Polyurethane Bushings
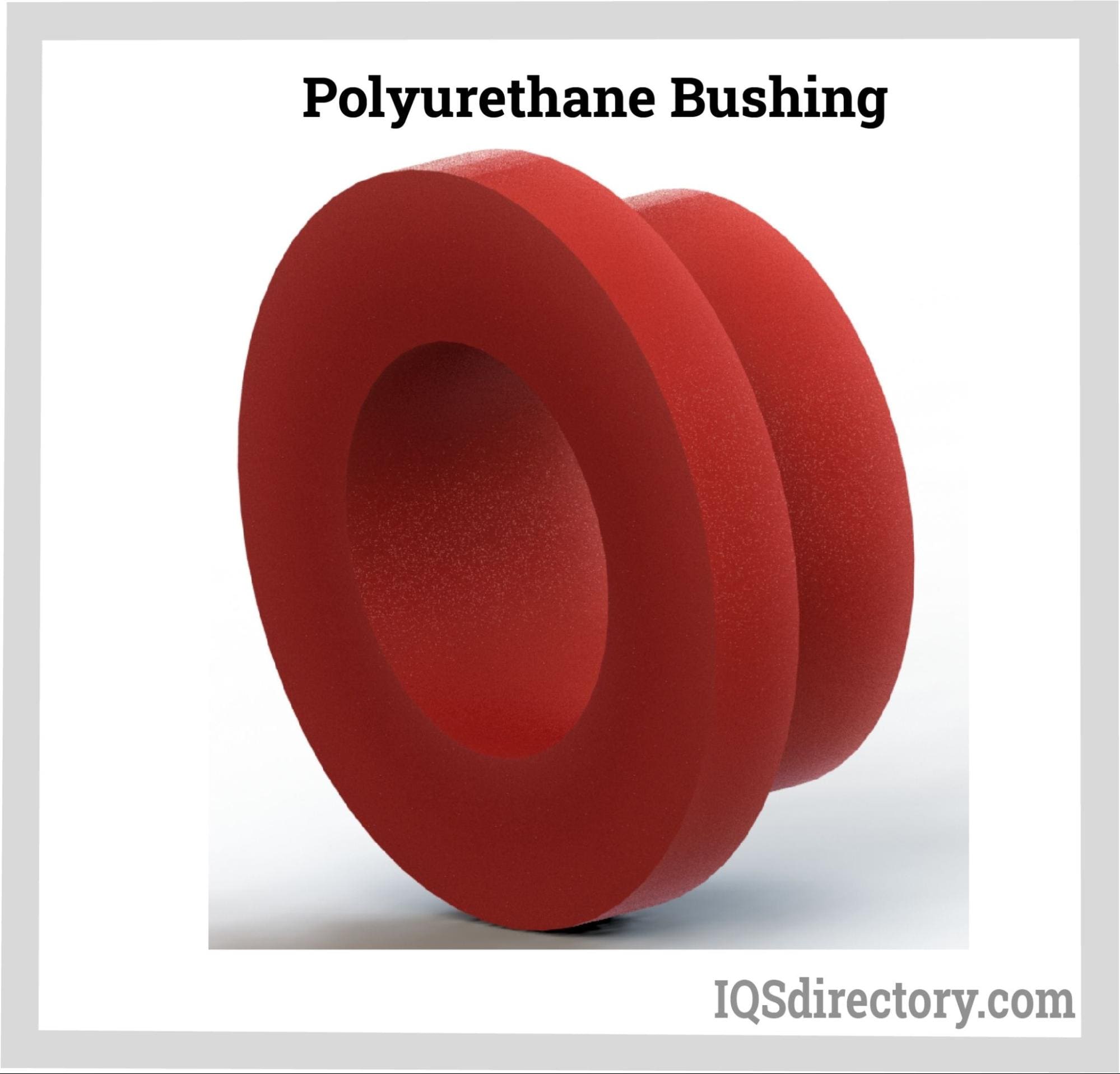
A polyurethane bushing is a friction reducing component that is placed between moving and stationary components as a replacement for lubricants. The use of polyurethane for the production of bushings is due to...
