Plastic Corrugated Boxes
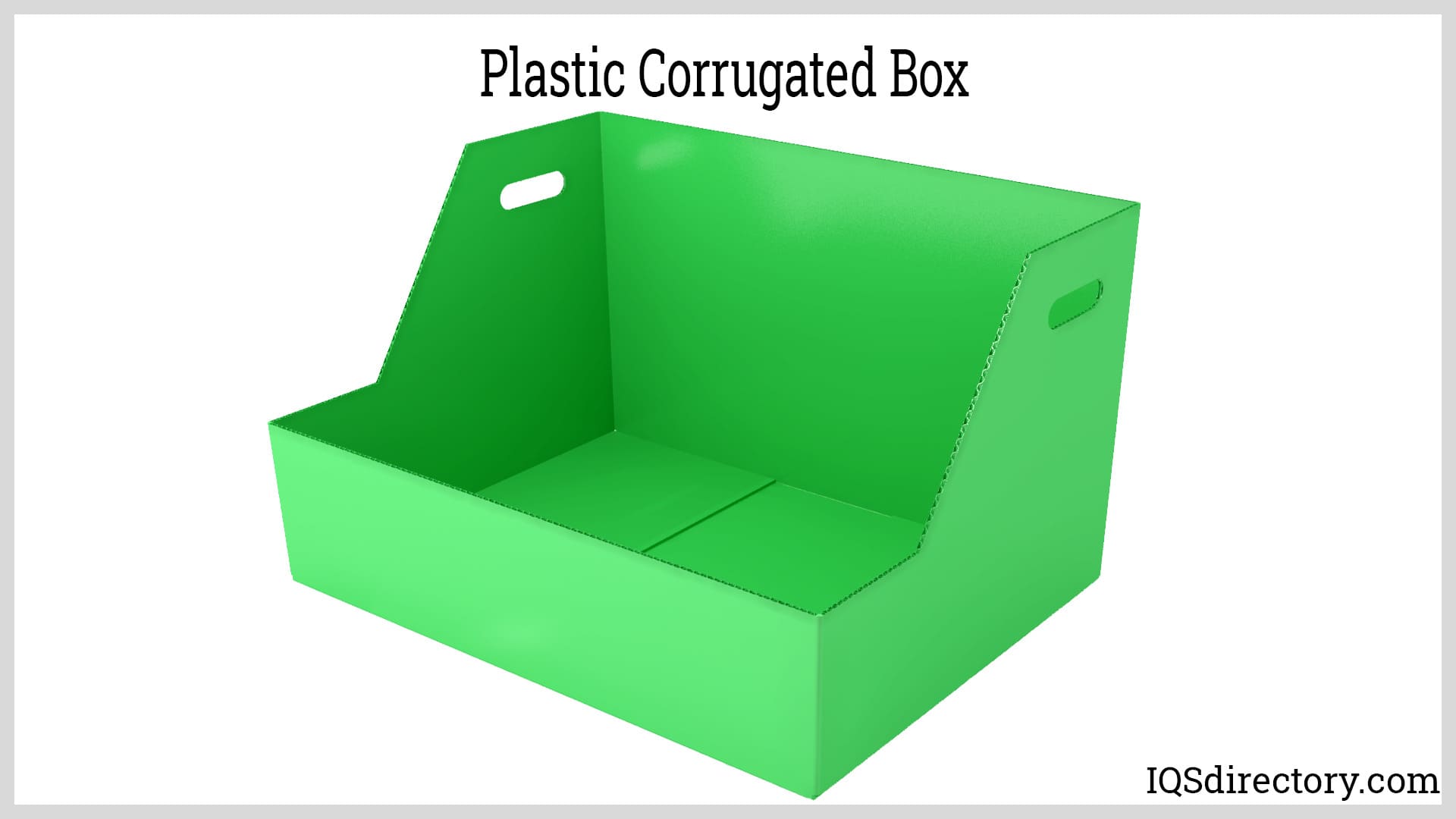
A plastic corrugated box is a disposable container with three layers of material consisting of an inner layer, an outer layer, and a middle layer on its sides. Corrugated plastic is known by various names, including...
