Bulk Bag Handling Equipment
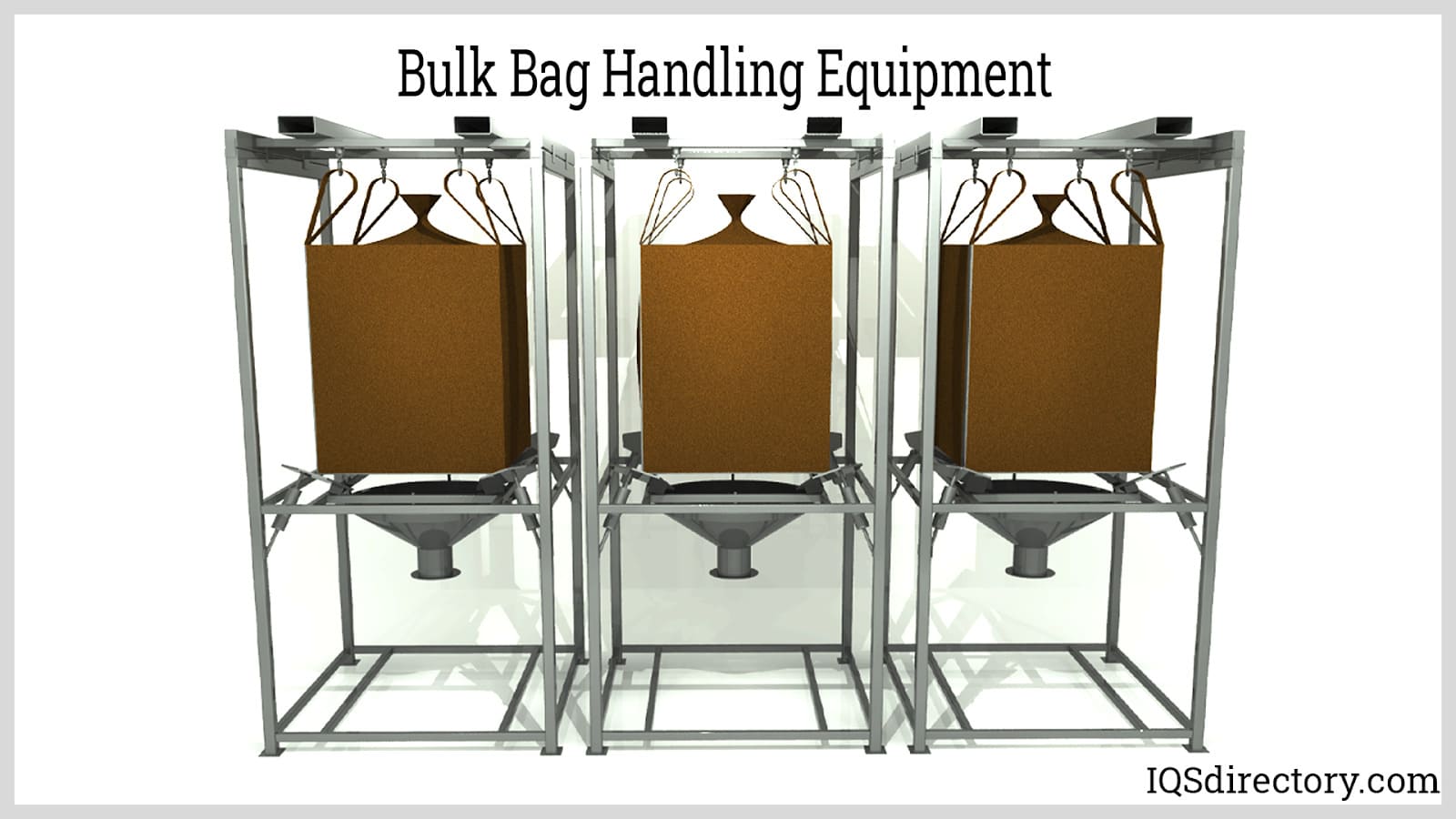
Processing equipment for holding and moving bulk bags is known as bulk bag equipment. This bulk bag equipment is typically used at the front end of the production process to hand off product to...