Please fill out the following form to submit a Request for Quote to any of the following companies listed on
This article will give you detailed insight into urethane casting and its uses.
You will learn:
Urethane casting is a method where polyurethane, along with other additive resins, is injected into pliable silicone elastomer molds. Although it bears similarities to injection molding, this technique doesn't require rigid, metal molds. Due to the susceptibility of silicone molds to wear, urethane casting is particularly suitable for producing short runs and low-to-medium volume outputs. It provides a cost-efficient and faster alternative compared to using metal molds, ensuring the delivery of high-quality molded items.
Castable polyurethane, a subtype of polyurethane, can be developed into advanced, engineering-grade products. Its mechanical characteristics vary from being soft and flexible to hard and rigid, based on its formulation.
Both urethane casting and injection molding are employed in manufacturing various plastic and polymer products, yet they significantly diverge in terms of materials used, production techniques, and economic efficiency.
Injection molding is predominantly a technique for high-volume, mass production, especially with thermoplastics. It involves melting plastic pellets, then injecting them under high pressure into a mold cavity. This process is efficient and precise, ideal for mass-producing identical items like automotive parts or consumer goods.
On the other hand, urethane casting is perfect for low-to-medium volume production suited for prototypes, small batch manufacturing, or tailored parts with varied geometries. This method uses liquid polyurethane or silicone, poured into molds and cured at ambient temperature, making it an economically feasible choice for small runs that demand more design flexibility.
While injection molding is tailored for extensive production with minimal design variation, urethane casting excels at producing low-to-medium quantities and creating intricate, personalized components. Consequently, both processes are invaluable, each catering to specific production needs.
Urethane casting involves four key components: polyol compounds, diisocyanate compounds, chain extenders or curatives, and additives. The mechanical properties of the cast depend on the formulation of the prepolymer resin (a mix of polyol and diisocyanate) and the curatives. Additives enhance properties such as resin curing time, machinability, color, and UV protection. However, additives must be carefully measured as excessive amounts can weaken the urethane cast.
One concern in urethane molding is the coefficient of friction (COF), which indicates how much plastic materials stick to each other. To reduce COF, "slip additives" are used. These organic compounds, such as acid amides, erucamide, and oleamide, coat the surfaces of plastic forms to minimize friction. Erucamide is a slow-moving additive, whereas oleamide is fast-moving.
The polyurethane reaction involves forming a polymer chain by reacting a polyol component (a carbon-chained molecule with alcohol groups at both ends) with a diisocyanate component (a molecule with isocyanate groups at both ends). This reaction results in a molecule with a reactive alcohol at one end and a reactive isocyanate at the other. The alcohol end links to another isocyanate, while the isocyanate end reacts with chain extenders (curatives like hydroxyl and amines), continuing the formation of long-chained polyurethane.
Formulating urethane can be achieved through different methods: single shot, prepolymer, and quasi-prepolymer processes. In the single shot process, all components are kept in separate chambers and then blended by a mixing head before being poured or injected into the mold. The prepolymer process involves mixing polyols and diisocyanates before pouring them into the mold, which helps to manage the heat generated from the exothermic reaction. The quasi-prepolymer process uses polyols that are partially reacted with diisocyanates, making the formulation easier due to the lower viscosity and reduced processing temperature required.
Urethane casting is a straightforward process that involves creating the pattern, making the mold, and pouring the resin. Below are the steps involved in producing urethane cast products.
The most common methods for creating a master pattern include 3D printing techniques such as SLA (stereolithography), PolyJet, and FDM (fused deposition modeling). CNC machining is another option. All methods begin with creating a CAD model of the part to be cast. When designing the 3D model, it is crucial to consider how the pattern will be molded and how the urethane cast will be removed. Keep the following suggestions in mind:
Avoid including problematic features such as deep or narrow holes, internal cavities, and channels in the initial pattern. These can be added through secondary processes after the urethane part has been cast.
Unlike die casting and injection molding, urethane casting does not require draft angles. The flexibility of silicone molds allows them to be deformed to easily remove the molded product.
Incorporate gates and vents into the CAD model. Gates are the entry points for injecting resin and curatives, while vents allow trapped air to escape from the mold. The size and placement of the gates should be based on the volume and shape of the pattern.