Please fill out the following form to submit a Request for Quote to any of the following companies listed on
This article gives deep industry insights into plastic containers. Read further to learn more about:
Plastic containers refer to storage units that are crafted using various types of polymers derived from crude oil or natural gas. These polymers are created through a series of complex chemical processes that convert raw petroleum into thermoplastics. Such materials are meticulously engineered to be molded, shaped, and formed into robust, highly durable, and long-lasting transport and storage containers. Since their emergence during the industrial revolution's inception, plastic containers have become indispensable components for industrial applications and logistics operations.
The production of plastic containers can vary based on the necessary specifications. Smaller-sized containers are usually manufactured through the injection molding process, whereas larger, uniform containers are generally produced by rotational molding techniques. These advanced manufacturing methods allow for the creation of a diverse array of plastic products, ranging from drink bottles to expansive shipping containers.
The inception of plastics can be traced back to the 1840s when Eduard Simon, a German scientist, first discovered polystyrene. This groundbreaking discovery was soon succeeded by the development of celluloid, marking the beginning of the polymerization process vital for plastic production. Initially confined to bottle manufacturing, plastic containers saw exponential growth in the 1930s due to the adoption of cellulose acetate. Following this, materials such as low-density polyethylene (LDPE) and polyvinyl chloride (PVC) emerged, significantly streamlining mass production processes.
In today's world, plastic containers are available in a multitude of styles and sizes. Continued advancements in production methodologies have resulted in the creation of vast-volume containers, delicate see-through clamshell packs, and resilient impact-proof cases. In 2018, the plastic container market was estimated to be worth around $86 billion globally and is anticipated to grow by an annual rate of 4% between the years 2019 and 2025. Key industries that heavily depend on plastic containers include food and beverages, pharmaceuticals, cosmetics, household products, industrial lubricants, and petroleum.
The most extensively utilized material for crafting plastic containers is polyethylene terephthalate (PET), predominantly used for water, soda, and juice bottles. High-density polyethylene (HDPE) is another popular choice, commonly employed for packaging everyday items such as shampoos, household cleaners, and detergents.
Plastics are versatile synthetic materials primarily manufactured from chemical compounds derived from petroleum and related fossil fuels. The most commonly used building blocks in the plastics industry include ethylene, propylene, styrene, and acetylene. These essential monomers—basic organic molecules containing double bonds and diverse functional groups—react through a process called polymerization to form long chains known as polymers. This chemical process is at the heart of plastic production, enabling the transformation of simple hydrocarbons into materials with a vast range of properties and uses. Plastics are foundational to industries such as packaging, automotive, medical devices, construction, and electronics due to their adaptability, durability, and cost-effectiveness.
During manufacturing, polymer chains are created by polymerizing one or more types of monomers. The selection and combination of different monomers are carefully engineered to achieve desired physical and chemical characteristics. Enhancing the properties of raw plastics involves a compounding stage, where additives, plasticizers, fillers, stabilizers, and reinforcements are thoroughly blended into the polymer matrix. This critical step allows plastic manufacturers to fine-tune attributes such as strength, flexibility, UV resistance, chemical resistance, thermal stability, flame retardance, impact resistance, transparency, and color. Additives may include antioxidants for anti-aging, plasticizers for increased flexibility, or pigments for coloration. After compounding, plastics are processed through various molding techniques—such as injection molding, blow molding, extrusion, and thermoforming—to produce finished goods, including plastic containers, bottles, films, and other consumer or industrial products.
Plastic polymers are generally categorized into two main types: thermoplastics and thermosets. This fundamental distinction determines their behavior during processing and end-use applications, making it crucial for material selection in manufacturing and product design.