Please fill out the following form to submit a Request for Quote to any of the following companies listed on
This article takes an in depth look at pneumatic conveying.
You will learn more topics such as:
Pneumatic conveying is a method employed for the transportation of bulk materials like powders and granules by utilizing compressed air or gas. This technique involves moving these materials via a sealed conveying line or tube, powered by a combination of pressure differences and airflow that is created by a fan or blower. By maintaining either a positive or negative pressure within the conveyor line, the materials are efficiently moved with minimal damage or loss.
The operation of pneumatic conveying is illustrated in the image below, showing how plastic flakes are transported in a dilute phase pneumatic system employing an eductor valve.
Every system requires some type of energy to function. Though most machines are powered by electricity, pneumatic systems use compressed air to create energy. This setup pulls air from a storage unit, relying on the pressure created when air enters an enclosed space.
The core principle behind pneumatic systems involves using air to transport bulk materials such as grains, cement, powders, and chips through a pipeline. The sealed, pressurized air serves both as the energy source and the transportation medium, generating the propulsion force needed to move these materials.
Pneumatic conveying systems are used for moving a wide range of materials, including cement, fly ash, starch, sugar, salt, sand, plastic pellets, oats, polymers, lime, soda ash, plastic resin, plastic powder, dry milk, and animal feeds. They provide an energy-efficient and cost-effective solution for transporting materials from railcars, trucks, or silos. Furthermore, pneumatic conveying is utilized in intermodal or transloading operations, in-plant transfers, and dust containment.
The pneumatic conveying process features meticulously engineered components that collaborate to transport substances and materials safely, cost-effectively, and efficiently.
The two primary forms of pneumatic conveying are pressure and vacuum systems. Pressure conveying uses pressurized air to move materials through the pipeline. This type of system requires components such as a feed line, rotary gate valve, and pressure containers. Pressure systems are typically employed for transporting large materials over long distances.
A vacuum conveying, or suction system, uses a vacuum pump to create a centralized or decentralized vacuum that moves the sucked up material to a loader where the vacuum air is separated from the material. When the vacuum air reaches the pump, it is filtered and released into the environment. Vacuum systems are able to supply multiple processing units with different materials due to their flexibility.
In certain vacuum systems, a vacuum is created using pressurized air and a venturi valve. The venturi valve draws material in and moves it to its destination with the aid of pressurized air. This type of system, often referred to as a suction system, is typically used for handling small loads of materials.
Pneumatic conveying systems are classified into two types: dilute phase and dense phase. Both types use air pressure and an enclosed line or tube to move materials. The key difference between them lies in their method of generating air pressure and the way materials are transported through the system.
There are two methods for moving materials using dilute phase, suspension, or lean phase pneumatic conveying: positive and negative pressure systems. A positive or blowing phase system utilizes a fan or blower to create pressure within the line, suspending the material. At the end of the line, a separator or filter removes the material. In this system, materials travel at speeds ranging from 15 to 35 meters per second (m/s). Key components for dilute phase systems include a pressure vessel and an inlet valve that operates intermittently, rather than continuously.
Negative pressure systems, or vacuum systems, operate in the opposite manner. Instead of pushing or blowing material through the line, these systems create a vacuum to pull the material through.
The distinction between these systems is illustrated in the diagram below. In the vacuum system (shown on the left), the blower is positioned on the right with the hoppers on the left. In contrast, the pressure system (shown on the right) features the blower to the left of the feed tube, pushing the material toward the storage silo.
Dense phase pneumatic conveying uses a small amount of air to move large amounts of material in slugs. The conveying system pushes denser concentrations of bulk solids at low velocity with the result of the conveying being less wear on components of the system. Dense phase pneumatic conveyors are a batch system that uses high pressure and a high product to air ratio, which allows the conveying system to push denser concentrations of solids at low velocity.
Dense phase pneumatic conveying is commonly used for products that are friable or prone to crumbling, such as those involved in food preparation. This method is ideal for preventing the degradation of delicate food products, including meat chunks, softened grains, and vegetables. For abrasive materials, dense phase conveying's low velocity helps prevent damage to pipes and minimizes product contamination.
