Perforated Aluminum
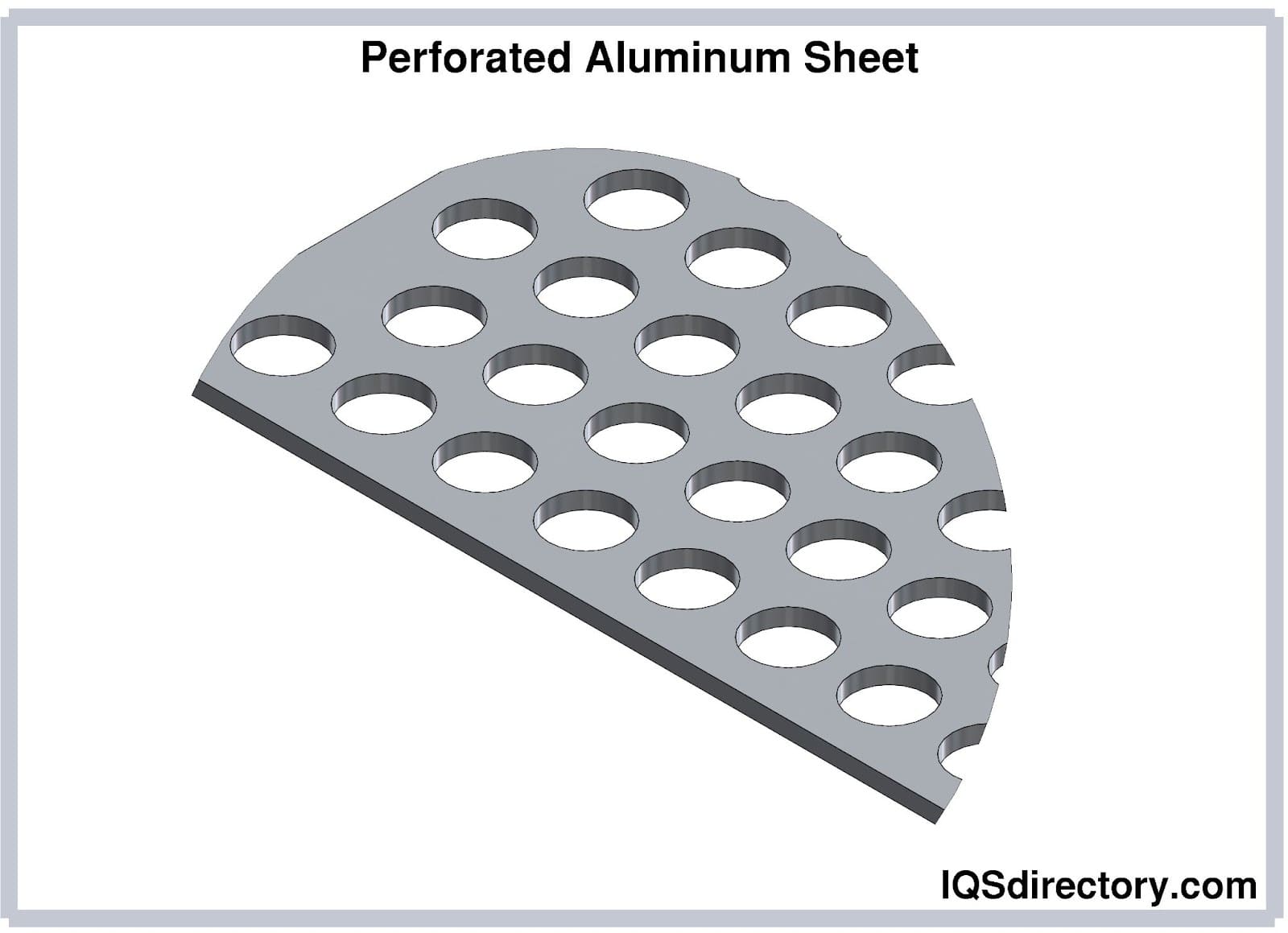
Perforated aluminum consists of an aluminum sheet which has been manually or mechanically pierced or punched using CNC (computerized numerical control) technology in order to produce shapes and patterns of various sizes...
Please fill out the following form to submit a Request for Quote to any of the following companies listed on Perforated Stainless Steel .
This article will give a detailed discussion on stainless steel perforated sheets.