Thermoplastic polymers, often referred to simply as thermoplastics, remain one of the most widely used categories within the plastics industry. Their defining feature is the capacity to be reshaped repeatedly through cycles of heating and cooling without undergoing any irreversible chemical changes. When subjected to heat, thermoplastics soften or become molten, a process that is entirely physical rather than chemical. Upon cooling, these plastics harden and return to their original state. This distinctive reversibility makes thermoplastics ideal for processes like injection molding, extrusion, and 3D printing, supporting high-volume manufacturing of parts with intricate geometries. Common thermoplastic types include polyethylene (PE), polypropylene (PP), polyvinyl chloride (PVC), polystyrene (PS), and polycarbonate (PC). Their extensive application spectrum covers packaging materials, pipes, automotive parts, electronic housings, and much more due to their recyclability and ease of processing.
Thermosetting polymers, or thermosets, represent a distinct class of plastics characterized by the formation of permanent crosslinks between polymer chains during processing. Unlike thermoplastics, thermosets undergo a chemical transformation when heated in the presence of a curing agent, leading to irreversible hardening and enhanced structural stability. This process—known as curing or crosslinking—creates a rigid, heat-resistant, and dimensionally stable material. Once set, thermosets cannot be re-melted or re-shaped, making them ideal for applications demanding high thermal resistance, mechanical strength, and chemical durability. Examples of thermosetting plastics include epoxy resins, phenolic resins, melamine, and bakelite. Industries utilize thermosets in advanced composites, circuit boards, adhesives, coatings, electrical insulators, and structural components where long-term performance and reliability are essential.
Choosing the Right Plastic Material: Understanding the differences between thermoplastics and thermosets is critical when selecting materials for product development or industrial applications. Factors to consider include the mechanical properties needed, target environment (such as exposure to temperature extremes, chemicals, or UV radiation), required product lifespan, moldability, recyclability, and cost effectiveness. Engineers, designers, and procurement specialists frequently work with plastics suppliers and manufacturers to evaluate technical data sheets and select optimal polymer grades for each use case, whether it’s for mass-produced packaging, automotive components, consumer goods, or highly engineered solutions.
For those interested in sourcing or specifying plastic materials, working with reputable plastic manufacturers and suppliers can help ensure access to high-quality polymers and expert technical guidance. Many leading companies offer custom compounding services, application support, and compliance documentation to meet unique industry standards and regulatory requirements.
Since their widespread adoption in the 1950s, plastics have been hailed as a "miracle material" and have revolutionized the packaging industry. Today, plastic containers are an essential part of daily life and industrial storage due to their economical production, lightweight nature, exceptional durability, and corrosion resistance. Their superior performance compared to traditional materials makes plastics ideal for food packaging, pharmaceutical containers, chemical storage, and a wide range of consumer goods. Below, we explore the key benefits driving the ongoing popularity of plastic containers and illustrate why they remain the preferred packaging solution for manufacturers and consumers alike.
Plastics offer exceptional versatility in shaping and molding, making them highly prized in custom packaging and container manufacturing. They can be processed through various methods such as injection molding, blow molding, casting, extrusion, stamping, and more. This flexibility enables the creation of complex shapes, ergonomic handles, and secure closures that may be challenging or cost-prohibitive with materials like glass, metal, or ceramics. The lower operating pressures required for forming plastic containers also streamline production and reduce energy costs, further enhancing their value for large-scale manufacturing and small business packaging solutions.
Unlike metals—which are susceptible to corrosion, rust, and contamination risks—plastic containers are highly resistant to moisture, UV radiation, and a wide variety of chemicals. This makes them ideal for food storage containers, pharmaceutical bottles, industrial chemical drums, and household cleaning product packaging. Even under prolonged exposure, plastic packaging maintains its integrity and barrier properties. While glass is also chemically resistant, its weight, cost, and fragility often limit its practicality in many storage and shipping scenarios.
Most plastics have densities ranging from 0.8 to 1.5 times that of water, making them significantly lighter than steel (7.8x water's density) or glass and ceramics (2-3x water's density). This noteworthy weight advantage translates into reduced transportation and shipping costs, easier storage, and increased logistical efficiency. With a high strength-to-weight ratio, plastic containers can be designed with thinner walls while retaining durability, supporting both eco-friendly packaging goals and supply chain optimization.