“Booster pulsers,” also known as “air saver boosters” or “air fluidizers,” are employed to ensure uniform bulk material movement during dense phase pneumatic conveying. These devices support both dilute and dense phase conveying methods as well as silo loading. Boosters are installed along the pneumatic conveying line and connected to a parallel air line controlled by the system. Multiple boosters are positioned through the hopper section and along the pipeline walls to loosen materials and regulate airflow with small bursts of air, thereby controlling product consistency and maintaining pipeline velocity.
The pipeline in dense phase pneumatic conveying systems is tightly packed, which helps prevent air from bypassing the material and enhances system efficiency. This configuration ensures that particles do not come into contact with the piping or tube, reducing abrasion and wear. The increased density of the conveyed material results in a slower transfer rate but allows for better control of velocity.
Pneumatic conveying is a safe and efficient method for transporting materials, utilized across thousands of industries. Its complexities are detailed in numerous books, journal articles, and white papers, complete with diagrams and intricate equations.
When selecting a pneumatic conveying system, several factors must be considered. It is crucial to ensure that the equipment and conveying method are well-suited to the material being transported. Below are some key points to guide your choice of a pneumatic conveying system.
The first factor to consider when selecting a conveying system is the type of material to be handled. Bulk density is crucial as it influences the requirements for vacuum receivers and air sources. It determines the necessary cubic feet per minute (CFM) for the conveying line. Additional factors to take into account include:
Understanding the characteristics of the material is essential, as each pneumatic system is specifically designed to handle particular types of materials.
It’s important to determine if the system can accommodate the distance—whether vertical or horizontal—that the material needs to travel and if it fits within the facility’s space. The system should be sized to allow for maintenance and oversight. The system shown below is a complex vacuum system connected to container storage units.
Other considerations include the number of pickup points, the size of the receiving container, whether the process is continuous, the feed rate, and if it’s a batch process, how frequently the batches will arrive and their sizes.
A vacuum system draws materials through the pipeline and is well-suited for pressure-sensitive, non-abrasive materials. In contrast, a pressure system pushes materials through the pipeline and can handle abrasive substances. For example, quartz and copper sulfate are types of abrasive materials that a pressure system can effectively transport.
Non-abrasive powders, such as moringa powder and powdered metals, are effectively conveyed using a vacuum pneumatic conveying system.
Dilute phase conveying moves materials at high velocities under pressure, which can result in some breakage during transport. In contrast, dense phase conveying operates at lower pressure and is better suited for fragile materials. Dilute phase systems have a high air-to-product ratio, while dense phase systems have a low ratio. The image below illustrates the difference between dilute phase on the left and dense phase on the right.
The initial cost of a pneumatic conveying system can range from several hundred thousand dollars for a complex setup designed to handle large volumes of material to tens of thousands of dollars for a simpler system. The first image below shows a sophisticated food conveying system intended to move tons of raw materials in food production. The second image depicts a more straightforward system used for conveying powdered materials.
All pneumatic systems utilize pipes or ducts to move materials using a stream of air. An air mover, positioned at the beginning to push materials through the line or at the end to pull materials through, generates either pressure or a vacuum.
The fundamental components of a pneumatic system include:
A pressure blower is one of the two primary methods for transporting material in a pneumatic conveying system. During system design, a critical consideration is the pressure drop throughout the system, which is greatest at the end of the pipeline. The blower's force dictates the flow rate in cubic feet per minute (CFM), velocity in meters or feet per second, and the pressure. It effectively pushes the material through the pipeline.
Vacuum pump is another method of moving material. Vacuum systems are often used as part of a dilute phase system but can also be applied to dense phase systems. An electric driven vacuum pump is the most efficient and recommended method for producing the vacuum. As can be seen in the diagram, the vacuum conveyor is located to the right at the end of the pneumatic pipeline and pulls the material through.
Eductors use compressed air to transport solids by creating a vacuum through the nozzle. The expanding air draws material into the suction chamber and moves it through the diffuser section into the conveying system. Eductors help prevent blowback, airlock wear, jamming, and product damage.
Rotary airlock valves manage solids by separating two areas under pressure while transferring material from one condition to another. They are typically used at both the beginning and end of a pneumatic conveying system.