After reading, it is anticipated that one should comprehend the following:
Perforated stainless steel sheets are produced through cutting, punching, or stamping techniques to form specific patterns of holes or apertures. These sheets have dual purposes: they serve functional needs like filtration and ventilation, as well as aesthetic uses such as architectural embellishments.
Aside from their aesthetic charm, perforated steel sheets provide a range of practical advantages. They allow light to pass through while offering an efficient screening solution. Furthermore, these sheets are used for reducing noise levels, contributing to a quieter, more comfortable environment. In architectural contexts, perforated steel sheets are frequently used as decorative components. They are also critical in industries like acoustics, food and beverage processing, chemicals, and energy, where they facilitate effective fluid filtration.
The primary factor to consider when choosing a perforated steel sheet is the specific application for which it is intended. A deep understanding of the product's particular needs and tasks significantly impacts other considerations during the selection process.
Perforated materials come in various base substrates, each offering unique properties suitable for diverse applications. Many suppliers offer options, but some of the most common materials used include:
Perforated steel sheets are available with a range of hole sizes and configurations. The cost is influenced by factors like the base material's thickness and hardness, the hole sizes and spacing, as well as production costs.
Perforated stainless steel sheets are available in various dimensions, with common sizes detailed below:
Perforated stainless steel products are created from 15 different grades, each offering resistance against bacteria, rust, and corrosion. These grades present in finishes such as matte, satin, brushed, reflective, rough, and abrasive. The perforations can be round, square, oval, triangular, diamond, hexagonal, slot, star-shaped, or tailored to custom designs, enabling the creation of intricate and visually appealing patterns.
There are two primary methods for perforating stainless steel sheets, chosen based on the design's complexity. Both techniques begin by feeding the stainless steel sheets into a punching press:
For creating non-repetitive holes, this process is often completed using CNC machines, which slide the sheet beneath a fixed punching ram.
The initial phase in creating perforated stainless steel sheets involves selecting high-quality, thin, flat stainless steel sheets that can be cut, bent, shaped, or otherwise processed to meet exacting project demands. These sheets are commonly made from grades such as 304 or 316 stainless steel, which are prized for their durability, corrosion resistance, and ease of fabrication. Stainless steel sheets are measured in gauges, with a higher gauge number signifying thinner material. Selecting the proper sheet thickness is critical for manufacturability and overall product performance in industries such as architecture, automotive, food processing, and filtration.
The pattern of perforated steel sheets or perforated metal panels is determined by their intended application, with options available in both standard and custom designs, and a variety of sizes, shapes, and hole arrangements. Common patterns include round holes, square holes, slotted holes, decorative designs, and custom geometric configurations. The effectiveness and functionality of these sheets are also influenced by the required strength, specific use, and the hole configuration. For example, round hole perforations maximize open area and air flow for ventilation and acoustic control, while staggered or custom patterns can deliver enhanced filtration or aesthetic appeal in architectural metal cladding.
In the decision-making process, both hole and bar sizes are carefully considered. The spaces between the holes are referred to as bars. The strength of the perforated stainless steel sheets for a given application relies heavily on achieving the right balance between holes and bars, which affects the sheet's structural integrity and load-bearing capacity. As the size of the holes increases, the bars become narrower. Typically, the thickness of the steel sheet should not exceed the diameter of the holes or the width of the bars. Adhering to these guidelines helps prevent tool failure during processing and ensures consistent quality in large-scale manufacturing projects such as industrial enclosures, screening, and filtration systems.
All-across perforating presses are capable of delivering up to 1600 punches per stroke quickly and accurately, making them highly efficient for producing perforated metal sheets. This perforation method is the fastest, most cost-effective, and ideal for large-scale projects requiring high-speed production, such as in industrial manufacturing, HVAC systems, and architectural façades. It is suitable for materials ranging from 0.002 inches to 0.25 inches thick and can handle workpieces wider than 60 inches. The all-across method can produce thousands of holes per minute, with the capability to perform up to 600 strokes per second, offering exceptional throughput and consistent pattern accuracy.
Unlike a wide punch press, which operates across the entire sheet, the XY axis punch press moves across the sheet to create symmetrical holes in sections. This method allows for the creation of intricate patterns without repetitive designs, making it ideal for custom perforated metal and small-run jobs that require flexibility in hole arrangement and design. Computer-controlled XY axis punches enable the fabrication of complex, high-precision patterns for demanding applications like custom screens, security panels, and decorative metalwork, where design requirements are unique and tolerances are tight.