Plastic containers are produced using a range of advanced polymers—including HDPE, PET, LDPE, polypropylene, and more—each offering distinct mechanical characteristics. These properties can be tailored using additives such as glass fibers, carbon fibers, and UV stabilizers during compounding. The resulting composites boast high tensile and flexural strength, enabling the production of robust, impact-resistant, and shatterproof packaging suitable for rigorous handling, industrial logistics, or retail shelf displays.
The molecular structure of plastics, featuring extended and interconnected polymer chains, provides them with flexibility and resilience. This configuration imparts outstanding resistance to impact, punctures, and tears—critical characteristics for heavy-duty packaging, industrial drums, shipping containers, and transportation packaging. Manufacturers often incorporate performance-enhancing additives or choose polymers with superior tensile strength for specialized uses such as hazardous material containers or reusable tote bins.
Plastic containers offer exceptional branding and design flexibility. They can be manufactured clear, translucent, or opaque; colored using a broad spectrum of pigments; and finished with a variety of textures, glosses, and tactile effects. This adaptability enables brands to enhance shelf appeal, product safety, and consumer engagement without the expense of secondary finishing processes often required with glass or metal. Printing, labeling, and embossing features are also easily achieved on plastic substrates.
Plastic containers are celebrated for their resistance to chemicals, weather, and mechanical wear, making them long-lasting and reliable solutions in both domestic and industrial environments. Their longevity is prolonged further by customized additives that provide UV protection, anti-oxidation, and antimicrobial properties. While their durability means excellent lifecycle performance, it also places responsibility on manufacturers and consumers to explore sustainable disposal and recycling practices to mitigate environmental impacts.
Most plastic packaging—including containers made of PET, HDPE, and polypropylene—are recyclable through municipal and industrial programs. The plastic recycling process generally involves sorting, cleaning, grinding, melting, and remanufacturing into new plastic products. Thermoplastics, in particular, can be recycled multiple times. Some industry innovations, such as chemical recycling and depolymerization technologies, allow plastics to be broken down into their original monomers, creating feedstocks for new plastics or even alternative fuels. Eco-conscious consumers and businesses are increasingly demanding post-consumer recycled (PCR) content and participating in closed-loop recycling systems to reduce plastic waste and support a circular economy. For resources on sustainable options, consult local recycling guidelines or environmental agencies (no rel="nofollow" link added as per existing hyperlinks only).
Plastic containers are among the most cost-effective packaging choices due to their low material cost, energy-efficient manufacturing, and scalability. Techniques such as injection molding, blow molding, and thermoforming allow high-speed, automated mass production with minimal labor and tooling expenses. Plastics become moldable under moderate heat and pressure, have lower melting points than metal and glass, and are often molded with compressed air—minimizing capital investment and ongoing energy usage. This combination of affordability, performance, and versatility cements plastics' role as a top choice for industrial and consumer packaging applications.
When evaluating packaging for food safety, pharmaceutical compliance, or hazardous materials, plastic containers consistently deliver superior economics and value without sacrificing durability or visual appeal. Understanding these advantages enables users to make informed decisions when selecting packaging solutions that align with cost, branding, transportation, and sustainability goals.
Plastic containers often feature a number stamped on the bottom, which denotes the specific type of plastic used. This numbering system facilitates easy identification and sorting during the recycling process. The number reflects the polymer used to create the resin, and each type of polymer requires distinct processing and recycling methods.
A useful guideline is shown below. Most recycling systems do not readily accept numbers three and six, but the others can generally be recycled without issue.
The numbers from one to six represent the commonly used plastics, listed sequentially below. The final number, seven, encompasses various types of plastics like polycarbonate and ABS that do not fit into the previous categories.
PET is the most commonly utilized plastic for manufacturing containers. Its excellent resistance to carbon dioxide, especially in its biaxially oriented form, makes it particularly suitable for carbonated drink bottles. Due to its ability to absorb moisture from the environment, PET needs to be dried before being processed with molding equipment.