Section the model or separate its parts if necessary, depending on the build volume of the 3D printer.
Include locators on the mold to prevent shifting of the mold halves. Without locators, shifting can make the parting line of the molds more visible and result in products that do not meet dimensional tolerances.
Silicone formulations typically start as a viscous fluid made from siloxane polymers, which are then mixed with a cross-linker and a catalyst. The conversion of this siloxane fluid into a semi-solid is commonly achieved using two-component room temperature vulcanizing (RTV-2) methods. RTV-2 methods are categorized into two types: condensation cure and addition cure.
Condensation curing uses organo-tin compounds as catalysts. The process involves mixing a reactive component (including the silane crosslinker and catalyst) with a non-reactive component (the polymer and filler). This method tends to be less favorable compared to addition curing because it can cause shrinkage of about 0.5% as the curing agent gradually leaches out of the mold. However, an advantage of condensation curing is its resistance to inhibition, which occurs when contaminants on the pattern's surface prevent proper curing of the silicone. For instance, sulfur, commonly found in modeling clays, can inhibit curing. Therefore, if modeling clay is used for the master pattern, condensation curing might be the preferred choice.
Addition curing involves mixing the siloxane polymer with a platinum complex catalyst. This method does not produce by-products, resulting in an odorless mold with a longer shelf life and no shrinkage. Addition-cured silicones generally exhibit superior mechanical properties compared to condensation-cured silicones. However, they are highly sensitive to contaminants such as sulfur, phosphorus, arsenic, organo-tin compounds, PVC stabilizers, epoxy resin stabilizers, and natural rubbers.
In addition to two-component room temperature vulcanizing (RTV-2), other methods of silicone polymerization include one-component room temperature vulcanizing (RTV-1) and high temperature vulcanizing (HTV). RTV-1 cures when the silicone mixture is exposed to atmospheric humidity, undergoing hydrolysis that releases by-products such as alcohols, acetic acid, and ketones, which contribute to its characteristic odor. HTV, or peroxide curing, involves breaking down peroxides into free radicals at high temperatures, which cross-link the silicone polymer. However, HTV can lead to mold shrinkage due to the high coefficient of thermal expansion of silicone.
The elastomer components are mixed in a container larger than the silicone volume to accommodate expansion during degassing. While degassing is not strictly required, it is recommended to remove air bubbles that can cause imperfections in the urethane cast. During degassing, the silicone mixture will rise as trapped air is released and then return to its original level.
The next step is to prepare the silicone mold. A mold box or frame is set up to contain the silicone during the pouring process, similar to a flask used in metal casting.
The master pattern is placed inside the mold box, and the silicone and catalyst mixture is poured over it. There are several mold types: book mold, two-part mold, and skin mold. The book mold, also known as a single-stage mold, involves suspending the master pattern within the mold box and pouring silicone until it completely covers the pattern. After curing, the silicone block is cut in half to remove the pattern.
The two-part mold involves creating a predefined parting line on the master pattern. In this method, silicone is poured into the mold box up to the parting line. After curing, the pattern is removed, and a second mold is prepared from the remaining silicone.
Skin molding involves applying the silicone mixture layer by layer until a desired thickness is achieved.
After curing the silicone mold, applying a release agent before introducing the urethane is optional. While silicone is flexible and does not readily bond with urethane, making a release agent often unnecessary, it can facilitate the removal of the cast from the mold.
Open silicone molds are a basic form of mold widely used by DIY hobbyists. They are simpler to create compared to other mold types, involving two halves that are easier to make and require less precision.
The process begins with a pattern created by 3D printing or CNC machining. Inspect the pattern for any defects such as cracks, chips, or uneven surfaces, as these will appear in the final molded shape. Sanding and painting the pattern multiple times can ensure a proper surface finish. Once the pattern is free of errors, spray it with a release agent and place it, face up, in the bottom of a tightly sealed wooden box with adequate clearance on all sides for proper coverage.
The type of silicone used depends on the mold's intended use, including its hardness, which can range from hard and inflexible to soft and pliable. The complexity of the pattern also influences the choice of silicone. Silicone mixing can be based on weight or volume, which impacts the final product.