Laser perforation is the most precise method for producing perforated steel sheets, allowing for the creation of intricate geometries with exact dimensions. This technique involves repeatedly and accurately burning small holes, leaving a reinforced ring around each cut. There are two main types of lasers used: CO2 lasers, which utilize a gas-based system for cutting, and fiber lasers, which employ a high-powered laser transmitted through optical fiber. Laser cutting is highly valued in the production of demanding components such as fine filters, precision screens, and advanced architectural panels due to its high level of accuracy, minimal material distortion, and flexibility in hole size and placement.
Plasma cutting involves generating an electric arc between a steel sheet's surface and a gas expelled from a nozzle. This electric discharge heats the plasma to slice through the steel, making it well-suited for thicker gauge stainless steel sheets and heavy-duty industrial applications. The plasma cutting process is capable of handling steel sheets of any thickness and achieves cutting speeds of up to 20 meters per minute, offering excellent speed, productivity, and cut quality for fabricating parts in the construction, shipbuilding, and heavy machinery sectors.
Steel sheets can be sliced into patterns using waterjet cutting, which employs water under high pressure. The two types of waterjet cutting are pure water with no additives, and an abrasive with grit added. Water is blasted through a nozzle to cut detailed designs in steel sheets. Robotic guiding is built into the water jet-cutting delivery system to provide accurate and precise cuts. It is a cold-cutting technique that removes material from steel sheets by eroding it with water-soluble particles, making it ideal for cutting heat-sensitive stainless steel grades and reducing the risk of material distortion. Waterjet technology is frequently utilized in the creation of precision architectural panels, custom perforated screens, and sensitive components for the aerospace and automotive industries.
Nibbling is a manufacturing process where steel sheets are repeatedly punched to cut and shape them. This technique utilizes an electrohydraulic motor in a nibbling machine to achieve precise cuts. Nibbling machines are versatile and can perform various tasks, including punching, slot cutting, and creating rectangular patterns, especially for prototypes, repair work, or complex custom fabrication requiring non-standard hole shapes and patterns. As such, nibbling is popular in industries where design flexibility and low-volume production are needed.
Throughout the perforation process, stainless steel sheets of all gauges tend to curl and must be leveled. Various leveling techniques are employed, including rolling machines and straightening presses. While automated machines can perform leveling efficiently, manual methods are also utilized, though they require skilled operators to ensure accuracy. Leveling is essential to produce perfectly flat perforated metal sheets, which are crucial for fabrication consistency, easy installation, and reliable product performance in end-use applications such as enclosures, panels, and screens.
Most stainless steel perforation manufacturers depend on the precision and accuracy of leveling equipment, which offers highly accurate tolerances and completes the task in minimal time. Ensuring flatness also helps to improve the finish and aesthetic quality, which is especially important for architectural and decorative applications.
Once perforated, stainless steel sheets might require additional processing or value-added procedures to enhance their functionality or better prepare them for their intended use. Depending on their capabilities and standards, perforating companies offer various value-added services. These can include shearing (cutting sheets to specified sizes), edge finishing, forming, and custom packaging. Below are descriptions of two such processes: welding and bending, and powder coating.
Perforated steel sheets are commonly used to make filter tubes, exhaust components, and structural supports. The process involves rolling the sheets into a tube shape using a machine, with the ends of the sheet welded together to complete the tubing. Welding ensures seamless joints and structural integrity, which are vital for products exposed to high pressures or demanding environments, such as in filtration, agriculture, and petrochemical industries.
Perforated steel sheets are bent according to the specific requirements of their application. Modern computer design software accurately determines the desired angle, which is then replicated by a hydraulic machine. The bending process involves clamping the sheets between upper and lower dies, allowing for bends up to 120°. This flexibility supports diverse uses, from ventilation grilles and balustrades to machine guards and conveyor belt systems.
Powder coating adds a thin polymer layer to stainless steel, enhancing not only its strength and resistance to corrosion, abrasion, and chemicals but also its visual appeal. The process begins with cleaning the stainless steel sheets, followed by passivation to remove surface layers and blasting to prepare the surface. Next, a primer is applied, and the powder coating is then applied using an electrostatic charge. Powder coating provides a uniform, durable finish and is available in a wide range of colors and textures to meet project-specific requirements in industries like architecture, signage, and industrial design.