PET's chemical stability ensures that it does not leach substances, making it a preferred choice for food-related applications. This characteristic also contributes to its safety and suitability for repeated use. The high recyclability of PET has positioned it as a key material in contemporary plastic container production. Recycled PET finds application in a wide range of uses across various industries.
Scientific data indicates that PET is the most environmentally friendly material for container production. Its recyclability and potential for reuse surpass those of aluminum, metals, and glass.
HDPE, a variant of polyethylene (PE), is known for its high strength-to-density ratio. Its linear molecular structure, with minimal branching, leads to stronger intermolecular bonds. This makes HDPE ideal for producing more rigid containers and bottles, such as those used for water, milk, detergents, and various drums. Additionally, HDPE is both recyclable and reusable, and is regarded as one of the safer plastic types available.
Polyvinyl chloride (PVC) is a versatile plastic that can be customized with various stabilizers, plasticizers, impact modifiers, and processing aids. By adjusting the levels of plasticizers, PVC can be formulated into either rigid or flexible containers. Additionally, PVC provides better clarity compared to many other flexible plastics. However, PVC can emit harmful pollutants, acids, and toxins during its production or breakdown. As a result, the additives used in PVC are now subject to regulation by agencies such as the FDA and EPA.
Low-density polyethylene (LDPE) is another form of polyethylene with a branched polymer structure and weaker intermolecular forces. This leads to reduced tensile strength and barrier performance compared to other types of polyethylene. However, LDPE offers superior impact resistance and flexibility. It is commonly used to produce flexible containers and bottles, including squeezable bottles, dispensing bottles, and sampling containers.
Polypropylene is a highly versatile polymer with properties that vary widely based on factors such as molecular weight, morphology, crystalline structure, additives, and copolymerization. It can be engineered to achieve a high degree of crystallinity, resulting in tensile strength and hardness comparable to that of HDPE. Additionally, polypropylene can endure elevated temperatures without significant loss of strength or degradation. However, polypropylene is prone to UV degradation and oxidation. It is frequently utilized in the manufacture of drums and pails.
Like polypropylene, polystyrene is a versatile plastic that can be adjusted through copolymerization and the incorporation of various additives. It can be produced in flexible, rigid, or cellular (foam) forms. However, polystyrene is susceptible to oxidation, which makes repeated recycling inadvisable. Additionally, its tendency to oxidize can lead to a yellowish discoloration over time. Polystyrene is commonly used for manufacturing disposable items, such as clamshell food containers and single-use cups.
Polycarbonate can be readily shaped using various molding techniques, with injection molding and sheet extrusion being particularly prevalent. It is commonly used for making beverage bottles and food storage containers. Polycarbonates are valued for their exceptional impact resistance, high heat tolerance, excellent electrical insulation, clarity, effective water barrier properties, and natural flame-retardant characteristics.
Acrylonitrile Butadiene Styrene (ABS) is a widely used plastic known for its hardness and rigidity, combined with moderate toughness. To enhance its durability, protective coatings are often applied because ABS has limited resistance to UV radiation and only moderate resistance to various acids and alkalis. It is frequently employed in the production of battery containers.
Polyamide is classified as an engineering plastic, known for its exceptional toughness, impact resistance, solvent resistance, abrasion resistance, and heat resistance. A typical use of polyamide is in the manufacture of automotive fuel tanks.
The method used to form plastic containers varies based on the container's shape and type. Plastic containers come in various forms, including intermediate bulk containers (IBCs), drums, bottles, bags, and enclosures. Each of these forms is best suited to specific manufacturing techniques. The following are some of the prevalent methods for creating plastic containers.
Injection molding is a technique used to shape plastics by forcing molten material into a mold or chamber. This method consists of three primary steps:
The most commonly used injection molding equipment is the reciprocating screw extruder. This machine blends and kneads the plastic through the rotating screw. Once the plastic is adequately prepared, the screw advances to eject the material from the extruder and into the mold.
The mold is designed to form the shape of the plastic container and typically consists of two parts: one stationary and one movable. After the molding process, the movable part shifts to eject the finished product. The mold includes various openings or channels for injecting plastic, allowing air to escape, and enabling excess plastic to flow out.
