Wastewater evaporators are used with parts washers to effectively separate water from contaminants collected during the cleaning process.
In modern industrial processes, which often involve lubricants, oil, grease, and other substances, cleaning parts is essential. After production, it's crucial to remove these residual materials. Parts washers provide a safe and efficient solution for this task by utilizing water, heat, agitation, and environmentally friendly chemicals.
Parts washers eliminate the need for manual labor in the cleaning process. Typically, human involvement is required only after the cleaning is finished. The entire process—handling, cleaning, rinsing, and drying—is carried out safely and efficiently by the parts washer.
Parts washers are capable of cleaning any type of part or component, no matter its size or complexity. Their diverse solutions and cleaning systems can access the most remote and intricate areas to remove contaminants. The primary limitation of parts washers is the size of the enclosure needed for the parts being cleaned.
A parts washer provides manufacturers with complete control over the entire production process of a part, from machining to final completion. This enhances quality assurance and ensures that production standards are consistently met.
Modern production methods demand meticulous attention to detail. By automating the cleaning process with a parts washer, manufacturers can initiate cleaning tasks without requiring constant worker oversight. This automation boosts individual productivity and efficiency, allowing personnel to focus on more critical and essential tasks.
Purchasing a parts washer may appear to be solely about achieving an efficient cleaning process. While this is a key benefit, acquiring a parts washer can also enhance overall processing, improve operational efficiency, and reduce costs associated with malfunctioning or damaged parts.
Proper handling and maintenance of a parts washer are crucial for its optimal performance. Neglecting these aspects can impair the washer's ability to clean parts effectively and accurately. Maintenance involves a thorough examination of the parts washer and all its components. This is especially important for petroleum-based solvent parts washers, which require more frequent upkeep.
Proper handling and maintenance of a parts washer are crucial for its optimal performance. Neglecting these aspects can impair the washer's ability to clean parts effectively and accurately. Maintenance involves a thorough examination of the parts washer and all its components. This is especially important for petroleum-based solvent parts washers, which require more frequent upkeep.
Proper handling and maintenance of a parts washer are crucial for its optimal performance. Neglecting these aspects can impair the washer's ability to clean parts effectively and accurately. Maintenance involves a thorough examination of the parts washer and all its components. This is especially important for petroleum-based solvent parts washers, which require more frequent upkeep.
Every parts cleaning system has specific loading guidelines that must be followed to ensure optimal performance. Overloading or forcing parts into the washer to accelerate the process can result in decreased quality and performance.
For oil-based contaminants, such as cutting fluids or coolants, a hydrocarbon cleaning process is ideal. For water-based contaminants, like grinding or lapping compounds, an aqueous cleaning method is more effective. Choosing the right cleaning solution is crucial for achieving optimal cleanliness and reducing cycle times.
Humans can unknowingly transfer contaminants like oils, skin cells, and hair, which can hinder the performance of parts washers. To minimize this risk, operators should wear hairnets, lint-free gloves, work coats, and bodysuits. This protective attire not only shields them from harmful corrosive wash materials and chemicals but also prevents interference or contamination of the parts being cleaned.
An aqueous part washer is an automated or semi-automated machine manufactured to clean, remove tough grease, and dry large or small parts before distribution or surface treatment. The washing is necessary since...
Automated parts washers are mechanical devices designed to efficiently remove grit, oil, grime, dirt, paint and other contaminating substances from parts with minimum manual supervision. These substances are removed...
A parts cleaner is a cleaning device that uses various types of solvents, cleaning agents, and processes to remove grease, grime, and contaminating materials from manufactured parts prior to shipment or movement for further processing...
A parts washer is a mechanical device designed to remove grit, grime, oil, miscellaneous debris, dirt, paint, and other contaminating substances from parts in preparation for their use in assembly operations, packaging, or coating...
A wastewater evaporator is a method of removing water from water-based waste by converting the water in the waste to a vapor and leaving contaminants. The function of a wastewater evaporator is to reduce the volume of waste materials...
Industries worldwide utilize abrasive blasting for various purposes, including cleaning rust and oil, removing surface coatings like paint and pollutants, preparing surfaces for paint and coatings, reinforcing metal surfaces and...
Deburring is a secondary operation of a machining process that enhances the final quality of the product by removing raised edges and unwanted pieces of material, known as burrs, left by the initial...
Finishing machines are machines used for metal finishing, which is the last stage of the metal fabrication process; the stage encompasses the use of machines in finishing the metal surface...
Sandblast cabinets include systems or machinery and components for projecting blast media against a part‘s surface to abrade, clean, or modify the surface. Sand, abrasive, metal shot, and other blast media are driven or propelled using pressurized water, compressed air, or a blast wheel...
Sandblasting equipment includes systems or machinery, and components for projecting blast media against a part‘s surface to abrade, clean, or modify the surface. Sand, abrasive, metal shot, and other blast media are driven or propelled using pressurized water, compressed air, or a blast wheel...
Shot peening equipment includes systems or machinery and components for projecting shot peening media against a part‘s surface to modify the surface or surface engineer the part...
A tumbling machine is a durable deburring and metal-polishing machine designed for finishing large parts or batches of smaller parts. A tumbling machine is also known as a barreling machine or a mass-finishing...
An ultrasonic cleaner is a type of sonic cleaner or sonic cleaning machine that uses cavitation to remove unwanted material. The cleaning effect is created by the compression and refraction of a cleaning medium. Miniscule vibrations propagate throughout the...
Ultrasonic cleaning is a type of cleaning process which uses cavitation induced by alternating compression and rarefaction cycles at ultrasonic frequencies. Ultrasonic frequencies are sound waves vibrating at 20 kHz or higher...
Vibratory tumbler is the equipment used in a vibratory finishing process, one of the most common methods in mass finishing. But how does a vibratory tumbler work...