In a rotary airlock valve, air is sealed between the valve's inlet and outlet ports. The rotating vanes create pockets where material enters through the inlet, and as the vane continues to rotate, the material exits through the outlet and moves downward. The rotary movement restricts airflow but allows for continuous material flow. For optimal operation, the system must maintain either pressure or vacuum.
The conveying line is the pathway through which the material is transported, encompassing both the material and the transport method, as illustrated in the diagram below.
Diverter valve prevents contamination and provides line switching as can be seen in the diagram. It is designed to reroute product from one conveying line to another and can be made of cast iron, aluminum, or stainless steel. Diverter valves are sealed with polyurethane rubber seals and have a parabolic shape that has without gaps.
Filter receivers capture and separate dust from the material in a pneumatic conveying system. The filter within the receiver unit traps unwanted airborne particles, as shown in the diagram on the right.
A cyclone separator utilizes centrifugal force to remove particles from the air in a pneumatic conveying system. As air enters the cyclone and rapidly rotates, particles are driven against the wall and then fall to the bottom of the container.
A batching system employs pneumatic conveying to mix ingredients by injecting them into the conveying line and directing them into a mixer. Batching operations significantly expand the size and complexity of a pneumatic system.
A hopper holds the material before it enters the conveying line. The material is released from the hopper by a rotary airlock valve, as illustrated in the diagram of a chip hopper feeding into the conveying line.
A controller is essential for a pneumatic conveying system, tailored to match the system's needs and configuration. Common types include microprocessors and PLC-based controllers. These devices manage operations such as blowers, filters, valves, receiving hoppers, loaders, and filter pulsing, typically using a PC for interface and control.
Bulk bags, also known as flexible intermediate bulk containers (FIBC), are constructed from various flexible materials that expand when filled. They are a popular and cost-effective solution for shipping dry materials, as they occupy less space and can be stacked when full. Additionally, bulk bags are designed for easy handling and can be folded for convenient storage on shelves or racks when not in use.
Despite differences in design, all bulk bags feature sewn fabric sides and come with one, two, or four handles. They are available in two basic shapes: circular or tubular and rectangular or square. Bulk bags are commonly used with pneumatic conveying systems to capture the transported product or materials, enhancing efficiency and ensuring proper containment with minimal loss.
Different types of bulk bags that work with pneumatic conveyors include plain bottom, discharge spout closure, conical discharge spout, discharge spout with flap, duffle bottom, diaper bottom, and iris closure. Each type of bulk bag configuration attaches differently to the pneumatic conveyor system.
Plain bottom bulk bags feature a flat, non-spouted bottom, making them an economical choice for capturing discharge. These bags are primarily used for product capture rather than discharge. Although they can be used for discharge by cutting open the bottom, this process destroys the bag's usability.
Bulk bags with discharge spout closures are designed to be reusable and include a built-in spout. These spouts can be adjusted to different diameters and lengths, typically around 14 inches (35.56 cm) in diameter and 18 inches (45.72 cm) long. These bags can be configured for either volume unloading or weight-based loading depending on process requirements.
Bulk bags with conical discharge spouts include a spout with a conical shape, designed to ensure complete emptying of the bag’s contents. This shape prevents product from accumulating in the corners and facilitates smooth, residue-free discharge.
Bulk bags featuring a discharge spout with a flap are designed with a protective flap at the base of the bag to prevent dust collection. The flap, which matches the dimensions of the bag's panels, functions as an access door for the spout and helps safeguard against contamination.
Duffle bottom bulk bags resemble standard bulk bags but differ in that their bottom can be completely opened to discharge contents. They are suitable for products that are prone to clumping or do not flow easily. The bottom is secured with ties when the bag is full, and some designs include a flap for additional security.
Diaper bottom bulk bags are similar to duffle bottom bags but feature a flap attached to the bottom edge of one of the panels. This flap is secured with ties to cover the discharge opening. Unlike full-opening bottoms, the diaper bottom provides a reusable solution with a permanent bottom design.
An iris closure discharge bulk bag utilizes an iris-style valve to control the flow of material. The iris valve, which secures around the spout, opens slowly when pulled, allowing controlled material flow while minimizing dust accumulation and preventing uncontrolled blasts.