Injection molding is limited to producing containers that are open on one side. Examples are pails, tubs, cups, bowls, and food containers. By itself, injection molding is not suited for producing closed, hollow products such as plastic bottles. To produce these products, an inert gas is introduced into the mold partially filled with molten plastic. This pushes the plastic on the surface of the mold, creating a hollow part. This process is known as gas-assisted injection molding.
Blow molding creates plastic containers by expanding a heated plastic material within a mold. The primary steps involved in blow molding include:
Similar to injection molding, blow molding utilizes screw extruders for melting and mixing the plastic. The creation of the preform in blow molding is divided into two distinct methods: extrusion blow molding and injection blow molding.
In extrusion blow molding, the preform is formed into a hollow tube that hangs from one end. Conversely, injection blow molding involves injecting plastic into a mold that includes a core for air injection to shape the preform. Both methods utilize air to expand the preform and mold it into the desired shape.
Blow molding is ideally used for manufacturing hollow plastic items like bottles, water jugs, tube packaging, intermediate bulk containers (IBCs), and storage tanks.
Rotational molding, often called "roto molding," is a technique for casting hollow and seamless plastic containers. Unlike other methods, this process does not rely on pressure to shape the product. Instead, the plastic melt is distributed across the interior surfaces of the mold through rotational movement. The operation of this process is outlined as follows:
Rotational molding machines vary based on the number and arrangement of molds, as well as the methods used for heating and rotating them. Examples of different types of rotational molding machines include clamshell, turret, shuttle, and swing machines.
Because rotational molding does not require high pressures, the molds used in this process are relatively inexpensive, allowing for the production of larger items. Additionally, this method can create double-walled containers in a single step, without the need for secondary processing.
Products made using rotational molding include industrial and agricultural storage tanks, drums, carboys, insulated boxes, and trash bins.
Thermoforming involves heating thin plastic sheets to their optimal forming temperature and then stretching them over a mold. This secondary plastic forming technique does not require raw plastic resin for compounding. Instead, it utilizes plastic sheets or films produced through preliminary methods like extrusion or calendering. The process of thermoforming includes the following steps:
Thermoforming encompasses four primary types: vacuum, pressure, mechanical, and twin sheet forming. Each method varies in its approach to applying pressure for shaping the plastic. Vacuum, pressure, and twin sheet thermoforming use compressed air to push the plastic sheet against the mold, while mechanical thermoforming employs two dies that press together to shape the plastic.
Thermoforming is generally restricted to creating parts with relatively thin walls. Additionally, the process can lead to defects like uneven thickness, webbing, and warping. It is not ideal for manufacturing containers that require high rigidity.
Thermoforming is commonly used to produce single-use containers for food and pharmaceutical applications. Typical examples include disposable cups, clamshell containers, and trays.
Compression molding involves shaping plastic resin by pressing it between two molds. This method is especially suited for creating large thermosetting plastic items. The process is outlined as follows:
In compression molding, the press typically closes in a downward direction, though upward-closing presses are also available. The mold is equipped with internal heating elements that soften the plastic material, enabling it to conform to the mold's shape. The heat also initiates the curing process of the plastic. During curing, some plastic may emit gases, which are expelled through an additional step known as degassing.
Compression molding is also employed to create containers that include fiber reinforcements. Glass or carbon fibers can be incorporated into the plastic charge before it is molded.
Similar to injection molding, which utilizes two mold halves, compression molding is restricted to making containers that are open on one side. Examples of products made through compression molding include large bins, tubs, trays, and plastic caps for bottles.
Plastic containers are ubiquitous in daily life, serving a wide range of purposes such as gas canisters, shipping containers for airlines and railroads, luggage, garage storage bins, barrels, drums, and tool chests. The robustness of various thermoplastic materials underpins the plastic container industry, which has continuously innovated and refined container designs to address the increasing demand.
Plastic folding boxes are a growing trend in the packaging industry. They are a cost-effective and elegant method for displaying products. Plastic folding boxes offer a clear view of a product while protecting the product from damage. They are made from a full array of thermoplastic materials and have the same endurance and stability as other plastic containers. Packaged products are kept secure during shipment to ensure safe delivery. Plastic folding boxes can be customized with graphics, artwork, and logos to enhance product presentation.