Pour the silicone over the pattern with careful control. Prior to pouring, determine the depth or height to which the silicone will be poured. Pour from the lowest point of the mold to fill crevices, intricate patterns, and openings effectively.
To avoid bubbles that can cause imperfections, place the silicone mixture in a vacuum degasser under pressure to remove any trapped air. This ensures a smooth, even solution.
Allow the silicone to cure after it has filled the box and covered the pattern. Curing agents can be tin or platinum, with platinum being the more expensive option. Curing time varies depending on the pattern’s complexity and silicone density, typically taking six hours or more under normal conditions.
After curing, gently remove the mold from the box. There may be bits of silicone, called flashing, that have seeped into the mold and need to be removed. Unlike injection molding, these fragments can be easily cut away.
A variety of polyurethane resins are available for casting, each with distinct properties. Selecting the appropriate urethane resins and curatives will be discussed in detail later. Once the silicone mold is prepared and the urethane resin chosen, the casting process can begin.
The casting process involves mixing the resin and curative, which react chemically to form the shape of the pattern. Similar to the silicone, the resin and curative are mixed in a container and degassed to remove trapped bubbles. The mixture is then introduced into the mold by either pouring or pressure filling. Pouring uses gravity to fill the mold, while pressure filling uses equipment like an injection ram or screw-type plunger to push the mixture into the mold.
After curing, the silicone mold is split into its two halves, and the urethane cast is removed.
Depending on the silicone mold’s quality, the urethane cast may have a smooth surface with minimal rough areas. Gates, vents, and flashings are trimmed and smoothed. Any holes or channels not included in the master pattern are drilled or milled to complete the product features. Note that urethane castings are susceptible to melting during machining; therefore, avoid aggressive machining and use coolants as necessary.
There are numerous machines available for urethane casting in the United States and Canada. These machines are crucial in today's industry as they facilitate the efficient production of custom polyurethane parts used across various sectors, including automotive, medical devices, and consumer goods. Below are several leading machines in this category.
The Baulé MK Series machines are renowned for their precision and versatility in handling a wide range of polyurethane materials, from flexible to rigid. Key features include automated mixing, precise temperature control, and user-friendly interfaces, making them a popular choice across various industries.
The Poly Purge series is highly regarded for its compact design, ease of use, and efficient material purging capabilities. These machines are well-suited for smaller-scale operations and prototyping due to their relatively lower capacity and cost.
Smooth-On is a leading manufacturer of urethane casting systems, offering a range of machines tailored to specific applications. Their systems often feature user-friendly controls, compatibility with multiple materials, and integrated vacuum degassing systems for high-quality casting results.
The Graco Reactor E-Series is renowned for its durability and efficient performance. It features precise mixing, temperature control, and ratio monitoring, making it ideal for large-scale industrial urethane casting applications.
The Moldman™ 8000 series offers automated solutions for precise and consistent urethane casting. These machines are equipped with advanced software controls, robotic handling, and closed-loop systems to enhance process control.
Note that the availability and popularity of specific models may have changed since this posting. For the most current information, it's advisable to contact manufacturers or suppliers of urethane casting machines in the United States and Canada.
Urethane castings offer distinct advantages over metals and other plastics due to their unique properties. Below are some key characteristics that make polyurethane resins exceptional.
Abrasion can be categorized into two types: sliding and impingement abrasion. Sliding abrasion occurs when a softer material rubs against a harder one, with or without contaminants present between the surfaces. Impingement abrasion, on the other hand, involves particles striking the surface, leading to erosion. Due to their resistance to both types of abrasion, cast urethanes are particularly well-suited for applications such as wheels and rollers.
Cast urethanes with a low coefficient of friction and high tear strength provide excellent resistance to sliding abrasion. For impingement abrasion, cast urethanes with high resilience are preferred. Resilient polyurethanes can easily deform elastically, which helps in distributing the impact forces from particles across the surface.
Abrasion resistance in urethane castings is largely influenced by the composition of the resin. Among the various polyol compounds used in polyurethane production, polyesters are known for their superior tear and abrasion resistance.