When selecting perforated stainless steel sheets for your project, consider the material grade, hole pattern, thickness, and surface finish based on performance requirements and industry standards. For projects demanding superior corrosion resistance, such as food processing or marine environments, 316 stainless steel is recommended. For general fabrication, filtration, and architectural metalwork, 304 stainless steel often provides an effective and cost-efficient solution. Consult with experienced perforated metal suppliers to determine ideal sheet dimensions, open area percentage, and value-added services such as custom cutting, forming, and finishing.
If you require custom perforated stainless steel sheets, reach out to trusted manufacturers who offer engineering support and CAD design capabilities. This ensures precise pattern creation, optimal fit, and best-in-class durability for your intended use. Knowing production processes and available finishing options allows you to make informed decisions, helping you select the right product for maximum efficiency, aesthetic appeal, and long-term value in your application.
Stainless steel perforating machinery is essential for producing high-quality perforated metal sheets, widely used in industries such as architecture, automotive manufacturing, HVAC systems, filtration, and construction. In the United States and Canada, top manufacturers offer advanced stainless steel perforating machines designed for enhanced productivity, superior accuracy, and versatile application. These machines enable the production of stainless steel perforated sheets, panels, and custom components for a range of projects, optimizing both design flexibility and product performance. Below, we explore some of the most innovative and in-demand stainless steel perforating machines available in today's market for metal fabrication professionals and industrial manufacturers.
Features: The Trumpf TruPunch 3000 series is renowned for its precision engineering, high-speed operation, and adaptability. This CNC turret punching machine delivers exceptional results for stainless steel perforation, supporting a variety of tooling options to achieve diverse hole shapes, sizes, and patterns. Notable for its automatic tool changer and intelligent programming interface, the TruPunch 3000 enhances sheet metal productivity, reduces processing time, and minimizes material waste. Its advanced automation features make it an optimal choice for manufacturers focused on scalability and consistent quality in perforated stainless steel sheet production.
Features: The Amada AE-2510NT series offers superior hydraulic punching technology with efficient sheet handling and automated tool change capabilities. Known for its energy-efficient operation and fast cycle times, this machine enables precise patterns in stainless steel sheets while supporting complex and custom design requirements. The advanced control system allows for easy integration within modern manufacturing facilities, making it a preferred option for large-scale perforated metal production, metal panel fabrication, and high-volume, high-precision applications.
Features: The Finn-Power C5 series combines reliability, durability, and versatility for stainless steel punching and perforation. With high-torque hydraulic units and robust automation solutions such as automatic sheet loading and unloading, the C5 series maximizes production throughput for sheet metal fabrication shops. This machine is ideal for fabricators focused on productivity, flexibility, and the manufacture of perforated stainless steel components used in commercial, industrial, and decorative applications.
Features: The Murata Motorum 2048EZ stands out as a servo-driven turret punch press providing high-efficiency processing and pinpoint accuracy for stainless steel perforation projects. Its dependable ram system and a broad selection of precision tooling facilitate the creation of intricate and uniform perforation patterns. Enhanced with energy-saving systems and a straightforward user interface, the 2048EZ is frequently chosen for custom perforated metalwork, industrial filtration, HVAC screens, and architectural cladding.
Features: The LVD Strippit PX-series boasts rugged construction and unparalleled performance for stainless steel perforating operations. Its hydraulic punching technology enables consistent, clean perforations in sheets and panels of varying thicknesses, supporting applications from decorative metal panels to functional industrial components. With minimal maintenance requirements and user-friendly controls, the PX-series is a popular choice for manufacturers specializing in custom stainless steel perforated panels and precision sheet metal fabrication.
When selecting the right stainless steel perforating machine for your facility, consider factors such as sheet thickness capability, automation features, punching force, and compatibility with different alloy grades. Whether you require small or large perforated metal runs, these industry-leading machines enable builders, architects, and OEMs to produce high-quality, customized stainless steel perforated sheets and components to precise specifications.