Mechanical systems, such as conveyors, can be expensive and inefficient when handling bulk materials. Their design, which includes troughs, sides, and dividers, often falls short in addressing issues like dust, contamination, and worker safety, leading to potential losses.
Efficient material conveying is vital across numerous industries, from automotive manufacturing to package delivery. Systems are typically tailored to the specific requirements of the materials they handle, ensuring timely production and delivery. This need for efficiency is driving the increased adoption of specialized conveying systems.
Pneumatic systems provide a cost-effective and efficient solution for transporting bulk materials over long distances. Their enclosed and sealed design ensures smooth material flow, reducing the need for manual oversight and guaranteeing timely, damage-free delivery of materials.
As businesses expand, they often need to revise their material handling processes. Mechanical systems usually require costly and disruptive re-engineering. In contrast, pneumatic systems can be adjusted with minimal impact on operations, offering a more adaptable solution to changing needs.
For handling bulk materials like powders, flakes, chips, or granules, pneumatic systems are an optimal choice. They can be configured to deliver materials to specific locations and easily adjusted to meet evolving needs. The key consideration is whether the material fits the criteria of bulk material. Once this is confirmed, implementing a pneumatic conveying system is the logical next step.
Pneumatic conveying systems, with their pressurized tubing, offer great flexibility. They can be easily repositioned and adapted to new routes and locations. As the supply chain expands, these systems can be scaled up to accommodate growth. They are capable of transporting bulk materials through, over, around, or under various infrastructure elements, providing versatile solutions for material handling.
Manufacturing operations constantly seek to reduce production costs to stay competitive. Companies are always exploring ways to cut maintenance, repair, and supply chain expenses. Pneumatic systems offer significant advantages in this regard.
Compared to other mechanical conveying methods, pneumatic systems are easier to install and require minimal maintenance. They deliver consistent, reliable performance without the need for additional labor or complex mechanisms. This cost-efficiency is a major reason why many bulk material handling companies prefer pneumatic conveying.
As industrial operations become more complex, worker safety becomes increasingly critical. Traditional methods like forklifts and manual handling can lead to injuries, downtime, and production delays. Pneumatic systems mitigate these risks effectively.
Pneumatic conveying systems isolate and contain bulk materials, minimizing direct contact with workers and reducing potential damage to the operation. The sealed design of these systems ensures that dust and contaminants are contained, filtered, and controlled, enhancing overall safety in the workplace.
Mechanical conveying systems are typically suited for transporting materials over short distances within a facility, such as using overhead or floor conveyors. For longer distances, especially outside the facility, alternative transport methods are often required.
Pneumatic conveying systems, however, are highly versatile and can handle bulk material transportation across considerable distances with ease. They can efficiently move materials between buildings, across towns, and to remote locations without significant risk of material loss or damage. This capability makes pneumatic systems particularly advantageous for large operations with multiple widely dispersed sites.
Pneumatic conveying systems must adapt swiftly to changes in the conveying line. When a storage container becomes full and the system needs to switch to another container, it must adjust both the volume and airflow accordingly. The ability to make these adjustments in real-time is essential, which is why pneumatic control systems are crucial. They ensure that the system maintains optimal performance by managing and responding to these changes efficiently.
An airflow controller continuously monitors the system's demands and provides real-time feedback. It measures material mass flow rates and adjusts them to maintain optimal performance. The data collected helps analyze overall system efficiency.
Closed-loop controllers integrate flow rate and process controls. They store data to identify potential leaks and errors. Based on this data, the system makes necessary adjustments to address issues. By considering pressure differences, medium density, and temperature, the system calculates the most efficient flow rate. Adjustments are made to the control valve stroke, minimizing pressure drops and ensuring precise volume flow.
Pneumatic conveying systems must adhere to a range of regulations and requirements concerning material handling. These regulations primarily focus on safety procedures and the handling of specific types of materials. The National Fire Protection Association (NFPA) and the Occupational Safety and Health Administration (OSHA) are the principal organizations responsible for developing these standards. Below is a brief overview of some key regulations and requirements.
NFPA 61 protects lives and property from fires and dust explosions in facilities handling, processing, or storing bulk agricultural materials, their byproducts, or other agricultural-related dusts and materials.