Polyurethane exhibits good impact resistance. It can absorb and dissipate energy when subjected to sudden or high-force impacts. This property is valuable in applications where protection against shocks and impacts is necessary, such as in sports equipment and automotive bumpers automotive bumpers.
Hardness refers to a material's resistance to localized surface deformation, typically assessed by measuring the depth of an indentation made by a standard indenter, ball, or presser foot. Materials are then ranked based on their relative hardness. For elastomers, hardness is often measured using the Shore hardness scale, which is determined with a durometer. The Shore hardness scale consists of 12 different scales, each with its own indenter configuration, profile, and force. The most commonly used scales for urethane castings are Shore A and Shore D. The Shore A scale is used for measuring the hardness of soft and semi-rigid polyurethanes, while the Shore D scale is used for hard rubbers and rigid polyurethanes. It's important to note that higher hardness does not necessarily indicate greater rigidity or strength.
Polyurethane generally offers excellent tensile strength, enabling it to endure stretching forces without breaking. The specific tensile strength can vary based on the formulation, but it is usually comparable to or exceeds that of many other plastics. Urethane casts can be engineered to achieve tensile strengths of up to 14,000 psi by incorporating composite materials such as fiberglass and carbon fibers.
Flexural strength is a measure of a material's ability to resist bending without undergoing permanent deformation or breakage. Polyurethane generally exhibits strong flexural strength, particularly in its rigid or semi-rigid forms. This property makes it suitable for applications involving structural components and load-bearing parts. Typically, polyurethane castings have a flexural strength of around 17,000 psi, with composite casts reaching up to 39,000 psi.
As previously discussed, urethane resins consist of four key components, with three of them significantly influencing the final mechanical properties of the product. The various formulations of these components allow for customization to meet specific application needs. Below is an overview of the urethane resin components, their types, and the properties they impart to the final product.
Polyols are low molecular weight compounds containing multiple hydroxyl (-OH) groups. They react with isocyanates to form polyurethane, with the isocyanates having two reactive ends that link with the polyols to create a network structure. This network gives polyurethane its distinctive properties. In urethane casting, polyols are primarily categorized into two types: polyether and polyester.
Polyethers are produced through the reaction of organic oxides with glycol. They are known for their resilience, high impact resistance, low heat build-up in dynamic applications, hydrolysis resistance, and good performance at low temperatures. Common polyether types used in polyurethane production include PTMEG and PPG. PTMEG offers superior quality but at a higher cost compared to PPG.
Polyesters are synthesized via the polycondensation reaction of diacids with glycol. Compared to polyethers, polyesters provide excellent abrasion resistance, heat aging resistance, oil and solvent resistance, as well as superior shock absorption and tear resistance.
Among the specialty polyols, polycarbonate and polycaprolactone are prominent. Although sometimes classified as polyesters, polycarbonates are valued for their engineering properties due to their strength and toughness. Polycaprolactone, on the other hand, enhances the urethane cast's resistance to water, oil, solvents, and chlorine.
Diisocyanates are chemical compounds featuring two isocyanate (-NCO) functional groups. They play a crucial role in producing polyurethane materials, including foams, coatings, and adhesives. The two primary types of diisocyanates are aliphatic diisocyanates and aromatic diisocyanates.
Aliphatic diisocyanates are known for their non-yellowing properties and lower reactivity. They are ideal for applications requiring color stability and chemical resistance, such as in polyurethane coatings, films, and castings. Common aliphatic diisocyanates include hexamethylene diisocyanate (HDI), hexamethylene diisocyanate (HMDI), and isophorone diisocyanate (IPDI).
Aromatic diisocyanates contain benzene rings in their chemical structure and are categorized into Naphthalenic Diisocyanates (NDI), Toluene Diisocyanate (TDI), and Methylenediphenyl Diisocyanate (MDI).
NDIs are more commonly used in Europe compared to the TDI and MDI-dominated American market. They offer excellent performance and durability for dynamic applications. However, NDIs have a high melting point, making them challenging to process, and they exhibit lower storage stability due to high reactivity. As a result, they are typically manufactured using specialized equipment at custom molders.