Staying informed about the latest stainless steel perforating machinery technology and advancements is crucial, as industry standards and product offerings continue to evolve rapidly. For expert advice or tailored solutions for your sheet metal fabrication project, always consult directly with machinery manufacturers or qualified industry suppliers. Their knowledge will help you choose the most efficient and appropriate metal perforation equipment for your unique business needs.
There are two main types of round hole designs: staggered and straight. In straight designs, the holes are aligned in parallel rows, whereas staggered designs feature holes arranged in a non-linear pattern. There are three options for the sheet's edges: finished, unfinished, and blank. Finished edges are smooth and complete, while unfinished edges are left solid. With blank margins, the round perforations extend all the way to the edge of the sheet.
Square hole perforations offer a contemporary look and create a significant amount of open space due to their linear arrangement. Steel sheets with square holes come in a variety of designs, sizes, and patterns. These sheets can be stacked either in a straight alignment or in a staggered configuration.
Slotted perforated steel sheets are characterized by elongated holes with either round or square ends, arranged in staggered or straight patterns. A slotted die is used to create these holes. These sheets are remarkably strong for their weight and allow for the passage of liquids, light, and sound. The diameter and length of the slots can vary depending on the die used.
Perforated plates, perforated screens, and punch plate screens are only a few of the various names for punch plates. Punch plates are made from solid steel sheets that are then CNC-perforated to produce perforated metal sheets that are fabricated into a completed product. Punch plates are made from stainless steel sheets that have been CNC-perforated into perforated metal sheets before being formed into a final product. Machines in the recycling and quarrying industries have punch plates or perforated screens installed.
Decorative perforated steel sheets are used as architectural accents to enhance aesthetic appeal. Designed to meet specific building layout requirements, they come in a variety of shapes and patterns. By modifying the pattern die, these sheets can be customized to improve their appearance and adapt to any application.
Hexagonal or honeycomb perforated steel sheets are ideal for architectural designs requiring continuous airflow, as they offer maximum open space. These sheets provide several advantages, including a high strength-to-weight ratio, an attractive appearance, and straightforward production. In the hexagonal pattern, each hole is staggered so that the center of one hole aligns with the edge of the adjacent hole. This design is commonly used in load-bearing architectural elements such as roofs, facades, fences, steps, and walkways.
Perforated type 304 stainless steel sheets are highly valued for their heat resistance and corrosion resistance, making them suitable for both interior and exterior applications. These sheets are widely used across various industries, including automotive, pharmaceutical, medical, and petrochemical. They serve diverse purposes such as filtration, sterilization, flooring, and architectural infill panels.
Perforated tubes are utilized for their strength and pressure resistance in applications such as filter flow, support, and filtration. Perforated steel sheets with micron-sized openings are effective in filtering materials like coal and gravel. The process begins with using various steel sheets to manufacture perforated tubing, incorporating carefully planned perforations to provide the necessary support. The holes are then customized to meet the specific requirements of the application.
Perforated stainless steel panels feature holes or perforations and can have varying sizes of holes distributed across the entire panel or within specific panel ribs. These panels are commonly used to enhance light and ventilation, as well as to provide sound absorption. Due to these benefits, perforated stainless steel panels are often utilized in applications such as soffits, gymnasiums, equipment screens, and structures like parking garages.
Perforated tubes are used in filtration and exhaust systems to capture hazardous particles and dust. Due to their resistance to pressure and capacity to maintain their shape under the constant pressure of filtering systems, perforated tubes are favored over other materials. Perforated stainless steel sheets are used as cores in filtration systems to support and catch impurities.
Liquid: Perforated steel sheets are utilized in various applications for liquid filtering, including hydraulic systems, fuel and oil filtration, lubricant systems, and food and beverage processing.
Hydraulic: In hydraulic systems, perforated steel sheets help purify hydraulic fluid, ensuring smooth operation of machinery.
Oil: Perforated tubes are essential in oil filtration systems, where they separate valuable materials from waste and impurities. On oil rigs, these tubes filter out contaminants such as sand and grit from crude oil.
Drainage: Large-scale drainage systems for infrastructure projects like dams, bridges, and barriers use perforated tubes to prevent debris from entering sewage systems.
Speaker grills protect sensitive equipment from pollutants while allowing sound to pass through. This includes devices such as loudspeakers, hearing aids, and telephones. To ensure durability and withstand heavy use, speaker grills must be made from materials that are resistant to vibration and weather. Expanded or perforated steel sheets are commonly used to manufacture these grills.