This standard provides the minimum requirements for safety to life and property from fire, flash fire, and explosion posed by agricultural and food processing combustible dust and represents the industry and commodity-specific requirements for agricultural and food processing.
Dust collector explosion venting, also called deflagration venting, allows pressure to safely escape during a fire. The vent design must ensure that the force of the deflagration or explosion is directed away from people and prevents material from being thrown into other buildings.
NFPA 91 provides minimum requirements for the design, construction, installation, operation, testing, and maintenance of exhaust systems used for air conveying of vapors, gases, mists, and particulate solids, focusing on fire and explosion prevention.
Organizations that process or convey dry bulk materials should implement a combustible dust plan. Combustible dust is any material that poses a fire or explosion hazard when mixed with oxygen and exposed to an ignition source.
Processing equipment for holding and moving bulk bags is known as bulk bag equipment. This bulk bag equipment is typically used at the front end of the production process to hand off product to...
Vacuum conveyors are suctioning machines that utilize air pressure in order to move materials through an enclosed pipeline. Vacuum conveyors have broad applications throughout the industrial and...
An AGV forklift is a driverless self-operating robotic device that has the ability to carry, lift, retrieve, and place loads for easy transfer from one location to another. An automatic guided vehicle (AGV) forklift is a computer controlled mechanism that...
Automated guided vehicles (AGV) or mobile robots are types of guided robotic systems that are not bounded by a fixed range of motion. Rather, it is self-contained and can move along a line, surface, or space...
An autonomous mobile robot (AMR) is a self-propelled self-powered mechanism designed to perform repetitive tasks or organizational functions using an internal guidance system. They are able to navigate their...
A bucket elevator or grain leg is used to move items in bulk. The usage of bucket elevators is widespread, notably in commercial agriculture and mining, and several specialized businesses manufacture bucket elevators and...
A conveyor belt is a material handling system designed to move supplies, materials, and components using an efficient and effortless process that saves on time, energy, and cost. The design of conveyor belts includes two motorized pulleys with the conveyor material looped over them...
Palletizing is the process of putting items on a pallet. The process of emptying the loaded objects in the reverse pattern is known as depalletizing. A pallet is a flat, square-shaped platform used to transport and...
Flat belts are power transmission belts that are flat and made of rubber, synthetic composites, or leather. They are used to transfer rotational power in industrial equipment and conveyor systems. Flat belts have a low profile with a positive grip, which...
When examining hydraulics and pneumatics, it is important to understand the mechanical differences between them. Both are essential parts of various industries and are critical to the performance of several types of tasks...
A metal conveyor belt is a conveyor belt that uses metal in the form of flat sheets or woven wire mesh as its belt surface. The use of a metal surface enhances the ability of a conveyor to handle parts and...
A palletizer is an automated material handling machine used to stack and orient several individual products into a single load for a more convenient and economical method of handling, storage, and shipment. Palletizers are usually part of a bigger packaging process...
A robotic palletizer is a type of palletizer that employs a robotic arm to pick, orient, and place individual products and arrange them into a single stack of load. They are the next generation of palletizers, and they will supersede conventional palletizers...
A timing belt is made of rubber with hard teeth capable of interlocking with camshafts and crankshafts cogwheels. It is an integral component of an internal combustion engine responsible for...
A v-belt is a flexible machine element used to transmit power between a set of grooved pulleys or sheaves. They are characterized as belts having a trapezium cross-section...
Screw conveyors, or auger conveyors, are industrial equipment used in transporting bulk quantities of granular solids (e.g., powder, grains, granules), semi-solids, liquids, and even non-flowing materials from one point to another...
A vertical conveyor is an engineered mechanical method for moving goods, products, supplies, parts, and components from a lower level to a higher level or from a higher level to a lower level. They are...
Vibratory conveyors are material-handling equipment used to transport fine to coarse-grained bulk materials. These vibratory conveyors are strong conveying equipment utilized for bulk commodities with fine to coarse graininess...
In 1954, when Arthur "Mac" Barrett, of Barrett Electronics Corporation, unveiled the first AGV, he named it Guide-o-Matic and described it as a driverless vehicle...