Aromatic diisocyanates, particularly Toluene Diisocyanate (TDI), are commonly used in applications requiring high hardness, such as guide rollers, unlike Methylenediphenyl Diisocyanate (MDI). In industrial settings, TDIs are typically used in an 80/20 blend of the 2,4 and 2,6 isomers. Achieving different proportions beyond this 80/20 blend necessitates an additional processing step.
Methylenediphenyl Diisocyanates (MDIs) are renowned for enhancing the resilience and impact strength of urethane casts. Consequently, MDIs, when paired with either polyethers or polyesters, are frequently used in dynamic and high-impact applications such as wheels, construction panels, and automotive bumpers. The most commonly used isomer for casting is the purified 4,4'-MDI.
Curatives are added to the polyol and diisocyanate prepolymer to transform the mixture into a solid or semi-solid elastomer. There are two primary types of curatives: hydroxyls and amines.
Hydroxyl curatives have hydroxyl groups (OH) at their molecular terminals, which facilitate the linking of prepolymers. A commonly used hydroxyl curative is 1,4-butanediol (BDO), often employed in MDI prepolymer systems at room temperature.
In addition to hydroxyl groups, amine groups (NH2) can also bond to the terminals of the prepolymer. A widely used amine curative is 4,4-methylenebis(2-chloroaniline), commonly known as MOCA, which serves as the base curative for TDI prepolymer systems. However, MOCA has been identified as a carcinogen by OSHA. As a result, alternative amine chain extenders, such as 4,4-methylenebis(3-chloro-2,6-diethylaniline) (MCDEA), are now used in place of MOCA.
Below are the main advantages of using urethane casting compared to die casting and injection molding.
Urethane casting benefits from using soft molds like silicone, which are significantly cheaper and easier to produce than metal molds. This makes it an ideal choice for casting prototypes and making modifications at a lower cost. Additionally, urethane casting does not require expensive equipment such as injection pumps, heaters, or kneading machines, further reducing overall investment costs.
Urethane molds can be created within three days as compared to hard molds that may require a week or two. Master patterns and silicone molds are easy to fabricate, making them suitable for pre-production runs that are usually on trial and error. Product design becomes much faster before transferring to hard tooling.
Urethane casting is favored for DIY and small-scale projects due to its straightforward processing requirements. Typically, only a few basic tools are needed: containers, a weighing scale, an air compressor, a mixer, and a spatula. Silicone molds can be made under atmospheric pressure and temperature conditions, while urethane resin usually requires heating to reduce viscosity, accelerate curing, or melt solid components.
Polyurethane systems offer versatility in physical properties, thanks to varying types and proportions of polyols, diisocyanates, and curatives. This flexibility allows for the formulation of materials with a wide range of characteristics. Urethanes can be tailored for high-performance, rigid applications like wheels and rollers, or for softer, shock-absorbing uses such as impact-absorbing pads and cushions. Various formulations are available, each designed for specific applications.
Due to their diverse range of properties, cast urethanes are utilized across various industries. Their versatility and low initial manufacturing costs make them a popular choice for many applications. Here are some common uses of urethane casting:
Urethane casting is frequently employed in product development to create prototypes for design validation and testing. This method provides a cost-effective and rapid way to iterate and refine designs before investing in expensive tooling for mass production.
Urethane wheels and rollers are known for their high load-bearing capacity, excellent wear resistance, and superior traction. They are also capable of absorbing shock and reducing noise levels, making them ideal for various industrial applications. Urethane's flexibility in durometer selection allows for tailored hardness, providing a perfect balance between grip and durability. Additionally, these cast components exhibit excellent resistance to chemicals and abrasion, ensuring longevity even in harsh environments.
Urethane castings can be engineered to be shock and vibration resistant, making them ideal for automotive applications. Additionally, their ability to withstand high temperatures allows them to serve as a replacement for steel in certain applications.
High vibration from rotating equipment causes rigid materials to crack. Urethane castings can be made to absorb vibrations, as seen from shock absorbers and dampers.
Urethane formulations that are FDA compliant are available, making urethane casting a suitable method for producing medical devices. This method is particularly advantageous for low-volume production of specialized or uniquely designed medical products.