Perforated steel sheets are used for the walls and floors of grain dryers to allow air circulation, helping to keep the grain safe and fresh. This ventilation system ensures a steady flow of air, facilitating rapid and thorough drying. Additionally, the perforated flooring in grain bins promotes airflow, which helps prevent bacterial growth and seed germination.
Perforated steel sheet guards serve as covers to keep leaves and other large debris out of gutters. These gutter guards have a robust surface with numerous small holes spaced closely together. They are designed with a steep edge to ensure a secure fit within the gutter, lying flat beneath the eaves to provide effective protection.
Backlit panels are used in architectural design to highlight the structure of a surface and create a dramatic effect by making surrounding materials stand out. These panels provide uniform illumination, have a low profile, and seamlessly blend with their environment. For instance, a perforated panel illuminated from behind can create a striking visual effect, enhancing its aesthetic appeal.
Perforated steel sheet barriers can transform an ordinary room into a distinctive and captivating space. These barriers effectively divide large areas while preserving an open, inviting atmosphere and enhancing visual appeal. Their design, shape, and configuration can be customized to fit various spatial and dimensional needs. Additionally, their lightweight and flexible nature makes them easy to move or store.
Designing perforated steel sheet fences involves several factors, including panel sizing, creating panels that fit between posts, precise production, and custom fitting. One of the main advantages of perforated fencing is its aesthetic appeal, which enhances the visual interest of otherwise conventional fencing. To prevent rust and flaking, environmental finishing is applied during manufacture. Additionally, the perforated design disrupts wind currents while allowing for open airflow.
Sunscreens and sun shades offer multiple benefits beyond just protecting against the sun's rays. They help reduce energy costs by minimizing the need for air conditioning and lighting while allowing a soft, natural light to filter through, creating a pleasant ambiance. Similar to perforated fences, sun shades also reduce airflow, which can lessen wind and rain noise. They enhance privacy and deter intrusions. Additionally, sun shades act as a protective barrier against the elements, reducing the need for exterior maintenance and repairs.
Construction of electronic enclosures must adhere to strict guidelines for electromagnetic (EMI) and radio frequency (RFI) interference. Most of the data in electronic enclosures are costly, prone to disturbance, and unsightly. Perforated enclosures offer protection from EMI and RFI interference and airflow to prevent electronics from overheating. Perforated panels are perfect for storing bulky, heavy electronics since they are composed of strong, long-lasting materials.
Stainless steel perforated sheets are used as handrail guards, offering both enhanced safety and visual appeal. The perforations in the sheets provide privacy while still allowing light and air to pass through, making them a preferred choice for pickets and other railing styles. Key benefits of perforated steel sheet panels include their strength, ease of maintenance, and attractive appearance.
Perforated steel sheets have various applications in agriculture. Farm equipment used for digging, planting, spraying, harvesting, and threshing generates dust and debris that can clog engines. Perforated steel sheets are utilized in the form of screens, exhaust system guards, and radiator grilles to protect machinery from damage caused by foreign objects.
Bins and hoppers are lined with perforated steel sheets for grain storage and protection, promoting aeration for grain drying. Cornmeal, wheat flour, seeds, and pet food are all ground in hammer mills using perforated steel sheet screens and parts.
Modern appliances require effective air and water filtration to maintain optimal performance and protect against contaminants. Perforated steel sheets play a crucial role by ensuring a consistent flow of air and light, supporting filtration substrates, preventing overheating, and protecting against moisture buildup. They also contribute to the safe operation of appliances.
Food production requires stringent sanitation and cleanliness standards, along with materials that can withstand high temperatures. Perforated steel sheets are used in processes such as heating, steaming, and cleaning. They also provide an effective environment for removing unwanted contaminants from corn, grain, seeds, rice, and legumes during thorough cleaning and pre-cleaning operations.
Perforated steel sheets are essential for removing impurities during the intensive cleaning process and provide an efficient method for storing and drying processed food. Pre-cleaned food is more stable and better prepared for storage.
In the automotive industry, perforated steel sheets are used to enhance strength without adding extra weight to vehicles. They are commonly employed as mufflers and radiator guards to prevent debris from obstructing exhaust and engine systems. By allowing airflow, these sheets support engine components while protecting the engine and exhaust systems. Additionally, perforated steel sheets are used on both the exterior and interior of cars to provide soundproofing, helping to reduce engine and exhaust noise.