Lighter plastic folding boxes are commonly used for product display and shipping purposes. There are also robust versions designed for heavy-duty shipping, featuring rigid plastic sides that can collapse flat when not in use. Available in various sizes, these containers have interlocking corners for quick assembly and stability. Despite their strength to support over 100 lbs (45 kg), they can be easily collapsed and stacked when not needed.
Plastic barrels are made from high-density polyethylene, which gives the barrels their strength and toughness. They are ideal for any form of industrial operation, including transfer, storage, waste disposal, fluid and parts storage, and packaging. The thermoplastic materials of plastic barrels can withstand the effects of chemicals and hazardous materials. Unlike drums and barrels made of metal, they are resistant to rusting and corrosion, increasing their longevity.
Plastic gas cans are made from all different types of thermoplastics and are engineered to be able to safely hold gas. They come in several gallon sizes, from one gallon to over ten gallons, and provide a safe and convenient way to transport and store gas. Under normal conditions, plastic gas cans can store gas for close to a year without seepage or leaks due to the molecular structure of the various polymers.
Plastic shipping crates are built to be exceptionally durable and robust, withstanding frequent use and the stresses of long-distance transportation. Their large size necessitates the use of rotary molding during manufacturing to achieve uniform wall thickness and create a seamless, single-piece unit.
Plastic shipping crates are designed to accommodate very heavy loads, including items like electrical tools, equipment, and convention displays. They are available in a range of sizes to suit various shipping requirements.
The four types of plastic containers mentioned are just a few examples of the extensive range offered by plastic container manufacturers. These manufacturers produce both standard-sized containers and custom-designed solutions tailored to meet specific and unique needs.
A plastic corrugated box is a disposable container with three layers of material consisting of an inner layer, an outer layer, and a middle layer on its sides. Corrugated plastic is known by various names, including...
Plastic crates are containers used for moving or transporting goods from point A to point B. They are also used for storage and are made of exclusively or partially plastic material. The basic material is plastic...
A plastic tote is a box type portable storage container that is made of resilient and durable plastic that is capable of withstanding heavy duty use in industrial and residential settings. They come in...
Nylon tubing, also known as polyamide tubing, is a type of tubing made from polyamide resin, which has a strong resistance to abrasion. It is used in high-pressure and high-temperature applications...
Plastic materials are objects artificially made from organic compounds called polymers along with other additive components. They possess excellent formability, making them extremely versatile for many different fabrication and manufacturing processes...
A plastic tank is a large capacity liquid or granular storage unit that can be vertical, horizontal, below or above ground, as well as movable. They are designed to hold several gallons of a variety of substances for long periods without experiencing wear, weathering, or deterioration...
Plastic tubing is a form of tubing that is manufactured from a mixture of a polymer with a variety of chemicals to form a material that can be solid or flexible. Since its first use in the 1950‘s, plastic tubing has revolutionized industrial processes and has found a use in a wide variety of applications...
A plastic water tank is a large capacity container designed to store water for household, agricultural, irrigation, and industrial manufacturing use. There are various types of water tanks produced to meet the needs of specific applications, with...
A poly tank is a plastic storage tank used to store, transport, and collect water, other liquids, and granular or powder materials. They are made of polyethylene or polypropylene and are a cost effective, lightweight, and easy to handle...
Poly tubing is a highly flexible, lightweight, and durable tubing that is produced from polyethylene, a polymer that is made from the polymerization of ethylene. It is a very versatile form of tubing that has break and crack resistant walls...
PVC is a tough chemically resistant synthetic polymer of vinyl chloride used especially for making pipes, films and electrical insulation. It is made by polymerizing vinyl chloride, and...
Silicone tubing is a very tough elastomer that exhibits high strength, flexibility, and resistance. Silicone tubing can be stretched without tearing and is highly versatile. It cannot be weakened with repeated bending and twisting due to...