Due to their versatile properties, urethane castings are used in a variety of consumer products. Examples include shoe soles, sports equipment, electronics casings, and more.
A polyurethane bushing is a friction reducing component that is placed between moving and stationary components as a replacement for lubricants. The use of polyurethane for the production of bushings is due to...
Polyurethane molding is the process of fabricating or manufacturing plastic parts by introducing a urethane polymer system into a tool or mold and allowing it to cure. Like any other type of plastic, the excellent processability...
Polyurethane rollers are cylindrical rollers covered by a layer of elastomer material called polyurethane. Depending on the application, the inner roller core is prone to scratches, dents, corrosion, and other types of damage...
Urethane wheels are wheels made of molded urethane, also known as polyurethane. Urethane is an elastomer that comprises urethane carbamate linkages and is a portmanteau phrase for elastic polymer...
Blow molding is a type of plastic forming process for creating hollow plastic products made from thermoplastic materials. The process involves heating and inflating a plastic tube known as a parison or preform. The parison is placed between two dies that contain the desired shape of the product...
Molding is a manufacturing process that uses a mold - the latter being a solid container used to give shape to a piece of material. It is a forming process. The form is transferred from the mold to the material by...
Fiberglass molding is a method for forming complex and intricate parts using fiberglass resin. Though there are several reasons for producing parts and components from fiberglass, the most pressing reasons are the...
Fiberglass is a plastic reinforced material where glass fiber is used as reinforcement, and the glass fiber is flattened into a sheet. It is also known as glass fiber reinforced plastic or glass reinforced plastic...
Many of the products used daily are made possible by producers and suppliers of rubber and plastic. These substances are robust, adaptable, and capable of practically any shape required for various industrial purposes. Several varieties are...
Plastic bottles are bottles made of high or low-density plastic, such as polyethylene terephthalate (PET), polyethylene (PE), polypropylene (PP), polycarbonate (PC), or polyvinyl chloride (PVC). Each of the materials mentioned has...
Plastic caps and plugs are two distinct ways for sealing the ends, tops, and openings of tubes and containers. Caps are placed over the opening, and plugs are placed in the opening. Due to the many varieties of...
Plastic coating is the application of liquid polymers or plastic on the surface of a workpiece by dipping or immersion. The result is a thick plastic finish for protective and decorative purposes. This gives the material additional resistance against...
Plastic injection molding, or commonly referred to as injection molding, is a manufacturing process used in the mass fabrication of plastic parts. It involves an injection of molten plastic material into the mold where it cools and...
Plastic overmolding has a long and interesting history, dating back to the early 1900s. The first overmolding process was developed by German chemist Leo Baekeland, who invented Bakelite, the first synthetic plastic. Baekeland used a...
Reaction injection molding or RIM molding is a molding process that involves the use of two chemical elements with high reactivity and low molecular mass that collide and mix before being injected into a closed mold. High pressure pumps circulate isocyanate and...
Rotational molding, commonly referred to as "rotomolding", is a plastic casting technique used to produce hollow, seamless, and double-walled parts. It uses a hollow mold tool wherein the thermoplastic powdered resin is heated while being rotated and cooled to solidify...
Rubber injection molding is when uncured rubber is transformed into a usable product by injecting raw rubber material into a mold cavity made of metal. The applied pressure produces a chemical reaction like...
Rubber molding is a process of transforming uncured rubber or an elastomer into a usable product by transferring, compressing, or injecting raw rubber material into a metal mold cavity...
There are several methods to perform rubber overmolding, and each method has its own unique advantages and disadvantages. The choice of method typically depends on the design and material requirements of the product being...
Silicone rubber molding is a method for shaping, forming, and fabricating silicone rubber parts and products using a heated mold. The process involves compressing or injecting silicone rubber into a mold...
Thermoplastic molding is a manufacturing process that works to create fully functional parts by injecting plastic resin into a pre-made mold. Thermoplastic polymers are more widely used than thermosetting...
A grommet edging is a flexible rubber or plastic strip that covers rough and sharp surfaces found in openings and edges of panel walls to protect the passing electrical cables, wires, and other sensitive components...