Perforated steel sheets are an elegant and hygienic choice for store fixtures and displays. They allow for a steady flow of air, keeping products looking fresh and new. Their versatility is another advantage, as businesses can easily rearrange perforated displays to suit different products and purposes. These displays are permanent, durable, strong, lightweight, and easy to install and assemble. Additionally, the aesthetic qualities of perforated steel sheets enhance a store's appearance and ambiance while boosting brand visibility.
The medical sector demands products with exceptional functionality and durability. Perforated steel sheets provide reliable, precise, and efficient support for various medical applications. They are utilized in test chambers, ventilation hoods, cadaver and autoclave trays, and test tube holders. These sheets are made from materials that are resistant to chemicals, offer continuous filtration of gases and liquids, and can withstand rapid temperature changes.
Perforated steel sheets are widely used in heating, ventilation, and air conditioning (HVAC) systems due to their ability to adapt to temperature fluctuations while operating smoothly with minimal vibration. Perforated steel sheets are effective for evenly distributing airflow and reducing HVAC system noise. They are used in diffusers to promote airflow, preventing stale air, heat pockets, and hard flooring issues. Additionally, perforated steel sheets act as silencers within ductwork, helping to disperse airflow and mitigate fan noise that may travel through the system hoses.
In industrial settings, equipment storage containers must meet industry standards, support the weight of parts, and provide adequate ventilation. Perforated steel sheets can be shaped into various containers such as baskets and storage bins. These containers benefit from being lightweight, which simplifies transportation and offers excellent visibility of their contents.
Perforated steel sheets also provide essential protection in industrial environments. They function as barriers that maintain visibility while allowing continuous airflow to prevent overheating of machinery. Additionally, perforated steel sheets are used in sieves and filters for washing, drying, baking, straining, and filtering processes. These applications require steel sheets that are precise, strong, durable, and resistant to acid, corrosion, and wear.
Perforated steel sheets are mostly used in the chemical industry as filters and screens to remove impurities and debris. Due to their high temperature and chemical resistance, the chemical industry prefers perforated steel sheets.
In the construction industry, perforated steel sheets offer both aesthetic appeal and structural support. They are used for cladding, sunscreens, room and space dividers, ventilation, lighting, and ceiling materials where airflow is crucial. The perforations enhance both functionality and visual interest in architectural designs.
Perforated steel sheets are also utilized for floors and stair treads in areas where slip resistance is important. Despite their lightweight and easy installation, these materials provide exceptional strength and durability, making them suitable for challenging environments while ensuring safety.
Additionally, perforated steel sheets are used in the fabrication of gates, fencing, paneling, ventilation grills, and cable trays. They offer superior durability and longevity compared to many other materials, making them a preferred choice for various applications.
Integrating designs, logos, and images into steel sheet panels for branding and identification is an emerging trend in the perforated steel sheets industry. Although this practice has been around for some time, it is gaining popularity as a design tool in architecture, allowing for creative and attractive building designs. The process begins with creating a computer-generated image, which is then transferred onto the steel panels. The image is applied to the perforated sheets using specialized perforating and fabrication equipment that processes the digital design.
Perforated stainless steel is used to manufacture a variety of products, including sheets, tubes, pipes, plates, screens, and panels. These perforated items are commonly employed in exterior building construction for applications such as grating, screens, sunshades, lighting diffusers, stair treads, facades, and decorative panels, thanks to their durability in all weather conditions.
Outdoor furniture, such as tables, benches, and chairs, often features perforated stainless steel to prevent the buildup of snow and rain. Its smooth surface and resistance to contamination make stainless steel easy to clean and sanitize. In the food, beverage, potable water, and pharmaceutical industries, it is used to create filters and sifters due to its hygienic properties.
Perforated stainless steel is also utilized in equipment for cleanroom workstations and kitchen appliances, including pans and filters, where its functionality and ease of maintenance are essential.
Perforated steel sheets serve multiple functions, including lighting and aesthetic applications. One of their most valuable uses is sound absorption. Perforated panels help reduce unwanted noise by dispersing sound waves, making them ideal for environments where loud and distracting noises are a concern. The porous and textured surface of these panels, suitable for both indoor and outdoor use, enhances their effectiveness in sound attenuation.
In construction, perforated steel sheets and sun protection screens are utilized to enhance shading and improve airflow, particularly when ventilation needs to be optimized. This method helps reduce energy costs associated with heating, ventilation, and air conditioning. Studies indicate that perforated panels can lead to energy savings of approximately 30% to 45%.
The versatility of perforated steel sheets provides designers and builders with numerous options for enhancing durable construction projects. Customizable to meet specific requirements, perforated steel sheets can be crafted to leave a lasting, distinctive impact on any structure. Additionally, when manufactured properly, perforated panels offer superior strength and weather resistance compared to other materials used for similar applications.
One of the standout features of perforated panels is their ability to create a sense of privacy without making a space feel confined. Traditional enclosed walls and panels can lead to a feeling of isolation within a workspace. In contrast, perforated panels can partition an area while still allowing for ventilation and visibility. These panels help to reflect and absorb typical noises and echoes, contributing to a more comfortable and pleasant environment.
As awareness of sustainability and conservation grows, designers and architects are increasingly seeking materials that reduce environmental impact. Perforated panels made from stainless steel offer a sustainable option, as the steel is recyclable, reducing the need for new production. Additionally, perforated panels are known for their durability and low maintenance requirements, contributing to their long lifespan. These factors enhance the sustainability and longevity of steel sheets in construction projects.
Efficiency and quality are vital in production processes. Perforated components simplify the delivery and storage of parts by allowing air to circulate, which helps prevent material buildup and dirt accumulation. For manufacturing applications, baskets, carts, and material handling equipment are commonly made from stainless steel, galvanized steel, or cold-rolled steel due to their durability and performance.
To manage and contain radiation from electromagnetic interference (EMI) and radio-frequency interference (RFI) generated by electrical components and appliances, perforated shielding is essential. It provides a shielding effectiveness of 40 decibels, meeting the minimum requirement for most applications, and achieves up to 99% attenuation of EMI and RFI radiation. Additionally, it remains highly effective at frequencies up to seven gigahertz.
Perforated aluminum consists of an aluminum sheet which has been manually or mechanically pierced or punched using CNC (computerized numerical control) technology in order to produce shapes and patterns of various sizes...
Perforated metals are sheets of metal that have had decorative shapes, and holes punched or stamped into their surface for practical or aesthetic purposes. The perforation of metal sheets takes several forms and includes a variety of geometrical patterns and designs...
A perforated metal is a piece of sheet metal that has been stamped, fabricated, or punched to create a pattern of holes, slots, and various aesthetic shapes. A wide range of metals are used in the perforating metal process, which include steel, aluminum, stainless steel, copper, and titanium...
Perforated metals are sheets of metal that have had decorative shapes, and holes punched or stamped into their surface for practical or aesthetic purposes. The perforation of metal sheets takes several forms and includes a variety of geometrical patterns and designs...
Wire mesh is fabricated by the intertwining, weaving, or welding of wires of various thicknesses to create proportionally equal parallel rows and intersecting columns. Also known as wire fabric, wire cloth, or...
Expanded metal is a sheet metal mesh. It is made by stretching a slitted sheet of malleable metal. The orientation of the slits is perpendicular to the direction of the stretch. The result of such stretching is an array of holes on the slits - to give a mesh form...
Hardware cloth is a woven mesh made by interlacing various sizes of wire to form a metal fabric that can be used for animal cages, fence material, strainers, and filtering screens. The differences between the various types of hardware cloth...
Metal grating is a metal product produced by perforating metal sheets or joining bars of metal to form a grid. They are a metal product that is widely used in various industries as stairs, platforms, scaffolding, and protective coverings...
The phrase "wire mesh" describes two- or three-dimensional structures constructed of two or more metallic wires connected by various techniques. In a wide range of settings, wire mesh products are...
Welded wire mesh is a series of wires that are welded where the individual wires cross. The openings of the mesh varies depending on the type of wire used and the function of the mesh. Regardless of size and wire, welded wire mesh is permanent and...
Wire cloth is a woven (or nonwoven) sheet or web material with a series of openings across the surface. Wire cloth is also known as: Metal Fabric or Metal Cloth; Wire Mesh, Metal Mesh, or Alloy Mesh...